Manufacturing Process Design and Optimization
Manufacturing process design and optimization lies at the heart of modern production strategy, enabling companies to achieve peak operational efficiency, quality consistency, and scalability. It integrates the principles of engineering, data analytics, and systems thinking to refine how products are built, from concept to completion. Within the realm of Industrial and Manufacturing Technologies, this discipline supports industries in navigating complex trade-offs between cost, performance, and sustainability.
As technologies evolve, innovative approaches like Digital Twin Technology allow engineers to simulate and optimize production processes before physical implementation. This is especially valuable when integrated with Computer-Integrated Manufacturing (CIM), ensuring seamless coordination between digital designs and physical operations.
The synergy between advanced processes and materials plays a critical role. Innovations covered in Advanced Materials and Manufacturing Technologies and Additive Manufacturing (3D Printing) help tailor production methods to meet performance needs while minimizing waste. These capabilities support goals of Sustainable Manufacturing by reducing environmental impact through resource-conscious design.
Closely aligned with this is the growing focus on Energy and Resource Efficiency in Manufacturing. Engineers optimize thermal loads, fluid flows, and energy use with support from foundational disciplines like Thermodynamics and Heat Transfer and Fluid Mechanics and Hydraulics.
Effective process design also incorporates human-centered thinking and automation. Understanding how people interact with tools and systems, as taught in Human Factors and Ergonomics in Manufacturing, helps shape workflows that improve safety and productivity. At the same time, Industrial Automation and Robotics expand capabilities for speed, precision, and consistency in repetitive or hazardous tasks.
The alignment of design intent with real-world output is verified through robust Manufacturing Quality Control and Assurance. This ensures that optimization doesn’t sacrifice reliability or compliance. Simultaneously, lean practices taught in Lean Manufacturing and modern data systems from Smart Manufacturing and Industry 4.0 drive continuous improvements based on real-time feedback.
Supply-side efficiency is equally important. Robust Supply Chain Management ensures that the inputs to optimized processes arrive on time, at the right cost and quality. Interdisciplinary insights from fields like Control Systems in Mechanical Engineering, Solid Mechanics, and Mechanical Design and CAD help shape effective systems for precision control and modeling.
Process design challenges also vary across application areas. Whether building components in Automotive Engineering, innovating in Biomechanical Engineering, or adopting emerging trends in Nanotechnology and Advanced Materials in Mechanical Engineering, engineers must tailor their optimization strategies accordingly.
A thorough understanding of these interwoven concepts—materials, automation, ergonomics, sustainability, control, and quality—equips students to master the core principles of manufacturing process design. This field forms a critical bridge between engineering innovation and scalable production, helping translate ideas into tangible, efficient realities.
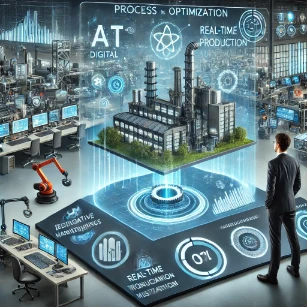
Table of Contents
Core Concepts in Manufacturing Process Design
Effective manufacturing process design is fundamental to achieving operational excellence, product quality, and cost efficiency. It encompasses the strategic planning of every step involved in transforming raw materials into finished goods. From selecting process routes to optimizing workflows and facility layouts, this discipline ensures that manufacturing operations are not only technically sound but also responsive to business and customer demands. Below are the essential pillars that support robust manufacturing process design.
Process Design
- Definition:
- Process design refers to the structured creation of plans, specifications, and workflows for converting raw materials into value-added finished products. It involves a detailed understanding of the production method, the nature of the product, and the required equipment and resources.
- Goals:
- Ensure smooth and efficient production: The design must eliminate unnecessary steps, avoid rework, and ensure optimal sequence to reduce cycle times.
- Meet quality standards: The process must consistently deliver outputs that conform to customer and regulatory requirements.
- Minimize resource consumption: Effective designs limit material waste, reduce energy usage, and optimize labor input for sustainable operation.
- Key Components:
- Identifying production steps and sequences: Defining the precise order in which operations are carried out to ensure logical and efficient progression.
- Determining equipment and tooling requirements: Selecting the right machines, tools, and fixtures to match product specifications and process parameters.
- Setting process parameters: Establishing appropriate levels of temperature, pressure, cutting speed, or feed rates to maintain consistency and reduce variability.
Process Optimization
- Definition:
- Process optimization involves continuously refining manufacturing operations to achieve better performance. It leverages data, analysis, and iterative improvements to reduce costs, improve throughput, and elevate product quality.
- Goals:
- Minimize production time and energy use: Identify and eliminate wasteful practices, idle time, and over-processing to improve sustainability and efficiency.
- Eliminate bottlenecks and inefficiencies: Use techniques such as capacity analysis, constraint management, and simulation to streamline flow and resource allocation.
- Enhance flexibility to adapt to changes in demand: Enable fast changeovers, modular setups, and agile scheduling to support varied production volumes and product types.
- Key Techniques:
- Lean manufacturing principles: Apply systematic tools such as Kaizen, 5S, and Just-In-Time (JIT) to remove waste and maximize value.
- Data-driven decision-making: Utilize real-time data, machine learning, and predictive analytics to monitor processes, identify anomalies, and make informed adjustments.
- Leading manufacturers now employ digital twins and AI-enhanced models to simulate process changes before implementation, greatly improving optimization success rates. Learn more from this overview of digital twin applications in manufacturing.
Workflow Design
- Definition:
- Workflow design refers to structuring the sequence and coordination of tasks, personnel, and material movements to create a streamlined and repeatable operational flow. It focuses on maximizing productivity while minimizing unnecessary activity or delays.
- Goals:
- Reduce unnecessary movement of materials and workers: Prevent time loss and ergonomic strain by minimizing travel distance, searching, and manual handling.
- Ensure balanced workloads across workstations: Use techniques like line balancing and takt time analysis to synchronize activities and prevent bottlenecks or idle stations.
- Applications:
- Assembly lines: Fixed-sequence setups where each station performs a specific task, ideal for high-volume production.
- Batch processing: A method used for moderate-volume, variety-driven production where tasks are grouped into batches.
- One-piece flow systems: A Lean-oriented design that moves products one unit at a time between workstations to reduce inventory and increase visibility.
Facility Layout Planning
- Definition:
- Facility layout planning involves arranging physical assets—such as machines, workstations, storage areas, and personnel zones—within a factory to maximize space utilization, productivity, and safety. The layout must support the overall workflow and be adaptable to change.
- Key Layout Types:
- Product Layout:
- Also known as a line layout, it arranges equipment and workstations in sequence based on the production steps of a single product. It supports high-volume, low-variety production, offering smooth flow and simplified management (e.g., automotive assembly).
- Process Layout:
- Organizes equipment based on similar functions (e.g., all drilling machines in one area). Suitable for low-volume, high-variety jobs such as custom manufacturing and repair shops, this layout offers flexibility but may require more handling and planning.
- Cellular Layout:
- Groups equipment and workers into “cells” that handle a specific product family or process group. This layout balances flexibility and efficiency, reducing transport and lead time while supporting small-batch or mixed-model production.
- Fixed-Position Layout:
- Used when the product is too large or complex to move (e.g., ships, aircraft, construction). Resources, workers, and equipment come to the product. It requires high coordination and flexibility but is essential for large-scale or on-site production projects.
- Product Layout:
Tools and Technologies in Manufacturing Process Design and Optimization
Modern manufacturing relies on a wide array of digital tools and advanced technologies to design, simulate, monitor, and continuously improve processes. These tools not only enhance efficiency and accuracy but also allow engineers to visualize complex systems, predict performance issues, and implement changes with minimal risk. From simulation software to AI-powered analytics, the following technologies play a pivotal role in designing and optimizing world-class manufacturing systems.
Simulation Software
- Role:
- Simulation software enables manufacturers to build virtual models of entire production systems, allowing engineers to experiment with configurations, resource allocations, and workflows before making physical changes. This reduces risk and supports data-driven design.
- Applications:
- Evaluating various production layouts to identify which offers the most efficient flow of materials and labor.
- Identifying bottlenecks, queuing problems, or machine conflicts that may not be obvious in a static layout diagram.
- Testing “what-if” scenarios under different demand loads or shift patterns without disrupting actual operations.
- Examples:
- Discrete Event Simulation (DES): Tools such as Arena, FlexSim, and Simul8 are used to model systems where events occur at discrete points in time.
- Digital Twins: Real-time digital replicas of physical systems that receive live data from IoT devices, enabling predictive optimization and performance tuning.
Computer-Aided Design (CAD)
- Role:
- CAD software is essential for the precise design and visualization of production equipment, tools, fixtures, and plant layouts. It allows engineers to draft, simulate, and refine components in a digital environment before prototyping or fabrication.
- Applications:
- Creating detailed 3D models of machines and systems, which can be evaluated for mechanical fit, ergonomic safety, and spatial efficiency.
- Designing modular fixtures and custom tooling to support Lean cell configurations and rapid changeovers.
- Examples:
- Autodesk Fusion 360 and SolidWorks are popular platforms used across industries for mechanical design and simulation, supporting both prototyping and production-ready engineering.
Internet of Things (IoT)
- Role:
- IoT devices bring intelligence and connectivity to manufacturing environments by collecting real-time data on equipment status, environmental conditions, and workflow metrics. This enables monitoring, traceability, and automation on an unprecedented scale.
- Applications:
- Monitoring machine health, cycle times, and energy usage through embedded sensors and wireless connectivity.
- Enabling predictive maintenance by analyzing performance trends and triggering alerts before failures occur.
- Tracking parts, materials, and tools across the shop floor to ensure proper sequencing and avoid bottlenecks.
Artificial Intelligence (AI) and Machine Learning
- Role:
- AI and machine learning technologies analyze vast and complex datasets to detect patterns, forecast outcomes, and recommend optimal process changes. These tools significantly enhance decision-making speed and accuracy in modern manufacturing environments.
- Applications:
- Demand forecasting using machine learning models that account for historical sales, seasonality, and market trends.
- Production schedule optimization based on real-time conditions, capacity constraints, and delivery priorities.
- Defect prediction and automated quality control using image recognition and anomaly detection algorithms.
- AI-driven systems also support adaptive control of robotic arms and CNC tools based on sensor feedback, reducing waste and improving consistency.
- According to this Deloitte report on AI in manufacturing, machine learning is transforming production optimization, supply chain agility, and product quality assurance at scale.
Advanced Manufacturing Technologies
- Additive Manufacturing (3D Printing):
- Enables fast prototyping, tooling, and custom part fabrication directly from CAD data. Reduces material waste and supports lightweight product design, especially in aerospace and medical sectors.
- CNC Machining:
- Computer Numerical Control (CNC) machines perform precision cutting, drilling, and shaping operations with high repeatability. Integrated with CAD/CAM software, they ensure exact replication of complex geometries.
- Automation and Robotics:
- Industrial robots and programmable automation systems boost throughput, reduce labor-intensive tasks, and improve consistency. Flexible robotic arms now work alongside humans in collaborative workspaces (cobots), enabling safer and more agile operations.
Lean Tools
- Value Stream Mapping (VSM):
- VSM is a fundamental Lean tool used to document and visualize material and information flows within a production system. It helps teams identify non-value-added steps and plan for a more streamlined future state.
- Kaizen Events:
- Structured, short-term improvement workshops that bring together cross-functional teams to tackle specific problems. Kaizen events often result in measurable gains in efficiency, quality, and team collaboration.
- These Lean tools remain essential even in high-tech environments, complementing digital innovations with people-driven problem-solving and cultural transformation.
Steps in Manufacturing Process Design and Optimization
Designing and optimizing a manufacturing process is a systematic, data-driven journey that involves analyzing current operations, identifying inefficiencies, and implementing targeted improvements. Each step plays a critical role in ensuring that production systems are cost-effective, flexible, and aligned with quality standards. The following six steps represent a structured roadmap for transforming raw inputs into efficient, resilient manufacturing workflows.
Process Mapping
- Definition:
- Process mapping involves diagramming every step in a production workflow to provide a visual representation of how materials, information, and tasks flow through the system. It reveals the sequence of activities, decision points, dependencies, and interactions across departments.
- Purpose:
- To identify redundancies, unnecessary steps, delays, and handoffs that contribute to inefficiency or inconsistency. Mapping makes it easier to engage stakeholders, align understanding, and define future improvements based on real operational insights.
- Tools:
- Flowcharts: Simple visual tools to depict sequential steps and decisions in a process.
- Value Stream Mapping (VSM): A Lean tool that shows both material and information flow, highlighting value-adding and non-value-adding activities.
- Gantt Charts: Used to visualize task timing, resource allocation, and project scheduling in process redesign projects.
Data Collection and Analysis
- Definition:
- This step involves systematically gathering data on current operations, machine performance, human activity, and process variability to create a fact-based foundation for improvement efforts.
- Metrics:
- Cycle time: The time taken to complete one unit of production from start to finish.
- Throughput: The number of units produced per time period.
- Defect rates: The frequency of quality deviations or non-conformances.
- Downtime: Unplanned equipment or process stoppages that reduce availability and output.
- Tools:
- IoT sensors: Embedded devices that collect data on temperature, vibration, speed, and other operational parameters.
- ERP systems: Enterprise Resource Planning platforms that integrate data from finance, inventory, and production.
- MES (Manufacturing Execution Systems): Software solutions that track and document real-time factory-floor operations, linking automation and ERP layers.
Identifying Bottlenecks
- Definition:
- A bottleneck is any step in a manufacturing process that slows down or limits the overall output due to capacity constraints or inefficiencies. Identifying and resolving bottlenecks is essential for improving flow and boosting productivity.
- Techniques:
- Analyzing workstation utilization rates: High utilization (approaching 100%) often signals that a process step cannot keep pace with upstream or downstream operations.
- Using simulation software: Tools like discrete event simulation allow manufacturers to model production flow and test how changes in setup, staffing, or equipment affect throughput.
- Visual observation and time studies: Direct shop-floor analysis can often uncover repetitive delays, work pileups, or imbalance between stations.
Layout Design and Simulation
- Definition:
- Layout design involves arranging machinery, storage areas, tools, and workstations within the factory to optimize spatial efficiency, material handling, and safety. Simulation helps validate these layouts under realistic operating conditions before physical implementation.
- Approach:
- Simulating alternative layouts: Virtual modeling software like AnyLogic or FlexSim is used to compare performance across different configurations based on metrics such as travel distance, queue times, and material flow velocity.
- Evaluating lean layouts: Cellular and U-shaped layouts are often tested for their ability to support one-piece flow and reduced lead times.
- For best practices and real-world layout solutions, the Plant Services guide on optimizing layouts offers practical insight into balancing efficiency and safety.
Implementing Process Improvements
- Definition:
- This step translates the insights and redesigns from earlier stages into real-world changes. It includes reconfiguring equipment, retraining staff, revising procedures, and updating control systems.
- Techniques:
- Automating repetitive tasks: Use robots, conveyors, or programmable logic controllers (PLCs) to handle standardized operations with higher speed and precision.
- Balancing workloads: Redistribute work across stations using takt time calculations and standardized work charts to eliminate bottlenecks and reduce idle time.
- Implementing visual management: Introduce visual cues like color coding, shadow boards, or digital dashboards to support clarity and accountability on the shop floor.
Monitoring and Continuous Improvement
- Definition:
- This final step ensures that process gains are sustained and improved upon. Monitoring provides feedback on key performance indicators (KPIs), while continuous improvement fosters a proactive mindset across all levels of the organization.
- Methods:
- Kaizen principles: Encourage small, incremental improvements suggested and implemented by frontline employees.
- Analyzing trends using real-time data: Dashboards and reports built from IoT and MES data can highlight performance drifts and trigger timely interventions.
- Standardizing successful changes: Once improvements prove effective, update standard operating procedures (SOPs) and training materials to ensure consistency and scalability.
Applications of Manufacturing Process Design and Optimization
Manufacturing process design and optimization techniques are widely applied across various industries to improve throughput, reduce costs, maintain quality, and respond rapidly to market demands. These applications range from the high-speed assembly of automobiles to the precision requirements of pharmaceutical production. Below are key sectors where advanced process design and optimization have become integral to competitiveness and innovation.
Automotive Manufacturing
- Applications:
- Designing assembly lines: Automotive manufacturers use detailed process planning to engineer high-throughput assembly lines that support mass production while maintaining flexibility for multiple vehicle models. Workstations are sequenced for minimal delays, and tools are organized to maximize ergonomics and speed.
- Optimizing customization workflows: As consumer preferences shift toward personalization, automakers use modular design and flexible cells to incorporate custom features (like interiors or infotainment options) without compromising takt time.
- Examples:
- Tesla’s Gigafactories: These state-of-the-art facilities integrate automation, robotics, and digital twins to simulate and optimize production lines in real time. From battery cell production to final assembly, every step is monitored and continuously refined.
Aerospace Industry
- Applications:
- Streamlining complex assembly: Aircraft involve thousands of components that must be assembled with high precision. Process design ensures that workflows accommodate the complexity while minimizing handling and ensuring traceability.
- Precision in machining: Tight tolerances for aerospace components necessitate highly controlled machining operations. Optimization includes automated tool path programming, temperature control, and fixture standardization.
- Examples:
- Boeing: Uses simulation platforms and 3D modeling to optimize layout, workstation design, and operator movements, leading to reduced cycle time and improved ergonomics in its aircraft production lines.
Electronics Manufacturing
- Applications:
- Balancing circuit board assembly lines: Electronics manufacturers optimize workflows to ensure that high-speed pick-and-place machines, soldering systems, and inspection stations operate in harmony, minimizing bottlenecks and downtime.
- Automated quality inspection: Machine vision systems equipped with AI algorithms are employed to detect surface defects, alignment errors, or soldering flaws with greater accuracy than human inspectors.
- Examples:
- Intel: Uses advanced manufacturing optimization to improve process nodes in semiconductor fabrication. Cleanroom layouts, airflow management, and photolithography steps are all designed for maximum yield and performance.
Food and Beverage Industry
- Applications:
- Workflow design for high-speed packaging: Food manufacturers engineer production lines that handle mixing, filling, sealing, and labeling at high volumes, ensuring consistency and hygiene.
- Waste reduction in processing: Techniques such as batch sizing optimization, ingredient pre-measuring, and real-time monitoring help reduce overuse or spillage, leading to cost savings and sustainability benefits.
- Examples:
- Coca-Cola: Employs IoT-enabled sensors and cloud-based analytics to monitor bottling lines for fill-level accuracy, cap torque, and line speed, adjusting operations instantly to prevent downtime and ensure quality.
Pharmaceutical Manufacturing
- Applications:
- Cleanroom layout design: Pharmaceutical production requires aseptic environments to avoid contamination. Layout planning ensures unidirectional flow, segregation of clean zones, and minimal personnel movement.
- Automated formulation and filling: Automation is key to maintaining consistency in active ingredient dosage, reducing human error, and ensuring compliance with regulatory standards such as FDA and GMP.
- Examples:
- Pfizer: During the COVID-19 pandemic, Pfizer rapidly scaled vaccine production by redesigning process steps, integrating automation, and optimizing cold chain logistics. Their efforts are detailed in this Wall Street Journal article on Pfizer’s vaccine manufacturing breakthrough.
Benefits of Manufacturing Process Design and Optimization
Investing in thoughtful manufacturing process design and ongoing optimization delivers substantial and measurable benefits across operational, financial, environmental, and human resource dimensions. These advantages are not limited to high-tech factories—they extend to all sectors seeking to improve competitiveness, resilience, and sustainability in a fast-changing industrial landscape. Below are six key benefits that highlight why process design is fundamental to manufacturing excellence.
- Increased Productivity:
- Carefully structured process design eliminates inefficiencies, removes unnecessary steps, and ensures that materials and information flow seamlessly from start to finish. Optimized layouts reduce transit times, and digital tools ensure accurate scheduling and synchronization between operations.
- Downtime is minimized through predictive maintenance and real-time monitoring, while well-balanced workflows prevent bottlenecks. The result is higher throughput with the same or fewer resources, enabling faster turnaround times and increased production capacity.
- Improved productivity also allows for better utilization of machinery and labor, lowering idle time and making operations more scalable.
- Cost Savings:
- Optimization efforts help cut costs at every level—by reducing waste, streamlining labor, minimizing energy consumption, and improving machine efficiency. Cost drivers such as excessive inventory, long lead times, and defective output are systematically addressed through tools like value stream mapping and Six Sigma analysis.
- Designing with cost-efficiency in mind ensures that capital investments in equipment or space are maximized, avoiding overcapacity or underutilization.
- Companies that regularly optimize their production processes can achieve savings of 10–30% in operational costs according to industry benchmarking from Bain & Company’s operational excellence reports.
- Enhanced Quality:
- Standardized and well-defined processes minimize variability, helping ensure that every product meets design and performance specifications. Consistency in procedures, equipment calibration, and material handling reduces the occurrence of defects and rework.
- Statistical process control (SPC), automated inspection systems, and root cause analysis tools further enhance quality outcomes by enabling proactive corrections before deviations escalate.
- As a result, organizations can improve customer satisfaction, reduce warranty claims, and reinforce brand credibility in competitive markets.
- Flexibility:
- Modern manufacturing demands agility—the ability to switch quickly between products, adapt to volume fluctuations, or accommodate design changes. Process design supports this by incorporating modular equipment setups, mixed-model lines, and flexible workstations that can be rapidly reconfigured.
- Optimization includes the integration of digital tools that allow real-time schedule adjustments, batch size variations, and remote reprogramming of machines.
- This flexibility enables manufacturers to stay competitive in industries where customization and rapid innovation cycles are the norm, such as electronics, automotive, and consumer goods.
- Sustainability:
- Process design and optimization are central to environmental sustainability initiatives. They reduce raw material consumption, eliminate overprocessing, lower energy usage, and support closed-loop recycling and lean packaging strategies.
- Optimized workflows reduce scrap rates, water waste, and emissions—helping manufacturers meet corporate social responsibility (CSR) goals and comply with environmental regulations.
- Lean design principles and energy-efficient equipment layouts also reduce a factory’s overall carbon footprint, paving the way toward greener production systems aligned with circular economy models.
- Employee Satisfaction:
- Thoughtfully designed manufacturing environments enhance employee well-being by minimizing physical strain, reducing clutter, and supporting ergonomic best practices. Balanced workloads reduce stress, fatigue, and the risk of repetitive strain injuries.
- Clear workflows, visual aids, and automated systems reduce mental load and empower employees to perform their tasks confidently and efficiently.
- Additionally, involving frontline workers in the optimization process boosts morale, strengthens ownership, and builds a culture of continuous improvement.
Challenges in Manufacturing Process Design and Optimization
While the benefits of manufacturing process design and optimization are substantial, implementing and sustaining these improvements is not without difficulties. Organizations often encounter technical, financial, cultural, and strategic challenges when transforming existing operations into more efficient systems. Below are six of the most common challenges, along with insights into how they can be managed or mitigated.
- High Initial Costs:
- One of the foremost barriers to process redesign is the significant upfront investment required. Purchasing new automation equipment, upgrading software platforms, redesigning plant layouts, and integrating Internet of Things (IoT) devices can involve substantial capital expenditure.
- Even when improvements promise long-term savings, budget constraints or risk aversion may delay or dilute implementation. Additionally, indirect costs—such as production downtime during installation or the need for staff retraining—can further strain resources.
- To address this, companies often start with pilot projects to demonstrate ROI, apply for government or green manufacturing grants, and phase deployments to align with annual investment cycles.
- Data Overload:
- With the rise of smart manufacturing and connected systems, plants now generate vast volumes of data from sensors, machines, and enterprise software. Without effective data architecture and analytics strategies, this information can overwhelm teams and obscure critical insights.
- Common issues include inconsistent data formats, siloed databases, lack of contextual tagging, and underutilized dashboards. As a result, valuable information is often locked away or misinterpreted.
- Overcoming this challenge involves investing in data integration platforms, hiring data analysts or engineers, and applying AI tools that can automatically detect trends and anomalies. According to McKinsey’s insights on analytics in manufacturing, firms that master data governance achieve far higher returns from process optimization.
- Resistance to Change:
- Employees accustomed to traditional processes may resist new workflows, software, or automation tools. This resistance can stem from fear of job displacement, lack of understanding, or discomfort with new technologies.
- Without adequate communication, involvement, and training, even well-planned improvement initiatives can fail due to lack of buy-in at the operational level. In unionized environments, changes to roles and responsibilities may also trigger negotiations or delays.
- To reduce resistance, organizations should adopt a participative change management strategy—engaging employees early, soliciting their feedback, and clearly communicating the benefits of proposed changes to both the company and individual roles.
- Complexity of Integration:
- Integrating modern technologies with legacy systems is a common technical challenge in older manufacturing environments. New automation equipment, cloud-based MES platforms, or AI-driven analytics tools may not easily connect with outdated PLCs, SCADA systems, or in-house ERP solutions.
- This can lead to data silos, compatibility issues, and the need for costly middleware or custom interfaces. Additionally, integration failures can disrupt operations, delay project timelines, or expose cybersecurity vulnerabilities.
- Addressing this challenge requires thorough system audits, vendor-neutral architecture planning, and involvement from experienced systems integrators. Open standards (e.g., OPC UA, MQTT) are increasingly adopted to facilitate interoperability.
- Skill Gaps:
- The success of process optimization depends on a workforce capable of operating and improving modern manufacturing systems. However, many facilities face a skills gap—particularly in areas like data analysis, digital troubleshooting, lean facilitation, and machine programming.
- Operators may lack confidence in using new HMI (Human-Machine Interface) systems, engineers may be unfamiliar with advanced analytics tools, and maintenance staff may be untrained in predictive diagnostics.
- To close these gaps, companies are increasingly investing in upskilling programs, cross-training teams, and collaborating with technical institutes to build future talent pipelines. E-learning, AR-based instruction, and gamified simulation environments are also being adopted to accelerate learning curves.
Future Trends in Manufacturing Process Design and Optimization
The future of manufacturing process design and optimization lies at the intersection of digital innovation, automation, and sustainable practices. As industries navigate increasing complexity, global competition, and environmental responsibility, emerging trends are shaping the next generation of factories and workflows. These advancements promise to enhance agility, efficiency, and responsiveness while fostering smarter, greener operations. The following five trends represent critical directions that will define how manufacturing evolves in the coming years.
- Digital Twins:
- Digital twins are virtual replicas of physical systems that are updated in real time using live data from sensors, machines, and enterprise systems. These tools enable manufacturers to simulate, monitor, and optimize every aspect of their operations—from machine performance and product flow to energy consumption and maintenance cycles.
- By modeling “what-if” scenarios in a digital twin environment, engineers can test changes to layouts, process steps, or inventory levels without disrupting actual production. Digital twins also support root cause analysis, downtime prediction, and dynamic workflow adjustment.
- As computing power and data integration improve, digital twins will become more precise and widely accessible, even to small and mid-sized manufacturers seeking to modernize operations efficiently.
- AI-Driven Optimization:
- Artificial intelligence (AI) and machine learning (ML) are transforming how manufacturers detect inefficiencies, identify improvement opportunities, and optimize processes. These systems ingest massive volumes of operational data to uncover patterns invisible to human analysts.
- AI algorithms continuously refine production workflows by dynamically adjusting schedules, routing orders, predicting demand, or reallocating resources in response to disruptions. This leads to faster decision-making, reduced waste, and higher output consistency.
- AI-enabled predictive maintenance also ensures that machines are serviced only when needed, minimizing unplanned downtime and extending equipment life.
- According to the Deloitte AI in Smart Factory Report, manufacturers using AI in operations see up to 20% improvement in throughput and quality performance.
- Smart Factories:
- Smart factories are fully connected production environments where machines, systems, people, and data interact seamlessly through IoT, cloud platforms, and edge computing. In a smart factory, all elements communicate in real time to enable decentralized decision-making and autonomous process control.
- Smart sensors monitor temperature, pressure, vibration, and inventory in real time, feeding data into centralized dashboards or AI models. Operators receive alerts, suggestions, or automated responses to optimize safety, efficiency, and output.
- This environment supports self-optimizing systems where machines coordinate with each other, workflows adjust autonomously, and energy is dynamically managed based on load requirements or grid signals.
- Smart factory adoption is accelerating worldwide, driven by the need for hyper-efficient, flexible production in fast-moving sectors such as electronics, automotive, and medical devices.
- Sustainability Integration:
- Future-oriented process design prioritizes environmental responsibility by integrating sustainability objectives into the core of production planning. This includes designing workflows to reduce emissions, eliminate waste, reuse materials, and maximize energy efficiency.
- New tools enable manufacturers to calculate and optimize the carbon footprint of specific process steps, equipment, or supply routes. Green metrics are embedded into digital dashboards, allowing decision-makers to balance productivity with eco-performance.
- Advanced control systems can shift energy loads based on real-time pricing or renewable availability, while AI models help identify opportunities for energy savings or waste heat recovery.
- These sustainability-focused enhancements are essential not just for regulatory compliance but for long-term profitability and brand equity in a climate-conscious market.
- Robotics and Autonomous Systems:
- Robots and autonomous systems are evolving rapidly, becoming more collaborative, mobile, and intelligent. Future manufacturing environments will feature a mix of fixed industrial robots, mobile robotic units, and cobots (collaborative robots) working alongside humans to perform repetitive, hazardous, or precision-intensive tasks.
- Mobile robots and automated guided vehicles (AGVs) are increasingly used for material transport, replenishment, and inspection. Cobots assist in assembly, packaging, or welding tasks where flexibility and adaptability are required.
- Integrated with vision systems and AI control, autonomous systems can respond to changes in part geometry, schedule fluctuations, or process variations with minimal programming or supervision.
- These technologies reduce labor strain, enhance consistency, and make lights-out manufacturing a viable goal for certain sectors.
Why Study Manufacturing Process Design and Optimization
Designing Efficient and Effective Production Systems
Manufacturing process design involves creating workflows that transform raw materials into finished products. Students learn to analyze and plan every step of production. This ensures quality output, cost-effectiveness, and resource efficiency.
Process Mapping and Flow Analysis
Students study tools like process flow diagrams, Gantt charts, and time-motion studies. These help visualize and evaluate current processes. This enables them to identify delays, redundancies, and areas for improvement.
Simulation and Optimization Techniques
The course introduces students to software-based modeling and optimization methods. They learn to test different scenarios to improve throughput, reduce cycle time, and balance workloads. These insights support data-driven process enhancement.
Scalability and Flexibility in Design
Students explore how to design systems that can scale with demand and adapt to changes. Flexibility is key to handling product variation and custom orders. This makes operations more responsive and resilient.
Sustainable and Smart Manufacturing Integration
Students learn how process design incorporates energy efficiency, digital technologies, and automation. This prepares them to align production with Industry 4.0 and environmental goals. The result is smarter and greener manufacturing systems.
Manufacturing Process Design: Conclusion
Manufacturing process design and optimization serves as the backbone of operational excellence in today’s competitive and technologically advanced industrial landscape. It combines strategic planning, system-level thinking, and cutting-edge tools to streamline production, ensure quality, and respond rapidly to customer and market needs. More than just a one-time effort, it is a dynamic and continuous discipline that underpins every aspect of successful manufacturing.
With the integration of powerful technologies such as simulation software, the Internet of Things (IoT), and Artificial Intelligence (AI), manufacturers can visualize workflows, predict disruptions, and fine-tune operations in real time. These tools not only enhance visibility and control but also enable predictive decision-making and rapid prototyping of new process designs. The result is a more resilient, flexible, and intelligent manufacturing system that can thrive under changing economic, environmental, and customer conditions.
As industries confront increasing pressures to reduce costs, accelerate lead times, adopt sustainable practices, and personalize products, manufacturing process optimization will be at the forefront of innovation. It enables organizations to minimize waste, maximize resource efficiency, and align operations with long-term business goals.
Ultimately, the future of manufacturing belongs to those who treat process design not just as an engineering task, but as a strategic advantage. By embedding continuous improvement, digital intelligence, and cross-functional collaboration into process development, manufacturers can build systems that are not only efficient—but also agile, scalable, and future-ready.
Manufacturing Process Design: Review Questions with Detailed Answers
1. What are the primary objectives of manufacturing process design and optimization?
Answer:
The primary objectives of manufacturing process design and optimization are to create efficient, cost-effective, and high-quality production systems that meet customer demands while minimizing waste and resource utilization. Key objectives include:
Efficiency Improvement:
- Objective: Streamline processes to increase output and reduce cycle times.
- Impact: Enhances productivity and allows for higher production volumes without proportional increases in costs.
Cost Reduction:
- Objective: Identify and eliminate unnecessary expenses in the production process.
- Impact: Lowers overall manufacturing costs, improving profit margins and competitiveness.
Quality Enhancement:
- Objective: Implement processes that consistently produce high-quality products.
- Impact: Reduces defect rates, increases customer satisfaction, and decreases costs associated with rework and returns.
Flexibility and Scalability:
- Objective: Design processes that can easily adapt to changes in product designs, volumes, and market demands.
- Impact: Enables manufacturers to respond swiftly to market changes, enhancing resilience and market responsiveness.
Sustainability:
- Objective: Incorporate environmentally friendly practices and reduce resource consumption.
- Impact: Minimizes environmental impact, complies with regulations, and meets the growing demand for sustainable products.
Safety and Compliance:
- Objective: Ensure that manufacturing processes adhere to safety standards and regulatory requirements.
- Impact: Protects workers, reduces the risk of legal issues, and maintains a positive organizational reputation.
Innovation Facilitation:
- Objective: Create a process environment that encourages continuous improvement and innovation.
- Impact: Drives technological advancements and process enhancements, maintaining competitive advantage.
Conclusion: Manufacturing process design and optimization aim to develop production systems that are efficient, cost-effective, high-quality, flexible, sustainable, and safe. Achieving these objectives ensures that manufacturers can meet customer needs, maintain profitability, and sustain long-term success in a competitive market.
2. How does Lean Manufacturing contribute to the optimization of manufacturing processes?
Answer:
Lean Manufacturing is a systematic approach focused on eliminating waste, improving process efficiency, and enhancing product quality. It contributes to the optimization of manufacturing processes through several key principles and practices:
Waste Elimination (Muda):
- Principle: Identify and eliminate non-value-adding activities.
- Impact: Reduces costs, increases efficiency, and streamlines workflows by removing unnecessary steps.
Continuous Improvement (Kaizen):
- Principle: Foster a culture of ongoing, incremental improvements.
- Impact: Encourages regular assessment and enhancement of processes, leading to sustained efficiency gains and adaptability.
Just-In-Time (JIT) Production:
- Principle: Produce only what is needed, when it is needed, and in the amount needed.
- Impact: Minimizes inventory costs, reduces lead times, and ensures a more responsive and flexible production system.
Value Stream Mapping (VSM):
- Principle: Visualize and analyze the flow of materials and information.
- Impact: Identifies bottlenecks and areas of waste, enabling targeted process improvements and enhanced flow.
Standardized Work:
- Principle: Develop and implement consistent procedures for tasks.
- Impact: Ensures uniformity, reduces variability, and enhances predictability and quality in production processes.
5S Methodology:
- Principle: Organize the workplace for efficiency and effectiveness (Sort, Set in Order, Shine, Standardize, Sustain).
- Impact: Creates a clean, organized, and safe work environment, reducing errors and enhancing productivity.
Total Productive Maintenance (TPM):
- Principle: Involve all employees in maintaining and improving equipment.
- Impact: Enhances equipment reliability, reduces downtime, and supports continuous production flow.
Pull Systems:
- Principle: Use demand-driven production signals to control workflow.
- Impact: Prevents overproduction, aligns production with actual demand, and improves inventory management.
Benefits of Lean Manufacturing in Process Optimization:
- Increased Efficiency: Streamlined processes and reduced waste lead to faster production cycles.
- Cost Savings: Eliminating waste and optimizing resource use lowers operational costs.
- Improved Quality: Standardized and continuous improvement practices enhance product quality and consistency.
- Enhanced Flexibility: Lean’s focus on adaptability allows for quicker adjustments to changing market demands.
- Employee Engagement: Involving employees in continuous improvement fosters a motivated and proactive workforce.
Conclusion: Lean Manufacturing provides a comprehensive framework for optimizing manufacturing processes by focusing on waste elimination, continuous improvement, and efficient resource utilization. By implementing Lean principles, manufacturers can achieve significant gains in efficiency, cost reduction, quality, and flexibility, thereby enhancing overall operational performance and competitiveness.
3. What are the key differences between process design and process optimization in manufacturing?
Answer:
Process design and process optimization are two critical stages in the manufacturing lifecycle, each serving distinct purposes and involving different activities. Understanding their key differences is essential for effective manufacturing management.
Process Design:
Definition:
- Process Design is the initial phase of developing a manufacturing process, focusing on creating a blueprint for how products will be produced.
Objectives:
- Create Efficient Processes: Develop workflows that effectively convert raw materials into finished products.
- Ensure Feasibility: Design processes that are technically and economically viable.
- Meet Quality Standards: Establish methods that ensure product quality and consistency.
- Incorporate Safety: Design processes that adhere to safety regulations and minimize hazards.
Activities:
- Conceptualization: Generating ideas for new manufacturing processes.
- Flowcharting: Mapping out the sequence of operations and steps involved.
- Resource Allocation: Determining the necessary equipment, materials, and labor.
- Prototyping: Creating and testing prototypes to validate process design.
- Documentation: Developing detailed process documentation and standard operating procedures (SOPs).
Focus:
- Foundation Building: Establishing the fundamental structure and framework of the manufacturing process.
- Innovation and Planning: Emphasizing the creation of new or improved processes from scratch.
Process Optimization:
Definition:
- Process Optimization involves refining and enhancing existing manufacturing processes to improve performance, efficiency, and quality.
Objectives:
- Increase Efficiency: Streamline workflows to reduce cycle times and resource consumption.
- Reduce Costs: Identify and eliminate inefficiencies and waste to lower operational expenses.
- Enhance Quality: Improve process consistency and product quality.
- Boost Productivity: Increase output without compromising quality or incurring additional costs.
- Enhance Flexibility: Make processes more adaptable to changes in demand or product specifications.
Activities:
- Data Analysis: Collecting and analyzing process data to identify bottlenecks and inefficiencies.
- Lean Techniques: Applying Lean tools like Value Stream Mapping (VSM), 5S, and Kaizen to streamline processes.
- Technology Integration: Incorporating advanced technologies such as automation, IoT, and AI to enhance process performance.
- Continuous Improvement: Implementing incremental changes to continually enhance process efficiency and effectiveness.
- Performance Monitoring: Using metrics and KPIs to track process performance and identify areas for further improvement.
Focus:
- Enhancement: Making incremental or significant improvements to existing processes.
- Sustainability: Ensuring that processes remain efficient, competitive, and capable of meeting evolving demands.
Key Differences:
Aspect | Process Design | Process Optimization |
---|---|---|
Stage | Initial development of manufacturing processes | Refinement of existing processes |
Objective | Create efficient and feasible workflows | Improve performance, efficiency, and quality |
Activities | Conceptualization, flowcharting, prototyping | Data analysis, Lean techniques, technology integration |
Focus | Foundation building and innovation | Enhancement and continuous improvement |
Outcome | Blueprint for production | Enhanced and more efficient production processes |
Approach | Planning and creation | Analysis and refinement |
Conclusion: Process design and process optimization are complementary activities in manufacturing. Process design lays the groundwork by creating efficient and feasible workflows, while process optimization focuses on enhancing and refining these processes to achieve higher efficiency, reduced costs, and improved quality. Both stages are essential for developing robust manufacturing systems that are both effective and adaptable to changing market demands.
4. How do simulation models aid in the design and optimization of manufacturing processes?
Answer:
Simulation models are powerful tools in the design and optimization of manufacturing processes, providing a virtual environment to analyze, predict, and enhance process performance without the risks and costs associated with real-world experimentation. They play a crucial role in decision-making, process validation, and continuous improvement.
Role of Simulation Models in Manufacturing Process Design and Optimization:
Process Visualization:
- Function: Create a visual representation of the manufacturing process, including workflows, machinery, and material flows.
- Benefit: Helps stakeholders understand the process layout and identify potential issues before implementation.
Performance Analysis:
- Function: Assess key performance indicators (KPIs) such as cycle time, throughput, resource utilization, and bottlenecks.
- Benefit: Provides insights into how the process performs under different conditions, enabling informed optimization decisions.
Scenario Testing:
- Function: Simulate various scenarios, such as changes in demand, equipment failures, or process modifications.
- Benefit: Allows manufacturers to evaluate the impact of potential changes and select the most effective strategies without disrupting actual operations.
Capacity Planning:
- Function: Analyze production capacity and identify constraints that limit output.
- Benefit: Helps in making decisions regarding resource allocation, equipment investment, and process adjustments to meet production targets.
Cost Analysis:
- Function: Estimate the costs associated with different process configurations, including labor, materials, and overheads.
- Benefit: Facilitates cost-benefit analysis, helping manufacturers choose the most cost-effective process designs and optimizations.
Quality Control:
- Function: Simulate quality control processes to predict defect rates and identify sources of variability.
- Benefit: Enhances product quality by allowing for the design of robust processes that minimize defects and ensure consistency.
Time Savings:
- Function: Reduce the time required for process development and optimization by testing ideas virtually.
- Benefit: Accelerates the design cycle and enables faster implementation of improvements.
Risk Mitigation:
- Function: Identify and assess potential risks associated with process changes or new designs.
- Benefit: Helps in developing contingency plans and reducing the likelihood of process failures.
Training and Education:
- How: Use simulation models as training tools for employees to understand and interact with new processes.
- Impact: Enhances workforce preparedness and reduces the learning curve when new processes are implemented.
Sustainability Assessment:
- How: Evaluate the environmental impact of different process designs, including energy consumption and waste generation.
- Impact: Supports the design of sustainable manufacturing processes that align with environmental goals and regulations.
Types of Simulation Models Used in Manufacturing:
Discrete Event Simulation (DES):
- Description: Models the operation of a system as a sequence of discrete events.
- Use Case: Analyzing production line performance, scheduling, and logistics.
Monte Carlo Simulation:
- Description: Uses random sampling and statistical modeling to estimate mathematical functions and mimic the operation of complex systems.
- Use Case: Risk assessment and decision-making under uncertainty.
Agent-Based Simulation:
- Description: Models the interactions of autonomous agents to assess their effects on the system.
- Use Case: Studying workforce behavior, machine interactions, and supply chain dynamics.
Computer-Aided Manufacturing (CAM) Simulation:
- Description: Integrates CAD and CAM to simulate the manufacturing process.
- Use Case: Optimizing machining operations and tool paths.
Virtual Reality (VR) and Augmented Reality (AR) Simulations:
- Description: Provide immersive environments for process design and training.
- Use Case: Ergonomic assessments, layout planning, and employee training.
Benefits of Using Simulation Models:
- Cost Efficiency: Reduces the need for physical prototypes and trial-and-error experiments, saving time and resources.
- Enhanced Accuracy: Provides precise data and predictions based on real-time process variables and historical data.
- Improved Decision-Making: Facilitates data-driven decisions by providing comprehensive insights into process performance.
- Flexibility: Allows for easy modifications and testing of various scenarios without impacting actual operations.
- Scalability: Supports the analysis of both small-scale and large-scale manufacturing processes.
Case Example: A car manufacturer used discrete event simulation to analyze its assembly line. By simulating different workstation layouts and production schedules, they identified bottlenecks and optimized the flow of materials. This led to a 15% increase in throughput and a 10% reduction in production costs without significant capital investment.
Conclusion: Simulation models are indispensable in the design and optimization of manufacturing processes, offering a risk-free and cost-effective means to analyze, predict, and enhance process performance. By leveraging various simulation techniques, manufacturers can achieve greater efficiency, quality, and flexibility, ultimately driving operational excellence and competitive advantage.
Manufacturing Process Design: Thought-Provoking Questions with Detailed and Elaborate Answers
1. How can the principles of Design for Manufacturability (DFM) be applied to minimize production costs without compromising product quality?
Answer:
Design for Manufacturability (DFM) is a set of principles aimed at simplifying the manufacturing process, reducing production costs, and ensuring product quality. By integrating DFM early in the product development cycle, manufacturers can identify and eliminate potential production challenges, leading to more efficient and cost-effective manufacturing without compromising quality.
Application of DFM Principles:
Simplify Design:
- How: Reduce the number of parts and use modular designs.
- Impact: Fewer components lead to simpler assembly processes, lower material costs, and reduced chances of defects.
Standardize Components:
- How: Use standard, off-the-shelf parts wherever possible.
- Impact: Reduces procurement costs, simplifies inventory management, and decreases lead times.
Design for Assembly (DFA):
- How: Design parts and assemblies that are easy to put together with minimal steps.
- Impact: Shortens assembly time, reduces labor costs, and lowers the risk of assembly errors.
Minimize Tolerances:
- How: Design parts with tolerances that are as loose as possible without affecting functionality.
- Impact: Reduces manufacturing precision requirements, lowering production costs and speeding up manufacturing processes.
Facilitate Automated Manufacturing:
- How: Design products that can be easily manufactured using automation technologies.
- Impact: Enhances production speed, consistency, and reduces labor costs.
Material Selection:
- How: Choose materials that are readily available, cost-effective, and suitable for the manufacturing process.
- Impact: Lowers material costs and simplifies processing, while ensuring the product meets quality standards.
Error-Proofing (Poka-Yoke):
- How: Incorporate features that prevent incorrect assembly or usage.
- Impact: Enhances product quality by reducing defects and ensuring consistency.
Design for Testing:
- How: Integrate features that make product testing easier and more reliable.
- Impact: Ensures that quality is maintained without significantly increasing production time or costs.
Benefits of Applying DFM Principles:
- Cost Reduction: Simplified designs and standardized components lower production and assembly costs.
- Quality Improvement: Error-proofing and design for testing enhance product reliability and consistency.
- Faster Time-to-Market: Streamlined manufacturing processes accelerate production timelines.
- Scalability: Easier manufacturing processes support increased production volumes without proportional cost increases.
- Sustainability: Efficient designs reduce material waste and energy consumption, supporting environmental goals.
Case Example: An automotive manufacturer redesigned a car’s door assembly by reducing the number of parts and using standardized hinges. This simplification led to a 20% reduction in production costs, a 15% decrease in assembly time, and maintained the door’s structural integrity and functionality, demonstrating the effectiveness of DFM principles in minimizing costs without compromising quality.
Conclusion: By applying Design for Manufacturability principles, manufacturers can achieve significant cost savings and enhance product quality. DFM fosters a collaborative approach between design and manufacturing teams, ensuring that products are not only innovative and functional but also efficient and cost-effective to produce. This alignment leads to sustainable manufacturing practices and a competitive advantage in the market.
2. In what ways can simulation models predict and mitigate potential bottlenecks in the manufacturing process?
Answer:
Simulation models are invaluable tools for predicting and mitigating potential bottlenecks in the manufacturing process. By creating a virtual representation of the manufacturing system, simulation allows manufacturers to analyze process flows, identify constraints, and test various scenarios to optimize performance and prevent bottlenecks from occurring.
How Simulation Models Predict and Mitigate Bottlenecks:
Process Flow Visualization:
- How: Simulate the entire manufacturing process, including workflows, machinery, and material movements.
- Impact: Provides a clear visual representation of the process, making it easier to identify stages where delays or inefficiencies may occur.
Capacity Analysis:
- How: Assess the capacity of each workstation and machine within the simulated environment.
- Impact: Identifies areas where demand exceeds capacity, indicating potential bottlenecks.
Scenario Testing:
- How: Simulate different production scenarios, such as changes in demand, equipment failures, or process modifications.
- Impact: Evaluates how these changes affect the overall system, identifying conditions that may lead to bottlenecks.
Resource Utilization Monitoring:
- How: Track the usage of resources (e.g., labor, machines, materials) in the simulation.
- Impact: Highlights overutilization or underutilization of resources, which can indicate potential bottlenecks or inefficiencies.
Cycle Time Analysis:
- How: Measure the time taken to complete each process step in the simulation.
- Impact: Identifies steps with longer cycle times that may slow down the entire production flow.
Bottleneck Identification:
- How: Analyze simulation data to pinpoint the exact location and cause of bottlenecks.
- Impact: Enables targeted interventions to address the root causes of delays and improve process flow.
Optimization Testing:
- How: Test different optimization strategies within the simulation, such as adjusting process parameters, adding resources, or reconfiguring workflows.
- Impact: Determines the most effective strategies to alleviate bottlenecks without disrupting other parts of the process.
Predictive Maintenance Scheduling:
- How: Use simulation to predict equipment wear and schedule maintenance before breakdowns occur.
- Impact: Prevents unexpected machine downtimes that can cause bottlenecks and disrupt production schedules.
Throughput Maximization:
- How: Simulate the impact of various changes on overall production throughput.
- Impact: Identifies modifications that can increase throughput without introducing new bottlenecks.
Feedback and Continuous Improvement:
- How: Use insights from simulation to implement and test continuous improvement initiatives.
- Impact: Ensures that process optimizations are based on accurate predictions and effective in mitigating bottlenecks.
Benefits of Using Simulation Models to Address Bottlenecks:
- Proactive Identification: Detects potential bottlenecks before they occur in the real world, allowing for timely interventions.
- Cost Savings: Reduces the costs associated with downtime, inefficiencies, and rushed problem-solving.
- Enhanced Efficiency: Streamlines process flows, maximizing resource utilization and improving overall manufacturing efficiency.
- Flexibility: Allows for the testing of multiple scenarios and solutions without disrupting actual operations.
- Informed Decision-Making: Provides data-driven insights that support strategic planning and process optimization.
Case Example: A beverage manufacturer used discrete event simulation to model its bottling line. The simulation revealed that the labeling machine was a potential bottleneck due to its lower throughput compared to other stations. By testing various solutions within the simulation, such as adding an additional labeling machine and optimizing the workflow, the manufacturer was able to implement changes that increased overall line throughput by 20% and eliminated the bottleneck without incurring excessive costs.
Conclusion: Simulation models are essential for predicting and mitigating bottlenecks in manufacturing processes. By providing a virtual environment to analyze and optimize workflows, simulation enables manufacturers to enhance efficiency, reduce costs, and maintain smooth production flows. This proactive approach to process design and optimization ensures that manufacturing operations remain agile, competitive, and capable of meeting market demands effectively.
3. How does the concept of Just-In-Time (JIT) production integrate with process optimization techniques to enhance manufacturing efficiency?
Answer:
Just-In-Time (JIT) production is a Lean Manufacturing strategy aimed at producing only what is needed, when it is needed, and in the amount needed. Integrating JIT with process optimization techniques significantly enhances manufacturing efficiency by minimizing waste, reducing inventory levels, and ensuring a smooth and responsive production flow.
Integration of JIT with Process Optimization Techniques:
Value Stream Mapping (VSM):
- How: Use VSM to visualize the entire production process and identify value-adding and non-value-adding activities.
- Impact: Helps in identifying waste and inefficiencies, allowing for the streamlined implementation of JIT by focusing on value-creating steps.
Continuous Flow:
- How: Design processes to ensure that products move smoothly through each stage without delays.
- Impact: Reduces lead times and aligns production closely with demand, supporting the JIT principle of producing only as needed.
Kanban Systems:
- How: Implement Kanban cards or digital signals to control the flow of materials and production based on actual demand.
- Impact: Ensures that production is closely aligned with customer demand, preventing overproduction and excess inventory.
Standardized Work:
- How: Develop standardized procedures for each process step to ensure consistency and predictability.
- Impact: Enhances process efficiency and reliability, facilitating the smooth implementation of JIT by reducing variability.
Total Productive Maintenance (TPM):
- How: Maintain equipment proactively to prevent breakdowns and ensure continuous production.
- Impact: Supports JIT by minimizing unplanned downtime, ensuring that production flows without interruptions.
Pull-Based Production Planning:
- How: Use pull-based systems where production is triggered by actual consumption rather than forecasts.
- Impact: Aligns production closely with real-time demand, reducing the risk of overproduction and excess inventory.
Inventory Optimization:
- How: Analyze inventory levels and turnover rates to maintain minimal yet sufficient stock.
- Impact: Reduces storage costs and minimizes the risk of inventory obsolescence, aligning with JIT’s focus on lean inventory.
Flexible Workforce:
- How: Train employees to perform multiple roles and adapt to varying production demands.
- Impact: Enhances workforce flexibility, enabling quick adjustments to production schedules in line with JIT requirements.
Process Redesign:
- How: Reconfigure production processes to eliminate bottlenecks and ensure a balanced workflow.
- Impact: Supports continuous flow and reduces lead times, essential for effective JIT implementation.
Supplier Integration:
- How: Develop close relationships with suppliers to ensure timely delivery of materials and components.
- Impact: Enhances supply chain reliability, enabling JIT by ensuring that materials arrive exactly when needed.
Benefits of Integrating JIT with Process Optimization:
- Waste Reduction: Minimizes waste by aligning production with actual demand and eliminating excess inventory.
- Cost Savings: Reduces costs associated with inventory storage, handling, and obsolescence.
- Enhanced Efficiency: Streamlined processes and continuous flow increase overall manufacturing efficiency.
- Improved Quality: Standardized work and proactive maintenance enhance product quality and consistency.
- Faster Response to Demand Changes: Enables quick adjustments to production schedules, enhancing responsiveness to market fluctuations.
- Lower Lead Times: Reduces the time from order to delivery, improving customer satisfaction and competitiveness.
Case Example: A furniture manufacturer integrated JIT with process optimization by implementing Kanban systems and conducting value stream mapping. They identified and eliminated non-value-adding activities, streamlined workflows, and established close relationships with key suppliers to ensure timely material deliveries. This integration led to a 30% reduction in inventory levels, a 25% decrease in lead times, and significant cost savings from reduced waste and improved efficiency.
Conclusion: Integrating Just-In-Time production with process optimization techniques is a powerful strategy for enhancing manufacturing efficiency. By aligning production closely with actual demand, minimizing waste, and streamlining processes, manufacturers can achieve significant improvements in cost savings, efficiency, and quality. This synergy not only supports Lean Manufacturing principles but also positions organizations for greater agility and competitiveness in dynamic market environments.
4. How can the principles of Six Sigma be applied alongside Lean Manufacturing to achieve process excellence in manufacturing?
Answer:
Six Sigma and Lean Manufacturing are complementary methodologies that, when combined, form Lean Six Sigma—a powerful approach to achieving process excellence in manufacturing. While Lean focuses on waste elimination and process efficiency, Six Sigma emphasizes reducing variability and defects. Integrating these principles leads to comprehensive improvements in both efficiency and quality.
Application of Six Sigma Principles alongside Lean Manufacturing:
Define Phase (Six Sigma) with Value Stream Mapping (Lean):
- How: Clearly define project goals and customer requirements using Lean’s Value Stream Mapping to visualize and understand the process flow.
- Impact: Aligns improvement projects with customer value and identifies critical areas for enhancement.
Measure Phase (Six Sigma) with Lean Metrics:
- How: Collect data on process performance using Six Sigma tools (e.g., process mapping, data collection plans) and integrate Lean metrics such as cycle time and throughput.
- Impact: Provides a comprehensive understanding of both quality and efficiency, establishing a baseline for improvement.
Analyze Phase (Six Sigma) with Root Cause Analysis (Lean):
- How: Use Six Sigma’s statistical analysis techniques and Lean’s root cause analysis methods (e.g., 5 Whys, Fishbone diagrams) to identify the underlying causes of defects and inefficiencies.
- Impact: Enables targeted and effective solutions that address both quality and process performance issues.
Improve Phase (Six Sigma) with Lean Solutions:
- How: Develop and implement improvements using Six Sigma’s DMAIC framework combined with Lean tools like Kaizen, 5S, and Kanban.
- Impact: Enhances process efficiency while simultaneously improving quality and reducing defects.
Control Phase (Six Sigma) with Standardized Work (Lean):
- How: Establish control mechanisms using Six Sigma’s control charts and Lean’s standardized work procedures to maintain improvements.
- Impact: Ensures sustained process performance and prevents regression to previous inefficiencies and defect rates.
Benefits of Combining Six Sigma with Lean Manufacturing:
- Comprehensive Improvement: Addresses both efficiency (Lean) and quality (Six Sigma), leading to holistic process optimization.
- Enhanced Problem-Solving: Utilizes a broader range of tools and techniques, enabling more effective identification and resolution of issues.
- Increased Flexibility: Combines the strengths of both methodologies, allowing organizations to adapt to various types of challenges.
- Greater Cost Savings: Reduces costs associated with waste, defects, and inefficiencies.
- Improved Customer Satisfaction: Delivers high-quality products efficiently, meeting or exceeding customer expectations.
- Stronger Competitive Advantage: Achieves operational excellence by leveraging the complementary strengths of Lean and Six Sigma, positioning the organization as a leader in quality and efficiency.
Case Example: A high-precision engineering company implemented Lean Six Sigma to optimize its machining processes. Lean tools like 5S and Kaizen were used to streamline workflows and eliminate non-value-adding activities. Concurrently, Six Sigma’s DMAIC framework was applied to reduce defects in machined parts. This integration resulted in a 40% reduction in production lead times, a 30% decrease in defect rates, and significant cost savings from reduced waste and rework.
Conclusion: Applying Six Sigma principles alongside Lean Manufacturing creates a synergistic approach that drives process excellence in manufacturing. By combining Lean’s focus on waste elimination and efficiency with Six Sigma’s emphasis on quality and defect reduction, organizations can achieve comprehensive improvements that enhance both operational performance and customer satisfaction. This integrated methodology, Lean Six Sigma, is instrumental in fostering a culture of continuous improvement and excellence, ensuring sustained competitive advantage in the manufacturing sector.
5. What are the key factors to consider when selecting software tools for manufacturing process design and optimization?
Answer:
Selecting the right software tools for manufacturing process design and optimization is critical for achieving operational excellence and maintaining a competitive edge. Key factors to consider ensure that the chosen tools align with organizational needs, enhance efficiency, and support continuous improvement initiatives.
Key Factors to Consider:
Functionality and Features:
- How: Assess whether the software offers the necessary features for process design, simulation, data analysis, and optimization.
- Impact: Ensures that the tool can handle specific manufacturing requirements and support comprehensive process management.
Integration Capabilities:
- How: Evaluate the software’s ability to integrate with existing systems such as ERP, CAD/CAM, and MES.
- Impact: Facilitates seamless data flow and communication between different systems, enhancing overall operational efficiency.
Scalability:
- How: Determine whether the software can scale with the organization’s growth and evolving process complexity.
- Impact: Ensures long-term usability and adaptability, preventing the need for frequent tool replacements.
User-Friendliness and Ease of Use:
- How: Consider the software’s user interface, ease of navigation, and learning curve.
- Impact: Enhances user adoption, reduces training time, and increases overall productivity by enabling users to efficiently utilize the tool.
Customization and Flexibility:
- How: Assess the ability to customize the software to fit specific process requirements and workflows.
- Impact: Allows for tailored solutions that meet unique manufacturing needs, improving process alignment and effectiveness.
Data Security and Compliance:
- How: Ensure that the software complies with industry standards and offers robust data security features.
- Impact: Protects sensitive manufacturing data, ensures compliance with regulations, and safeguards intellectual property.
Cost and Return on Investment (ROI):
- How: Evaluate the total cost of ownership, including licensing, implementation, training, and maintenance.
- Impact: Determines the financial feasibility and ensures that the software provides a positive ROI through cost savings and efficiency gains.
Vendor Support and Reliability:
- How: Consider the vendor’s reputation, customer support services, and software reliability.
- Impact: Ensures timely assistance, regular updates, and minimal downtime, enhancing the tool’s effectiveness and reliability.
Analytical and Reporting Capabilities:
- How: Assess the software’s ability to analyze process data, generate reports, and visualize performance metrics.
- Impact: Provides actionable insights and supports data-driven decision-making for process optimization.
Training and Documentation:
- How: Evaluate the availability of training resources, user manuals, and documentation.
- Impact: Facilitates effective use of the software, reducing the learning curve and ensuring that users can maximize its potential.
User Community and Reviews:
- How: Research user communities, forums, and reviews to gauge user satisfaction and gather feedback.
- Impact: Provides insights into the software’s real-world performance and helps identify potential issues or benefits.
Future-Proofing:
- How: Consider the software’s ability to adapt to future technological advancements and industry trends.
- Impact: Ensures that the tool remains relevant and capable of supporting future process enhancements and innovations.
Benefits of Selecting the Right Software Tools:
- Enhanced Efficiency: Streamlines process design and optimization tasks, saving time and resources.
- Improved Quality: Enables precise process control and quality assurance, reducing defects and variability.
- Data-Driven Decisions: Provides comprehensive data analysis and reporting, supporting informed decision-making.
- Flexibility and Adaptability: Facilitates quick adjustments to processes in response to changing demands or conditions.
- Cost Savings: Optimizes resource utilization and reduces waste, leading to significant cost reductions.
- Competitive Advantage: Empowers organizations to innovate and optimize processes more effectively, enhancing competitiveness.
Case Example: A high-tech electronics manufacturer selected a comprehensive process design and optimization software that integrated seamlessly with their existing ERP and CAD systems. The software’s robust simulation and data analysis features enabled the company to identify and eliminate inefficiencies in their production line, resulting in a 20% reduction in process planning time, a 15% decrease in production errors, and a 10% increase in overall manufacturing efficiency.
Conclusion: Selecting the right software tools for manufacturing process design and optimization is a strategic decision that requires careful consideration of functionality, integration capabilities, scalability, user-friendliness, customization, cost, vendor support, and more. By thoroughly evaluating these factors, manufacturers can choose tools that not only meet their current needs but also support future growth and continuous improvement, thereby driving operational excellence and maintaining a competitive edge in the market.
6. How can Design of Experiments (DOE) methodologies be leveraged to identify optimal process settings in manufacturing?
Answer:
Design of Experiments (DOE) is a structured, statistical approach used to determine the relationship between factors affecting a process and the output of that process. In manufacturing, DOE methodologies can be leveraged to identify optimal process settings by systematically experimenting with different variables to understand their effects and interactions, ultimately leading to enhanced process performance and product quality.
Leveraging DOE Methodologies to Identify Optimal Process Settings:
Define Objectives:
- How: Clearly outline the goals of the experiment, such as maximizing product yield, minimizing defects, or reducing cycle time.
- Impact: Ensures that the DOE focuses on relevant factors that contribute to achieving the desired outcomes.
Identify Factors and Levels:
- How: Determine the process variables (factors) that influence the output and select the specific values or settings (levels) for each factor.
- Impact: Facilitates a comprehensive exploration of the factors that significantly impact process performance.
Choose an Experimental Design:
- How: Select an appropriate DOE design, such as full factorial, fractional factorial, or response surface methodology, based on the number of factors and desired precision.
- Impact: Ensures efficient and comprehensive data collection, allowing for accurate analysis of factor effects and interactions.
Conduct the Experiments:
- How: Execute the experiments according to the selected design, systematically varying the factors and recording the corresponding outputs.
- Impact: Generates reliable data for analyzing the effects of different factor combinations on process performance.
Analyze the Results:
- How: Use statistical tools and software to analyze the data, identifying significant factors and determining the optimal settings.
- Impact: Provides insights into how factors influence the process, enabling the identification of optimal conditions for desired outcomes.
Implement Optimal Settings:
- How: Apply the identified optimal factor settings to the manufacturing process.
- Impact: Enhances process performance, leading to improved product quality and efficiency.
Validate and Monitor:
- How: Conduct additional experiments or monitoring to confirm that the optimal settings achieve the desired results consistently.
- Impact: Ensures that the process remains stable and continues to perform optimally under real-world conditions.
Benefits of Using DOE in Manufacturing:
- Systematic Approach: Provides a structured method for investigating process variables and their effects.
- Efficiency: Reduces the number of experiments needed to identify significant factors, saving time and resources.
- Improved Quality: Identifies optimal settings that enhance product quality and consistency.
- Cost Reduction: Optimizes process parameters to minimize waste, defects, and operational costs.
- Enhanced Understanding: Facilitates a deeper understanding of the process dynamics and factor interactions.
- Data-Driven Decisions: Supports informed decision-making based on empirical data and statistical analysis.
Case Example: A pharmaceutical manufacturer sought to optimize its tablet compression process to minimize variability in tablet weight. Using DOE, they identified that pressure, dwell time, and material moisture content were significant factors affecting tablet weight. By systematically experimenting with different levels of these factors, they determined the optimal settings that reduced weight variability by 40%, ensuring consistent product quality and compliance with regulatory standards.
Conclusion: Design of Experiments methodologies are invaluable in manufacturing process optimization, providing a systematic and efficient approach to identifying optimal process settings. By leveraging DOE, manufacturers can enhance process performance, improve product quality, and achieve significant cost savings, thereby driving operational excellence and maintaining a competitive edge in the market.
7. How can the integration of IoT technologies enhance the real-time monitoring and control of manufacturing processes?
Answer:
Integrating Internet of Things (IoT) technologies into manufacturing processes significantly enhances real-time monitoring and control by enabling continuous data collection, connectivity, and intelligent automation. This integration transforms traditional manufacturing into a smart, connected ecosystem that optimizes performance, increases efficiency, and ensures high-quality production.
Enhancements to Real-Time Monitoring and Control through IoT Integration:
Continuous Data Collection:
- How: Deploy IoT sensors and devices to collect real-time data on various process parameters (e.g., temperature, pressure, machine vibrations).
- Impact: Provides a constant stream of data, allowing for immediate detection of anomalies and process deviations.
Remote Monitoring:
- How: Utilize cloud-based platforms to access process data from anywhere, enabling remote supervision.
- Impact: Enhances flexibility and allows managers to monitor operations in real-time without being physically present, improving responsiveness.
Predictive Analytics:
- How: Analyze data from IoT devices using machine learning algorithms to predict equipment failures and maintenance needs.
- Impact: Enables proactive maintenance scheduling, reducing unplanned downtime and extending equipment lifespan.
Automated Control Systems:
- How: Integrate IoT with control systems to enable automatic adjustments based on real-time data.
- Impact: Enhances process stability and efficiency by maintaining optimal conditions without manual intervention.
Enhanced Quality Control:
- How: Monitor quality parameters continuously and use IoT data to identify and correct quality issues in real-time.
- Impact: Ensures consistent product quality, reduces defect rates, and minimizes rework and scrap.
Energy Management:
- How: Track and analyze energy usage across different parts of the manufacturing process using IoT sensors.
- Impact: Identifies energy-saving opportunities, reduces energy consumption, and lowers operational costs.
Supply Chain Integration:
- How: Use IoT to track inventory levels, material movements, and supplier performance in real-time.
- Impact: Enhances supply chain visibility, reduces lead times, and ensures timely availability of materials, supporting Just-In-Time (JIT) production.
Real-Time Dashboards and Visualization:
- How: Implement dashboards that display real-time data and key performance indicators (KPIs) for easy monitoring.
- Impact: Facilitates quick decision-making and ensures that all stakeholders have access to up-to-date information.
Scalability and Flexibility:
- How: Easily scale IoT deployments to cover additional processes or facilities as needed.
- Impact: Supports growing manufacturing operations and the integration of new technologies without significant overhauls.
Enhanced Safety and Compliance:
- How: Monitor safety parameters and ensure compliance with regulatory standards through real-time data.
- Impact: Enhances workplace safety, reduces the risk of accidents, and ensures adherence to industry regulations.
Benefits of IoT Integration in Real-Time Monitoring and Control:
- Improved Efficiency: Real-time insights enable immediate adjustments to optimize process performance.
- Reduced Downtime: Predictive maintenance and automated controls minimize equipment failures and operational interruptions.
- Enhanced Quality: Continuous monitoring ensures that products meet quality standards consistently.
- Cost Savings: Optimized energy usage and reduced waste lower operational costs.
- Increased Agility: Real-time data allows manufacturers to quickly respond to changes in demand or production conditions.
- Better Decision-Making: Data-driven insights support informed and strategic decision-making, enhancing overall operational performance.
- Enhanced Collaboration: Shared real-time data fosters better communication and collaboration among teams and departments.
Case Example: A semiconductor manufacturer integrated IoT sensors across its fabrication equipment to monitor temperature and pressure in real-time. The data was analyzed using predictive analytics to forecast potential equipment failures. By implementing proactive maintenance based on these insights, the manufacturer reduced unplanned downtime by 30%, increased overall equipment effectiveness (OEE) by 20%, and maintained consistent product quality, leading to higher customer satisfaction and reduced operational costs.
Conclusion: The integration of IoT technologies into manufacturing processes revolutionizes real-time monitoring and control by providing continuous data, enhancing connectivity, and enabling intelligent automation. This integration leads to improved efficiency, reduced downtime, enhanced quality, and significant cost savings, positioning manufacturers for sustained operational excellence and competitive advantage in the evolving industrial landscape.
8. What are the common challenges faced when integrating Computer-Aided Process Planning (CAPP) with existing manufacturing systems, and how can they be addressed?
Answer:
Integrating Computer-Aided Process Planning (CAPP) with existing manufacturing systems can present several challenges that may hinder seamless operation and full utilization of the CAPP tool’s capabilities. Understanding these challenges and implementing effective strategies to address them is essential for successful integration and optimization.
Common Challenges:
Compatibility Issues:
- Description: Ensuring that CAPP software is compatible with existing systems such as ERP, CAD/CAM, and MES.
- Impact: Incompatibility can lead to data silos, communication breakdowns, and inefficiencies in process planning and execution.
Data Integration and Migration:
- Description: Transferring and synchronizing data between CAPP and other manufacturing systems.
- Impact: Data inconsistencies, loss of information, and errors can occur, affecting the accuracy and reliability of process plans.
High Implementation Costs:
- Description: Significant financial investment required for purchasing, customizing, and implementing CAPP software.
- Impact: Can be a barrier for small and medium-sized enterprises (SMEs) with limited budgets, delaying or preventing adoption.
Complexity of Implementation:
- Description: The technical complexity involved in integrating CAPP with diverse manufacturing systems and workflows.
- Impact: Requires specialized knowledge and expertise, increasing the time and resources needed for successful implementation.
Resistance to Change:
- Description: Employees and managers may resist adopting new technologies and changing established workflows.
- Impact: Can lead to low user adoption, reduced effectiveness of the CAPP system, and hindered process improvements.
Training and Skill Development:
- Description: Ensuring that employees are adequately trained to use the new CAPP system effectively.
- Impact: Lack of proper training can result in underutilization of the system’s capabilities and continued reliance on manual processes.
Customization and Scalability:
- Description: Adapting CAPP software to meet specific manufacturing needs and ensuring it can scale with business growth.
- Impact: May require additional customization and investment to ensure that systems remain effective and relevant.
Data Security and Privacy:
- Description: Protecting sensitive manufacturing data during and after integration.
- Impact: Data breaches or unauthorized access can lead to loss of intellectual property, regulatory penalties, and damage to the organization’s reputation.
Maintenance and Support:
- Description: Providing ongoing technical support and maintenance for the integrated CAPP system.
- Impact: Ensures the system remains functional and up-to-date, but can be resource-intensive.
Strategies to Address Integration Challenges:
Comprehensive Planning:
- Action: Develop a detailed integration plan that outlines objectives, timelines, resource requirements, and key milestones.
- Impact: Provides a clear roadmap, ensuring all aspects of the integration are considered and managed effectively.
Choose Compatible CAPP Software:
- Action: Select CAPP software that is designed to integrate seamlessly with existing systems and supports standard communication protocols.
- Impact: Minimizes compatibility issues and facilitates smoother data exchange between systems.
Engage Stakeholders Early:
- Action: Involve key stakeholders, including IT, manufacturing, and process planning teams, in the integration process.
- Impact: Ensures that all perspectives are considered, fostering collaboration and addressing concerns proactively.
Data Standardization and Cleaning:
- Action: Standardize data formats and clean existing data before migration to ensure consistency and accuracy.
- Impact: Reduces the risk of data inconsistencies and errors, enhancing the reliability of process plans.
Phased Implementation:
- Action: Implement the CAPP system in phases, starting with specific departments or processes before scaling up.
- Impact: Allows for testing and refinement, minimizing disruptions and enabling gradual adaptation.
Provide Comprehensive Training:
- Action: Offer extensive training programs to educate employees on using the CAPP system effectively.
- Impact: Increases user competence and confidence, promoting higher adoption rates and effective utilization of the system.
Customizable Solutions:
- Action: Choose CAPP software that offers customization options to align with specific manufacturing workflows and requirements.
- Impact: Ensures that the system meets the unique needs of the organization, enhancing its effectiveness.
Robust Data Security Measures:
- Action: Implement strong data security protocols, including encryption, access controls, and regular security audits.
- Impact: Protects sensitive manufacturing data, ensuring compliance with data privacy regulations and safeguarding intellectual property.
Vendor Collaboration:
- Action: Work closely with the CAPP software vendor for support, customization, and troubleshooting during and after integration.
- Impact: Ensures that systems are tailored to meet specific manufacturing needs and integrate smoothly with existing infrastructure.
Continuous Monitoring and Improvement:
- Action: Regularly monitor the performance of the integrated CAPP system and seek feedback from users to identify areas for improvement.
- Impact: Facilitates ongoing optimization, ensuring that the system continues to meet evolving manufacturing needs effectively.
Case Example: A medium-sized automotive parts manufacturer faced challenges integrating its CAPP system with existing CAD and ERP systems. To address compatibility issues, they selected a CAPP software known for its seamless integration capabilities and worked closely with the vendor to customize the interface. They conducted comprehensive training sessions for employees and implemented the system in phases, starting with the most critical production lines. As a result, the manufacturer achieved a 20% reduction in process planning time, improved accuracy in production orders, and enhanced overall manufacturing efficiency.
Conclusion: Integrating Computer-Aided Process Planning with existing manufacturing systems presents several challenges, including compatibility issues, data integration, high costs, complexity, and resistance to change. However, by adopting strategic approaches such as comprehensive planning, phased implementation, thorough training, and robust data security measures, manufacturers can successfully overcome these challenges. Effective integration of CAPP systems enhances process design and optimization, leading to improved efficiency, reduced costs, and higher product quality, thereby driving operational excellence and competitive advantage.
9. How can Lean Manufacturing principles be applied to supply chain management to enhance efficiency and reduce costs?
Answer:
Applying Lean Manufacturing principles to supply chain management can significantly enhance efficiency, reduce costs, and improve overall supply chain performance. Lean focuses on eliminating waste, optimizing processes, and ensuring that all activities add value to the customer, making it highly effective for streamlining supply chain operations.
Application of Lean Principles to Supply Chain Management:
Value Stream Mapping (VSM):
- How: Map out the entire supply chain process from supplier to customer to identify value-adding and non-value-adding activities.
- Impact: Provides a comprehensive view of the supply chain, highlighting areas where waste can be eliminated and efficiency can be improved.
Just-In-Time (JIT) Inventory:
- How: Implement JIT strategies to align inventory levels with actual demand, minimizing excess stock.
- Impact: Reduces inventory holding costs, lowers the risk of obsolescence, and improves cash flow by producing and delivering products only as needed.
Kanban Systems:
- How: Use Kanban cards or digital signals to control the flow of materials and production based on real-time demand.
- Impact: Ensures that production is closely aligned with customer demand, preventing overproduction and excess inventory.
Supplier Integration and Collaboration:
- How: Develop close relationships with key suppliers to enhance communication, share forecasts, and coordinate production schedules.
- Impact: Improves supplier reliability, reduces lead times, and ensures the timely delivery of quality materials, enhancing overall supply chain efficiency.
Continuous Improvement (Kaizen) in Supply Chain Processes:
- How: Encourage ongoing evaluation and refinement of supply chain processes through employee involvement and Kaizen events.
- Impact: Drives incremental improvements that enhance efficiency, reduce waste, and adapt to changing market conditions.
Standardization of Processes:
- How: Establish standardized procedures for ordering, receiving, storing, and handling materials across the supply chain.
- Impact: Reduces variability, minimizes errors, and ensures consistency in supply chain operations.
Demand Forecasting and Planning:
- How: Utilize Lean tools and techniques to improve demand forecasting accuracy and production planning.
- Impact: Enhances the alignment between supply and demand, reducing the risk of stockouts and overproduction.
Lean Warehousing:
- How: Apply Lean principles to warehouse layout, inventory management, and material handling to optimize space and improve flow.
- Impact: Increases warehouse efficiency, reduces storage costs, and enhances the speed and accuracy of order fulfillment.
Transportation Optimization:
- How: Streamline transportation routes and schedules to minimize delays and reduce transportation costs.
- Impact: Enhances delivery speed, reduces fuel consumption, and lowers overall logistics expenses.
Supplier Development and Training:
- How: Provide Lean training and support to suppliers to ensure they can meet quality and delivery standards.
- Impact: Improves supplier performance, reliability, and alignment with Lean supply chain objectives.
Benefits of Applying Lean to Supply Chain Management:
- Cost Reduction: Eliminates waste and inefficiencies, leading to lower operational costs.
- Enhanced Efficiency: Streamlined processes improve the speed and reliability of the supply chain.
- Improved Quality: Consistent processes and close supplier collaboration enhance product quality.
- Reduced Lead Times: Efficient supply chain operations shorten lead times, enabling quicker response to customer demands.
- Greater Flexibility: Lean supply chains can quickly adapt to changes in demand, product variations, and market conditions.
- Better Customer Satisfaction: Reliable and efficient supply chains ensure timely delivery of quality products, increasing customer satisfaction and loyalty.
- Sustainable Operations: Lean practices promote efficient resource utilization and waste reduction, supporting environmental sustainability goals.
Case Example: A consumer electronics manufacturer applied Lean principles to its supply chain by implementing Kanban systems and conducting value stream mapping. They identified and eliminated non-value-adding activities, streamlined workflows, and established close relationships with key suppliers to ensure timely material deliveries. This integration led to a 30% reduction in inventory levels, a 25% decrease in lead times, and significant cost savings from reduced waste and improved efficiency.
Conclusion: Integrating Lean Manufacturing principles into supply chain management offers substantial benefits, including enhanced efficiency, reduced costs, improved quality, and greater flexibility. By focusing on waste elimination, process optimization, and close supplier collaboration, manufacturers can create more responsive, reliable, and cost-effective supply chains. This alignment not only improves operational performance but also strengthens the organization’s ability to meet customer demands effectively, driving sustained success and competitive advantage in the market.
10. How can manufacturers ensure the scalability and flexibility of their automation and robotics systems to adapt to changing production needs?
Answer:
Ensuring the scalability and flexibility of automation and robotics systems is crucial for manufacturers to adapt to evolving production needs, market demands, and technological advancements. Scalability allows systems to grow with increased production, while flexibility enables quick adjustments to handle different tasks or product variations. Manufacturers can achieve scalability and flexibility through thoughtful design, modularity, advanced software, and strategic planning.
Strategies to Ensure Scalability and Flexibility:
Modular System Design:
- How: Implement automation and robotics systems composed of interchangeable modules that can be easily added, removed, or reconfigured.
- Impact: Facilitates incremental expansion and adaptation to different production requirements without overhauling the entire system.
Standardized Interfaces and Protocols:
- How: Use standardized communication protocols and interfaces for system components to ensure interoperability.
- Impact: Simplifies the integration of new technologies and components, enhancing system scalability and flexibility.
Cloud-Based Control Systems:
- How: Utilize cloud computing for centralized control, data storage, and system management.
- Impact: Enables remote monitoring, real-time data access, and easier system updates, supporting scalable and flexible operations.
Flexible Robotics:
- How: Deploy robots designed for multi-tasking and easy reprogramming to handle various production processes.
- Impact: Allows for quick adaptation to different tasks and product types, increasing the versatility of robotic systems.
Advanced Software and AI Integration:
- How: Integrate advanced software solutions and AI algorithms to enable adaptive and intelligent system behavior.
- Impact: Enhances the ability of automation systems to learn from data, optimize processes, and adjust to changing conditions dynamically.
Predictive Maintenance and Monitoring:
- How: Implement predictive maintenance tools to monitor system health and anticipate maintenance needs.
- Impact: Reduces downtime, ensures continuous operation, and allows for smoother scaling as production demands increase.
Collaborative Robots (Cobots):
- How: Use cobots that can easily work alongside human workers and adapt to different tasks.
- Impact: Enhances system flexibility by allowing robots to handle a variety of functions without extensive reprogramming.
Flexible Material Handling Systems:
- How: Implement automated guided vehicles (AGVs) and conveyor systems that can be reconfigured to accommodate different workflows.
- Impact: Supports dynamic changes in production layout and process flows, enhancing overall system adaptability.
Data Analytics and Real-Time Monitoring:
- How: Utilize data analytics to gain insights into system performance and identify areas for improvement.
- Impact: Enables proactive adjustments and optimizations, ensuring that automation systems remain efficient and responsive to changing needs.
Scalable Workforce Training Programs:
- How: Develop training programs that can scale with the implementation of new automation technologies.
- Impact: Ensures that the workforce can effectively operate and maintain scalable and flexible automation systems.
Benefits of Scalability and Flexibility:
- Adaptability to Market Changes: Enables manufacturers to respond quickly to shifts in market demand, product variations, and new business opportunities.
- Cost Efficiency: Avoids the need for significant capital investment when scaling operations, as systems can be incrementally expanded.
- Operational Resilience: Flexible systems can better withstand disruptions, such as changes in supply chains or sudden increases in demand.
- Enhanced Innovation: Scalable and flexible systems encourage experimentation and the adoption of new technologies, promoting continuous improvement and innovation.
- Sustained Competitiveness: Ensures that manufacturing operations remain agile and capable of meeting evolving customer needs, maintaining a competitive advantage.
Case Example: A high-tech electronics manufacturer implemented flexible ergonomic workstations equipped with adjustable heights and modular components. Whenever a new production line was introduced, ergonomists conducted assessments and adjusted workstations accordingly. Additionally, the company provided regular training on ergonomic practices and utilized wearable posture sensors to monitor worker movements. As a result, they maintained low injury rates, high worker satisfaction, and sustained productivity levels despite frequent changes in production processes and equipment.
Conclusion: Ensuring the scalability and flexibility of automation and robotics systems is essential for manufacturers to remain agile and competitive in a dynamic market. By adopting modular designs, standardized interfaces, advanced software, and flexible workforce training, manufacturers can create adaptable and expandable systems that respond effectively to changing production needs. This strategic approach not only supports growth and operational resilience but also fosters innovation and cost efficiency, positioning manufacturers for sustained success in the future of manufacturing.
11. How can manufacturers integrate ergonomic principles into the design of manufacturing tools and equipment to enhance usability and reduce strain on workers?
Answer:
Integrating ergonomic principles into the design of manufacturing tools and equipment is essential for enhancing usability, reducing physical strain on workers, and improving overall productivity and job satisfaction. Ergonomically designed tools and equipment align with the natural movements and capabilities of workers, minimizing the risk of musculoskeletal disorders (MSDs) and other injuries.
Key Ergonomic Principles for Tool and Equipment Design:
Anthropometric Considerations:
- How: Design tools and equipment to accommodate a wide range of body sizes, shapes, and strengths.
- Impact: Ensures that tools are comfortable and easy to use for all workers, reducing the risk of strain and injury.
Neutral Postures:
- How: Design tools that allow workers to maintain neutral body postures, avoiding excessive bending, twisting, or reaching.
- Impact: Minimizes musculoskeletal strain and fatigue, enhancing worker comfort and endurance.
Minimize Force Requirements:
- How: Design tools that require minimal force to operate, using lightweight materials and efficient mechanisms.
- Impact: Reduces the physical effort required by workers, decreasing muscle fatigue and the risk of overexertion injuries.
Enhance Grip Comfort and Control:
- How: Incorporate ergonomic grips with contoured shapes, soft materials, and appropriate sizes to fit the hand naturally.
- Impact: Improves control and precision in tool use, reducing the likelihood of slips and errors while enhancing worker comfort.
Balanced Weight Distribution:
- How: Ensure that tools and equipment have balanced weight distribution to reduce the physical strain on specific body parts.
- Impact: Enhances ease of handling, reducing fatigue and improving task performance.
Adjustable Features:
- How: Include adjustable components such as handle angles, tool heights, and extension lengths to customize tools for different tasks and user preferences.
- Impact: Increases versatility and adaptability, allowing workers to optimize tool use for various tasks and reduce ergonomic risks.
Vibration and Noise Reduction:
- How: Design tools with vibration-dampening materials and noise-reducing features to minimize exposure to harmful vibrations and excessive noise.
- Impact: Protects workers from vibration-induced injuries and reduces noise-related stress, enhancing overall comfort and safety.
Intuitive Design:
- How: Create tools and equipment with intuitive controls and interfaces that align with natural human movements and cognitive processes.
- Impact: Simplifies tool operation, reducing the learning curve and minimizing the risk of user errors.
Durability and Maintenance:
- How: Design tools and equipment for easy maintenance and durability, ensuring that they remain in optimal condition with minimal effort.
- Impact: Enhances tool longevity and reliability, reducing downtime and maintenance-related strain on workers.
Safety Features:
- How: Integrate safety mechanisms such as guards, automatic shut-offs, and emergency stops into tool and equipment designs.
- Impact: Protects workers from accidental injuries and ensures safe operation of tools and equipment.
Examples of Ergonomic Tool and Equipment Design:
Ergonomic Hand Tools:
- Example: Screwdrivers with soft, cushioned grips and balanced weights reduce hand fatigue and improve precision in assembly tasks.
Adjustable Assembly Tables:
- Example: Height-adjustable tables allow workers to switch between sitting and standing positions, promoting neutral postures and reducing back strain.
Robotic Exoskeletons:
- Example: Wearable exoskeletons assist workers in lifting heavy objects, reducing the physical effort required and minimizing the risk of back injuries.
Anti-Vibration Gloves:
- Example: Gloves designed to absorb and dampen vibrations from power tools protect workers from vibration-induced injuries and enhance grip comfort.
Automated Material Handling Systems:
- Example: Conveyor belts and robotic arms handle repetitive or heavy lifting tasks, reducing the physical demands on human workers and enhancing efficiency.
Benefits of Integrating Ergonomic Principles:
Enhanced Usability:
- Impact: Tools and equipment that are easy and comfortable to use improve task performance and reduce the likelihood of user errors.
Reduced Physical Strain:
- Impact: Ergonomically designed tools minimize muscle fatigue and strain, promoting worker health and longevity.
Increased Productivity:
- Impact: Comfortable and efficient tools enable workers to perform tasks more quickly and accurately, boosting overall productivity.
Improved Worker Satisfaction:
- Impact: Ergonomic tools contribute to a more satisfying work experience, enhancing job satisfaction and reducing turnover rates.
Lower Injury Rates:
- Impact: Reduced physical strain and enhanced safety features decrease the risk of workplace injuries, leading to a healthier workforce.
Case Example: A manufacturing plant integrated TPM with Lean by implementing autonomous maintenance practices and using OEE to monitor equipment performance. Operators were trained to perform daily maintenance tasks, and predictive maintenance schedules were established based on real-time data. This integration led to a 35% reduction in equipment downtime, a 20% increase in overall productivity, and a significant improvement in product quality, demonstrating the effectiveness of combining TPM with Lean principles.
Conclusion: Integrating ergonomic principles into the design of manufacturing tools and equipment is essential for enhancing usability, reducing physical strain, and improving overall worker well-being and productivity. By focusing on user-centered design, manufacturers can create tools and equipment that support healthy and efficient work practices, leading to safer, more productive, and more satisfying manufacturing environments.
12. How does Lean Manufacturing influence the financial performance of a manufacturing organization, and what financial metrics can be used to assess its impact?
Answer:
Lean Manufacturing significantly influences the financial performance of a manufacturing organization by enhancing efficiency, reducing costs, improving product quality, and increasing customer satisfaction. These improvements collectively contribute to higher profitability, better cash flow, and a stronger competitive position in the market.
Influence of Lean on Financial Performance:
Cost Reduction:
- How: Lean eliminates waste (Muda), optimizes processes, and reduces inefficiencies.
- Impact: Lowers operational costs, improves profit margins, and enhances overall financial health.
Increased Productivity:
- How: Streamlined processes and continuous improvement initiatives enhance workforce and equipment productivity.
- Impact: Increases output without a proportional increase in costs, leading to higher revenues and profitability.
Improved Quality:
- How: Lean focuses on quality assurance and defect reduction, ensuring that products meet high standards.
- Impact: Reduces costs associated with rework, scrap, and warranty claims, and increases customer satisfaction and loyalty.
Faster Time-to-Market:
- How: Efficient processes and rapid prototyping accelerate product development and production timelines.
- Impact: Enables quicker response to market demands, capturing sales opportunities and improving competitive positioning.
Optimized Inventory Levels:
- How: Lean’s Just-In-Time (JIT) production minimizes excess inventory and associated holding costs.
- Impact: Frees up capital, reduces storage costs, and lowers the risk of inventory obsolescence, improving cash flow.
Enhanced Cash Flow:
- How: Reduced inventory levels, lower production costs, and faster receivables turnaround improve liquidity.
- Impact: Strengthens the organization’s ability to invest in growth opportunities and manage financial obligations effectively.
Higher Asset Utilization:
- How: Lean optimizes the use of equipment and facilities, reducing idle time and maximizing asset productivity.
- Impact: Enhances return on assets (ROA) and contributes to better overall financial performance.
Employee Productivity and Morale:
- How: Engaged and empowered employees are more productive and contribute to continuous improvement efforts.
- Impact: Leads to higher efficiency, lower turnover costs, and a more stable workforce, supporting sustained financial performance.
Financial Metrics to Assess Lean Impact:
Overall Equipment Effectiveness (OEE):
- Description: Measures the efficiency and effectiveness of equipment by combining availability, performance, and quality.
- Relevance: Higher OEE indicates better utilization of machinery, reducing costs and increasing production capacity.
Cost of Goods Sold (COGS):
- Description: Represents the direct costs attributable to the production of goods sold by a company.
- Relevance: Lean initiatives that reduce waste and improve efficiency lower COGS, enhancing gross profit margins.
Inventory Turnover Ratio:
- Description: Indicates how often inventory is sold and replaced over a period.
- Relevance: Higher turnover rates suggest efficient inventory management, aligning with Lean’s JIT principles and improving cash flow.
Return on Assets (ROA):
- Description: Measures the profitability relative to total assets.
- Relevance: Improved asset utilization through Lean practices increases ROA, reflecting better financial performance.
Net Profit Margin:
- Description: Shows the percentage of revenue that remains as profit after all expenses are deducted.
- Relevance: Lean’s cost reduction and efficiency improvements enhance net profit margins, contributing to overall profitability.
Production Lead Time:
- Description: The total time taken from the start of production to the delivery of the finished product.
- Relevance: Shorter lead times indicate more efficient processes, enabling quicker response to market demands and improving customer satisfaction.
Defect Rate:
- Description: The percentage of products that do not meet quality standards.
- Relevance: Lower defect rates reduce costs associated with rework and scrap, and improve customer satisfaction, positively impacting financial performance.
Labor Productivity:
- Description: Measures the output produced per labor hour.
- Relevance: Increased productivity through Lean initiatives leads to higher output with the same or fewer labor resources, reducing labor costs per unit.
Cash Conversion Cycle (CCC):
- Description: The time it takes for a company to convert its investments in inventory and other resources into cash flows from sales.
- Relevance: Lean’s efficient inventory and production management can shorten the CCC, enhancing liquidity and financial flexibility.
Return on Investment (ROI):
- Description: Measures the profitability of investments made in Lean initiatives.
- Relevance: Positive ROI indicates that Lean projects are generating financial benefits that exceed their costs, validating the investment in Lean practices.
Employee Turnover Rate:
- Description: The rate at which employees leave the organization.
- Relevance: Lower turnover rates due to higher job satisfaction and engagement from Lean practices reduce recruitment and training costs, positively impacting financial performance.
Energy Consumption:
- Description: The amount of energy used in the manufacturing process.
- Relevance: Lean initiatives that optimize processes and reduce waste can lead to lower energy consumption, reducing utility costs and enhancing sustainability.
Case Example: A textile manufacturer implemented Lean Manufacturing by introducing 5S, Kanban, and Kaizen practices. They achieved a 25% reduction in COGS through waste elimination, a 30% increase in OEE by improving equipment reliability, and a 20% increase in inventory turnover. These improvements led to a 15% increase in net profit margin and enhanced cash flow, demonstrating the positive financial impact of Lean adoption.
Conclusion: Lean Manufacturing profoundly influences the financial performance of manufacturing organizations by driving cost reductions, enhancing productivity, improving quality, and optimizing inventory and asset utilization. By leveraging financial metrics such as OEE, COGS, inventory turnover, ROA, net profit margin, and others, manufacturers can effectively assess the impact of Lean initiatives. This comprehensive approach not only strengthens financial health but also ensures that Lean practices contribute to long-term operational excellence and competitive advantage.
Conclusion:
The above review questions and detailed answers provide a comprehensive exploration of Manufacturing Process Design and Optimization. Covering essential topics such as process design objectives, Lean Manufacturing integration, differences between design and optimization, simulation models, Design of Experiments (DOE), Computer-Aided Process Planning (CAPP), Six Sigma, IoT integration, Total Productive Maintenance (TPM), Lean in product design, and financial performance metrics, these questions facilitate a deep understanding of how to design and optimize manufacturing processes effectively. Engaging with these questions equips students and professionals with the knowledge to implement best practices, overcome challenges, and achieve sustained success in competitive manufacturing environments.