Smart Manufacturing and Industry 4.0
Smart Manufacturing and Industry 4.0 represent a transformative leap in the way modern factories and industrial systems are designed, operated, and optimized. At the heart of this shift is the integration of advanced digital technologies into traditional industrial and manufacturing technologies, enabling a more agile, connected, and data-driven production environment. These advancements are not simply about automation—they signify a convergence of cyber-physical systems, cloud computing, and the Industrial Internet of Things (IIoT), reshaping how goods are produced and delivered globally.
One of the core enablers of Industry 4.0 is Digital Twin Technology, which allows real-time simulation of processes, enabling manufacturers to predict failures, optimize performance, and improve product quality. When combined with Computer-Integrated Manufacturing (CIM), this approach ensures seamless interaction between design, fabrication, and feedback systems.
The transition to smart manufacturing also intersects with emerging techniques such as Additive Manufacturing (3D Printing) and the adoption of advanced materials and manufacturing technologies. These innovations support mass customization and decentralized production, two defining features of Industry 4.0.
Efficiency plays a central role. Enhancing energy and resource efficiency in manufacturing is a strategic priority, especially in light of global sustainability goals. Smart factories often incorporate sustainable manufacturing principles and environmental stewardship into their digital workflows.
The human component is also crucial. With the growing complexity of automated systems, attention to human factors and ergonomics in manufacturing ensures that systems are designed to support human decision-making and safety. Similarly, collaborative technologies in industrial automation and robotics allow machines and operators to work side-by-side efficiently.
Smart manufacturing extends beyond the shop floor. Strategies such as lean manufacturing and intelligent supply chain management link real-time production data with logistics, minimizing waste and aligning inventory with demand.
Core to these changes are robust design principles and predictive analytics. Fields such as manufacturing quality control and assurance and manufacturing process design and optimization are being enhanced through machine learning and AI-driven monitoring, reducing human error and improving overall system reliability.
Smart manufacturing ecosystems draw on a broad base of engineering disciplines. For example, mechanical engineering provides foundational insight into mechanical systems and materials, while specialties like robotics and automation in mechanical engineering expand into sensor integration and adaptive control. Simultaneously, disciplines such as control systems, thermodynamics and heat transfer, and solid mechanics remain essential for high-performance systems.
Applications of Industry 4.0 principles can already be seen in areas such as automotive engineering and biomechanical engineering, where real-time data, cloud platforms, and digital simulations improve both process and product. Tools such as mechanical design and CAD are now linked directly with smart production workflows.
Ultimately, Smart Manufacturing and Industry 4.0 define a vision for the future of production—intelligent, adaptive, and sustainable. Understanding this ecosystem prepares learners to lead in digital transformation and participate in a new era of industrial innovation.
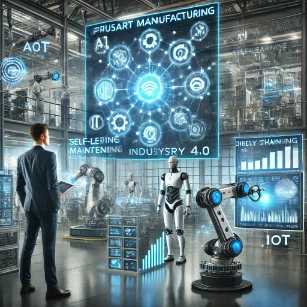
Table of Contents
Core Principles of Smart Manufacturing and Industry 4.0
Interconnectivity
- Definition:
- Devices, machines, systems, and even human interfaces are interconnected through the Internet of Things (IoT), allowing seamless communication and collaboration across all levels of production and operations.
- Applications:
- Smart sensors embedded in machines continuously monitor variables like temperature, vibration, or load capacity and transmit this data to centralized cloud platforms, enabling predictive analytics and proactive maintenance scheduling.
- Industrial IoT networks connect supply chain partners, warehouse systems, and logistics providers to synchronize inventory levels and minimize lead times.
- Smart wearables on workers enhance situational awareness and safety by integrating with centralized dashboards that can alert supervisors in real-time to potential hazards or performance metrics.
Real-Time Data Collection and Analysis
- Definition:
- Using sensors and intelligent devices to gather immediate data from machines, production lines, logistics systems, and even customer usage patterns, enabling rapid, data-driven decisions.
- Applications:
- Manufacturing Execution Systems (MES) collect data at each stage of production to optimize scheduling, resource allocation, and workflow efficiency.
- Advanced analytics platforms use real-time data to detect quality issues early, reducing waste and improving first-pass yield.
- Energy management systems analyze real-time consumption patterns, allowing manufacturers to shift loads or reduce power during peak periods.
Decentralized Decision-Making
- Definition:
- Enabling machines and subsystems to process data and make operational decisions locally, reducing dependency on centralized control systems and enhancing agility in dynamic environments.
- Applications:
- Autonomous mobile robots (AMRs) in warehouses detect traffic congestion and reroute themselves in real time to maintain optimal delivery speeds.
- Machine tools adapt their machining paths autonomously based on real-time feedback from embedded sensors, reducing error rates and improving precision.
- Distributed control systems allow individual modules of a production line to continue operating even if other parts are under maintenance or facing issues.
Cyber-Physical Systems (CPS)
- Definition:
- Systems where physical components (e.g., machines, actuators) are tightly integrated with software, data networks, and computational models, allowing real-world operations to be dynamically controlled and optimized through digital intelligence.
- Applications:
- CPS in packaging lines use feedback loops to adjust fill levels and sealing parameters on-the-fly, ensuring consistent product quality despite fluctuations in input materials or environmental conditions.
- In CNC machining, CPS monitor cutting forces and tool wear in real-time, allowing automatic adjustments to feed rates and spindle speeds to prolong tool life and improve surface finish.
- Smart building systems in factories use CPS to regulate lighting, HVAC, and air filtration based on occupancy and operational needs, improving energy efficiency and worker comfort.
Advanced Automation
- Definition:
- Harnessing the power of robotics, artificial intelligence, and machine learning to perform tasks with greater speed, accuracy, and adaptability than traditional automation systems.
- Applications:
- Collaborative robots (cobots) work safely alongside humans, assisting with repetitive, hazardous, or ergonomically challenging tasks without the need for physical barriers.
- AI-powered visual inspection systems use deep learning algorithms to detect defects on high-speed production lines with precision surpassing that of human inspectors.
- Automated guided vehicles (AGVs) dynamically adjust routes based on facility traffic and delivery priority, reducing delays and optimizing material flow.
Digital Twins
- Definition:
- Virtual representations of real-world systems, processes, or products that continuously receive data from sensors and devices, allowing for simulation, monitoring, and real-time optimization of physical operations.
- Applications:
- Before implementing layout changes in a production plant, digital twins simulate how alterations affect throughput, energy use, and labor efficiency.
- Maintenance teams use digital twins to test repair scenarios on critical equipment, avoiding downtime by identifying the least disruptive strategy.
- In product development, engineers leverage digital twins to predict how new designs will perform under real-world conditions, accelerating innovation cycles.
- As highlighted by McKinsey & Company, digital twins are evolving from isolated tools to living models that continuously improve business outcomes.
Key Technologies Driving Smart Manufacturing and Industry 4.0
Internet of Things (IoT)
- Role:
- IoT serves as the digital nervous system of smart factories by connecting a vast array of sensors, devices, and industrial machines. These interconnected systems gather and share critical data in real-time, enabling manufacturers to monitor performance, detect anomalies, and automate responses without human intervention.
- Applications:
- IoT-enabled production lines offer constant feedback on operating conditions such as temperature, vibration, and pressure, allowing predictive maintenance and reducing unexpected downtime.
- Smart inventory systems utilize RFID tags and IoT scanners to automatically update stock levels, issue replenishment alerts, and prevent material shortages or overstocking.
- IoT facilitates condition-based monitoring in equipment, triggering maintenance only when needed instead of on a fixed schedule, which lowers maintenance costs and extends equipment life.
Big Data and Advanced Analytics
- Role:
- Big data technologies process massive volumes of structured and unstructured data generated from every corner of a smart factory—from machine logs to environmental sensors and operator inputs. Advanced analytics tools then identify hidden patterns, correlations, and outliers to drive data-informed decisions.
- Applications:
- Predictive maintenance models use historical machine data to forecast potential failures and alert technicians before breakdowns occur, reducing unplanned stoppages and improving asset reliability.
- Analytics platforms evaluate yield loss across production lines, pinpointing specific bottlenecks or inefficiencies and providing actionable insights to optimize processes.
- Customer demand trends are analyzed in real-time, enabling flexible production planning and inventory control that closely align with market fluctuations.
Artificial Intelligence (AI) and Machine Learning
- Role:
- AI and machine learning empower machines to learn from historical data, adapt to new conditions, and make autonomous decisions. These technologies dramatically improve the accuracy, speed, and efficiency of industrial processes while supporting innovation in design and quality control.
- Applications:
- AI algorithms detect defects in products by analyzing images or sensor data in milliseconds, vastly outperforming traditional inspection methods.
- Machine learning models are used to forecast customer orders, optimize inventory turnover, and minimize obsolescence.
- AI-driven systems autonomously adjust parameters in production equipment to compensate for input variability, maintaining consistent quality and reducing waste.
Robotics and Automation
- Role:
- Robotics and automation technologies take over tasks that are repetitive, dangerous, or require high precision. These systems not only enhance productivity but also reduce operational risk and improve overall safety.
- Applications:
- Collaborative robots, or cobots, work side-by-side with human operators, performing complex tasks such as screw tightening, welding, or component insertion while ensuring safety through built-in sensors.
- Automated guided vehicles (AGVs) transport materials autonomously across the factory floor, reducing human error and improving logistics efficiency.
- Pick-and-place robotic arms are used in high-speed packaging lines, ensuring uniformity and reducing physical strain on workers.
Cloud Computing
- Role:
- Cloud computing offers virtually unlimited data storage and computational resources, allowing manufacturers to scale operations, store historical data securely, and run powerful simulations without the need for on-premises infrastructure.
- Applications:
- Cloud platforms host centralized dashboards that integrate data from multiple plants, enabling enterprise-wide performance visibility and benchmarking.
- Global manufacturers use cloud-based systems to coordinate supply chains across continents, sharing production schedules, inventory status, and quality data with partners in real time.
- Software-as-a-Service (SaaS) solutions provide remote access to enterprise applications for maintenance planning, ERP, and analytics, enhancing collaboration among distributed teams.
Blockchain
- Role:
- Blockchain introduces a secure and immutable ledger system for recording transactions across a distributed network. It fosters trust and traceability in manufacturing ecosystems, especially in scenarios involving multiple suppliers or regulatory compliance.
- Applications:
- Blockchain tracks the provenance of raw materials from source to final product, ensuring ethical sourcing and preventing counterfeit components from entering the supply chain.
- Smart contracts automate compliance and certification processes, ensuring suppliers meet quality and environmental standards before transactions are executed.
- As detailed by IBM Blockchain for Supply Chain, these technologies enhance transparency and resilience in manufacturing logistics.
Augmented Reality (AR) and Virtual Reality (VR)
- Role:
- AR and VR bridge the physical and digital realms, enabling immersive training environments, real-time guidance, and enhanced visualization of manufacturing operations. They reduce errors, accelerate learning, and improve safety.
- Applications:
- Technicians use AR glasses that project assembly instructions directly onto machinery, minimizing the need for printed manuals and reducing setup time.
- VR simulators train workers in hazardous scenarios such as chemical spills or equipment failures without real-world risk.
- Product designers employ VR environments to prototype factory layouts and ergonomics before construction or reconfiguration.
Edge Computing
- Role:
- Edge computing processes data near its source—on machines or devices—reducing reliance on centralized cloud servers. This local processing is critical for latency-sensitive applications like real-time machine control or safety monitoring.
- Applications:
- Robotic arms executing precision welding require real-time decision-making enabled by edge processors to ensure accuracy and prevent quality issues.
- Condition monitoring systems detect vibrations or temperature spikes and trigger instant responses to prevent damage or halt dangerous operations.
- Edge-enabled cameras perform on-the-spot image analysis for defect detection, transmitting only relevant results to cloud databases.
5G Connectivity
- Role:
- 5G technology offers ultra-high-speed, low-latency communication essential for time-sensitive and data-intensive industrial applications. It underpins the responsiveness and agility of connected manufacturing environments.
- Applications:
- AGVs and mobile robots navigate dynamically across smart warehouses using 5G connectivity to receive updated routing data instantly.
- High-resolution video streams from production lines are transmitted with near-zero lag for remote quality inspections or troubleshooting.
- 5G enables decentralized control of manufacturing equipment, allowing remote technicians to intervene in real-time, regardless of geographic distance.
Applications of Smart Manufacturing and Industry 4.0
Predictive Maintenance
- Definition:
- Predictive maintenance harnesses the power of sensors, real-time monitoring, and machine learning algorithms to forecast potential equipment failures before they disrupt operations. By analyzing performance data such as vibration, temperature, and acoustics, predictive systems can identify anomalies that precede mechanical breakdowns.
- Benefits:
- This approach significantly reduces unplanned downtime, minimizes maintenance costs, and extends the lifespan of critical machinery. It enables companies to move from reactive or scheduled maintenance to condition-based strategies, ensuring that interventions are made only when necessary.
- Example:
- In a high-speed bottling plant, vibration sensors installed on rotary filling machines detect early signs of bearing wear. The system issues alerts to maintenance staff, who replace the components during planned downtime, thereby avoiding costly line stoppages.
Quality Control
- Definition:
- Smart quality control leverages AI-powered machine vision systems and real-time analytics to inspect products continuously during manufacturing. These systems detect even the smallest defects that might go unnoticed by human inspectors, improving overall product reliability and compliance with stringent standards.
- Benefits:
- Automated quality inspection reduces scrap rates, ensures customer satisfaction, and lowers warranty claims. It enables immediate feedback for process adjustments, helping manufacturers maintain consistent quality throughout production.
- Example:
- In electronics manufacturing, high-resolution cameras equipped with AI algorithms scan printed circuit boards (PCBs) for misaligned components and soldering issues. The system flags defective units in real-time, allowing immediate removal from the line and eliminating the risk of defective products reaching end-users.
Flexible Manufacturing Systems
- Definition:
- Flexible manufacturing systems (FMS) incorporate modular machines and reprogrammable automation that allow quick transitions between different products or variants. These systems are enabled by digital twins, advanced robotics, and software-defined control, creating agile production lines.
- Benefits:
- FMS allows manufacturers to respond swiftly to changing market demands without requiring significant downtime or reconfiguration. It enhances product variety, shortens lead times, and increases resource utilization efficiency.
- Example:
- In automotive manufacturing, smart factories can shift production from a sedan to an SUV model on the same assembly line. Robots adapt automatically through software updates, and tooling systems reconfigure themselves based on the digital instructions provided.
Supply Chain Optimization
- Definition:
- Smart manufacturing enables end-to-end visibility and coordination across supply chains by collecting and analyzing data from suppliers, logistics providers, and internal systems. Advanced analytics tools evaluate everything from shipment locations to production schedules in real time.
- Benefits:
- This leads to reduced inventory carrying costs, fewer delays, and enhanced agility in responding to disruptions. Supply chain stakeholders can collaborate more effectively, adjusting procurement and logistics based on live data.
- Example:
- IoT-enabled cargo containers report their GPS location and internal temperature throughout transit. In case of temperature deviations in pharmaceutical shipments, alerts are sent to logistics teams for immediate intervention, reducing spoilage risk. As illustrated by Supply Chain Digital’s Industry 4.0 report, such technologies are redefining supply chain visibility and responsiveness.
Energy Management
- Definition:
- Energy management systems track energy consumption patterns across facilities and use AI to optimize energy distribution, load balancing, and scheduling. Smart grids and meters work in tandem with real-time energy analytics platforms.
- Benefits:
- Companies can reduce energy waste, lower utility bills, and improve environmental sustainability. Integration with renewable sources like solar and wind is facilitated through intelligent load control.
- Example:
- A smart factory equipped with an energy management dashboard identifies peak consumption during the afternoon shift. The system automatically reschedules non-critical processes, such as equipment cleaning cycles, to off-peak hours, thereby reducing overall energy costs by 15% monthly.
Human-Machine Collaboration
- Definition:
- Collaborative robots (cobots) and augmented reality interfaces enable seamless cooperation between humans and machines. Smart interfaces adapt to human behavior, allowing operators to work more safely and intuitively alongside automation.
- Benefits:
- Enhances productivity, reduces injury risks, and makes complex tasks more manageable for workers. It also supports inclusive design by accommodating operators of different skill levels and physical capabilities.
- Example:
- In an aerospace facility, cobots assist workers by holding and aligning heavy turbine components while technicians perform precision fitting. The robot senses human presence and pauses when needed, ensuring a safe collaborative environment.
Mass Customization
- Definition:
- Mass customization enables manufacturers to produce tailored products with the same efficiency as mass production. Technologies such as additive manufacturing, digital twins, and modular production lines support this paradigm shift.
- Benefits:
- Delivers personalized experiences to customers, increases market competitiveness, and reduces waste from overproduction. It fosters brand loyalty by addressing unique consumer needs without sacrificing scalability.
- Example:
- Orthopedic clinics use 3D scanning and printing technologies to produce bespoke prosthetics and insoles that match each patient’s anatomy. Orders are sent digitally to manufacturing units, which automatically fabricate the required devices within hours.
Benefits of Smart Manufacturing and Industry 4.0
- Increased Productivity:
- Smart manufacturing dramatically enhances productivity by leveraging real-time data, autonomous decision-making, and advanced automation. Traditional bottlenecks such as manual inspection or scheduled maintenance are replaced with intelligent systems that anticipate and resolve issues before they cause disruptions. Equipment efficiency is continuously optimized through AI-driven algorithms that adapt to workload variations and material properties.
- For instance, AI-integrated CNC machines can autonomously adjust cutting parameters based on feedback from vibration sensors, reducing cycle times and improving yield. Overall equipment effectiveness (OEE) metrics show measurable gains as downtime and changeover delays are minimized.
- Enhanced Flexibility:
- One of the standout advantages of Industry 4.0 is the ability to swiftly adapt to shifting market demands. Smart factories can reprogram production lines remotely, enabling the manufacturing of different products or configurations with minimal manual intervention. This flexibility supports just-in-time production models and customized manufacturing without lengthy retooling.
- For example, a packaging plant can instantly switch between bottle sizes or labeling schemes using digital control panels and IoT-enabled equipment. This agility allows manufacturers to respond quickly to seasonal demand, new product launches, or customer-specific requirements.
- Improved Quality:
- Quality improvement is achieved through closed-loop systems where smart sensors and machine vision continuously inspect products and adjust process parameters. AI algorithms analyze defect patterns, identify root causes, and recommend process enhancements, thereby reducing error rates and enhancing product reliability.
- In pharmaceutical production, smart equipment verifies capsule fill levels and tablet coating thickness in real time, ensuring compliance with stringent quality standards. Such improvements reduce recalls and regulatory risks while boosting customer trust and satisfaction.
- Cost Savings:
- Operational cost reduction is realized through automation, predictive analytics, and resource efficiency. Smart systems detect and eliminate waste, optimize energy usage, and streamline inventory management. Downtime caused by breakdowns or manual scheduling inefficiencies is substantially reduced.
- For example, automated warehouses employ robotic picking and real-time inventory tracking to reduce labor costs and storage overhead. A report by Deloitte Insights on Industrial IoT highlights how manufacturers adopting IIoT have reported double-digit cost savings across various operational domains.
- Sustainability:
- Smart manufacturing fosters environmentally responsible practices by reducing raw material consumption, lowering carbon emissions, and promoting circular economy models. Advanced monitoring tools track energy usage and waste production, allowing companies to implement targeted sustainability initiatives.
- Additionally, digital twins simulate eco-friendly alternatives in process design, while blockchain-enabled supply chains ensure ethical sourcing. These efforts contribute to corporate social responsibility goals and help meet regulatory compliance for emissions and sustainability standards.
- Enhanced Decision-Making:
- Data-driven decision-making is a cornerstone of Industry 4.0. With continuous access to accurate, real-time data, decision-makers can respond swiftly to market changes, operational anomalies, and strategic opportunities. Dashboards powered by analytics platforms visualize KPIs across production, quality, supply chain, and maintenance domains.
- Machine learning models further aid decision-making by forecasting trends, identifying correlations, and recommending optimal actions. This level of insight enables proactive leadership, minimizes risks, and fosters continuous improvement at all organizational levels.
Challenges in Implementing Smart Manufacturing and Industry 4.0
- High Initial Costs:
- Transitioning to smart manufacturing demands substantial capital investment in sensors, robotics, edge computing infrastructure, and high-speed connectivity. The costs extend beyond equipment to include system integration, software platforms, cybersecurity infrastructure, and workforce development programs. For small and medium-sized enterprises (SMEs), these upfront expenses can be prohibitive, creating a barrier to entry into the Industry 4.0 space.
- Even for large manufacturers, achieving ROI may take years and depends heavily on efficient deployment and utilization. Budget allocation must account for hidden costs such as downtime during upgrades, staff retraining, and ongoing system maintenance.
- Cybersecurity Risks:
- Increased connectivity in smart factories opens up multiple vectors for cyber threats. Industrial IoT (IIoT) devices, cloud-based platforms, and interconnected control systems become potential targets for malicious actors. Ransomware attacks on manufacturing have risen sharply, with significant disruptions to production and supply chains.
- Cybersecurity must evolve from simple firewalls to layered defenses including encryption, multi-factor authentication, intrusion detection systems, and incident response plans. A report from the National Institute of Standards and Technology (NIST) outlines specific frameworks for strengthening cybersecurity in manufacturing environments.
- Data Management:
- Smart manufacturing generates massive volumes of real-time data from sensors, machines, and production systems. Without robust data management strategies, manufacturers face challenges in storing, cleaning, securing, and analyzing this information. Fragmented data silos, inconsistent formats, and lack of standardization hinder effective decision-making.
- Scalable data architecture and skilled data engineers are critical for transforming raw data into actionable insights. Manufacturers must also comply with data governance policies and regulations, especially when operating across borders.
- Workforce Transition:
- The shift to digital manufacturing requires a significant evolution in workforce skills. Traditional roles are being replaced or augmented by new positions in data analytics, AI integration, cybersecurity, and automation maintenance. However, there exists a global shortage of workers proficient in these areas.
- Companies must invest in upskilling and reskilling initiatives through vocational training, certification programs, and partnerships with educational institutions. Ensuring that employees are not left behind in this digital transformation is both a social and operational imperative.
- Interoperability Issues:
- Smart factories often contain a mix of legacy equipment, proprietary software, and modern IoT platforms. Achieving seamless interoperability among these heterogeneous systems is technically complex and costly. Lack of standardized communication protocols can lead to data bottlenecks, miscommunication between machines, and integration failures.
- Open architecture systems, middleware solutions, and industry-wide adoption of standards like OPC UA (Open Platform Communications Unified Architecture) are critical to enabling plug-and-play compatibility across platforms and vendors.
Emerging Trends in Smart Manufacturing and Industry 4.0
Autonomous Manufacturing
- Autonomous manufacturing represents the evolution of fully self-directed production environments where machines, robots, and systems operate independently with minimal or no human intervention. These systems leverage advanced AI algorithms, real-time sensor data, and machine learning to make autonomous decisions regarding workflow adjustments, equipment calibration, quality control, and maintenance scheduling.
- Lights-out factories, also known as “dark factories,” are real-world examples where the entire production process continues without human presence. Such environments maximize productivity, reduce operational costs, and eliminate errors caused by human fatigue or variability. However, achieving this level of autonomy requires an integrated technological ecosystem, robust cybersecurity, and fail-safe protocols to ensure continuity in the face of unexpected disruptions.
Green Manufacturing
- With growing environmental concerns and tightening regulations, green manufacturing has emerged as a critical pillar of Industry 4.0. This trend involves embedding sustainable practices into smart production processes to minimize energy consumption, reduce waste, and limit carbon emissions. From the design phase to end-of-life product management, manufacturers are reevaluating their practices to align with circular economy principles.
- Green smart factories integrate renewable energy sources like solar and wind, utilize energy-efficient equipment, and implement closed-loop recycling systems. For instance, some manufacturers repurpose waste heat for power or recycle process water. Additionally, digital twin models help assess the environmental impact of production decisions before implementation. According to the U.S. EPA’s Sustainable Manufacturing Program, aligning environmental and economic goals can boost competitiveness while promoting ecological responsibility.
AI-Driven Optimization
- Artificial intelligence plays an increasingly pivotal role in smart manufacturing by continuously analyzing both historical and real-time data to uncover patterns, diagnose inefficiencies, and make predictive decisions. AI systems optimize production scheduling, quality assurance, supply chain logistics, and maintenance routines by adapting dynamically to shifting inputs and operational conditions.
- For example, AI algorithms can reschedule production orders in response to fluctuating customer demand or raw material delays. These systems also contribute to defect prevention by identifying deviations in process parameters before they result in faulty products. The agility and intelligence provided by AI make it indispensable for managing the complexity of modern manufacturing networks.
Digital Thread
- The digital thread is a transformative concept that enables the continuous flow of information across the entire lifecycle of a product—from initial concept through design, production, usage, and end-of-life disposal. This seamless data integration creates a traceable, real-time digital narrative that enhances decision-making, traceability, and accountability.
- By closing the loop between product performance and design, manufacturers can implement rapid iterative improvements. For instance, performance data collected from end users can inform future product enhancements, reduce warranty claims, and personalize offerings. The digital thread also facilitates compliance documentation, reduces errors, and supports agile engineering changes across globally distributed teams.
Additive Manufacturing Integration
- As 3D printing matures, its integration into smart manufacturing workflows is reshaping production models. Additive manufacturing allows the fabrication of complex, customized parts with reduced material waste and lead times. When combined with digital design tools and AI, additive processes enable decentralized, on-demand production that is both agile and cost-effective.
- Smart systems can automatically initiate the production of spare parts when inventory levels fall or predictive analytics forecast future demand. This capability is particularly valuable in aerospace, automotive, and healthcare sectors where part obsolescence, downtime, or emergency repairs can be costly. In many advanced factories, additive manufacturing cells are now embedded directly into automated production lines, enabling hybrid production systems that combine subtractive and additive methods for maximum flexibility.
Future Directions for Smart Manufacturing and Industry 4.0
- Hyperconnectivity:
- Hyperconnectivity refers to the advanced integration of all elements in a manufacturing environment—machines, sensors, control systems, humans, and digital platforms—through ubiquitous connectivity. With the proliferation of IoT devices and 5G networks, future factories will experience unprecedented levels of data exchange and inter-device communication. Every stage of the production cycle, from raw material acquisition to post-sale services, will be linked in real time.
- Such comprehensive connectivity enables adaptive responses to production anomalies, predictive resource allocation, and real-time optimization of entire value chains. Smart warehouses, intelligent transportation systems, and connected customer interfaces will also be part of the hyperconnected fabric. This integration not only boosts efficiency and flexibility but also allows for global visibility and control from centralized platforms, accelerating responsiveness and collaboration.
- Collaborative Ecosystems:
- The future of manufacturing lies in interconnected ecosystems where manufacturers, suppliers, distributors, customers, and even competitors co-create value through shared digital infrastructures. These ecosystems operate on principles of transparency, agility, and real-time coordination, enabling more efficient inventory management, faster delivery cycles, and reduced redundancy.
- Blockchain technology is expected to play a major role in ensuring data integrity and trust across participants. For example, smart contracts can automate compliance and payment terms across international supply chains. According to the World Economic Forum, these collaborative ecosystems will become key to achieving resilience and innovation in a rapidly evolving global economy.
- Artificial Intelligence Dominance:
- Artificial Intelligence is poised to become the nerve center of Industry 4.0, taking over increasingly complex tasks that require perception, cognition, and action. AI will orchestrate end-to-end manufacturing—from predictive design and autonomous production planning to intelligent quality control and self-optimizing maintenance.
- Reinforcement learning models will enable machines to improve performance autonomously through trial and feedback. Deep learning systems will extract insights from unstructured data like images and voice inputs to identify defects, detect anomalies, or improve human-machine collaboration. Ultimately, AI will transcend its current supportive role to become the primary decision-making entity across digital factories.
- Quantum Computing:
- Quantum computing promises to revolutionize manufacturing by solving complex optimization and simulation problems that are intractable for classical computers. For instance, quantum algorithms could determine the optimal layout for a manufacturing plant, sequence production tasks with billions of variables, or simulate molecular behavior for advanced materials development.
- While the technology is still in its early stages, early prototypes are already demonstrating potential in logistics, materials science, and AI model training. Future factories may use quantum computing to perform real-time scenario simulations that improve decision-making under uncertainty, enhance energy efficiency, and accelerate product development cycles.
- Edge-to-Cloud Integration:
- Edge computing allows for low-latency data processing close to where it is generated—on factory floors, in robots, or on smart machines—while cloud computing provides scalable analytics, storage, and centralized coordination. The integration of these two computing paradigms will define the next wave of smart manufacturing capabilities.
- For example, edge devices can make instant safety-related decisions without needing to consult the cloud, while cloud platforms analyze long-term performance trends across facilities. This architecture ensures reliability, scalability, and agility in managing vast manufacturing ecosystems. Moreover, it enables hybrid AI solutions, where real-time models are run at the edge and periodically refined in the cloud, striking a balance between responsiveness and strategic optimization.
Why Study Smart Manufacturing and Industry 4.0
Digitizing and Automating Manufacturing
Smart manufacturing uses digital technologies to enhance production agility, quality, and visibility. Students learn how sensors, automation, and connectivity transform factories into intelligent systems. This drives real-time decision-making and productivity.
Cyber-Physical Systems and IoT
Students explore how physical machines are integrated with digital systems through the Internet of Things (IoT). These systems enable remote monitoring, control, and optimization. This creates smarter, safer, and more responsive operations.
Big Data and Advanced Analytics
The course introduces students to data collection, storage, and analytics in manufacturing. They learn how to extract insights from large datasets to improve processes and prevent issues. This supports predictive and prescriptive decision-making.
Cloud Platforms and Digital Integration
Students study how cloud computing enables collaboration, scalability, and remote access to data. They learn how digital platforms integrate systems from design to delivery. This enables seamless and transparent supply chains.
Shaping the Future of Manufacturing
Smart manufacturing empowers flexible, customized, and sustainable production. Students prepare to lead innovation in Industry 4.0 with interdisciplinary skills. This field offers exciting opportunities at the frontier of technology and industry.
Smart Manufacturing and Industry 4.0: Conclusion
Smart Manufacturing and Industry 4.0 represent a fundamental transformation in the way products are designed, produced, and distributed. Unlike previous industrial revolutions that focused on mechanization, electrification, and automation, this fourth wave integrates digital intelligence into every facet of manufacturing, enabling machines, systems, and humans to operate in an interconnected, data-driven environment. The result is a manufacturing paradigm that is not only more efficient but also significantly more responsive, adaptive, and resilient in the face of changing market demands and global disruptions.
At the core of Smart Manufacturing are technologies such as the Internet of Things (IoT), artificial intelligence (AI), robotics, and digital twins. These tools allow for continuous data collection and real-time analytics, enabling predictive maintenance, automated quality control, and demand-driven production scheduling. For example, digital twins—virtual representations of physical processes—allow manufacturers to simulate operational changes before implementing them, reducing risk and downtime. AI-driven algorithms detect anomalies in product quality or energy usage patterns, facilitating swift corrective actions without human intervention.
Smart factories also prioritize sustainability and energy efficiency. Advanced monitoring systems track environmental metrics such as carbon emissions, water usage, and waste production. By optimizing operations with real-time data, manufacturers can reduce their ecological footprint while also improving profitability. Furthermore, flexible production lines that incorporate robotics and modular automation enable rapid reconfiguration, allowing businesses to respond swiftly to market fluctuations, customized orders, or supply chain disruptions. This flexibility is critical in today’s era of mass customization and high consumer expectations.
Another key element of Industry 4.0 is the democratization of manufacturing through decentralized and collaborative ecosystems. Edge computing and 5G connectivity facilitate low-latency decision-making at the source, while cloud platforms provide global scalability and oversight. This hybrid approach ensures that both local and enterprise-wide objectives are met efficiently. Workforce development is also central to the success of Smart Manufacturing. Employees are increasingly working alongside collaborative robots (cobots) and using AR/VR interfaces for training, troubleshooting, and real-time process adjustments. These advances support a safer, more skilled, and more empowered labor force.
As adoption accelerates globally, the competitive advantage of smart manufacturing becomes increasingly evident. Organizations that embrace these technologies are not only achieving lower production costs and shorter time-to-market but also setting new standards in product quality, innovation, and sustainability. Governments and industry leaders are recognizing this shift and investing in infrastructure and policy frameworks to support digital transformation. According to McKinsey & Company, companies that implement smart factory initiatives can increase productivity by up to 30% while significantly reducing waste and energy consumption.
In conclusion, Smart Manufacturing and Industry 4.0 are ushering in a new era of industrial excellence. By embedding intelligence, connectivity, and adaptability into manufacturing processes, these paradigms lay the foundation for sustainable growth, economic resilience, and technological leadership. As industries continue to evolve in response to digital pressures and environmental challenges, the principles of smart manufacturing will remain vital in shaping the factories of the future and ensuring global competitiveness in the years to come.
Smart Manufacturing and Industry 4.0: Review Questions with Detailed Answers
1. What is Industry 4.0, and how does it revolutionize modern manufacturing?
Answer:
Industry 4.0, also known as the Fourth Industrial Revolution, refers to the integration of digital technologies into manufacturing processes. It encompasses advancements such as the Internet of Things (IoT), artificial intelligence (AI), robotics, big data analytics, and cloud computing. Industry 4.0 revolutionizes modern manufacturing by enabling smarter, more efficient, and highly automated production systems. Key benefits include increased productivity, enhanced flexibility, improved quality, reduced operational costs, and the ability to quickly adapt to changing market demands. By leveraging real-time data and interconnected systems, Industry 4.0 facilitates predictive maintenance, optimized supply chains, and personalized manufacturing, thereby transforming the traditional manufacturing landscape into a more agile and intelligent ecosystem.
2. How do IoT and connected devices contribute to Smart Manufacturing under Industry 4.0?
Answer:
The Internet of Things (IoT) and connected devices are fundamental components of Smart Manufacturing within the Industry 4.0 framework. IoT enables the seamless connectivity of machines, sensors, and devices across the manufacturing floor, allowing for real-time data collection and communication. This connectivity facilitates several key contributions:
Real-Time Monitoring: Sensors on machinery track performance metrics such as temperature, vibration, and speed, enabling continuous monitoring of equipment health and process conditions.
Predictive Maintenance: By analyzing data from connected devices, manufacturers can predict when equipment is likely to fail, allowing for timely maintenance and reducing unplanned downtime.
Enhanced Efficiency: IoT devices optimize production workflows by providing accurate data on resource utilization, enabling better scheduling, and minimizing waste.
Supply Chain Integration: Connected devices facilitate end-to-end visibility across the supply chain, improving coordination with suppliers, reducing lead times, and enhancing inventory management.
Data-Driven Decision Making: The vast amount of data generated by IoT devices is analyzed using big data analytics and AI, providing insights that drive strategic decisions and continuous improvement.
Overall, IoT and connected devices empower manufacturers to create more responsive, efficient, and intelligent production environments, significantly enhancing the capabilities and competitiveness of manufacturing operations under Industry 4.0.
3. What role does artificial intelligence (AI) play in optimizing manufacturing processes in Industry 4.0?
Answer:
Artificial Intelligence (AI) plays a pivotal role in optimizing manufacturing processes within the Industry 4.0 paradigm by enabling smarter, more adaptive, and highly efficient operations. Key roles of AI in manufacturing include:
Predictive Maintenance: AI algorithms analyze data from machinery sensors to predict potential failures before they occur, allowing for proactive maintenance and reducing downtime.
Quality Control: AI-powered computer vision systems inspect products in real-time, identifying defects with higher accuracy and speed than manual inspections, thus ensuring consistent product quality.
Supply Chain Optimization: AI enhances supply chain management by forecasting demand, optimizing inventory levels, and improving logistics, resulting in reduced costs and increased responsiveness.
Process Automation: AI-driven robots and automated systems handle complex tasks with precision, increasing production speed and reducing human error.
Energy Management: AI optimizes energy usage by analyzing consumption patterns and adjusting processes to minimize energy waste, leading to cost savings and sustainability.
Customization and Flexibility: AI enables mass customization by quickly adapting production processes to meet specific customer requirements without sacrificing efficiency.
Data Analytics and Insights: AI analyzes vast amounts of data to uncover patterns and insights that inform strategic decisions, driving continuous improvement and innovation in manufacturing processes.
By integrating AI into manufacturing, Industry 4.0 fosters a more intelligent and efficient production environment, enhancing overall operational performance, reducing costs, and enabling manufacturers to remain competitive in a rapidly evolving market.
4. How does additive manufacturing (3D printing) fit into the framework of Industry 4.0?
Answer:
Additive manufacturing, commonly known as 3D printing, is a key component of Industry 4.0, integrating seamlessly into the digital and automated manufacturing landscape. Its role within Industry 4.0 includes:
Customization and Flexibility: Additive manufacturing allows for the production of highly customized products without the need for expensive tooling, enabling manufacturers to meet specific customer requirements and adapt quickly to changing demands.
Rapid Prototyping: It facilitates the quick creation of prototypes, reducing the time and cost associated with product development cycles and accelerating innovation.
Complex Geometries: 3D printing enables the production of complex and lightweight structures that are difficult or impossible to achieve with traditional manufacturing methods, enhancing product performance and material efficiency.
On-Demand Production: Additive manufacturing supports on-demand production, reducing the need for large inventories and allowing for just-in-time manufacturing practices.
Integration with Digital Systems: It works seamlessly with digital design and simulation tools, allowing for real-time adjustments and optimizations in the manufacturing process.
Sustainability: Additive manufacturing minimizes material waste by building products layer by layer, improving resource utilization and reducing the environmental impact of production.
Supply Chain Optimization: By enabling decentralized production, additive manufacturing reduces dependence on centralized manufacturing facilities and long supply chains, enhancing resilience and reducing lead times.
In the Industry 4.0 framework, additive manufacturing complements other technologies such as IoT, AI, and robotics, contributing to a more integrated, flexible, and efficient manufacturing ecosystem. It empowers manufacturers to innovate, respond swiftly to market changes, and produce high-quality, customized products with greater efficiency.
5. What is the significance of data analytics in Smart Manufacturing and Industry 4.0?
Answer:
Data analytics is a cornerstone of Smart Manufacturing and Industry 4.0, playing a crucial role in transforming raw data into actionable insights that drive informed decision-making and continuous improvement. The significance of data analytics in this context includes:
Enhanced Decision-Making:
- Significance: Data analytics provides real-time insights into manufacturing operations, enabling managers to make informed decisions based on accurate and timely information.
- Impact: Improves operational efficiency, optimizes resource allocation, and enhances strategic planning.
Predictive Maintenance:
- Significance: Analyzing data from machinery sensors helps predict potential equipment failures before they occur.
- Impact: Reduces unplanned downtime, extends the lifespan of equipment, and lowers maintenance costs by enabling proactive maintenance scheduling.
Process Optimization:
- Significance: Data analytics identifies inefficiencies and bottlenecks in manufacturing processes.
- Impact: Enables targeted improvements that enhance productivity, reduce cycle times, and minimize waste.
Quality Improvement:
- Significance: Analyzing quality-related data helps identify trends and root causes of defects.
- Impact: Facilitates continuous quality enhancement, reducing defect rates, and ensuring consistent product quality.
Supply Chain Management:
- Significance: Data analytics enhances visibility and coordination across the supply chain.
- Impact: Improves inventory management, optimizes logistics, and ensures timely delivery of materials and products.
Energy Efficiency:
- Significance: Monitoring and analyzing energy consumption data helps identify opportunities for energy savings.
- Impact: Reduces operational costs and supports sustainability initiatives by minimizing energy waste.
Customization and Personalization:
- Significance: Data analytics enables the analysis of customer preferences and market trends.
- Impact: Supports mass customization and personalized manufacturing, meeting specific customer demands more effectively.
Risk Management:
- Significance: Data analytics assesses and mitigates risks by identifying potential disruptions and vulnerabilities in manufacturing processes.
- Impact: Enhances operational resilience and ensures smoother production continuity.
Innovation and Development:
- Significance: Analyzing data from various sources fosters innovation by uncovering new opportunities and areas for development.
- Impact: Drives the creation of new products, services, and manufacturing techniques, keeping the organization competitive.
Compliance and Reporting:
- Significance: Data analytics ensures that manufacturing processes comply with industry standards and regulatory requirements.
- Impact: Simplifies reporting, reduces the risk of non-compliance penalties, and enhances the organization’s credibility.
Benefits of Big Data and Analytics in Industry 4.0:
- Improved Efficiency: Streamlines operations by identifying and eliminating inefficiencies.
- Enhanced Quality: Ensures consistent product quality through continuous monitoring and improvement.
- Cost Savings: Reduces costs associated with defects, maintenance, and energy consumption.
- Innovation: Drives innovation by uncovering new opportunities and insights from data.
- Agility: Enables manufacturers to quickly adapt to changing market conditions and customer demands.
- Competitive Advantage: Provides a data-driven approach that enhances the organization’s ability to compete effectively in the market.
Case Example: A manufacturing company implemented a big data analytics platform to analyze data from its production lines. By leveraging predictive analytics, they identified patterns indicating early signs of equipment wear. This allowed them to schedule maintenance before failures occurred, reducing downtime by 40% and saving significant maintenance costs. Additionally, process optimization based on data insights led to a 25% increase in production efficiency and improved product quality, resulting in higher customer satisfaction and increased sales.
Conclusion: Data analytics is integral to the success of Smart Manufacturing and Industry 4.0, providing the foundation for intelligent and efficient manufacturing operations. By leveraging data-driven insights, manufacturers can optimize processes, improve quality, reduce costs, enhance customer satisfaction, and drive continuous innovation, ultimately achieving a competitive advantage in the market.
6. How do robotics and automation technologies enhance production efficiency in Industry 4.0?
Answer:
Robotics and automation technologies are fundamental enablers of Industry 4.0, significantly enhancing production efficiency through increased speed, precision, and reliability. Their integration into manufacturing processes brings several key benefits:
Increased Productivity:
- Enhancement: Robots and automated systems can operate continuously without fatigue, leading to higher production rates compared to manual labor.
- Impact: Increases overall output and meets growing demand more effectively.
Precision and Consistency:
- Enhancement: Automation ensures high levels of precision and repeatability in manufacturing processes.
- Impact: Reduces defects and variability, leading to superior product quality and reliability.
Cost Reduction:
- Enhancement: Automation minimizes labor costs and reduces the likelihood of human errors.
- Impact: Lowers overall production costs and enhances profitability.
Safety Improvement:
- Enhancement: Robots can handle hazardous tasks, such as working with toxic materials or performing heavy lifting.
- Impact: Reduces workplace accidents and improves overall safety conditions for human workers.
Flexibility and Scalability:
- Enhancement: Modern robotic systems are programmable and adaptable to different tasks and product types.
- Impact: Facilitates quick adjustments to production lines and scalability to meet changing market demands.
Data Integration and Analytics:
- Enhancement: Automated systems can collect and transmit data on performance metrics in real-time.
- Impact: Supports data-driven decision-making, process optimization, and continuous improvement initiatives.
Resource Optimization:
- Enhancement: Automation optimizes the use of materials and energy through precise control of manufacturing processes.
- Impact: Reduces waste, lowers energy consumption, and promotes sustainable manufacturing practices.
Enhanced Supply Chain Coordination:
- Enhancement: Automation integrates seamlessly with supply chain systems, improving synchronization and flow of materials.
- Impact: Enhances overall supply chain efficiency, reducing lead times and ensuring timely production.
Rapid Prototyping and Innovation:
- Enhancement: Automation facilitates the rapid production of prototypes and small batches.
- Impact: Accelerates product development cycles and supports innovation by enabling quick iterations and testing.
Employee Augmentation:
- Enhancement: Robots and automated systems can complement human workers, handling repetitive or strenuous tasks while humans focus on more complex and creative activities.
- Impact: Enhances workforce efficiency and job satisfaction by allowing employees to engage in higher-value tasks.
Case Example: A car manufacturer integrated automated robotic arms into its assembly line to handle welding and painting tasks. This integration resulted in a 30% increase in production speed, a 25% reduction in defects, and a 20% decrease in operational costs. Additionally, the automation improved workplace safety by minimizing human exposure to hazardous processes, demonstrating the significant impact of robotics and automation on production efficiency.
Conclusion: Robotics and automation technologies are essential components of Industry 4.0, driving substantial improvements in production efficiency, product quality, and operational costs. By leveraging these technologies, manufacturers can achieve higher productivity, enhanced safety, greater flexibility, and sustained competitive advantage in a rapidly evolving industrial landscape.
7. What are the key challenges faced by manufacturers in implementing Smart Manufacturing and Industry 4.0 technologies, and how can they be addressed?
Answer:
Implementing Smart Manufacturing and Industry 4.0 technologies presents several challenges for manufacturers. Addressing these challenges is essential for successful integration and realization of the benefits associated with Industry 4.0. The key challenges and potential solutions include:
High Initial Investment Costs:
- Challenge: Significant capital investment is required for acquiring advanced technologies, upgrading infrastructure, and training employees.
- Solution: Manufacturers can adopt a phased implementation approach, starting with pilot projects to demonstrate value and secure funding. Leveraging government grants, incentives, and financing options can also mitigate financial burdens.
Cybersecurity Risks:
- Challenge: Increased connectivity and data exchange heighten the risk of cyberattacks and data breaches.
- Solution: Implement robust cybersecurity measures, including firewalls, encryption, access controls, and regular security audits. Training employees on cybersecurity best practices and developing incident response plans are also crucial.
Integration with Legacy Systems:
- Challenge: Integrating new Industry 4.0 technologies with existing legacy systems can be complex and resource-intensive.
- Solution: Use middleware and integration platforms to facilitate seamless communication between old and new systems. Additionally, conducting thorough compatibility assessments and planning for system upgrades can ease integration challenges.
Skill Gaps and Workforce Readiness:
- Challenge: The adoption of advanced technologies requires new skill sets that may be lacking in the current workforce.
- Solution: Invest in comprehensive training and development programs to upskill employees. Partnering with educational institutions and providing continuous learning opportunities can bridge skill gaps.
Data Management and Analysis:
- Challenge: Handling the vast amount of data generated by smart manufacturing technologies can overwhelm existing data management systems.
- Solution: Implement advanced data management platforms and utilize big data analytics tools to efficiently store, process, and analyze data. Establishing clear data governance policies ensures data quality and accessibility.
Change Management and Organizational Culture:
- Challenge: Resistance to change and a lack of supportive organizational culture can impede the adoption of new technologies.
- Solution: Foster a culture of innovation and continuous improvement by involving employees in the transition process. Communicate the benefits of Industry 4.0, provide incentives for adoption, and ensure leadership support to drive change.
Interoperability and Standardization:
- Challenge: Lack of standardized protocols and interoperability between different technologies and devices can hinder integration efforts.
- Solution: Adopt industry standards and protocols to ensure compatibility and interoperability. Participating in industry consortia and collaborating with technology providers can also promote standardization.
Scalability and Flexibility:
- Challenge: Ensuring that smart manufacturing technologies can scale with business growth and adapt to changing requirements is essential.
- Solution: Choose scalable and flexible technologies that can grow with the organization. Modular and cloud-based solutions offer the adaptability needed to accommodate future expansions and evolving needs.
Return on Investment (ROI) Uncertainty:
- Challenge: Unclear or uncertain ROI can make it difficult to justify the investment in smart manufacturing technologies.
- Solution: Conduct thorough ROI analyses and establish clear metrics for measuring success. Piloting technologies and gathering data on performance improvements can help demonstrate value and secure stakeholder buy-in.
Supply Chain Complexity:
- Challenge: Integrating smart manufacturing with complex and global supply chains can complicate operations and coordination.
- Solution: Enhance supply chain visibility through IoT and data analytics, improve collaboration with suppliers, and adopt flexible supply chain strategies to manage complexity effectively.
Conclusion: Manufacturers face numerous challenges in implementing Smart Manufacturing and Industry 4.0 technologies, including financial, technical, and organizational obstacles. By adopting strategic approaches such as phased implementation, robust cybersecurity measures, comprehensive training programs, and fostering a culture of continuous improvement, manufacturers can overcome these challenges and successfully integrate Industry 4.0 technologies. Addressing these challenges effectively enables organizations to realize the full potential of Smart Manufacturing, driving efficiency, innovation, and competitive advantage in the modern industrial landscape.
8. What is the role of Big Data and analytics in Industry 4.0, and how do they impact decision-making in manufacturing?
Answer:
Big Data and analytics are integral to Industry 4.0, playing a crucial role in transforming raw data into valuable insights that enhance decision-making in manufacturing. Their role and impact include:
Data Collection and Integration:
- Role: Big Data encompasses the vast volumes of structured and unstructured data generated by various sources, including IoT sensors, machines, production systems, and supply chain activities.
- Impact: Enables comprehensive data collection and integration, providing a holistic view of manufacturing operations.
Real-Time Monitoring and Control:
- Role: Analytics tools process and analyze real-time data to monitor production processes continuously.
- Impact: Allows for immediate detection of anomalies, enabling prompt corrective actions to maintain process stability and quality.
Predictive Maintenance:
- Role: Analyzing historical and real-time data to predict equipment failures before they occur.
- Impact: Reduces unplanned downtime, extends the lifespan of machinery, and lowers maintenance costs by enabling proactive maintenance scheduling.
Process Optimization:
- Role: Utilizing data analytics to identify inefficiencies and optimize manufacturing processes.
- Impact: Enhances operational efficiency, reduces cycle times, minimizes waste, and improves overall productivity.
Quality Assurance and Control:
- Role: Analyzing quality data to identify patterns, trends, and root causes of defects.
- Impact: Facilitates continuous quality improvement, reduces defect rates, and ensures consistent product quality.
Supply Chain Optimization:
- Role: Leveraging data analytics to enhance supply chain visibility, forecast demand, and optimize inventory levels.
- Impact: Improves supply chain efficiency, reduces lead times, and ensures timely availability of materials, supporting Just-In-Time (JIT) production.
Customer Insights and Personalization:
- Role: Analyzing customer data and market trends to understand preferences and demand patterns.
- Impact: Enables manufacturers to tailor products and services to meet specific customer needs, enhancing customer satisfaction and loyalty.
Energy Management:
- Role: Monitoring and analyzing energy consumption data to identify opportunities for energy savings.
- Impact: Reduces energy costs, supports sustainability initiatives, and minimizes the environmental impact of manufacturing operations.
Strategic Decision-Making:
- Role: Providing data-driven insights that inform strategic business decisions related to production planning, resource allocation, and market expansion.
- Impact: Enhances the accuracy and effectiveness of decision-making, leading to better business outcomes and competitive advantage.
Risk Management:
- Role: Identifying potential risks and vulnerabilities through data analysis.
- Impact: Enables proactive risk mitigation strategies, ensuring smoother and more resilient manufacturing operations.
Benefits of Big Data and Analytics in Industry 4.0:
- Improved Efficiency: Streamlines operations by identifying and eliminating inefficiencies.
- Enhanced Quality: Ensures consistent product quality through continuous monitoring and improvement.
- Cost Savings: Reduces costs associated with defects, maintenance, and energy consumption.
- Innovation: Drives innovation by uncovering new opportunities and insights from data.
- Agility: Enables manufacturers to quickly adapt to changing market conditions and customer demands.
- Competitive Advantage: Provides a data-driven approach that enhances the organization’s ability to compete effectively in the market.
Case Example: A manufacturing company implemented a big data analytics platform to analyze data from its production lines. By leveraging predictive analytics, they identified patterns indicating early signs of equipment wear. This allowed them to schedule maintenance before failures occurred, reducing downtime by 40% and saving significant maintenance costs. Additionally, process optimization based on data insights led to a 25% increase in production efficiency and improved product quality, resulting in higher customer satisfaction and increased sales.
Conclusion: Big Data and analytics are transformative forces in Industry 4.0, enabling manufacturers to harness vast amounts of data for informed decision-making, process optimization, and continuous improvement. By integrating big data analytics into their operations, manufacturers can enhance efficiency, quality, and competitiveness, ultimately achieving a competitive advantage in the market.
9. How do collaborative robots (cobots) differ from traditional industrial robots, and what advantages do they offer in Smart Manufacturing?
Answer:
Collaborative robots, commonly known as cobots, differ from traditional industrial robots in several key aspects, including their design, functionality, interaction capabilities, and intended use within manufacturing environments. The advantages they offer in Smart Manufacturing are substantial, enhancing flexibility, safety, and efficiency.
Differences Between Cobots and Traditional Industrial Robots:
Aspect | Collaborative Robots (Cobots) | Traditional Industrial Robots |
---|---|---|
Design and Size | Smaller, lightweight, and often more flexible | Larger and more rigid, designed for heavy-duty tasks |
Operation Mode | Designed to work alongside humans safely | Typically operate in segregated, fenced-off areas |
Safety Features | Equipped with sensors and force-limiting technology to ensure safe human-robot interaction | Require safety cages and barriers to prevent human contact |
Programming and Use | Easy to program and reconfigure for various tasks | Require specialized programming and are often task-specific |
Flexibility | Highly adaptable and capable of handling multiple tasks | Primarily designed for repetitive, fixed tasks |
Cost | Generally more affordable and accessible for small to medium-sized enterprises (SMEs) | Higher initial investment, often suited for large-scale operations |
Integration | Easily integrated into existing workflows without extensive modifications | Often require significant changes to production lines for integration |
Learning Capability | Often equipped with AI and machine learning for improved adaptability | Limited adaptability and learning capabilities |
Advantages of Cobots in Smart Manufacturing:
Enhanced Flexibility:
- Advantage: Cobots can be easily reprogrammed and redeployed for different tasks, allowing manufacturers to adapt quickly to changing production needs.
- Impact: Increases operational agility and supports diverse manufacturing processes without significant downtime.
Improved Safety:
- Advantage: Cobots are designed to work safely alongside human workers, with features such as force sensing and collision detection.
- Impact: Reduces the risk of workplace injuries, enhances worker safety, and promotes a collaborative working environment.
Cost-Effectiveness:
- Advantage: Cobots are generally more affordable and require less infrastructure investment compared to traditional industrial robots.
- Impact: Makes automation accessible to small and medium-sized enterprises, enabling wider adoption of smart manufacturing practices.
Increased Productivity:
- Advantage: Cobots can handle repetitive and mundane tasks, allowing human workers to focus on more complex and value-added activities.
- Impact: Boosts overall productivity and efficiency by optimizing the division of labor between humans and robots.
Ease of Integration:
- Advantage: Cobots are designed to integrate seamlessly into existing production lines with minimal modifications.
- Impact: Facilitates smoother and faster implementation of automation technologies, reducing downtime and disruption.
Enhanced Precision and Consistency:
- Advantage: Cobots perform tasks with high precision and consistency, ensuring quality and reducing variability in production.
- Impact: Improves product quality, reduces defects, and enhances customer satisfaction.
Scalability:
- Advantage: Cobots can be easily scaled up or down based on production demands, allowing manufacturers to respond to market fluctuations.
- Impact: Provides the flexibility to expand or contract operations without significant capital investment.
Employee Satisfaction:
- Advantage: Cobots take over physically demanding and repetitive tasks, reducing worker fatigue and improving job satisfaction.
- Impact: Enhances employee morale and retention by allowing workers to engage in more fulfilling and creative tasks.
Case Example: A small electronics manufacturer implemented cobots to handle component assembly tasks. The cobots worked alongside human operators, performing repetitive and precise assembly steps. This integration led to a 30% increase in production speed, a 20% reduction in assembly errors, and improved worker satisfaction as employees could focus on quality control and innovation rather than repetitive tasks.
Conclusion: Collaborative robots offer significant advantages over traditional industrial robots, particularly in the context of Smart Manufacturing and Industry 4.0. Their flexibility, safety, cost-effectiveness, and ease of integration make them ideal for enhancing productivity and quality in modern manufacturing environments. By leveraging cobots, manufacturers can create more adaptable, efficient, and worker-friendly production systems, driving operational excellence and competitive advantage.
10. What are the environmental implications of adopting Smart Manufacturing and Industry 4.0 technologies, and how can they contribute to sustainability?
Answer:
Adopting Smart Manufacturing and Industry 4.0 technologies has significant environmental implications, offering numerous opportunities to enhance sustainability and reduce the ecological footprint of manufacturing operations. These technologies enable more efficient resource utilization, waste reduction, and energy conservation, contributing to greener and more sustainable manufacturing practices.
Environmental Implications and Contributions to Sustainability:
Energy Efficiency:
- Implication: Smart Manufacturing technologies such as IoT sensors and AI-driven energy management systems optimize energy usage.
- Contribution: Reduces overall energy consumption, lowers greenhouse gas emissions, and decreases operational costs through more efficient energy use.
Waste Reduction:
- Implication: Data analytics and process optimization tools identify and eliminate waste in production processes.
- Contribution: Minimizes material waste, reduces landfill usage, and conserves natural resources, leading to more sustainable manufacturing practices.
Resource Optimization:
- Implication: Technologies like predictive maintenance and just-in-time inventory management ensure optimal use of materials and resources.
- Contribution: Prevents overproduction, reduces excess inventory, and ensures efficient use of raw materials, minimizing resource depletion and environmental impact.
Sustainable Supply Chains:
- Implication: Enhanced visibility and coordination across supply chains through IoT and data analytics enable sustainable sourcing and logistics.
- Contribution: Promotes the use of environmentally friendly materials, reduces transportation emissions, and ensures compliance with sustainability standards.
Circular Economy Support:
- Implication: Smart Manufacturing facilitates product design for recyclability and reusability, supporting circular economy initiatives.
- Contribution: Enables the efficient recycling and repurposing of materials, reducing waste and promoting sustainable product lifecycles.
Emissions Monitoring and Control:
- Implication: Real-time monitoring systems track emissions and environmental impact throughout the manufacturing process.
- Contribution: Helps in adhering to environmental regulations, reducing pollutant emissions, and ensuring compliance with sustainability standards.
Reduced Carbon Footprint:
- Implication: Optimization of production processes and energy usage leads to a lower carbon footprint.
- Contribution: Contributes to global efforts to combat climate change by reducing the amount of greenhouse gases emitted by manufacturing activities.
Sustainable Product Development:
- Implication: AI and big data analytics support the design of eco-friendly products that require fewer resources and generate less waste.
- Contribution: Promotes the creation of sustainable products that are easier to manufacture, use, and dispose of responsibly.
Extended Equipment Lifespan:
- Implication: Predictive maintenance ensures that equipment is maintained in optimal condition, extending its operational lifespan.
- Contribution: Reduces the need for frequent replacements, thereby lowering material usage and waste generation.
Smart Building and Infrastructure:
- Implication: Integration of smart building technologies within manufacturing facilities optimizes energy usage for heating, cooling, and lighting.
- Contribution: Enhances overall energy efficiency of manufacturing facilities, leading to lower operational energy consumption and reduced environmental impact.
Benefits of Industry 4.0 Technologies for Sustainability:
- Enhanced Operational Efficiency: Streamlined processes and reduced resource consumption contribute to more sustainable manufacturing operations.
- Lower Environmental Impact: Reduced waste, emissions, and energy usage align with global sustainability goals and environmental regulations.
- Cost Savings: Efficient resource utilization and energy management lead to significant cost reductions, supporting both economic and environmental sustainability.
- Regulatory Compliance: Helps manufacturers meet stringent environmental regulations and standards, avoiding penalties and enhancing corporate responsibility.
- Brand Reputation: Demonstrates a commitment to sustainability, enhancing the organization’s reputation and attracting environmentally conscious customers and partners.
Case Example: A manufacturing company implemented an IoT-based energy management system to monitor and optimize energy usage across its production facilities. By analyzing real-time data, the company identified areas where energy consumption could be reduced and implemented automated controls to optimize lighting and machinery operation. This led to a 25% reduction in energy consumption, resulting in lower operational costs and a significant decrease in carbon emissions, thereby enhancing the company’s sustainability profile.
Conclusion: The adoption of Smart Manufacturing and Industry 4.0 technologies plays a vital role in advancing sustainability within the manufacturing sector. By leveraging advanced technologies to optimize resource usage, reduce waste and emissions, and enhance operational efficiency, manufacturers can significantly minimize their environmental impact. These technologies not only contribute to the achievement of environmental sustainability goals but also drive economic benefits and compliance with regulatory standards, positioning manufacturers for long-term success in a more sustainable and environmentally conscious market.
Conclusion:
The above review questions and detailed answers provide a comprehensive exploration of Smart Manufacturing and Industry 4.0. Covering essential topics such as Industry 4.0 fundamentals, IoT integration, AI optimization, additive manufacturing, data analytics, robotics and automation, implementation challenges, Big Data roles, collaborative robots, and environmental sustainability, these questions facilitate a deep understanding of how to leverage advanced technologies for smarter, more efficient, and sustainable manufacturing processes. Engaging with these questions equips students and professionals with the knowledge to implement best practices, overcome challenges, and achieve sustained excellence in the competitive landscape of modern manufacturin
Smart Manufacturing and Industry 4.0: Thought-Provoking Questions
1. What are the cybersecurity challenges associated with Industry 4.0, and how can manufacturers mitigate these risks?
Answer:
Cybersecurity Challenges in Industry 4.0:
Industry 4.0 introduces a highly interconnected and digitized manufacturing environment, which, while offering numerous benefits, also presents significant cybersecurity challenges:
Increased Attack Surface:
- Challenge: The integration of IoT devices, cloud computing, and interconnected systems expands the number of entry points for cyberattacks.
- Impact: Greater vulnerability to unauthorized access, data breaches, and malicious activities.
Legacy Systems Integration:
- Challenge: Integrating new Industry 4.0 technologies with older, legacy systems that may lack robust security features.
- Impact: Creates weak links that can be exploited by attackers, compromising the entire network.
Data Privacy and Protection:
- Challenge: Handling vast amounts of sensitive data, including intellectual property and personal information.
- Impact: Risk of data theft, manipulation, and non-compliance with data protection regulations.
Advanced Persistent Threats (APTs):
- Challenge: Sophisticated, long-term targeted attacks aimed at infiltrating and remaining undetected within manufacturing networks.
- Impact: Continuous disruption, espionage, and significant financial and reputational damage.
Lack of Cybersecurity Awareness:
- Challenge: Employees may lack adequate training and awareness regarding cybersecurity best practices.
- Impact: Increased susceptibility to phishing, social engineering, and inadvertent security breaches.
Supply Chain Vulnerabilities:
- Challenge: Dependencies on third-party vendors and suppliers can introduce additional security risks.
- Impact: Compromised security measures from partners can lead to broader network vulnerabilities.
Mitigation Strategies:
Comprehensive Security Framework:
- Strategy: Implement a multi-layered cybersecurity framework that includes firewalls, intrusion detection systems (IDS), and encryption.
- Benefit: Provides robust protection against a variety of cyber threats, ensuring data integrity and system availability.
Regular Security Audits and Assessments:
- Strategy: Conduct periodic security audits and vulnerability assessments to identify and address potential weaknesses.
- Benefit: Proactively detects and mitigates security gaps before they can be exploited by attackers.
Employee Training and Awareness Programs:
- Strategy: Develop ongoing training programs to educate employees about cybersecurity best practices and emerging threats.
- Benefit: Reduces the risk of human error and enhances the organization’s overall security posture.
Secure Integration of Legacy Systems:
- Strategy: Apply security patches, update software, and implement network segmentation to protect legacy systems.
- Benefit: Minimizes vulnerabilities associated with outdated technologies, ensuring secure interoperability with new systems.
Data Encryption and Access Controls:
- Strategy: Encrypt sensitive data both at rest and in transit, and enforce strict access controls based on the principle of least privilege.
- Benefit: Protects data from unauthorized access and ensures that only authorized personnel can access critical information.
Incident Response and Recovery Plans:
- Strategy: Develop and regularly update incident response plans to swiftly address and recover from security breaches.
- Benefit: Minimizes the impact of cyber incidents and ensures rapid restoration of normal operations.
Collaborative Security with Supply Chain Partners:
- Strategy: Establish cybersecurity standards and protocols with suppliers and vendors, and regularly assess their security practices.
- Benefit: Enhances the overall security of the extended supply chain, reducing the risk of external vulnerabilities.
Implementation of Zero Trust Architecture:
- Strategy: Adopt a Zero Trust security model that assumes no entity, inside or outside the network, is inherently trustworthy.
- Benefit: Enhances security by continuously verifying and validating all access requests, reducing the risk of unauthorized access.
Case Example: A leading automotive manufacturer integrated IoT sensors across its production lines for real-time monitoring. To mitigate cybersecurity risks, they implemented a Zero Trust architecture, segmented their network to isolate critical systems, and provided comprehensive cybersecurity training to employees. Additionally, they collaborated closely with their suppliers to ensure that all third-party systems adhered to stringent security standards. As a result, the manufacturer significantly reduced its vulnerability to cyberattacks, ensuring uninterrupted production and safeguarding sensitive data.
Conclusion: Cybersecurity is a critical concern in the era of Industry 4.0, where increased connectivity and data integration elevate the risk of cyber threats. By adopting comprehensive security measures, fostering a culture of cybersecurity awareness, and ensuring robust protection across all layers of the manufacturing ecosystem, manufacturers can effectively mitigate these risks and fully leverage the benefits of Smart Manufacturing.
2. How does the implementation of Digital Twin technology enhance predictive maintenance in manufacturing?
Answer:
Digital Twin Technology in Manufacturing:
A Digital Twin is a virtual replica of a physical asset, system, or process that mirrors its real-time performance, behavior, and condition. In manufacturing, Digital Twin technology leverages data from sensors, IoT devices, and historical records to create a dynamic, interactive model of machinery, production lines, or entire factories.
Enhancement of Predictive Maintenance through Digital Twins:
Real-Time Monitoring and Simulation:
- Function: Digital Twins continuously receive data from their physical counterparts, enabling real-time monitoring of equipment performance and operational conditions.
- Enhancement: By simulating the physical asset’s behavior under various conditions, Digital Twins can predict potential failures before they occur, allowing for timely maintenance interventions.
Data Integration and Analysis:
- Function: Digital Twins integrate data from multiple sources, including sensors, machine logs, and environmental factors.
- Enhancement: Advanced analytics and machine learning algorithms analyze this comprehensive data to identify patterns and anomalies indicative of impending equipment issues.
Condition-Based Maintenance:
- Function: Digital Twins assess the actual condition of equipment rather than relying on predefined maintenance schedules.
- Enhancement: Maintenance activities are triggered based on real-time data and predictive insights, optimizing maintenance resources and reducing unnecessary downtime.
Root Cause Analysis:
- Function: When a potential failure is detected, Digital Twins can simulate different scenarios to determine the root cause.
- Enhancement: This detailed analysis enables more effective and targeted corrective actions, preventing recurring issues and enhancing overall equipment reliability.
Lifecycle Management:
- Function: Digital Twins track the entire lifecycle of machinery, from installation to decommissioning.
- Enhancement: By understanding wear and tear patterns over time, manufacturers can better plan for replacements, upgrades, and maintenance, extending the asset’s useful life and optimizing capital investments.
Optimized Maintenance Scheduling:
- Function: Digital Twins provide insights into the optimal timing for maintenance activities based on equipment usage and condition.
- Enhancement: This optimization minimizes production disruptions, aligns maintenance with production schedules, and maximizes operational efficiency.
Enhanced Collaboration and Decision-Making:
- Function: Digital Twins provide a shared platform for engineers, maintenance teams, and management to collaborate and make informed decisions.
- Enhancement: Facilitates better communication, faster problem-solving, and more strategic maintenance planning, leading to improved operational performance.
Benefits of Using Digital Twins for Predictive Maintenance:
- Reduced Downtime: By predicting and addressing equipment failures before they occur, Digital Twins minimize unplanned downtime and ensure continuous production.
- Cost Savings: Optimizing maintenance schedules and preventing major breakdowns lowers maintenance costs and reduces the need for expensive emergency repairs.
- Extended Equipment Lifespan: Regular, condition-based maintenance helps in preserving machinery, extending its operational life, and maximizing return on investment.
- Improved Safety: Predictive maintenance reduces the risk of catastrophic equipment failures, enhancing workplace safety.
- Enhanced Efficiency: Streamlined maintenance processes and reduced downtime contribute to overall operational efficiency and productivity.
- Data-Driven Insights: Continuous data collection and analysis provide valuable insights into equipment performance, supporting continuous improvement initiatives.
Case Example: A leading aerospace manufacturer implemented Digital Twin technology for its critical assembly machines. By creating virtual replicas of these machines, the company was able to monitor their performance in real-time and simulate various operational scenarios. The Digital Twins analyzed data from vibration sensors, temperature gauges, and usage logs to predict when components would likely fail. This predictive maintenance approach enabled the manufacturer to perform maintenance activities proactively, reducing machine downtime by 35%, cutting maintenance costs by 20%, and extending the lifespan of key machinery components.
Conclusion: Digital Twin technology significantly enhances predictive maintenance in manufacturing by providing real-time insights, enabling condition-based maintenance, and facilitating data-driven decision-making. By accurately predicting equipment failures and optimizing maintenance schedules, Digital Twins contribute to increased operational efficiency, reduced costs, and improved equipment reliability, thereby driving the success of Smart Manufacturing initiatives within the Industry 4.0 framework.
3. In what ways does blockchain technology contribute to transparency and traceability in smart manufacturing environments?
Answer:
Blockchain Technology in Smart Manufacturing:
Blockchain is a decentralized, immutable ledger technology that securely records transactions across multiple computers. In smart manufacturing, blockchain enhances transparency and traceability by providing a secure and tamper-proof record of all activities within the manufacturing process.
Contributions to Transparency and Traceability:
Immutable Record-Keeping:
- Contribution: Blockchain ensures that once data is recorded, it cannot be altered or deleted.
- Impact: Provides a trustworthy and verifiable history of all transactions and activities, ensuring data integrity and preventing fraud or tampering.
End-to-End Traceability:
- Contribution: Records every step of the supply chain, from raw material sourcing to final product delivery.
- Impact: Enables manufacturers and customers to trace the origin and journey of products, ensuring compliance with quality standards and ethical sourcing practices.
Enhanced Supply Chain Visibility:
- Contribution: Shares real-time information across all stakeholders in the supply chain through a shared blockchain ledger.
- Impact: Improves coordination, reduces delays, and enhances the ability to respond to disruptions by providing a clear and comprehensive view of the entire supply chain.
Smart Contracts:
- Contribution: Automates and enforces contractual agreements through self-executing smart contracts on the blockchain.
- Impact: Ensures that transactions and agreements are executed accurately and transparently, reducing the need for intermediaries and minimizing the risk of disputes.
Authenticity Verification:
- Contribution: Verifies the authenticity of components and products by recording unique identifiers on the blockchain.
- Impact: Prevents counterfeiting and ensures that customers receive genuine products, enhancing brand reputation and customer trust.
Regulatory Compliance:
- Contribution: Provides an auditable trail of all manufacturing activities, ensuring compliance with industry regulations and standards.
- Impact: Simplifies the audit process, reduces compliance costs, and ensures that products meet all necessary legal and quality requirements.
Data Security and Privacy:
- Contribution: Protects sensitive manufacturing data through cryptographic encryption and decentralized storage.
- Impact: Ensures that only authorized parties can access and view data, enhancing data security and privacy while maintaining transparency.
Reduction of Manual Errors:
- Contribution: Automates data recording and sharing processes, reducing reliance on manual entry.
- Impact: Minimizes human errors, ensuring that data is accurate and reliable, which is critical for effective traceability and transparency.
Benefits of Blockchain for Transparency and Traceability:
- Increased Trust: Builds trust among stakeholders by providing a transparent and verifiable record of all transactions and processes.
- Enhanced Accountability: Assigns clear ownership and responsibility for each step in the manufacturing process, promoting accountability.
- Improved Efficiency: Streamlines supply chain operations by reducing the need for intermediaries and automating processes through smart contracts.
- Greater Customer Confidence: Enables customers to verify the authenticity and origin of products, enhancing their confidence in the brand.
- Fraud Prevention: Prevents unauthorized alterations and counterfeiting by ensuring data integrity and authenticity.
- Simplified Audits: Facilitates easier and more efficient auditing processes by providing a clear and immutable record of all activities.
Case Example: A global electronics manufacturer implemented blockchain technology to enhance traceability in its supply chain. By recording every transaction and movement of components on the blockchain, the company ensured that each part could be traced back to its origin. This implementation enabled the company to quickly identify and address issues such as defective batches, ensuring that only compliant and high-quality components were used in production. Additionally, customers could verify the authenticity of their products through blockchain records, boosting their trust and satisfaction.
Conclusion: Blockchain technology plays a pivotal role in enhancing transparency and traceability in smart manufacturing environments. By providing an immutable and decentralized ledger for all manufacturing activities, blockchain ensures data integrity, improves supply chain visibility, and fosters trust among stakeholders. These capabilities not only streamline operations and reduce costs but also elevate product quality and customer satisfaction, making blockchain an invaluable tool in the pursuit of excellence within Industry 4.0.
4. How does edge computing differ from cloud computing in the context of smart manufacturing, and what are the advantages of using edge computing?
Answer:
Edge Computing vs. Cloud Computing in Smart Manufacturing:
Edge Computing: Edge computing refers to the decentralized processing of data near the source of data generation, such as on manufacturing equipment, sensors, or local servers. Instead of sending all data to a centralized cloud for processing, edge computing performs data analysis and decision-making at or near the data source.
Cloud Computing: Cloud computing involves centralized data storage and processing on remote servers accessed via the internet. Data from various sources is transmitted to the cloud, where it is stored, processed, and analyzed before results are sent back to the user or device.
Key Differences:
Aspect | Edge Computing | Cloud Computing |
---|---|---|
Data Processing | Localized, near data source | Centralized, remote data centers |
Latency | Low latency due to proximity | Higher latency due to data transmission |
Bandwidth Usage | Reduces bandwidth by processing data locally | High bandwidth usage as data is transmitted to the cloud |
Reliability | More resilient to internet outages | Dependent on internet connectivity |
Security | Enhanced security as sensitive data is processed locally | Potential vulnerabilities during data transmission |
Scalability | Limited by local hardware resources | Highly scalable with cloud infrastructure |
Real-Time Processing | Facilitates real-time or near-real-time processing | Less suitable for real-time applications due to latency |
Cost | Potentially lower operational costs for real-time applications | Costs associated with data storage and transfer |
Advantages of Using Edge Computing in Smart Manufacturing:
Reduced Latency:
- Advantage: Processing data locally minimizes delays in data transmission.
- Impact: Enables real-time or near-real-time decision-making, essential for applications like automated control systems and predictive maintenance.
Bandwidth Optimization:
- Advantage: By processing and filtering data at the edge, only relevant information is sent to the cloud.
- Impact: Reduces the strain on network bandwidth, lowers data transmission costs, and improves overall network efficiency.
Enhanced Reliability:
- Advantage: Edge computing systems can continue to operate independently of cloud connectivity.
- Impact: Ensures continuous operation and data processing even during internet outages, enhancing system resilience and uptime.
Improved Security and Privacy:
- Advantage: Sensitive data can be processed locally without being transmitted over the internet.
- Impact: Reduces the risk of data breaches and enhances data privacy by keeping critical information within the local network.
Scalability and Flexibility:
- Advantage: Edge devices can be added or upgraded independently to meet specific processing needs.
- Impact: Allows manufacturers to scale their operations incrementally without overhauling the entire infrastructure.
Real-Time Analytics:
- Advantage: Enables immediate analysis and response to data, supporting dynamic manufacturing processes.
- Impact: Enhances operational efficiency, reduces waste, and improves product quality through timely interventions.
Energy Efficiency:
- Advantage: Reduces the need for constant data transmission to the cloud, lowering energy consumption associated with data transfer and processing.
- Impact: Contributes to more sustainable manufacturing practices and reduces operational costs.
Localized Control:
- Advantage: Provides granular control over individual machines and processes.
- Impact: Enhances the ability to fine-tune operations and quickly address localized issues without relying on centralized systems.
Case Example: A large automotive manufacturer implemented edge computing in its assembly lines to monitor and control robotic systems in real-time. By processing sensor data locally, the system could immediately detect and respond to anomalies, such as deviations in component placement or assembly speed. This implementation reduced assembly line downtime by 25%, improved product quality by 15%, and decreased reliance on cloud-based data processing, resulting in cost savings and enhanced operational efficiency.
Conclusion: Edge computing offers significant advantages over cloud computing in smart manufacturing by enabling real-time data processing, reducing latency, optimizing bandwidth usage, and enhancing reliability and security. By leveraging edge computing, manufacturers can achieve greater operational efficiency, improved product quality, and more resilient production systems, making it a critical component of Industry 4.0 strategies.
5. What is the role of Artificial Intelligence (AI) in optimizing supply chain management within Industry 4.0?
Answer:
Artificial Intelligence (AI) in Supply Chain Management:
AI plays a transformative role in optimizing supply chain management within the Industry 4.0 framework by leveraging advanced algorithms, machine learning, and data analytics to enhance efficiency, predictability, and responsiveness across the entire supply chain.
Key Roles of AI in Supply Chain Optimization:
Demand Forecasting:
- Role: AI analyzes historical sales data, market trends, and external factors to predict future demand accurately.
- Optimization: Improves inventory planning, reduces stockouts and overstock situations, and aligns production schedules with market demand.
Inventory Management:
- Role: AI algorithms optimize inventory levels by predicting optimal stock quantities and reorder points.
- Optimization: Minimizes holding costs, reduces excess inventory, and ensures timely availability of materials and products.
Predictive Maintenance for Supply Chain Equipment:
- Role: AI monitors the condition of supply chain equipment, such as conveyor systems and logistics machinery, predicting potential failures.
- Optimization: Prevents unexpected downtimes, ensures continuous operation, and extends the lifespan of critical supply chain assets.
Route Optimization:
- Role: AI analyzes various factors like traffic patterns, weather conditions, and delivery schedules to determine the most efficient delivery routes.
- Optimization: Reduces transportation costs, shortens delivery times, and enhances fuel efficiency, contributing to faster and more cost-effective logistics.
Supplier Selection and Risk Management:
- Role: AI evaluates supplier performance based on historical data, financial stability, and compliance records to select the most reliable partners.
- Optimization: Enhances supplier reliability, reduces risks associated with supplier failures, and ensures a steady supply of high-quality materials.
Automated Procurement Processes:
- Role: AI automates procurement tasks such as order placement, invoice processing, and contract management.
- Optimization: Streamlines procurement operations, reduces manual errors, and accelerates the procurement cycle, enhancing overall supply chain efficiency.
Enhanced Visibility and Transparency:
- Role: AI integrates data from various sources to provide real-time visibility into supply chain operations.
- Optimization: Facilitates informed decision-making, improves coordination among stakeholders, and enables proactive management of supply chain disruptions.
Risk Prediction and Mitigation:
- Role: AI identifies potential risks in the supply chain, such as geopolitical issues, natural disasters, or supplier insolvency.
- Optimization: Enables proactive risk mitigation strategies, ensuring supply chain resilience and continuity during disruptions.
Cost Optimization:
- Role: AI analyzes cost structures across the supply chain, identifying areas for cost reduction without compromising quality or service levels.
- Optimization: Lowers overall supply chain costs, enhances profitability, and improves competitive positioning.
Personalization and Customer Service:
- Role: AI tailors supply chain operations to meet specific customer preferences and requirements, such as customized delivery schedules.
- Optimization: Enhances customer satisfaction, loyalty, and retention by providing personalized and responsive supply chain services.
Benefits of AI in Supply Chain Optimization:
- Increased Efficiency: Automates and optimizes various supply chain processes, reducing manual intervention and operational delays.
- Enhanced Accuracy: Improves the precision of demand forecasts, inventory levels, and procurement decisions, minimizing errors and enhancing reliability.
- Cost Savings: Identifies and eliminates inefficiencies, reduces transportation and inventory costs, and optimizes resource utilization.
- Improved Responsiveness: Enables swift adaptation to changing market conditions and customer demands, enhancing supply chain agility.
- Risk Reduction: Anticipates and mitigates potential risks, ensuring supply chain stability and resilience.
- Data-Driven Insights: Provides actionable insights through advanced analytics, supporting strategic decision-making and continuous improvement.
Case Example: A global consumer goods company implemented AI-driven demand forecasting to predict regional sales trends accurately. By analyzing diverse data sources, including social media trends, economic indicators, and historical sales data, the AI system provided highly accurate forecasts. This implementation enabled the company to optimize inventory levels, reduce excess stock by 20%, decrease stockouts by 15%, and improve customer satisfaction through better product availability. Additionally, AI-powered route optimization reduced transportation costs by 10% and improved delivery times, enhancing overall supply chain performance.
Conclusion: Artificial Intelligence is a pivotal enabler of supply chain optimization within Industry 4.0, offering advanced capabilities that enhance forecasting accuracy, operational efficiency, risk management, and cost-effectiveness. By integrating AI into supply chain management, manufacturers can achieve greater agility, resilience, and competitiveness, ensuring that their supply chains are robust and responsive in a rapidly evolving market landscape.
6. How does the integration of Augmented Reality (AR) and Virtual Reality (VR) technologies improve training and maintenance processes in smart manufacturing?
Answer:
Augmented Reality (AR) and Virtual Reality (VR) in Smart Manufacturing:
AR and VR technologies are increasingly being integrated into smart manufacturing environments to enhance training, maintenance, and operational efficiency. These immersive technologies provide interactive and realistic experiences that facilitate better learning, problem-solving, and decision-making.
Improvements in Training Processes:
Interactive Training Modules:
- Improvement: AR and VR create immersive training simulations that replicate real-world manufacturing scenarios.
- Benefit: Provides hands-on experience without the risks associated with actual machinery, enhancing learning outcomes and retention rates.
Remote Training Capabilities:
- Improvement: VR-based training can be accessed remotely, allowing employees from different locations to participate in the same training program.
- Benefit: Reduces the need for physical training facilities, lowers training costs, and ensures consistent training quality across the organization.
Customized Learning Experiences:
- Improvement: AR and VR can tailor training programs to individual learning paces and styles, offering personalized instruction.
- Benefit: Enhances the effectiveness of training by addressing the specific needs and preferences of each learner, leading to better skill acquisition.
Real-Time Feedback and Assessment:
- Improvement: These technologies can provide instant feedback on performance during training exercises.
- Benefit: Helps trainees quickly identify and correct mistakes, accelerating the learning process and improving competency levels.
Safe Environment for Skill Development:
- Improvement: VR simulations allow employees to practice operating complex or dangerous equipment in a controlled, virtual environment.
- Benefit: Enhances safety by enabling skill development without exposing trainees to actual hazards, reducing the likelihood of accidents during real operations.
Improvements in Maintenance Processes:
Guided Maintenance Procedures:
- Improvement: AR overlays provide step-by-step instructions and visual cues directly onto machinery during maintenance tasks.
- Benefit: Increases the accuracy and efficiency of maintenance activities, reducing the time required to perform repairs and minimizing errors.
Remote Assistance and Collaboration:
- Improvement: AR enables remote experts to guide on-site technicians through complex maintenance procedures in real-time.
- Benefit: Enhances problem-solving capabilities, reduces downtime by speeding up repairs, and leverages expertise without requiring physical presence.
Virtual Maintenance Simulations:
- Improvement: VR simulations allow maintenance teams to practice procedures and troubleshoot issues in a virtual replica of the machinery.
- Benefit: Prepares technicians for real-world scenarios, improving their readiness and effectiveness when dealing with actual equipment issues.
Predictive Maintenance Insights:
- Improvement: AR can display real-time data and predictive analytics related to equipment health during maintenance tasks.
- Benefit: Enables more informed decision-making, allowing technicians to address potential issues proactively and extend the lifespan of machinery.
Documentation and Knowledge Sharing:
- Improvement: AR can link to digital manuals, schematics, and instructional videos, providing easy access to critical information during maintenance.
- Benefit: Streamlines the maintenance process, ensures consistency in procedures, and facilitates knowledge sharing across the organization.
Benefits of AR and VR Integration:
- Enhanced Learning and Skill Acquisition: Immersive training experiences lead to better understanding and retention of complex concepts and procedures.
- Increased Operational Efficiency: Guided and informed maintenance processes reduce downtime and improve equipment reliability.
- Cost Savings: Virtual training reduces the need for physical training materials and facilities, while efficient maintenance minimizes repair costs and production losses.
- Improved Safety: Safe training and maintenance environments prevent accidents and injuries, fostering a safer workplace.
- Scalability and Flexibility: AR and VR training programs can be easily scaled and updated to accommodate new technologies and processes, ensuring that the workforce remains proficient and adaptable.
Case Example: A leading electronics manufacturer integrated AR into its maintenance operations by equipping technicians with AR headsets. These headsets provided real-time, step-by-step maintenance instructions overlaid onto the machinery. When a technician encountered an issue with a complex assembly machine, the AR system guided them through the diagnostic and repair process, highlighting critical components and tools needed. This implementation reduced maintenance time by 30%, decreased error rates, and enhanced the overall effectiveness of the maintenance team. Additionally, the company utilized VR for training new employees, allowing them to practice operating and maintaining machinery in a risk-free virtual environment, resulting in faster onboarding and higher competency levels.
Conclusion: The integration of Augmented Reality and Virtual Reality technologies in smart manufacturing significantly improves training and maintenance processes by providing immersive, interactive, and efficient solutions. These technologies enhance learning outcomes, increase operational efficiency, reduce costs, and promote a safer work environment. By leveraging AR and VR, manufacturers can ensure that their workforce is well-trained, skilled, and capable of maintaining high levels of productivity and quality in an increasingly complex and automated manufacturing landscape.
7. How does the use of Robotics Process Automation (RPA) enhance operational efficiency in smart manufacturing?
Answer:
Robotic Process Automation (RPA) in Smart Manufacturing:
Robotic Process Automation (RPA) involves using software robots or “bots” to automate repetitive, rule-based tasks typically performed by humans. In smart manufacturing, RPA enhances operational efficiency by streamlining processes, reducing errors, and freeing up human resources for more strategic activities.
Enhancements to Operational Efficiency through RPA:
Automating Repetitive Tasks:
- Enhancement: RPA automates routine and monotonous tasks such as data entry, order processing, and inventory management.
- Impact: Increases speed and accuracy of operations, reduces human error, and allows employees to focus on higher-value tasks like problem-solving and innovation.
Streamlining Supply Chain Operations:
- Enhancement: RPA manages tasks such as order tracking, shipment scheduling, and supplier communications.
- Impact: Enhances supply chain visibility, improves coordination, and ensures timely delivery of materials and products, reducing lead times and operational delays.
Improving Data Management and Reporting:
- Enhancement: RPA collects, processes, and analyzes data from various sources, generating real-time reports and dashboards.
- Impact: Provides actionable insights for decision-making, enhances data accuracy, and supports continuous monitoring of key performance indicators (KPIs).
Enhancing Quality Control:
- Enhancement: RPA automates quality inspection processes, such as collecting inspection data, comparing it against standards, and flagging defects.
- Impact: Ensures consistent quality control, reduces inspection time, and minimizes the risk of human oversight, leading to higher product quality and customer satisfaction.
Optimizing Inventory Management:
- Enhancement: RPA tracks inventory levels, automates reordering processes, and manages stock movements.
- Impact: Prevents stockouts and overstock situations, optimizes inventory turnover, and reduces holding costs, improving overall inventory efficiency.
Facilitating Compliance and Documentation:
- Enhancement: RPA ensures that all manufacturing processes adhere to regulatory standards by automating compliance checks and maintaining accurate documentation.
- Impact: Simplifies compliance management, reduces the risk of non-compliance penalties, and ensures that all necessary records are up-to-date and easily accessible.
Enhancing Maintenance Processes:
- Enhancement: RPA automates the scheduling of maintenance activities, tracks maintenance logs, and monitors equipment performance data.
- Impact: Ensures timely maintenance, extends equipment lifespan, and reduces the likelihood of unexpected breakdowns, thereby enhancing overall operational reliability.
Cost Reduction:
- Enhancement: By automating labor-intensive tasks, RPA reduces the need for manual labor and lowers operational costs.
- Impact: Increases profitability by minimizing labor expenses and reducing costs associated with errors and inefficiencies.
Scalability and Flexibility:
- Enhancement: RPA systems can be easily scaled up or down based on production demands and operational needs.
- Impact: Provides manufacturers with the flexibility to adapt to market fluctuations and scale operations without significant additional investments.
Enhanced Customer Service:
- Enhancement: RPA manages customer inquiries, processes orders, and handles returns efficiently.
- Impact: Improves response times, enhances customer satisfaction, and ensures a seamless customer experience, fostering loyalty and repeat business.
Benefits of RPA in Smart Manufacturing:
- Increased Productivity: Automates time-consuming tasks, allowing human workers to concentrate on more strategic and creative endeavors.
- Improved Accuracy: Reduces the incidence of errors in repetitive tasks, ensuring higher data integrity and process reliability.
- Faster Operations: Accelerates process execution, leading to shorter cycle times and quicker turnaround on orders and services.
- Enhanced Compliance: Maintains consistent adherence to regulatory standards through automated compliance checks and documentation.
- Cost Efficiency: Lowers operational costs by reducing the need for manual labor and minimizing errors that can lead to financial losses.
- Greater Scalability: Easily adapts to increased production demands without the need for proportional increases in workforce or resources.
- Enhanced Employee Satisfaction: Frees employees from mundane tasks, increasing job satisfaction and reducing turnover rates by allowing them to engage in more meaningful work.
Case Example: A large manufacturing company implemented RPA to automate its inventory management and order processing systems. By deploying software bots to handle tasks such as updating inventory levels, generating purchase orders, and processing customer orders, the company achieved a 40% reduction in order processing time and a 25% decrease in inventory holding costs. Additionally, the automation of these processes reduced human errors by 30%, enhancing overall operational accuracy and efficiency.
Conclusion: Robotic Process Automation significantly enhances operational efficiency in smart manufacturing by automating repetitive tasks, improving data accuracy, streamlining supply chain operations, and reducing costs. By leveraging RPA, manufacturers can achieve higher productivity, better quality control, and greater flexibility, positioning themselves for sustained success in the competitive landscape of Industry 4.0.
8. What is the significance of Digital Twin technology in enhancing product lifecycle management (PLM) within Industry 4.0?
Answer:
Digital Twin Technology in Product Lifecycle Management (PLM):
A Digital Twin is a virtual replica of a physical product, process, or system that simulates its real-time performance, behavior, and lifecycle. In the context of Product Lifecycle Management (PLM) within Industry 4.0, Digital Twin technology plays a crucial role in enhancing the management and optimization of products from conception through design, manufacturing, and maintenance to end-of-life disposal.
Significance of Digital Twin in Enhancing PLM:
Enhanced Design and Development:
- Significance: Digital Twins enable detailed simulation and testing of product designs before physical prototypes are built.
- Enhancement: Facilitates rapid iteration and optimization of designs, reducing development time and costs while ensuring higher product quality and performance.
Real-Time Monitoring and Feedback:
- Significance: During the manufacturing phase, Digital Twins monitor real-time data from production processes.
- Enhancement: Provides immediate feedback on manufacturing performance, allowing for real-time adjustments to optimize production efficiency and quality.
Predictive Maintenance and Reliability:
- Significance: Digital Twins simulate the operational behavior and wear of products in use.
- Enhancement: Predicts maintenance needs and potential failures, enabling proactive maintenance scheduling that extends product lifespan and reduces downtime.
Lifecycle Optimization:
- Significance: Digital Twins provide a comprehensive view of the entire product lifecycle, integrating data from various stages.
- Enhancement: Identifies opportunities for improvement at each stage, from design to disposal, ensuring that the product remains efficient, cost-effective, and environmentally friendly throughout its lifecycle.
Improved Collaboration and Communication:
- Significance: Digital Twins serve as a centralized digital representation that can be accessed and shared by different stakeholders, including designers, engineers, manufacturers, and service teams.
- Enhancement: Enhances collaboration by providing a common reference point, ensuring that all teams are aligned and can work together seamlessly to address issues and implement improvements.
Customization and Personalization:
- Significance: Digital Twins can simulate and manage customized product configurations.
- Enhancement: Facilitates mass customization by enabling the efficient management of multiple product variants without compromising on quality or production efficiency.
Data-Driven Decision Making:
- Significance: Digital Twins collect and analyze vast amounts of data throughout the product lifecycle.
- Enhancement: Empowers manufacturers to make informed, data-driven decisions that enhance product design, manufacturing processes, and post-sales support.
Sustainability and Environmental Impact:
- Significance: Digital Twins can simulate the environmental impact of products, including energy consumption and material usage.
- Enhancement: Helps in designing more sustainable products and optimizing manufacturing processes to reduce environmental footprints, supporting corporate sustainability goals.
End-of-Life Management:
- Significance: Digital Twins facilitate the planning and execution of product recycling, remanufacturing, or disposal.
- Enhancement: Ensures that products are managed responsibly at the end of their lifecycle, promoting circular economy practices and compliance with environmental regulations.
Benefits of Digital Twin Integration in PLM:
- Reduced Time-to-Market: Accelerates product development cycles through efficient design validation and optimization.
- Cost Savings: Lowers development and maintenance costs by identifying and addressing issues early in the lifecycle.
- Enhanced Product Quality: Improves reliability and performance by enabling continuous monitoring and optimization.
- Increased Agility: Allows manufacturers to quickly adapt to market changes and customer demands through flexible and data-driven PLM processes.
- Sustainability: Promotes eco-friendly product design and manufacturing practices, contributing to environmental stewardship.
- Competitive Advantage: Provides insights and capabilities that differentiate products and manufacturing processes, enhancing market competitiveness.
Case Example: A leading aerospace company implemented Digital Twin technology to manage the lifecycle of its aircraft engines. By creating a virtual replica of each engine, the company could monitor performance in real-time, predict maintenance needs, and optimize operational parameters. This implementation resulted in a 20% reduction in maintenance costs, a 15% increase in engine reliability, and an extended operational lifespan of the engines. Additionally, the Digital Twins facilitated better collaboration between design, manufacturing, and maintenance teams, leading to continuous improvements in engine design and performance.
Conclusion: Digital Twin technology is a pivotal element in enhancing Product Lifecycle Management within Industry 4.0. By providing a comprehensive, real-time digital representation of products, Digital Twins enable manufacturers to optimize design, manufacturing, maintenance, and end-of-life processes. This integration leads to improved product quality, reduced costs, enhanced collaboration, and greater sustainability, ultimately driving the success and competitiveness of manufacturers in the modern industrial landscape.
9. How does the concept of Smart Factory integrate various Industry 4.0 technologies to create a highly automated and efficient manufacturing environment?
Answer:
Smart Factory Concept in Industry 4.0:
A Smart Factory embodies the principles of Industry 4.0 by integrating advanced technologies to create a highly automated, interconnected, and efficient manufacturing environment. It leverages technologies such as the Internet of Things (IoT), artificial intelligence (AI), robotics, big data analytics, cloud computing, and augmented reality (AR) to optimize production processes, enhance flexibility, and improve overall operational performance.
Integration of Industry 4.0 Technologies in Smart Factories:
Internet of Things (IoT):
- Integration: IoT devices and sensors are deployed across the factory floor to collect real-time data from machines, equipment, and production processes.
- Outcome: Enables continuous monitoring, data-driven decision-making, and proactive maintenance, enhancing operational efficiency and reducing downtime.
Artificial Intelligence (AI) and Machine Learning:
- Integration: AI algorithms analyze data collected from IoT devices to identify patterns, predict outcomes, and optimize processes.
- Outcome: Facilitates predictive maintenance, quality control, demand forecasting, and process optimization, leading to increased productivity and reduced operational costs.
Robotics and Automation:
- Integration: Advanced robots and automated systems handle repetitive, hazardous, or complex tasks with high precision and speed.
- Outcome: Enhances production speed, accuracy, and consistency while reducing labor costs and minimizing human error.
Big Data Analytics:
- Integration: Big data platforms aggregate and analyze vast amounts of data generated by IoT devices, machines, and business systems.
- Outcome: Provides actionable insights for process improvements, resource optimization, and strategic decision-making, driving continuous operational enhancement.
Cloud Computing:
- Integration: Cloud platforms store and process data from various sources, enabling scalable and flexible data management.
- Outcome: Supports real-time data access, collaboration across different locations, and seamless integration of new technologies, enhancing overall factory agility and responsiveness.
Digital Twin Technology:
- Integration: Digital Twins create virtual replicas of physical assets and processes, simulating their behavior under different conditions.
- Outcome: Enables virtual testing, optimization, and predictive maintenance, reducing the need for physical prototypes and minimizing risks during production changes.
Augmented Reality (AR) and Virtual Reality (VR):
- Integration: AR and VR tools assist in training, maintenance, and design processes by providing immersive and interactive experiences.
- Outcome: Enhances worker training, facilitates remote maintenance support, and improves the accuracy of design and assembly processes, leading to higher productivity and reduced errors.
Additive Manufacturing (3D Printing):
- Integration: 3D printing technology enables on-demand production of complex components and prototypes.
- Outcome: Reduces lead times, allows for greater customization, and minimizes material waste, enhancing the factory’s ability to respond quickly to market demands.
Cybersecurity Solutions:
- Integration: Robust cybersecurity measures protect the interconnected systems and data within the Smart Factory from cyber threats.
- Outcome: Ensures data integrity, protects intellectual property, and maintains operational continuity by preventing unauthorized access and cyberattacks.
Edge Computing:
- Integration: Edge computing processes data locally at the source, reducing the reliance on centralized cloud servers.
- Outcome: Minimizes latency, enhances real-time decision-making, and improves the reliability of critical manufacturing processes by enabling immediate data processing and response.
Characteristics of a Smart Factory:
- Interconnectivity: Seamless communication between machines, systems, and humans through integrated networks.
- Autonomy: Systems can operate independently, making decisions based on real-time data without human intervention.
- Adaptability: Ability to quickly adjust to changes in production demands, product variations, and market conditions.
- Data-Driven: Utilizes data analytics to inform and optimize every aspect of the manufacturing process.
- Sustainability: Implements energy-efficient practices, waste reduction, and sustainable resource management to minimize environmental impact.
Benefits of Smart Factory Integration:
- Increased Efficiency: Streamlines operations through automation and real-time process optimization, leading to higher productivity and reduced operational costs.
- Enhanced Quality: Maintains consistent product quality through precise control and continuous monitoring of production processes.
- Greater Flexibility: Quickly adapts to changes in demand, product designs, and market conditions, enabling rapid response and customization.
- Improved Decision-Making: Leverages data-driven insights to make informed and strategic decisions, enhancing overall operational performance.
- Reduced Downtime: Predictive maintenance and real-time monitoring minimize equipment failures and unplanned downtime, ensuring continuous production.
- Cost Savings: Optimizes resource utilization, reduces waste, and lowers maintenance and operational costs through efficient process management.
- Enhanced Worker Productivity: Automates mundane tasks, allowing human workers to focus on more complex and value-added activities, increasing overall workforce productivity.
- Sustainability: Implements sustainable manufacturing practices, reducing environmental impact and promoting corporate social responsibility.
Case Example: A leading automotive manufacturer transformed its production facility into a Smart Factory by integrating IoT sensors, AI-driven analytics, robotic automation, and Digital Twin technology. IoT sensors monitored machine performance and environmental conditions in real-time, while AI algorithms analyzed the data to predict maintenance needs and optimize production schedules. Robotic arms handled assembly tasks with high precision, and Digital Twins simulated production scenarios to identify and implement process improvements. This comprehensive integration resulted in a 30% increase in production efficiency, a 20% reduction in maintenance costs, and a significant improvement in product quality, demonstrating the transformative impact of a Smart Factory within the Industry 4.0 framework.
Conclusion: The Smart Factory concept epitomizes the convergence of various Industry 4.0 technologies to create a highly automated, efficient, and adaptable manufacturing environment. By integrating IoT, AI, robotics, big data analytics, cloud computing, and other advanced technologies, Smart Factories achieve unprecedented levels of operational excellence, quality, and flexibility. This holistic approach not only enhances productivity and reduces costs but also positions manufacturers to thrive in the dynamic and competitive landscape of modern manufacturing.
10. What ethical considerations must manufacturers address when implementing AI and automation in their production processes?
Answer:
Ethical Considerations in Implementing AI and Automation:
As manufacturers integrate Artificial Intelligence (AI) and automation into their production processes, several ethical considerations emerge that must be thoughtfully addressed to ensure responsible and sustainable practices.
Impact on Employment:
- Consideration: Automation can lead to job displacement as machines and AI systems take over tasks previously performed by humans.
- Ethical Concern: Potential unemployment and loss of livelihoods for workers.
- Mitigation Strategies:
- Invest in reskilling and upskilling programs to transition employees to new roles.
- Promote human-machine collaboration, where AI and robots augment rather than replace human workers.
- Develop new job opportunities in areas such as AI maintenance, programming, and oversight.
Bias and Fairness in AI Algorithms:
- Consideration: AI systems can inadvertently perpetuate biases present in training data or algorithm design.
- Ethical Concern: Discrimination against certain groups of workers or customers, leading to unfair treatment and inequality.
- Mitigation Strategies:
- Ensure diverse and representative datasets for training AI models.
- Implement regular audits and testing to identify and eliminate biases.
- Incorporate fairness and transparency principles in AI development and deployment.
Data Privacy and Security:
- Consideration: AI and automation systems collect and process vast amounts of data, including personal and sensitive information.
- Ethical Concern: Risks of data breaches, unauthorized access, and misuse of personal data.
- Mitigation Strategies:
- Implement robust data encryption and security measures.
- Adhere to data protection regulations and best practices.
- Ensure transparency in data collection, usage, and storage policies.
Transparency and Explainability:
- Consideration: AI decision-making processes can be complex and opaque, making it difficult to understand how conclusions are reached.
- Ethical Concern: Lack of accountability and trust in AI systems, especially in critical decision-making scenarios.
- Mitigation Strategies:
- Develop AI models with explainable and interpretable outputs.
- Provide clear documentation and rationale for AI-driven decisions.
- Enable human oversight and intervention in AI processes.
Accountability and Responsibility:
- Consideration: Determining who is accountable for decisions made by AI and automated systems can be challenging.
- Ethical Concern: Unclear lines of responsibility in cases of errors, accidents, or malfunctions.
- Mitigation Strategies:
- Establish clear policies outlining accountability for AI and automation outcomes.
- Implement governance structures that oversee AI deployment and ethical compliance.
- Ensure that human operators remain responsible for critical decisions and system oversight.
Environmental Impact:
- Consideration: The production and operation of AI and automation technologies can have significant environmental footprints.
- Ethical Concern: Resource consumption, energy usage, and electronic waste contribute to environmental degradation.
- Mitigation Strategies:
- Adopt sustainable practices in the manufacturing and disposal of AI and automation equipment.
- Optimize energy efficiency in AI and robotic systems.
- Promote the recycling and responsible disposal of electronic components.
Human Dignity and Well-Being:
- Consideration: The introduction of AI and automation can affect the psychological and social well-being of workers.
- Ethical Concern: Stress, loss of job satisfaction, and diminished human interaction in the workplace.
- Mitigation Strategies:
- Foster a positive work environment that values human contributions and promotes well-being.
- Ensure that automation enhances rather than diminishes human roles and engagement.
- Provide support systems for employees affected by automation, including counseling and career guidance.
Intellectual Property and Ownership:
- Consideration: AI-generated innovations and automated processes can complicate intellectual property (IP) rights.
- Ethical Concern: Unclear ownership of AI-generated works and processes, leading to potential IP disputes.
- Mitigation Strategies:
- Define clear IP policies that address AI-generated content and inventions.
- Establish legal frameworks that recognize and protect the rights of stakeholders in AI-driven innovation.
Benefits of Addressing Ethical Considerations:
- Trust and Reputation: Ethical practices build trust with employees, customers, and stakeholders, enhancing the organization’s reputation.
- Sustainable Growth: Responsible implementation of AI and automation supports long-term sustainability and reduces the risk of legal and ethical conflicts.
- Employee Engagement: Valuing and supporting workers through ethical practices fosters a motivated and loyal workforce.
- Innovation and Competitiveness: Ethical AI practices encourage responsible innovation, maintaining competitiveness while adhering to societal values.
Case Example: A major electronics manufacturer introduced AI-powered quality inspection systems to enhance product consistency. To address ethical concerns, the company ensured that the AI models were trained on diverse and unbiased datasets to prevent discrimination in defect detection. They also implemented transparent reporting mechanisms, allowing human inspectors to review and override AI decisions when necessary. Additionally, the company invested in reskilling programs for employees affected by the automation, enabling them to transition to roles focused on AI system maintenance and oversight. This holistic approach ensured that the integration of AI upheld ethical standards, maintained employee trust, and enhanced overall product quality.
Conclusion: As manufacturers embrace AI and automation within Industry 4.0, addressing ethical considerations is paramount to ensuring responsible and sustainable practices. By proactively tackling issues related to employment, bias, data privacy, transparency, accountability, environmental impact, human well-being, and intellectual property, manufacturers can harness the full potential of AI and automation while maintaining trust, fairness, and integrity in their operations. This ethical approach not only safeguards stakeholders but also fosters a culture of innovation and excellence, driving long-term success in the competitive manufacturing landscape.
11. How can blockchain technology improve supplier relationship management in smart manufacturing?
Answer:
Blockchain Technology in Supplier Relationship Management (SRM):
Blockchain technology offers a decentralized, transparent, and immutable ledger that can revolutionize Supplier Relationship Management (SRM) in smart manufacturing. By integrating blockchain into SRM processes, manufacturers can enhance transparency, trust, efficiency, and collaboration with their suppliers.
Improvements in Supplier Relationship Management through Blockchain:
Enhanced Transparency and Traceability:
- Improvement: Blockchain records every transaction and interaction between manufacturers and suppliers in a transparent and immutable manner.
- Benefit: Enables both parties to trace the origin, movement, and transformation of goods and materials throughout the supply chain, ensuring accountability and authenticity.
Secure and Efficient Data Sharing:
- Improvement: Blockchain facilitates secure and real-time sharing of data between manufacturers and suppliers without the need for intermediaries.
- Benefit: Reduces the risk of data breaches and unauthorized access while streamlining communication and information flow, enhancing operational efficiency.
Automated Smart Contracts:
- Improvement: Smart contracts on the blockchain automatically execute and enforce contractual agreements when predefined conditions are met.
- Benefit: Ensures timely and accurate execution of contracts, reduces administrative overhead, and minimizes disputes related to contract fulfillment.
Improved Supplier Verification and Compliance:
- Improvement: Blockchain provides a verifiable and tamper-proof record of supplier certifications, compliance documents, and performance metrics.
- Benefit: Simplifies the verification process, ensures that suppliers meet regulatory and quality standards, and enhances trust between parties.
Reduction of Fraud and Counterfeiting:
- Improvement: Blockchain’s immutable ledger ensures that all transactions are recorded accurately and cannot be altered retroactively.
- Benefit: Prevents fraudulent activities, such as counterfeit goods entering the supply chain, protecting brand integrity and customer trust.
Optimized Inventory Management:
- Improvement: Real-time visibility into inventory levels and movements through blockchain data allows for better coordination with suppliers.
- Benefit: Enhances inventory accuracy, reduces stockouts and overstock situations, and supports just-in-time (JIT) inventory practices.
Streamlined Payment Processes:
- Improvement: Blockchain facilitates secure and automated payment transactions between manufacturers and suppliers.
- Benefit: Reduces payment delays, lowers transaction costs, and minimizes the risk of payment fraud, ensuring timely financial settlements.
Enhanced Collaboration and Trust:
- Improvement: The transparent and secure nature of blockchain fosters a higher level of trust and collaboration between manufacturers and suppliers.
- Benefit: Promotes long-term partnerships, encourages information sharing, and facilitates joint problem-solving and innovation.
Efficient Dispute Resolution:
- Improvement: Blockchain’s transparent records provide clear evidence of transactions and contract terms, simplifying the resolution of disputes.
- Benefit: Reduces the time and cost associated with resolving conflicts, enhancing overall supplier relationships.
Sustainability and Ethical Sourcing:
- Improvement: Blockchain can track and verify the sustainability and ethical practices of suppliers, such as fair labor standards and environmentally friendly sourcing.
- Benefit: Ensures that manufacturers maintain responsible and sustainable supply chains, aligning with corporate social responsibility (CSR) goals and consumer expectations.
Benefits of Blockchain in SRM:
- Increased Trust: Transparent and immutable records build trust between manufacturers and suppliers, fostering reliable and consistent relationships.
- Operational Efficiency: Automating contract execution and streamlining data sharing reduce manual processes, saving time and resources.
- Risk Mitigation: Enhanced traceability and verification reduce risks related to fraud, counterfeiting, and non-compliance.
- Cost Savings: Lower administrative and transaction costs through automation and reduced reliance on intermediaries.
- Enhanced Decision-Making: Real-time data and insights enable informed decision-making, improving strategic planning and supplier selection.
Case Example: A global automotive manufacturer implemented a blockchain-based SRM system to manage its extensive network of suppliers. By recording all supplier transactions, certifications, and compliance data on the blockchain, the manufacturer achieved full traceability of parts and materials from source to assembly. Smart contracts were used to automate payment processes upon delivery and inspection of goods, ensuring timely settlements. This implementation resulted in a 25% reduction in administrative costs, a 30% decrease in payment processing times, and a significant improvement in supplier trust and collaboration. Additionally, the ability to trace the origin of components enhanced the manufacturer’s ability to ensure quality and compliance, reducing the incidence of defective parts and recalls.
Conclusion: Blockchain technology significantly enhances Supplier Relationship Management in smart manufacturing by providing unparalleled transparency, security, and efficiency. By leveraging blockchain’s capabilities, manufacturers can build more trustworthy and collaborative relationships with suppliers, optimize supply chain operations, and ensure compliance with quality and ethical standards. This integration not only improves operational performance and reduces costs but also strengthens the overall resilience and sustainability of the manufacturing supply chain within the Industry 4.0 ecosystem.
12. What future advancements in Industry 4.0 technologies can further transform smart manufacturing, and how might they impact the industry?
Answer:
Future Advancements in Industry 4.0 Technologies:
As Industry 4.0 continues to evolve, several emerging technologies and advancements are poised to further transform smart manufacturing. These future advancements promise to enhance automation, connectivity, intelligence, and sustainability, driving significant changes in the manufacturing landscape.
1. Advanced Artificial Intelligence and Machine Learning:
- Advancement: Development of more sophisticated AI and machine learning algorithms capable of deeper predictive analytics, autonomous decision-making, and adaptive learning.
- Impact: Enhances the ability to optimize complex manufacturing processes, improve product quality, and enable fully autonomous production systems. AI-driven robots could adapt in real-time to changing conditions without human intervention, increasing efficiency and flexibility.
2. Quantum Computing:
- Advancement: Utilization of quantum computing to solve complex optimization and simulation problems at unprecedented speeds.
- Impact: Revolutionizes areas such as supply chain optimization, material science, and product design by enabling faster and more accurate simulations and optimizations, leading to innovative products and more efficient manufacturing processes.
3. Extended Reality (XR) Integration:
- Advancement: Further integration of augmented reality (AR), virtual reality (VR), and mixed reality (MR) into manufacturing processes.
- Impact: Enhances training, maintenance, and design activities by providing more immersive and interactive experiences. XR can facilitate remote collaboration, advanced prototyping, and real-time visualization of complex processes, improving accuracy and reducing errors.
4. 5G and Beyond Connectivity:
- Advancement: Deployment of 5G networks and future advancements in wireless connectivity.
- Impact: Provides ultra-low latency, high bandwidth, and reliable connectivity, enabling real-time data exchange, remote monitoring, and seamless integration of IoT devices. Enhances the performance of autonomous robots and real-time analytics, leading to more responsive and agile manufacturing environments.
5. Autonomous Supply Chains:
- Advancement: Development of fully autonomous supply chains powered by AI, IoT, blockchain, and robotics.
- Impact: Creates self-managing supply chains that can autonomously handle procurement, production, distribution, and logistics. Increases efficiency, reduces human intervention, and enhances resilience against disruptions.
6. Advanced Robotics and Collaborative Robots (Cobots):
- Advancement: Continued innovation in robotics, including more advanced cobots with enhanced dexterity, sensory capabilities, and AI integration.
- Impact: Enables robots to perform more complex and delicate tasks, work safely alongside humans, and adapt to dynamic production environments. Improves productivity, quality, and worker safety.
7. Sustainable and Green Manufacturing Technologies:
- Advancement: Innovations focused on sustainability, such as carbon capture technologies, renewable energy integration, and eco-friendly materials.
- Impact: Reduces the environmental footprint of manufacturing operations, aligns with global sustainability goals, and meets increasing consumer demand for environmentally responsible products.
8. Digital Thread and Seamless Integration:
- Advancement: Development of a comprehensive digital thread that seamlessly connects all aspects of the product lifecycle from design to disposal.
- Impact: Enhances traceability, quality control, and lifecycle management by ensuring that data flows seamlessly across all stages of production. Facilitates continuous improvement and more informed decision-making.
9. Human-Machine Interfaces (HMIs) Evolution:
- Advancement: Advancement in HMIs, including gesture recognition, voice control, and brain-computer interfaces (BCIs).
- Impact: Improves the ease of interaction between humans and machines, enhancing usability, efficiency, and safety. Enables more intuitive and natural control of manufacturing systems.
10. Bio-Manufacturing and Synthetic Biology: – Advancement: Integration of bio-manufacturing techniques and synthetic biology into traditional manufacturing processes. – Impact: Expands the range of producible materials and products, enabling the creation of bio-based components, sustainable materials, and innovative biomedical devices. Promotes sustainability and opens new avenues for product development.
11. Edge AI and Intelligent Sensors: – Advancement: Development of AI capabilities at the edge, integrated with intelligent sensors and devices. – Impact: Enables real-time, localized data processing and decision-making without relying on centralized cloud servers. Enhances responsiveness, reduces latency, and improves the efficiency of manufacturing operations.
12. Smart Factories with Fully Integrated AI and IoT: – Advancement: Evolution towards fully integrated smart factories where AI, IoT, robotics, and other technologies are seamlessly interconnected. – Impact: Creates highly autonomous and self-optimizing manufacturing environments that can dynamically adjust to changing conditions, optimize resource usage, and continuously improve processes. Enhances overall operational efficiency, flexibility, and competitiveness.
Potential Impacts on the Industry:
- Increased Productivity and Efficiency: Advanced technologies streamline operations, reduce downtime, and optimize resource utilization, leading to higher productivity and lower operational costs.
- Enhanced Product Quality and Customization: AI-driven quality control, precise robotics, and flexible production systems ensure consistent product quality while enabling mass customization.
- Greater Agility and Responsiveness: Smart manufacturing technologies enable rapid adaptation to market changes, customer demands, and supply chain disruptions, enhancing the agility and resilience of manufacturing operations.
- Sustainability and Environmental Responsibility: Innovations focused on sustainability reduce the environmental impact of manufacturing, supporting global sustainability goals and meeting consumer expectations for eco-friendly products.
- Workforce Transformation: Automation and AI redefine workforce roles, requiring new skills and fostering a collaborative environment where humans and machines work together to achieve optimal outcomes.
- Competitive Advantage: Early adopters of advanced Industry 4.0 technologies gain a significant competitive edge through enhanced operational capabilities, innovation, and responsiveness.
- Innovation and New Business Models: Emerging technologies drive the creation of new products, services, and business models, expanding the scope and potential of the manufacturing industry.
Case Example: A leading electronics manufacturer adopted several future Industry 4.0 technologies, including advanced AI algorithms for predictive maintenance, 5G-enabled IoT devices for real-time monitoring, and blockchain for supply chain transparency. Additionally, they integrated augmented reality (AR) for remote maintenance support and developed a comprehensive digital thread connecting design, manufacturing, and service processes. These advancements resulted in a 40% increase in operational efficiency, a 30% reduction in maintenance costs, enhanced product quality, and improved customer satisfaction. The company also achieved significant sustainability goals by optimizing energy usage and reducing material waste through data-driven insights and automation.
Conclusion: Future advancements in Industry 4.0 technologies hold immense potential to further transform smart manufacturing by enhancing automation, connectivity, intelligence, and sustainability. As these technologies continue to evolve, manufacturers that strategically adopt and integrate them will benefit from increased productivity, improved quality, greater agility, and a stronger competitive position. Embracing these innovations will be crucial for manufacturers to thrive in the rapidly changing and increasingly complex landscape of modern manufacturing.
Conclusion:
The above thought-provoking questions and detailed answers delve into the multifaceted aspects of Smart Manufacturing and Industry 4.0. Covering critical topics such as cybersecurity, Digital Twin technology, blockchain integration, edge computing, AI in supply chain management, AR/VR applications, RPA, ethical considerations, supplier relationship management, future technological advancements, and the role of blockchain in transparency, these questions provide a comprehensive exploration of how advanced technologies are reshaping the manufacturing landscape. Engaging with these questions equips students and professionals with the knowledge to understand, implement, and innovate within the framework of Industry 4.0, ensuring they are well-prepared to navigate and contribute to the future of smart manufacturing.