Automotive Engineering
Automotive engineering stands at the crossroads of innovation, performance, and sustainability, playing a central role in shaping the future of transportation. This interdisciplinary field blends mechanical principles with systems design to produce safe, efficient, and intelligent vehicles. It draws heavily from core disciplines such as mechanical engineering and extends into advanced areas including industrial and manufacturing technologies, making it essential for anyone interested in vehicle design, dynamics, propulsion, and mobility systems.
At the heart of automotive design is a deep understanding of mechanical systems. Engineers rely on solid mechanics to assess structural integrity and resilience under real-world stress. The principles of fluid mechanics and hydraulics are applied to optimize cooling systems, fuel injection, and aerodynamic performance. Managing energy within these systems involves mastery of thermodynamics and heat transfer, ensuring thermal efficiency and minimizing losses.
Automotive systems also depend on responsive feedback mechanisms. Engineers integrate control systems to regulate functions like cruise control, braking, and steering. Advanced technologies such as digital twin technology now allow simulation of vehicle behavior before physical prototypes are built, reducing development time and enhancing design accuracy.
The design process itself relies on tools like CAD-based mechanical design, which facilitate iterative modelling and streamline the path from concept to production. Alongside these, innovations in 3D printing and advanced materials are enabling lightweight vehicle components and enhanced fuel efficiency.
Vehicle safety and ride quality are influenced by studies in vibrations and acoustics, ensuring noise reduction and occupant comfort. Similarly, insights from ergonomics shape the interior layout, control accessibility, and user experience.
Production efficiency is another vital element of automotive engineering. Students explore manufacturing and production engineering to optimize processes, while embracing concepts like lean manufacturing and Industry 4.0 for automation, real-time monitoring, and data-driven decision-making. Components must meet high standards through rigorous quality control and assurance.
Modern vehicle systems are becoming increasingly sophisticated, often involving collaborative technologies like robotics and automation in both design and assembly lines. Sustainability is also rising on the agenda, with engineers incorporating principles of sustainable manufacturing and improving energy efficiency throughout the lifecycle of automotive products.
From integrating biomechanical engineering for safer crash simulations to exploring emerging applications in nanotechnology, the automotive sector offers a dynamic environment for engineering creativity. Strong supply chain coordination is also critical, and insights from supply chain management help streamline logistics and parts delivery globally.
Automotive engineering not only focuses on what moves people and goods—it drives the transformation of industries. Its fusion of traditional engineering with digital innovation equips future professionals to develop smarter, cleaner, and more efficient transportation solutions for tomorrow’s world.
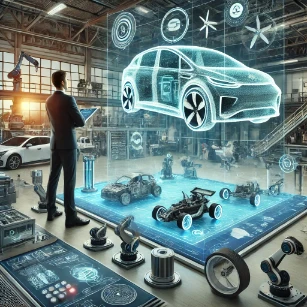
Table of Contents
Core Areas of Automotive Engineering
Vehicle Design and Development
- Concept Design:
- Concept design marks the beginning of any vehicle’s development journey, where creativity meets functionality. Engineers and designers collaborate to create preliminary sketches, clay models, and digital renderings that define the car’s exterior silhouette, proportions, and interior layout. The process integrates brand identity, market trends, and user expectations to craft compelling designs that stand out.
- Computer-aided design (CAD) tools such as CATIA, SolidWorks, and Alias are used to digitally sculpt the vehicle, enabling precise iterations and seamless integration of styling with mechanical components. This stage often includes the use of virtual reality (VR) to simulate driver perspectives and validate visibility, accessibility, and intuitiveness of controls.
- Ergonomics is a key concern during concept development. Seat dimensions, control placements, and ingress/egress are optimized through anthropometric data and human modeling software. This ensures comfort for drivers and passengers of various body types and mobility needs. In electric and autonomous vehicles, new packaging freedom further influences cabin layout and user interface design.
- Concept validation includes rapid prototyping using 3D printing and full-scale mockups to gather feedback and assess the visual impact and practicality of the design. Teams also study sustainability, incorporating recyclable materials and life-cycle design principles right from the early stage to align with evolving environmental standards.
- Additionally, market positioning strategies are interwoven with design language, targeting luxury, utility, or performance niches. Consumer behavior studies and demographic analytics guide key design decisions. For example, urban electric compact cars prioritize minimal footprint and interior modularity, while sports cars highlight aerodynamic aesthetics and aggressive stance.
- Structural Engineering:
- Structural engineering in automotive design ensures that the vehicle frame supports intended loads, protects occupants during crashes, and withstands long-term stress without failure. Engineers utilize finite element analysis (FEA) to simulate load paths, stress concentrations, and deformation under various scenarios, including frontal and side impacts, rollover, and torsional forces.
- Materials play a pivotal role in optimizing strength-to-weight ratio. High-strength steel is favored for its cost-effectiveness and durability, while aluminum alloys reduce weight and improve fuel economy. Carbon fiber composites offer superior performance for sports and premium vehicles but are costlier. Engineers often employ mixed-material strategies with tailored welding, riveting, and adhesive bonding techniques to balance performance, cost, and manufacturability.
- Crashworthiness is a vital metric for structure, involving controlled deformation through crumple zones and energy-absorbing members. Rigid safety cages surround the occupant compartment, designed to maintain structural integrity during severe collisions. The integration of side beams, roof reinforcements, and subframe geometries are meticulously engineered to meet global safety standards such as Euro NCAP or IIHS ratings.
- Innovations in structural engineering also embrace modular platforms, enabling manufacturers to produce multiple models using shared underpinnings. This approach reduces development time and cost while allowing scalability in design. Noise, vibration, and harshness (NVH) performance is also embedded into structural design, using damping materials and resonant tuning to enhance cabin comfort.
- Structural engineers now collaborate more closely with software and electronics teams to integrate features like battery enclosures in EVs or mounting structures for advanced driver-assistance systems (ADAS). Lightweighting efforts are further supported by topology optimization and generative design tools, which explore complex geometries previously unfeasible through traditional methods. A notable example is the use of [automotive-grade carbon composites](https://www.sciencedirect.com/topics/engineering/carbon-composites) for high-performance and energy-efficient cars.
- Aerodynamics:
- Aerodynamic design is essential in reducing drag, enhancing stability, and improving fuel efficiency or electric range. Engineers rely on computational fluid dynamics (CFD) to model airflow around the vehicle and identify areas of turbulence, lift, and pressure buildup. Wind tunnel testing is used to validate virtual results and fine-tune design modifications.
- Active aerodynamics represents a frontier in modern vehicle design, with deployable spoilers, adjustable ride heights, and grille shutters that dynamically optimize airflow based on driving conditions. These features balance performance with energy savings, particularly at highway speeds or during sporty driving modes.
- Examples include diffusers that manage underbody airflow, vortex generators that delay flow separation, and aerodynamic wheel covers that reduce turbulence. In electric vehicles, designers pay special attention to smoothing underbody panels, reducing front cross-sectional area, and incorporating rear-end tapering to enhance laminar flow.
- Drag coefficient (Cd) is a benchmark metric, and manufacturers strive to achieve values below 0.30 for fuel-efficient models. Luxury sedans and EVs like the Tesla Model S or Mercedes EQS push boundaries with Cd values as low as 0.20. Lower drag directly translates to improved acceleration, range, and reduced noise at high speeds.
- Aerodynamics also affects cooling efficiency, requiring delicate balancing between airflow for radiators and minimizing front-end resistance. Innovations such as air curtains and adaptive vents help achieve this goal. The use of aeroacoustic studies ensures reduced wind noise, enhancing user comfort and aligning with luxury expectations.
Propulsion Systems
- Internal Combustion Engines (ICE):
- Internal combustion engines (ICEs) have historically been the cornerstone of automotive propulsion. These engines operate by burning fuel—typically gasoline or diesel—within cylinders to produce mechanical energy. Despite growing environmental concerns, ICEs remain prevalent due to their high energy density and established refueling infrastructure.
- Ongoing advancements focus on improving thermal efficiency, reducing fuel consumption, and minimizing emissions. Technologies like variable valve timing, direct injection, and cylinder deactivation are now standard in modern ICEs. Turbocharging and downsizing help manufacturers meet strict regulatory standards without compromising performance.
- Emission control systems such as catalytic converters, diesel particulate filters (DPF), and selective catalytic reduction (SCR) have become integral in achieving Euro 6 and U.S. Tier 3 compliance. The development of synthetic fuels and biofuels also offers pathways to cleaner combustion with minimal retrofitting.
- Modern ICEs are also increasingly integrated with mild hybrid systems to support engine start-stop functionality and regenerative braking, contributing to better fuel economy and reduced idling emissions.
- Electric Vehicles (EVs):
- Electric vehicles (EVs) use electric motors powered by energy stored in rechargeable battery packs, offering a zero-emission alternative to traditional propulsion. Their rise has been driven by concerns over climate change, fossil fuel dependency, and urban air quality.
- EV propulsion systems are far simpler mechanically, with fewer moving parts and lower maintenance needs. Key performance characteristics include instant torque delivery, silent operation, and regenerative braking.
- Key components:
- Battery Pack:
- Most EVs today use lithium-ion battery technology, known for high energy density and reliability. Battery management systems (BMS) regulate temperature, voltage, and charging cycles to ensure safety and performance. Research is rapidly advancing toward solid-state batteries, which promise higher capacities, faster charging, and enhanced safety. Other alternatives under development include lithium-sulfur and sodium-ion chemistries.
- Electric Motor:
- Electric motors, typically permanent magnet synchronous or induction types, convert stored electrical energy into mechanical energy with exceptional efficiency. Their compact design allows for creative drivetrain layouts, including in-wheel motors and skateboard platforms.
- Inverters and Controllers:
- Inverters convert direct current (DC) from the battery into alternating current (AC) for the motor. Controllers govern motor output, throttle response, and torque delivery. These systems work together to manage regenerative braking, dynamic torque vectoring, and drive modes, ensuring optimal performance across varied conditions.
- Battery Pack:
- Challenges:
- Extending battery life, increasing range, and reducing degradation over time are ongoing challenges. Innovations in thermal management, advanced cathode materials, and solid electrolytes aim to address these issues.
- Developing a fast-charging infrastructure is equally crucial. While home charging suffices for daily commuting, public DC fast-charging networks are essential for longer journeys. The adoption of ultra-fast chargers (350 kW and beyond) is growing, enabling vehicles to recharge in under 30 minutes. Industry collaboration is advancing this rollout, supported by projects like IONITY, a pan-European high-power charging network for EVs.
- Hybrid Electric Vehicles (HEVs):
- Hybrid electric vehicles combine an ICE with one or more electric motors to enhance fuel efficiency and reduce emissions. They intelligently switch between or blend power sources based on driving conditions.
- HEVs recover braking energy via regenerative systems and use it to supplement propulsion. The presence of a small battery helps with acceleration, reduces engine workload, and supports stop-start functionality.
- Types:
- Mild Hybrids: These use a small electric motor to assist the ICE during acceleration and coasting, but cannot power the vehicle independently. They offer moderate efficiency improvements at a low cost.
- Full Hybrids: Full hybrid systems can operate using electric-only mode for short distances, especially at low speeds. They use a more powerful battery and complex energy management system, as seen in vehicles like the Toyota Prius.
- Plug-In Hybrid Electric Vehicles (PHEVs):
- PHEVs feature larger battery packs than traditional hybrids, allowing them to travel significant distances—often 30 to 60 kilometers—purely on electric power. After depleting the battery, the ICE engages to extend range, eliminating range anxiety while reducing emissions.
- These vehicles can be recharged via external power sources such as wall sockets or public charging stations. Government incentives, tax rebates, and urban access exemptions have encouraged PHEV adoption in many markets. However, optimal environmental benefit depends on regular charging and responsible usage.
- Fuel Cell Electric Vehicles (FCEVs):
- FCEVs generate electricity onboard using hydrogen gas and a fuel cell stack. The electrochemical reaction combines hydrogen with oxygen from the air to produce electricity, with water vapor as the only emission.
- Fuel cell systems offer rapid refueling and long driving ranges, making them ideal for commercial vehicles and long-distance travel. Vehicles like the Toyota Mirai and Hyundai Nexo exemplify this technology.
- Challenges include hydrogen production, storage, and refueling infrastructure. Currently, most hydrogen is derived from fossil fuels, though green hydrogen from electrolysis using renewable energy is being developed to make FCEVs truly sustainable.
- Fuel cell technology also finds application in buses, trucks, and industrial transport, supported by global efforts to decarbonize heavy-duty transportation and logistics sectors.
Autonomous Vehicles (AVs)
- Autonomous vehicles (AVs), also known as self-driving cars, represent a paradigm shift in mobility. They leverage a suite of cutting-edge sensors, control systems, artificial intelligence (AI), and real-time data processing to navigate roads and execute driving tasks with minimal or no human intervention. The ultimate vision is to create safer, more efficient, and accessible transportation networks by reducing human error, which accounts for the majority of traffic accidents.
- Levels of Autonomy:
- Autonomy is classified by the Society of Automotive Engineers (SAE) into six levels, from Level 0 to Level 5:
- Level 0: No automation – the driver has full control, with only warning systems like lane departure alerts.
- Level 1: Driver assistance – includes features such as adaptive cruise control or lane-keeping assist, where either steering or acceleration/deceleration is automated, but not both simultaneously.
- Level 2: Partial automation – systems like Tesla Autopilot can control both steering and acceleration, but the driver must remain engaged and monitor the environment at all times.
- Level 3: Conditional automation – the vehicle handles all driving tasks under certain conditions, but the driver must be ready to take over when requested. This is a transitional phase requiring complex handoff protocols.
- Level 4: High automation – vehicles operate independently in geofenced or predefined environments without human input. They can handle all situations in those zones and do not need human fallback in normal conditions.
- Level 5: Full automation – the car is entirely autonomous and capable of handling all driving scenarios without any human intervention or presence.
- Autonomy is classified by the Society of Automotive Engineers (SAE) into six levels, from Level 0 to Level 5:
- Key Technologies:
- LiDAR and Radar:
- LiDAR (Light Detection and Ranging) uses laser pulses to create high-resolution 3D maps of the surroundings, accurately detecting distances and object shapes. Radar systems complement this by functioning reliably in adverse weather and low visibility, identifying the speed and position of objects even through fog, rain, or darkness.
- Cameras:
- Mounted across the vehicle’s body, cameras capture real-time imagery for detecting road signs, traffic lights, pedestrians, and lane boundaries. Advanced computer vision algorithms analyze these feeds to support tasks such as lane centering and obstacle avoidance.
- GPS and HD Maps:
- High-definition (HD) maps are layered with centimeter-level details like lane boundaries, curb geometry, and traffic signals. Combined with GPS data and inertial measurement units (IMUs), they allow AVs to localize themselves with exceptional accuracy, even in dense urban areas.
- AI and Machine Learning:
- AI is the brain of autonomous systems, enabling vehicles to interpret sensor data, predict traffic behavior, and make context-aware decisions in real time. Deep learning algorithms are trained on vast datasets of driving scenarios to recognize patterns and adapt to dynamic environments. Companies like [Waymo are pioneering these technologies, demonstrating real-world deployments of fully autonomous vehicles.
- LiDAR and Radar:
- Applications:
- AVs are increasingly used in commercial and experimental contexts. Robotaxis offer ride-hailing services without human drivers, promising reduced costs and increased availability. Autonomous delivery vehicles are transforming last-mile logistics by reducing operational expenses and carbon emissions. In freight transportation, platooning technology enables a lead truck to guide multiple automated vehicles in close formation, improving fuel efficiency and reducing road congestion.
Safety Systems
- Passive Safety:
- Passive safety systems are designed to minimize injury during a crash. These features become active only during or immediately before an accident. Examples include seatbelts with pre-tensioners, airbags that deploy based on impact sensors, crumple zones that absorb kinetic energy, and high-strength reinforced cabins that maintain structural integrity during rollovers or collisions.
- Advances in materials science have enabled the use of multi-phase steels and composite reinforcements to strengthen critical zones while maintaining vehicle weight targets. Passive safety designs also undergo rigorous crash testing under global protocols such as Euro NCAP and IIHS ratings to ensure occupant protection.
- Active Safety:
- Active safety refers to systems that assist the driver in avoiding accidents altogether. These technologies use a combination of sensors, actuators, and software to monitor road conditions, detect hazards, and take preventive action when needed.
- Examples include:
- Anti-lock Braking Systems (ABS): Prevent wheel lockup during emergency braking, helping maintain steering control.
- Electronic Stability Control (ESC): Helps prevent skidding and loss of control by applying brakes to individual wheels based on yaw and steering angle inputs.
- Advanced Driver Assistance Systems (ADAS):
- ADAS encompasses a broad range of features such as lane-keeping assist, which gently steers the car back to its lane; automatic emergency braking (AEB), which applies brakes to avoid a collision; blind-spot monitoring; and adaptive cruise control, which adjusts speed based on traffic flow.
- These systems not only reduce accident risks but also reduce driver fatigue during long journeys, promoting overall safety and convenience.
- Vehicle-to-Everything (V2X) Communication:
- V2X technologies enable vehicles to communicate with other vehicles (V2V), infrastructure (V2I), pedestrians (V2P), and networks (V2N). This connectivity enhances situational awareness, enabling cars to anticipate hazards beyond the driver’s line of sight. For instance, a car could receive alerts about an upcoming road hazard, traffic congestion, or emergency vehicle approach in real time.
- V2X plays a crucial role in future smart city ecosystems and autonomous vehicle coordination. It supports intelligent traffic signaling, dynamic routing, and intersection management systems that reduce congestion and emissions while improving safety. As 5G connectivity expands, V2X capabilities are expected to grow, enabling faster and more reliable data exchanges critical for next-generation mobility.
Emerging Trends in Automotive Engineering
Electric Vehicles (EVs)
- Battery Technology Advancements:
- Battery innovation is at the forefront of the electric vehicle revolution. Traditional lithium-ion batteries are continuously being refined for greater capacity, longevity, and affordability. Researchers are exploring new chemistries and architectures, such as lithium-silicon anodes and cobalt-free cathodes, to reduce costs and environmental impact.
- Solid-state batteries represent a major leap forward. By replacing the liquid electrolyte with a solid one, these batteries can achieve significantly higher energy densities, improved thermal stability, and reduced fire risk. Automakers and startups alike are racing to bring solid-state EVs to market within the next decade.
- Recycling and second-life use are also becoming crucial. End-of-life EV batteries can be repurposed for grid storage or home backup power. Recycling technologies are evolving to extract valuable materials like lithium, nickel, and cobalt efficiently. Companies such as Redwood Materials are leading efforts to build a circular battery economy, which is essential for scaling EVs sustainably.
- Charging Infrastructure:
- Charging speed and accessibility are critical to EV adoption. Ultra-fast chargers, offering up to 350 kW, can replenish a vehicle’s battery in under 15–20 minutes. These chargers are being deployed across highways, shopping centers, and city hubs to support long-distance travel and reduce range anxiety.
- Innovations such as wireless charging pads embedded in roads and stationary parking spots are being trialed in several countries. These systems aim to deliver energy without physical connectors, enhancing user convenience and enabling dynamic in-motion charging for public transport and logistics fleets.
- Vehicle-to-grid (V2G) integration allows EVs to send power back to the grid during peak demand, turning parked cars into distributed energy resources. This bidirectional charging enhances grid resilience and creates value for EV owners. According to [BloombergNEF](https://about.bnef.com/blog/electric-vehicles-boom-quietly-charges-the-global-battery-supply-chain/), these technologies are reshaping global energy systems and making mobility more sustainable.
- Global Adoption:
- EV adoption is accelerating globally, driven by supportive government policies, tax incentives, and regulatory targets. Many countries have committed to phasing out internal combustion engine vehicles between 2030 and 2040. Norway leads in adoption, with over 80% of new cars sold being electric.
- Major automakers like General Motors, Ford, Volkswagen, and Toyota have committed to electrifying significant portions of their fleets. Some are transitioning to EV-only lineups in select markets. Startups and new entrants such as Rivian, Lucid Motors, and NIO are also challenging traditional players with innovative designs and direct-to-consumer sales models.
- Affordability remains a key barrier. However, declining battery costs, increased production scale, and local manufacturing are expected to make EVs cost-competitive with ICE vehicles within this decade.
Autonomous Driving
- Fleet Integration:
- Autonomous driving is being introduced at scale through shared mobility services. Companies like Waymo, Cruise, and Baidu are deploying robotaxis in urban environments, offering passengers fully autonomous rides in geofenced areas. In logistics, autonomous delivery vans and long-haul trucking solutions are being tested to streamline freight operations.
- These fleets benefit from centralized control systems, predictive maintenance, and route optimization, which enhance reliability and economic viability.
- Edge Computing:
- Edge computing plays a crucial role in autonomous systems by enabling data processing directly on the vehicle. This reduces latency and ensures rapid response to real-time events such as pedestrian crossings or sudden braking by nearby vehicles.
- Vehicle control units (VCUs) now contain AI accelerators and high-performance GPUs to process sensor data locally. This decentralized architecture minimizes dependence on cloud infrastructure and improves safety in scenarios with limited connectivity.
- Regulatory Challenges:
- The legal landscape for autonomous driving is still evolving. Governments must develop safety benchmarks, liability frameworks, and data privacy regulations to govern AV deployment. Cross-border cooperation is necessary to standardize testing protocols and certification procedures.
- Public trust is also a hurdle. Transparency in AI decision-making, accountability for accidents, and clear human-machine interface (HMI) design are critical for gaining user confidence.
Sustainability and Eco-Friendly Solutions
- Lightweight Materials:
- Reducing vehicle weight directly enhances fuel efficiency and EV range. Engineers are incorporating lightweight materials such as aluminum-magnesium alloys, high-strength steels, and carbon fiber composites into body structures and components.
- These materials also contribute to safety by maintaining crash resistance while lowering mass. Advanced joining techniques, including friction stir welding and structural adhesives, are used to combine dissimilar materials effectively.
- Alternative Fuels:
- Alternative fuels offer pathways to decarbonize transportation. Biofuels made from algae, waste oils, and agricultural residues can power modified ICEs with reduced lifecycle emissions. Synthetic fuels created from captured carbon dioxide and renewable electricity are also being explored.
- Hydrogen is gaining momentum as a clean fuel, particularly for commercial and heavy-duty applications. Fuel cell electric vehicles (FCEVs) produce zero tailpipe emissions and can refuel quickly, making them ideal for long-range operations.
- Circular Economy in Manufacturing:
- Automakers are shifting toward circular manufacturing by designing vehicles for disassembly and material recovery. Modular components and standardized parts make recycling more efficient and cost-effective.
- Factories are also adopting closed-loop systems, reusing water, energy, and materials. Digital twins and lifecycle assessment tools help monitor environmental performance throughout the production chain.
Connected Vehicles
- Internet of Things (IoT):
- IoT integration transforms vehicles into intelligent nodes within a connected network. Sensors collect data on tire pressure, engine diagnostics, driver behavior, and environmental conditions. This data is transmitted in real time for monitoring, predictive maintenance, and usage-based insurance.
- IoT connectivity also enables remote start, geofencing, smart key systems, and user preference synchronization across shared vehicles.
- Cloud Integration:
- Cloud platforms aggregate data from millions of vehicles to improve software, detect anomalies, and refine AI models. Over-the-air (OTA) updates deliver new features, security patches, and performance optimizations without physical service visits.
- This enhances user convenience while reducing manufacturer costs and accelerating innovation cycles. Cloud computing also supports fleet analytics, enabling ride-sharing and delivery companies to manage assets more efficiently.
- 5G Connectivity:
- Fifth-generation (5G) mobile networks are critical to enabling real-time communication between vehicles, infrastructure, and cloud systems. With ultra-low latency and high bandwidth, 5G supports applications such as cooperative driving, remote vehicle control, immersive infotainment, and augmented navigation.
- Connected vehicles using 5G can anticipate hazards, adjust to traffic flow, and interact seamlessly with smart city infrastructure for safer and more efficient journeys.
Performance Optimization
- Aerodynamics:
- Automotive engineers are increasingly using active aerodynamic systems that respond to speed and road conditions. Movable spoilers, adjustable air dams, and grille shutters are deployed to balance drag reduction and cooling requirements.
- These dynamic systems help vehicles maintain optimal fuel efficiency or electric range while enhancing handling at high speeds.
- Advanced Drivetrains:
- Performance vehicles benefit from advanced drivetrains with torque vectoring systems that actively distribute power between wheels for improved grip, cornering stability, and agility.
- Dual-motor or tri-motor electric drivetrains allow independent control of each axle or wheel group, enabling unparalleled responsiveness and control under various traction conditions.
- Thermal Management Systems:
- Effective thermal management is essential for optimizing the performance and longevity of engines, batteries, and power electronics. Engineers use liquid cooling, heat exchangers, and phase-change materials to dissipate heat efficiently.
- Smart thermal control algorithms adapt to real-time conditions, balancing energy use and maintaining ideal temperature ranges to avoid degradation and performance losses.
Applications of Automotive Engineering
Passenger Vehicles
- Passenger vehicles form the core of automotive engineering applications, encompassing a wide range of body styles such as sedans, hatchbacks, SUVs, and crossovers. Engineers in this domain prioritize occupant comfort, ride quality, energy efficiency, and aesthetics to appeal to individual consumers and families.
- Safety is a key design driver, prompting the integration of advanced passive and active safety systems including reinforced chassis structures, airbag deployment algorithms, adaptive cruise control, and lane-keeping systems. These features are tailored to meet global crash safety regulations such as Euro NCAP, NHTSA, and GNCAP.
- Comfort and ergonomics are addressed through interior layout design, climate control systems, acoustic insulation, and seating posture analysis. Infotainment systems now play a crucial role in user satisfaction, with touch interfaces, voice control, and smartphone connectivity enhancing the driving experience.
- Powertrain options range from internal combustion engines to hybrid and all-electric drivetrains, with platform flexibility allowing manufacturers to cater to various markets and regulatory environments. Engineers focus on optimizing emissions, improving fuel economy, and integrating regenerative braking systems in electrified models.
- New trends in passenger vehicle design include digital cockpits, over-the-air updates, personalized driving modes, and integration with smart home ecosystems. As urban mobility evolves, compact and modular electric vehicles are gaining popularity in densely populated cities.
Commercial Vehicles
- Commercial vehicles—such as cargo trucks, semi-trailers, vans, and buses—are designed for reliability, payload efficiency, and low total cost of ownership. These vehicles operate in rigorous environments and often accumulate high mileage, requiring robust engineering for chassis strength, powertrain durability, and serviceability.
- Engineers optimize aerodynamics, axle configurations, and power distribution systems to support high load capacities while reducing fuel consumption. Increasingly, manufacturers are transitioning commercial fleets to electric and hybrid powertrains to meet emissions targets and lower operating costs.
- Key considerations include power-to-weight ratio, brake wear resistance, thermal load management, and compliance with weight and emission regulations across various jurisdictions. Technologies like automated manual transmissions (AMTs), tire pressure monitoring, and remote diagnostics enhance performance and uptime.
- In logistics, telematics systems enable fleet operators to monitor vehicle location, driving behavior, maintenance needs, and fuel usage in real time. Innovations such as platooning and autonomous freight corridors are being developed to improve efficiency and reduce human error.
- Manufacturers collaborate with bodybuilders to customize vehicle configurations for diverse applications such as refrigeration, waste management, fire services, and mining. According to the [International Council on Clean Transportation](https://theicct.org/), electrification of commercial fleets has the potential to cut urban emissions dramatically, especially when paired with renewable energy sources.
High-Performance Vehicles
- High-performance vehicles, including sports cars and supercars, represent the pinnacle of automotive engineering. These vehicles are engineered to deliver exceptional speed, handling, and acceleration while offering a distinct sensory experience.
- Advanced aerodynamics plays a key role in ensuring high-speed stability and downforce. Active elements such as deployable spoilers, adaptive diffusers, and air intakes adjust based on speed and cornering forces to optimize grip and minimize drag.
- Lightweight construction using carbon fiber monocoques, titanium components, and aerospace-grade alloys improves the power-to-weight ratio. Every gram saved translates into performance gains and fuel economy benefits.
- Powertrains range from turbocharged and naturally aspirated V8/V12 engines to dual-motor electric systems with torque vectoring. Engineers employ advanced cooling systems and transmission tuning for track-level endurance.
- These vehicles often serve as testbeds for emerging technologies, such as brake-by-wire, predictive suspension, and digital twin simulations. Beyond their performance metrics, they embody craftsmanship, brand identity, and engineering excellence.
Off-Road Vehicles
- Off-road vehicles are engineered for extreme terrain conditions, including deserts, mountains, forests, and agricultural landscapes. These include all-terrain vehicles (ATVs), SUVs with off-road packages, military utility vehicles, and specialty agricultural machines.
- Design considerations include increased ground clearance, reinforced suspension arms, underbody protection, and high-approach/departure angles. Multi-link suspension systems and long-travel shock absorbers enable comfort and control on uneven ground.
- Drivetrain components such as locking differentials, low-range transfer cases, and advanced traction control allow effective torque distribution on slippery or uneven surfaces. Engineers also design tire and wheel systems to prevent punctures and increase surface contact.
- Water fording, rock crawling, and sand dune traversal capabilities are validated through rigorous simulations and field testing. Modular design supports add-ons like winches, snorkels, skid plates, and rooftop tents for adventure travel and overlanding.
- Modern off-road vehicles integrate digital trail navigation, inclinometer displays, hill descent control, and off-road cruise control to aid novice drivers and expand user confidence in remote terrains.
Public Transportation
- Automotive engineering plays a central role in designing safe, efficient, and environmentally friendly public transport vehicles. This includes city buses, intercity coaches, trams, and shuttle vans, many of which are shifting to electric and hybrid propulsion systems.
- Engineers focus on optimizing passenger capacity, minimizing vibration and noise, and ensuring low-floor accessibility for elderly and disabled passengers. Safety enhancements include collision warning systems, pedestrian detection, and secure driver cabins.
- Electric buses offer low-noise, emission-free urban mobility, with regenerative braking and energy-efficient HVAC systems. Battery thermal management and fast-charging infrastructure are essential for reliability and turnaround times.
- Connectivity features such as GPS tracking, digital displays, Wi-Fi, and automated fare collection improve service quality and passenger experience. In advanced markets, autonomous shuttle buses are being piloted to serve short-distance routes in urban and campus settings.
- Government policies and smart city initiatives are driving the adoption of sustainable transport fleets, supported by public-private partnerships and international funding mechanisms. These advancements reflect a commitment to inclusive, low-carbon urban mobility.
Challenges in Automotive Engineering
Battery Efficiency and Range:
- Electric vehicles (EVs) face persistent challenges related to battery efficiency and driving range. Consumers demand long-range capabilities comparable to internal combustion engine vehicles, but increasing energy storage often comes at the cost of higher weight, price, and space constraints.
- Automotive engineers strive to improve the energy density of battery cells while ensuring safety, thermal stability, and longevity. Innovations in solid-state batteries, lithium-silicon anodes, and new electrolyte chemistries are being pursued aggressively to overcome current limitations.
- At the system level, thermal management and lightweight chassis design are critical to reducing auxiliary loads and maximizing efficiency. Aerodynamics and rolling resistance also significantly influence the real-world range of EVs.
- Cost remains a substantial hurdle. Battery packs still account for a significant portion of the total EV cost. Engineers work to streamline manufacturing processes, reduce rare earth dependencies, and optimize supply chains to make EVs more affordable across all market segments.
- Additionally, the range must be preserved over time, which means managing battery degradation due to repeated fast-charging cycles, extreme temperatures, and high-discharge driving behaviors. Battery management systems (BMS) must evolve to predict and mitigate these effects accurately.
Autonomous Driving Safety:
- Ensuring the safety of autonomous vehicles (AVs) is one of the most complex and urgent challenges in automotive engineering. Unlike human drivers, AVs must make consistent, fail-safe decisions in a wide variety of unpredictable scenarios including jaywalking pedestrians, emergency vehicles, temporary construction zones, and erratic drivers.
- Perception systems must reliably interpret sensor data in real time, even under poor lighting, fog, heavy rain, or snow. AVs need redundancy across LiDAR, radar, and vision systems to reduce reliance on any single modality. Sensor fusion algorithms must integrate these data streams to maintain situational awareness.
- Advanced neural networks are trained on billions of miles of driving data, but edge cases—uncommon yet dangerous scenarios—still pose a risk. Engineers conduct simulations and closed-course testing to identify and mitigate system vulnerabilities. For example, unpredictable human behavior or rare object types may confuse classifiers.
- Ethical dilemmas around risk distribution, liability in the event of a crash, and decision-making under constrained conditions require interdisciplinary solutions involving law, philosophy, and public policy. Regulatory approval and consumer acceptance hinge on clear demonstrations of safety superiority over human driving.
- Organizations like NHTSA and Euro NCAP are developing frameworks for safety validation, but globally harmonized standards are still evolving. Real-world deployment requires constant software updates and cybersecurity protections to keep AVs safe from malicious interference.
Emissions Regulations:
- Emissions compliance is increasingly difficult as global regulations tighten. Automakers must meet rigorous targets for carbon dioxide (CO₂), nitrogen oxides (NOₓ), and particulate matter (PM), particularly in Europe, China, and North America.
- This challenge impacts ICE vehicles through the adoption of after-treatment systems such as diesel particulate filters, selective catalytic reduction, and advanced exhaust gas recirculation. Engineers also fine-tune combustion parameters and engine control software for improved efficiency.
- Hybridization is used to supplement ICE performance and reduce emissions in urban traffic. For EVs, the challenge shifts upstream to the energy mix used for electricity generation and the carbon footprint of battery manufacturing.
- Compliance also requires lifecycle analysis (LCA) tools to assess the total environmental impact of vehicles from cradle to grave. As sustainability metrics become more important to consumers and regulators, engineers must align product design with these expectations.
- Failure to meet these regulations leads to costly penalties, sales restrictions, or loss of market access, pushing companies to invest in cleaner powertrains, renewable fuel compatibility, and digital emissions monitoring systems.
Supply Chain Disruptions:
- The COVID-19 pandemic and geopolitical tensions have exposed deep vulnerabilities in global automotive supply chains. Semiconductors, in particular, have become a critical bottleneck, affecting production volumes across all vehicle segments.
- Engineers must design flexible electronics architectures that can accommodate alternate components or firmware updates. Supply diversification strategies and just-in-case inventory models are replacing just-in-time practices in many firms.
- Raw material availability—such as lithium, cobalt, and rare earth elements—used in batteries and motors is also constrained. Local sourcing, recycling, and material substitution are key engineering priorities.
- Increased complexity in vehicles, with more electronic content and connected features, amplifies the risk of multi-tiered component shortages. Engineers are now tasked with supply chain resilience modeling as part of early-stage product development.
- Digitization of logistics, predictive analytics, and supplier monitoring tools are becoming essential to foresee and mitigate disruptions. Cross-functional coordination between engineering, procurement, and manufacturing is now more critical than ever.
Cybersecurity:
- As vehicles become more connected and software-driven, they are increasingly vulnerable to cyber threats. Attackers could exploit vehicle control systems, telematics, infotainment, or over-the-air update channels to gain unauthorized access or cause harm.
- Cybersecurity in automotive engineering involves building secure electronic control units (ECUs), encrypting communication protocols, and implementing intrusion detection systems that monitor for abnormal behavior.
- With autonomous and connected vehicles relying on vehicle-to-everything (V2X) communication, the attack surface expands to include external devices and networks. Engineers must ensure data integrity and prevent spoofing or man-in-the-middle attacks.
- Standards such as ISO/SAE 21434 and UNECE WP.29 provide guidelines for secure system development and incident response readiness. Manufacturers must demonstrate compliance through rigorous risk assessments and threat modeling.
- Cybersecurity is a moving target. Engineers must design vehicles that can adapt through secure updates and support long-term monitoring. Collaboration with ethical hackers, security firms, and regulatory bodies ensures a proactive approach to protecting digital infrastructure in modern vehicles.
Future Directions in Automotive Engineering
Shared Mobility:
- Shared mobility is reshaping how individuals access transportation. Rather than owning a personal vehicle, users increasingly rely on ride-hailing, car-sharing, and micro-mobility services such as electric scooters and bikes for short trips.
- The integration of autonomous vehicles (AVs) into shared mobility platforms will further revolutionize this model. AVs enable fleets of self-driving taxis that can operate continuously, reduce operational costs, and enhance accessibility for those who are elderly or disabled.
- Engineers are developing modular vehicles with interchangeable interiors for passengers, cargo, or hybrid use-cases. These vehicles prioritize ease of cleaning, digital onboarding, and remote diagnostics for high utilization rates.
- Software algorithms play a central role in fleet optimization, dynamically assigning vehicles based on demand, energy levels, and proximity. AI-based predictive analytics improve scheduling and minimize wait times while optimizing fleet size.
- Shared autonomous mobility also presents unique challenges such as liability determination, vehicle cleanliness standards, cybersecurity, and user data privacy—all of which require interdisciplinary solutions involving engineers, policy makers, and service providers.
Flying Cars:
- Flying cars, or personal air vehicles (PAVs), represent a radical rethinking of urban transportation. With growing urban congestion and limited road expansion, vertical mobility offers an alternative that bypasses traditional infrastructure constraints.
- Engineers are designing electric vertical take-off and landing (eVTOL) aircraft that combine the principles of aeronautics with automotive design. These vehicles aim for quiet, compact, and safe operation in urban environments, often with electric or hybrid propulsion systems and distributed rotors for stability.
- Key design considerations include aerodynamic efficiency, lightweight materials, power-to-weight ratios, and noise mitigation. Battery performance, redundancy in flight control systems, and collision avoidance technologies are essential for safe operation in dense airspace.
- Companies like Joby Aviation, Volocopter, and Archer Aviation are developing air taxis for commercial use, with regulatory certification under way. According to NASA, urban air mobility (UAM) is expected to become viable within the next decade, supported by smart air traffic management systems and digital sky corridors.
- Challenges remain in public acceptance, infrastructure development, noise pollution, and integration with existing transportation networks. Engineers must work with aviation authorities to meet certification requirements while ensuring scalability and economic viability.
Quantum Computing:
- Quantum computing holds transformative potential for automotive engineering by enabling computations that are exponentially faster than classical computers. This power can be leveraged to optimize complex systems such as traffic flows, supply chains, and aerodynamic simulations.
- In vehicle design, quantum algorithms can significantly reduce the time required to analyze millions of potential material combinations, structural geometries, and crash scenarios. This accelerates development cycles and supports the discovery of novel materials and configurations.
- In logistics, quantum computing helps solve combinatorial optimization problems, such as vehicle routing and fleet scheduling, with unprecedented efficiency. This results in lower fuel consumption, reduced emissions, and enhanced delivery performance.
- Automakers are collaborating with quantum computing firms and research institutions to explore use cases and develop quantum-ready algorithms. Early-stage applications include battery material modeling, autonomous driving simulations, and predictive maintenance planning at the fleet level.
- Though practical implementation is still emerging, engineers are already preparing for a hybrid computing environment where classical and quantum systems coexist to tackle the most demanding engineering challenges.
Hyperloop Systems:
- Hyperloop technology aims to revolutionize ground-based transportation by enabling high-speed travel inside low-pressure tubes. Vehicles or pods within these systems float using magnetic levitation and face minimal air resistance, allowing them to reach speeds over 1000 km/h.
- Automotive engineering principles—particularly in propulsion, aerodynamics, and vehicle stability—are being applied to the development of these pods. Engineers must design safe, lightweight, pressurized cabins capable of withstanding high-speed transit and emergency deceleration.
- Suspension systems must be capable of absorbing vibration in a vacuum environment while ensuring ride comfort. Magnetic propulsion systems and regenerative braking methods are also being optimized for energy efficiency and safety.
- Hyperloop projects, such as those led by Virgin Hyperloop and TransPod, are being tested with the goal of reducing intercity travel times and congestion. These systems promise environmentally friendly alternatives to short-haul flights and high-speed rail.
- Engineers must address challenges in system scalability, thermal management, passenger evacuation protocols, and economic viability. Cross-disciplinary collaboration is key to making hyperloop a feasible and sustainable solution for future transportation needs.
Next-Gen Infotainment:
- Future automotive infotainment systems are evolving beyond traditional dashboards and screens into fully immersive, intelligent interfaces. Augmented reality (AR) head-up displays (HUDs) project information such as navigation, hazard alerts, and speed directly into the driver’s line of sight, reducing distraction and improving situational awareness.
- Immersive audio environments, gesture-based controls, voice-activated assistants, and haptic feedback are being integrated to enhance user interaction. These systems are tailored to personal preferences and offer adaptive content delivery based on user profiles, location, and driving context.
- Next-gen infotainment integrates deeply with vehicle-to-everything (V2X) and cloud platforms. Real-time content updates, dynamic route suggestions, and traffic-based entertainment choices are made possible through edge computing and 5G connectivity.
- Rear-seat entertainment is also undergoing transformation, with AR/VR headsets, streaming services, and interactive gaming platforms becoming available in premium and autonomous vehicle segments. These systems turn vehicles into mobile entertainment hubs, particularly for long trips or shared rides.
- Privacy and cybersecurity remain important, as infotainment systems handle sensitive user data. Engineers must implement encrypted data flows, multi-user access controls, and secure API integrations to maintain trust and system integrity in this highly personalized domain.
Why Study Automotive Engineering
Designing the Future of Mobility
Automotive engineering focuses on the design, development, and manufacturing of vehicles. Students learn how engines, transmissions, and electronic systems work together. This knowledge supports innovation in both conventional and electric vehicles.
Vehicle Dynamics and Powertrain Systems
Students study how vehicles accelerate, brake, steer, and handle various terrains. They explore combustion engines, hybrid powertrains, and battery technologies. This helps them build safer and more efficient vehicles.
Safety, Emissions, and Sustainability
The course emphasizes designing vehicles that meet safety standards and environmental regulations. Students explore crashworthiness, emissions control, and alternative fuels. These topics align with global trends in clean transportation.
Computer-Aided Engineering and Prototyping
Students use tools like CAD, CAM, and simulation software to design and test vehicle components. They develop and evaluate prototypes using real-world data. This prepares them for careers in R&D and product development.
Electrification and Smart Vehicle Technologies
Automotive engineering is evolving with autonomous systems, electric drivetrains, and connected cars. Students explore innovations like driver-assist features, battery management, and vehicle-to-grid systems. This makes the field exciting and future-focused.
Automotive Engineering: Conclusion
Automotive engineering stands as a cornerstone of modern technological advancement, serving not only as a driver of economic development but also as a catalyst for innovation across numerous industries. It integrates disciplines such as mechanical design, materials science, electrical engineering, artificial intelligence, and environmental sustainability into a cohesive and dynamic field. As vehicles evolve from purely mechanical machines to smart, connected, and autonomous systems, automotive engineers must adapt their methodologies and expand their technical fluency to accommodate this transformation.
The shift toward electric mobility represents a profound redefinition of vehicle architecture, requiring engineers to rethink propulsion, energy storage, thermal management, and system integration. Electric drivetrains, battery technologies, and charging infrastructure must achieve breakthroughs in cost-efficiency, energy density, and durability. This transition also calls for significant redesigns of production processes and supply chains to accommodate new materials and components while reducing the industry’s carbon footprint.
Simultaneously, the rise of autonomous vehicles introduces new frontiers in safety, ethics, regulation, and machine intelligence. Engineers must develop reliable sensor fusion frameworks, robust fail-safe architectures, and adaptive AI algorithms that can interpret complex traffic environments. Ensuring these systems can operate safely in unpredictable, real-world conditions is essential to gaining public trust and regulatory approval.
Connectivity is another transformative force. Through vehicle-to-everything (V2X) communication, cloud integration, and 5G-enabled real-time data exchange, modern vehicles are becoming intelligent nodes in the broader digital ecosystem. Engineers are increasingly tasked with embedding cybersecurity protocols, over-the-air (OTA) update capabilities, and user-centric infotainment features that enhance both functionality and user experience.
Moreover, sustainability extends beyond emissions reductions. Engineers are now tasked with designing vehicles that align with circular economy principles—vehicles that are easier to dismantle, reuse, and recycle. Life-cycle assessments (LCAs) guide design choices, and regulatory pressures demand transparency in sourcing, production, and end-of-life strategies. Initiatives such as the Global Battery Alliance aim to ensure ethical and environmentally responsible practices in battery value chains, adding another layer of accountability to the engineering process.
The future of automotive engineering is not a single path but a convergence of parallel advances: electrification, automation, digitization, and sustainability. Each trend reshapes the skillsets, tools, and thinking needed in the profession. Engineers must now operate in a multidisciplinary, collaborative environment that values systems thinking, rapid prototyping, and continuous learning.
Ultimately, automotive engineering will continue to shape how humanity moves, interacts, and innovates. From urban micro-mobility solutions to intercontinental freight automation, the influence of this field extends well beyond vehicles. It defines the contours of smart cities, clean energy strategies, and even climate change mitigation efforts. As we navigate the road ahead, automotive engineers will remain pivotal architects of a more connected, efficient, and sustainable world.
Automotive Engineering: Review Questions with Detailed Answers
Question:
What distinguishes automotive engineering from general mechanical engineering, and why is this specialization increasingly important today?Answer:
Automotive engineering focuses on designing, developing, and refining vehicles and their subsystems, including engines, transmissions, and safety systems. While it shares core mechanical principles with broader mechanical engineering, automotive engineering applies them specifically to meet regulations, optimize fuel efficiency, and incorporate emerging technologies (like electrification and autonomous driving). Its growing importance stems from rapidly evolving consumer demands, tighter environmental standards, and technological advancements that push the boundaries of vehicle performance and sustainability.Question:
How have modern powertrain technologies evolved to address environmental concerns, and what role do electric and hybrid powertrains play?Answer:
Traditional internal combustion engines (ICEs) have improved significantly through better fuel injection systems, turbocharging, and downsizing to reduce emissions and enhance efficiency. However, electric and hybrid powertrains represent a major shift in the industry. Hybrids combine ICEs with electric motors, reducing fuel consumption and emissions in city driving. Fully electric vehicles eliminate tailpipe emissions entirely and rely on battery technology. Advances in battery capacity, charging infrastructure, and energy management systems have made EVs increasingly viable, helping automotive engineers address climate change and regulatory pressures.Question:
In what ways do modern vehicles rely on electronic control systems, and how do these systems impact vehicle performance and safety?Answer:
Electronic control systems manage everything from engine timing and fuel injection to traction control and stability management. Sensors monitor vehicle speed, engine parameters, and wheel slip, allowing controllers to optimize power delivery and maintain driver control in various conditions. Additionally, advanced driver-assist systems (ADAS) use radar, lidar, and cameras to detect potential hazards, support lane-keeping, and enable adaptive cruise control. These electronic systems not only improve performance and fuel efficiency but also significantly enhance occupant and pedestrian safety.Question:
Why is chassis engineering pivotal in automotive design, and what factors must engineers consider to ensure optimal vehicle dynamics?Answer:
The chassis is the structural backbone of a vehicle, supporting all components and bearing loads during acceleration, braking, and cornering. Engineers focus on stiffness, weight distribution, and material selection to balance safety, ride comfort, and handling. Suspension geometry, spring and damper rates, and steering system design collectively determine how the car responds to driver inputs and road conditions. By carefully tuning these elements, engineers can achieve desired performance—such as sporty handling, luxury comfort, or off-road capability—without compromising safety or durability.Question:
How do automotive engineers approach the trade-offs between weight reduction and vehicle safety, especially in the context of performance and efficiency?Answer:
Reducing weight improves efficiency and agility but must not compromise structural integrity. Automotive engineers employ advanced materials like high-strength steel, aluminum alloys, and carbon-fiber composites to maintain crashworthiness while shedding unnecessary mass. Computer simulations and crash testing validate designs, ensuring that safety crumple zones, occupant protection, and overall chassis rigidity meet or exceed regulatory standards. The challenge is optimizing these factors simultaneously to deliver a vehicle that’s lightweight, safe, and fuel-efficient.Question:
What are some emerging trends in automotive design that focus on user experience, and how do these innovations influence vehicle development?Answer:
Modern vehicles increasingly integrate infotainment systems, connectivity features, and user-friendly interfaces. Touchscreen dashboards, voice recognition, and heads-up displays aim to minimize driver distraction while providing real-time information. Over-the-air software updates keep vehicles current and enable new functionalities (e.g., enhanced driver-assist features). Interior designs are also evolving to offer comfort and personalization, such as customizable lighting and adaptive seat ergonomics. These innovations require collaboration between mechanical, electrical, and software engineers to ensure seamless integration and a positive user experience.Question:
Why is aerodynamics a critical aspect of automotive engineering, and what methods are used to refine a vehicle’s aerodynamic profile?Answer:
Aerodynamics directly affects fuel efficiency, handling stability, and noise levels. A well-designed shape reduces drag, which in turn lowers fuel or energy consumption and improves high-speed performance. Engineers use wind tunnels, computational fluid dynamics (CFD), and scale models to visualize and refine airflow over the car’s body. Small changes—like adjusting side mirrors, optimizing the underbody, or adding subtle spoiler lips—can significantly improve aerodynamics. As electric vehicles gain traction, aerodynamic optimization becomes even more pivotal to extend battery range.Question:
How do industry regulations and standards influence automotive engineering processes, and what are the consequences of non-compliance?Answer:
Regulatory bodies set emissions limits, safety requirements, and testing protocols that manufacturers must meet before selling vehicles. These can mandate specific design criteria, such as seat belt anchorage strength or permissible exhaust emissions. Non-compliance can result in heavy fines, recall campaigns, and reputational damage. Hence, automotive engineers must stay updated with evolving regulations and incorporate compliance checks throughout the design cycle. This emphasis on regulatory adherence drives innovation in cleaner powertrains, safer chassis structures, and advanced driver-assist systems.Question:
In what ways can aspiring automotive engineers gain practical experience while studying, and how does this experience prepare them for industry challenges?Answer:
Hands-on projects—like building prototype vehicles in university design teams (e.g., Formula Student or Baja SAE)—equip students with real-world insights into vehicle dynamics, powertrain integration, and teamwork. Internships in automotive companies allow them to apply theoretical principles, learn industry-standard software, and interact with experienced engineers. This practical exposure teaches project management, problem-solving, and communication skills that are vital for tackling future challenges—such as integrating electrified systems or navigating global supply chain complexities.Question:
What career paths are available in automotive engineering, and how can students tailor their education to pursue specific roles within the industry?
Answer:
Automotive engineers can specialize in powertrain development, vehicle dynamics, electronics and software, manufacturing, or research and development. Roles include design engineer, test engineer, and product manager. Some positions focus on emerging areas like autonomous driving or electric vehicle systems. Students aiming for specific roles often choose electives in advanced powertrain technologies, control systems, or materials science. They can also join specialized extracurricular teams or research projects, attend relevant workshops, and network with industry professionals to strengthen their prospects in a chosen niche.
Automotive Engineering: Thought-Provoking Questions
1. Question:
How has the shift toward electrified powertrains challenged traditional automotive engineering principles, and what strategies are manufacturers using to meet these new demands?
Answer:
The move toward hybrid and electric vehicles (EVs) disrupts well-established engineering frameworks focused on internal combustion engines (ICEs). Engineers must re-evaluate vehicle layout, drivetrain architecture, and thermal management to accommodate batteries and electric motors. Traditional engineering relies heavily on fuel-based power density, but electrification introduces new constraints: weight distribution changes due to battery placement, demanding advanced materials and chassis designs to handle increased mass and maintain vehicle dynamics. Manufacturers are adopting multi-faceted strategies—investing in battery R&D to improve energy density, developing scalable modular platforms, and expanding charging infrastructure partnerships. By combining lightweight materials, regenerative braking systems, and improved aerodynamics, automakers optimize efficiency and performance, effectively aligning next-generation automotive engineering with sustainability goals.
2. Question:
In what ways do electronic control units (ECUs) and software integration shape modern automotive design, and why is cross-disciplinary expertise vital for this process?
Answer:
ECUs function as the “brain” of contemporary vehicles, managing critical functions such as engine timing, safety features, driver-assist systems, and infotainment. Effective software integration ensures these systems communicate seamlessly to deliver optimal performance, reliability, and user experience. This demands collaboration between mechanical, electrical, and software engineers, who must reconcile hardware constraints with sophisticated algorithms. Mechanical components, for instance, rely on real-time sensor data processed by the ECU to adjust fuel injection or activate anti-lock braking systems. A unified cross-disciplinary approach is essential: software developers must understand physical limitations, while mechanical engineers need familiarity with embedded systems. As vehicles incorporate more advanced driver-assistance and autonomous capabilities, the synergy of diverse expertise becomes a cornerstone of efficient, safe, and future-ready automotive designs.
3. Question:
Why is aerodynamics increasingly critical in automotive engineering, and how does this emphasis impact vehicle design choices beyond fuel efficiency?
Answer:
Aerodynamics plays a pivotal role not only in boosting fuel economy or extending electric range but also in enhancing stability, reducing wind noise, and maximizing overall performance. Improving a car’s aerodynamic profile demands careful body sculpting, strategic vent placements, and underbody optimization—each balancing drag reduction with cooling needs for the powertrain or braking systems. Aerodynamics also influences aesthetic decisions and manufacturing complexity; smooth curves and integrated components may call for specialized production techniques. High-performance vehicles exploit active aerodynamics, such as adjustable wings or grills, to adapt to changing driving conditions. Thus, engineering teams must juggle form and function, ensuring the final design meets safety standards, manufacturing feasibility, and consumer preferences while maintaining the aerodynamic efficiency that’s increasingly vital in a competitive market.
4. Question:
How do shifting environmental regulations shape the innovation cycle in automotive engineering, and what implications do these regulations have for long-term industry growth?
Answer:
Stringent emissions standards, fuel economy mandates, and regional zero-emission vehicle (ZEV) targets compel automakers to continually refine engine technologies, lightweight materials, and EV powertrains. Compliance with regulations accelerates the adoption of cutting-edge solutions such as hybrid drivetrains, advanced catalysts, and battery management systems. This regulatory environment often drives large-scale investments into R&D, collaborative ventures with tech firms, and workforce re-skilling. While meeting stringent regulations can be costly in the short term, it encourages technological breakthroughs that shape consumer expectations for cleaner, more efficient vehicles. In the long run, adherence to these policies spurs global competitiveness, fosters sustainable growth, and positions automotive companies at the forefront of next-generation transportation solutions.
5. Question:
In what ways do autonomous driving technologies challenge traditional automotive engineering paradigms, and how must engineers adapt their methods to accommodate these systems?
Answer:
Autonomous driving introduces layers of complexity beyond conventional mechanical design. Vehicles need robust sensor suites—cameras, radar, lidar—that continuously feed data into AI-driven control systems capable of making split-second decisions. This significantly alters design and validation processes: engineers must consider hardware–software redundancy, cybersecurity, fail-safe mechanisms, and human–machine interface design. Additionally, testing scenarios expand from standard reliability assessments to complex real-world simulations encompassing varied traffic, weather, and road conditions. Automotive engineers now collaborate with data scientists and robotics experts to refine sensor fusion algorithms and ensure these systems can anticipate and respond to unpredictable events. This integrated approach requires new validation frameworks, such as virtual simulations and scenario-based testing, reflecting the transformative shift autonomous driving represents.
6. Question:
What unique materials and manufacturing innovations are emerging in the automotive sector, and how do they address consumer and environmental pressures?
Answer:
The drive for lighter, stronger, and greener components has catalyzed the development of high-strength steel alloys, aluminum-magnesium blends, and carbon-fiber composites. These materials reduce weight without compromising structural integrity, thereby enhancing fuel efficiency or extending electric range. Novel manufacturing processes—like additive manufacturing (3D printing)—enable rapid prototyping and complex geometries unachievable through traditional methods, supporting customizable parts production. Environmentally, bio-based composites and recycled polymers offer sustainable alternatives while cutting down waste. As manufacturers integrate these new materials and processes, they face challenges such as ensuring repairability, ramping up mass production, and maintaining affordability. Nevertheless, these innovations meet growing consumer demands for efficient, eco-conscious vehicles, positioning the automotive industry as a leader in responsible manufacturing.
7. Question:
How are advanced driver-assist systems (ADAS) influencing everyday vehicle use, and what skill sets do engineers need to develop these technologies effectively?
Answer:
ADAS features—like adaptive cruise control, lane departure warnings, and automated parking—are revolutionizing the driving experience by enhancing safety, reducing driver fatigue, and gradually shifting toward semi-autonomous operation. Developing ADAS requires a blend of skills: mechanical expertise for sensor placement and integration, electrical engineering know-how for signal processing, and software proficiency in machine learning and sensor fusion algorithms. Engineers also must understand human factors to design intuitive interfaces and ensure drivers trust and correctly use these features. Regulatory knowledge is similarly pivotal, as ADAS must comply with safety standards that continue to evolve. Altogether, these multidisciplinary abilities enable robust, user-friendly systems that pave the way for fully autonomous vehicles.
8. Question:
What are the major challenges of integrating sustainable materials and processes into automotive supply chains, and how might these obstacles be overcome?
Answer:
Shifting to sustainable materials—like recycled metals, bioplastics, or low-emission manufacturing techniques—requires re-engineering supply chains originally optimized for cost and volume. Challenges include limited raw material availability, higher upfront costs, and insufficient recycling infrastructure. Additionally, integrating new materials demands new quality control measures and close collaboration with suppliers to ensure consistency and reliability. Overcoming these hurdles often involves forging strategic partnerships, investing in research, and leveraging economies of scale to drive down costs. Governments can accelerate this transition via incentives, grants, and clear sustainability guidelines. By gradually phasing in greener practices—perhaps starting with high-end or niche models—manufacturers develop proven methods and frameworks that can later be scaled across entire product lines.
9. Question:
How do current trends in shared mobility—like car-sharing and ride-hailing services—impact automotive engineering priorities, and what might the future look like in this sphere?
Answer:
Shared mobility reduces individual car ownership rates, emphasizing durability, low maintenance costs, and high daily usage resilience. Engineers must design vehicles optimized for frequent start–stop cycles, easy interior cleaning, and extended component lifespans. Flexible cabin layouts may cater to diverse passenger scenarios, from solo commuting to group travel. As data and usage patterns become increasingly central, over-the-air software updates and predictive maintenance features help maintain fleet efficiency and customer satisfaction. In the future, autonomous pods or shuttles could represent the next generation of shared mobility, demanding even more advanced vehicle-to-infrastructure communication and modular design approaches that streamline production and servicing for mass deployment.
10. Question:
What critical factors influence vehicle testing and validation processes in an era of constant automotive innovation, and how do these processes ensure public safety?
Answer:
Fast-evolving technologies, from electric drivetrains to driver-assist systems, require rigorous and adaptive testing frameworks that go beyond conventional crash tests and emissions checks. Engineers must evaluate hardware–software interoperability, sensor reliability under real-world conditions, and performance across varied environments (e.g., extreme temperatures or high humidity). Digital simulations and hardware-in-the-loop (HIL) systems complement physical prototypes, allowing complex scenarios—such as emergency braking around unexpected obstacles—to be safely tested in virtual spaces. Regulatory organizations set performance benchmarks, and real-world trials validate these metrics. This comprehensive approach, integrating simulations with controlled track testing and on-road assessments, ensures that new features reliably protect passengers, pedestrians, and other road users before market release.
11. Question:
How does global collaboration shape the current landscape of automotive engineering, and what benefits arise from multinational partnerships in research and development?
Answer:
Modern vehicles often result from collaborative efforts among manufacturers, suppliers, and tech companies scattered across continents. By pooling resources, multinational R&D teams can accelerate breakthroughs in battery technology, AI-driven control systems, and lightweight composites. This global synergy reduces costs through shared supply chains and leverages regional expertise—European safety standards, Japanese lean manufacturing methods, or North American software innovation, for example. Engineers benefit from a broader range of perspectives and skill sets, leading to more robust, culturally aware designs that can succeed in multiple markets. Furthermore, global partnerships foster knowledge exchange, fueling the continuous evolution of automotive technology while helping companies remain competitive and responsive to worldwide regulatory changes.
12. Question:
Why is it crucial for future automotive engineers to develop both technical knowledge and a strong grasp of social and environmental responsibilities, and how can education programs support this?
Answer:
The automotive sector profoundly influences global energy use, urban infrastructure, and public safety. Engineers who understand the societal and environmental implications of their work can drive responsible innovation—designing cleaner, safer, and more accessible vehicles. They must evaluate carbon footprints, materials sourcing, and community impacts, ensuring that mobility solutions resonate with ethical and regulatory standards. Education programs can foster this mindset by integrating sustainability modules, ethics seminars, and community-based design projects into the curriculum. Encouraging multidisciplinary collaborations—where engineering students team up with policy, economics, or environmental science peers—further expands their awareness. Ultimately, a holistic outlook helps future engineers create technologies that balance consumer desires, profitability, and ecological stewardship.