Thermodynamics and Heat Transfer
Thermodynamics and heat transfer form the scientific backbone of how energy is transformed and moved in mechanical systems. These fields are essential in understanding engines, power plants, refrigeration cycles, and heating systems. For aspiring engineers, mastering thermodynamic principles enables them to design efficient systems across industries—from industrial technologies to automotive engineering. Energy conservation, work interactions, entropy changes, and heat flow mechanisms are central concerns not only in classical applications but also in modern innovations such as smart manufacturing and energy-efficient designs.
With rising emphasis on sustainability, engineers must incorporate thermodynamic analysis into systems that promote energy and resource efficiency. Understanding heat engines and thermal cycles is vital for advancing sustainable manufacturing and reducing carbon footprints. Thermodynamic insights also influence material selection and system performance in nanotechnology and advanced materials, where thermal conductivity and energy dissipation are critical considerations.
Real-world mechanical systems do not operate in isolation. They interact with mechanical structures studied in solid mechanics, and fluid flow behaviors explored in fluid mechanics. Whether designing an aircraft turbine or a building’s HVAC system, a well-rounded understanding of thermal systems is essential. The relationship between heat, work, and energy storage in thermal systems informs key design decisions in CAD-based mechanical design and performance simulations.
Thermodynamic principles also underpin the development of emerging technologies such as digital twins, where real-time thermal performance can be modeled and optimized. Integrating lean manufacturing principles and automated controls based on thermal conditions further enhances process reliability. As robotics and automation become more prevalent in thermal-sensitive environments, engineers must incorporate dynamic heat flow considerations into the system architecture.
Thermal analysis also plays a critical role in areas like biomechanical engineering, where human tissue interactions with prosthetics or implants depend on heat transfer properties. As engineers work across interdisciplinary boundaries, familiarity with thermal behaviors becomes invaluable in optimizing production processes, refining quality control, and integrating automation with industrial robotics. Furthermore, engineers must consider human-machine interaction, where ergonomics often overlaps with heat exposure and thermal comfort. As energy systems evolve, so does the importance of thermodynamics in engineering education and practice, making it a vital subject for any mechanical or control system specialist.
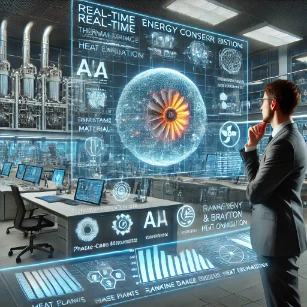
Table of Contents
Core Concepts of Thermodynamics
The Laws of Thermodynamics
- First Law of Thermodynamics (Conservation of Energy):
- This law asserts that the total energy of an isolated system remains constant. Energy may change form—such as from thermal to mechanical or chemical—but it cannot be created or destroyed.
- In practical applications, this principle forms the basis for analyzing energy flows in engines, power plants, and heating systems.
- Example: In an internal combustion engine, the chemical energy stored in gasoline is transformed into mechanical energy that propels a vehicle and heat that is expelled through the exhaust system.
- Mathematically, it is expressed as ΔU = Q – W, where ΔU is the change in internal energy, Q is the heat added to the system, and W is the work done by the system.
- Second Law of Thermodynamics:
- This law introduces the concept of entropy and dictates that natural processes tend to move toward a state of greater disorder or randomness.
- It explains why certain energy conversions are irreversible and why perpetual motion machines are impossible.
- Example: A hot cup of coffee left in a room eventually cools down; the heat dissipates into the surroundings, increasing the system’s entropy.
- The second law is also the basis for determining the maximum efficiency of heat engines, described by the Carnot cycle.
- Third Law of Thermodynamics:
- This law posits that as the temperature of a system approaches absolute zero, the entropy of a perfect crystalline structure approaches zero as well.
- It has implications for low-temperature physics, such as cryogenics, and the limitations of cooling systems.
- At absolute zero (0 K), atomic motion virtually ceases, making entropy minimal.
- Zeroth Law of Thermodynamics:
- Though listed last in discovery, it forms the logical basis for temperature measurement and thermal equilibrium.
- It states that if two systems are in thermal equilibrium with a third system, they are in thermal equilibrium with each other.
- This principle justifies the use of thermometers as a third system to measure temperature consistently.
Thermodynamic Properties
- Temperature (T):
- Represents the average kinetic energy of particles in a system and governs the direction of heat transfer.
- Increases in temperature typically increase reaction rates and energy availability within a system.
- Pressure (P):
- The force exerted by gas or liquid molecules on the walls of their container per unit area.
- It plays a critical role in thermodynamic cycles, particularly in gas laws and engine systems.
- Volume (V):
- The three-dimensional space occupied by a system. Changes in volume are associated with work done in thermodynamic processes.
- For gases, volume variations significantly affect pressure and temperature, governed by Boyle’s and Charles’s laws.
- Internal Energy (U):
- The total energy (kinetic + potential) of all particles within a system. It changes when heat or work is exchanged with the surroundings.
- Internal energy is a state function and is foundational to analyzing closed and open thermodynamic systems.
- Enthalpy (H):
- Represents the total heat content of a system at constant pressure, defined as H = U + PV.
- Enthalpy changes are used extensively in calculating energy balance in processes like boiling, melting, and chemical reactions.
- Entropy (S):
- A quantitative measure of disorder or randomness in a system. Higher entropy reflects higher irreversibility and energy dispersal.
- Entropy is central to predicting the feasibility and spontaneity of processes, especially in the second law of thermodynamics.
- Entropy concepts are being applied in modern fields such as energy-efficient system design and information theory.
Thermodynamic Processes
- Isothermal Process:
- Characterized by constant temperature, requiring heat exchange to balance work output/input.
- Example: Gas expansion in a piston immersed in a thermal reservoir.
- Described mathematically by PV = constant for ideal gases.
- Adiabatic Process:
- Occurs with no heat transfer between the system and surroundings, often leading to rapid compression or expansion.
- Used in modeling insulated engines and shock wave behavior.
- Follows the relation PVγ = constant, where γ is the heat capacity ratio.
- Isobaric Process:
- Involves constant pressure, typical in heating water at atmospheric pressure or expansion in a piston-cylinder device.
- Involves enthalpy change as the primary energy descriptor.
- Isochoric Process:
- Also known as an isometric process, it occurs at constant volume, meaning no boundary work is done.
- All energy transferred appears as internal energy, useful in calorimetry and pressure vessel analysis.
Core Concepts of Heat Transfer
Heat transfer is a fundamental topic in thermodynamics and engineering that deals with how thermal energy moves through and between materials and systems. Understanding heat transfer mechanisms is essential in the design and operation of systems ranging from household appliances and industrial machinery to spacecraft and biological systems. The three primary modes of heat transfer—conduction, convection, and radiation—each have distinct physical principles and governing equations that determine the rate and direction of thermal energy flow.
Conduction
- Conduction refers to the transfer of heat through a stationary material due to a temperature gradient within the medium. It occurs at the microscopic level when high-energy (hotter) particles collide with lower-energy (colder) particles, transferring kinetic energy.
- Fourier’s Law:
- This law quantifies the heat flux (*q*) as proportional to the negative gradient of temperature and the thermal conductivity (*k*) of the material: q = -k (dT/dx).
- Materials with high thermal conductivity, such as copper and aluminum, conduct heat more efficiently than insulators like wood or fiberglass.
- Example: When a metal rod is heated at one end, thermal energy moves toward the cooler end, establishing a temperature profile along its length. Engineers must account for this when designing heat sinks, engine blocks, and cooking utensils.
- Factors influencing conduction include material type, cross-sectional area, temperature gradient, and thickness.
Convection
- Convection is the transfer of heat between a solid surface and a fluid (liquid or gas) that is in motion. The moving fluid transports heat from one location to another by the combined effects of conduction within the fluid and advection due to bulk motion.
- Types:
- Natural Convection:
- Occurs when fluid motion is caused by buoyancy forces that result from temperature-induced density differences.
- Example: Warm air rising from a heater in a room, creating circulation patterns without any mechanical assistance.
- Forced Convection:
- Occurs when fluid movement is driven by external means such as fans, blowers, or pumps.
- Example: Coolant flowing through a car radiator, where a water pump maintains circulation for effective heat dissipation.
- Natural Convection:
- Newton’s Law of Cooling:
- This empirical law states that the rate of convective heat transfer is proportional to the temperature difference between the solid surface and the surrounding fluid: q = hA(Tsurface – Tfluid), where *h* is the convective heat transfer coefficient, and *A* is the surface area.
- The value of *h* depends on fluid properties, surface geometry, and flow conditions (laminar or turbulent).
- This principle is applied in HVAC systems, industrial drying processes, and electronics cooling solutions such as heat exchangers and fan-cooled devices.
Radiation
- Unlike conduction and convection, radiation does not require a medium to transfer heat. Instead, it involves the emission of electromagnetic waves—primarily infrared—from all matter above absolute zero temperature.
- Stefan-Boltzmann Law:
- This law defines the power radiated per unit area by a black body as proportional to the fourth power of its absolute temperature: q = εσT⁴, where *ε* is the emissivity, *σ* is the Stefan-Boltzmann constant, and *T* is the temperature in Kelvin.
- Objects with higher surface temperatures and emissivity values emit more radiation. Black matte surfaces are efficient radiators, while polished metals reflect more than they emit.
- Example: Solar energy reaching Earth from the Sun is transmitted entirely by radiation. Similarly, thermal cameras detect infrared radiation emitted by warm objects.
- Radiation is significant in applications such as spacecraft thermal control, industrial furnaces, and building insulation. Engineers also study radiation interactions using advanced thermometry techniques to achieve precise temperature control in high-precision manufacturing.
Applications of Thermodynamics and Heat Transfer
HVAC Systems (Heating, Ventilation, and Air Conditioning)
- Heating:
- Heating applications in buildings utilize thermodynamic cycles and principles to ensure thermal comfort and energy efficiency. Common technologies include furnaces, electric heaters, radiant floor heating, and heat pumps. Heat pumps, in particular, exploit the refrigeration cycle in reverse to extract heat from the environment and deliver it indoors, making them highly efficient even in moderately cold climates.
- Boilers convert water into steam or hot water using combustion or electric heating, distributing thermal energy through radiators or underfloor systems.
- Proper insulation and heat load calculations are vital to prevent energy losses and oversizing of equipment.
- Ventilation:
- Thermodynamic analysis helps engineers design airflow systems that ensure adequate air exchange rates, humidity control, and contaminant removal while minimizing energy costs. Ventilation strategies vary from natural systems using pressure differences to mechanical systems with air handling units and ductwork.
- Energy recovery ventilators (ERVs) and heat recovery ventilators (HRVs) help pre-condition incoming air using the outgoing exhaust, enhancing thermal performance without increasing the energy demand.
- Air Conditioning:
- Air conditioners rely on the vapor-compression refrigeration cycle, where refrigerants absorb heat from indoor spaces and reject it outdoors via a condenser coil. The cycle involves compression, condensation, expansion, and evaporation stages, all governed by the laws of thermodynamics.
- Proper sizing and seasonal energy efficiency ratios (SEER) are critical for effective cooling without excessive energy use. Multi-zone systems, variable refrigerant flow (VRF), and ductless split units expand flexibility in modern residential and commercial environments.
- These systems also rely on psychrometric principles to balance temperature and humidity levels for maximum comfort and health.
Engines
- Internal Combustion Engines:
- These engines operate based on thermodynamic cycles such as the Otto and Diesel cycles. In both cases, fuel combustion increases the internal energy of the working fluid (air-fuel mixture), which is then converted into mechanical work by piston motion.
- Heat losses, friction, and imperfect combustion reduce real-world efficiency below the ideal Carnot limit. Engineers use thermodynamic analysis to optimize compression ratios, air-fuel mixtures, and exhaust heat recovery for performance gains.
- Jet Engines:
- Jet propulsion systems are governed by the Brayton cycle, which compresses air, adds heat via combustion, and expands it through turbines and nozzles to produce thrust. Key parameters include turbine inlet temperature, pressure ratio, and exhaust velocity.
- These systems require extensive cooling and materials that can withstand extreme thermal gradients, making thermodynamics essential in material selection and engine architecture.
- Rocket Engines:
- Rocket engines operate in a vacuum and must carry both fuel and oxidizer. They rely on chemical reactions that release immense heat to generate high-speed exhaust, providing thrust via Newton’s third law. Thermodynamics governs nozzle design, combustion chamber pressure, and propellant selection.
- Thermal insulation and regenerative cooling techniques are crucial to prevent engine failure due to overheating.
Power Plants
- Thermal Power Plants:
- These facilities typically use Rankine cycles where water is heated into steam, expanded through turbines, and then condensed back into liquid. Improving the thermal efficiency of each stage can result in significant energy and cost savings.
- Combined heat and power (CHP) systems capture waste heat for district heating or industrial use, enhancing overall energy utilization.
- Nuclear Power Plants:
- Thermodynamics is vital in converting the thermal energy released from fission reactions into mechanical work. Pressurized Water Reactors (PWRs) and Boiling Water Reactors (BWRs) differ in how they manage steam generation, pressure control, and safety systems.
- Advanced reactors may use molten salts, liquid metals, or gas coolants to achieve higher efficiencies and safety margins.
- Combined Cycle Power Plants:
- These systems integrate a gas turbine (Brayton cycle) with a steam turbine (Rankine cycle). Waste heat from the gas turbine’s exhaust is recovered and used to generate steam, significantly boosting overall efficiency compared to single-cycle plants.
- This approach is widely used in modern grid-scale power generation for its ability to balance efficiency, flexibility, and environmental performance.
Renewable Energy Systems
- Solar Thermal Power:
- Parabolic troughs, solar towers, and dish Stirling systems concentrate sunlight to heat fluids, generate steam, and produce electricity. Thermodynamic analysis is used to improve storage capacity, thermal conductivity, and conversion efficiency.
- Molten salt storage allows for energy use during cloudy periods or nighttime, addressing intermittency issues.
- Geothermal Systems:
- Geothermal plants extract heat from the Earth’s interior using deep wells and injectors. This heat is used in binary or flash steam cycles to drive turbines.
- Applications range from district heating and industrial processes to greenhouse agriculture and therapeutic spas.
- Heat Pumps:
- These devices can both heat and cool spaces by moving thermal energy from one environment to another. Ground-source heat pumps are especially efficient in moderate climates due to stable underground temperatures.
- Innovative heat pump applications are now being explored for district energy systems and industrial waste heat recovery. Learn more about current research through this U.S. Department of Energy article on heat pump innovation.
Industrial Processes
- Heat Exchangers:
- Shell-and-tube, plate, and spiral heat exchangers enable efficient thermal energy transfer between fluids. Their design depends on flow arrangement (parallel, counterflow, cross-flow), heat load, and material compatibility.
- Industries such as petroleum refining, chemical production, pharmaceuticals, and food processing rely heavily on custom heat exchanger systems to control process temperatures and ensure product quality.
- Furnaces and Kilns:
- Used in high-temperature processes like metal smelting, glass blowing, and ceramic firing, these devices convert chemical or electrical energy into thermal energy for precise temperature control.
- Refractory materials and combustion analysis are crucial to minimize heat loss and maximize throughput.
Aerospace and Automotive Applications
- Thermal Management:
- Heat dissipation in compact, high-power systems such as jet engines, lithium-ion battery packs, and avionics requires advanced thermal analysis. Phase-change materials, active cooling systems, and high-conductivity composites are used for thermal regulation.
- Reentry Vehicles:
- Spacecraft reentering Earth’s atmosphere experience intense thermal flux due to air compression and friction. Thermal protection systems (TPS) made from ablative or heat-resistant materials like reinforced carbon-carbon ensure structural integrity and crew safety.
Electronics Cooling
- Thermal energy generated by microprocessors, graphics cards, and power regulators must be dissipated efficiently to prevent performance degradation or failure. Solutions include heat sinks, thermal interface materials (TIMs), liquid cooling loops, and thermoelectric coolers (TECs).
- Engineers use Computational Fluid Dynamics (CFD) and transient thermal analysis to model heat transfer within electronic enclosures and printed circuit boards (PCBs).
Cryogenics
- Cryogenic systems operate at extremely low temperatures, often below −150°C, and are used for liquefying gases like oxygen, nitrogen, and hydrogen. Applications include MRI machines, superconducting magnets, quantum computing, and rocket fuel storage.
- Thermodynamic properties at cryogenic temperatures deviate significantly from standard models, requiring specialized instrumentation and insulation materials to minimize boil-off and ensure energy efficiency.
Advanced Research and Innovations
Advanced Heat Transfer Materials
- High-Entropy Alloys:
- High-entropy alloys (HEAs) are a new class of materials composed of multiple principal elements mixed in near-equal proportions. Unlike traditional alloys, which typically include one dominant element, HEAs exhibit remarkable properties due to their high configurational entropy. This results in improved thermal stability, corrosion resistance, and structural robustness at high temperatures.
- In heat transfer applications, HEAs are being explored for use in environments where thermal gradients, mechanical loads, and chemical corrosion are extreme—such as in nuclear reactors, hypersonic vehicles, and turbine blades.
- Research is ongoing to understand their phase stability, oxidation behavior, and performance under thermal cycling conditions.
- Nanofluids:
- Nanofluids consist of nanoparticles suspended in base fluids such as water, ethylene glycol, or oil. The addition of these nanoparticles—typically metals, metal oxides, or carbon-based structures—significantly enhances the thermal conductivity and convective heat transfer performance of the fluid.
- Applications of nanofluids include cooling of high-performance electronic devices, solar thermal systems, and automotive radiators. Their high surface area and energy transport properties make them effective in compact heat exchanger designs.
- Challenges remain in terms of long-term stability, nanoparticle agglomeration, and manufacturing cost, but promising results are emerging in experimental and simulation studies.
Computational Methods
- CFD (Computational Fluid Dynamics):
- CFD is revolutionizing thermal system design by allowing engineers to simulate fluid flow, temperature distribution, and turbulence within complex geometries. It is widely applied in the automotive, aerospace, HVAC, and biomedical industries.
- By solving the Navier-Stokes equations numerically, CFD software can predict the interaction of heat and fluids, assess component-level thermal performance, and reduce prototyping costs.
- Advanced turbulence models, multi-phase flow analysis, and conjugate heat transfer simulations enable detailed optimization of thermal management systems.
- Finite Element Analysis (FEA):
- FEA is used to simulate heat conduction within solids, evaluate thermal stresses, and understand failure mechanisms due to thermal cycling. It divides complex geometries into discrete elements, enabling numerical solutions for temperature fields and deformation under thermal loads.
- FEA tools are essential in the design of electronic packaging, welding processes, battery enclosures, and turbine blades. Coupled thermomechanical analysis is especially important in evaluating fatigue and creep in high-stress thermal environments.
- Integration with machine learning is also emerging as a means to accelerate design cycles and uncover hidden performance trends.
Energy Efficiency and Sustainability
- Waste Heat Recovery:
- Waste heat is an untapped resource in many industrial and commercial processes. Technologies like Organic Rankine Cycles (ORCs), thermoelectric generators, and heat pipes are being developed to capture and reuse this low-grade heat.
- ORCs operate similarly to traditional steam cycles but use organic working fluids with low boiling points, making them suitable for recovering heat from flue gases, geothermal sources, and engine exhaust.
- Integrating waste heat recovery systems can reduce energy consumption, lower greenhouse gas emissions, and enhance process efficiency. Research on cost-effective and scalable designs is expanding rapidly across manufacturing and transportation sectors.
- Zero-Energy Buildings:
- Zero-energy buildings (ZEBs) aim to balance annual energy consumption with renewable energy production. Thermodynamics plays a central role in designing these structures to minimize energy demand for heating, cooling, and ventilation.
- Advanced building envelopes, passive solar heating, radiant floor systems, and energy-recovery ventilators are common components. Building Information Modeling (BIM) and thermal simulation tools guide architects in achieving optimal insulation, window-to-wall ratios, and air tightness.
- Organizations like the National Renewable Energy Laboratory provide valuable guidelines and case studies on net-zero design and implementation.
Micro- and Nano-Scale Heat Transfer
- At the micro- and nano-scales, classical Fourier-based heat conduction models break down due to quantum effects and ballistic transport phenomena. Research in this domain focuses on understanding phonon behavior, thermal boundary resistance, and electron-phonon interactions.
- Applications include microprocessors, MEMS devices, thin-film coatings, and biomedical implants. Efficient thermal management at these scales is essential for device reliability and performance.
- Experimental techniques such as time-domain thermoreflectance (TDTR) and scanning thermal microscopy are used to measure localized thermal properties with nanometer resolution.
Thermoelectric Materials
- Thermoelectric materials enable direct conversion between thermal and electrical energy via the Seebeck and Peltier effects. These materials are critical for power generation in remote areas, vehicle exhaust recovery, and cooling of microelectronic systems.
- Recent research focuses on enhancing their figure of merit (ZT) by manipulating band structures, using nanostructuring techniques, and combining organic and inorganic compounds.
- Common thermoelectric materials include bismuth telluride, lead telluride, and skutterudites. Emerging applications in wearable electronics and green energy solutions are driving a surge of interdisciplinary innovation in this field.
Challenges in Thermodynamics and Heat Transfer
Energy Losses:
- One of the most significant challenges in thermodynamics is minimizing energy losses in practical systems. The second law of thermodynamics dictates that all real processes involve an increase in entropy, leading to irreversible losses, particularly in the form of wasted heat. For example, in internal combustion engines, a large fraction of the energy from fuel is lost as exhaust heat and friction, rather than being converted to useful mechanical work.
- In thermal power plants, the Carnot efficiency sets a theoretical upper limit, but real-world performance often falls far below it due to imperfect insulation, component inefficiencies, and suboptimal operating conditions.
- Advanced materials, better system designs, and improved insulation are being pursued to limit energy dissipation. Still, it remains an uphill battle to approach thermodynamic ideality in complex systems operating under dynamic conditions.
- Smart monitoring and predictive maintenance tools using AI and IoT are also being integrated to reduce hidden losses and improve overall efficiency.
Material Limitations:
- Thermal systems often operate in demanding environments characterized by extreme heat, rapid temperature fluctuations, and aggressive chemical exposures. Finding materials that can maintain their structural integrity, thermal conductivity, and resistance to fatigue under such conditions is a constant challenge.
- For instance, in aerospace propulsion or nuclear power systems, materials must endure thousands of thermal cycles without cracking or degrading. Conventional materials such as steel or copper may fail prematurely due to creep, oxidation, or thermal expansion mismatch.
- To address this, researchers are developing ceramics, high-temperature polymers, and superalloys with tailored microstructures. However, issues like cost, manufacturability, and recyclability limit their widespread adoption.
- Thermal barrier coatings (TBCs), often used in gas turbines, represent an intermediate solution, but even they face delamination and failure at elevated operational cycles.
System Integration:
- Modern energy systems are no longer isolated; they involve intricate interactions between components such as heat exchangers, pumps, turbines, batteries, and control units. Achieving high efficiency requires seamless integration of thermodynamic and heat transfer subsystems across mechanical, electrical, and chemical interfaces.
- For example, integrating a heat recovery unit into an industrial plant must consider not only the thermodynamic compatibility but also space constraints, flow dynamics, safety protocols, and real-time control mechanisms. Improper integration can lead to backflows, temperature imbalances, or even catastrophic failures.
- Multi-physics simulation tools and digital twins are emerging as essential for visualizing these complex systems and optimizing their performance before physical implementation. Yet, the need for accurate models and real-world validation remains a bottleneck.
- Additionally, the adoption of renewable energy systems—such as solar thermal or geothermal—introduces variability and intermittency, complicating thermal management at both system and grid levels.
Environmental Concerns:
- Many traditional thermodynamic processes, especially those relying on fossil fuels, contribute heavily to greenhouse gas emissions and global warming. Even technologies that are efficient in converting energy often generate byproducts that pose environmental risks.
- For instance, refrigerants used in air conditioning and heat pumps are potent greenhouse gases. Replacing them with eco-friendly alternatives requires redesigning entire systems to accommodate new working fluids with different thermodynamic properties.
- In the quest for sustainability, lifecycle analysis of materials, energy use, and emissions is becoming standard in thermal system design. Engineers must now weigh thermodynamic efficiency against environmental impact and economic viability.
- Global initiatives such as the International Energy Agency’s energy efficiency programs are pushing for policies and technologies that minimize waste and pollution across all thermodynamic applications.
- Finally, regulatory pressures and carbon pricing are forcing industries to innovate cleaner and more responsible thermal management solutions, which requires interdisciplinary collaboration between thermodynamicists, materials scientists, and environmental engineers.
Future Trends for Thermodynamics and Heat Transfer
- Green Energy Technologies:
- As the global community intensifies its efforts to combat climate change, thermodynamics and heat transfer are central to advancing green energy solutions. Renewable technologies like solar thermal systems rely on improved heat capture, storage, and conversion efficiencies to be economically viable on large scales.
- Wind energy systems are also benefiting from enhanced thermal management in generator components, especially at offshore installations where environmental stresses are high. Moreover, thermodynamic modeling is essential in designing energy storage units—such as molten salt or phase-change materials—that enable solar and wind power to deliver consistent energy even when natural input fluctuates.
- Hydrogen fuel cells, poised as a clean energy alternative, require intricate thermal regulation to maintain performance and prevent overheating. In building technologies, innovations in insulation, ventilation, and heat recovery contribute to the goal of net-zero or even net-positive energy buildings. These developments underscore the increasing need for thermodynamic optimization across all green energy platforms.
- High-Performance Computing:
- The convergence of thermodynamics and digital technologies is revolutionizing how thermal systems are designed, monitored, and controlled. High-performance computing (HPC) platforms are enabling multi-scale simulations that were previously computationally prohibitive, from the atomic interactions in materials to large-scale energy system behavior.
- Artificial Intelligence (AI) and machine learning algorithms are being deployed to optimize thermal performance in real-time. These tools analyze sensor data streams to adjust parameters dynamically, improving efficiency, detecting anomalies, and extending the lifespan of thermal systems.
- This fusion of data science and thermofluid engineering is particularly transformative in smart grids, HVAC systems in large buildings, and advanced manufacturing plants. An external perspective from the U.S. Department of Energy’s Office of Scientific and Technical Information highlights ongoing research that leverages HPC and AI to simulate and manage next-generation energy systems.
- Additive Manufacturing:
- The advent of additive manufacturing (AM), or 3D printing, is reshaping how thermal devices are conceptualized and fabricated. Engineers are no longer bound by conventional machining constraints, enabling the production of complex geometries that enhance heat transfer rates and reduce pressure drops in heat exchangers.
- Lattice structures, conformal cooling channels, and topology-optimized components are now feasible, significantly boosting thermal management in aerospace, automotive, and electronics applications. Furthermore, AM allows for the use of composite or functionally graded materials with spatially varying thermal conductivities, opening doors to unprecedented customization of thermal behavior.
- As the cost of 3D printing technologies drops and materials expand to include high-performance ceramics and metals, additive manufacturing is poised to become a standard method for developing next-generation thermal systems across diverse industries.
- Space Exploration:
- Thermodynamic and heat transfer research is fundamental to the success of future space exploration missions. In the vacuum of space, where convection is absent, radiation becomes the dominant mode of heat transfer, requiring new materials and thermal management strategies for spacecraft and extraterrestrial habitats.
- Advanced thermal control systems are being developed for applications ranging from Mars rovers and orbiters to human habitats on the Moon. These systems must withstand intense radiation, extreme temperature cycles, and abrasive lunar or Martian dust—all while operating reliably for years with minimal maintenance.
- Technologies like heat pipes, variable conductance radiators, and thermoelectric generators are evolving rapidly to meet these unique demands. Additionally, simulation tools that incorporate the nuances of extraterrestrial environments are enabling engineers to test and refine systems before launch, ensuring safety and efficiency in unforgiving conditions.
Why Study Thermodynamics and Heat Transfer
Understanding Energy Systems
Thermodynamics explains how energy is converted and conserved in physical systems. This is crucial for designing engines, power plants, and refrigeration systems. Mastery of thermodynamic principles enables engineers to create efficient and sustainable energy solutions.
Heat Transfer in Engineering Applications
Heat transfer governs how thermal energy moves through materials and systems, affecting performance and safety. Applications include cooling of electronics, insulation, and thermal management in buildings and vehicles. Engineers must understand conduction, convection, and radiation to manage heat effectively.
Designing Efficient Systems
Engineers use thermodynamic and heat transfer principles to maximize system efficiency and reduce energy losses. This leads to innovations such as energy recovery systems and green technologies. Knowledge in this area supports global efforts to combat climate change.
Core to Mechanical and Aerospace Engineering
Thermodynamics and heat transfer are central to mechanical and aerospace engineering disciplines. They form the basis for understanding propulsion systems, HVAC systems, and thermal protection. A strong foundation in these subjects is essential for advanced engineering roles.
Preparation for Research and Innovation
These subjects prepare students for research into new materials, renewable energy sources, and innovative energy systems. They provide the theoretical base for computational modeling and experimentation. This fosters creativity and critical thinking in engineering research.
Thermodynamics and Heat Transfer: Conclusion
Thermodynamics and heat transfer form the foundation upon which much of modern engineering and technology is built. These disciplines underpin our ability to harness, transform, and control energy—capabilities essential for human development, comfort, and survival. As we move further into the 21st century, the relevance and scope of these fields continue to expand, playing a pivotal role in driving progress across energy systems, manufacturing processes, transportation, and even biological and environmental sciences.
Thermodynamics offers a systematic framework for understanding energy flows and transformations, allowing engineers and scientists to analyze complex systems ranging from nuclear reactors and power grids to living organisms. By applying the laws of thermodynamics, we gain predictive control over how energy behaves under different conditions—enabling optimization of engines, design of more sustainable buildings, and modeling of large-scale phenomena such as climate systems and ocean currents.
Meanwhile, heat transfer principles enable us to manage thermal energy effectively within these systems. Whether it’s dissipating heat from a microprocessor in a laptop, optimizing insulation in a spacecraft, or maximizing efficiency in a geothermal power plant, the ability to control how heat moves is a core challenge and opportunity in every field of engineering. The growing demand for high-efficiency thermal management in sectors like electric vehicles, data centers, and advanced manufacturing highlights the vital role of heat transfer science.
Recent advancements in materials science have significantly expanded what is possible in these domains. High-performance materials such as thermal barrier coatings, nanofluids, and thermoelectric composites are pushing the boundaries of efficiency and durability. Coupled with powerful simulation tools like computational fluid dynamics (CFD) and finite element analysis (FEA), engineers can now model complex thermal systems with incredible accuracy. These digital tools reduce time-to-market, improve safety, and open up novel design possibilities never before achievable with traditional trial-and-error methods.
Equally important is the integration of data-driven energy analysis and automation, allowing systems to self-regulate, adapt to changing conditions, and minimize energy loss in real time. As artificial intelligence (AI) and the Internet of Things (IoT) become more embedded in infrastructure and manufacturing, thermal systems will increasingly respond dynamically to user needs and environmental fluctuations—improving both performance and sustainability.
Thermodynamics and heat transfer are also central to tackling global challenges. In the energy sector, they are essential for reducing carbon emissions, increasing the penetration of renewables, and improving the efficiency of fossil fuel systems during the transition to cleaner sources. In climate science, these principles help model atmospheric and oceanic dynamics, providing insights critical for policy and mitigation. In healthcare, precise thermal control is crucial for technologies such as cryopreservation, diagnostic imaging, and laser surgery.
Looking to the future, the convergence of these fields with emerging technologies—such as quantum computing, space colonization, and bio-inspired engineering—will further amplify their impact. From enabling heat-resistant materials for Mars missions to developing zero-energy buildings and personalized thermal comfort systems, the possibilities are vast and transformative. Education and research in thermodynamics and heat transfer will continue to be a cornerstone of engineering curricula, inspiring the next generation of scientists and engineers to push boundaries and develop solutions that benefit humanity.
In conclusion, thermodynamics and heat transfer are not just academic subjects—they are dynamic, applied sciences that shape nearly every facet of modern life. Their continued evolution will determine how effectively we meet the technological, environmental, and societal challenges of the coming decades.
Thermodynamics and Heat Transfer: Review Questions with Detailed Answers
Q1. What is the First Law of Thermodynamics, and why is it important in mechanical engineering?
A1. The First Law of Thermodynamics states that energy cannot be created or destroyed, only transformed from one form to another. In mechanical engineering, it underpins the principle of energy conservation in systems such as engines, turbines, and HVAC units. By quantifying heat and work exchanges, engineers can design and optimize systems to use energy more efficiently.
Q2. Differentiate between conduction, convection, and radiation as modes of heat transfer.
A2.
- Conduction is heat transfer through direct molecular contact, occurring primarily in solids where molecules vibrate and pass thermal energy to adjacent molecules.
- Convection involves bulk fluid motion, where heated fluid (liquid or gas) moves and carries heat with it; common in boilers or radiators.
- Radiation is heat transfer through electromagnetic waves and does not require a medium, allowing heat transfer even in a vacuum (as with solar radiation).
Q3. How do open, closed, and isolated systems differ in thermodynamics?
A3.
- Open Systems exchange both mass and energy with their surroundings (e.g., a boiler with water and heat flows in and out).
- Closed Systems only exchange energy (heat or work) but not mass (e.g., a sealed piston-cylinder device).
- Isolated Systems exchange neither mass nor energy with their surroundings, essentially remaining thermally and materially self-contained (e.g., an ideal thermos).
Q4. What role does the Second Law of Thermodynamics play in determining the direction of heat flow?
A4. The Second Law of Thermodynamics states that heat naturally flows from a higher temperature body to a lower temperature body and that processes involving energy transformation are irreversible in real-world scenarios. It introduces the concept of entropy, which measures the degree of disorder and helps predict the feasibility and efficiency of thermodynamic processes.
Q5. Explain the concept of specific heat capacity and its relevance in thermal system design.
A5. Specific heat capacity is the amount of heat required to raise the temperature of a unit mass of a substance by one degree Celsius (or Kelvin). It is crucial in thermal system design for determining how much energy is needed to achieve a desired temperature change. Engineers use this property to size and select materials for heat exchangers, cooling systems, and thermal storage devices.
Q6. What is entropy, and how does it relate to the performance of heat engines?
A6. Entropy is a measure of a system’s disorder or randomness. In thermodynamics, it quantifies the energy unavailable for work. The Second Law dictates that entropy increases in isolated systems, influencing the maximum theoretical efficiency of heat engines. Lower entropy production typically indicates higher efficiency, meaning designs that minimize irreversible losses yield better performance.
Q7. How do isobaric, isochoric, isothermal, and adiabatic processes differ in thermodynamic analysis?
A7.
- Isobaric: Pressure remains constant; volume and temperature change.
- Isochoric: Volume remains constant; pressure and temperature change.
- Isothermal: Temperature remains constant; pressure and volume change.
- Adiabatic: No heat transfer occurs; pressure, volume, and temperature can all change but the total heat exchange is zero.
Q8. Describe the role of thermal conductivity in selecting materials for heat exchangers.
A8. Thermal conductivity measures how quickly heat can pass through a material. In heat exchangers, materials with high thermal conductivity (e.g., copper or aluminum) are preferred because they transfer heat efficiently from one fluid to another, improving overall system performance. Material cost, corrosion resistance, and structural strength are also considered in design.
Q9. In practical applications, why is convection often enhanced using fins or extended surfaces?
A9. Fins or extended surfaces increase the surface area over which heat exchange takes place. By enlarging the contact area with the surrounding fluid, convection is enhanced, and more heat can be transferred in a shorter time. This principle is widely used in car radiators, air-cooled engines, and electronic component heat sinks.
Q10. What factors influence heat transfer by radiation, and how can engineers control radiative heat loss or gain?
A10. Radiative heat transfer depends on the surface emissivity, surface temperature (to the fourth power), and geometry/orientation of surfaces. Engineers can control radiative heat loss or gain by selecting surface coatings with appropriate emissivity (e.g., reflective finishes to reduce heat emission) and by insulating or shielding systems to reflect or block unwanted radiation.
Thermodynamics and Heat Transfer: Thought-Provoking Questions
1. What is the practical significance of differentiating between open, closed, and isolated systems in thermodynamic analysis?
Answer:
- Open Systems allow both mass and energy to cross their boundaries, which is crucial in applications like internal combustion engines or turbine systems where fluids flow in and out. By modeling the flow of fluid (and the energy carried with it), engineers can optimize the performance of these machines (e.g., better fuel injection in combustion engines).
- Closed Systems only allow energy (in forms such as heat or work) to cross the boundary, making them useful for analyzing piston–cylinder devices or refrigeration cycles. This helps in designing processes where mass remains constant but temperature and pressure must be controlled.
- Isolated Systems exchange neither mass nor energy, serving as theoretical models for conservation of total energy and entropy considerations. Real applications use this concept as a baseline to compare how much actual systems deviate from the ideal of no loss or gain from the surroundings.
2. How does the Second Law of Thermodynamics guide engineers in predicting the feasibility and efficiency of real-world thermodynamic processes?
Answer:
The Second Law of Thermodynamics introduces the concept of entropy and states that entropy tends to increase in isolated systems. In engineering practice, this law:
- Predicts Feasibility: Certain processes (like spontaneous heat flow from hot to cold) are naturally favored, while the reverse (from cold to hot without work input) is not feasible on its own.
- Limits Efficiency: No heat engine can be 100% efficient since some energy must always be rejected as waste heat. This guides engineers to seek designs that minimize irreversibilities (like friction, turbulence, unrestrained expansion) and reduce entropy production to improve efficiency.
3. In what ways do conduction, convection, and radiation each play a critical role in everyday heating and cooling systems?
Answer:
- Conduction: Dominates within solid components (for example, heat moving through a metal pot on a stove). In HVAC systems, conduction is key in heat exchangers where solid surfaces transfer thermal energy to or from fluids.
- Convection: Central to fluid flow in heating and cooling. Whether it’s forced convection with fans in air conditioning units or natural convection in radiators, it ensures that hot or cool fluid circulates, distributing thermal energy effectively.
- Radiation: Emission of heat through electromagnetic waves. Sunlight is the most obvious example; in building design, understanding radiative heat gain or loss through windows and reflective surfaces helps regulate interior temperatures efficiently.
4. Why is understanding entropy crucial when designing high-efficiency engines or refrigeration systems, and how do engineers practically reduce entropy generation?
Answer:
Entropy quantifies the ‘unavailable’ energy in a system and represents the irreversibility of real processes. In engines or refrigerators, higher entropy generation means lower usable energy output or increased energy input for the same effect. Engineers reduce entropy generation by:
- Optimizing Heat Transfer Steps: Minimizing temperature differences across which heat is transferred reduces losses.
- Reducing Friction and Turbulence: Streamlined flows and better lubrication prevent chaotic flow patterns that raise entropy.
- Employing Multistage Processes: Such as multi-stage turbines and compressors, which split large temperature or pressure changes into smaller steps, minimizing irreversibility.
5. How do phase-change processes (e.g., boiling and condensation) fit within the framework of thermodynamics and heat transfer, and why are they essential in power generation cycles?
Answer:
Phase changes involve latent heat, a significant amount of energy exchanged at constant temperature. In power generation (e.g., steam turbines), water boils into steam (absorbing latent heat), which then expands through turbines to produce work. Afterward, the steam condenses back to water (releasing latent heat) in condensers, ready for the cycle to repeat. This cyclical process efficiently harnesses energy because latent heat transfer can be relatively large and occurs at constant temperature, simplifying control and energy recovery.
6. In real-life engineering scenarios, why is it important to consider both the macroscopic (thermodynamics) and microscopic (statistical mechanics) perspectives of heat and energy transfer?
Answer:
- Macroscopic (Thermodynamics) Perspective: Provides system-wide laws and equations (like the First and Second Laws) for analyzing heat, work, and energy interactions without delving into molecular details. This is ideal for large-scale system design (e.g., power plants or refrigeration systems).
- Microscopic (Statistical Mechanics) Perspective: Offers insight into how molecular motion and interactions drive energy exchange, temperature, and entropy on a fundamental level. This can inform materials selection, nanotechnology-based heat transfer improvements, and the prediction of phenomena like phase transitions at fine scales.
Balancing both views ensures engineers can design systems effectively, from choosing materials with the right thermal properties to optimizing large-scale processes for maximum efficiency.
7. How does the concept of “thermal resistance” in conduction parallel electrical resistance, and what practical steps do engineers take to reduce heat loss in systems?
Answer:
Thermal resistance is analogous to electrical resistance: just as electrical current meets resistance in a circuit, heat flow meets resistance in a thermal path. Materials or composite walls that have high thermal resistance impede heat flow. Engineers reduce unwanted heat loss by:
- Using Insulation: Materials with low thermal conductivity, such as fiberglass or aerogels, slow heat flow.
- Minimizing Thermal Bridges: Points where highly conductive materials (metal frames, studs) bypass insulation are carefully addressed to prevent localized heat paths.
- Optimizing Geometries: Design choices (like thicker walls or strategic layering of materials) are employed to lengthen the thermal path and raise overall thermal resistance.
8. What are the most common dimensionless parameters (like Reynolds number, Prandtl number, and Nusselt number) in convective heat transfer, and how do they influence design decisions?
Answer:
- Reynolds Number (Re): Indicates the ratio of inertial to viscous forces in a fluid flow. Whether flow is laminar or turbulent affects heat transfer rates and pressure drops.
- Prandtl Number (Pr): Relates momentum diffusivity to thermal diffusivity. It helps characterize how fast heat moves through a fluid compared to the fluid’s motion.
- Nusselt Number (Nu): Describes the ratio of convective to conductive heat transfer across a boundary layer. High values imply strong convective heat transfer relative to conduction.
Engineers leverage these parameters to choose appropriate flow rates, surface geometries, and fluid types in heat exchangers and cooling systems to balance efficiency, cost, and reliability.
9. In what ways can the Carnot cycle be seen as an ideal reference for real-world heat engines, and why can’t real engines achieve Carnot efficiency?
Answer:
The Carnot cycle is the theoretical maximum efficiency cycle operating between two temperature reservoirs. It’s ideal because it assumes fully reversible processes and no entropy generation. However, real engines cannot achieve Carnot efficiency due to:
- Friction and Turbulence: Mechanical and fluid friction generate heat and dissipate energy.
- Finite Time for Heat Transfer: Achieving completely reversible processes would require infinite time for heat exchange, which is impractical.
- Non-ideal Materials: Real materials undergo wear and have limitations on temperature resistance, increasing irreversibility.
Despite these limitations, the Carnot cycle sets the upper benchmark engineers aim to approach with better designs and advanced materials.
10. How do engineers account for heat transfer by radiation in large-scale applications such as power plants or high-temperature industrial processes?
Answer:
- High Temperatures: At elevated temperatures, radiation can dominate over conduction and convection (e.g., in furnaces). Engineers use radiative heat transfer equations that involve emissivity, temperature differences (to the fourth power), and geometry factors.
- Reflective Surfaces & Insulation: Surfaces with high reflectivity (low emissivity) or advanced insulation (ceramic coatings) minimize radiative heat loss.
- Computational Tools: Complex geometries are often analyzed with radiative models in simulations to optimize furnace design, turbine blades, or heat shields for uniform temperature distribution and efficiency.
11. What challenges do engineers face when developing cooling systems for high-performance electronics, and how do thermodynamics and heat transfer principles help overcome them?
Answer:
- Compact Geometries: Electronic components pack tightly, generating hotspots that are difficult to cool.
- Low Thermal Margin: Modern chips operate at high clock speeds and power densities, leaving little tolerance for temperature increases.
- Thermodynamic & Heat Transfer Applications:
- Conduction Solutions: Using highly conductive materials (e.g., copper, graphene) or heat pipes to spread heat quickly away from the source.
- Convection Methods: Fans or liquid cooling loops for forced convection.
- Phase-Change Techniques: Vapor chambers or immersion cooling in specialized fluids leverage latent heat transfer for more efficient cooling.
Engineers rely on thermodynamic analysis and advanced heat transfer methods to keep electronics within safe temperature ranges and maintain optimal performance.
12. Looking ahead, how might emerging technologies like nanofluids, advanced composites, or phase-change materials revolutionize the field of heat transfer and thermal management?
Answer:
- Nanofluids: Fluids containing nanoparticles can exhibit significantly higher thermal conductivity, improving convective heat transfer in radiators, heat exchangers, or electronic cooling loops.
- Advanced Composites: Lightweight, thermally conductive composites might replace heavier metals, leading to more efficient automotive and aerospace designs due to lower mass and better heat dissipation.
- Phase-Change Materials (PCMs): These materials absorb or release large amounts of latent heat at specific temperatures, enabling advanced thermal storage solutions for renewable energy systems or smart building envelopes.
As these materials become more accessible, they could redefine efficiency benchmarks, reduce system sizes, and open up new applications in energy sustainability and high-performance engineering.
Thermodynamics and Heat Transfer: Sample Numerical Questions with Solutions
These problems cover various core concepts—conduction, convection, radiation, and basic thermodynamic laws
1. Heat Conduction Through a Metal Rod
Question
A cylindrical metal rod is 0.5 m long, with a cross-sectional area of
The thermal conductivity k of the metal is 200W/(m.K). One end of the rod is maintained at 100ºC and the other end at 20ºC .
Calculate the steady-state heat flow rate (Q) through the rod.
Solution
- Formula for steady-state conduction:
- Plug in the values:
Numerical calculation:
- Result:
2. Convective Heat Transfer From a Flat Plate
Question
Air at
flows over a flat plate maintained at
. If the convective heat transfer coefficient
is
and the plate’s surface area is
, calculate the rate of heat transfer by convection.
Solution
- Formula for convective heat transfer:
- Plug in the values (converting temperatures to Kelvin differences is not strictly necessary here, as it’s a temperature difference):
- Numerical calculation:
- Result:
3. Radiation Heat Transfer Between Two Surfaces
Question
Two large parallel plates each have an emissivity of
. Plate A is at
and Plate B is at
. Calculate the net radiative heat transfer rate per unit area (
) from Plate A to Plate B. Use
.
Solution
- Formula for net radiation exchange between two large parallel plates:
Here,
εA=εB=0.8.
- Calculate the denominator for emissivities:
- Calculate
TA4−TB4:
- Compute
qnet:
- Result:
(Note: Depending on rounding, results may slightly differ.)
4. First Law of Thermodynamics in a Piston-Cylinder
Question
A piston-cylinder device contains
of a gas. The gas is heated from
to
at constant pressure. If the specific heat at constant pressure
, calculate the heat added (
) in kilojoules, assuming negligible work other than boundary work at constant pressure.
Solution
- Formula for heat added at constant pressure:
- Plug in the values:
- Numerical calculation:
- Result:
5. Efficiency of a Carnot Engine
Question
A Carnot heat engine operates between two reservoirs at
and
. Calculate the maximum theoretical efficiency (
) of this engine as a percentage.
Solution
- Carnot efficiency formula:
- Plug in the temperatures:
- Convert to a percentage:
- Result:
6. Mass Flow Rate in a Steady-Flow System
Question
In a steady-flow device, water enters at a mass flow rate of
. It gains
of energy from a heat source as it passes through. If there is no significant change in kinetic or potential energy, how much heat transfer (
˙) occurs per second?
Solution
- First Law for steady-flow with negligible changes in KE and PE:
Δh is the change in specific enthalpy, which equals
in the form of heat gained.
- Plug in the values:
- Calculate in
, and the temperature difference across the entire wall is
20 K 20\,\mathrm{K} . Calculate the heat flux (
Q ˙ / A \dot{Q}/A ) through the wall.
- First Law for steady-flow with negligible changes in KE and PE:
Solution
- Equivalent thermal resistance
R total R_{\text{total}} Rtotal in series:
R total = L 1 k 1 + L 2 k 2 R_{\text{total}} \;=\; \frac{L_1}{k_1} \;+\; \frac{L_2}{k_2} - Compute each term:
R 1 = 0.02 0.8 = 0.025 m 2 K / W R_1 = \frac{0.02}{0.8} = 0.025\,\mathrm{m^2 K/W} R 2 = 0.01 0.04 = 0.25 m 2 K / W R_2 = \frac{0.01}{0.04} = 0.25\,\mathrm{m^2 K/W} R total = 0.025 + 0.25 = 0.275 m 2 K / W R_{\text{total}} = 0.025 + 0.25 = 0.275\,\mathrm{m^2 K/W} - Overall heat transfer:
Q ˙ = Δ T R total × A \dot{Q} \;=\; \frac{\Delta T}{R_{\text{total}}} \times A - Heat flux (per unit area) is:
Q ˙ A = Δ T R total = 20 0.275 ≈ 72.73 W / m 2 \frac{\dot{Q}}{A} = \frac{\Delta T}{R_{\text{total}}} = \frac{20}{0.275} \approx 72.73\,\mathrm{W/m^2} - Result:
Heat flux = 72.73 W / m 2 \text{Heat flux} = 72.73\,\mathrm{W/m^2}
- Equivalent thermal resistance
8. Determining Outlet Temperature in a Heat Exchanger
Question
Water enters a heat exchanger at
and flows at
. It absorbs heat at a rate of
10kW. Given the specific heat of water
cp, determine the water outlet temperature.
Solution
- First, relate heat absorbed (
Q ˙ \dot{Q} ) to mass flow rate (
m ˙ \dot{m} ), specific heat (
c p c_p ), and temperature change (
Δ T \Delta T ):
Q ˙ = m ˙ c p Δ T \dot{Q} = \dot{m} \, c_p \, \Delta T - Rearrange to find
Δ T \Delta T :
Δ T = Q ˙ m ˙ c p \Delta T = \frac{\dot{Q}}{\dot{m} \, c_p} - Plug in the values (converting kW to kJ/s if needed—1 kW = 1 kJ/s):
Q ˙ = 10 k W = 10 k J / s \dot{Q} = 10\,\mathrm{kW} = 10\,\mathrm{kJ/s} m ˙ = 0.05 k g / s , c p = 4.2 k J / ( k g ⋅ K ) \dot{m} = 0.05\,\mathrm{kg/s}, \quad c_p = 4.2\,\mathrm{kJ/(kg \cdot K)} Δ T = 10 k J / s 0.05 k g / s × 4.2 k J / ( k g ⋅ K ) \Delta T = \frac{10\,\mathrm{kJ/s}}{0.05\,\mathrm{kg/s} \times 4.2\,\mathrm{kJ/(kg \cdot K)}} = 10 0.21 = 47.62 K ≈ 47.6 ∘ C = \frac{10}{0.21} = 47.62\,\mathrm{K} \approx 47.6^\circ\mathrm{C} - Outlet temperature:
T out = T in + Δ T = 15 ∘ C + 47.6 ∘ C = 62.6 ∘ C T_{\text{out}} = T_{\text{in}} + \Delta T = 15^\circ\mathrm{C} + 47.6^\circ\mathrm{C} = 62.6^\circ\mathrm{C} - Result:
T out ≈ 62.6 ∘ C T_{\text{out}} \approx 62.6^\circ\mathrm{C}
- First, relate heat absorbed (
9. Calculating Entropy Change in an Isothermal Process
Question
0.1kg of an ideal gas undergoes an isothermal expansion at
from a volume of
to
3. The gas constant
R for the gas is
. Calculate the entropy change
of the gas in
.
Solution
- Entropy change for an isothermal process (ideal gas):
Δ S = R ln ( V 2 V 1 ) \Delta S = R \,\ln\!\biggl(\frac{V_2}{V_1}\biggr) This is per unit mass for a gas with specific gas constant R.
- Plug in volumes and R
Δ S = 0.287 k J / ( k g ⋅ K ) × ln ( 0.04 0.02 ) \Delta S = 0.287\,\mathrm{kJ/(kg \cdot K)} \times \ln\!\biggl(\frac{0.04}{0.02}\biggr) - Calculate the logarithmic term:
ln ( 0.04 0.02 ) = ln ( 2 ) ≈ 0.693 \ln\!\biggl(\frac{0.04}{0.02}\biggr) = \ln(2) \approx 0.693 - Numerical result:
Δ S = 0.287 × 0.693 ≈ 0.199 k J / ( k g ⋅ K ) \Delta S = 0.287 \times 0.693 \approx 0.199\,\mathrm{kJ/(kg \cdot K)} - Result:
Δ S ≈ 0.20 k J / ( k g ⋅ K ) \Delta S \approx 0.20\,\mathrm{kJ/(kg \cdot K)}
- Entropy change for an isothermal process (ideal gas):
10. Work Done in an Adiabatic Expansion
Question
An ideal gas expands adiabatically from an initial state of
to a final volume of
. The process follows
, with
. If the gas is assumed ideal, calculate the work done by the gas (
) in joules. Assume no heat transfer (
).
Solution
- Relationship for an adiabatic process (ideal gas):
P 1 V 1 γ = P 2 V 2 γ P_1 V_1^\gamma = P_2 V_2^\gamma We need to find
P 2 P_2 first, then compute the work.
- Find
P 2 P_2 :
P 2 = P 1 ( V 1 V 2 ) γ P_2 = P_1 \biggl(\frac{V_1}{V_2}\biggr)^\gamma Converting
P 1 P_1 into Pa (SI units):
1bar=105Pa,5bar=5×105Pa P 2 = 5 × 10 5 P a × ( 0.01 0.02 ) 1.4 = 5 × 10 5 P a × ( 0.5 ) 1.4 P_2 = 5 \times 10^5 \,\mathrm{Pa} \times \biggl(\frac{0.01}{0.02}\biggr)^{1.4} = 5 \times 10^5 \,\mathrm{Pa} \times \bigl(0.5\bigr)^{1.4}
Approximate( 0.5 ) 1.4 (0.5)^{1.4}
. Numerically,0.5 1.4 ≈ 0.38 0.5^{1.4} \approx 0.38
.P 2 ≈ 5 × 10 5 × 0.38 = 1.9 × 10 5 P a P_2 \approx 5 \times 10^5 \times 0.38 = 1.9 \times 10^5\,\mathrm{Pa} - Formula for work in an adiabatic process (no heat exchange, ideal gas):
W = P 2 V 2 − P 1 V 1 1 − γ W = \frac{P_2 V_2 – P_1 V_1}{1 – \gamma} (This is derived from the energy balance and the polytropic relation, noting
γ = C p / C v \gamma = C_p/C_v .)
\gamma = C_p/C_v - Plug in the values:
W = ( 1.9 × 10 5 P a × 0.02 m 3 ) − ( 5 × 10 5 P a × 0.01 m 3 ) 1 − 1.4 W = \frac{(1.9 \times 10^5 \,\mathrm{Pa} \times 0.02\,\mathrm{m^3}) – (5 \times 10^5 \,\mathrm{Pa} \times 0.01\,\mathrm{m^3})}{1 – 1.4} = ( 3800 ) − ( 5000 ) − 0.4 = − 1200 − 0.4 = 3000 J = \frac{(3800) – (5000)}{ -0.4} = \frac{-1200}{-0.4} = 3000\,\mathrm{J} - Result:
W = 3000 J W = 3000\,\mathrm{J} Final Notes
- Units have been carefully chosen or converted to SI where necessary.
- Small variations in numerical answers may occur based on rounding at intermediate steps.
- These examples illustrate fundamental thermodynamics and heat transfer principles—conduction, convection, radiation, and the application of the First/Second Laws in different processes.
Use these problems and solutions to reinforce conceptual understanding and to practice the analytical methods essential in mechanical engineering thermodynamics and heat transfer.
- Formula for work in an adiabatic process (no heat exchange, ideal gas):
- Relationship for an adiabatic process (ideal gas):