Sustainable Manufacturing
Sustainable manufacturing represents a transformative approach to production that prioritizes environmental stewardship, economic viability, and social responsibility. By integrating principles of resource efficiency and lifecycle thinking, it seeks to reduce the environmental footprint of manufacturing while enhancing long-term competitiveness. The field draws from foundational knowledge in industrial and manufacturing technologies, evolving in response to increasing global concerns about climate change, resource depletion, and industrial emissions.
Modern strategies for sustainability include the adoption of energy and resource efficiency in manufacturing, which emphasizes lean input use and minimal waste. This aligns with the goals of lean manufacturing, creating operational synergy between cost reduction and ecological impact minimization. Incorporating digital twin technology enables simulations of environmental performance, helping firms preemptively optimize product and process sustainability.
Innovations like Additive Manufacturing (3D Printing) contribute to sustainable practices by reducing material waste and supporting decentralized production. Similarly, advanced materials and manufacturing technologies introduce lightweight, recyclable, and energy-efficient alternatives to conventional components.
At the design level, computer-aided design (CAD) empowers engineers to create products with minimal environmental impact, integrating end-of-life considerations from the outset. Complementing these efforts, manufacturing process design and optimization focuses on streamlining workflows to conserve energy, time, and materials.
Sustainability also depends on human-centered engineering. Incorporating human factors and ergonomics helps create healthier and safer workplaces, which contributes to social sustainability. Simultaneously, quality control and assurance ensures products meet regulatory standards and minimize rework, reducing resource waste.
Automation and intelligent systems play a crucial role in sustainability. The rise of industrial automation and robotics helps optimize energy use and enhances precision, reducing unnecessary consumption. When embedded within computer-integrated manufacturing, these systems offer a framework for holistic sustainability monitoring across facilities.
Sustainable manufacturing must also embrace broader systemic shifts. The concept of Smart Manufacturing and Industry 4.0 introduces real-time data integration, predictive maintenance, and self-adaptive systems that reduce downtime and resource waste. Equally important is supply chain management, which ensures sustainable sourcing, transportation, and end-user delivery.
Beyond industrial systems, sustainable thinking influences cross-disciplinary domains. In automotive engineering, lightweight materials and fuel efficiency are emphasized. Biomechanical engineering explores eco-friendly prosthetics and health devices. Even fundamental areas like thermodynamics and heat transfer contribute to developing efficient heating and cooling systems within factories.
Supportive fields such as fluid mechanics and hydraulics enhance the design of low-energy transport and cooling systems, while solid mechanics underpins structural integrity and material conservation. Advances in nanotechnology further support the development of green coatings and energy-efficient surfaces.
Finally, the integration of robotics in mechanical engineering accelerates smart manufacturing, while the foundational knowledge offered in mechanical engineering remains indispensable for designing efficient systems. As global industries strive for decarbonization and resilience, sustainable manufacturing becomes a vital field that bridges innovation, efficiency, and ethics in engineering.
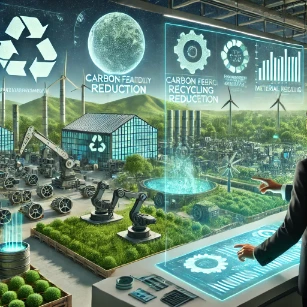
Table of Contents
Core Principles of Sustainable Manufacturing
Resource Efficiency
- Definition:
- Resource efficiency is the strategic approach of extracting the maximum possible value from resources such as raw materials, energy, and water while reducing waste, emissions, and costs. It forms the backbone of sustainable production by promoting responsible consumption and optimizing input-output ratios across all stages of the manufacturing lifecycle.
- Techniques:
- Optimizing production processes through lean methodologies that reduce unnecessary steps and minimize energy-intensive operations.
- Implementing smart scheduling systems to minimize downtime and batch production inefficiencies.
- Upgrading machinery to energy-efficient models and integrating automation to reduce overuse of inputs.
- Recycling and reusing materials and byproducts within the production facility, such as turning metal shavings into feedstock or recovering heat from exhaust systems for internal use.
- Adopting predictive maintenance strategies to extend machine life and reduce resource-intensive breakdowns.
Waste Reduction
- Definition:
- Waste reduction in sustainable manufacturing entails minimizing both solid and liquid waste outputs through efficient design, resource planning, and operational control. It involves not only decreasing waste at the source but also ensuring that any unavoidable waste is reused, recycled, or properly managed.
- Techniques:
- Implementing lean manufacturing principles to systematically identify and eliminate non-value-added activities and inefficiencies.
- Deploying real-time monitoring systems to detect process leaks, material overuse, or defective products early in the cycle.
- Designing modular production systems that allow flexible adaptation to different product configurations with minimal scrap.
- Developing closed-loop systems where waste streams from one process become the raw input for another, such as repurposing wastewater for secondary operations.
- Training workers on material handling best practices and incentivizing waste-conscious behavior through internal reward programs.
Emission Reduction
- Definition:
- Emission reduction involves limiting the output of greenhouse gases (GHGs) and other airborne pollutants generated during manufacturing. It focuses on transforming production systems to be less carbon-intensive, comply with environmental standards, and contribute to global climate action goals.
- Techniques:
- Switching to renewable energy sources such as solar, wind, and hydroelectric power for all factory operations, including lighting, heating, and machinery.
- Installing advanced air filtration systems that capture volatile organic compounds (VOCs), particulate matter, and other emissions before they exit into the atmosphere.
- Implementing carbon capture and storage (CCS) technologies to trap carbon dioxide at emission sources and store it underground or use it in other applications.
- Redesigning combustion processes to reduce nitrogen oxide (NOx) emissions and transition to low-emission fuels.
- Using life cycle analysis (LCA) tools to identify emission hotspots in the production chain and prioritize mitigation strategies.
- Learn more about emission control strategies from authoritative sources like the EPA Center for Corporate Climate Leadership.
Use of Sustainable Materials
- Definition:
- This principle emphasizes the substitution of non-renewable or environmentally damaging materials with sustainable alternatives. It supports circular economy practices and reduces dependence on virgin raw materials while enabling innovation in green product development.
- Examples:
- Bioplastics made from plant-based sources such as corn starch, sugarcane, or algae that biodegrade more quickly than traditional petroleum-based plastics.
- Recycled metals and composites such as aluminum and carbon fiber reclaimed from industrial or post-consumer waste streams.
- Natural fibers like hemp, bamboo, or flax used in composites or textiles to replace synthetic fibers.
- Reclaimed wood, rubber, and glass used in flooring, insulation, and packaging applications.
- Innovative materials like mycelium-based packaging or biodegradable foams derived from starch or cellulose.
Lifecycle Thinking
- Definition:
- Lifecycle thinking is the approach of evaluating the environmental and social impacts of a product across its entire existence—from raw material extraction and production to usage, disposal, and recycling. It encourages holistic decision-making that goes beyond immediate manufacturing costs.
- Techniques:
- Designing products for durability and long-term usability, reducing the frequency of replacement and associated resource consumption.
- Incorporating modular design principles that allow parts to be easily repaired, upgraded, or replaced without discarding the entire product.
- Using digital twins and lifecycle simulation tools to model environmental impacts before production decisions are made.
- Establishing take-back programs and reverse logistics to reclaim used products and components for remanufacturing or recycling.
- Engaging in environmental product declarations (EPDs) and third-party certifications that quantify the lifecycle impact and increase transparency to consumers.
Key Strategies in Sustainable Manufacturing
Renewable Energy Integration
- Definition:
- Renewable energy integration involves transitioning from fossil fuel-based energy sources to cleaner, sustainable alternatives such as solar, wind, hydro, geothermal, and biomass. This shift aims to reduce the carbon footprint of manufacturing facilities and align operations with global climate goals.
- Benefits:
- Reduces dependency on finite fossil fuel resources, improving long-term energy security and cost predictability.
- Cuts operational carbon emissions and helps facilities meet increasingly stringent regulatory requirements for environmental performance.
- Enhances brand image and aligns corporate identity with environmental responsibility, which is appealing to investors and consumers alike.
- Creates opportunities for decentralized energy production, such as rooftop solar arrays or on-site biomass systems, which reduce reliance on grid electricity.
- Examples:
- Solar-powered factories in regions with high sunlight availability, such as manufacturing plants in California or Southeast Asia.
- Biomass boilers converting agricultural waste into thermal energy for industrial heating, particularly in food processing or paper industries.
- Wind turbines directly powering production lines in northern Europe and North America, reducing grid dependency.
Circular Economy Practices
- Definition:
- This strategy focuses on designing products, services, and production systems that support continuous cycles of reuse, repair, refurbishment, and recycling, minimizing the generation of waste and maximizing the value of materials throughout their lifecycle.
- Applications:
- Integrating recycled content into manufacturing inputs, such as reprocessed polymers, reclaimed metals, or reused glass.
- Establishing take-back programs that retrieve end-of-life products from consumers for reprocessing or safe disposal.
- Redesigning product packaging to be biodegradable or returnable, reducing the environmental impact of logistics and post-use waste.
- Building product ecosystems where components are interchangeable or upgradable rather than disposable.
Process Optimization
- Definition:
- Process optimization refers to the continuous improvement of manufacturing workflows to minimize energy use, reduce waste generation, enhance quality, and lower costs while maintaining or improving product output and consistency.
- Techniques:
- Adopting lean manufacturing to eliminate inefficiencies, overproduction, waiting time, and unnecessary movement of resources.
- Utilizing advanced control systems to ensure equipment operates within optimal parameters, adjusting in real-time to variable conditions.
- Conducting energy audits and material flow analyses to identify key performance bottlenecks and opportunities for improvement.
- Implementing Six Sigma methodologies to reduce process variation and improve product quality and throughput.
Green Product Design
- Definition:
- Green product design, also known as sustainable or eco-design, focuses on developing goods that minimize adverse environmental impacts throughout their entire lifecycle—from raw material selection and manufacturing to usage and eventual disposal or recycling.
- Principles:
- Eco-Design: Incorporates strategies like reducing material use, selecting non-toxic inputs, simplifying components, and using renewable materials to ensure sustainability from the start.
- Cradle-to-Cradle Design: Encourages products to be fully recyclable or biodegradable, enabling them to enter a new production cycle without becoming waste.
- Modular design to facilitate maintenance, repair, and eventual reuse of components.
- Product disassembly planning to enable easy separation of materials at the end of life.
Digital Transformation
- Definition:
- Digital transformation in sustainable manufacturing refers to the application of digital tools and platforms—such as Internet of Things (IoT), artificial intelligence (AI), cloud computing, and digital twins—to improve decision-making, reduce waste, and enhance resource efficiency across the production lifecycle.
- Technologies:
- IoT-enabled sensors that collect real-time data on energy consumption, material flows, and equipment status, enabling more precise control over resource usage.
- AI and machine learning systems that analyze production data to detect inefficiencies, predict maintenance requirements, and optimize scheduling and logistics.
- Digital twins that simulate factory conditions, allowing virtual experimentation to improve layouts, streamline processes, and test sustainability scenarios without physical trial-and-error.
- Cloud platforms that centralize sustainability metrics for easier reporting and compliance with regulations.
- For more insights into how digital tools are transforming manufacturing, visit McKinsey’s Digital Manufacturing Insights.
Additive Manufacturing (3D Printing)
- Definition:
- Additive manufacturing, commonly known as 3D printing, involves creating objects by layering material based on a digital model. This technique minimizes waste compared to subtractive methods (cutting, drilling) and enables rapid prototyping and customization with fewer resources.
- Applications:
- Producing lightweight components for sectors like aerospace, automotive, and healthcare, where material savings translate directly to energy and cost savings.
- Creating complex geometries that are not possible with traditional manufacturing, reducing the number of parts needed and streamlining assembly.
- Using recycled materials such as plastic pellets or metal powders reclaimed from other processes to close the material loop.
- Printing replacement parts on-demand, reducing the need for inventory and associated environmental costs.
Water Management
- Definition:
- Water management strategies in sustainable manufacturing involve optimizing water use through conservation, treatment, and recycling systems. The goal is to reduce freshwater withdrawal, minimize wastewater discharge, and ensure compliance with environmental standards.
- Techniques:
- Deploying closed-loop water systems for cooling and washing operations, which allow water to be reused multiple times before treatment or discharge.
- Collecting rainwater for non-potable uses, such as cleaning equipment or irrigating facility grounds.
- Recycling greywater from wash stations and other non-toxic processes for secondary uses like flushing or cooling towers.
- Investing in filtration and reverse osmosis systems that allow wastewater to be treated on-site to a reusable quality.
- Monitoring water quality in real-time with sensors to ensure environmental compliance and optimize treatment costs.
Applications of Sustainable Manufacturing
Automotive Industry
- Applications:
- Lightweighting vehicles involves using materials like aluminum, carbon fiber, and advanced composites to reduce the overall mass of vehicles. This directly improves fuel economy and reduces greenhouse gas emissions during operation.
- Incorporating recycled materials such as plastics, metals, and textiles into car interiors, dashboards, and structural components helps reduce raw material extraction and waste sent to landfills.
- Integrating sustainable design principles into vehicle manufacturing processes allows for greater modularity and end-of-life recyclability of automotive parts.
- Applying closed-loop systems in automotive production enables manufacturers to reuse scrap material generated during stamping, cutting, and welding processes.
- Examples:
- Tesla’s Gigafactories operate with solar and wind energy, utilizing vertical integration and sustainable supply chains to produce batteries and electric vehicles with lower lifecycle emissions.
- BMW’s manufacturing process includes the use of recycled aluminum and thermoplastics, reducing the embedded carbon footprint of each vehicle while ensuring structural integrity and performance.
- Ford and General Motors have adopted soybean-based foam for seats and recycled plastic bottles for underbody components, showcasing the industry’s shift toward green materials.
Electronics Manufacturing
- Applications:
- Designing electronics with modular components allows for easier disassembly, repair, and upgrade, extending product life and reducing electronic waste.
- Reducing dependency on rare earth materials by substituting with more abundant or recycled elements ensures resource sustainability and decreases geopolitical supply risks.
- Implementing energy-efficient fabrication techniques like low-temperature soldering and optimized circuit board layouts contributes to lower environmental impact during manufacturing.
- Minimizing packaging and transitioning to biodegradable or reusable packaging materials reduces the environmental footprint associated with logistics.
- Examples:
- Apple’s aggressive sustainability targets include using 100% recycled aluminum in the enclosures of MacBooks and iPhones, and transitioning to recycled rare earth elements in magnets.
- Dell and HP have implemented closed-loop recycling programs, allowing customers to return old equipment, which is then dismantled and reintroduced into the production stream.
Food and Beverage Industry
- Applications:
- Reducing food waste during processing involves optimizing production lines, improving storage conditions, and refining logistics to minimize spoilage.
- Using renewable energy for packaging, refrigeration, and cooking helps cut carbon emissions in facilities that traditionally rely heavily on fossil fuels.
- Switching to biodegradable packaging and sourcing ingredients locally decreases transportation emissions and landfill waste.
- Implementing anaerobic digestion systems allows food producers to convert waste into biogas, which can then power equipment or be fed back into the grid.
- Examples:
- Breweries like Sierra Nevada and Heineken capture CO₂ emissions during fermentation and reuse them for carbonation, reducing the need for externally sourced gases.
- Companies such as Unilever and Nestlé have incorporated sustainable farming practices into their supply chains to ensure long-term agricultural viability.
Textile and Apparel Industry
- Applications:
- Producing fabrics from recycled or biodegradable materials like organic cotton, bamboo fibers, and reclaimed polyester reduces water consumption, chemical usage, and landfill burden.
- Water-saving dyeing techniques, such as digital printing and supercritical CO₂ dyeing, significantly reduce water and chemical use compared to traditional dye baths.
- Supply chain transparency and traceability tools are increasingly used to ensure responsible sourcing and ethical labor practices throughout production networks.
- Closed-loop recycling initiatives encourage consumers to return used garments, which are then reprocessed into new textiles or products.
- Examples:
- Patagonia’s innovative use of recycled polyester from plastic bottles, as well as its garment repair and take-back programs, demonstrates leadership in sustainable apparel.
- Waterless dyeing technologies adopted by Nike and Adidas reduce both water use and effluent discharge, supporting eco-friendly production goals.
- Learn more about cutting-edge sustainable apparel practices at Common Objective’s Innovation Series.
Construction and Building Materials
- Applications:
- Reusing concrete and steel from demolition sites reduces the need for virgin materials and lowers the embodied carbon in new construction projects.
- Modular and prefabricated construction allows for more precise use of resources, less waste, and faster build times.
- Green insulation materials such as sheep wool, cellulose, and aerogels enhance energy efficiency while being non-toxic and renewable.
- Installing smart HVAC systems and automated lighting in buildings reduces operational energy consumption and supports LEED certification.
- Examples:
- Buildings certified by LEED (Leadership in Energy and Environmental Design) and BREEAM (Building Research Establishment Environmental Assessment Method) use performance metrics to track sustainability goals from design through occupancy.
- Eco-friendly skyscrapers in Singapore, London, and Toronto feature green walls, solar façades, and rainwater harvesting systems.
Pharmaceutical Manufacturing
- Applications:
- Reducing waste in drug formulation includes minimizing solvent use, scaling down batch sizes, and optimizing reaction pathways for higher yields and less byproduct.
- Green chemistry principles are applied to minimize hazardous substances, reduce reaction steps, and improve atom economy in drug synthesis.
- Recycling solvents through distillation and membrane separation technologies conserves resources and reduces hazardous waste disposal.
- Shifting to continuous manufacturing enables more consistent quality, less material loss, and smaller facility footprints compared to batch processing.
- Examples:
- Pharmaceutical firms like GlaxoSmithKline and Pfizer are investing in green manufacturing technologies to align with environmental regulations and reduce lifecycle impacts.
- The American Chemical Society’s Green Chemistry Institute promotes tools and training for sustainable pharmaceutical manufacturing practices.
Technologies Enabling Sustainable Manufacturing
Internet of Things (IoT)
- Role:
- The Internet of Things (IoT) refers to interconnected sensors and devices that collect and transmit data across manufacturing systems in real time. These networks enable continuous monitoring of energy usage, raw material flow, and water consumption, allowing operators to quickly identify inefficiencies and anomalies.
- Applications:
- IoT sensors embedded in equipment can detect abnormal performance, helping maintenance teams prevent breakdowns that cause energy waste and material losses.
- Smart meters and real-time dashboards allow facility managers to monitor utility consumption trends, enabling targeted improvements such as switching off idle equipment or optimizing HVAC usage.
- Data from IoT-enabled systems also feeds into sustainability reports and helps companies track progress toward regulatory and ESG goals.
Artificial Intelligence (AI)
- Role:
- AI enhances decision-making by analyzing complex datasets and identifying optimization opportunities. In sustainable manufacturing, AI models predict equipment maintenance needs, reduce overproduction, and optimize energy consumption patterns.
- Applications:
- AI algorithms dynamically adjust production schedules based on energy grid signals, shifting high-energy processes to off-peak hours to reduce carbon intensity.
- Machine learning models process historical sensor data to forecast component failures, enabling predictive maintenance that extends equipment life and reduces downtime.
- AI-based quality control systems use computer vision to detect defects early, reducing waste from faulty products and rework.
Blockchain
- Role:
- Blockchain offers a decentralized, tamper-proof way to track and verify data throughout the supply chain. It enhances trust and transparency by providing immutable records of material origins, processing methods, and environmental impacts.
- Applications:
- Manufacturers use blockchain to verify that raw materials come from certified sustainable sources, such as recycled metals or responsibly harvested timber.
- Blockchain systems enable customers to scan a QR code on a product and access its entire sustainability journey, from extraction to production to logistics.
- The World Economic Forum explores how blockchain strengthens traceability and accountability in sustainability-focused supply chains.
Renewable Energy Systems
- Role:
- Renewable energy technologies allow manufacturers to decarbonize operations by replacing fossil fuel use with clean, abundant power sources such as solar, wind, geothermal, and biomass.
- Examples:
- Many factories now integrate rooftop solar arrays or solar farms to meet a portion of their electricity demand on-site, reducing emissions and utility costs.
- Wind turbines installed at industrial parks feed clean electricity directly into the grid or on-site microgrids.
- Biomass boilers using agricultural or wood waste provide carbon-neutral heat for manufacturing processes, reducing reliance on natural gas or coal.
Robotics and Automation
- Role:
- Automation through robotics improves precision, consistency, and speed in manufacturing, leading to significant material and energy savings. Robots minimize human error and help standardize production workflows with minimal waste.
- Applications:
- Advanced robotic arms perform high-precision tasks such as laser cutting, additive manufacturing, and micro-welding with exceptional accuracy, ensuring optimal material use and minimal scrap.
- Automated systems in warehouses and assembly lines reduce idle times and streamline logistics, which cuts emissions associated with storage and internal transport.
- Collaborative robots (cobots) work alongside human operators, enhancing ergonomics and allowing repetitive, high-risk tasks to be handled with reduced energy usage and higher safety.
Benefits of Sustainable Manufacturing
- Environmental Protection:
- Sustainable manufacturing prioritizes minimizing environmental impact by reducing greenhouse gas emissions, cutting down waste generation, and conserving non-renewable resources. Through the implementation of clean technologies and responsible sourcing, companies can significantly lower their ecological footprint. For example, installing energy-efficient machinery and using biodegradable packaging materials can substantially reduce pollution across the product lifecycle. The use of closed-loop systems further ensures that waste is recycled into new production processes, preserving ecosystems and biodiversity.
- Cost Savings:
- By streamlining operations and improving efficiency, sustainable manufacturing can lead to considerable cost reductions. Lower utility bills from decreased energy and water usage, less spending on raw materials due to reuse and recycling, and savings from reduced regulatory penalties all contribute to financial benefits. For instance, manufacturers that adopt lean processes and LED lighting systems often report noticeable drops in operational costs. Over time, these savings can offset the initial investments in green technologies and create long-term financial resilience.
- Regulatory Compliance:
- Governments around the world are implementing stricter environmental standards. Sustainable manufacturing ensures compliance with laws related to emissions, waste disposal, and product safety, reducing the risk of fines and legal action. Adhering to certifications like ISO 14001 not only fulfills legal obligations but also strengthens internal environmental governance. Companies that proactively align with such regulations often find it easier to enter new markets and build trusted partnerships.
- Enhanced Brand Reputation:
- In today’s consumer-driven market, environmental responsibility is a strong differentiator. Businesses that integrate sustainability into their operations attract attention from ethically minded consumers, institutional investors, and the general public. A strong green image can lead to increased brand loyalty and media coverage. For instance, brands that are transparent about their carbon footprint and actively pursue sustainability goals are frequently featured in sustainability indices and environmental rankings. A notable example is CDP’s A List, which recognizes companies demonstrating environmental leadership.
- Market Competitiveness:
- Sustainable practices offer a competitive edge by driving innovation and opening access to green markets. Products designed with lower environmental impact are increasingly preferred in procurement policies and consumer purchases. Moreover, sustainable companies often experience lower risks in volatile markets due to their reduced dependence on fluctuating fossil fuel prices and fragile global supply chains. The integration of eco-design principles and circular economy strategies also fosters the development of new product lines that resonate with emerging sustainability trends.
- Resilience:
- Reducing reliance on finite and non-renewable resources enhances long-term operational stability. Sustainable manufacturing promotes the use of locally sourced materials, renewable inputs, and modular systems, all of which contribute to supply chain resilience. During global disruptions—such as pandemics or geopolitical tensions—sustainably oriented manufacturers tend to recover faster due to their flexible and diversified resource bases. In addition, incorporating lifecycle thinking allows organizations to anticipate risks and adapt to shifting environmental and regulatory conditions more effectively.
Challenges in Sustainable Manufacturing
- High Initial Investment:
- Implementing sustainable manufacturing often demands substantial capital expenditures, especially when transitioning from traditional to green processes. The costs of renewable energy systems, waste reduction infrastructure, and eco-friendly machinery can be a major deterrent for small and medium enterprises. While these investments typically result in long-term savings and efficiency gains, the payback period may be too extended for companies with tight budgets. Furthermore, justifying such investments internally can be difficult without immediate financial returns, especially in highly competitive markets.
- Complexity in Supply Chains:
- Modern manufacturing relies on complex, multi-tiered supply chains that span continents. Ensuring sustainability at every level—from raw material sourcing to final product delivery—is an intricate task. It requires rigorous tracking of suppliers’ practices, compliance with varying regional environmental standards, and alignment of sustainability goals across partners. Achieving transparency in supply chains also demands significant investment in monitoring technologies and collaboration tools. Initiatives like the WBCSD Decarbonizing Supply Chains project aim to help organizations manage these challenges through shared frameworks and tools.
- Technology Integration:
- Many manufacturers rely on legacy systems that were not designed with sustainability in mind. Retrofitting or replacing these systems with modern, eco-friendly alternatives is technically complex and expensive. It often involves major operational disruptions, workforce retraining, and compatibility issues with existing equipment. Moreover, not all sustainability technologies are plug-and-play; they require customized adaptation to specific industrial environments. Bridging the gap between traditional processes and digital sustainability tools such as IoT or AI can pose a steep learning curve and demand significant change management efforts.
- Limited Access to Sustainable Materials:
- Accessing sustainable raw materials remains a critical bottleneck for many manufacturers. The supply of eco-friendly inputs such as bioplastics, recycled metals, and renewable textiles is not yet consistent or scalable in many regions. Additionally, these materials are often more expensive than conventional alternatives due to low production volumes or complex processing requirements. Price volatility and uncertain quality further complicate procurement decisions. To overcome this, manufacturers must build long-term relationships with sustainable material suppliers and invest in alternative material research and development.
- Workforce Training:
- Transitioning to sustainable manufacturing requires not only technological upgrades but also a cultural and operational shift within the organization. Employees at all levels need to understand sustainability principles, new processes, and the rationale behind them. This necessitates comprehensive training programs, continuous professional development, and a proactive change management strategy. Without proper workforce engagement, even the most advanced sustainable technologies may fail to deliver desired outcomes. Investing in sustainability education helps cultivate a workforce capable of driving innovation and maintaining long-term compliance with evolving standards.
Emerging Trends in Sustainable Manufacturing
- Circular Manufacturing:
- One of the most transformative trends is the shift toward circular manufacturing, which prioritizes closed-loop systems where materials and products are reused, repaired, and recycled rather than discarded. This model aims to extend the lifecycle of products and minimize the use of virgin resources. Manufacturers adopting circular principles redesign their products to be modular, durable, and recyclable. They also implement take-back schemes, remanufacturing initiatives, and material recovery programs to reduce dependency on raw inputs. This approach not only lowers environmental impact but also strengthens economic resilience by reducing supply chain risks.
- Green Supply Chains:
- Green supply chains integrate environmental considerations into every aspect of the supply network—from sourcing raw materials to logistics and final delivery. This includes selecting suppliers based on their sustainability practices, optimizing transportation routes to reduce fuel usage, and using eco-friendly packaging. Companies are also collaborating more closely with their partners to establish shared sustainability goals and improve overall supply chain transparency. Digital tools like blockchain and real-time monitoring systems are increasingly deployed to track sustainability metrics across the supply chain and ensure compliance with green standards. The McKinsey report on sustainable supply chains provides insights into how organizations can create value through green logistics and sourcing.
- Decarbonization Goals:
- Decarbonization is a cornerstone of sustainable manufacturing, with companies committing to ambitious targets such as achieving net-zero emissions by mid-century. To meet these goals, manufacturers are transitioning to renewable energy sources like solar, wind, and hydroelectric power. They are also investing in carbon capture and storage (CCS) technologies, energy efficiency upgrades, and cleaner fuels such as green hydrogen. Decarbonization strategies often involve redefining supply chains, redesigning energy-intensive processes, and incorporating lifecycle carbon accounting into product development. These initiatives are crucial for aligning with global climate agreements and national emissions targets.
- Smart Factories:
- Smart factories represent the convergence of digital technology with sustainable practices. These highly automated and connected manufacturing environments use sensors, Internet of Things (IoT) devices, and artificial intelligence to monitor, analyze, and optimize energy and resource consumption in real time. For example, smart systems can detect inefficiencies in energy usage, schedule machinery during off-peak hours, and predict maintenance needs to avoid wasteful breakdowns. Such technologies not only reduce the environmental footprint of manufacturing but also improve productivity, agility, and safety across the production lifecycle.
- Bio-Based Materials:
- With growing concerns over the environmental impact of synthetic and petroleum-derived materials, bio-based alternatives are gaining traction. These materials are derived from renewable biological sources like corn, algae, and agricultural waste. Bioplastics, bio-resins, and natural fiber composites are increasingly used in packaging, automotive, and consumer electronics industries. They offer benefits such as biodegradability, reduced carbon footprint, and compatibility with circular economy models. Research and development in this area are focused on enhancing the performance and scalability of bio-based materials to make them viable substitutes in high-demand applications.
Future Directions in Sustainable Manufacturing
- Net-Zero Manufacturing:
- The pursuit of net-zero manufacturing has become a defining objective for industries aiming to align with global climate targets. This involves not only reducing greenhouse gas emissions from production processes but also offsetting any residual emissions through verified carbon offset programs. Manufacturers are transitioning to renewable energy sources such as solar, wind, and geothermal power to reduce reliance on fossil fuels. In parallel, energy efficiency measures—like upgrading insulation, adopting LED lighting, and optimizing machinery—are being widely implemented. Some organizations are also exploring nature-based solutions like reforestation to complement technological strategies. The ultimate goal is to establish carbon-neutral production lines that support long-term climate resilience.
- Global Collaboration:
- Addressing the multifaceted challenges of sustainability requires international cooperation. Global collaboration facilitates the exchange of best practices, sustainable technologies, and harmonized standards. Governments, multinational corporations, NGOs, and academic institutions are forming consortia to tackle issues such as climate change, e-waste management, and sustainable resource extraction. These partnerships often lead to the development of innovative solutions that are scalable and adaptable across diverse industrial contexts. For instance, collaborative research projects may accelerate the adoption of green manufacturing techniques in developing countries. Platforms like the UNIDO Global Environment Facility play a critical role in enabling such international efforts.
- Policy and Regulation:
- Governmental policies are instrumental in shaping the future landscape of sustainable manufacturing. Through legislation, financial incentives, and regulatory frameworks, governments can catalyze industry-wide transformation. Examples include carbon pricing schemes, green tax credits, and mandatory sustainability reporting standards. In many regions, manufacturers are now required to meet strict environmental performance benchmarks to maintain their licenses or qualify for public contracts. Furthermore, trade agreements are increasingly incorporating environmental clauses that encourage manufacturers to adopt cleaner technologies and practices. These policy instruments not only encourage innovation but also level the playing field by internalizing the environmental costs of production.
- Advanced Recycling Technologies:
- Recycling technologies are rapidly evolving to handle increasingly complex waste streams. Traditional recycling methods are often insufficient for dealing with multi-material products like smartphones, batteries, and composite structures. Advanced methods—such as chemical recycling, pyrolysis, and enzymatic breakdown—offer higher recovery rates and enable the separation of valuable materials at a molecular level. These technologies make it feasible to recover rare earth metals, plastics, and fibers with minimal degradation, facilitating their reuse in high-performance applications. Moreover, innovations in automated sorting and AI-driven material recognition enhance the efficiency and cost-effectiveness of recycling operations.
- Integration with Industry 4.0:
- Industry 4.0 represents the digital transformation of manufacturing through technologies such as the Internet of Things (IoT), artificial intelligence (AI), cloud computing, and cyber-physical systems. When integrated with sustainability objectives, these technologies enable real-time monitoring of environmental parameters, predictive maintenance, and smart resource allocation. For example, AI algorithms can identify inefficiencies in energy usage, while IoT sensors track waste levels and emissions across the production floor. This integration empowers manufacturers to make data-driven decisions that align with both economic and environmental performance goals. Ultimately, Industry 4.0 lays the foundation for agile, transparent, and eco-conscious manufacturing systems.
Why Study Sustainable Manufacturing
Balancing Production with Environmental Responsibility
Sustainable manufacturing focuses on minimizing the environmental impact of production processes. Students learn how to reduce waste, energy consumption, and emissions. This supports long-term ecological balance and regulatory compliance.
Green Technologies and Materials
Students study renewable energy systems, biodegradable materials, and eco-friendly processes. They explore how to design products and systems with sustainability in mind. This fosters innovation that aligns with environmental goals.
Life Cycle Assessment and Resource Efficiency
The course introduces tools for analyzing the environmental impact of products over their lifespan. Students learn to optimize resource use from raw materials to disposal. This enables more sustainable decision-making in engineering and design.
Compliance with Regulations and Standards
Students explore environmental laws, certifications, and sustainability reporting. They learn how to align operations with global frameworks like ISO 14001. This ensures ethical and responsible business practices.
Innovation for a Circular Economy
Sustainable manufacturing supports reuse, remanufacturing, and recycling. Students study how to design closed-loop systems that reduce environmental impact. This prepares them to lead in circular economy transitions.
Sustainable Manufacturing: Conclusion
Sustainable manufacturing represents a transformative paradigm shift in how goods are produced, emphasizing not only economic productivity but also environmental stewardship and social responsibility. As industrialization continues to expand globally, traditional manufacturing approaches are increasingly recognized as unsustainable due to their reliance on finite resources, high energy consumption, and substantial waste generation. In contrast, sustainable manufacturing aims to balance profitability with the urgent need to preserve ecological systems, reduce carbon footprints, and foster ethical labor practices.
One of the cornerstones of sustainable manufacturing is the integration of eco-friendly technologies that minimize environmental impact across every stage of the production lifecycle. These technologies range from renewable energy systems and clean process innovations to closed-loop recycling mechanisms and digital monitoring tools. When deployed effectively, such innovations not only reduce the strain on natural resources but also enhance operational efficiency, enabling businesses to achieve greater output with fewer inputs.
Waste minimization plays a critical role in this transformation. By adopting lean manufacturing, additive manufacturing, and circular economy models, companies can significantly lower material usage and extend the lifespan of components and products. Furthermore, by reusing by-products or remanufacturing used goods, industries move toward a more regenerative model of production that aligns with nature’s cyclical patterns rather than linear consumption models.
Energy use is another domain where sustainable manufacturing has a profound impact. The shift from fossil fuels to solar, wind, biomass, and geothermal energy helps manufacturers decouple growth from carbon emissions. Additionally, technologies like smart grids, advanced energy storage, and AI-powered predictive analytics optimize energy flows in real-time, reducing operational costs while meeting sustainability targets.
Social responsibility is also deeply intertwined with sustainable manufacturing. Ethical sourcing, fair labor practices, and community engagement are key elements that ensure the well-being of workers and local populations. This holistic approach acknowledges that long-term industrial success depends on more than profitability—it requires trust, transparency, and equitable treatment of stakeholders throughout the supply chain.
As global priorities shift toward climate resilience, regulatory compliance, and sustainable development, companies that embrace sustainable manufacturing are better positioned to navigate emerging challenges and seize new market opportunities. Consumers are increasingly favoring environmentally responsible brands, and investors are prioritizing companies with robust environmental, social, and governance (ESG) strategies. As a result, sustainable practices are becoming both a moral imperative and a competitive advantage.
Looking forward, the continuous evolution of enabling technologies—such as blockchain for supply chain transparency, IoT for resource tracking, and AI for decision-making—will further enhance the effectiveness of sustainable manufacturing. Moreover, collaboration among governments, industries, and academic institutions will be essential for scaling these practices globally and ensuring their accessibility to small and medium enterprises.
In conclusion, sustainable manufacturing is not a temporary trend but a foundational principle for future industrial development. By embedding sustainability into design, production, logistics, and corporate governance, manufacturers contribute to a circular, inclusive, and low-carbon economy. These efforts not only benefit the planet but also create value for shareholders, employees, and society at large—ensuring long-term resilience in an increasingly resource-constrained world.
Sustainable Manufacturing: Review Questions and Detailed Answers
1. What is sustainable manufacturing, and why is it important in today’s industrial landscape?
Answer:
Sustainable Manufacturing Defined: Sustainable manufacturing refers to the creation of products through economically-sound processes that minimize negative environmental impacts while conserving energy and natural resources. It also aims to enhance the quality of life for employees, communities, and society as a whole.
Importance in Today’s Industrial Landscape:
Environmental Protection:
- Impact: Reduces pollution, waste, and carbon emissions, mitigating climate change and preserving ecosystems.
- Reason: Industrial activities are significant contributors to environmental degradation; sustainable practices help minimize this impact.
Resource Efficiency:
- Impact: Optimizes the use of materials and energy, reducing dependency on finite resources.
- Reason: Ensures long-term availability of essential resources and reduces operational costs.
Regulatory Compliance:
- Impact: Helps companies adhere to increasingly stringent environmental laws and regulations.
- Reason: Non-compliance can result in hefty fines, legal actions, and damage to reputation.
Market Demand:
- Impact: Meets the growing consumer preference for eco-friendly and ethically produced products.
- Reason: Enhances brand loyalty and opens new market opportunities.
Economic Benefits:
- Impact: Lowers costs through energy savings, waste reduction, and improved efficiency.
- Reason: Sustainable practices often lead to operational efficiencies and long-term profitability.
Social Responsibility:
- Impact: Promotes ethical labor practices and contributes positively to communities.
- Reason: Enhances corporate reputation and fosters a positive relationship with stakeholders.
Conclusion: Sustainable manufacturing is crucial for balancing economic growth with environmental stewardship and social responsibility. It ensures that industrial progress does not come at the expense of the planet or future generations, making it an essential strategy for modern businesses.
2. How can energy efficiency be achieved in sustainable manufacturing processes?
Answer:
Achieving Energy Efficiency in Sustainable Manufacturing:
Energy Audits:
- Action: Conduct comprehensive energy audits to identify areas of high energy consumption and inefficiencies.
- Benefit: Provides a clear understanding of where energy is used and where savings can be made.
Upgrade to Energy-Efficient Equipment:
- Action: Replace old machinery and equipment with energy-efficient models that consume less power.
- Benefit: Reduces energy consumption and operational costs while enhancing productivity.
Implementing Automation and Smart Controls:
- Action: Use automated systems and smart controls to optimize energy use in real-time.
- Benefit: Ensures machinery operates only when needed, reducing idle energy consumption.
Optimizing Manufacturing Processes:
- Action: Streamline production processes to eliminate unnecessary steps and reduce energy usage.
- Benefit: Enhances efficiency and minimizes energy waste.
Heat Recovery Systems:
- Action: Install systems to capture and reuse waste heat generated during manufacturing.
- Benefit: Provides additional energy for other processes, reducing overall energy demand.
Lighting Upgrades:
- Action: Switch to LED lighting and incorporate motion sensors to reduce lighting energy use.
- Benefit: Lowers electricity consumption and maintenance costs.
Insulation and Building Efficiency:
- Action: Improve insulation and optimize HVAC systems to maintain optimal temperatures with less energy.
- Benefit: Reduces the energy required for heating and cooling manufacturing facilities.
Employee Training and Awareness:
- Action: Educate employees on energy-saving practices and encourage their participation in energy efficiency initiatives.
- Benefit: Promotes a culture of sustainability and ensures collective effort towards energy conservation.
Renewable Energy Integration:
- Action: Incorporate renewable energy sources such as solar, wind, or biomass to power manufacturing operations.
- Benefit: Reduces reliance on fossil fuels and lowers greenhouse gas emissions.
Continuous Monitoring and Improvement:
- Action: Use energy management systems to continuously monitor energy use and identify opportunities for further improvements.
- Benefit: Ensures ongoing energy efficiency and adapts to changing operational needs.
Conclusion: Achieving energy efficiency in sustainable manufacturing involves a combination of technological upgrades, process optimization, and cultural shifts within the organization. By implementing these strategies, manufacturers can significantly reduce their energy consumption, lower costs, and contribute to environmental sustainability.
3. What role does waste reduction play in sustainable manufacturing, and what methods can be employed to achieve it?
Answer:
Role of Waste Reduction in Sustainable Manufacturing:
Environmental Impact:
- Role: Minimizes the amount of waste sent to landfills and reduces pollution.
- Impact: Helps preserve natural resources and reduces the carbon footprint of manufacturing activities.
Cost Savings:
- Role: Reduces costs associated with waste disposal and raw material consumption.
- Impact: Enhances profitability by lowering operational expenses.
Resource Efficiency:
- Role: Ensures that materials are used effectively, reducing the need for new raw materials.
- Impact: Promotes the sustainable use of resources and reduces dependency on finite supplies.
Regulatory Compliance:
- Role: Helps manufacturers comply with environmental regulations regarding waste management.
- Impact: Avoids fines, legal issues, and enhances corporate reputation.
Innovation and Competitive Advantage:
- Role: Encourages the development of innovative processes and products that generate less waste.
- Impact: Differentiates companies in the market and meets consumer demand for sustainable products.
Methods to Achieve Waste Reduction:
Lean Manufacturing:
- Method: Implement lean principles to eliminate non-value-adding activities and reduce waste.
- Benefit: Streamlines processes and enhances efficiency.
Recycling and Reusing Materials:
- Method: Establish systems to recycle waste materials and reuse them in the production process.
- Benefit: Reduces the need for new raw materials and minimizes waste disposal.
Process Optimization:
- Method: Analyze and improve manufacturing processes to reduce material waste.
- Benefit: Increases efficiency and lowers the generation of scrap and defective products.
Design for Sustainability:
- Method: Design products with minimal material use and consider their end-of-life disposal.
- Benefit: Reduces waste generation and facilitates easier recycling or reuse.
Employee Training and Engagement:
- Method: Educate employees on waste reduction techniques and involve them in sustainability initiatives.
- Benefit: Promotes a culture of waste minimization and continuous improvement.
Advanced Manufacturing Technologies:
- Method: Use technologies such as additive manufacturing (3D printing) to reduce material waste.
- Benefit: Enhances precision in production and minimizes excess material usage.
Waste Audits:
- Method: Conduct regular audits to identify sources of waste and areas for improvement.
- Benefit: Provides actionable insights to target waste reduction efforts effectively.
Supplier Collaboration:
- Method: Work with suppliers to minimize packaging waste and adopt sustainable materials.
- Benefit: Reduces waste generation upstream in the supply chain.
Closed-Loop Systems:
- Method: Implement closed-loop systems where waste from one process becomes input for another.
- Benefit: Maximizes resource utilization and minimizes overall waste.
Monitoring and Reporting:
- Method: Use waste tracking systems to monitor waste generation and set reduction targets.
- Benefit: Ensures accountability and tracks progress towards waste reduction goals.
Conclusion: Waste reduction is a fundamental aspect of sustainable manufacturing, contributing to environmental protection, cost savings, and resource efficiency. By employing a combination of lean principles, recycling, process optimization, and technological innovations, manufacturers can significantly reduce waste and enhance the sustainability of their operations.
4. How can renewable energy sources be integrated into manufacturing processes to promote sustainability?
Answer:
Integrating Renewable Energy Sources into Manufacturing Processes:
Solar Power Integration:
- Method: Install solar panels on manufacturing facilities to generate electricity.
- Benefit: Reduces reliance on fossil fuels, lowers energy costs, and decreases greenhouse gas emissions.
- Example: A factory rooftops equipped with photovoltaic panels can supply a significant portion of its energy needs.
Wind Energy Utilization:
- Method: Invest in wind turbines either on-site or through wind farms to generate power.
- Benefit: Provides a clean and renewable source of energy, particularly effective in regions with consistent wind patterns.
- Example: Offshore wind farms can supply large-scale energy to manufacturing plants located near coastal areas.
Geothermal Energy:
- Method: Utilize geothermal heat pumps for heating and cooling manufacturing facilities.
- Benefit: Offers a stable and efficient energy source with minimal environmental impact.
- Example: Geothermal systems can maintain optimal temperatures in factories, reducing energy consumption for HVAC systems.
Biomass Energy:
- Method: Use organic materials such as agricultural waste, wood chips, or dedicated energy crops to generate heat and power.
- Benefit: Converts waste into valuable energy, reducing landfill use and carbon emissions.
- Example: A manufacturing plant can use biomass boilers to produce steam for industrial processes.
Hydropower:
- Method: Harness energy from flowing water through small-scale hydroelectric systems.
- Benefit: Provides a consistent and renewable energy source with low operational costs.
- Example: Facilities located near rivers can install micro-hydro turbines to generate electricity for their operations.
Energy Storage Solutions:
- Method: Incorporate battery storage systems to store excess renewable energy for use during peak demand or when renewable sources are unavailable.
- Benefit: Enhances the reliability and consistency of renewable energy supply.
- Example: Large-scale lithium-ion batteries can store solar energy generated during the day for use at night.
Hybrid Energy Systems:
- Method: Combine multiple renewable energy sources (e.g., solar and wind) to create a more resilient and reliable energy supply.
- Benefit: Balances the variability of different renewable sources, ensuring a steady energy flow.
- Example: A manufacturing plant might use both solar panels and wind turbines to ensure continuous power generation.
On-site Renewable Energy Generation:
- Method: Develop renewable energy projects directly on manufacturing sites to tailor energy production to specific needs.
- Benefit: Maximizes energy efficiency and reduces transmission losses.
- Example: Integrating solar canopies over parking lots to generate electricity while providing shade for vehicles.
Renewable Energy Purchasing:
- Method: Purchase renewable energy credits (RECs) or enter into power purchase agreements (PPAs) with renewable energy providers.
- Benefit: Supports the development of renewable energy projects without the need for on-site installations.
- Example: A manufacturer can sign a PPA with a wind farm to supply a portion of its electricity needs.
Energy Management Systems:
- Method: Implement advanced energy management systems to optimize the use of renewable energy within manufacturing processes.
- Benefit: Enhances energy efficiency, reduces waste, and ensures optimal utilization of renewable sources.
- Example: Smart grids can dynamically allocate energy from renewable sources based on real-time demand and supply conditions.
Benefits of Integrating Renewable Energy:
- Environmental Sustainability: Reduces carbon footprint and reliance on non-renewable energy sources.
- Cost Savings: Lowers long-term energy costs and protects against volatile fossil fuel prices.
- Energy Security: Enhances energy independence and reduces vulnerability to supply disruptions.
- Regulatory Compliance: Helps meet environmental regulations and sustainability standards.
- Corporate Image: Enhances brand reputation as a responsible and eco-friendly manufacturer.
- Innovation and Competitiveness: Positions the company as a leader in sustainable practices, attracting environmentally conscious customers and partners.
Case Example: A large automotive manufacturer integrated solar power into its production facilities by installing photovoltaic panels on the rooftops of its plants. The solar installation provided 25% of the facility’s electricity needs, resulting in annual energy cost savings of $2 million and a reduction of 3,000 metric tons of CO2 emissions. Additionally, the company implemented energy storage systems to ensure a steady energy supply during cloudy days and nighttime operations. This integration not only enhanced the company’s sustainability profile but also provided a competitive advantage in the market by appealing to eco-conscious consumers.
Conclusion: Integrating renewable energy sources into manufacturing processes is a pivotal strategy for promoting sustainability. By adopting a combination of solar, wind, geothermal, biomass, and other renewable energy technologies, manufacturers can significantly reduce their environmental impact, achieve cost savings, and enhance their competitive position. Implementing these strategies requires careful planning, investment in appropriate technologies, and a commitment to continuous improvement in energy management.
5. What are the key principles of green supply chain management, and how do they contribute to sustainability?
Answer:
Key Principles of Green Supply Chain Management (GSCM):
Environmental Integration:
- Principle: Incorporate environmental considerations into all supply chain processes and decisions.
- Contribution to Sustainability: Ensures that environmental impacts are minimized throughout the entire supply chain, from sourcing to delivery.
Sustainable Sourcing:
- Principle: Choose suppliers that adhere to environmental and social standards.
- Contribution to Sustainability: Promotes the use of eco-friendly materials and ethical labor practices, reducing the overall environmental footprint.
Eco-Design:
- Principle: Design products with their entire lifecycle in mind, focusing on reducing environmental impact.
- Contribution to Sustainability: Facilitates easier recycling, reuse, and disposal, minimizing waste and resource consumption.
Waste Minimization:
- Principle: Implement strategies to reduce, reuse, and recycle waste generated during production and distribution.
- Contribution to Sustainability: Lowers the amount of waste sent to landfills and reduces the environmental impact of manufacturing processes.
Energy Efficiency:
- Principle: Optimize energy use across all supply chain activities.
- Contribution to Sustainability: Reduces greenhouse gas emissions and lowers operational costs through efficient energy management.
Reverse Logistics:
- Principle: Manage the return and disposal of products in an environmentally responsible manner.
- Contribution to Sustainability: Encourages recycling and proper disposal, reducing environmental pollution and promoting resource recovery.
Green Transportation:
- Principle: Optimize logistics and transportation to reduce emissions and energy consumption.
- Contribution to Sustainability: Minimizes the carbon footprint associated with moving goods, enhancing overall supply chain sustainability.
Supplier Collaboration:
- Principle: Work closely with suppliers to improve their environmental performance.
- Contribution to Sustainability: Enhances the sustainability of the entire supply chain through shared best practices and continuous improvement.
Lifecycle Assessment:
- Principle: Evaluate the environmental impact of products throughout their entire lifecycle.
- Contribution to Sustainability: Identifies areas for improvement and ensures that sustainability is considered from production to end-of-life.
Continuous Improvement:
- Principle: Commit to ongoing efforts to enhance environmental performance.
- Contribution to Sustainability: Drives innovation and ensures that the supply chain adapts to new sustainability challenges and opportunities.
Contribution of GSCM Principles to Sustainability:
- Reduced Environmental Impact: By integrating environmental considerations into all aspects of the supply chain, GSCM minimizes pollution, waste, and resource depletion.
- Cost Savings: Energy efficiency and waste reduction lead to lower operational costs, enhancing economic sustainability.
- Regulatory Compliance: Adhering to environmental standards and regulations prevents legal issues and fines, ensuring operational continuity.
- Enhanced Brand Reputation: Commitment to sustainability builds a positive brand image, attracting environmentally conscious consumers and partners.
- Innovation and Competitive Advantage: Sustainable practices encourage innovation in product design and processes, providing a competitive edge in the market.
- Resource Conservation: Efficient use of resources ensures their availability for future generations, promoting long-term sustainability.
Case Example: A global electronics company adopted green supply chain management principles by sourcing conflict-free minerals, implementing energy-efficient manufacturing processes, and optimizing its transportation routes to reduce emissions. They also established a robust reverse logistics system to manage product returns and recycling. As a result, the company reduced its carbon footprint by 20%, achieved significant cost savings through energy efficiency, and enhanced its reputation as a leader in sustainable electronics. These efforts not only contributed to environmental sustainability but also increased customer loyalty and opened new market opportunities focused on eco-friendly products.
Conclusion: Green Supply Chain Management is essential for achieving sustainability in manufacturing and other industries. By adhering to key principles such as environmental integration, sustainable sourcing, waste minimization, and energy efficiency, organizations can significantly reduce their environmental impact, achieve cost savings, comply with regulations, and enhance their competitive position. Implementing GSCM principles fosters a sustainable and responsible approach to supply chain management, ensuring long-term success and positive societal impact.
6. What are the benefits of implementing a circular economy model in manufacturing, and how can manufacturers transition to this model?
Answer:
Benefits of Implementing a Circular Economy Model in Manufacturing:
Resource Efficiency:
- Benefit: Maximizes the use of materials by reusing, recycling, and refurbishing products.
- Impact: Reduces the need for virgin raw materials, conserving natural resources and lowering production costs.
Waste Reduction:
- Benefit: Minimizes waste generation by designing products for longevity, repairability, and recyclability.
- Impact: Decreases landfill usage and environmental pollution, contributing to a cleaner ecosystem.
Cost Savings:
- Benefit: Lowers costs associated with material procurement, waste management, and disposal.
- Impact: Enhances profitability through reduced operational expenses and efficient resource utilization.
Innovation and Product Development:
- Benefit: Encourages the development of innovative products and processes that support reuse and recycling.
- Impact: Drives technological advancements and opens new market opportunities for sustainable products.
Enhanced Brand Reputation:
- Benefit: Demonstrates a commitment to sustainability and environmental responsibility.
- Impact: Attracts eco-conscious consumers, increases customer loyalty, and differentiates the brand in the marketplace.
Regulatory Compliance:
- Benefit: Helps manufacturers comply with environmental regulations and standards.
- Impact: Avoids legal penalties, ensures operational continuity, and fosters good relationships with regulatory bodies.
Risk Mitigation:
- Benefit: Reduces dependency on finite resources and mitigates risks associated with resource scarcity and price volatility.
- Impact: Enhances supply chain resilience and ensures long-term business sustainability.
Economic Growth:
- Benefit: Creates new business models and revenue streams through services like product-as-a-service, leasing, and remanufacturing.
- Impact: Contributes to economic growth while promoting sustainable consumption and production patterns.
Environmental Impact:
- Benefit: Lowers greenhouse gas emissions, reduces pollution, and conserves biodiversity by minimizing resource extraction and waste.
- Impact: Contributes to global sustainability goals and combats climate change.
How Manufacturers Can Transition to a Circular Economy Model:
Design for Longevity and Repairability:
- Action: Develop products that are durable, easy to repair, and upgradeable.
- Implementation: Use modular designs and standardized components to facilitate repairs and extensions of product life.
Implement Recycling and Reuse Programs:
- Action: Establish systems to collect, recycle, and reuse products at the end of their lifecycle.
- Implementation: Create take-back programs, partner with recycling facilities, and use recycled materials in new products.
Adopt Product-as-a-Service (PaaS) Models:
- Action: Shift from selling products to offering them as services, such as leasing or renting.
- Implementation: Develop subscription-based models where customers pay for the use of a product rather than owning it outright.
Collaborate with Supply Chain Partners:
- Action: Work closely with suppliers and partners to ensure sustainability throughout the supply chain.
- Implementation: Share sustainability goals, collaborate on material sourcing, and develop joint recycling initiatives.
Invest in Advanced Manufacturing Technologies:
- Action: Utilize technologies that support circular practices, such as additive manufacturing and automation.
- Implementation: Implement 3D printing for on-demand production, reducing waste and enabling customization.
Redefine Business Models:
- Action: Transition to business models that emphasize sustainability and resource efficiency.
- Implementation: Incorporate circular principles into the core business strategy, aligning operations with circular economy goals.
Educate and Engage Consumers:
- Action: Raise awareness about the benefits of circular products and encourage sustainable consumer behavior.
- Implementation: Provide information on product care, recycling options, and the environmental benefits of circular practices.
Measure and Report Sustainability Metrics:
- Action: Track progress towards circular economy goals using specific metrics and KPIs.
- Implementation: Use lifecycle assessment tools and sustainability reporting frameworks to monitor and communicate achievements.
Foster a Culture of Innovation:
- Action: Encourage continuous improvement and innovation focused on sustainability.
- Implementation: Support research and development initiatives that explore new materials, processes, and business models aligned with circular principles.
Leverage Policy and Incentives:
- Action: Take advantage of government policies, incentives, and subsidies that support circular economy initiatives.
- Implementation: Align business practices with regulatory frameworks and seek funding opportunities for sustainable projects.
Case Example: A leading furniture manufacturer transitioned to a circular economy model by redesigning its products for easy disassembly and recycling. They introduced a take-back program where customers could return old furniture for refurbishment or recycling. The company also partnered with suppliers to use recycled materials in new products and adopted a leasing model for office furniture, allowing businesses to upgrade their furnishings without disposing of old items. As a result, the manufacturer reduced material costs by 15%, decreased waste by 30%, and enhanced its brand reputation as a sustainable and responsible company.
Conclusion: Implementing a circular economy model offers significant benefits for manufacturers, including cost savings, enhanced sustainability, and competitive advantage. Transitioning to this model requires strategic planning, collaboration with supply chain partners, investment in sustainable technologies, and a commitment to continuous innovation. By embracing circular principles, manufacturers can create a more sustainable and resilient business, contributing positively to the environment and society.
7. What are the main challenges faced by manufacturers in adopting sustainable manufacturing practices, and how can they overcome them?
Answer:
Main Challenges in Adopting Sustainable Manufacturing Practices:
High Initial Costs:
- Challenge: Implementing sustainable practices often requires significant upfront investments in new technologies, equipment, and training.
- Solution: Seek financial incentives, grants, and subsidies from governments and organizations that support sustainability initiatives. Additionally, adopt a phased implementation approach to spread out costs over time.
Lack of Awareness and Expertise:
- Challenge: Manufacturers may lack the necessary knowledge and expertise to implement sustainable practices effectively.
- Solution: Invest in training programs and hire sustainability experts to guide the transition. Engage with industry associations and participate in sustainability workshops and seminars.
Supply Chain Complexity:
- Challenge: Ensuring sustainability across a complex and global supply chain can be difficult due to varying standards and practices.
- Solution: Collaborate closely with suppliers to establish clear sustainability criteria and provide support for them to meet these standards. Use supply chain management software to monitor and manage sustainability metrics.
Resistance to Change:
- Challenge: Employees and management may resist adopting new sustainable practices due to fear of the unknown or reluctance to change established processes.
- Solution: Foster a culture of sustainability by communicating the benefits, involving employees in decision-making, and recognizing and rewarding sustainable initiatives.
Measurement and Reporting:
- Challenge: Tracking and measuring the impact of sustainable practices can be complex and resource-intensive.
- Solution: Implement robust data collection and management systems to monitor sustainability metrics. Use standardized reporting frameworks like the Global Reporting Initiative (GRI) to ensure consistency and transparency.
Balancing Sustainability with Profitability:
- Challenge: Manufacturers may struggle to balance the costs of sustainable practices with the need to maintain profitability.
- Solution: Identify areas where sustainability can lead to cost savings, such as energy efficiency and waste reduction. Demonstrate the long-term financial benefits of sustainability to stakeholders.
Technological Limitations:
- Challenge: Existing technologies may not support the desired level of sustainability, requiring upgrades or replacements.
- Solution: Invest in research and development to innovate new sustainable technologies. Partner with technology providers to integrate advanced solutions that enhance sustainability.
Regulatory Compliance:
- Challenge: Navigating and complying with diverse and evolving environmental regulations can be challenging.
- Solution: Stay informed about relevant regulations and work with legal experts to ensure compliance. Proactively adopt best practices that exceed regulatory requirements to stay ahead of changes.
Market Pressure and Consumer Expectations:
- Challenge: Meeting increasing consumer demand for sustainable products while maintaining product quality and affordability.
- Solution: Incorporate sustainable design principles to create high-quality, eco-friendly products. Educate consumers about the value of sustainable products to justify any premium pricing.
Integration with Existing Processes:
- Challenge: Integrating sustainable practices into existing manufacturing processes without disrupting operations can be difficult.
- Solution: Conduct thorough planning and pilot programs to test and refine sustainable practices before full-scale implementation. Use process mapping to identify integration points and minimize disruptions.
Strategies to Overcome Challenges:
Leadership Commitment:
- Strategy: Ensure that top management is committed to sustainability and actively supports sustainable initiatives.
- Benefit: Provides direction, resources, and motivation for the entire organization to embrace sustainability.
Stakeholder Engagement:
- Strategy: Involve all stakeholders, including employees, suppliers, customers, and investors, in sustainability efforts.
- Benefit: Builds a shared sense of responsibility and fosters collaboration towards common sustainability goals.
Continuous Improvement:
- Strategy: Adopt a mindset of continuous improvement to regularly assess and enhance sustainability practices.
- Benefit: Ensures that sustainability efforts evolve and adapt to new challenges and opportunities.
Innovation and Technology Adoption:
- Strategy: Embrace innovation and adopt advanced technologies that support sustainable manufacturing.
- Benefit: Enhances efficiency, reduces environmental impact, and creates new opportunities for sustainable growth.
Benchmarking and Best Practices:
- Strategy: Benchmark against industry leaders and adopt best practices in sustainability.
- Benefit: Provides valuable insights and proven strategies to enhance sustainability performance.
Case Example: A mid-sized manufacturing company aimed to implement sustainable practices but faced challenges related to high initial costs and resistance to change among employees. To overcome these challenges, the company secured a government grant to fund energy-efficient equipment upgrades, reducing the financial burden. They also launched an employee engagement program that included training sessions and incentives for sustainable initiatives. By demonstrating the cost savings from reduced energy consumption and involving employees in the sustainability journey, the company successfully integrated sustainable practices, resulting in a 20% reduction in energy usage and improved employee morale.
Conclusion: Adopting sustainable manufacturing practices presents several challenges, including high costs, supply chain complexity, and resistance to change. However, by implementing strategic solutions such as securing financial support, fostering a culture of sustainability, leveraging technology, and engaging stakeholders, manufacturers can overcome these obstacles. Embracing sustainability not only benefits the environment but also enhances operational efficiency, reduces costs, and builds a competitive advantage in the market.
8. How can life cycle assessment (LCA) be utilized to improve sustainability in manufacturing processes?
Answer:
Life Cycle Assessment (LCA) in Sustainable Manufacturing:
Definition of Life Cycle Assessment (LCA): LCA is a systematic methodology used to evaluate the environmental impacts of a product or service throughout its entire life cycle, from raw material extraction and production to use, disposal, and recycling. It provides a comprehensive view of the environmental aspects associated with a product, enabling manufacturers to make informed decisions to enhance sustainability.
How LCA Improves Sustainability in Manufacturing Processes:
Identifying Environmental Hotspots:
- Usage: LCA helps pinpoint stages in the product lifecycle that have the highest environmental impacts, such as energy consumption, emissions, or resource use.
- Improvement: Allows manufacturers to target these hotspots for improvement, optimizing processes to reduce environmental burdens.
Informed Decision-Making:
- Usage: Provides data-driven insights into the environmental performance of different materials, processes, and technologies.
- Improvement: Facilitates the selection of more sustainable options, such as choosing eco-friendly materials or adopting energy-efficient technologies.
Product Design Optimization:
- Usage: Assesses the environmental implications of design choices, including materials, manufacturing methods, and product durability.
- Improvement: Enables the design of products that are easier to recycle, use fewer resources, and have a lower overall environmental footprint.
Supply Chain Management:
- Usage: Evaluates the environmental impact of suppliers and their processes.
- Improvement: Encourages collaboration with suppliers to improve their sustainability practices, ensuring a greener supply chain.
Regulatory Compliance and Reporting:
- Usage: Assists in meeting environmental regulations and standards by providing comprehensive environmental data.
- Improvement: Simplifies compliance reporting and helps avoid legal penalties by ensuring that products meet regulatory requirements.
Benchmarking and Performance Tracking:
- Usage: Allows manufacturers to benchmark their products against industry standards or competitors.
- Improvement: Facilitates the tracking of sustainability performance over time, promoting continuous improvement.
Cost Reduction:
- Usage: Identifies areas where resource use can be minimized, such as reducing material waste or lowering energy consumption.
- Improvement: Leads to cost savings by optimizing resource use and reducing waste disposal expenses.
Enhancing Brand Reputation:
- Usage: Demonstrates a commitment to sustainability through transparent reporting of environmental impacts.
- Improvement: Builds trust with consumers, investors, and other stakeholders, enhancing the company’s reputation and market position.
Steps to Conduct a Life Cycle Assessment:
Goal and Scope Definition:
- Action: Define the purpose of the LCA, the boundaries of the assessment, and the functional unit (e.g., per unit of product).
- Benefit: Ensures that the LCA is focused and relevant to the specific sustainability objectives.
Inventory Analysis:
- Action: Collect data on all inputs and outputs associated with each stage of the product lifecycle, including energy use, materials, emissions, and waste.
- Benefit: Provides a comprehensive dataset for evaluating environmental impacts.
Impact Assessment:
- Action: Analyze the inventory data to assess potential environmental impacts, such as global warming potential, acidification, eutrophication, and resource depletion.
- Benefit: Quantifies the environmental effects of the product, highlighting areas for improvement.
Interpretation:
- Action: Analyze the results, draw conclusions, and make recommendations for enhancing sustainability.
- Benefit: Translates the LCA findings into actionable strategies for reducing environmental impacts.
Case Example: A beverage manufacturer conducted an LCA for its bottled water product. The assessment revealed that the majority of environmental impacts occurred during the packaging stage due to plastic production and transportation. Based on these insights, the company switched to lightweight, recyclable bottles and optimized its transportation routes to reduce emissions. As a result, the LCA showed a 25% reduction in the product’s overall carbon footprint, enhancing the company’s sustainability profile and reducing costs associated with materials and logistics.
Conclusion: Life Cycle Assessment is a powerful tool for improving sustainability in manufacturing by providing a holistic view of a product’s environmental impacts. By identifying key areas for improvement, informing sustainable design and procurement decisions, and supporting regulatory compliance, LCA enables manufacturers to enhance their environmental performance, reduce costs, and build a strong reputation for sustainability.
9. What are the advantages of using eco-friendly materials in manufacturing, and how can manufacturers source these materials effectively?
Answer:
Advantages of Using Eco-Friendly Materials in Manufacturing:
Environmental Protection:
- Advantage: Eco-friendly materials reduce environmental impact by minimizing pollution, conserving natural resources, and lowering carbon emissions.
- Impact: Helps preserve ecosystems, reduce waste, and combat climate change.
Regulatory Compliance:
- Advantage: Using sustainable materials ensures compliance with environmental regulations and standards.
- Impact: Avoids legal penalties, fines, and operational disruptions caused by non-compliance.
Cost Savings:
- Advantage: Many eco-friendly materials, such as recycled or renewable resources, can be cost-effective in the long run.
- Impact: Reduces material costs and waste disposal expenses, enhancing overall profitability.
Market Demand and Competitive Advantage:
- Advantage: Increasing consumer preference for sustainable and ethically produced products drives demand for eco-friendly materials.
- Impact: Enhances brand reputation, attracts environmentally conscious customers, and differentiates products in the marketplace.
Innovation and Product Differentiation:
- Advantage: Incorporating eco-friendly materials fosters innovation in product design and functionality.
- Impact: Leads to the development of unique and high-value products that stand out in the market.
Resource Efficiency:
- Advantage: Eco-friendly materials often require less energy and fewer resources to produce and process.
- Impact: Increases overall manufacturing efficiency and reduces the environmental footprint of production processes.
Long-Term Sustainability:
- Advantage: Sustainable materials ensure the availability of resources for future generations.
- Impact: Promotes the long-term viability of manufacturing operations and supports global sustainability goals.
Enhanced Corporate Image:
- Advantage: Commitment to sustainability through the use of eco-friendly materials improves corporate social responsibility (CSR) credentials.
- Impact: Builds trust with stakeholders, including customers, investors, and employees, fostering loyalty and support.
How Manufacturers Can Source Eco-Friendly Materials Effectively:
Supplier Assessment and Selection:
- Action: Evaluate suppliers based on their sustainability practices, certifications, and environmental performance.
- Implementation: Use criteria such as ISO 14001 certification, fair trade practices, and the use of renewable or recycled materials.
Building Strong Supplier Relationships:
- Action: Collaborate closely with suppliers to ensure the consistent supply of eco-friendly materials.
- Implementation: Establish long-term partnerships, provide support for suppliers to improve their sustainability practices, and engage in joint sustainability initiatives.
Sustainable Procurement Policies:
- Action: Develop and implement procurement policies that prioritize the purchase of eco-friendly materials.
- Implementation: Include sustainability criteria in procurement guidelines, requiring the use of environmentally responsible materials.
Utilizing Certification Programs:
- Action: Source materials from suppliers that are certified by recognized sustainability standards.
- Implementation: Look for certifications such as Forest Stewardship Council (FSC), Global Organic Textile Standard (GOTS), and Cradle to Cradle (C2C).
Diversifying Material Sources:
- Action: Identify and engage with multiple suppliers of eco-friendly materials to ensure a reliable and resilient supply chain.
- Implementation: Avoid dependency on a single supplier by sourcing from various regions and suppliers committed to sustainability.
Investment in Research and Development:
- Action: Invest in R&D to identify and develop new eco-friendly materials that meet product requirements.
- Implementation: Collaborate with research institutions, industry consortia, and material innovators to explore sustainable alternatives.
Lifecycle Cost Analysis:
- Action: Conduct lifecycle cost analyses to assess the long-term financial benefits of using eco-friendly materials.
- Implementation: Compare the total cost of ownership, including material costs, energy use, and waste disposal, between conventional and sustainable materials.
Supply Chain Transparency:
- Action: Enhance visibility into the supply chain to ensure the traceability and authenticity of eco-friendly materials.
- Implementation: Utilize technologies like blockchain and supply chain management software to track material origins and certifications.
Education and Training:
- Action: Educate procurement teams and other relevant staff about the benefits and sourcing of eco-friendly materials.
- Implementation: Provide training programs and resources to build expertise in sustainable procurement practices.
Continuous Monitoring and Improvement:
- Action: Regularly monitor the performance of eco-friendly materials and suppliers to ensure ongoing compliance and improvement.
- Implementation: Use sustainability metrics and audits to assess material performance and supplier adherence to sustainability standards.
Case Example: A sustainable fashion brand sought to use eco-friendly fabrics to reduce its environmental impact. The company implemented a sustainable procurement policy that prioritized suppliers with organic cotton and recycled polyester certifications. They built strong relationships with these suppliers, providing support to improve their sustainability practices. By conducting lifecycle cost analyses, the company identified cost savings through reduced waste and energy use. Additionally, they utilized blockchain technology to ensure the traceability of materials from farm to factory. This approach not only enhanced the brand’s sustainability credentials but also attracted a loyal customer base seeking environmentally responsible products.
Conclusion: Using eco-friendly materials offers numerous advantages, including environmental protection, cost savings, and enhanced market competitiveness. By adopting effective sourcing strategies such as supplier assessment, sustainable procurement policies, certification utilization, and supply chain transparency, manufacturers can successfully integrate eco-friendly materials into their production processes. This transition not only supports sustainability goals but also drives long-term business success and positive societal impact.
10. How can automation and smart technologies enhance sustainable manufacturing practices?
Answer:
Enhancing Sustainable Manufacturing with Automation and Smart Technologies:
1. Energy Management:
- Enhancement: Automation systems can monitor and control energy usage in real-time.
- Benefit: Optimizes energy consumption, reduces waste, and lowers greenhouse gas emissions by ensuring machines operate only when necessary and at optimal efficiency.
2. Waste Reduction:
- Enhancement: Smart technologies can identify and minimize waste generation through precise control and monitoring of manufacturing processes.
- Benefit: Reduces material waste, lowers disposal costs, and minimizes environmental impact by ensuring efficient use of resources.
3. Precision Manufacturing:
- Enhancement: Automation enables high-precision manufacturing, ensuring consistent product quality and reducing defects.
- Benefit: Decreases the need for rework and waste, leading to more sustainable production practices and resource conservation.
4. Predictive Maintenance:
- Enhancement: Smart sensors and AI algorithms predict equipment failures before they occur.
- Benefit: Minimizes downtime, extends the lifespan of machinery, and reduces the need for premature replacements, contributing to resource efficiency and cost savings.
5. Supply Chain Optimization:
- Enhancement: Automation and smart technologies enhance supply chain visibility and coordination.
- Benefit: Reduces transportation-related emissions by optimizing routes, improving inventory management to prevent overproduction, and ensuring timely deliveries.
6. Sustainable Product Design:
- Enhancement: Smart design tools use data analytics to create products that are easier to recycle and have a lower environmental footprint.
- Benefit: Facilitates the development of eco-friendly products that align with circular economy principles, enhancing sustainability throughout the product lifecycle.
7. Resource Tracking and Traceability:
- Enhancement: Automation systems track the flow of materials and products throughout the manufacturing process.
- Benefit: Ensures responsible sourcing, enhances transparency, and supports compliance with sustainability standards by providing detailed records of material origins and usage.
8. Reduced Water Usage:
- Enhancement: Automated systems monitor and control water usage in manufacturing processes.
- Benefit: Minimizes water waste, ensures efficient usage, and reduces the environmental impact of water consumption.
9. Enhanced Worker Safety and Well-being:
- Enhancement: Automation takes over hazardous tasks, reducing the risk of workplace accidents.
- Benefit: Promotes a safer work environment, improving worker health and satisfaction, which is a key aspect of social sustainability.
10. Data-Driven Sustainability Initiatives: – Enhancement: Smart technologies collect and analyze vast amounts of data on manufacturing processes and environmental impacts. – Benefit: Provides actionable insights to continuously improve sustainability practices, set measurable goals, and track progress towards environmental targets.
Case Example: A leading automotive manufacturer integrated automation and smart technologies into its production line to enhance sustainability. They implemented automated energy management systems that adjusted energy use based on real-time production needs, resulting in a 15% reduction in energy consumption. Smart sensors monitored material usage and waste generation, enabling the company to identify and eliminate inefficiencies, reducing waste by 20%. Additionally, predictive maintenance systems extended the lifespan of machinery, lowering the need for new equipment and minimizing resource consumption. These initiatives not only improved the company’s environmental performance but also reduced operational costs and enhanced product quality.
Conclusion: Automation and smart technologies play a pivotal role in advancing sustainable manufacturing practices by enhancing energy efficiency, reducing waste, improving precision, and enabling data-driven decision-making. By integrating these technologies, manufacturers can achieve significant environmental, economic, and social benefits, fostering a more sustainable and resilient manufacturing ecosystem. Embracing automation and smart technologies is essential for manufacturers committed to sustainability and long-term operational excellence.
11. What strategies can manufacturers employ to ensure the longevity and recyclability of their products?
Answer:
Strategies to Ensure Longevity and Recyclability of Products:
Design for Durability:
- Strategy: Create products that are built to last, using high-quality materials and robust construction.
- Benefit: Extends the product’s usable life, reducing the frequency of replacements and minimizing waste generation.
Modular Design:
- Strategy: Design products with interchangeable and replaceable components.
- Benefit: Facilitates easy repairs, upgrades, and part replacements, enhancing product longevity and reducing the need for complete product disposal.
Standardization of Components:
- Strategy: Use standardized parts across different products.
- Benefit: Simplifies repairs and recycling processes by allowing interchangeable components, reducing complexity and costs.
Material Selection:
- Strategy: Choose materials that are easily recyclable and have a low environmental impact.
- Benefit: Enhances the recyclability of products and supports the use of sustainable materials, contributing to a circular economy.
Simplified Product Design:
- Strategy: Minimize the number of materials and components used in product design.
- Benefit: Makes disassembly and recycling easier, reducing the environmental footprint and improving resource efficiency.
Eco-Design Principles:
- Strategy: Incorporate eco-design principles that consider the entire lifecycle of the product.
- Benefit: Ensures that products are designed for easy recycling, reduced energy consumption during use, and minimal environmental impact at end-of-life.
Recycling Programs:
- Strategy: Establish take-back and recycling programs to collect used products.
- Benefit: Facilitates the proper recycling and disposal of products, ensuring that materials are recovered and reused, reducing waste and resource extraction.
Use of Recycled Materials:
- Strategy: Integrate recycled materials into new product designs.
- Benefit: Promotes the reuse of materials, lowers the demand for virgin resources, and reduces the environmental impact of manufacturing.
Lifecycle Assessment (LCA):
- Strategy: Conduct LCAs to evaluate the environmental impact of products throughout their lifecycle.
- Benefit: Identifies opportunities for improving product sustainability, enhancing recyclability, and increasing product longevity.
Consumer Education and Engagement:
- Strategy: Educate consumers on the importance of product care, maintenance, and recycling.
- Benefit: Encourages responsible usage and disposal, extending product life and ensuring proper recycling practices.
Collaborative Partnerships:
- Strategy: Partner with recycling companies and other stakeholders to develop effective recycling systems.
- Benefit: Enhances the efficiency and effectiveness of recycling processes, ensuring that materials are recovered and reused appropriately.
Innovation in Recycling Technologies:
- Strategy: Invest in research and development of advanced recycling technologies.
- Benefit: Improves the efficiency and quality of recycling processes, enabling the recovery of a wider range of materials and reducing environmental impact.
Benefits of Ensuring Longevity and Recyclability:
- Environmental Sustainability: Reduces waste, conserves natural resources, and minimizes pollution.
- Cost Savings: Lowers costs associated with raw material procurement and waste management.
- Regulatory Compliance: Meets environmental regulations and standards, avoiding legal penalties.
- Market Advantage: Appeals to environmentally conscious consumers, enhancing brand reputation and competitiveness.
- Innovation: Drives the development of new materials and designs that support sustainability goals.
Case Example: A smartphone manufacturer adopted a modular design approach, allowing users to easily replace components such as batteries, screens, and cameras. This design strategy extended the product’s lifespan, as consumers could upgrade specific parts without purchasing a new device. Additionally, the company established a take-back program where old smartphones were collected, disassembled, and recycled. Recycled materials were then used in the production of new smartphones, reducing the need for virgin resources and minimizing electronic waste. These initiatives resulted in a 25% increase in product longevity, a significant reduction in waste, and enhanced customer satisfaction due to the ease of repairs and upgrades.
Conclusion: Ensuring the longevity and recyclability of products is essential for sustainable manufacturing. By implementing strategies such as designing for durability, using recyclable materials, establishing recycling programs, and engaging consumers, manufacturers can significantly reduce their environmental impact, lower costs, and enhance their market competitiveness. These practices not only support sustainability goals but also contribute to the development of a circular economy, ensuring the responsible use of resources and the long-term viability of manufacturing operations.
12. How can manufacturers measure the success of their sustainable manufacturing initiatives?
Answer:
Measuring the Success of Sustainable Manufacturing Initiatives:
Key Performance Indicators (KPIs):
- Description: Establish specific, measurable KPIs to track progress towards sustainability goals.
- Examples: Energy consumption per unit produced, carbon footprint, waste generation, water usage, and percentage of recycled materials used.
- Benefit: Provides clear metrics to evaluate the effectiveness of sustainability initiatives and identify areas for improvement.
Lifecycle Assessment (LCA):
- Description: Conduct LCAs to assess the environmental impact of products throughout their lifecycle.
- Benefit: Offers a comprehensive view of sustainability performance, highlighting areas where environmental impacts can be reduced.
Carbon Footprint Analysis:
- Description: Measure the total greenhouse gas emissions produced by manufacturing operations.
- Benefit: Tracks progress in reducing emissions and helps set targets for further reductions.
Energy Audits:
- Description: Perform regular energy audits to evaluate energy efficiency and identify opportunities for improvement.
- Benefit: Ensures that energy-saving measures are effective and contributes to cost savings and emission reductions.
Waste Audits:
- Description: Analyze waste streams to quantify the amount of waste generated and the effectiveness of waste reduction strategies.
- Benefit: Measures the success of waste minimization initiatives and guides future waste management efforts.
Water Usage Metrics:
- Description: Track water consumption in manufacturing processes and identify areas for conservation.
- Benefit: Promotes efficient water use and reduces the environmental impact of water consumption.
Sustainability Reporting:
- Description: Publish regular sustainability reports that detail progress towards sustainability goals and initiatives.
- Benefit: Enhances transparency, builds trust with stakeholders, and demonstrates commitment to sustainability.
ISO 14001 Certification:
- Description: Achieve and maintain ISO 14001 certification, which sets standards for environmental management systems.
- Benefit: Validates the effectiveness of sustainability practices and provides a framework for continuous improvement.
Supplier Sustainability Assessments:
- Description: Evaluate the sustainability performance of suppliers through audits and assessments.
- Benefit: Ensures that the entire supply chain adheres to sustainability standards, enhancing overall supply chain sustainability.
Employee Engagement and Training:
- Description: Measure employee participation in sustainability programs and training sessions.
- Benefit: Gauges the effectiveness of internal sustainability initiatives and fosters a culture of sustainability within the organization.
Customer Feedback and Market Performance:
- Description: Collect feedback from customers regarding sustainable products and measure market performance.
- Benefit: Assesses the market acceptance and success of sustainable products, guiding future sustainability efforts.
Return on Investment (ROI):
- Description: Calculate the financial return from sustainability initiatives by comparing the costs of implementation with the savings and benefits achieved.
- Benefit: Demonstrates the economic viability of sustainability investments and justifies further investment in sustainable practices.
Steps to Effectively Measure Success:
Define Clear Objectives:
- Action: Set specific, measurable, achievable, relevant, and time-bound (SMART) sustainability goals.
- Benefit: Provides a clear direction and benchmarks for measuring progress.
Select Relevant Metrics:
- Action: Choose metrics that align with the defined sustainability objectives and are relevant to the manufacturing processes.
- Benefit: Ensures that the measurements accurately reflect the success of sustainability initiatives.
Implement Data Collection Systems:
- Action: Utilize software and technologies to collect and manage data related to sustainability metrics.
- Benefit: Facilitates accurate and efficient data tracking and analysis.
Regular Monitoring and Reporting:
- Action: Continuously monitor sustainability metrics and report progress regularly.
- Benefit: Enables timely adjustments to initiatives and ensures ongoing accountability.
Benchmarking:
- Action: Compare sustainability performance against industry standards and best practices.
- Benefit: Identifies areas where the organization excels and where improvement is needed.
Continuous Improvement:
- Action: Use the insights gained from measurements to refine and enhance sustainability initiatives.
- Benefit: Promotes a culture of continuous improvement and ensures sustained progress towards sustainability goals.
Case Example: A manufacturing company implemented several sustainable practices, including energy-efficient machinery, waste recycling programs, and water conservation measures. To measure the success of these initiatives, they established KPIs such as energy consumption per unit produced, percentage of waste recycled, and water usage per production cycle. They conducted regular energy and waste audits, achieved ISO 14001 certification, and published annual sustainability reports. The company saw a 20% reduction in energy consumption, a 30% increase in waste recycling, and a 15% decrease in water usage over three years. These measurements validated the effectiveness of their sustainable manufacturing practices and guided further improvements.
Conclusion: Measuring the success of sustainable manufacturing initiatives is essential for evaluating their effectiveness, demonstrating progress, and identifying areas for improvement. By establishing clear objectives, selecting relevant metrics, implementing robust data collection systems, and fostering a culture of continuous improvement, manufacturers can effectively track and enhance their sustainability performance. These measurements not only ensure environmental and social responsibility but also contribute to long-term economic success and competitive advantage.
13. How can manufacturers leverage Industry 4.0 technologies to enhance sustainable manufacturing practices?
Answer:
Leveraging Industry 4.0 Technologies for Sustainable Manufacturing:
1. Internet of Things (IoT):
- Usage: Deploy sensors and connected devices to monitor and optimize manufacturing processes in real-time.
- Benefit: Enhances energy efficiency, reduces waste, and improves resource management by providing accurate data on equipment performance and environmental conditions.
- Example: IoT-enabled machines can adjust their operations based on real-time energy consumption data to minimize energy use.
2. Artificial Intelligence (AI) and Machine Learning:
- Usage: Utilize AI and machine learning algorithms to analyze data and optimize manufacturing operations.
- Benefit: Improves predictive maintenance, reduces downtime, enhances process efficiency, and minimizes resource consumption by anticipating equipment failures and optimizing production schedules.
- Example: AI can predict when machinery needs maintenance, preventing unexpected breakdowns and reducing energy waste.
3. Big Data Analytics:
- Usage: Analyze large volumes of data generated from manufacturing processes to identify patterns and trends.
- Benefit: Enables data-driven decision-making, improves process optimization, and supports sustainability initiatives by identifying areas for efficiency improvements.
- Example: Analyzing production data to identify and eliminate inefficiencies that lead to excess energy use or material waste.
4. Additive Manufacturing (3D Printing):
- Usage: Implement 3D printing for prototyping and production to reduce material waste and enable on-demand manufacturing.
- Benefit: Minimizes material usage, reduces transportation emissions, and allows for the creation of complex, lightweight structures that enhance product sustainability.
- Example: Using 3D printing to produce custom parts as needed, reducing inventory and waste associated with overproduction.
5. Advanced Robotics and Automation:
- Usage: Integrate advanced robotics to perform precision tasks and automate repetitive processes.
- Benefit: Increases operational efficiency, reduces human error, and optimizes resource use, contributing to lower energy consumption and waste generation.
- Example: Automated systems can optimize material handling and reduce the need for manual intervention, minimizing waste and improving safety.
6. Digital Twins:
- Usage: Create virtual replicas of manufacturing processes, products, or systems for simulation and optimization.
- Benefit: Allows for the testing of sustainability initiatives in a virtual environment, identifying potential improvements before implementing them in the real world.
- Example: Simulating energy usage in a production line to identify and implement energy-saving measures.
7. Blockchain Technology:
- Usage: Utilize blockchain for supply chain transparency and traceability.
- Benefit: Ensures the responsible sourcing of materials, verifies sustainability claims, and reduces fraud, enhancing the overall sustainability of the supply chain.
- Example: Tracking the origin and journey of raw materials to ensure they are sourced sustainably and ethically.
8. Cloud Computing:
- Usage: Employ cloud-based platforms for data storage, processing, and collaboration.
- Benefit: Enhances accessibility and scalability of sustainability data, supports real-time monitoring, and facilitates collaborative sustainability efforts across global operations.
- Example: Using cloud-based dashboards to monitor energy consumption and sustainability metrics in real-time from any location.
9. Virtual and Augmented Reality (VR/AR):
- Usage: Implement VR and AR for training, maintenance, and process optimization.
- Benefit: Improves efficiency and reduces errors by providing immersive training and real-time guidance, enhancing the sustainability of manufacturing operations.
- Example: AR-assisted maintenance can guide technicians to perform repairs more accurately, reducing downtime and resource use.
10. Smart Manufacturing Platforms: – Usage: Integrate comprehensive smart manufacturing platforms that connect various Industry 4.0 technologies. – Benefit: Enables seamless data flow, enhances process coordination, and supports holistic sustainability strategies by providing a unified view of manufacturing operations. – Example: A smart manufacturing platform can integrate IoT sensors, AI analytics, and automation systems to optimize production in real-time for sustainability.
Benefits of Leveraging Industry 4.0 Technologies for Sustainability:
- Enhanced Efficiency: Optimizes resource use, reduces energy consumption, and minimizes waste generation.
- Real-Time Monitoring: Provides immediate insights into environmental performance, enabling swift corrective actions.
- Predictive Capabilities: Anticipates and prevents potential issues that could lead to inefficiencies or environmental harm.
- Data-Driven Decisions: Facilitates informed decision-making based on comprehensive data analysis.
- Improved Product Lifecycle Management: Enhances the design, production, and end-of-life management of products to ensure sustainability.
- Greater Supply Chain Transparency: Ensures responsible sourcing and reduces environmental impacts across the supply chain.
- Innovation and Continuous Improvement: Drives the development of new sustainable practices and technologies, fostering a culture of innovation.
Case Example: A smart electronics manufacturer integrated IoT sensors and AI analytics into its production line to monitor energy usage and material flow in real-time. The data collected was analyzed to identify inefficiencies and optimize operations, resulting in a 20% reduction in energy consumption and a 15% decrease in material waste. Additionally, the company implemented a digital twin of its manufacturing process to simulate and test sustainability initiatives before real-world implementation. This approach not only enhanced the company’s sustainability performance but also reduced operational costs and improved product quality.
Conclusion: Industry 4.0 technologies offer powerful tools for enhancing sustainable manufacturing practices. By leveraging IoT, AI, big data, additive manufacturing, robotics, and other advanced technologies, manufacturers can significantly improve their environmental performance, optimize resource use, and drive continuous innovation. Integrating these technologies into manufacturing operations is essential for achieving sustainability goals, reducing environmental impact, and maintaining a competitive edge in the modern industrial landscape.
14. How can manufacturers balance the trade-offs between sustainability and cost in their operations?
Answer:
Balancing Sustainability and Cost in Manufacturing Operations:
1. Conduct Cost-Benefit Analyses:
- Action: Evaluate the financial implications of sustainability initiatives by comparing the costs of implementation with the long-term benefits.
- Benefit: Identifies initiatives that offer a favorable return on investment (ROI), ensuring that sustainability efforts are economically viable.
2. Prioritize High-Impact Initiatives:
- Action: Focus on sustainability projects that provide significant environmental benefits while offering cost savings, such as energy efficiency and waste reduction.
- Benefit: Maximizes the positive impact on sustainability without incurring excessive costs.
3. Implement Lean Manufacturing Principles:
- Action: Adopt lean practices to eliminate waste, improve process efficiency, and reduce costs.
- Benefit: Enhances both sustainability and profitability by optimizing resource use and minimizing waste.
4. Invest in Energy-Efficient Technologies:
- Action: Upgrade to energy-efficient machinery and systems to lower energy consumption.
- Benefit: Reduces long-term energy costs and decreases the environmental footprint, leading to both financial and sustainability gains.
5. Utilize Renewable Energy Sources:
- Action: Incorporate renewable energy sources such as solar and wind power into manufacturing operations.
- Benefit: Lowers energy costs over time and reduces reliance on fossil fuels, contributing to sustainability goals.
6. Optimize Supply Chain Management:
- Action: Streamline supply chain processes to reduce transportation costs and minimize environmental impact.
- Benefit: Achieves cost savings and enhances sustainability through efficient logistics and reduced emissions.
7. Foster Supplier Collaboration:
- Action: Work closely with suppliers to implement sustainable practices that can lead to cost reductions, such as bulk purchasing of eco-friendly materials.
- Benefit: Creates a mutually beneficial relationship that supports both cost management and sustainability objectives.
8. Implement Circular Economy Practices:
- Action: Adopt circular economy models that focus on recycling, reusing, and refurbishing materials and products.
- Benefit: Reduces material costs, minimizes waste disposal expenses, and promotes sustainability through resource conservation.
9. Leverage Government Incentives and Grants:
- Action: Take advantage of government programs that offer financial incentives for implementing sustainable practices.
- Benefit: Lowers the initial cost burden of sustainability initiatives, making them more financially feasible.
10. Educate and Engage Employees: – Action: Train employees on sustainability practices and encourage their involvement in cost-saving initiatives. – Benefit: Enhances operational efficiency and fosters a culture of sustainability that drives continuous improvement.
11. Monitor and Optimize Resource Use: – Action: Use data analytics and monitoring tools to track resource consumption and identify areas for optimization. – Benefit: Ensures efficient use of resources, reducing costs and environmental impact simultaneously.
12. Incremental Implementation: – Action: Implement sustainability initiatives gradually rather than all at once. – Benefit: Spreads out costs over time and allows for adjustments based on financial performance and operational impact.
Strategies to Achieve Balance:
Integrated Sustainability Planning:
- Strategy: Incorporate sustainability goals into the overall business strategy and operational planning.
- Benefit: Ensures that sustainability and cost considerations are addressed together, aligning efforts towards common objectives.
Collaborative Decision-Making:
- Strategy: Involve cross-functional teams in decision-making to consider both sustainability and cost aspects.
- Benefit: Promotes a holistic approach to balancing sustainability with financial performance.
Continuous Improvement:
- Strategy: Adopt a mindset of continuous improvement to regularly assess and enhance sustainability practices.
- Benefit: Enables ongoing optimization of both sustainability and cost-efficiency measures.
Performance Tracking and Reporting:
- Strategy: Monitor the performance of sustainability initiatives and their financial impact.
- Benefit: Provides insights into the effectiveness of initiatives and guides future investments in sustainability.
Case Example: A manufacturing company aimed to reduce its carbon footprint while managing costs. They conducted a cost-benefit analysis of implementing energy-efficient lighting and machinery. The analysis showed that although the initial investment was significant, the long-term energy savings would offset the costs within five years. The company prioritized these high-impact initiatives and phased the implementation to manage expenses. Additionally, they optimized their supply chain to reduce transportation costs and emissions by consolidating shipments and choosing more efficient routes. As a result, the company achieved a 20% reduction in energy consumption, lowered operational costs by 15%, and significantly decreased its carbon emissions, successfully balancing sustainability with cost management.
Conclusion: Balancing sustainability and cost requires a strategic and integrated approach that prioritizes high-impact initiatives, leverages cost-saving opportunities, and fosters collaboration across the organization and supply chain. By conducting thorough analyses, adopting lean and circular practices, and continuously monitoring performance, manufacturers can achieve sustainable operations that are both environmentally responsible and economically viable. This balance not only supports long-term business success but also contributes to global sustainability goals.
Sustainable Manufacturing: Thought-Provoking Questions
1. What is sustainable manufacturing, and why is it essential in today’s industrial landscape?
Answer:
Definition of Sustainable Manufacturing: Sustainable manufacturing refers to the creation of products through processes that minimize negative environmental impacts, conserve energy and natural resources, are economically viable, and are socially responsible. It integrates environmentally friendly practices into every aspect of the manufacturing process, from design and production to distribution and disposal.
Importance in Today’s Industrial Landscape:
Environmental Protection:
- Impact: Reduces pollution, waste generation, and carbon emissions, thereby mitigating climate change and preserving ecosystems.
- Reason: Industrial activities are significant contributors to environmental degradation; sustainable practices help minimize this impact.
Resource Efficiency:
- Impact: Optimizes the use of materials and energy, reducing dependency on finite resources.
- Reason: Ensures long-term availability of essential resources and lowers operational costs.
Regulatory Compliance:
- Impact: Helps companies adhere to increasingly stringent environmental laws and regulations.
- Reason: Non-compliance can result in hefty fines, legal actions, and damage to reputation.
Market Demand:
- Impact: Meets the growing consumer preference for eco-friendly and ethically produced products.
- Reason: Enhances brand loyalty and opens new market opportunities.
Economic Benefits:
- Impact: Lowers costs through energy savings, waste reduction, and improved efficiency.
- Reason: Sustainable practices often lead to operational efficiencies and long-term profitability.
Social Responsibility:
- Impact: Promotes ethical labor practices and contributes positively to communities.
- Reason: Enhances corporate reputation and fosters a positive relationship with stakeholders.
Conclusion: Sustainable manufacturing is crucial for balancing economic growth with environmental stewardship and social responsibility. It ensures that industrial progress does not come at the expense of the planet or future generations, making it an essential strategy for modern businesses.
2. How can energy efficiency be achieved in sustainable manufacturing processes?
Answer:
Achieving Energy Efficiency in Sustainable Manufacturing:
Energy Audits:
- Action: Conduct comprehensive energy audits to identify areas of high energy consumption and inefficiencies.
- Benefit: Provides a clear understanding of where energy is used and where savings can be made.
Upgrade to Energy-Efficient Equipment:
- Action: Replace old machinery and equipment with energy-efficient models that consume less power.
- Benefit: Reduces energy consumption and operational costs while enhancing productivity.
Implementing Automation and Smart Controls:
- Action: Use automated systems and smart controls to optimize energy use in real-time.
- Benefit: Ensures machinery operates only when needed, reducing idle energy consumption.
Optimizing Manufacturing Processes:
- Action: Streamline production processes to eliminate unnecessary steps and reduce energy usage.
- Benefit: Enhances efficiency and minimizes energy waste.
Heat Recovery Systems:
- Action: Install systems to capture and reuse waste heat generated during manufacturing.
- Benefit: Provides additional energy for other processes, reducing overall energy demand.
Lighting Upgrades:
- Action: Switch to LED lighting and incorporate motion sensors to reduce lighting energy use.
- Benefit: Lowers electricity consumption and maintenance costs.
Insulation and Building Efficiency:
- Action: Improve insulation and optimize HVAC systems to maintain optimal temperatures with less energy.
- Benefit: Reduces the energy required for heating and cooling manufacturing facilities.
Employee Training and Awareness:
- Action: Educate employees on energy-saving practices and encourage their participation in energy efficiency initiatives.
- Benefit: Promotes a culture of sustainability and ensures collective effort towards energy conservation.
Renewable Energy Integration:
- Action: Incorporate renewable energy sources such as solar, wind, or biomass to power manufacturing operations.
- Benefit: Reduces reliance on fossil fuels and lowers greenhouse gas emissions.
Continuous Monitoring and Improvement:
- Action: Use energy management systems to continuously monitor energy use and identify opportunities for further improvements.
- Benefit: Ensures ongoing energy efficiency and adapts to changing operational needs.
Conclusion: Achieving energy efficiency in sustainable manufacturing involves a combination of technological upgrades, process optimization, and cultural shifts within the organization. By implementing these strategies, manufacturers can significantly reduce their energy consumption, lower costs, and contribute to environmental sustainability.
3. What role does waste reduction play in sustainable manufacturing, and what methods can be employed to achieve it?
Answer:
Role of Waste Reduction in Sustainable Manufacturing:
Environmental Impact:
- Role: Minimizes the amount of waste sent to landfills and reduces pollution.
- Impact: Helps preserve natural resources and lowers the carbon footprint of manufacturing activities.
Cost Savings:
- Role: Reduces costs associated with waste disposal and raw material consumption.
- Impact: Enhances profitability by lowering operational expenses.
Resource Efficiency:
- Role: Ensures that materials are used effectively, reducing the need for new raw materials.
- Impact: Promotes the sustainable use of resources and reduces dependency on finite supplies.
Regulatory Compliance:
- Role: Helps manufacturers comply with environmental regulations regarding waste management.
- Impact: Avoids fines, legal issues, and enhances corporate reputation.
Innovation and Competitive Advantage:
- Role: Encourages the development of innovative processes and products that generate less waste.
- Impact: Differentiates companies in the market and meets consumer demand for sustainable products.
Methods to Achieve Waste Reduction:
Lean Manufacturing:
- Method: Implement lean principles to eliminate non-value-adding activities and reduce waste.
- Benefit: Streamlines processes and enhances efficiency.
Recycling and Reusing Materials:
- Method: Establish systems to recycle waste materials and reuse them in the production process.
- Benefit: Reduces the need for new raw materials and minimizes waste disposal.
Process Optimization:
- Method: Analyze and improve manufacturing processes to reduce material waste.
- Benefit: Increases efficiency and lowers the generation of scrap and defective products.
Design for Sustainability:
- Method: Design products with minimal material use and consider their end-of-life disposal.
- Benefit: Reduces waste generation and facilitates easier recycling or reuse.
Employee Training and Engagement:
- Method: Educate employees on waste reduction techniques and involve them in sustainability initiatives.
- Benefit: Promotes a culture of waste minimization and continuous improvement.
Advanced Manufacturing Technologies:
- Method: Use technologies such as additive manufacturing (3D printing) to reduce material waste.
- Benefit: Enhances precision in production and minimizes excess material usage.
Waste Audits:
- Method: Conduct regular audits to identify sources of waste and areas for improvement.
- Benefit: Provides actionable insights to target waste reduction efforts effectively.
Supplier Collaboration:
- Method: Work with suppliers to minimize packaging waste and adopt sustainable materials.
- Benefit: Reduces waste generation upstream in the supply chain.
Closed-Loop Systems:
- Method: Implement closed-loop systems where waste from one process becomes input for another.
- Benefit: Maximizes resource utilization and minimizes overall waste.
Monitoring and Reporting:
- Method: Use waste tracking systems to monitor waste generation and set reduction targets.
- Benefit: Ensures accountability and tracks progress towards waste reduction goals.
Conclusion: Waste reduction is a fundamental aspect of sustainable manufacturing, contributing to environmental protection, cost savings, and resource efficiency. By employing a combination of lean principles, recycling, process optimization, and technological innovations, manufacturers can significantly reduce waste and enhance the sustainability of their operations.
4. How can renewable energy sources be integrated into manufacturing processes to promote sustainability?
Answer:
Integrating Renewable Energy Sources into Manufacturing Processes:
Solar Power Integration:
- Method: Install solar panels on manufacturing facilities to generate electricity.
- Benefit: Reduces reliance on fossil fuels, lowers energy costs, and decreases greenhouse gas emissions.
- Example: Factory rooftops equipped with photovoltaic panels can supply a significant portion of its energy needs.
Wind Energy Utilization:
- Method: Invest in wind turbines either on-site or through wind farms to generate power.
- Benefit: Provides a clean and renewable source of energy, particularly effective in regions with consistent wind patterns.
- Example: Offshore wind farms can supply large-scale energy to manufacturing plants located near coastal areas.
Geothermal Energy:
- Method: Utilize geothermal heat pumps for heating and cooling manufacturing facilities.
- Benefit: Offers a stable and efficient energy source with minimal environmental impact.
- Example: Geothermal systems can maintain optimal temperatures in factories, reducing energy consumption for HVAC systems.
Biomass Energy:
- Method: Use organic materials such as agricultural waste, wood chips, or dedicated energy crops to generate heat and power.
- Benefit: Converts waste into valuable energy, reducing landfill use and carbon emissions.
- Example: A manufacturing plant can use biomass boilers to produce steam for industrial processes.
Hydropower:
- Method: Harness energy from flowing water through small-scale hydroelectric systems.
- Benefit: Provides a consistent and renewable energy source with low operational costs.
- Example: Facilities located near rivers can install micro-hydro turbines to generate electricity for their operations.
Energy Storage Solutions:
- Method: Incorporate battery storage systems to store excess renewable energy for use during peak demand or when renewable sources are unavailable.
- Benefit: Enhances the reliability and consistency of renewable energy supply.
- Example: Large-scale lithium-ion batteries can store solar energy generated during the day for use at night.
Hybrid Energy Systems:
- Method: Combine multiple renewable energy sources (e.g., solar and wind) to create a more resilient and reliable energy supply.
- Benefit: Balances the variability of different renewable sources, ensuring a steady energy flow.
- Example: A manufacturing plant might use both solar panels and wind turbines to ensure continuous power generation.
On-site Renewable Energy Generation:
- Method: Develop renewable energy projects directly on manufacturing sites to tailor energy production to specific needs.
- Benefit: Maximizes energy efficiency and reduces transmission losses.
- Example: Integrating solar canopies over parking lots to generate electricity while providing shade for vehicles.
Renewable Energy Purchasing:
- Method: Purchase renewable energy credits (RECs) or enter into power purchase agreements (PPAs) with renewable energy providers.
- Benefit: Supports the development of renewable energy projects without the need for on-site installations.
- Example: A manufacturer can sign a PPA with a wind farm to supply a portion of its electricity needs.
Energy Management Systems:
- Method: Implement advanced energy management systems to optimize the use of renewable energy within manufacturing processes.
- Benefit: Enhances energy efficiency, reduces waste, and ensures optimal utilization of renewable sources.
- Example: Smart grids can dynamically allocate energy from renewable sources based on real-time demand and supply conditions.
Benefits of Integrating Renewable Energy:
- Environmental Sustainability: Reduces carbon footprint and reliance on non-renewable energy sources.
- Cost Savings: Lowers long-term energy costs and protects against volatile fossil fuel prices.
- Energy Security: Enhances energy independence and reduces vulnerability to supply disruptions.
- Regulatory Compliance: Helps meet environmental regulations and sustainability standards.
- Corporate Image: Enhances brand reputation as a responsible and eco-friendly manufacturer.
- Innovation and Competitiveness: Positions the company as a leader in sustainable practices, attracting environmentally conscious customers and partners.
Conclusion: Integrating renewable energy sources into manufacturing processes is a pivotal strategy for promoting sustainability. By adopting a combination of solar, wind, geothermal, biomass, and other renewable energy technologies, manufacturers can significantly reduce their environmental impact, achieve cost savings, and enhance their competitive position. Implementing these strategies requires careful planning, investment in appropriate technologies, and a commitment to continuous improvement in energy management.
5. What are the key principles of green supply chain management, and how do they contribute to sustainability?
Answer:
Key Principles of Green Supply Chain Management (GSCM):
Environmental Integration:
- Principle: Incorporate environmental considerations into all supply chain processes and decisions.
- Contribution to Sustainability: Ensures that environmental impacts are minimized throughout the entire supply chain, from sourcing to delivery.
Sustainable Sourcing:
- Principle: Choose suppliers that adhere to environmental and social standards.
- Contribution to Sustainability: Promotes the use of eco-friendly materials and ethical labor practices, reducing the overall environmental footprint.
Eco-Design:
- Principle: Design products with their entire lifecycle in mind, focusing on reducing environmental impact.
- Contribution to Sustainability: Facilitates easier recycling, reuse, and disposal, minimizing waste and resource consumption.
Waste Minimization:
- Principle: Implement strategies to reduce, reuse, and recycle waste generated during production and distribution.
- Contribution to Sustainability: Lowers the amount of waste sent to landfills and reduces the environmental impact of manufacturing processes.
Energy Efficiency:
- Principle: Optimize energy use across all supply chain activities.
- Contribution to Sustainability: Reduces greenhouse gas emissions and lowers operational costs through efficient energy management.
Reverse Logistics:
- Principle: Manage the return and disposal of products in an environmentally responsible manner.
- Contribution to Sustainability: Encourages recycling and proper disposal, reducing environmental pollution and promoting resource recovery.
Green Transportation:
- Principle: Optimize logistics and transportation to reduce emissions and energy consumption.
- Contribution to Sustainability: Minimizes the carbon footprint associated with moving goods, enhancing overall supply chain sustainability.
Supplier Collaboration:
- Principle: Work closely with suppliers to improve their environmental performance.
- Contribution to Sustainability: Enhances the sustainability of the entire supply chain through shared best practices and continuous improvement.
Lifecycle Assessment:
- Principle: Evaluate the environmental impact of products throughout their entire lifecycle.
- Contribution to Sustainability: Identifies areas for improvement and ensures that sustainability is considered from production to end-of-life.
Continuous Improvement:
- Principle: Commit to ongoing efforts to enhance environmental performance.
- Contribution to Sustainability: Drives innovation and ensures that the supply chain adapts to new sustainability challenges and opportunities.
Contribution of GSCM Principles to Sustainability:
- Reduced Environmental Impact: By integrating environmental considerations, GSCM minimizes pollution, waste, and resource depletion.
- Cost Savings: Energy efficiency and waste reduction lead to lower operational costs, enhancing economic sustainability.
- Regulatory Compliance: Adhering to environmental standards and regulations prevents legal issues and fines, ensuring operational continuity.
- Enhanced Brand Reputation: Commitment to sustainability builds a positive brand image, attracting environmentally conscious consumers and partners.
- Innovation and Competitive Advantage: Sustainable practices encourage innovation in product design and processes, providing a competitive edge in the market.
- Resource Conservation: Efficient use of resources ensures their availability for future generations, promoting long-term sustainability.
Conclusion: Green Supply Chain Management is essential for achieving sustainability in manufacturing and other industries. By adhering to key principles such as environmental integration, sustainable sourcing, waste minimization, and energy efficiency, organizations can significantly reduce their environmental impact, achieve cost savings, comply with regulations, and enhance their competitive position. Implementing GSCM principles fosters a sustainable and responsible approach to supply chain management, ensuring long-term success and positive societal impact.
6. What are the benefits of implementing a circular economy model in manufacturing, and how can manufacturers transition to this model?
Answer:
Benefits of Implementing a Circular Economy Model in Manufacturing:
Resource Efficiency:
- Benefit: Maximizes the use of materials by reusing, recycling, and refurbishing products.
- Impact: Reduces the need for virgin raw materials, conserving natural resources and lowering production costs.
Waste Reduction:
- Benefit: Minimizes waste generation by designing products for longevity, repairability, and recyclability.
- Impact: Decreases landfill usage and environmental pollution, contributing to a cleaner ecosystem.
Cost Savings:
- Benefit: Lowers costs associated with material procurement, waste management, and disposal.
- Impact: Enhances profitability through reduced operational expenses and efficient resource utilization.
Innovation and Product Development:
- Benefit: Encourages the development of innovative products and processes that support reuse and recycling.
- Impact: Drives technological advancements and opens new market opportunities for sustainable products.
Enhanced Brand Reputation:
- Benefit: Demonstrates a commitment to sustainability and environmental responsibility.
- Impact: Attracts eco-conscious consumers, increases customer loyalty, and differentiates the brand in the marketplace.
Regulatory Compliance:
- Benefit: Helps manufacturers comply with environmental regulations and standards.
- Impact: Avoids legal penalties, ensures operational continuity, and fosters good relationships with regulatory bodies.
Risk Mitigation:
- Benefit: Reduces dependency on finite resources and mitigates risks associated with resource scarcity and price volatility.
- Impact: Enhances supply chain resilience and ensures long-term business sustainability.
Economic Growth:
- Benefit: Creates new business models and revenue streams through services like product-as-a-service, leasing, and remanufacturing.
- Impact: Contributes to economic growth while promoting sustainable consumption and production patterns.
Environmental Impact:
- Benefit: Lowers greenhouse gas emissions, reduces pollution, and conserves biodiversity by minimizing resource extraction and waste.
- Impact: Contributes to global sustainability goals and combats climate change.
How Manufacturers Can Transition to a Circular Economy Model:
Design for Longevity and Repairability:
- Strategy: Develop products that are durable, easy to repair, and upgradeable.
- Benefit: Extends the product’s usable life, reducing the frequency of replacements and minimizing waste generation.
Implement Recycling and Reuse Programs:
- Strategy: Establish systems to collect, recycle, and reuse products at the end of their lifecycle.
- Benefit: Facilitates the proper recycling and disposal of products, ensuring that materials are recovered and reused, reducing waste and resource extraction.
Adopt Product-as-a-Service (PaaS) Models:
- Strategy: Shift from selling products to offering them as services, such as leasing or renting.
- Benefit: Encourages the return and reuse of products, reducing the need for new production and minimizing waste.
Collaborate with Supply Chain Partners:
- Strategy: Work closely with suppliers and partners to ensure sustainability throughout the supply chain.
- Benefit: Enhances the sustainability of the entire supply chain through shared best practices and continuous improvement.
Invest in Advanced Manufacturing Technologies:
- Strategy: Utilize technologies that support circular practices, such as additive manufacturing and automation.
- Benefit: Reduces material waste, enables on-demand production, and facilitates customization.
Redefine Business Models:
- Strategy: Transition to business models that emphasize sustainability and resource efficiency.
- Benefit: Aligns operations with circular economy goals, promoting long-term sustainability and profitability.
Educate and Engage Consumers:
- Strategy: Raise awareness about the benefits of circular products and encourage sustainable consumer behavior.
- Benefit: Increases consumer participation in circular initiatives, such as returning used products for recycling or refurbishment.
Measure and Report Sustainability Metrics:
- Strategy: Track progress towards circular economy goals using specific metrics and KPIs.
- Benefit: Ensures accountability and provides insights into the effectiveness of circular initiatives.
Foster a Culture of Innovation:
- Strategy: Encourage continuous improvement and innovation focused on sustainability.
- Benefit: Drives the development of new materials, processes, and business models that support the circular economy.
Leverage Policy and Incentives:
- Strategy: Take advantage of government policies, incentives, and subsidies that support circular economy initiatives.
- Benefit: Reduces the financial burden of transitioning to a circular model and accelerates the adoption of sustainable practices.
Case Example: A leading furniture manufacturer transitioned to a circular economy model by redesigning its products for easy disassembly and recycling. They introduced a take-back program where customers could return old furniture for refurbishment or recycling. The company also partnered with suppliers to use recycled materials in new products and adopted a leasing model for office furniture, allowing businesses to upgrade their furnishings without disposing of old items. As a result, the manufacturer reduced material costs by 15%, decreased waste by 30%, and enhanced its brand reputation as a sustainable and responsible company.
Conclusion: Implementing a circular economy model offers significant benefits for manufacturers, including cost savings, enhanced sustainability, and competitive advantage. Transitioning to this model requires strategic planning, collaboration with supply chain partners, investment in sustainable technologies, and a commitment to continuous innovation. By embracing circular principles, manufacturers can create a more sustainable and resilient business, contributing positively to the environment and society.
7. What are the main challenges faced by manufacturers in adopting sustainable manufacturing practices, and how can they overcome them?
Answer:
Main Challenges in Adopting Sustainable Manufacturing Practices:
High Initial Costs:
- Challenge: Implementing sustainable practices often requires significant upfront investments in new technologies, equipment, and training.
- Solution: Seek financial incentives, grants, and subsidies from governments and organizations that support sustainability initiatives. Additionally, adopt a phased implementation approach to spread out costs over time.
Lack of Awareness and Expertise:
- Challenge: Manufacturers may lack the necessary knowledge and expertise to implement sustainable practices effectively.
- Solution: Invest in training programs and hire sustainability experts to guide the transition. Engage with industry associations and participate in sustainability workshops and seminars.
Supply Chain Complexity:
- Challenge: Ensuring sustainability across a complex and global supply chain can be difficult due to varying standards and practices.
- Solution: Collaborate closely with suppliers to establish clear sustainability criteria and provide support for them to meet these standards. Use supply chain management software to monitor and manage sustainability metrics.
Resistance to Change:
- Challenge: Employees and management may resist adopting new sustainable practices due to fear of the unknown or reluctance to change established processes.
- Solution: Foster a culture of sustainability by communicating the benefits, involving employees in decision-making, and recognizing and rewarding sustainable initiatives.
Measurement and Reporting:
- Challenge: Tracking and measuring the impact of sustainable practices can be complex and resource-intensive.
- Solution: Implement robust data collection and management systems to monitor sustainability metrics. Use standardized reporting frameworks like the Global Reporting Initiative (GRI) to ensure consistency and transparency.
Balancing Sustainability with Profitability:
- Challenge: Manufacturers may struggle to balance the costs of sustainable practices with the need to maintain profitability.
- Solution: Identify areas where sustainability can lead to cost savings, such as energy efficiency and waste reduction. Demonstrate the long-term financial benefits of sustainability to stakeholders.
Technological Limitations:
- Challenge: Existing technologies may not support the desired level of sustainability, requiring upgrades or replacements.
- Solution: Invest in research and development to innovate new sustainable technologies. Partner with technology providers to integrate advanced solutions that enhance sustainability.
Regulatory Compliance:
- Challenge: Navigating and complying with diverse and evolving environmental regulations can be challenging.
- Solution: Stay informed about relevant regulations and work with legal experts to ensure compliance. Proactively adopt best practices that exceed regulatory requirements to stay ahead of changes.
Market Pressure and Consumer Expectations:
- Challenge: Meeting increasing consumer demand for sustainable products while maintaining product quality and affordability.
- Solution: Incorporate sustainable design principles to create high-quality, eco-friendly products. Educate consumers about the value of sustainable products to justify any premium pricing.
Integration with Existing Processes:
- Challenge: Integrating sustainable practices into existing manufacturing processes without disrupting operations can be difficult.
- Solution: Conduct thorough planning and pilot programs to test and refine sustainable practices before full-scale implementation. Use process mapping to identify integration points and minimize disruptions.
Strategies to Overcome Challenges:
Leadership Commitment:
- Strategy: Ensure that top management is committed to sustainability and actively supports sustainable initiatives.
- Benefit: Provides direction, resources, and motivation for the entire organization to embrace sustainability.
Stakeholder Engagement:
- Strategy: Involve all stakeholders, including employees, suppliers, customers, and investors, in sustainability efforts.
- Benefit: Builds a shared sense of responsibility and fosters collaboration towards common sustainability goals.
Continuous Improvement:
- Strategy: Adopt a mindset of continuous improvement to regularly assess and enhance sustainability practices.
- Benefit: Ensures that sustainability efforts evolve and adapt to new challenges and opportunities.
Innovation and Technology Adoption:
- Strategy: Embrace innovation and adopt advanced technologies that support sustainable manufacturing.
- Benefit: Enhances efficiency, reduces environmental impact, and creates new opportunities for sustainable growth.
Benchmarking and Best Practices:
- Strategy: Benchmark against industry leaders and adopt best practices in sustainability.
- Benefit: Provides valuable insights and proven strategies to enhance sustainability performance.
Case Example: A manufacturing company aimed to implement sustainable practices but faced challenges related to high initial costs and resistance to change among employees. To overcome these challenges, the company secured a government grant to fund energy-efficient equipment upgrades, reducing the financial burden. They also launched an employee engagement program that included training sessions and incentives for sustainable initiatives. By demonstrating the cost savings from reduced energy consumption and involving employees in the sustainability journey, the company successfully integrated sustainable practices, resulting in a 20% reduction in energy usage and improved employee morale.
Conclusion: Adopting sustainable manufacturing practices presents several challenges, including high costs, supply chain complexity, and resistance to change. However, by implementing strategic solutions such as securing financial support, fostering a culture of sustainability, leveraging technology, and engaging stakeholders, manufacturers can overcome these obstacles. Embracing sustainability not only benefits the environment but also enhances operational efficiency, reduces costs, and builds a competitive advantage in the market.
8. How can life cycle assessment (LCA) be utilized to improve sustainability in manufacturing processes?
Answer:
Life Cycle Assessment (LCA) in Sustainable Manufacturing:
Definition of Life Cycle Assessment (LCA): LCA is a systematic methodology used to evaluate the environmental impacts of a product or service throughout its entire life cycle, from raw material extraction and production to use, disposal, and recycling. It provides a comprehensive view of the environmental aspects associated with a product, enabling manufacturers to make informed decisions to enhance sustainability.
How LCA Improves Sustainability in Manufacturing Processes:
Identifying Environmental Hotspots:
- Usage: LCA helps pinpoint stages in the product lifecycle that have the highest environmental impacts, such as energy consumption, emissions, or resource use.
- Improvement: Allows manufacturers to target these hotspots for improvement, optimizing processes to reduce environmental burdens.
Informed Decision-Making:
- Usage: Provides data-driven insights into the environmental performance of different materials, processes, and technologies.
- Improvement: Facilitates the selection of more sustainable options, such as choosing eco-friendly materials or adopting energy-efficient technologies.
Product Design Optimization:
- Usage: Assesses the environmental implications of design choices, including materials, manufacturing methods, and product durability.
- Improvement: Enables the design of products that are easier to recycle, use fewer resources, and have a lower overall environmental footprint.
Supply Chain Management:
- Usage: Evaluates the environmental impact of suppliers and their processes.
- Improvement: Encourages collaboration with suppliers to improve their sustainability practices, ensuring a greener supply chain.
Regulatory Compliance and Reporting:
- Usage: Assists in meeting environmental regulations and standards by providing comprehensive environmental data.
- Improvement: Simplifies compliance reporting and helps avoid legal penalties by ensuring that products meet regulatory requirements.
Benchmarking and Performance Tracking:
- Usage: Allows manufacturers to benchmark their products against industry standards or competitors.
- Improvement: Facilitates the tracking of sustainability performance over time, promoting continuous improvement.
Cost Reduction:
- Usage: Identifies areas where resource use can be minimized, such as reducing material waste or lowering energy consumption.
- Improvement: Leads to cost savings by optimizing resource use and reducing waste disposal expenses.
Enhancing Brand Reputation:
- Usage: Demonstrates a commitment to sustainability through transparent reporting of environmental impacts.
- Improvement: Builds trust with consumers, investors, and other stakeholders, enhancing the company’s reputation and market position.
Steps to Conduct a Life Cycle Assessment:
Goal and Scope Definition:
- Action: Define the purpose of the LCA, the boundaries of the assessment, and the functional unit (e.g., per unit of product).
- Benefit: Ensures that the LCA is focused and relevant to the specific sustainability objectives.
Inventory Analysis:
- Action: Collect data on all inputs and outputs associated with each stage of the product lifecycle, including energy use, materials, emissions, and waste.
- Benefit: Provides a comprehensive dataset for evaluating environmental impacts.
Impact Assessment:
- Action: Analyze the inventory data to assess potential environmental impacts, such as global warming potential, acidification, eutrophication, and resource depletion.
- Benefit: Quantifies the environmental effects of the product, highlighting areas for improvement.
Interpretation:
- Action: Analyze the results, draw conclusions, and make recommendations for enhancing sustainability.
- Benefit: Translates the LCA findings into actionable strategies for reducing environmental impacts.
Case Example: A beverage manufacturer conducted an LCA for its bottled water product. The assessment revealed that the majority of environmental impacts occurred during the packaging stage due to plastic production and transportation. Based on these insights, the company switched to lightweight, recyclable bottles and optimized its transportation routes to reduce emissions. As a result, the LCA showed a 25% reduction in the product’s overall carbon footprint, enhancing the company’s sustainability profile and reducing costs associated with materials and logistics.
Conclusion: Life Cycle Assessment is a powerful tool for improving sustainability in manufacturing by providing a holistic view of a product’s environmental impacts. By identifying key areas for improvement, informing sustainable design and procurement decisions, and supporting regulatory compliance, LCA enables manufacturers to enhance their environmental performance, reduce costs, and build a strong reputation for sustainability.
9. What are the advantages of using eco-friendly materials in manufacturing, and how can manufacturers source these materials effectively?
Answer:
Advantages of Using Eco-Friendly Materials in Manufacturing:
Environmental Protection:
- Advantage: Eco-friendly materials reduce environmental impact by minimizing pollution, conserving natural resources, and lowering carbon emissions.
- Impact: Helps preserve ecosystems, reduce waste, and combat climate change.
Regulatory Compliance:
- Advantage: Using sustainable materials ensures compliance with environmental regulations and standards.
- Impact: Avoids legal penalties, fines, and operational disruptions caused by non-compliance.
Cost Savings:
- Advantage: Many eco-friendly materials, such as recycled or renewable resources, can be cost-effective in the long run.
- Impact: Reduces material costs and waste disposal expenses, enhancing overall profitability.
Market Demand and Competitive Advantage:
- Advantage: Increasing consumer preference for sustainable and ethically produced products drives demand for eco-friendly materials.
- Impact: Enhances brand reputation, attracts environmentally conscious customers, and differentiates products in the marketplace.
Innovation and Product Differentiation:
- Advantage: Incorporating eco-friendly materials fosters innovation in product design and functionality.
- Impact: Leads to the development of unique and high-value products that stand out in the market.
Resource Efficiency:
- Advantage: Eco-friendly materials often require less energy and fewer resources to produce and process.
- Impact: Increases overall manufacturing efficiency and reduces the environmental footprint of production processes.
Long-Term Sustainability:
- Advantage: Sustainable materials ensure the availability of resources for future generations.
- Impact: Promotes the long-term viability of manufacturing operations and supports global sustainability goals.
Enhanced Corporate Image:
- Advantage: Commitment to sustainability through the use of eco-friendly materials improves corporate social responsibility (CSR) credentials.
- Impact: Builds trust with stakeholders, including customers, investors, and employees, fostering loyalty and support.
How Manufacturers Can Source Eco-Friendly Materials Effectively:
Supplier Assessment and Selection:
- Action: Evaluate suppliers based on their sustainability practices, certifications, and environmental performance.
- Implementation: Use criteria such as ISO 14001 certification, fair trade practices, and the use of renewable or recycled materials.
Building Strong Supplier Relationships:
- Action: Collaborate closely with suppliers to ensure the consistent supply of eco-friendly materials.
- Implementation: Establish long-term partnerships, provide support for suppliers to improve their sustainability practices, and engage in joint sustainability initiatives.
Sustainable Procurement Policies:
- Action: Develop and implement procurement policies that prioritize the purchase of eco-friendly materials.
- Implementation: Include sustainability criteria in procurement guidelines, requiring the use of environmentally responsible materials.
Utilizing Certification Programs:
- Action: Source materials from suppliers that are certified by recognized sustainability standards.
- Implementation: Look for certifications such as Forest Stewardship Council (FSC), Global Organic Textile Standard (GOTS), and Cradle to Cradle (C2C).
Diversifying Material Sources:
- Action: Identify and engage with multiple suppliers of eco-friendly materials to ensure a reliable and resilient supply chain.
- Implementation: Avoid dependency on a single supplier by sourcing from various regions and suppliers committed to sustainability.
Investment in Research and Development:
- Action: Invest in R&D to identify and develop new eco-friendly materials that meet product requirements.
- Implementation: Collaborate with research institutions, industry consortia, and material innovators to explore sustainable alternatives.
Lifecycle Cost Analysis:
- Action: Conduct lifecycle cost analyses to assess the long-term financial benefits of using eco-friendly materials.
- Implementation: Compare the total cost of ownership, including material costs, energy use, and waste disposal, between conventional and sustainable materials.
Supply Chain Transparency:
- Action: Enhance visibility into the supply chain to ensure the traceability and authenticity of eco-friendly materials.
- Implementation: Utilize technologies like blockchain and supply chain management software to track material origins and certifications.
Education and Training:
- Action: Educate procurement teams and other relevant staff about the benefits and sourcing of eco-friendly materials.
- Implementation: Provide training programs and resources to build expertise in sustainable procurement practices.
Continuous Monitoring and Improvement:
- Action: Regularly monitor the performance of eco-friendly materials and suppliers to ensure ongoing compliance and improvement.
- Implementation: Use sustainability metrics and audits to assess material performance and supplier adherence to sustainability standards.
Conclusion: Using eco-friendly materials offers numerous advantages, including environmental protection, cost savings, and enhanced market competitiveness. By adopting effective sourcing strategies such as supplier assessment, sustainable procurement policies, certification utilization, and supply chain transparency, manufacturers can successfully integrate eco-friendly materials into their production processes. This transition not only supports sustainability goals but also drives long-term business success and positive societal impact.
10. How can automation and smart technologies enhance sustainable manufacturing practices?
Answer:
Enhancing Sustainable Manufacturing with Automation and Smart Technologies:
Energy Management:
- Enhancement: Automation systems can monitor and control energy usage in real-time.
- Benefit: Optimizes energy consumption, reduces waste, and lowers greenhouse gas emissions by ensuring machines operate only when necessary and at optimal efficiency.
- Example: IoT-enabled machines can adjust their operations based on real-time energy consumption data to minimize energy use.
Waste Reduction:
- Enhancement: Smart technologies can identify and minimize waste generation through precise control and monitoring of manufacturing processes.
- Benefit: Reduces material waste, lowers disposal costs, and minimizes environmental impact by ensuring efficient use of resources.
- Example: Automated systems can optimize material usage, reducing excess and scrap production.
Precision Manufacturing:
- Enhancement: Automation enables high-precision manufacturing, ensuring consistent product quality and reducing defects.
- Benefit: Decreases the need for rework and waste, leading to more sustainable production practices and resource conservation.
- Example: Robotic assembly lines can perform tasks with greater accuracy, minimizing errors and material waste.
Predictive Maintenance:
- Enhancement: Smart sensors and AI algorithms predict equipment failures before they occur.
- Benefit: Minimizes downtime, extends the lifespan of machinery, and reduces the need for premature replacements, contributing to resource efficiency and cost savings.
- Example: AI can predict when machinery needs maintenance, preventing unexpected breakdowns and reducing energy waste.
Supply Chain Optimization:
- Enhancement: Automation and smart technologies enhance supply chain visibility and coordination.
- Benefit: Reduces transportation-related emissions by optimizing routes, improves inventory management to prevent overproduction, and ensures timely deliveries.
- Example: Automated logistics systems can optimize delivery routes to reduce fuel consumption and emissions.
Sustainable Product Design:
- Enhancement: Smart design tools use data analytics to create products that are easier to recycle and have a lower environmental footprint.
- Benefit: Facilitates the development of eco-friendly products that align with circular economy principles, enhancing sustainability throughout the product lifecycle.
- Example: Design software can simulate the recyclability of different materials, aiding in the selection of sustainable options.
Resource Tracking and Traceability:
- Enhancement: Automation systems track the flow of materials and products throughout the manufacturing process.
- Benefit: Ensures responsible sourcing, enhances transparency, and supports compliance with sustainability standards by providing detailed records of material origins and usage.
- Example: Blockchain-integrated systems can provide real-time tracking of materials from suppliers to finished products.
Reduced Water Usage:
- Enhancement: Automated systems monitor and control water usage in manufacturing processes.
- Benefit: Minimizes water waste, ensures efficient usage, and reduces the environmental impact of water consumption.
- Example: Smart sensors can detect leaks and optimize water use in cooling systems.
Enhanced Worker Safety and Well-being:
- Enhancement: Automation takes over hazardous tasks, reducing the risk of workplace accidents.
- Benefit: Promotes a safer work environment, improving worker health and satisfaction, which is a key aspect of social sustainability.
- Example: Automated handling systems can manage heavy lifting, reducing the risk of musculoskeletal injuries among workers.
Data-Driven Sustainability Initiatives:
- Enhancement: Smart technologies collect and analyze vast amounts of data on manufacturing processes and environmental impacts.
- Benefit: Provides actionable insights to continuously improve sustainability practices, set measurable goals, and track progress towards environmental targets.
- Example: Data analytics platforms can identify patterns in energy usage, enabling targeted energy-saving initiatives.
Benefits of Leveraging Industry 4.0 Technologies for Sustainability:
- Enhanced Efficiency: Optimizes resource use, reduces energy consumption, and minimizes waste generation.
- Real-Time Monitoring: Provides immediate insights into environmental performance, enabling swift corrective actions.
- Predictive Capabilities: Anticipates and prevents potential issues that could lead to inefficiencies or environmental harm.
- Data-Driven Decisions: Facilitates informed decision-making based on comprehensive data analysis.
- Improved Product Lifecycle Management: Enhances the design, production, and end-of-life management of products to ensure sustainability.
- Greater Supply Chain Transparency: Ensures responsible sourcing and reduces environmental impacts across the supply chain.
- Innovation and Continuous Improvement: Drives the development of new sustainable practices and technologies, fostering a culture of innovation.
Case Example: A smart electronics manufacturer integrated IoT sensors and AI analytics into its production line to monitor energy usage and material flow in real-time. The data collected was analyzed to identify inefficiencies and optimize operations, resulting in a 20% reduction in energy consumption and a 15% decrease in material waste. Additionally, the company implemented a digital twin of its manufacturing process to simulate and test sustainability initiatives before real-world implementation. This approach not only enhanced the company’s sustainability performance but also reduced operational costs and improved product quality.
Conclusion: Automation and smart technologies play a pivotal role in advancing sustainable manufacturing practices by enhancing energy efficiency, reducing waste, improving precision, and enabling data-driven decision-making. By integrating these technologies, manufacturers can achieve significant environmental, economic, and social benefits, fostering a more sustainable and resilient manufacturing ecosystem. Embracing automation and smart technologies is essential for manufacturers committed to sustainability and long-term operational excellence.
11. How can manufacturers leverage Industry 4.0 technologies to enhance sustainable manufacturing practices?
Answer:
Leveraging Industry 4.0 Technologies for Sustainable Manufacturing:
Internet of Things (IoT):
- Usage: Deploy sensors and connected devices to monitor and optimize manufacturing processes in real-time.
- Benefit: Enhances energy efficiency, reduces waste, and improves resource management by providing accurate data on equipment performance and environmental conditions.
- Example: IoT-enabled machines can adjust their operations based on real-time energy consumption data to minimize energy use.
Artificial Intelligence (AI) and Machine Learning:
- Usage: Utilize AI and machine learning algorithms to analyze data and optimize manufacturing operations.
- Benefit: Improves predictive maintenance, reduces downtime, enhances process efficiency, and minimizes resource consumption by anticipating equipment failures and optimizing production schedules.
- Example: AI can predict when machinery needs maintenance, preventing unexpected breakdowns and reducing energy waste.
Big Data Analytics:
- Usage: Analyze large volumes of data generated from manufacturing processes to identify patterns and trends.
- Benefit: Enables data-driven decision-making, improves process optimization, and supports sustainability initiatives by identifying areas for efficiency improvements.
- Example: Analyzing production data to identify and eliminate inefficiencies that lead to excess energy use or material waste.
Additive Manufacturing (3D Printing):
- Usage: Implement 3D printing for prototyping and production to reduce material waste and enable on-demand manufacturing.
- Benefit: Minimizes material usage, reduces transportation emissions, and allows for the creation of complex, lightweight structures that enhance product sustainability.
- Example: Using 3D printing to produce custom parts as needed, reducing inventory and waste associated with overproduction.
Advanced Robotics and Automation:
- Usage: Integrate advanced robotics to perform precision tasks and automate repetitive processes.
- Benefit: Increases operational efficiency, reduces human error, and optimizes resource use, contributing to lower energy consumption and waste generation.
- Example: Automated systems can optimize material handling and reduce the need for manual intervention, minimizing waste and improving safety.
Digital Twins:
- Usage: Create virtual replicas of manufacturing processes, products, or systems for simulation and optimization.
- Benefit: Allows for the testing of sustainability initiatives in a virtual environment, identifying potential improvements before implementing them in the real world.
- Example: Simulating energy usage in a production line to identify and implement energy-saving measures.
Blockchain Technology:
- Usage: Utilize blockchain for supply chain transparency and traceability.
- Benefit: Ensures the responsible sourcing of materials, verifies sustainability claims, and reduces fraud, enhancing the overall sustainability of the supply chain.
- Example: Tracking the origin and journey of raw materials to ensure they are sourced sustainably and ethically.
Cloud Computing:
- Usage: Employ cloud-based platforms for data storage, processing, and collaboration.
- Benefit: Enhances accessibility and scalability of sustainability data, supports real-time monitoring, and facilitates collaborative sustainability efforts across global operations.
- Example: Using cloud-based dashboards to monitor energy consumption and sustainability metrics in real-time from any location.
Virtual and Augmented Reality (VR/AR):
- Usage: Implement VR and AR for training, maintenance, and process optimization.
- Benefit: Improves efficiency and reduces errors by providing immersive training and real-time guidance, enhancing the sustainability of manufacturing operations.
- Example: AR-assisted maintenance can guide technicians to perform repairs more accurately, reducing downtime and resource use.
Smart Manufacturing Platforms:
- Usage: Integrate comprehensive smart manufacturing platforms that connect various Industry 4.0 technologies.
- Benefit: Enables seamless data flow, enhances process coordination, and supports holistic sustainability strategies by providing a unified view of manufacturing operations.
- Example: A smart manufacturing platform can integrate IoT sensors, AI analytics, and automation systems to optimize production in real-time for sustainability.
Benefits of Leveraging Industry 4.0 Technologies for Sustainability:
- Enhanced Efficiency: Optimizes resource use, reduces energy consumption, and minimizes waste generation.
- Real-Time Monitoring: Provides immediate insights into environmental performance, enabling swift corrective actions.
- Predictive Capabilities: Anticipates and prevents potential issues that could lead to inefficiencies or environmental harm.
- Data-Driven Decisions: Facilitates informed decision-making based on comprehensive data analysis.
- Improved Product Lifecycle Management: Enhances the design, production, and end-of-life management of products to ensure sustainability.
- Greater Supply Chain Transparency: Ensures responsible sourcing and reduces environmental impacts across the supply chain.
- Innovation and Continuous Improvement: Drives the development of new sustainable practices and technologies, fostering a culture of innovation.
Case Example: A smart electronics manufacturer integrated IoT sensors and AI analytics into its production line to monitor energy usage and material flow in real-time. The data collected was analyzed to identify inefficiencies and optimize operations, resulting in a 20% reduction in energy consumption and a 15% decrease in material waste. Additionally, the company implemented a digital twin of its manufacturing process to simulate and test sustainability initiatives before real-world implementation. This approach not only enhanced the company’s sustainability performance but also reduced operational costs and improved product quality.
Conclusion: Industry 4.0 technologies offer powerful tools for enhancing sustainable manufacturing practices. By leveraging IoT, AI, big data, additive manufacturing, robotics, and other advanced technologies, manufacturers can significantly improve their environmental performance, optimize resource use, and drive continuous innovation. Integrating these technologies into manufacturing operations is essential for achieving sustainability goals, reducing environmental impact, and maintaining a competitive edge in the modern industrial landscape.
12. How can manufacturers balance the trade-offs between sustainability and cost in their operations?
Answer:
Balancing Sustainability and Cost in Manufacturing Operations:
Conduct Cost-Benefit Analyses:
- Action: Evaluate the financial implications of sustainability initiatives by comparing the costs of implementation with the long-term benefits.
- Benefit: Identifies initiatives that offer a favorable return on investment (ROI), ensuring that sustainability efforts are economically viable.
Prioritize High-Impact Initiatives:
- Action: Focus on sustainability projects that provide significant environmental benefits while offering cost savings, such as energy efficiency and waste reduction.
- Benefit: Maximizes the positive impact on sustainability without incurring excessive costs.
Implement Lean Manufacturing Principles:
- Action: Adopt lean practices to eliminate waste, improve process efficiency, and reduce costs.
- Benefit: Enhances both sustainability and profitability by optimizing resource use and minimizing waste.
Invest in Energy-Efficient Technologies:
- Action: Upgrade to energy-efficient machinery and systems to lower energy consumption.
- Benefit: Reduces long-term energy costs and decreases the environmental footprint, leading to both financial and sustainability gains.
Utilize Renewable Energy Sources:
- Action: Incorporate renewable energy sources such as solar and wind power into manufacturing operations.
- Benefit: Lowers energy costs over time and reduces reliance on fossil fuels, contributing to sustainability goals.
Optimize Supply Chain Management:
- Action: Streamline supply chain processes to reduce transportation costs and minimize environmental impact.
- Benefit: Achieves cost savings and enhances sustainability through efficient logistics and reduced emissions.
Foster Supplier Collaboration:
- Action: Work closely with suppliers to implement sustainable practices that can lead to cost reductions, such as bulk purchasing of eco-friendly materials.
- Benefit: Creates a mutually beneficial relationship that supports both cost management and sustainability objectives.
Implement Circular Economy Practices:
- Action: Adopt circular economy models that focus on recycling, reusing, and refurbishing materials and products.
- Benefit: Reduces material costs, minimizes waste disposal expenses, and promotes sustainability through resource conservation.
Leverage Government Incentives and Grants:
- Action: Take advantage of government programs that offer financial incentives for implementing sustainable practices.
- Benefit: Lowers the initial cost burden of sustainability initiatives, making them more financially feasible.
Educate and Engage Employees:
- Action: Train employees on sustainability practices and encourage their involvement in cost-saving initiatives.
- Benefit: Enhances operational efficiency and fosters a culture of sustainability that drives continuous improvement.
Monitor and Optimize Resource Use:
- Action: Use data analytics and monitoring tools to track resource consumption and identify areas for optimization.
- Benefit: Ensures efficient use of resources, reducing costs and environmental impact simultaneously.
Incremental Implementation:
- Action: Implement sustainability initiatives gradually rather than all at once.
- Benefit: Spreads out costs over time and allows for adjustments based on financial performance and operational impact.
Strategies to Achieve Balance:
Integrated Sustainability Planning:
- Strategy: Incorporate sustainability goals into the overall business strategy and operational planning.
- Benefit: Ensures that sustainability and cost considerations are addressed together, aligning efforts towards common objectives.
Collaborative Decision-Making:
- Strategy: Involve cross-functional teams in decision-making to consider both sustainability and cost aspects.
- Benefit: Promotes a holistic approach to balancing sustainability with financial performance.
Continuous Improvement:
- Strategy: Adopt a mindset of continuous improvement to regularly assess and enhance sustainability practices.
- Benefit: Enables ongoing optimization of both sustainability and cost-efficiency measures.
Performance Tracking and Reporting:
- Strategy: Monitor the performance of sustainability initiatives and their financial impact.
- Benefit: Provides insights into the effectiveness of initiatives and guides future investments in sustainability.
Case Example: A manufacturing company aimed to reduce its carbon footprint while managing costs. They conducted a cost-benefit analysis of implementing energy-efficient lighting and machinery. The analysis showed that although the initial investment was significant, the long-term energy savings would offset the costs within five years. The company prioritized these high-impact initiatives and phased the implementation to manage expenses. Additionally, they optimized their supply chain to reduce transportation costs and emissions by consolidating shipments and choosing more efficient routes. As a result, the company achieved a 20% reduction in energy consumption, lowered operational costs by 15%, and significantly decreased its carbon emissions, successfully balancing sustainability with cost management.
Conclusion: Balancing sustainability and cost requires a strategic and integrated approach that prioritizes high-impact initiatives, leverages cost-saving opportunities, and fosters collaboration across the organization and supply chain. By conducting thorough analyses, adopting lean and circular practices, and continuously monitoring performance, manufacturers can achieve sustainable operations that are both environmentally responsible and economically viable. This balance not only supports long-term business success but also contributes to global sustainability goals.
12. How can manufacturers leverage Industry 4.0 technologies to enhance sustainable manufacturing practices?
Answer:
Leveraging Industry 4.0 Technologies for Sustainable Manufacturing:
Internet of Things (IoT):
- Usage: Deploy sensors and connected devices to monitor and optimize manufacturing processes in real-time.
- Benefit: Enhances energy efficiency, reduces waste, and improves resource management by providing accurate data on equipment performance and environmental conditions.
- Example: IoT-enabled machines can adjust their operations based on real-time energy consumption data to minimize energy use.
Artificial Intelligence (AI) and Machine Learning:
- Usage: Utilize AI and machine learning algorithms to analyze data and optimize manufacturing operations.
- Benefit: Improves predictive maintenance, reduces downtime, enhances process efficiency, and minimizes resource consumption by anticipating equipment failures and optimizing production schedules.
- Example: AI can predict when machinery needs maintenance, preventing unexpected breakdowns and reducing energy waste.
Big Data Analytics:
- Usage: Analyze large volumes of data generated from manufacturing processes to identify patterns and trends.
- Benefit: Enables data-driven decision-making, improves process optimization, and supports sustainability initiatives by identifying areas for efficiency improvements.
- Example: Analyzing production data to identify and eliminate inefficiencies that lead to excess energy use or material waste.
Additive Manufacturing (3D Printing):
- Usage: Implement 3D printing for prototyping and production to reduce material waste and enable on-demand manufacturing.
- Benefit: Minimizes material usage, reduces transportation emissions, and allows for the creation of complex, lightweight structures that enhance product sustainability.
- Example: Using 3D printing to produce custom parts as needed, reducing inventory and waste associated with overproduction.
Advanced Robotics and Automation:
- Usage: Integrate advanced robotics to perform precision tasks and automate repetitive processes.
- Benefit: Increases operational efficiency, reduces human error, and optimizes resource use, contributing to lower energy consumption and waste generation.
- Example: Automated systems can optimize material handling and reduce the need for manual intervention, minimizing waste and improving safety.
Digital Twins:
- Usage: Create virtual replicas of manufacturing processes, products, or systems for simulation and optimization.
- Benefit: Allows for the testing of sustainability initiatives in a virtual environment, identifying potential improvements before implementing them in the real world.
- Example: Simulating energy usage in a production line to identify and implement energy-saving measures.
Blockchain Technology:
- Usage: Utilize blockchain for supply chain transparency and traceability.
- Benefit: Ensures the responsible sourcing of materials, verifies sustainability claims, and reduces fraud, enhancing the overall sustainability of the supply chain.
- Example: Tracking the origin and journey of raw materials to ensure they are sourced sustainably and ethically.
Cloud Computing:
- Usage: Employ cloud-based platforms for data storage, processing, and collaboration.
- Benefit: Enhances accessibility and scalability of sustainability data, supports real-time monitoring, and facilitates collaborative sustainability efforts across global operations.
- Example: Using cloud-based dashboards to monitor energy consumption and sustainability metrics in real-time from any location.
Virtual and Augmented Reality (VR/AR):
- Usage: Implement VR and AR for training, maintenance, and process optimization.
- Benefit: Improves efficiency and reduces errors by providing immersive training and real-time guidance, enhancing the sustainability of manufacturing operations.
- Example: AR-assisted maintenance can guide technicians to perform repairs more accurately, reducing downtime and resource use.
Smart Manufacturing Platforms:
- Usage: Integrate comprehensive smart manufacturing platforms that connect various Industry 4.0 technologies.
- Benefit: Enables seamless data flow, enhances process coordination, and supports holistic sustainability strategies by providing a unified view of manufacturing operations.
- Example: A smart manufacturing platform can integrate IoT sensors, AI analytics, and automation systems to optimize production in real-time for sustainability.
Benefits of Leveraging Industry 4.0 Technologies for Sustainability:
- Enhanced Efficiency: Optimizes resource use, reduces energy consumption, and minimizes waste generation.
- Real-Time Monitoring: Provides immediate insights into environmental performance, enabling swift corrective actions.
- Predictive Capabilities: Anticipates and prevents potential issues that could lead to inefficiencies or environmental harm.
- Data-Driven Decisions: Facilitates informed decision-making based on comprehensive data analysis.
- Improved Product Lifecycle Management: Enhances the design, production, and end-of-life management of products to ensure sustainability.
- Greater Supply Chain Transparency: Ensures responsible sourcing and reduces environmental impacts across the supply chain.
- Innovation and Continuous Improvement: Drives the development of new sustainable practices and technologies, fostering a culture of innovation.
Case Example: A smart electronics manufacturer integrated IoT sensors and AI analytics into its production line to monitor energy usage and material flow in real-time. The data collected was analyzed to identify inefficiencies and optimize operations, resulting in a 20% reduction in energy consumption and a 15% decrease in material waste. Additionally, the company implemented a digital twin of its manufacturing process to simulate and test sustainability initiatives before real-world implementation. This approach not only enhanced the company’s sustainability performance but also reduced operational costs and improved product quality.
Conclusion: Industry 4.0 technologies offer powerful tools for enhancing sustainable manufacturing practices. By leveraging IoT, AI, big data, additive manufacturing, robotics, and other advanced technologies, manufacturers can significantly improve their environmental performance, optimize resource use, and drive continuous innovation. Integrating these technologies into manufacturing operations is essential for achieving sustainability goals, reducing environmental impact, and maintaining a competitive edge in the modern industrial landscape.
Conclusion:
The above thought-provoking questions and detailed answers provide a comprehensive exploration of Sustainable Manufacturing, covering essential topics such as the definition and importance of sustainable manufacturing, energy efficiency, waste reduction, renewable energy integration, green supply chain management, circular economy, eco-friendly materials, Industry 4.0 technologies, life cycle assessment, challenges in adopting sustainable practices, balancing sustainability with cost, and leveraging advanced technologies for sustainability. These questions facilitate a deep understanding of how to implement and optimize sustainable practices in manufacturing, enhancing environmental performance, reducing costs, and building a competitive advantage in the market. Engaging with these questions equips students and professionals with the knowledge and strategies needed to manage sustainable manufacturing operations effectively, drive continuous improvement, and achieve long-term operational excellence in an increasingly eco-conscious and regulated industrial environment.
More Questions and Answers on Sustainable Manufacturing
1. What is sustainable manufacturing, and why is it crucial for modern industries?
Answer:
Definition of Sustainable Manufacturing: Sustainable manufacturing refers to the creation of products through processes that minimize negative environmental impacts, conserve energy and natural resources, are economically viable, and are socially responsible. It integrates environmentally friendly practices into every aspect of the manufacturing process, from design and production to distribution and disposal.
Importance in Modern Industries:
Environmental Stewardship:
- Impact: Sustainable manufacturing reduces pollution, lowers carbon emissions, and minimizes waste generation.
- Reason: Industrial activities are significant contributors to environmental degradation. Adopting sustainable practices helps mitigate climate change and preserve ecosystems.
Resource Efficiency:
- Impact: Optimizes the use of materials and energy, reducing dependency on finite resources.
- Reason: Efficient resource utilization ensures long-term availability of essential resources and reduces operational costs.
Regulatory Compliance:
- Impact: Helps companies adhere to increasingly stringent environmental laws and regulations.
- Reason: Non-compliance can result in hefty fines, legal actions, and damage to a company’s reputation.
Market Competitiveness:
- Impact: Meets the growing consumer demand for eco-friendly and ethically produced products.
- Reason: Enhances brand loyalty, attracts environmentally conscious consumers, and opens new market opportunities.
Economic Benefits:
- Impact: Lowers costs through energy savings, waste reduction, and improved efficiency.
- Reason: Sustainable practices often lead to operational efficiencies and long-term profitability.
Social Responsibility:
- Impact: Promotes ethical labor practices and contributes positively to communities.
- Reason: Enhances corporate reputation and fosters a positive relationship with stakeholders.
Conclusion: Sustainable manufacturing is essential for balancing economic growth with environmental stewardship and social responsibility. It ensures that industrial progress does not come at the expense of the planet or future generations, making it a fundamental strategy for modern businesses aiming for long-term success and resilience.
2. How can energy efficiency be achieved in sustainable manufacturing processes?
Answer:
Achieving Energy Efficiency in Sustainable Manufacturing:
Energy Audits:
- Action: Conduct comprehensive energy audits to identify areas of high energy consumption and inefficiencies.
- Benefit: Provides a clear understanding of where energy is used and where savings can be made, enabling targeted improvements.
Upgrade to Energy-Efficient Equipment:
- Action: Replace old machinery and equipment with energy-efficient models that consume less power.
- Benefit: Reduces energy consumption and operational costs while enhancing productivity and performance.
Implementing Automation and Smart Controls:
- Action: Use automated systems and smart controls to optimize energy use in real-time.
- Benefit: Ensures machinery operates only when needed, reducing idle energy consumption and improving overall efficiency.
Optimizing Manufacturing Processes:
- Action: Streamline production processes to eliminate unnecessary steps and reduce energy usage.
- Benefit: Enhances efficiency, minimizes energy waste, and increases throughput without additional energy costs.
Heat Recovery Systems:
- Action: Install systems to capture and reuse waste heat generated during manufacturing.
- Benefit: Provides additional energy for other processes, reducing overall energy demand and improving sustainability.
Lighting Upgrades:
- Action: Switch to LED lighting and incorporate motion sensors to reduce lighting energy use.
- Benefit: Lowers electricity consumption and maintenance costs while improving lighting quality and reliability.
Insulation and Building Efficiency:
- Action: Improve insulation and optimize HVAC systems to maintain optimal temperatures with less energy.
- Benefit: Reduces the energy required for heating and cooling manufacturing facilities, leading to significant energy savings.
Employee Training and Awareness:
- Action: Educate employees on energy-saving practices and encourage their participation in energy efficiency initiatives.
- Benefit: Promotes a culture of sustainability, ensuring collective effort towards energy conservation and operational efficiency.
Renewable Energy Integration:
- Action: Incorporate renewable energy sources such as solar, wind, or biomass to power manufacturing operations.
- Benefit: Reduces reliance on fossil fuels, lowers greenhouse gas emissions, and contributes to long-term energy sustainability.
Continuous Monitoring and Improvement:
- Action: Use energy management systems to continuously monitor energy use and identify opportunities for further improvements.
- Benefit: Ensures ongoing energy efficiency, adapts to changing operational needs, and fosters a culture of continuous improvement.
Conclusion: Achieving energy efficiency in sustainable manufacturing involves a combination of technological upgrades, process optimization, and cultural shifts within the organization. By implementing these strategies, manufacturers can significantly reduce their energy consumption, lower costs, and contribute to environmental sustainability.
3. What role does waste reduction play in sustainable manufacturing, and what methods can be employed to achieve it?
Answer:
Role of Waste Reduction in Sustainable Manufacturing:
Environmental Impact:
- Role: Minimizes the amount of waste sent to landfills and reduces pollution.
- Impact: Helps preserve natural resources, reduces greenhouse gas emissions, and lowers the environmental footprint of manufacturing activities.
Cost Savings:
- Role: Reduces costs associated with waste disposal and raw material consumption.
- Impact: Enhances profitability by lowering operational expenses and improving resource utilization.
Resource Efficiency:
- Role: Ensures that materials are used effectively, reducing the need for new raw materials.
- Impact: Promotes the sustainable use of resources and decreases dependency on finite supplies, ensuring long-term viability.
Regulatory Compliance:
- Role: Helps manufacturers comply with environmental regulations regarding waste management.
- Impact: Avoids fines, legal issues, and enhances corporate reputation by demonstrating commitment to environmental stewardship.
Innovation and Competitive Advantage:
- Role: Encourages the development of innovative processes and products that generate less waste.
- Impact: Differentiates companies in the market, meets consumer demand for sustainable products, and fosters a culture of continuous improvement.
Methods to Achieve Waste Reduction:
Lean Manufacturing:
- Method: Implement lean principles to eliminate non-value-adding activities and reduce waste.
- Benefit: Streamlines processes, enhances efficiency, and minimizes waste generation by focusing on value creation.
Recycling and Reusing Materials:
- Method: Establish systems to recycle waste materials and reuse them in the production process.
- Benefit: Reduces the need for new raw materials, minimizes waste disposal, and lowers environmental impact.
Process Optimization:
- Method: Analyze and improve manufacturing processes to reduce material waste.
- Benefit: Increases efficiency, lowers the generation of scrap and defective products, and enhances overall productivity.
Design for Sustainability:
- Method: Design products with minimal material use and consider their end-of-life disposal.
- Benefit: Reduces waste generation, facilitates easier recycling or reuse, and extends the product lifecycle.
Employee Training and Engagement:
- Method: Educate employees on waste reduction techniques and involve them in sustainability initiatives.
- Benefit: Promotes a culture of waste minimization, encourages proactive identification of waste reduction opportunities, and fosters collective responsibility.
Advanced Manufacturing Technologies:
- Method: Use technologies such as additive manufacturing (3D printing) to reduce material waste.
- Benefit: Enhances precision in production, minimizes excess material usage, and allows for on-demand manufacturing, reducing inventory and waste.
Waste Audits:
- Method: Conduct regular audits to identify sources of waste and areas for improvement.
- Benefit: Provides actionable insights to target waste reduction efforts effectively and monitor progress over time.
Supplier Collaboration:
- Method: Work with suppliers to minimize packaging waste and adopt sustainable materials.
- Benefit: Reduces waste generation upstream in the supply chain, promotes sustainable sourcing, and fosters mutually beneficial relationships.
Closed-Loop Systems:
- Method: Implement closed-loop systems where waste from one process becomes input for another.
- Benefit: Maximizes resource utilization, minimizes overall waste, and supports circular economy principles by ensuring materials are continuously cycled through the production system.
Monitoring and Reporting:
- Method: Use waste tracking systems to monitor waste generation and set reduction targets.
- Benefit: Ensures accountability, tracks progress towards waste reduction goals, and provides data for informed decision-making.
Conclusion: Waste reduction is a fundamental aspect of sustainable manufacturing, contributing to environmental protection, cost savings, and resource efficiency. By employing a combination of lean principles, recycling, process optimization, and technological innovations, manufacturers can significantly reduce waste and enhance the sustainability of their operations.
4. How can renewable energy sources be integrated into manufacturing processes to promote sustainability?
Answer:
Integrating Renewable Energy Sources into Manufacturing Processes:
Solar Power Integration:
- Method: Install solar panels on manufacturing facilities to generate electricity.
- Benefit: Reduces reliance on fossil fuels, lowers energy costs, and decreases greenhouse gas emissions.
- Example: Factory rooftops equipped with photovoltaic panels can supply a significant portion of their energy needs, reducing overall energy costs and carbon footprint.
Wind Energy Utilization:
- Method: Invest in wind turbines either on-site or through wind farms to generate power.
- Benefit: Provides a clean and renewable source of energy, particularly effective in regions with consistent wind patterns.
- Example: Offshore wind farms can supply large-scale energy to manufacturing plants located near coastal areas, ensuring a steady and reliable energy supply.
Geothermal Energy:
- Method: Utilize geothermal heat pumps for heating and cooling manufacturing facilities.
- Benefit: Offers a stable and efficient energy source with minimal environmental impact.
- Example: Geothermal systems can maintain optimal temperatures in factories, reducing energy consumption for HVAC systems and lowering operational costs.
Biomass Energy:
- Method: Use organic materials such as agricultural waste, wood chips, or dedicated energy crops to generate heat and power.
- Benefit: Converts waste into valuable energy, reducing landfill use and carbon emissions.
- Example: A manufacturing plant can use biomass boilers to produce steam for industrial processes, utilizing waste materials and lowering reliance on fossil fuels.
Hydropower:
- Method: Harness energy from flowing water through small-scale hydroelectric systems.
- Benefit: Provides a consistent and renewable energy source with low operational costs.
- Example: Facilities located near rivers can install micro-hydro turbines to generate electricity for their operations, ensuring a reliable energy supply.
Energy Storage Solutions:
- Method: Incorporate battery storage systems to store excess renewable energy for use during peak demand or when renewable sources are unavailable.
- Benefit: Enhances the reliability and consistency of renewable energy supply, ensuring continuous operations.
- Example: Large-scale lithium-ion batteries can store solar energy generated during the day for use at night, balancing energy supply and demand.
Hybrid Energy Systems:
- Method: Combine multiple renewable energy sources (e.g., solar and wind) to create a more resilient and reliable energy supply.
- Benefit: Balances the variability of different renewable sources, ensuring a steady energy flow and reducing dependence on a single source.
- Example: A manufacturing plant might use both solar panels and wind turbines to ensure continuous power generation, even when one source is intermittent.
On-site Renewable Energy Generation:
- Method: Develop renewable energy projects directly on manufacturing sites to tailor energy production to specific needs.
- Benefit: Maximizes energy efficiency, reduces transmission losses, and allows for greater control over energy sources.
- Example: Integrating solar canopies over parking lots to generate electricity while providing shade for vehicles, simultaneously utilizing space effectively.
Renewable Energy Purchasing:
- Method: Purchase renewable energy credits (RECs) or enter into power purchase agreements (PPAs) with renewable energy providers.
- Benefit: Supports the development of renewable energy projects without the need for on-site installations, providing flexibility and scalability.
- Example: A manufacturer can sign a PPA with a wind farm to supply a portion of its electricity needs, ensuring a steady supply of renewable energy.
Energy Management Systems:
- Method: Implement advanced energy management systems to optimize the use of renewable energy within manufacturing processes.
- Benefit: Enhances energy efficiency, reduces waste, and ensures optimal utilization of renewable sources, leading to cost savings and sustainability.
- Example: Smart grids can dynamically allocate energy from renewable sources based on real-time demand and supply conditions, ensuring efficient energy use.
Benefits of Integrating Renewable Energy:
- Environmental Sustainability: Reduces carbon footprint and reliance on non-renewable energy sources, contributing to global climate goals.
- Cost Savings: Lowers long-term energy costs and protects against volatile fossil fuel prices, enhancing financial stability.
- Energy Security: Enhances energy independence and reduces vulnerability to supply disruptions, ensuring consistent operations.
- Regulatory Compliance: Helps meet environmental regulations and sustainability standards, avoiding penalties and fostering good relations with regulatory bodies.
- Corporate Image: Enhances brand reputation as a responsible and eco-friendly manufacturer, attracting environmentally conscious customers and partners.
- Innovation and Competitiveness: Positions the company as a leader in sustainable practices, attracting investments and partnerships focused on sustainability.
Case Example: A large automotive manufacturer integrated solar power into its production facilities by installing photovoltaic panels on the rooftops of its plants. The solar installation provided 25% of the facility’s electricity needs, resulting in annual energy cost savings of $2 million and a reduction of 3,000 metric tons of CO2 emissions. Additionally, the company implemented energy storage systems to ensure a steady energy supply during cloudy days and nighttime operations. This integration not only enhanced the company’s sustainability profile but also provided a competitive advantage in the market by appealing to eco-conscious consumers.
Conclusion: Integrating renewable energy sources into manufacturing processes is a pivotal strategy for promoting sustainability. By adopting a combination of solar, wind, geothermal, biomass, and other renewable energy technologies, manufacturers can significantly reduce their environmental impact, achieve cost savings, and enhance their competitive position. Implementing these strategies requires careful planning, investment in appropriate technologies, and a commitment to continuous improvement in energy management.
5. What are the key principles of green supply chain management, and how do they contribute to sustainability?
Answer:
Key Principles of Green Supply Chain Management (GSCM):
Environmental Integration:
- Principle: Incorporate environmental considerations into all supply chain processes and decisions.
- Contribution to Sustainability: Ensures that environmental impacts are minimized throughout the entire supply chain, from sourcing to delivery, promoting a holistic approach to sustainability.
Sustainable Sourcing:
- Principle: Choose suppliers that adhere to environmental and social standards.
- Contribution to Sustainability: Promotes the use of eco-friendly materials and ethical labor practices, reducing the overall environmental footprint and ensuring responsible sourcing.
Eco-Design:
- Principle: Design products with their entire lifecycle in mind, focusing on reducing environmental impact.
- Contribution to Sustainability: Facilitates easier recycling, reuse, and disposal, minimizing waste and resource consumption, and extending product lifecycle.
Waste Minimization:
- Principle: Implement strategies to reduce, reuse, and recycle waste generated during production and distribution.
- Contribution to Sustainability: Lowers the amount of waste sent to landfills and reduces the environmental impact of manufacturing processes, enhancing resource efficiency.
Energy Efficiency:
- Principle: Optimize energy use across all supply chain activities.
- Contribution to Sustainability: Reduces greenhouse gas emissions and lowers operational costs through efficient energy management, contributing to both environmental and economic sustainability.
Reverse Logistics:
- Principle: Manage the return and disposal of products in an environmentally responsible manner.
- Contribution to Sustainability: Encourages recycling and proper disposal, reducing environmental pollution and promoting resource recovery, aligning with circular economy principles.
Green Transportation:
- Principle: Optimize logistics and transportation to reduce emissions and energy consumption.
- Contribution to Sustainability: Minimizes the carbon footprint associated with moving goods, enhancing overall supply chain sustainability and reducing operational costs.
Supplier Collaboration:
- Principle: Work closely with suppliers to improve their environmental performance.
- Contribution to Sustainability: Enhances the sustainability of the entire supply chain through shared best practices, continuous improvement, and fostering mutually beneficial relationships.
Lifecycle Assessment:
- Principle: Evaluate the environmental impact of products throughout their entire lifecycle.
- Contribution to Sustainability: Identifies areas for improvement, ensures that sustainability is considered from production to end-of-life, and supports informed decision-making to reduce environmental impact.
Continuous Improvement:
- Principle: Commit to ongoing efforts to enhance environmental performance.
- Contribution to Sustainability: Drives innovation, ensures that the supply chain adapts to new sustainability challenges and opportunities, and maintains a commitment to long-term sustainability goals.
Contribution of GSCM Principles to Sustainability:
- Reduced Environmental Impact: By integrating environmental considerations, GSCM minimizes pollution, waste, and resource depletion, contributing significantly to environmental preservation.
- Cost Savings: Energy efficiency and waste reduction lead to lower operational costs, enhancing economic sustainability and profitability.
- Regulatory Compliance: Adhering to environmental standards and regulations prevents legal issues and fines, ensuring smooth operations and maintaining a positive corporate image.
- Enhanced Brand Reputation: Commitment to sustainability builds a positive brand image, attracting environmentally conscious consumers and partners, and differentiating the company in the marketplace.
- Innovation and Competitive Advantage: Sustainable practices encourage innovation in product design and processes, providing a competitive edge and fostering a culture of continuous improvement.
- Resource Conservation: Efficient use of resources ensures their availability for future generations, promoting long-term sustainability and reducing dependency on finite resources.
Case Example: A global electronics company adopted green supply chain management principles by sourcing conflict-free minerals, implementing energy-efficient manufacturing processes, and optimizing its transportation routes to reduce emissions. They also established a robust reverse logistics system to manage product returns and recycling. As a result, the company reduced its carbon footprint by 20%, achieved significant cost savings through energy efficiency, and enhanced its reputation as a leader in sustainable electronics. These efforts not only contributed to environmental sustainability but also increased customer loyalty and opened new market opportunities focused on eco-friendly products.
Conclusion: Green Supply Chain Management is essential for achieving sustainability in manufacturing and other industries. By adhering to key principles such as environmental integration, sustainable sourcing, waste minimization, and energy efficiency, organizations can significantly reduce their environmental impact, achieve cost savings, comply with regulations, and enhance their competitive position. Implementing GSCM principles fosters a sustainable and responsible approach to supply chain management, ensuring long-term success and positive societal impact.
6. What are the benefits of implementing a circular economy model in manufacturing, and how can manufacturers transition to this model?
Answer:
Benefits of Implementing a Circular Economy Model in Manufacturing:
Resource Efficiency:
- Benefit: Maximizes the use of materials by reusing, recycling, and refurbishing products.
- Impact: Reduces the need for virgin raw materials, conserving natural resources and lowering production costs.
Waste Reduction:
- Benefit: Minimizes waste generation by designing products for longevity, repairability, and recyclability.
- Impact: Decreases landfill usage and environmental pollution, contributing to a cleaner ecosystem.
Cost Savings:
- Benefit: Lowers costs associated with material procurement, waste management, and disposal.
- Impact: Enhances profitability through reduced operational expenses and efficient resource utilization.
Innovation and Product Development:
- Benefit: Encourages the development of innovative products and processes that support reuse and recycling.
- Impact: Drives technological advancements and opens new market opportunities for sustainable products.
Enhanced Brand Reputation:
- Benefit: Demonstrates a commitment to sustainability and environmental responsibility.
- Impact: Attracts eco-conscious consumers, increases customer loyalty, and differentiates the brand in the marketplace.
Regulatory Compliance:
- Benefit: Helps manufacturers comply with environmental regulations and standards.
- Impact: Avoids legal penalties, ensures operational continuity, and fosters good relationships with regulatory bodies.
Risk Mitigation:
- Benefit: Reduces dependency on finite resources and mitigates risks associated with resource scarcity and price volatility.
- Impact: Enhances supply chain resilience and ensures long-term business sustainability.
Economic Growth:
- Benefit: Creates new business models and revenue streams through services like product-as-a-service, leasing, and remanufacturing.
- Impact: Contributes to economic growth while promoting sustainable consumption and production patterns.
Environmental Impact:
- Benefit: Lowers greenhouse gas emissions, reduces pollution, and conserves biodiversity by minimizing resource extraction and waste.
- Impact: Contributes to global sustainability goals and combats climate change.
How Manufacturers Can Transition to a Circular Economy Model:
Design for Longevity and Repairability:
- Strategy: Develop products that are durable, easy to repair, and upgradeable.
- Benefit: Extends the product’s usable life, reducing the frequency of replacements and minimizing waste generation.
- Implementation: Use modular designs and standardized components to facilitate repairs and extensions of product life.
Implement Recycling and Reuse Programs:
- Strategy: Establish systems to collect, recycle, and reuse products at the end of their lifecycle.
- Benefit: Facilitates the proper recycling and disposal of products, ensuring that materials are recovered and reused, reducing waste and resource extraction.
- Implementation: Create take-back programs, partner with recycling facilities, and use recycled materials in new products.
Adopt Product-as-a-Service (PaaS) Models:
- Strategy: Shift from selling products to offering them as services, such as leasing or renting.
- Benefit: Encourages the return and reuse of products, reducing the need for new production and minimizing waste.
- Implementation: Develop subscription-based models where customers pay for the use of a product rather than owning it outright.
Collaborate with Supply Chain Partners:
- Strategy: Work closely with suppliers and partners to ensure sustainability throughout the supply chain.
- Benefit: Enhances the sustainability of the entire supply chain through shared best practices and continuous improvement.
- Implementation: Share sustainability goals, collaborate on material sourcing, and develop joint recycling initiatives.
Invest in Advanced Manufacturing Technologies:
- Strategy: Utilize technologies that support circular practices, such as additive manufacturing and automation.
- Benefit: Reduces material waste, enables on-demand production, and facilitates customization.
- Implementation: Implement 3D printing for on-demand production, reducing waste and enabling customization.
Redefine Business Models:
- Strategy: Transition to business models that emphasize sustainability and resource efficiency.
- Benefit: Aligns operations with circular economy goals, promoting long-term sustainability and profitability.
- Implementation: Incorporate circular principles into the core business strategy, aligning operations with circular economy goals.
Educate and Engage Consumers:
- Strategy: Raise awareness about the benefits of circular products and encourage sustainable consumer behavior.
- Benefit: Increases consumer participation in circular initiatives, such as returning used products for recycling or refurbishment.
- Implementation: Provide information on product care, recycling options, and the environmental benefits of circular practices.
Measure and Report Sustainability Metrics:
- Strategy: Track progress towards circular economy goals using specific metrics and KPIs.
- Benefit: Ensures accountability and provides insights into the effectiveness of circular initiatives.
- Implementation: Use lifecycle assessment tools and sustainability reporting frameworks to monitor and communicate achievements.
Foster a Culture of Innovation:
- Strategy: Encourage continuous improvement and innovation focused on sustainability.
- Benefit: Drives the development of new materials, processes, and business models that support the circular economy.
- Implementation: Support research and development initiatives that explore new materials, processes, and business models aligned with circular principles.
Leverage Policy and Incentives:
- Strategy: Take advantage of government policies, incentives, and subsidies that support circular economy initiatives.
- Benefit: Reduces the financial burden of transitioning to a circular model and accelerates the adoption of sustainable practices.
- Implementation: Align business practices with regulatory frameworks and seek funding opportunities for sustainable projects.
Case Example: A leading furniture manufacturer transitioned to a circular economy model by redesigning its products for easy disassembly and recycling. They introduced a take-back program where customers could return old furniture for refurbishment or recycling. The company also partnered with suppliers to use recycled materials in new products and adopted a leasing model for office furniture, allowing businesses to upgrade their furnishings without disposing of old items. As a result, the manufacturer reduced material costs by 15%, decreased waste by 30%, and enhanced its brand reputation as a sustainable and responsible company.
Conclusion: Implementing a circular economy model offers significant benefits for manufacturers, including cost savings, enhanced sustainability, and competitive advantage. Transitioning to this model requires strategic planning, collaboration with supply chain partners, investment in sustainable technologies, and a commitment to continuous innovation. By embracing circular principles, manufacturers can create a more sustainable and resilient business, contributing positively to the environment and society.
7. What are the main challenges faced by manufacturers in adopting sustainable manufacturing practices, and how can they overcome them?
Answer:
Main Challenges in Adopting Sustainable Manufacturing Practices:
High Initial Costs:
- Challenge: Implementing sustainable practices often requires significant upfront investments in new technologies, equipment, and training.
- Solution: Seek financial incentives, grants, and subsidies from governments and organizations that support sustainability initiatives. Additionally, adopt a phased implementation approach to spread out costs over time.
Lack of Awareness and Expertise:
- Challenge: Manufacturers may lack the necessary knowledge and expertise to implement sustainable practices effectively.
- Solution: Invest in training programs and hire sustainability experts to guide the transition. Engage with industry associations and participate in sustainability workshops and seminars.
Supply Chain Complexity:
- Challenge: Ensuring sustainability across a complex and global supply chain can be difficult due to varying standards and practices.
- Solution: Collaborate closely with suppliers to establish clear sustainability criteria and provide support for them to meet these standards. Use supply chain management software to monitor and manage sustainability metrics.
Resistance to Change:
- Challenge: Employees and management may resist adopting new sustainable practices due to fear of the unknown or reluctance to change established processes.
- Solution: Foster a culture of sustainability by communicating the benefits, involving employees in decision-making, and recognizing and rewarding sustainable initiatives.
Measurement and Reporting:
- Challenge: Tracking and measuring the impact of sustainable practices can be complex and resource-intensive.
- Solution: Implement robust data collection and management systems to monitor sustainability metrics. Use standardized reporting frameworks like the Global Reporting Initiative (GRI) to ensure consistency and transparency.
Balancing Sustainability with Profitability:
- Challenge: Manufacturers may struggle to balance the costs of sustainable practices with the need to maintain profitability.
- Solution: Identify areas where sustainability can lead to cost savings, such as energy efficiency and waste reduction. Demonstrate the long-term financial benefits of sustainability to stakeholders.
Technological Limitations:
- Challenge: Existing technologies may not support the desired level of sustainability, requiring upgrades or replacements.
- Solution: Invest in research and development to innovate new sustainable technologies. Partner with technology providers to integrate advanced solutions that enhance sustainability.
Regulatory Compliance:
- Challenge: Navigating and complying with diverse and evolving environmental regulations can be challenging.
- Solution: Stay informed about relevant regulations and work with legal experts to ensure compliance. Proactively adopt best practices that exceed regulatory requirements to stay ahead of changes.
Market Pressure and Consumer Expectations:
- Challenge: Meeting increasing consumer demand for sustainable products while maintaining product quality and affordability.
- Solution: Incorporate sustainable design principles to create high-quality, eco-friendly products. Educate consumers about the value of sustainable products to justify any premium pricing.
Integration with Existing Processes:
- Challenge: Integrating sustainable practices into existing manufacturing processes without disrupting operations can be difficult.
- Solution: Conduct thorough planning and pilot programs to test and refine sustainable practices before full-scale implementation. Use process mapping to identify integration points and minimize disruptions.
Strategies to Overcome Challenges:
Leadership Commitment:
- Strategy: Ensure that top management is committed to sustainability and actively supports sustainable initiatives.
- Benefit: Provides direction, resources, and motivation for the entire organization to embrace sustainability.
Stakeholder Engagement:
- Strategy: Involve all stakeholders, including employees, suppliers, customers, and investors, in sustainability efforts.
- Benefit: Builds a shared sense of responsibility and fosters collaboration towards common sustainability goals.
Continuous Improvement:
- Strategy: Adopt a mindset of continuous improvement to regularly assess and enhance sustainability practices.
- Benefit: Ensures that sustainability efforts evolve and adapt to new challenges and opportunities.
Innovation and Technology Adoption:
- Strategy: Embrace innovation and adopt advanced technologies that support sustainable manufacturing.
- Benefit: Enhances efficiency, reduces environmental impact, and creates new opportunities for sustainable growth.
Benchmarking and Best Practices:
- Strategy: Benchmark against industry leaders and adopt best practices in sustainability.
- Benefit: Provides valuable insights and proven strategies to enhance sustainability performance.
Case Example: A mid-sized manufacturing company aimed to implement sustainable practices but faced challenges related to high initial costs and resistance to change among employees. To overcome these challenges, the company secured a government grant to fund energy-efficient equipment upgrades, reducing the financial burden. They also launched an employee engagement program that included training sessions and incentives for sustainable initiatives. By demonstrating the cost savings from reduced energy consumption and involving employees in the sustainability journey, the company successfully integrated sustainable practices, resulting in a 20% reduction in energy usage and improved employee morale.
Conclusion: Adopting sustainable manufacturing practices presents several challenges, including high costs, supply chain complexity, and resistance to change. However, by implementing strategic solutions such as securing financial support, fostering a culture of sustainability, leveraging technology, and engaging stakeholders, manufacturers can overcome these obstacles. Embracing sustainability not only benefits the environment but also enhances operational efficiency, reduces costs, and builds a competitive advantage in the market.
8. How can life cycle assessment (LCA) be utilized to improve sustainability in manufacturing processes?
Answer:
Life Cycle Assessment (LCA) in Sustainable Manufacturing:
Definition of Life Cycle Assessment (LCA): LCA is a systematic methodology used to evaluate the environmental impacts of a product or service throughout its entire life cycle, from raw material extraction and production to use, disposal, and recycling. It provides a comprehensive view of the environmental aspects associated with a product, enabling manufacturers to make informed decisions to enhance sustainability.
How LCA Improves Sustainability in Manufacturing Processes:
Identifying Environmental Hotspots:
- Usage: LCA helps pinpoint stages in the product lifecycle that have the highest environmental impacts, such as energy consumption, emissions, or resource use.
- Improvement: Allows manufacturers to target these hotspots for improvement, optimizing processes to reduce environmental burdens.
Informed Decision-Making:
- Usage: Provides data-driven insights into the environmental performance of different materials, processes, and technologies.
- Improvement: Facilitates the selection of more sustainable options, such as choosing eco-friendly materials or adopting energy-efficient technologies.
Product Design Optimization:
- Usage: Assesses the environmental implications of design choices, including materials, manufacturing methods, and product durability.
- Improvement: Enables the design of products that are easier to recycle, use fewer resources, and have a lower overall environmental footprint.
Supply Chain Management:
- Usage: Evaluates the environmental impact of suppliers and their processes.
- Improvement: Encourages collaboration with suppliers to improve their sustainability practices, ensuring a greener supply chain.
Regulatory Compliance and Reporting:
- Usage: Assists in meeting environmental regulations and standards by providing comprehensive environmental data.
- Improvement: Simplifies compliance reporting and helps avoid legal penalties by ensuring that products meet regulatory requirements.
Benchmarking and Performance Tracking:
- Usage: Allows manufacturers to benchmark their products against industry standards or competitors.
- Improvement: Facilitates the tracking of sustainability performance over time, promoting continuous improvement.
Cost Reduction:
- Usage: Identifies areas where resource use can be minimized, such as reducing material waste or lowering energy consumption.
- Improvement: Leads to cost savings by optimizing resource use and reducing waste disposal expenses.
Enhancing Brand Reputation:
- Usage: Demonstrates a commitment to sustainability through transparent reporting of environmental impacts.
- Improvement: Builds trust with consumers, investors, and other stakeholders, enhancing the company’s reputation and market position.
Steps to Conduct a Life Cycle Assessment:
Goal and Scope Definition:
- Action: Define the purpose of the LCA, the boundaries of the assessment, and the functional unit (e.g., per unit of product).
- Benefit: Ensures that the LCA is focused and relevant to the specific sustainability objectives.
Inventory Analysis:
- Action: Collect data on all inputs and outputs associated with each stage of the product lifecycle, including energy use, materials, emissions, and waste.
- Benefit: Provides a comprehensive dataset for evaluating environmental impacts.
Impact Assessment:
- Action: Analyze the inventory data to assess potential environmental impacts, such as global warming potential, acidification, eutrophication, and resource depletion.
- Benefit: Quantifies the environmental effects of the product, highlighting areas for improvement.
Interpretation:
- Action: Analyze the results, draw conclusions, and make recommendations for enhancing sustainability.
- Benefit: Translates the LCA findings into actionable strategies for reducing environmental impacts.
Case Example: A beverage manufacturer conducted an LCA for its bottled water product. The assessment revealed that the majority of environmental impacts occurred during the packaging stage due to plastic production and transportation. Based on these insights, the company switched to lightweight, recyclable bottles and optimized its transportation routes to reduce emissions. As a result, the LCA showed a 25% reduction in the product’s overall carbon footprint, enhancing the company’s sustainability profile and reducing costs associated with materials and logistics.
Conclusion: Life Cycle Assessment is a powerful tool for improving sustainability in manufacturing by providing a holistic view of a product’s environmental impacts. By identifying key areas for improvement, informing sustainable design and procurement decisions, and supporting regulatory compliance, LCA enables manufacturers to enhance their environmental performance, reduce costs, and build a strong reputation for sustainability.
9. What are the advantages of using eco-friendly materials in manufacturing, and how can manufacturers source these materials effectively?
Answer:
Advantages of Using Eco-Friendly Materials in Manufacturing:
Environmental Protection:
- Advantage: Eco-friendly materials reduce environmental impact by minimizing pollution, conserving natural resources, and lowering carbon emissions.
- Impact: Helps preserve ecosystems, reduce waste, and combat climate change.
Regulatory Compliance:
- Advantage: Using sustainable materials ensures compliance with environmental regulations and standards.
- Impact: Avoids legal penalties, fines, and operational disruptions caused by non-compliance.
Cost Savings:
- Advantage: Many eco-friendly materials, such as recycled or renewable resources, can be cost-effective in the long run.
- Impact: Reduces material costs and waste disposal expenses, enhancing overall profitability.
Market Demand and Competitive Advantage:
- Advantage: Increasing consumer preference for sustainable and ethically produced products drives demand for eco-friendly materials.
- Impact: Enhances brand reputation, attracts environmentally conscious customers, and differentiates products in the marketplace.
Innovation and Product Differentiation:
- Advantage: Incorporating eco-friendly materials fosters innovation in product design and functionality.
- Impact: Leads to the development of unique and high-value products that stand out in the market.
Resource Efficiency:
- Advantage: Eco-friendly materials often require less energy and fewer resources to produce and process.
- Impact: Increases overall manufacturing efficiency and reduces the environmental footprint of production processes.
Long-Term Sustainability:
- Advantage: Sustainable materials ensure the availability of resources for future generations.
- Impact: Promotes the long-term viability of manufacturing operations and supports global sustainability goals.
Enhanced Corporate Image:
- Advantage: Commitment to sustainability through the use of eco-friendly materials improves corporate social responsibility (CSR) credentials.
- Impact: Builds trust with stakeholders, including customers, investors, and employees, fostering loyalty and support.
How Manufacturers Can Source Eco-Friendly Materials Effectively:
Supplier Assessment and Selection:
- Action: Evaluate suppliers based on their sustainability practices, certifications, and environmental performance.
- Implementation: Use criteria such as ISO 14001 certification, fair trade practices, and the use of renewable or recycled materials.
- Benefit: Ensures that materials are sourced responsibly, aligning with the company’s sustainability goals.
Building Strong Supplier Relationships:
- Action: Collaborate closely with suppliers to ensure the consistent supply of eco-friendly materials.
- Implementation: Establish long-term partnerships, provide support for suppliers to improve their sustainability practices, and engage in joint sustainability initiatives.
- Benefit: Enhances the sustainability of the entire supply chain through shared best practices and mutual support.
Sustainable Procurement Policies:
- Action: Develop and implement procurement policies that prioritize the purchase of eco-friendly materials.
- Implementation: Include sustainability criteria in procurement guidelines, requiring the use of environmentally responsible materials.
- Benefit: Creates a structured approach to sourcing that emphasizes sustainability, ensuring that eco-friendly materials are consistently selected.
Utilizing Certification Programs:
- Action: Source materials from suppliers that are certified by recognized sustainability standards.
- Implementation: Look for certifications such as Forest Stewardship Council (FSC), Global Organic Textile Standard (GOTS), and Cradle to Cradle (C2C).
- Benefit: Provides assurance of the sustainability and ethical sourcing of materials, enhancing product credibility.
Diversifying Material Sources:
- Action: Identify and engage with multiple suppliers of eco-friendly materials to ensure a reliable and resilient supply chain.
- Implementation: Avoid dependency on a single supplier by sourcing from various regions and suppliers committed to sustainability.
- Benefit: Reduces the risk of supply chain disruptions and ensures a steady supply of eco-friendly materials.
Investment in Research and Development:
- Action: Invest in R&D to identify and develop new eco-friendly materials that meet product requirements.
- Implementation: Collaborate with research institutions, industry consortia, and material innovators to explore sustainable alternatives.
- Benefit: Expands the range of sustainable materials available, fostering innovation and enhancing product sustainability.
Lifecycle Cost Analysis:
- Action: Conduct lifecycle cost analyses to assess the long-term financial benefits of using eco-friendly materials.
- Implementation: Compare the total cost of ownership, including material costs, energy use, and waste disposal, between conventional and sustainable materials.
- Benefit: Demonstrates the economic viability of eco-friendly materials, justifying their adoption based on long-term cost savings.
Supply Chain Transparency:
- Action: Enhance visibility into the supply chain to ensure the traceability and authenticity of eco-friendly materials.
- Implementation: Utilize technologies like blockchain and supply chain management software to track material origins and certifications.
- Benefit: Ensures that materials are sourced sustainably and ethically, building trust with consumers and stakeholders.
Education and Training:
- Action: Educate procurement teams and other relevant staff about the benefits and sourcing of eco-friendly materials.
- Implementation: Provide training programs and resources to build expertise in sustainable procurement practices.
- Benefit: Empowers employees to make informed decisions that prioritize sustainability in material sourcing.
Continuous Monitoring and Improvement:
- Action: Regularly monitor the performance of eco-friendly materials and suppliers to ensure ongoing compliance and improvement.
- Implementation: Use sustainability metrics and audits to assess material performance and supplier adherence to sustainability standards.
- Benefit: Maintains high standards of sustainability, identifies areas for improvement, and ensures that sourcing practices remain aligned with environmental goals.
Conclusion: Using eco-friendly materials offers numerous advantages, including environmental protection, cost savings, and enhanced market competitiveness. By adopting effective sourcing strategies such as supplier assessment, sustainable procurement policies, certification utilization, and supply chain transparency, manufacturers can successfully integrate eco-friendly materials into their production processes. This transition not only supports sustainability goals but also drives long-term business success and positive societal impact.
10. How can automation and smart technologies enhance sustainable manufacturing practices?
Answer:
Enhancing Sustainable Manufacturing with Automation and Smart Technologies:
Energy Management:
- Enhancement: Automation systems can monitor and control energy usage in real-time.
- Benefit: Optimizes energy consumption, reduces waste, and lowers greenhouse gas emissions by ensuring machines operate only when necessary and at optimal efficiency.
- Example: IoT-enabled machines can adjust their operations based on real-time energy consumption data to minimize energy use.
Waste Reduction:
- Enhancement: Smart technologies can identify and minimize waste generation through precise control and monitoring of manufacturing processes.
- Benefit: Reduces material waste, lowers disposal costs, and minimizes environmental impact by ensuring efficient use of resources.
- Example: Automated systems can optimize material usage, reducing excess and scrap production.
Precision Manufacturing:
- Enhancement: Automation enables high-precision manufacturing, ensuring consistent product quality and reducing defects.
- Benefit: Decreases the need for rework and waste, leading to more sustainable production practices and resource conservation.
- Example: Robotic assembly lines can perform tasks with greater accuracy, minimizing errors and material waste.
Predictive Maintenance:
- Enhancement: Smart sensors and AI algorithms predict equipment failures before they occur.
- Benefit: Minimizes downtime, extends the lifespan of machinery, and reduces the need for premature replacements, contributing to resource efficiency and cost savings.
- Example: AI can predict when machinery needs maintenance, preventing unexpected breakdowns and reducing energy waste.
Supply Chain Optimization:
- Enhancement: Automation and smart technologies enhance supply chain visibility and coordination.
- Benefit: Reduces transportation-related emissions by optimizing routes, improves inventory management to prevent overproduction, and ensures timely deliveries.
- Example: Automated logistics systems can optimize delivery routes to reduce fuel consumption and emissions.
Sustainable Product Design:
- Enhancement: Smart design tools use data analytics to create products that are easier to recycle and have a lower environmental footprint.
- Benefit: Facilitates the development of eco-friendly products that align with circular economy principles, enhancing sustainability throughout the product lifecycle.
- Example: Design software can simulate the recyclability of different materials, aiding in the selection of sustainable options.
Resource Tracking and Traceability:
- Enhancement: Automation systems track the flow of materials and products throughout the manufacturing process.
- Benefit: Ensures responsible sourcing, enhances transparency, and supports compliance with sustainability standards by providing detailed records of material origins and usage.
- Example: Blockchain-integrated systems can provide real-time tracking of materials from suppliers to finished products.
Reduced Water Usage:
- Enhancement: Automated systems monitor and control water usage in manufacturing processes.
- Benefit: Minimizes water waste, ensures efficient usage, and reduces the environmental impact of water consumption.
- Example: Smart sensors can detect leaks and optimize water use in cooling systems.
Enhanced Worker Safety and Well-being:
- Enhancement: Automation takes over hazardous tasks, reducing the risk of workplace accidents.
- Benefit: Promotes a safer work environment, improving worker health and satisfaction, which is a key aspect of social sustainability.
- Example: Automated handling systems can manage heavy lifting, reducing the risk of musculoskeletal injuries among workers.
Data-Driven Sustainability Initiatives:
- Enhancement: Smart technologies collect and analyze vast amounts of data on manufacturing processes and environmental impacts.
- Benefit: Provides actionable insights to continuously improve sustainability practices, set measurable goals, and track progress towards environmental targets.
- Example: Data analytics platforms can identify patterns in energy usage, enabling targeted energy-saving initiatives.
Benefits of Leveraging Industry 4.0 Technologies for Sustainability:
- Enhanced Efficiency: Optimizes resource use, reduces energy consumption, and minimizes waste generation.
- Real-Time Monitoring: Provides immediate insights into environmental performance, enabling swift corrective actions.
- Predictive Capabilities: Anticipates and prevents potential issues that could lead to inefficiencies or environmental harm.
- Data-Driven Decisions: Facilitates informed decision-making based on comprehensive data analysis.
- Improved Product Lifecycle Management: Enhances the design, production, and end-of-life management of products to ensure sustainability.
- Greater Supply Chain Transparency: Ensures responsible sourcing and reduces environmental impacts across the supply chain.
- Innovation and Continuous Improvement: Drives the development of new sustainable practices and technologies, fostering a culture of innovation.
Case Example: A smart electronics manufacturer integrated IoT sensors and AI analytics into its production line to monitor energy usage and material flow in real-time. The data collected was analyzed to identify inefficiencies and optimize operations, resulting in a 20% reduction in energy consumption and a 15% decrease in material waste. Additionally, the company implemented a digital twin of its manufacturing process to simulate and test sustainability initiatives before real-world implementation. This approach not only enhanced the company’s sustainability performance but also reduced operational costs and improved product quality.
Conclusion: Automation and smart technologies play a pivotal role in advancing sustainable manufacturing practices by enhancing energy efficiency, reducing waste, improving precision, and enabling data-driven decision-making. By integrating these technologies, manufacturers can achieve significant environmental, economic, and social benefits, fostering a more sustainable and resilient manufacturing ecosystem. Embracing automation and smart technologies is essential for manufacturers committed to sustainability and long-term operational excellence.
11. How can manufacturers leverage Industry 4.0 technologies to enhance sustainable manufacturing practices?
Answer:
Leveraging Industry 4.0 Technologies for Sustainable Manufacturing:
Internet of Things (IoT):
- Usage: Deploy sensors and connected devices to monitor and optimize manufacturing processes in real-time.
- Benefit: Enhances energy efficiency, reduces waste, and improves resource management by providing accurate data on equipment performance and environmental conditions.
- Example: IoT-enabled machines can adjust their operations based on real-time energy consumption data to minimize energy use.
Artificial Intelligence (AI) and Machine Learning:
- Usage: Utilize AI and machine learning algorithms to analyze data and optimize manufacturing operations.
- Benefit: Improves predictive maintenance, reduces downtime, enhances process efficiency, and minimizes resource consumption by anticipating equipment failures and optimizing production schedules.
- Example: AI can predict when machinery needs maintenance, preventing unexpected breakdowns and reducing energy waste.
Big Data Analytics:
- Usage: Analyze large volumes of data generated from manufacturing processes to identify patterns and trends.
- Benefit: Enables data-driven decision-making, improves process optimization, and supports sustainability initiatives by identifying areas for efficiency improvements.
- Example: Analyzing production data to identify and eliminate inefficiencies that lead to excess energy use or material waste.
Additive Manufacturing (3D Printing):
- Usage: Implement 3D printing for prototyping and production to reduce material waste and enable on-demand manufacturing.
- Benefit: Minimizes material usage, reduces transportation emissions, and allows for the creation of complex, lightweight structures that enhance product sustainability.
- Example: Using 3D printing to produce custom parts as needed, reducing inventory and waste associated with overproduction.
Advanced Robotics and Automation:
- Usage: Integrate advanced robotics to perform precision tasks and automate repetitive processes.
- Benefit: Increases operational efficiency, reduces human error, and optimizes resource use, contributing to lower energy consumption and waste generation.
- Example: Automated systems can optimize material handling and reduce the need for manual intervention, minimizing waste and improving safety.
Digital Twins:
- Usage: Create virtual replicas of manufacturing processes, products, or systems for simulation and optimization.
- Benefit: Allows for the testing of sustainability initiatives in a virtual environment, identifying potential improvements before implementing them in the real world.
- Example: Simulating energy usage in a production line to identify and implement energy-saving measures.
Blockchain Technology:
- Usage: Utilize blockchain for supply chain transparency and traceability.
- Benefit: Ensures the responsible sourcing of materials, verifies sustainability claims, and reduces fraud, enhancing the overall sustainability of the supply chain.
- Example: Tracking the origin and journey of raw materials to ensure they are sourced sustainably and ethically.
Cloud Computing:
- Usage: Employ cloud-based platforms for data storage, processing, and collaboration.
- Benefit: Enhances accessibility and scalability of sustainability data, supports real-time monitoring, and facilitates collaborative sustainability efforts across global operations.
- Example: Using cloud-based dashboards to monitor energy consumption and sustainability metrics in real-time from any location.
Virtual and Augmented Reality (VR/AR):
- Usage: Implement VR and AR for training, maintenance, and process optimization.
- Benefit: Improves efficiency and reduces errors by providing immersive training and real-time guidance, enhancing the sustainability of manufacturing operations.
- Example: AR-assisted maintenance can guide technicians to perform repairs more accurately, reducing downtime and resource use.
Smart Manufacturing Platforms:
- Usage: Integrate comprehensive smart manufacturing platforms that connect various Industry 4.0 technologies.
- Benefit: Enables seamless data flow, enhances process coordination, and supports holistic sustainability strategies by providing a unified view of manufacturing operations.
- Example: A smart manufacturing platform can integrate IoT sensors, AI analytics, and automation systems to optimize production in real-time for sustainability.
Benefits of Leveraging Industry 4.0 Technologies for Sustainability:
- Enhanced Efficiency: Optimizes resource use, reduces energy consumption, and minimizes waste generation.
- Real-Time Monitoring: Provides immediate insights into environmental performance, enabling swift corrective actions.
- Predictive Capabilities: Anticipates and prevents potential issues that could lead to inefficiencies or environmental harm.
- Data-Driven Decisions: Facilitates informed decision-making based on comprehensive data analysis.
- Improved Product Lifecycle Management: Enhances the design, production, and end-of-life management of products to ensure sustainability.
- Greater Supply Chain Transparency: Ensures responsible sourcing and reduces environmental impacts across the supply chain.
- Innovation and Continuous Improvement: Drives the development of new sustainable practices and technologies, fostering a culture of innovation.
Case Example: A smart electronics manufacturer integrated IoT sensors and AI analytics into its production line to monitor energy usage and material flow in real-time. The data collected was analyzed to identify inefficiencies and optimize operations, resulting in a 20% reduction in energy consumption and a 15% decrease in material waste. Additionally, the company implemented a digital twin of its manufacturing process to simulate and test sustainability initiatives before real-world implementation. This approach not only enhanced the company’s sustainability performance but also reduced operational costs and improved product quality.
Conclusion: Industry 4.0 technologies offer powerful tools for enhancing sustainable manufacturing practices. By leveraging IoT, AI, big data, additive manufacturing, robotics, and other advanced technologies, manufacturers can significantly improve their environmental performance, optimize resource use, and drive continuous innovation. Integrating these technologies into manufacturing operations is essential for achieving sustainability goals, reducing environmental impact, and maintaining a competitive edge in the modern industrial landscape.
12. How can manufacturers balance the trade-offs between sustainability and cost in their operations?
Answer:
Balancing Sustainability and Cost in Manufacturing Operations:
1. Conduct Cost-Benefit Analyses:
- Action: Evaluate the financial implications of sustainability initiatives by comparing the costs of implementation with the long-term benefits.
- Benefit: Identifies initiatives that offer a favorable return on investment (ROI), ensuring that sustainability efforts are economically viable.
- Example: Analyzing the upfront costs of installing energy-efficient machinery against the projected savings in energy bills over five years.
2. Prioritize High-Impact Initiatives:
- Action: Focus on sustainability projects that provide significant environmental benefits while offering cost savings, such as energy efficiency and waste reduction.
- Benefit: Maximizes the positive impact on sustainability without incurring excessive costs.
- Example: Implementing a waste recycling program that reduces disposal costs and decreases environmental impact.
3. Implement Lean Manufacturing Principles:
- Action: Adopt lean practices to eliminate waste, improve process efficiency, and reduce costs.
- Benefit: Enhances both sustainability and profitability by optimizing resource use and minimizing waste.
- Example: Streamlining production processes to reduce material waste and lower operational costs.
4. Invest in Energy-Efficient Technologies:
- Action: Upgrade to energy-efficient machinery and systems to lower energy consumption.
- Benefit: Reduces long-term energy costs and decreases the environmental footprint, leading to both financial and sustainability gains.
- Example: Replacing old lighting systems with LED lights to save on electricity bills and reduce energy use.
5. Utilize Renewable Energy Sources:
- Action: Incorporate renewable energy sources such as solar and wind power into manufacturing operations.
- Benefit: Lowers energy costs over time and reduces reliance on fossil fuels, contributing to sustainability goals.
- Example: Installing solar panels to generate a portion of the facility’s electricity needs, reducing energy bills and carbon emissions.
6. Optimize Supply Chain Management:
- Action: Streamline supply chain processes to reduce transportation costs and minimize environmental impact.
- Benefit: Achieves cost savings and enhances sustainability through efficient logistics and reduced emissions.
- Example: Consolidating shipments to reduce the number of trips and fuel consumption, lowering transportation costs and emissions.
7. Foster Supplier Collaboration:
- Action: Work closely with suppliers to implement sustainable practices that can lead to cost reductions, such as bulk purchasing of eco-friendly materials.
- Benefit: Creates a mutually beneficial relationship that supports both cost management and sustainability objectives.
- Example: Negotiating bulk discounts with suppliers for purchasing recycled materials, reducing material costs and promoting sustainability.
8. Implement Circular Economy Practices:
- Action: Adopt circular economy models that focus on recycling, reusing, and refurbishing materials and products.
- Benefit: Reduces material costs, minimizes waste disposal expenses, and promotes sustainability through resource conservation.
- Example: Establishing a take-back program where customers can return used products for refurbishment or recycling, reducing the need for new raw materials.
9. Leverage Government Incentives and Grants:
- Action: Take advantage of government programs that offer financial incentives for implementing sustainable practices.
- Benefit: Lowers the initial cost burden of sustainability initiatives, making them more financially feasible.
- Example: Applying for grants to fund energy-efficient upgrades, reducing the financial strain on the company.
10. Educate and Engage Employees: – Action: Train employees on sustainability practices and encourage their involvement in cost-saving initiatives. – Benefit: Enhances operational efficiency and fosters a culture of sustainability that drives continuous improvement. – Example: Launching an employee suggestion program to identify energy-saving opportunities, leading to both cost reductions and sustainability enhancements.
11. Monitor and Optimize Resource Use: – Action: Use data analytics and monitoring tools to track resource consumption and identify areas for optimization. – Benefit: Ensures efficient use of resources, reducing costs and environmental impact simultaneously. – Example: Implementing an energy management system to monitor and optimize energy use across different departments, identifying areas for improvement and cost savings.
12. Incremental Implementation: – Action: Implement sustainability initiatives gradually rather than all at once. – Benefit: Spreads out costs over time and allows for adjustments based on financial performance and operational impact. – Example: Phasing the adoption of sustainable practices, such as starting with energy-efficient lighting before upgrading machinery, to manage financial and operational impacts effectively.
Strategies to Achieve Balance:
Integrated Sustainability Planning:
- Strategy: Incorporate sustainability goals into the overall business strategy and operational planning.
- Benefit: Ensures that sustainability and cost considerations are addressed together, aligning efforts towards common objectives.
Collaborative Decision-Making:
- Strategy: Involve cross-functional teams in decision-making to consider both sustainability and cost aspects.
- Benefit: Promotes a holistic approach to balancing sustainability with financial performance, ensuring that all perspectives are considered.
Continuous Improvement:
- Strategy: Adopt a mindset of continuous improvement to regularly assess and enhance sustainability practices.
- Benefit: Enables ongoing optimization of both sustainability and cost-efficiency measures, ensuring sustained progress.
Performance Tracking and Reporting:
- Strategy: Monitor the performance of sustainability initiatives and their financial impact.
- Benefit: Provides insights into the effectiveness of initiatives and guides future investments in sustainability, ensuring that efforts are aligned with both sustainability and cost-saving goals.
Case Example: A manufacturing company aimed to reduce its carbon footprint while managing costs. They conducted a cost-benefit analysis of implementing energy-efficient lighting and machinery. The analysis showed that although the initial investment was significant, the long-term energy savings would offset the costs within five years. The company prioritized these high-impact initiatives and phased the implementation to manage expenses. Additionally, they optimized their supply chain to reduce transportation costs and emissions by consolidating shipments and choosing more efficient routes. As a result, the company achieved a 20% reduction in energy consumption, lowered operational costs by 15%, and significantly decreased its carbon emissions, successfully balancing sustainability with cost management.
Conclusion: Balancing sustainability and cost requires a strategic and integrated approach that prioritizes high-impact initiatives, leverages cost-saving opportunities, and fosters collaboration across the organization and supply chain. By conducting thorough analyses, adopting lean and circular practices, and continuously monitoring performance, manufacturers can achieve sustainable operations that are both environmentally responsible and economically viable. This balance not only supports long-term business success but also contributes to global sustainability goals.
Conclusion:
The above thought-provoking questions and detailed answers provide a comprehensive exploration of Sustainable Manufacturing, covering essential topics such as the definition and importance of sustainable manufacturing, energy efficiency, waste reduction, renewable energy integration, green supply chain management, circular economy, eco-friendly materials, Industry 4.0 technologies, life cycle assessment, challenges in adopting sustainable practices, balancing sustainability with cost, and leveraging advanced technologies for sustainability. These questions facilitate a deep understanding of how to implement and optimize sustainable practices in manufacturing, enhancing environmental performance, reducing costs, and building a competitive advantage in the market. Engaging with these questions equips students and professionals with the knowledge and strategies needed to manage sustainable manufacturing operations effectively, drive continuous improvement, and achieve long-term operational excellence in an increasingly eco-conscious and regulated industrial environment.