Human Factors and Ergonomics in Manufacturing
In the age of automation and advanced manufacturing systems, understanding human factors and ergonomics in manufacturing has never been more critical. This field focuses on optimizing the interaction between humans and machines to improve safety, productivity, and overall well-being in industrial settings. Rooted in the broader scope of Industrial and Manufacturing Technologies, ergonomic design and analysis enhance both workforce performance and technological efficiency.
Modern factories that embrace Smart Manufacturing and Industry 4.0 rely on data-driven insights to tailor machine interfaces and workflows to human capabilities. Coupled with Computer-Integrated Manufacturing (CIM) systems, these ergonomic enhancements reduce fatigue, errors, and accidents, making production processes more resilient and adaptive. The incorporation of Digital Twin Technology enables engineers to simulate human-machine interactions before implementation, identifying ergonomic risks and improving workplace design.
Ergonomics also plays a key role in Lean Manufacturing by streamlining operations through user-centered task design. As manufacturing shifts toward Additive Manufacturing (3D Printing) and Advanced Materials and Manufacturing Technologies, new ergonomic considerations emerge related to workstation layout, repetitive movement, and user interface design. A focus on Manufacturing Quality Control and Assurance is closely linked, as ergonomic failures can lead to inconsistencies and safety incidents.
Incorporating human factors principles into Industrial Automation and Robotics improves usability and collaboration between humans and robotic systems. Wearable technology, sensor feedback, and intuitive control systems bridge the gap between traditional labor and machine intelligence. The drive for Energy and Resource Efficiency in Manufacturing further underscores the need to reduce unnecessary physical strain and motion, minimizing both worker fatigue and wasted effort.
At the systems level, ergonomic thinking influences strategic decisions in Supply Chain Management and Sustainable Manufacturing. From packaging ergonomics to transport logistics, human-centered design supports efficient movement of goods while reducing injury risks. These considerations are aligned with the physical and organizational infrastructure developed in fields like Mechanical Engineering and its applications in Manufacturing and Production Engineering.
Ergonomics research draws upon multiple physical sciences. Concepts from Thermodynamics and Heat Transfer, Fluid Mechanics and Hydraulics, and Solid Mechanics support the design of thermal environments, tools, and posture-supporting devices. Innovations in Nanotechnology and Advanced Materials in Mech Eng are also contributing to ergonomic progress, offering lighter, more adaptive equipment and materials.
Whether applied in Automotive Engineering, Biomechanical Engineering, or Robotics and Automation in Mech Eng, the central aim remains the same: harmonizing the strengths of human operators with the capabilities of machines. Through effective Control Systems in Mech Engineering and thoughtful design using Mechanical Design and CAD, engineers can ensure that humans remain at the core of innovation and manufacturing excellence.
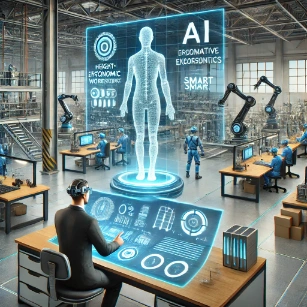
Table of Contents
Core Principles of Human Factors and Ergonomics
Worker-Centered Design
- Definition:
- Adapting tools, machines, and processes to fit human capabilities and limitations.
- Key Elements:
- Ensuring tasks match workers’ physical, cognitive, and sensory abilities.
- Designing systems to reduce error and enhance ease of use.
- Promoting inclusive design to accommodate diverse populations, including those with disabilities or varying levels of expertise.
- Incorporating feedback from users during iterative design phases to continuously refine usability.
- Implementing safety features that align with natural human reflexes and responses.
Task Analysis
- Definition:
- Breaking down tasks into their individual components to identify potential risks or inefficiencies.
- Applications:
- Evaluating physical demands, cognitive load, and environmental factors.
- Designing processes to streamline tasks and reduce complexity.
- Creating training programs tailored to task-specific skills and risk areas.
- Developing standard operating procedures that align with real-world practices.
- Incorporating time-motion studies to optimize workflow and reduce idle time.
Physical Ergonomics
- Definition:
- Focuses on the physical interaction between workers and their environment, including posture, force, and movement.
- Key Considerations:
- Designing tools and workstations to prevent repetitive strain injuries (RSIs).
- Adjusting workstation heights and seating to reduce awkward postures.
- Ensuring lighting, temperature, and noise levels are within comfort and safety thresholds.
- Providing adjustable equipment and personal protective gear for individual needs.
- Conducting ergonomic risk assessments regularly to prevent musculoskeletal disorders.
Cognitive Ergonomics
- Definition:
- Focuses on mental processes such as perception, memory, and decision-making in work environments.
- Key Considerations:
- Reducing cognitive overload by simplifying machine interfaces.
- Designing displays and controls for intuitive use.
- Incorporating error-tolerant design to prevent critical mistakes.
- Using color coding, icons, and auditory signals to reinforce information recognition.
- Aligning information flow with human attention spans and multitasking limitations.
Organizational Ergonomics
- Definition:
- Examines how organizational structures and workflows influence human performance and well-being.
- Key Considerations:
- Improving communication and collaboration between workers.
- Designing shift schedules to reduce fatigue.
- Developing job roles and responsibilities that prevent burnout and overwork.
- Implementing ergonomic policies within human resource practices and corporate culture.
- Encouraging employee participation in decision-making to improve morale and ownership.
For deeper insights into workplace ergonomics research and standards, resources such as the Human Factors and Ergonomics Society (HFES) provide valuable guidance and publications for professionals and organizations alike.
Key Areas of Application of Human Factors and Ergonomics in Manufacturing
Workstation Design
- Principles:
- Arrange tools and materials within easy reach to minimize unnecessary movements.
- Adjust workstation height to accommodate various worker sizes.
- Incorporate modular setups to allow personalization for specific tasks.
- Ensure line of sight for visual tasks to minimize neck strain and eye fatigue.
- Account for left- and right-handed users when arranging tools and interfaces.
- Techniques:
- Use ergonomic chairs and adjustable desks.
- Implement anti-fatigue mats for standing workstations.
- Provide footrests and adjustable lighting to support various working positions.
- Introduce sit-stand desks to allow posture variation during long shifts.
- Benefits:
- Reduces musculoskeletal disorders (MSDs).
- Enhances comfort and efficiency.
- Promotes job satisfaction and reduces absenteeism due to physical discomfort.
Tool and Equipment Design
- Principles:
- Design tools with handles that fit the human grip to reduce strain.
- Minimize tool vibrations and weight to prevent fatigue.
- Ensure intuitive tool interfaces that align with user expectations.
- Incorporate safety locks and guards into tool designs.
- Applications:
- Power tools with anti-vibration features.
- Equipment with adjustable controls for different users.
- Tools with color-coded indicators to signal operational status.
- Ergonomic grips on frequently used hand tools to reduce repetitive strain injuries.
Process and Workflow Optimization
- Principles:
- Eliminate unnecessary steps to reduce physical and mental fatigue.
- Use automation to handle repetitive or hazardous tasks.
- Apply Lean principles to remove inefficiencies and standardize procedures.
- Balance workloads across teams to minimize bottlenecks and overloads.
- Applications:
- Assembly lines with rotating tasks to prevent repetitive strain.
- Streamlined workflows to reduce worker movement.
- Workflow simulations using digital manufacturing models to test ergonomic improvements.
- Integration of real-time feedback systems to monitor workflow efficiency and worker strain.
Safety Systems
- Principles:
- Design systems that prioritize worker safety through hazard prevention and control.
- Incorporate fail-safes and intuitive emergency response mechanisms.
- Use predictive analytics to identify potential safety risks before they occur.
- Applications:
- Guardrails and safety interlocks on machinery.
- Warning systems for potential hazards.
- Wearable technology that monitors posture and alerts workers of unsafe positions.
- Vision-based safety systems that detect proximity breaches near dangerous machinery.
- Benefits:
- Reduces workplace accidents and injuries.
- Enhances compliance with occupational safety standards.
Training and Education
- Principles:
- Train workers to use equipment safely and efficiently.
- Educate managers on the importance of ergonomics in improving productivity.
- Utilize feedback loops to tailor training to actual user experiences.
- Foster a culture of continuous improvement in ergonomic practices.
- Applications:
- Simulation-based training for new machinery.
- Workshops on proper lifting techniques.
- Gamified safety modules to increase engagement and knowledge retention.
- Refresher courses for long-term employees on updated ergonomic standards.
Environmental Design
- Principles:
- Optimize lighting, temperature, and noise levels to support worker comfort and focus.
- Promote biophilic elements to enhance mental well-being and reduce stress.
- Ensure proper ventilation and air quality to prevent fatigue and headaches.
- Applications:
- Installing LED lighting to reduce glare and shadows.
- Using noise-canceling barriers in noisy manufacturing environments.
- Dynamic temperature zoning to cater to different physical workspaces.
- Use of natural daylight and green interior design elements to reduce eyestrain and enhance mood.
Tools and Technologies for Human Factors and Ergonomics in Manufacturing
Motion Capture Systems
- Role:
- Analyze worker movements to identify inefficiencies or potential injury risks.
- Track real-time biomechanical patterns to assess ergonomic posture compliance.
- Applications:
- Improving assembly line workflows by identifying awkward or repetitive movements.
- Designing tools and equipment layouts that reduce stress on joints and muscles.
- Supporting rehabilitation strategies for injured workers by visualizing movement deviations.
- Benchmarking best practices across different production environments using motion pattern databases.
Digital Human Modeling (DHM)
- Role:
- Simulate human interactions with systems and environments to optimize ergonomic design.
- Visualize anthropometric diversity and posture variability across tasks.
- Applications:
- Testing workstation designs for ergonomics before implementation.
- Analyzing the impact of repetitive motions on worker health and long-term fatigue.
- Creating virtual prototypes for inclusive design, accommodating various worker body types.
- Conducting ergonomic assessments for global manufacturing sites using shared DHM models.
Wearable Technology
- Role:
- Monitor physical activity, posture, and fatigue in real time to prevent injuries.
- Track vital signs to detect early signs of exhaustion or stress in workers.
- Applications:
- Wearable sensors tracking improper lifting techniques in warehouses and production areas.
- Smart clothing monitoring worker fatigue and stress levels to support scheduling decisions.
- Real-time feedback devices alerting workers when their posture deviates from ergonomic guidelines.
- Data-driven dashboards enabling supervisors to identify high-risk zones and plan interventions.
Exoskeletons
- Role:
- Provide physical support to workers performing heavy or repetitive tasks to reduce musculoskeletal strain.
- Distribute mechanical load away from vulnerable muscle groups.
- Applications:
- Reducing strain during lifting and carrying tasks in logistics and construction environments.
- Assisting in precision tasks that require extended holding positions, such as welding or assembly.
- Supporting rehabilitation for workers returning from injury by limiting load-bearing on affected areas.
- Boosting worker stamina and reducing injury-related absenteeism across shift cycles.
Augmented Reality (AR)
- Role:
- Enhance worker training and assist in complex tasks with visual guidance overlays.
- Improve cognitive ergonomics by reducing memory burden and instruction recall errors.
- Applications:
- AR overlays providing step-by-step instructions for machine maintenance and troubleshooting.
- Training workers on new assembly techniques without halting production lines.
- Real-time error prevention through AR prompts that highlight incorrect procedures.
- Remote collaboration for expert ergonomists to guide on-site improvements via AR interfaces.
- Emerging solutions like PTC Vuforia are accelerating AR’s role in industrial ergonomics.
IoT and Smart Sensors
- Role:
- Collect data on environmental conditions and worker interactions to support proactive ergonomic improvements.
- Enable predictive alerts based on historical strain or motion patterns.
- Applications:
- Monitoring noise levels to ensure compliance with safety standards and reduce auditory fatigue.
- Tracking machine vibrations to identify ergonomic risks associated with prolonged exposure.
- Gathering environmental metrics like temperature, lighting, and humidity to improve overall comfort.
- Interlinking ergonomic data with production KPIs to correlate performance with well-being indicators.
Benefits of Human Factors and Ergonomics in Manufacturing
- Enhanced Worker Safety:
- Reduces injuries caused by repetitive motions, awkward postures, or hazardous environments through better workstation layouts and task designs.
- Minimizes exposure to physical and environmental risks by integrating ergonomic principles in machine interface and workflow planning.
- Incorporates proactive monitoring tools to detect early signs of strain and correct poor posture before injuries occur.
- Increased Productivity:
- Optimized workflows and ergonomic designs minimize fatigue and maximize efficiency by reducing unnecessary movement and simplifying task sequences.
- Improved physical comfort leads to sustained energy and focus, boosting overall task output per hour.
- Enhanced cognitive ergonomics support better decision-making and reduce time lost due to interface confusion or errors.
- Improved Job Satisfaction:
- Comfortable work environments and user-friendly tools increase employee morale, leading to higher engagement and motivation.
- Empowered workers feel more in control and experience reduced stress, especially when they can customize their workspace to suit individual needs.
- Organizations that prioritize ergonomics are viewed as caring employers, contributing to a positive corporate culture.
- Lower Absenteeism:
- Reduces workplace injuries and related absences by eliminating common causes such as poor lifting techniques, repetitive stress, and poor workstation design.
- Healthier work conditions contribute to improved mental and physical well-being, keeping employees consistently present and engaged.
- Real-time ergonomic monitoring allows for timely interventions before fatigue or discomfort escalates into long-term health issues.
- Cost Savings:
- Minimizes costs associated with injuries, downtime, and turnover by reducing medical expenses, compensation claims, and retraining efforts.
- Improved efficiency means less overtime and fewer production delays, leading to financial benefits across departments.
- Investments in ergonomics often yield substantial ROI over time, as shown by many case studies including those featured by the National Institute for Occupational Safety and Health.
- Compliance with Regulations:
- Meets occupational safety and health standards, such as OSHA and ISO guidelines, thereby reducing legal risks and penalties.
- Facilitates easier audits and reporting by embedding ergonomics into operational documentation and safety protocols.
- Proactive compliance also enhances the organization’s reputation with regulators and clients alike.
Challenges in Implementing Human Factors and Ergonomics in Manufacturing
- High Initial Costs:
- Investment in ergonomic equipment, tools, and training can be substantial, especially for large-scale operations or companies transitioning from outdated systems.
- Budget constraints often lead to prioritization of immediate production needs over long-term ergonomic benefits.
- Smaller enterprises may struggle to justify capital expenditure without clear short-term ROI, making implementation less feasible.
- Resistance to Change:
- Workers and management may be reluctant to adopt new processes or tools due to unfamiliarity or perceived complexity.
- Behavioral inertia and skepticism toward new technologies can impede acceptance, especially when current systems appear to function adequately.
- To address this, successful implementation often depends on robust change management strategies and inclusive communication practices.
- Complexity of Implementation:
- Integrating ergonomics into existing workflows and systems can be challenging due to mismatched standards, legacy infrastructure, and diverse task requirements.
- Interdisciplinary coordination among designers, engineers, health professionals, and line managers is often required but difficult to synchronize.
- Even minor ergonomic changes may necessitate significant re-engineering of tools, layouts, or operational procedures.
- Data Collection and Analysis:
- Gathering and interpreting data to identify ergonomic risks requires expertise in biomechanics, physiology, and analytics.
- Accurate assessments depend on high-quality input from motion tracking, user feedback, and environmental sensors.
- Without proper training, collected data may be misinterpreted, leading to ineffective or even counterproductive interventions. According to Ergonomenon, successful data-driven ergonomics programs hinge on specialist oversight.
- Customization:
- Tailoring ergonomic solutions to individual workers or tasks can be resource-intensive in terms of time, technology, and training.
- Mass production environments often struggle to accommodate individual needs without compromising efficiency or standardization.
- Balancing personalization with organizational constraints requires adaptive design strategies and ongoing adjustments.
Emerging Trends in Human Factors and Ergonomics for Manufacturing
- AI and Machine Learning:
- Using AI to analyze worker behavior and recommend ergonomic improvements based on real-time motion and productivity data.
- Machine learning models can identify patterns of fatigue or strain and suggest workflow modifications to mitigate injury risk.
- Advanced algorithms may even predict future ergonomic issues before they arise, enabling proactive interventions and cost savings.
- Personalized Ergonomics:
- Wearable devices providing customized feedback on posture and movements by continuously monitoring biomechanical stress levels.
- These technologies allow dynamic adaptation of tools and workstations to each worker’s unique physiology and workload.
- Such individualized data improves both safety and performance, making ergonomics more inclusive and effective across a diverse workforce.
- Virtual Reality (VR):
- VR simulations for training workers on ergonomic practices and safety protocols in highly immersive, low-risk environments.
- This approach enhances retention of ergonomic knowledge while allowing experimentation with new workstation designs or tool configurations.
- It is particularly valuable for onboarding new hires or re-skilling employees for complex or hazardous roles. For example, NIST research highlights VR’s growing role in enhancing ergonomic training outcomes.
- Sustainable Ergonomics:
- Designing tools and workstations using eco-friendly materials and sustainable manufacturing practices that align with corporate ESG goals.
- This includes incorporating recycled or biodegradable components, minimizing material waste, and designing for disassembly or reusability.
- These efforts promote environmental stewardship while supporting employee well-being through healthier, more adaptable workspaces.
- Collaborative Robots (Cobots):
- Robots working alongside humans to reduce physical strain and enhance task precision, especially in repetitive or high-risk operations.
- Unlike traditional industrial robots, cobots are equipped with safety sensors and intuitive controls, making them ideal ergonomic partners.
- They can handle tasks like heavy lifting or precision placement while enabling humans to focus on cognitively demanding or supervisory roles.
Future Directions in Human Factors and Ergonomics
- Integration with Industry 4.0:
- Smart factories leveraging IoT and automation to optimize human-machine interactions, enhancing safety, efficiency, and adaptability in dynamic environments.
- Future ergonomic systems will include real-time feedback loops between workers, machines, and digital twins to continuously refine task allocation and work conditions.
- This deep integration will create seamless collaboration between humans and intelligent systems, reshaping job roles to emphasize oversight, creativity, and adaptive problem-solving.
- Ergonomics for Aging Workforces:
- Designing solutions tailored to older workers, addressing physical limitations, slower reflexes, and potential chronic conditions without compromising productivity or dignity.
- These include adjustable workstations, voice-controlled systems, and ergonomically designed tools that reduce physical strain and accommodate limited mobility or vision changes.
- As global demographics shift, incorporating universal design principles will become essential for inclusive and sustainable workforce planning.
- Global Ergonomic Standards:
- Harmonizing ergonomic practices across multinational manufacturing operations to ensure consistency, safety, and compliance across diverse legal and cultural landscapes.
- Organizations will increasingly adopt standardized frameworks like ISO 6385 to unify ergonomic principles, training, and measurement methodologies worldwide.
- Such global alignment facilitates knowledge transfer, reduces injury risks, and supports ethical labor practices throughout international supply chains. See the ISO 6385 standard for more information.
- Health Monitoring Systems:
- Advanced sensors tracking long-term impacts of repetitive tasks on worker health, enabling preventive measures against musculoskeletal disorders and mental fatigue.
- Wearables and embedded systems will offer continuous assessments of posture, exertion, heart rate variability, and stress levels, integrated with personalized feedback loops.
- Longitudinal data from these systems will empower data-driven adjustments in work design and wellness interventions.
- AI-Driven Workplace Design:
- Automated systems suggesting ergonomic improvements based on real-time and historical data, reducing reliance on manual assessments.
- AI can simulate various task scenarios, forecast ergonomic risks, and recommend adaptive equipment or layout adjustments tailored to specific roles or individuals.
- Eventually, workplaces will become self-optimizing environments capable of anticipating and responding to workers’ needs dynamically.
Why Study Human Factors and Ergonomics in Manufacturing
Designing Workplaces That Fit People
Human factors and ergonomics focus on adapting work environments to human needs. Students learn how to design tools, workstations, and tasks that reduce strain and injury. This supports safety, comfort, and productivity.
Understanding Human Capabilities and Limitations
Students study anatomy, biomechanics, and cognitive psychology. They learn how people perceive, think, and move in industrial settings. This knowledge informs better equipment design and workflow organization.
Applications in Manufacturing and Automation
Ergonomics is essential in manual assembly, machine operation, and interface design. Students learn to assess risks and recommend improvements. This contributes to quality, efficiency, and worker satisfaction.
Data Collection and Usability Testing
Students gain skills in task analysis, observational studies, and usability testing. They learn to evaluate human performance and system interaction. These methods support evidence-based design decisions.
Enhancing Workplace Safety and Organizational Outcomes
Ergonomic design reduces injuries, boosts morale, and lowers healthcare costs. Students understand how human-centered design benefits both workers and companies. This creates healthier, more sustainable manufacturing environments.
Human Factors and Ergonomics: Conclusion
Human Factors and Ergonomics (HFE) is an essential aspect of modern manufacturing, ensuring the safety, well-being, and productivity of workers. It goes beyond simple adjustments to tools or environments—it encompasses a systemic approach to designing tasks, technologies, and organizational structures that align with human strengths and limitations. By optimizing the interaction between humans and machines, HFE reduces injuries, enhances operational efficiency, and supports long-term organizational success.
As manufacturing continues to embrace digitization and automation, the role of HFE will expand to address the cognitive and emotional dimensions of work in high-tech environments. Future developments will likely integrate real-time feedback systems, AI-powered ergonomic analysis, and immersive simulation tools to model worker-machine interactions under various conditions. These advancements will empower proactive interventions before discomfort, fatigue, or injury occur, transforming reactive ergonomics into predictive safety systems.
Furthermore, the growing emphasis on diversity, equity, and inclusion will encourage ergonomic designs that accommodate varied body types, ages, and abilities, ensuring that all employees can contribute effectively and comfortably. Platforms like the Human Factors and Ergonomics Society (HFES) are leading efforts to align research, standards, and industry practices.
Ultimately, the evolution of HFE will play a pivotal role in humanizing the future of manufacturing—where technology and people not only coexist but thrive together in environments designed for mutual growth and resilience.
Human Factors and Ergonomics: Review Questions with Detailed Answers:
1. What are human factors and ergonomics, and why are they important in the manufacturing industry?
Answer:
Human factors and ergonomics (HF&E) involve designing workplaces, products, and systems that fit the users’ needs, capabilities, and limitations to enhance performance, safety, and comfort. In manufacturing, HF&E is crucial because it directly impacts worker productivity, safety, and overall operational efficiency.
Concepts:
- Human Factors: The study of how humans interact with elements of a system, focusing on improving performance and reducing errors.
- Ergonomics: The practice of designing workspaces and tools to fit the user’s physical and cognitive abilities, minimizing strain and injury.
Importance in Manufacturing:
Enhanced Safety:
- How: By designing workstations and tools that reduce the risk of accidents and injuries.
- Impact: Lowers workplace injury rates, reduces downtime, and minimizes costs associated with worker compensation and lost productivity.
Increased Productivity:
- How: Optimizing workflow and equipment layout to match worker capabilities.
- Impact: Streamlines operations, reduces fatigue, and enhances overall efficiency, leading to higher production rates.
Improved Worker Well-being:
- How: Creating comfortable and supportive work environments that reduce physical and mental strain.
- Impact: Increases job satisfaction, reduces absenteeism, and fosters a more motivated and engaged workforce.
Reduced Error Rates:
- How: Designing intuitive interfaces and processes that align with human cognitive abilities.
- Impact: Decreases the likelihood of mistakes, ensuring higher quality products and fewer defects.
Cost Savings:
- How: Minimizing injuries and errors reduces costs related to healthcare, rework, and waste.
- Impact: Enhances the financial health of the manufacturing operation by lowering operational expenses.
Conclusion: Human factors and ergonomics are integral to the manufacturing industry as they enhance safety, productivity, worker well-being, and overall operational efficiency. By prioritizing HF&E, manufacturers can create more effective, sustainable, and profitable workplaces.
2. How can ergonomic workplace design reduce the risk of musculoskeletal disorders (MSDs) in manufacturing workers?
Answer:
Ergonomic workplace design focuses on arranging workstations, tools, and tasks to fit the physical capabilities and limitations of workers, thereby reducing the risk of musculoskeletal disorders (MSDs). MSDs, such as carpal tunnel syndrome, tendonitis, and lower back pain, are common in manufacturing due to repetitive motions, awkward postures, and heavy lifting.
Concepts:
- Musculoskeletal Disorders (MSDs): Injuries or disorders affecting the muscles, nerves, tendons, ligaments, joints, cartilage, or spinal discs.
- Ergonomic Design Principles: Strategies aimed at optimizing the interaction between workers and their work environment to prevent strain and injury.
Strategies to Reduce MSDs:
Adjustable Workstations:
- How: Implement height-adjustable tables and chairs to accommodate different worker sizes and preferences.
- Impact: Promotes neutral body postures, reducing strain on the back, neck, and shoulders.
Proper Tool Design:
- How: Use tools that fit the hand comfortably and require minimal force to operate.
- Impact: Decreases the risk of repetitive strain injuries and enhances precision in tasks.
Task Rotation:
- How: Rotate workers between different tasks to prevent prolonged repetitive motions.
- Impact: Reduces muscle fatigue and minimizes the likelihood of MSDs by varying the physical demands on the body.
Mechanical Assistance:
- How: Utilize lifting aids, conveyors, and other mechanical systems to handle heavy or awkward loads.
- Impact: Lessens the physical effort required, preventing overexertion and associated injuries.
Optimized Workflow Layout:
- How: Arrange equipment and materials within easy reach to minimize excessive reaching, bending, or twisting.
- Impact: Promotes efficient movement patterns, reducing the risk of awkward postures and overextension.
Ergonomic Training:
- How: Educate workers on proper body mechanics, posture, and safe lifting techniques.
- Impact: Empowers employees to maintain healthy practices, preventing the onset of MSDs.
Adequate Rest Breaks:
- How: Schedule regular breaks to allow muscles to recover and reduce fatigue.
- Impact: Prevents prolonged strain on specific muscle groups, lowering the risk of MSDs.
Benefits of Ergonomic Workplace Design:
- Reduced Injury Rates: Lower incidence of MSDs among workers.
- Increased Productivity: Healthier workers are more productive and have fewer sick days.
- Enhanced Worker Satisfaction: Comfortable work environments lead to higher job satisfaction and morale.
- Cost Savings: Reduced medical expenses and workers’ compensation claims.
Conclusion: Ergonomic workplace design is essential in minimizing the risk of musculoskeletal disorders in manufacturing workers. By implementing ergonomic principles, manufacturers can create safer, more comfortable, and more efficient work environments that benefit both employees and the organization.
3. What are the key components of a successful ergonomics program in a manufacturing setting?
Answer:
A successful ergonomics program in a manufacturing setting involves a systematic approach to identifying, evaluating, and mitigating ergonomic risks to improve worker health, safety, and productivity. Key components of such a program include management commitment, employee involvement, hazard identification, ergonomic assessments, training, intervention implementation, and continuous evaluation.
Concepts:
- Ergonomics Program: A structured plan that incorporates policies, procedures, and practices to optimize the interaction between workers and their work environment.
- Total Worker Health: An approach that integrates occupational safety and health protection with health promotion to prevent worker injury and illness and to advance health and well-being.
Key Components:
Management Commitment:
- How: Ensure that organizational leaders prioritize ergonomics by providing necessary resources and support.
- Impact: Demonstrates the organization’s dedication to worker health and encourages participation at all levels.
Employee Involvement:
- How: Engage workers in identifying ergonomic issues and developing solutions.
- Impact: Promotes ownership, ensures practical and effective interventions, and enhances program acceptance.
Ergonomic Hazard Identification:
- How: Conduct regular inspections and surveys to identify potential ergonomic risks, such as repetitive motions, awkward postures, and excessive force.
- Impact: Facilitates early detection of issues, preventing the development of MSDs and other injuries.
Ergonomic Assessments:
- How: Perform detailed evaluations of workstations, tools, and processes to assess ergonomic risks using standardized assessment tools like REBA (Rapid Entire Body Assessment) or RULA (Rapid Upper Limb Assessment).
- Impact: Provides objective data to inform targeted ergonomic interventions.
Training and Education:
- How: Educate employees and supervisors on ergonomic principles, safe work practices, and the proper use of ergonomic equipment.
- Impact: Empowers workers with the knowledge to maintain good ergonomics and prevent injuries.
Intervention Implementation:
- How: Develop and implement solutions to address identified ergonomic risks, such as redesigning workstations, providing ergonomic tools, and modifying work processes.
- Impact: Reduces ergonomic hazards, enhances worker comfort, and improves operational efficiency.
Continuous Monitoring and Evaluation:
- How: Regularly review and assess the effectiveness of ergonomic interventions and the overall program through feedback, injury tracking, and performance metrics.
- Impact: Ensures the program remains effective, adapts to changing conditions, and continuously improves worker health and productivity.
Documentation and Record-Keeping:
- How: Maintain detailed records of ergonomic assessments, interventions, training sessions, and incident reports.
- Impact: Provides evidence of compliance, facilitates program evaluation, and supports continuous improvement efforts.
Integration with Other Safety Programs:
- How: Coordinate ergonomics efforts with broader occupational health and safety initiatives.
- Impact: Creates a cohesive approach to worker well-being, enhancing overall safety culture.
Feedback Mechanisms:
- How: Establish channels for employees to report ergonomic concerns and suggest improvements.
- Impact: Encourages proactive identification of issues and fosters a collaborative environment for problem-solving.
Benefits of a Successful Ergonomics Program:
- Reduced Injury Rates: Lower incidence of MSDs and other ergonomics-related injuries.
- Increased Productivity: More comfortable workers are more efficient and have higher morale.
- Enhanced Worker Satisfaction: Improved workplace conditions lead to greater job satisfaction and retention.
- Cost Savings: Decreased medical and compensation costs associated with workplace injuries.
- Compliance: Meets regulatory requirements and avoids potential fines or legal issues.
Conclusion: A comprehensive ergonomics program in manufacturing settings is essential for promoting worker health, safety, and productivity. By incorporating key components such as management commitment, employee involvement, hazard identification, ergonomic assessments, training, interventions, and continuous evaluation, organizations can create a sustainable and effective ergonomics program that benefits both employees and the business.
4. How can ergonomic assessments be conducted in a manufacturing environment, and what tools are commonly used?
Answer:
Ergonomic assessments in a manufacturing environment involve systematically evaluating workstations, tasks, and workflows to identify ergonomic risks and implement solutions that enhance worker comfort, safety, and efficiency. Conducting these assessments requires a structured approach and the use of standardized tools to ensure comprehensive and objective evaluations.
Concepts:
- Ergonomic Assessment: A process of evaluating work conditions to identify and mitigate ergonomic risks.
- Standardized Assessment Tools: Instruments designed to provide objective measurements of ergonomic factors.
Steps to Conduct Ergonomic Assessments:
Preparation and Planning:
- How: Define the scope of the assessment, identify high-risk areas, and gather necessary resources.
- Impact: Ensures a focused and efficient assessment process, targeting areas with the highest potential for ergonomic improvement.
Data Collection:
- How: Observe and record work processes, interview workers, and collect data on task frequency, duration, and physical demands.
- Impact: Provides a comprehensive understanding of the work environment and identifies potential ergonomic hazards.
Using Standardized Assessment Tools:
- How: Apply specific tools to evaluate different aspects of ergonomics, such as posture, force, repetition, and workstation layout.
- Impact: Ensures objective and consistent measurements across different assessments.
Common Ergonomic Assessment Tools:
REBA (Rapid Entire Body Assessment):
- Purpose: Evaluates the risk of musculoskeletal disorders based on body posture, force, repetition, and coupling.
- How It Works: Observers score postures of different body parts and combine scores to determine overall risk levels.
- Impact: Identifies areas where ergonomic interventions are needed to reduce MSD risks.
RULA (Rapid Upper Limb Assessment):
- Purpose: Focuses on assessing the posture of the neck, trunk, and upper limbs.
- How It Works: Observers rate the severity of musculoskeletal risks based on the positions and movements of the upper body.
- Impact: Highlights specific upper body ergonomic issues that require attention.
NEBA (Niosh Ergonomics Body Assessment):
- Purpose: Measures physical exposures and ergonomic risk factors in the workplace.
- How It Works: Combines observational data with measurements of physical demands.
- Impact: Provides a detailed analysis of ergonomic stressors, facilitating targeted interventions.
OCRA (Occupational Repetitive Actions):
- Purpose: Assesses the risk of repetitive strain injuries based on task repetition, force, and duration.
- How It Works: Evaluators score tasks based on their repetitiveness, required force, and duration to determine injury risk.
- Impact: Identifies highly repetitive tasks that may require redesign or automation to prevent injuries.
Strain Index:
- Purpose: Evaluates the risk of developing distal upper limb disorders.
- How It Works: Assesses factors such as intensity of exertion, duration of exertion, efforts per minute, hand/wrist posture, speed of work, and duration of task.
- Impact: Helps in identifying high-risk tasks that need ergonomic improvements to protect the upper limbs.
Visual Inspection Checklists:
- Purpose: Provide a structured approach to identifying ergonomic hazards through visual observation.
- How It Works: Inspectors use checklists to evaluate various ergonomic factors such as workstation height, lighting, and tool design.
- Impact: Ensures that all relevant ergonomic aspects are reviewed systematically during the assessment.
Implementing Ergonomic Assessments:
Training Assessors:
- How: Ensure that individuals conducting assessments are trained in using ergonomic tools and understanding ergonomic principles.
- Impact: Enhances the accuracy and reliability of the assessments.
Involving Employees:
- How: Engage workers in the assessment process by gathering their input and observations.
- Impact: Provides valuable insights and fosters collaboration in identifying and addressing ergonomic issues.
Analyzing Data:
- How: Compile and analyze the collected data to identify trends and high-risk areas.
- Impact: Facilitates informed decision-making for implementing effective ergonomic interventions.
Implementing Solutions:
- How: Develop and execute ergonomic improvements based on assessment findings, such as redesigning workstations, providing ergonomic tools, or modifying work processes.
- Impact: Reduces ergonomic risks, enhances worker comfort, and improves overall productivity.
Monitoring and Follow-Up:
- How: Continuously monitor the effectiveness of implemented solutions and conduct periodic reassessments.
- Impact: Ensures sustained ergonomic improvements and adapts to any changes in the work environment.
Conclusion: Conducting ergonomic assessments in manufacturing involves a systematic approach using standardized tools like REBA, RULA, NEBA, OCRA, and the Strain Index to identify and mitigate ergonomic risks. By following structured steps and utilizing appropriate assessment instruments, manufacturers can create safer, more comfortable, and more efficient work environments that enhance worker well-being and operational performance.
5. What are the common ergonomic hazards in manufacturing, and how can they be mitigated?
Answer:
Common ergonomic hazards in manufacturing include repetitive motions, awkward postures, excessive force, vibration, and improper workstation design. These hazards can lead to musculoskeletal disorders (MSDs), reduced productivity, and increased absenteeism. Mitigating these hazards involves implementing a combination of ergonomic principles, workplace redesign, employee training, and the use of appropriate tools and equipment.
Concepts:
- Ergonomic Hazards: Workplace conditions that can cause musculoskeletal injuries or discomfort.
- Musculoskeletal Disorders (MSDs): Injuries affecting muscles, nerves, tendons, joints, cartilage, or spinal discs, often resulting from repetitive strain or poor posture.
Common Ergonomic Hazards and Mitigation Strategies:
Repetitive Motions:
- Hazard: Performing the same motion repeatedly, leading to strain on muscles and joints.
- Mitigation:
- Task Rotation: Rotate workers between different tasks to vary muscle use and reduce repetitive strain.
- Automation: Use machines or robotic systems to handle repetitive tasks, minimizing human repetition.
- Breaks and Rest Periods: Schedule regular breaks to allow muscles to recover.
Awkward Postures:
- Hazard: Maintaining positions that cause excessive bending, twisting, reaching, or lifting.
- Mitigation:
- Workstation Design: Adjust workstation height and layout to promote neutral body postures.
- Ergonomic Tools: Provide tools with adjustable heights and ergonomic grips to reduce the need for awkward positioning.
- Training: Educate workers on proper posture and body mechanics to minimize strain.
Excessive Force:
- Hazard: Applying more force than necessary to perform tasks, leading to muscle fatigue and injury.
- Mitigation:
- Mechanical Aids: Implement lifting equipment, conveyors, and assistive devices to reduce the need for manual force.
- Tool Design: Use tools that require less force and are easier to handle.
- Process Optimization: Streamline tasks to require minimal force input.
Vibration:
- Hazard: Exposure to continuous or intermittent vibrations from machinery and tools, causing hand-arm vibration syndrome (HAVS) and other issues.
- Mitigation:
- Vibration Dampeners: Install vibration-absorbing materials or dampeners on equipment.
- Tool Maintenance: Regularly maintain tools and machinery to reduce vibration levels.
- Personal Protective Equipment (PPE): Provide anti-vibration gloves and other protective gear to workers.
Improper Workstation Design:
- Hazard: Workstations that do not accommodate the physical needs of workers, leading to discomfort and injury.
- Mitigation:
- Adjustability: Design adjustable workstations that can be tailored to individual worker sizes and preferences.
- Layout Optimization: Arrange equipment and materials within easy reach to minimize unnecessary movements.
- Ergonomic Assessments: Regularly evaluate and redesign workstations based on ergonomic assessments and worker feedback.
Prolonged Standing or Sitting:
- Hazard: Extended periods of standing or sitting can cause fatigue, circulation issues, and musculoskeletal strain.
- Mitigation:
- Anti-Fatigue Mats: Provide mats for standing workers to reduce discomfort and strain.
- Sit-Stand Workstations: Implement adjustable workstations that allow workers to alternate between sitting and standing.
- Movement Breaks: Encourage regular movement and posture changes to alleviate prolonged static positions.
Poor Lighting:
- Hazard: Inadequate or excessive lighting can cause eye strain, headaches, and poor posture.
- Mitigation:
- Proper Lighting Design: Ensure adequate lighting levels that reduce glare and shadows, enhancing visibility and reducing eye strain.
- Task Lighting: Provide focused lighting for specific tasks to improve visibility and reduce the need for awkward postures.
- Natural Light Utilization: Maximize the use of natural light where possible to create a comfortable and well-lit work environment.
Manual Handling of Heavy Loads:
- Hazard: Lifting, carrying, and moving heavy objects can lead to back injuries and other musculoskeletal issues.
- Mitigation:
- Mechanical Lifting Aids: Use forklifts, hoists, and conveyors to handle heavy loads, minimizing manual lifting.
- Ergonomic Training: Train workers in proper lifting techniques to reduce the risk of injury.
- Workload Management: Distribute heavy tasks among multiple workers to prevent overexertion.
Cluttered Work Areas:
- Hazard: Disorganized and cluttered workspaces can lead to tripping hazards and inefficient movements.
- Mitigation:
- 5S Methodology: Implement the 5S principles (Sort, Set in order, Shine, Standardize, Sustain) to maintain organized and clean work areas.
- Storage Solutions: Provide adequate storage options to keep tools and materials neatly arranged and easily accessible.
- Regular Housekeeping: Conduct routine cleaning and organization to prevent clutter buildup.
Inadequate Training and Awareness:
- Hazard: Lack of knowledge about ergonomic principles and safe work practices can increase the risk of injury.
- Mitigation:
- Comprehensive Training Programs: Provide ongoing training on ergonomics, proper tool use, and safe work practices.
- Awareness Campaigns: Promote ergonomic awareness through posters, reminders, and regular communications.
- Employee Involvement: Encourage workers to participate in identifying ergonomic issues and suggesting improvements.
Conclusion: Common ergonomic hazards in manufacturing, such as repetitive motions, awkward postures, excessive force, vibration, and improper workstation design, can significantly impact worker health and productivity. By implementing targeted mitigation strategies, including ergonomic workplace design, the use of mechanical aids, employee training, and regular assessments, manufacturers can create safer, more efficient, and more comfortable work environments that enhance overall operational performance and worker well-being.
6. How can the implementation of ergonomic tools and equipment improve productivity and reduce errors in manufacturing processes?
Answer:
The implementation of ergonomic tools and equipment in manufacturing processes can significantly enhance productivity and reduce errors by aligning work conditions with human capabilities and limitations. Ergonomic tools are designed to minimize physical strain, enhance precision, and streamline workflows, leading to more efficient and accurate production.
Concepts:
- Ergonomic Tools: Equipment and devices designed to fit the user’s needs, reducing strain and improving efficiency.
- Productivity: The rate at which goods are produced by workers, machines, and processes.
- Error Reduction: Minimizing mistakes in production to ensure higher quality and fewer defects.
Benefits of Ergonomic Tools and Equipment:
Reduced Physical Strain:
- How: Ergonomic tools are designed to fit the natural movements and postures of workers, reducing muscle fatigue and strain.
- Impact: Enables workers to perform tasks more comfortably and for longer periods without fatigue, maintaining consistent productivity levels.
Enhanced Precision and Control:
- How: Ergonomic tools often feature better grips, adjustable settings, and intuitive designs that improve control and accuracy.
- Impact: Reduces the likelihood of errors and defects by allowing workers to perform tasks with greater precision.
Improved Workflow Efficiency:
- How: Ergonomic equipment is often designed to streamline processes, such as adjustable workstations that can be tailored to individual tasks.
- Impact: Minimizes unnecessary movements and adjustments, speeding up production cycles and increasing overall efficiency.
Decreased Downtime:
- How: Ergonomic tools and equipment are typically more reliable and easier to use, reducing the need for frequent maintenance and adjustments.
- Impact: Lowers the incidence of equipment-related interruptions, ensuring a smoother and more continuous production flow.
Lower Injury Rates:
- How: By reducing physical strain and improving task design, ergonomic tools decrease the risk of musculoskeletal injuries.
- Impact: Minimizes absenteeism and medical costs associated with workplace injuries, maintaining a healthy and productive workforce.
Increased Worker Satisfaction and Morale:
- How: Providing ergonomic tools demonstrates a commitment to worker well-being, enhancing job satisfaction.
- Impact: Boosts morale and motivation, leading to higher engagement and productivity levels.
Enhanced Training and Onboarding:
- How: Ergonomic tools are often more intuitive and easier to learn, simplifying the training process for new employees.
- Impact: Reduces the time and resources required for training, allowing new workers to become productive more quickly.
Flexibility and Adaptability:
- How: Adjustable ergonomic equipment can be customized to suit different tasks and worker preferences.
- Impact: Increases the adaptability of manufacturing processes, allowing for smoother transitions between different products or production runs.
Higher Quality Output:
- How: Improved precision and reduced errors lead to higher quality products with fewer defects.
- Impact: Enhances customer satisfaction, reduces rework costs, and strengthens the company’s reputation for quality.
Sustainability and Cost Savings:
- How: Efficient tools and processes reduce material waste and energy consumption.
- Impact: Lowers operational costs and supports sustainability initiatives, contributing to long-term business success.
Examples of Ergonomic Tools and Equipment:
- Adjustable Workstations: Allow workers to customize their workspace height and layout to suit their tasks.
- Ergonomic Hand Tools: Designed with comfortable grips and optimal weight distribution to reduce strain.
- Anti-Fatigue Mats: Provide cushioning for workers who stand for extended periods.
- Automated Assistive Devices: Such as lift assists and conveyor systems to handle heavy or repetitive tasks.
Conclusion: The implementation of ergonomic tools and equipment in manufacturing not only enhances worker comfort and safety but also drives significant improvements in productivity and error reduction. By aligning work environments and tools with human capabilities, manufacturers can achieve higher efficiency, better quality, and a more engaged workforce, ultimately leading to sustained operational success and competitive advantage.
7. What role does employee training play in the effective implementation of ergonomics in manufacturing, and what key topics should be covered?
Answer:
Employee training is a critical component in the effective implementation of ergonomics in manufacturing. It ensures that workers understand ergonomic principles, recognize ergonomic hazards, and are equipped with the skills and knowledge to utilize ergonomic tools and practices effectively. Comprehensive training fosters a culture of safety and continuous improvement, leading to reduced injuries, increased productivity, and enhanced worker well-being.
Concepts:
- Employee Training: Educational programs designed to equip workers with the necessary knowledge and skills.
- Ergonomic Principles: Guidelines and practices aimed at optimizing the interaction between workers and their work environment.
Role of Employee Training in Ergonomics Implementation:
Awareness and Understanding:
- How: Educate employees about the importance of ergonomics and its impact on health and productivity.
- Impact: Increases awareness of ergonomic issues and motivates workers to engage in ergonomics initiatives.
Hazard Recognition:
- How: Train employees to identify ergonomic hazards such as awkward postures, repetitive motions, and excessive force.
- Impact: Empowers workers to proactively recognize and report ergonomic risks, facilitating timely interventions.
Proper Use of Ergonomic Tools and Equipment:
- How: Instruct employees on how to correctly use ergonomic tools and equipment, including adjustable workstations, ergonomic hand tools, and assistive devices.
- Impact: Ensures that workers can effectively utilize ergonomic solutions, maximizing their benefits and reducing the risk of injury.
Safe Work Practices:
- How: Provide training on safe lifting techniques, posture maintenance, and movement strategies to minimize strain and injury.
- Impact: Promotes healthier work habits, reducing the incidence of musculoskeletal disorders (MSDs).
Ergonomic Assessment Participation:
- How: Involve employees in ergonomic assessments and the development of improvement plans.
- Impact: Enhances the relevance and effectiveness of ergonomic interventions by incorporating worker input and insights.
Continuous Improvement and Feedback:
- How: Encourage ongoing feedback from employees regarding ergonomic practices and potential improvements.
- Impact: Fosters a collaborative environment where continuous improvement is supported and sustained.
Key Topics to Cover in Ergonomic Training:
Fundamentals of Ergonomics:
- Topics: Definition, principles, and benefits of ergonomics in the workplace.
- Objective: Provide a foundational understanding of ergonomics and its importance in manufacturing.
Ergonomic Hazard Identification:
- Topics: Common ergonomic hazards in manufacturing, such as repetitive tasks, awkward postures, and excessive force.
- Objective: Equip workers with the ability to recognize and assess ergonomic risks.
Workstation Setup and Adjustment:
- Topics: Proper arrangement of tools, equipment, and materials to promote neutral body postures.
- Objective: Teach employees how to set up and adjust their workstations for optimal ergonomics.
Safe Lifting and Material Handling Techniques:
- Topics: Correct methods for lifting, carrying, and moving heavy or awkward objects.
- Objective: Prevent injuries related to manual handling tasks by promoting safe practices.
Use of Ergonomic Tools and Equipment:
- Topics: Proper use and maintenance of ergonomic tools, such as adjustable chairs, ergonomic hand tools, and lifting aids.
- Objective: Ensure that workers can effectively utilize ergonomic solutions to reduce strain and improve efficiency.
Posture and Movement Strategies:
- Topics: Techniques for maintaining good posture and minimizing repetitive motions and awkward positions.
- Objective: Encourage healthier work habits that reduce the risk of MSDs.
Breaks and Work-Rest Cycles:
- Topics: Importance of regular breaks and how to structure work-rest cycles to prevent fatigue.
- Objective: Promote practices that allow for muscle recovery and reduce fatigue-related risks.
Reporting and Feedback Mechanisms:
- Topics: Procedures for reporting ergonomic concerns and providing feedback on ergonomic initiatives.
- Objective: Facilitate open communication and continuous improvement in ergonomic practices.
Ergonomic Assessment Procedures:
- Topics: How ergonomic assessments are conducted and the role of employees in the process.
- Objective: Involve workers in identifying and solving ergonomic issues, ensuring that interventions are practical and effective.
Health and Wellness Programs:
- Topics: Programs that support overall worker health, such as stretching exercises, fitness initiatives, and stress management.
- Objective: Enhance worker well-being, which complements ergonomic efforts and promotes a healthier workforce.
Benefits of Comprehensive Ergonomic Training:
- Reduced Injury Rates: Lower incidence of MSDs and other ergonomic-related injuries.
- Increased Productivity: Healthier and more comfortable workers are more efficient and have higher output.
- Enhanced Worker Satisfaction: Employees feel valued and supported, leading to higher job satisfaction and retention.
- Cost Savings: Decreased medical and compensation costs associated with workplace injuries.
- Improved Quality: Reduced errors and defects due to improved worker comfort and precision.
Conclusion: Employee training is essential for the successful implementation of ergonomics in manufacturing. By covering key topics such as hazard identification, safe work practices, and the proper use of ergonomic tools, organizations can empower their workforce to maintain a safe and efficient work environment. Comprehensive training not only prevents injuries but also enhances productivity and worker satisfaction, contributing to the overall success and sustainability of manufacturing operations.
8. How can the integration of ergonomic principles into the design of manufacturing processes enhance overall operational efficiency?
Answer:
Integrating ergonomic principles into the design of manufacturing processes can significantly enhance overall operational efficiency by optimizing the interaction between workers and their work environment. This integration leads to improved workflow, reduced fatigue, minimized errors, and increased productivity, ultimately contributing to smoother and more efficient operations.
Concepts:
- Ergonomic Principles: Guidelines aimed at designing work environments and processes that fit the capabilities and limitations of workers.
- Operational Efficiency: The ability to deliver products or services in the most cost-effective manner without sacrificing quality.
Enhancements to Operational Efficiency through Ergonomic Integration:
Optimized Workflow Design:
- How: Arrange workstations and equipment in a logical sequence that minimizes unnecessary movements and reduces the time spent transitioning between tasks.
- Impact: Streamlines operations, reduces cycle times, and increases the speed and consistency of production processes.
Reduction of Physical Strain and Fatigue:
- How: Implement ergonomic solutions such as adjustable workstations, ergonomic seating, and tools designed to reduce strain.
- Impact: Decreases worker fatigue, enabling sustained productivity and reducing the likelihood of errors caused by tiredness.
Enhanced Worker Comfort and Morale:
- How: Create a comfortable and supportive work environment that addresses worker needs and preferences.
- Impact: Improves worker satisfaction and morale, leading to higher engagement, reduced absenteeism, and increased commitment to quality work.
Minimized Errors and Defects:
- How: Design processes that align with natural human movements and cognitive capabilities, reducing the likelihood of mistakes.
- Impact: Enhances product quality, lowers defect rates, and minimizes rework and waste, contributing to overall efficiency.
Improved Tool and Equipment Design:
- How: Use ergonomic tools that are easier to handle, reduce the required force, and fit comfortably in the worker’s hand.
- Impact: Increases precision and reduces the time needed to perform tasks, enhancing both speed and accuracy in production.
Streamlined Training and Onboarding:
- How: Design processes that are intuitive and easy to learn, supported by ergonomic training programs.
- Impact: Reduces the time and resources required for training new employees, allowing them to become productive more quickly.
Increased Flexibility and Adaptability:
- How: Create processes and workstations that can be easily adjusted to accommodate different tasks and worker needs.
- Impact: Enhances the ability to adapt to changing production demands and customize workflows, improving overall operational flexibility.
Safety Enhancements:
- How: Incorporate safety features into process design, such as emergency stops, proper ventilation, and ergonomic safeguards.
- Impact: Reduces the risk of accidents and injuries, ensuring a safer work environment and minimizing disruptions to operations.
Better Utilization of Space:
- How: Design workspaces that maximize the efficient use of available space, reducing clutter and optimizing layout.
- Impact: Enhances workflow efficiency, reduces the time spent searching for tools and materials, and creates a more organized and productive workspace.
Sustainable Practices:
- How: Integrate ergonomic principles with sustainable manufacturing practices, such as reducing energy consumption and minimizing waste.
- Impact: Promotes a sustainable and efficient operation that aligns with environmental goals and regulatory requirements, enhancing overall operational resilience.
Examples of Ergonomic Integration Enhancing Efficiency:
- Adjustable Conveyor Systems: Allowing workers to easily change conveyor heights to match different tasks, reducing the need for bending and lifting.
- Ergonomic Assembly Tools: Tools designed to fit comfortably in the hand and reduce the effort required to perform assembly tasks, increasing speed and accuracy.
- Automated Material Handling: Implementing robotic arms and automated guided vehicles (AGVs) to move materials, minimizing manual handling and reducing physical strain on workers.
Benefits of Integrating Ergonomic Principles:
- Higher Productivity: Efficient workflows and reduced worker fatigue lead to increased production rates.
- Lower Operational Costs: Reduced errors, rework, and injury-related expenses contribute to cost savings.
- Enhanced Quality: Improved precision and consistency in tasks lead to higher-quality products.
- Worker Retention: A comfortable and safe work environment fosters loyalty and reduces turnover rates.
- Competitive Advantage: Organizations that prioritize ergonomics can differentiate themselves through higher efficiency and better product quality.
Conclusion: Integrating ergonomic principles into the design of manufacturing processes is a strategic approach that enhances overall operational efficiency. By optimizing workflows, reducing physical strain, improving tool design, and fostering a supportive work environment, manufacturers can achieve higher productivity, better quality, and reduced costs. This holistic integration not only benefits the organization but also contributes to the well-being and satisfaction of the workforce, ensuring sustained success in a competitive market.
9. How can the principles of ergonomics be applied to improve the design of manufacturing tools and equipment?
Answer:
Applying the principles of ergonomics to the design of manufacturing tools and equipment involves creating products that fit the user’s physical and cognitive capabilities, thereby enhancing comfort, efficiency, and safety. Ergonomic design ensures that tools and equipment minimize strain, reduce the risk of injury, and improve overall task performance.
Concepts:
- Ergonomic Design: The process of designing tools, systems, and environments to optimize human well-being and overall system performance.
- User-Centered Design: Focusing on the needs, preferences, and limitations of the end-users throughout the design process.
Principles of Ergonomics Applied to Tool and Equipment Design:
Fit the User:
- How: Design tools and equipment to accommodate a range of body sizes, shapes, and strengths.
- Impact: Ensures that all workers can use the tools comfortably and effectively, reducing the risk of strain and injury.
Minimize Force Requirements:
- How: Design tools that require minimal effort to operate, using lightweight materials and efficient mechanisms.
- Impact: Reduces muscle fatigue and strain, allowing workers to perform tasks more easily and for longer periods without discomfort.
Enhance Grip Comfort and Control:
- How: Incorporate ergonomic grips with contoured shapes, soft materials, and appropriate sizes to fit the hand naturally.
- Impact: Improves control and precision in tool use, reducing the likelihood of slips and errors while enhancing worker comfort.
Optimize Tool Weight and Balance:
- How: Distribute weight evenly and keep tools as lightweight as possible without compromising functionality.
- Impact: Reduces the physical burden on workers, enhancing ease of use and minimizing fatigue during repetitive or prolonged tasks.
Provide Adjustable Features:
- How: Include adjustable components, such as handle angles, heights, and lengths, to allow customization based on individual preferences and task requirements.
- Impact: Enhances flexibility and adaptability, ensuring that tools can be tailored to fit different tasks and user needs, improving overall efficiency.
Reduce Vibration and Noise:
- How: Design tools with vibration dampening materials and noise-reducing features.
- Impact: Minimizes the risk of vibration-related injuries and reduces noise-induced stress, creating a more comfortable and safer work environment.
Simplify Controls and Interfaces:
- How: Design intuitive and easily accessible controls that align with natural hand movements and cognitive processes.
- Impact: Enhances ease of use, reduces the learning curve, and decreases the likelihood of operational errors.
Ensure Proper Lighting and Visibility:
- How: Incorporate built-in lighting or design tools to enhance visibility of the work area and task.
- Impact: Improves accuracy and reduces eye strain, allowing workers to perform tasks more effectively and safely.
Facilitate Easy Maintenance and Cleaning:
- How: Design tools and equipment with easy access to components for maintenance and cleaning.
- Impact: Reduces downtime, ensures consistent tool performance, and enhances hygiene, contributing to overall operational efficiency.
Incorporate Safety Features:
- How: Integrate safety mechanisms such as guards, automatic shut-offs, and emergency stops into tool and equipment design.
- Impact: Protects workers from potential hazards, reduces the risk of accidents, and ensures a safer working environment.
Examples of Ergonomically Designed Tools and Equipment:
- Ergonomic Hand Tools: Screwdrivers, pliers, and hammers with contoured grips and lightweight materials to reduce strain.
- Adjustable Workstations: Height-adjustable tables and chairs that allow workers to maintain neutral postures.
- Power Tools with Vibration Dampening: Drills and grinders designed to minimize vibration and reduce the risk of hand-arm vibration syndrome (HAVS).
- Automated Assistive Devices: Lifting aids and robotic arms that handle heavy or repetitive tasks, minimizing manual effort and reducing the risk of injury.
Benefits of Ergonomic Tool and Equipment Design:
- Increased Productivity: Tools designed for ease of use enable workers to perform tasks more efficiently and accurately.
- Reduced Injury Rates: Minimizes the risk of musculoskeletal disorders and other ergonomic-related injuries.
- Enhanced Worker Comfort: Improves overall job satisfaction and reduces fatigue, leading to a more engaged and motivated workforce.
- Higher Quality Output: Better control and precision in tool use result in higher-quality products with fewer defects.
- Cost Savings: Lower injury rates and increased productivity contribute to reduced operational costs and higher profitability.
Conclusion: Applying ergonomic principles to the design of manufacturing tools and equipment is essential for creating a safer, more efficient, and comfortable work environment. By focusing on user-centered design, minimizing physical strain, enhancing control and precision, and incorporating safety features, manufacturers can significantly improve operational efficiency, reduce injury rates, and enhance worker satisfaction. Ergonomic tool and equipment design not only benefits the workers but also contributes to the overall success and sustainability of manufacturing operations.
10. How can human factors engineering be used to design safer and more efficient manufacturing systems?
Answer:
Human factors engineering (HFE) integrates knowledge of human behavior, capabilities, and limitations into the design of systems, processes, and environments to enhance safety, efficiency, and user satisfaction. In manufacturing, HFE plays a vital role in designing systems that accommodate human needs, reduce errors, and optimize performance, thereby creating safer and more efficient manufacturing operations.
Concepts:
- Human Factors Engineering (HFE): The discipline of designing systems that account for human strengths and limitations.
- System Design: The process of defining the architecture, components, and interfaces of a system to achieve specified requirements.
Applications of HFE in Manufacturing Systems Design:
Workstation Design and Layout:
- How: Arrange workstations to minimize unnecessary movements, reduce reaching and bending, and promote neutral postures.
- Impact: Enhances worker comfort, reduces fatigue, and decreases the risk of musculoskeletal injuries, leading to increased productivity and safety.
Control Interface Design:
- How: Design user-friendly control panels with clear labeling, intuitive layouts, and accessible controls.
- Impact: Reduces the likelihood of operator errors, enhances ease of use, and improves overall system reliability and efficiency.
Automation and Human-Machine Interaction:
- How: Design automated systems that complement human capabilities, providing clear feedback and intuitive controls.
- Impact: Enhances collaboration between humans and machines, improves task performance, and reduces the risk of accidents and errors.
Lighting and Environmental Conditions:
- How: Optimize lighting levels, reduce glare, and control noise to create a comfortable and conducive work environment.
- Impact: Improves visibility, reduces eye strain and hearing fatigue, and enhances overall worker focus and accuracy.
Error-Proofing and Safety Mechanisms:
- How: Implement design features that prevent incorrect operations, such as interlocks, alarms, and fail-safes.
- Impact: Minimizes the occurrence of human errors, enhances system safety, and protects workers from potential hazards.
Task Design and Workflow Optimization:
- How: Structure tasks to align with human cognitive and physical capabilities, avoiding overload and reducing complexity.
- Impact: Enhances task performance, reduces mental and physical strain, and increases overall operational efficiency.
Training and Support Systems:
- How: Develop comprehensive training programs and support systems that educate workers on system use and best practices.
- Impact: Ensures that workers are proficient in operating systems, reduces the likelihood of errors, and enhances overall system performance.
Cognitive Load Management:
- How: Design systems that provide clear information, reduce information overload, and support decision-making processes.
- Impact: Enhances worker focus, reduces mental fatigue, and improves the accuracy and speed of task execution.
Feedback and Monitoring Systems:
- How: Incorporate real-time feedback mechanisms that inform workers of their performance and system status.
- Impact: Enables immediate corrective actions, enhances situational awareness, and supports continuous improvement.
Flexibility and Adaptability:
- How: Design systems that can be easily reconfigured to accommodate different tasks and worker preferences.
- Impact: Increases operational flexibility, allows for customization based on worker needs, and supports diverse production requirements.
Benefits of Using HFE in Manufacturing Systems Design:
- Enhanced Safety: Reduces the risk of accidents and injuries by designing systems that account for human limitations.
- Increased Efficiency: Optimizes workflows and task designs to align with human capabilities, improving productivity and reducing cycle times.
- Improved Quality: Minimizes errors and defects by creating user-friendly and intuitive systems that support precise and accurate task execution.
- Higher Worker Satisfaction: Creates a comfortable and supportive work environment, enhancing job satisfaction and reducing turnover rates.
- Cost Savings: Lower injury rates, reduced error-related costs, and increased productivity contribute to overall cost savings and profitability.
Examples of HFE in Manufacturing:
- Ergonomic Assembly Lines: Designing assembly lines that allow workers to maintain comfortable postures and reduce repetitive motions.
- Intuitive Control Panels: Creating control interfaces that are easy to understand and operate, reducing the learning curve and minimizing operator errors.
- Automated Safety Systems: Implementing sensors and automated shut-off mechanisms that respond to unsafe conditions, protecting workers from potential hazards.
Conclusion: Human factors engineering is essential for designing safer and more efficient manufacturing systems. By integrating HFE principles into system design, manufacturers can create environments that enhance worker safety, optimize performance, and improve overall operational efficiency. This holistic approach not only benefits the workforce but also contributes to the long-term success and sustainability of manufacturing operations.
11. How can wearable ergonomic devices be utilized in manufacturing to monitor and improve worker health and performance?
Answer:
Wearable ergonomic devices, such as smart gloves, exoskeletons, and fitness trackers, can play a significant role in monitoring and improving worker health and performance in manufacturing settings. These devices collect real-time data on various physiological and movement parameters, providing insights that can be used to enhance ergonomics, prevent injuries, and optimize productivity.
Concepts:
- Wearable Ergonomic Devices: Electronic devices worn on the body that monitor physical activities, movements, and health indicators.
- Real-Time Monitoring: The continuous tracking and analysis of data as it is generated, allowing for immediate feedback and intervention.
Applications of Wearable Ergonomic Devices in Manufacturing:
Posture Monitoring:
- How: Wearable sensors track body posture and movements to identify awkward positions or excessive strain.
- Impact: Alerts workers and supervisors to poor posture, enabling timely adjustments to prevent musculoskeletal disorders (MSDs).
Motion Tracking:
- How: Devices like smart gloves or motion capture suits monitor repetitive motions and ergonomic risks.
- Impact: Identifies repetitive strain patterns, allowing for task rotation or ergonomic interventions to reduce the risk of injury.
Fatigue Detection:
- How: Fitness trackers and smartwatches measure indicators such as heart rate variability and activity levels to assess worker fatigue.
- Impact: Provides alerts when workers show signs of fatigue, prompting rest breaks to prevent accidents and maintain productivity.
Load Monitoring:
- How: Exoskeletons and smart lifting aids measure the weight being lifted and the force exerted by workers.
- Impact: Ensures that lifting tasks are performed within safe limits, reducing the risk of back injuries and overexertion.
Environmental Monitoring:
- How: Wearable devices equipped with sensors track exposure to environmental factors like temperature, noise, and humidity.
- Impact: Alerts workers to unsafe environmental conditions, allowing for immediate corrective actions to protect worker health.
Activity Recognition:
- How: Devices use algorithms to recognize and categorize different types of physical activities performed by workers.
- Impact: Provides data on work patterns and identifies opportunities for process optimization and ergonomic improvements.
Health Monitoring:
- How: Wearables track vital signs such as heart rate, blood pressure, and respiratory rate.
- Impact: Enables early detection of health issues, ensuring timely medical intervention and promoting overall worker well-being.
Training and Feedback:
- How: Wearable devices provide real-time feedback on movements and actions during training sessions.
- Impact: Enhances the effectiveness of ergonomic training by providing immediate corrections and reinforcing proper techniques.
Data Analytics for Ergonomic Improvements:
- How: Collected data is analyzed to identify trends, patterns, and areas of ergonomic risk.
- Impact: Informs the development of targeted ergonomic interventions and process improvements based on empirical data.
Enhanced Worker Engagement:
- How: Providing workers with access to their own ergonomic data and feedback.
- Impact: Empowers workers to take an active role in maintaining their health and optimizing their performance.
Benefits of Utilizing Wearable Ergonomic Devices:
- Injury Prevention: Early detection of ergonomic risks and health issues helps prevent workplace injuries.
- Increased Productivity: Healthy and comfortable workers are more efficient and less prone to errors.
- Data-Driven Decisions: Real-time and historical data enable informed decisions for ergonomic improvements and process optimizations.
- Enhanced Safety Compliance: Continuous monitoring ensures adherence to safety standards and regulations.
- Worker Well-Being: Promotes a culture of health and safety, improving overall worker satisfaction and morale.
Challenges and Considerations:
- Privacy Concerns: Ensuring that data collected from wearable devices is used ethically and with worker consent.
- Cost of Implementation: Initial investment in wearable technology and the associated infrastructure.
- Data Management: Handling and analyzing large volumes of data requires robust systems and expertise.
- Worker Acceptance: Encouraging workers to adopt and consistently use wearable devices through education and incentives.
Conclusion: Wearable ergonomic devices offer valuable tools for monitoring and improving worker health and performance in manufacturing environments. By providing real-time data on posture, movement, fatigue, and environmental conditions, these devices enable proactive ergonomic interventions, injury prevention, and enhanced productivity. Despite challenges such as privacy concerns and implementation costs, the benefits of wearable technology in promoting a safe and efficient workplace make it a worthwhile investment for forward-thinking manufacturers.
12. How can participatory ergonomics enhance the effectiveness of ergonomic interventions in manufacturing?
Answer:
Participatory ergonomics involves actively engaging workers in the identification, analysis, and resolution of ergonomic issues within the workplace. By involving employees in the ergonomics process, organizations can enhance the effectiveness of ergonomic interventions, ensuring that solutions are practical, relevant, and sustainable. This collaborative approach leverages the firsthand knowledge and insights of workers, fostering a sense of ownership and commitment to ergonomic improvements.
Concepts:
- Participatory Ergonomics: A collaborative approach that involves workers in ergonomic problem-solving and decision-making.
- Worker Involvement: Encouraging active participation and feedback from employees in the ergonomics process.
Benefits of Participatory Ergonomics:
Enhanced Problem Identification:
- How: Workers can provide detailed insights into daily tasks, identifying specific ergonomic challenges that may not be apparent to management.
- Impact: Leads to a more accurate and comprehensive understanding of ergonomic issues, ensuring that interventions address real-world problems.
Improved Solution Development:
- How: Collaborating with workers in designing ergonomic solutions ensures that interventions are practical and feasible.
- Impact: Increases the likelihood of successful implementation and acceptance of ergonomic measures.
Increased Worker Buy-In and Compliance:
- How: Involving employees in the decision-making process fosters a sense of ownership and responsibility towards ergonomic initiatives.
- Impact: Enhances adherence to ergonomic practices and promotes sustained behavioral changes that support long-term ergonomic improvements.
Faster Implementation of Solutions:
- How: When workers are part of the solution development, they can assist in the timely implementation of ergonomic interventions.
- Impact: Reduces delays and ensures that ergonomic improvements are integrated smoothly into existing workflows.
Enhanced Communication and Trust:
- How: Participatory ergonomics fosters open communication between workers and management, building trust and mutual respect.
- Impact: Creates a positive work environment where ergonomic concerns are addressed collaboratively, enhancing overall workplace morale.
Continuous Improvement:
- How: Ongoing worker involvement encourages continuous feedback and iterative improvements to ergonomic interventions.
- Impact: Ensures that ergonomic solutions remain effective and adapt to changing work conditions and worker needs.
Cost-Effective Solutions:
- How: Leveraging worker insights can lead to innovative and cost-effective ergonomic solutions that maximize resource utilization.
- Impact: Reduces the financial burden of implementing ergonomic interventions while enhancing their effectiveness.
Implementing Participatory Ergonomics:
Establish Ergonomic Committees:
- How: Form committees that include representatives from different departments and levels of the organization.
- Impact: Ensures diverse perspectives are considered in identifying and solving ergonomic issues.
Conduct Worker Surveys and Interviews:
- How: Gather feedback from workers through surveys, interviews, and focus groups to understand their ergonomic challenges and suggestions.
- Impact: Provides valuable data to inform targeted ergonomic interventions.
Organize Ergonomic Workshops and Brainstorming Sessions:
- How: Facilitate interactive sessions where workers can collaborate with ergonomists and management to develop solutions.
- Impact: Encourages creative problem-solving and ensures that solutions are tailored to specific work environments.
Pilot Testing of Ergonomic Solutions:
- How: Implement proposed ergonomic interventions on a small scale to evaluate their effectiveness and gather worker feedback.
- Impact: Allows for adjustments and improvements before full-scale implementation, ensuring that solutions are practical and effective.
Provide Training and Education:
- How: Educate workers on ergonomic principles and the importance of their involvement in the ergonomics process.
- Impact: Empowers employees to actively participate and contribute to ergonomic improvements.
Recognize and Reward Participation:
- How: Acknowledge and reward workers who actively contribute to ergonomic initiatives.
- Impact: Motivates continued participation and reinforces the value of ergonomic contributions.
Challenges and Solutions:
Resistance to Change:
- Challenge: Some workers may be skeptical about ergonomic initiatives or resistant to altering established workflows.
- Solution: Communicate the benefits of ergonomics, involve workers in the process, and provide evidence of positive outcomes to gain buy-in.
Time and Resource Constraints:
- Challenge: Implementing participatory ergonomics requires time and resources that may be limited.
- Solution: Integrate ergonomics into existing workflows and allocate dedicated resources to support ergonomic initiatives.
Ensuring Diverse Representation:
- Challenge: Ensuring that all worker groups are adequately represented in ergonomic committees and discussions.
- Solution: Actively include representatives from various departments, roles, and levels to capture a comprehensive range of perspectives.
Conclusion: Participatory ergonomics significantly enhances the effectiveness of ergonomic interventions in manufacturing by fostering collaboration, leveraging worker insights, and ensuring that solutions are practical and sustainable. By actively involving employees in the ergonomics process, organizations can create safer, more efficient, and more comfortable work environments that benefit both workers and the overall manufacturing operation.
12. How can ergonomics contribute to reducing workplace accidents and enhancing overall safety in manufacturing environments?
Answer:
Ergonomics plays a pivotal role in reducing workplace accidents and enhancing overall safety in manufacturing environments by designing work systems that align with human capabilities and limitations. By addressing ergonomic risks, organizations can create safer workspaces, minimize the likelihood of accidents, and promote a culture of safety and well-being.
Concepts:
- Ergonomics: The science of designing work environments and tasks to fit the worker, enhancing performance and reducing the risk of injury.
- Workplace Safety: The practices and measures implemented to prevent accidents, injuries, and illnesses in the workplace.
Ways Ergonomics Enhances Workplace Safety:
Improved Workstation Design:
- How: Ergonomically designed workstations accommodate a range of body sizes and promote neutral postures.
- Impact: Reduces the risk of musculoskeletal injuries and fatigue, enhancing worker comfort and safety.
Reduction of Repetitive Strain:
- How: Implementing task rotation, using ergonomic tools, and redesigning processes to minimize repetitive motions.
- Impact: Lowers the incidence of repetitive strain injuries (RSIs) and associated workplace accidents.
Enhanced Visibility and Accessibility:
- How: Designing work areas with adequate lighting, clear sightlines, and easily accessible tools and materials.
- Impact: Reduces the likelihood of accidents caused by poor visibility, cluttered workspaces, or difficulty accessing necessary equipment.
Minimized Manual Handling Risks:
- How: Using mechanical aids, ergonomic lifting techniques, and proper training for manual handling tasks.
- Impact: Decreases the risk of lifting-related injuries and accidents, promoting safer material handling practices.
Vibration and Noise Control:
- How: Designing equipment to reduce vibration levels and implementing noise control measures in the workplace.
- Impact: Protects workers from vibration-induced injuries and hearing loss, enhancing overall safety and comfort.
Error-Proofing Designs:
- How: Incorporating safety features such as interlocks, guards, and fail-safes into equipment and processes.
- Impact: Prevents operator errors and unintended machine actions, reducing the risk of accidents and injuries.
Enhanced Worker Training:
- How: Providing ergonomic training that includes safe work practices, proper tool use, and awareness of ergonomic hazards.
- Impact: Empowers workers to maintain safe postures, use tools correctly, and recognize potential safety risks, reducing the likelihood of accidents.
Proactive Hazard Identification:
- How: Conducting regular ergonomic assessments and involving workers in identifying and reporting ergonomic hazards.
- Impact: Allows for early detection and mitigation of safety risks, preventing accidents before they occur.
Stress Reduction:
- How: Designing work systems that minimize cognitive and physical stress through balanced workloads and supportive environments.
- Impact: Reduces the risk of stress-related accidents and errors, promoting a healthier and safer workforce.
Sustainable and Safe Work Practices:
- How: Integrating ergonomic principles with safety protocols to create comprehensive safety strategies.
- Impact: Ensures that ergonomic improvements are aligned with broader safety goals, enhancing overall workplace safety.
Case Studies and Examples:
- Ergonomic Tool Redesign: Replacing traditional, heavy hand tools with lightweight, ergonomically designed alternatives can reduce the risk of hand and arm injuries.
- Adjustable Workstations: Implementing height-adjustable tables and chairs allows workers to maintain comfortable postures, reducing the risk of back injuries and fatigue-related accidents.
- Automated Safety Systems: Installing automated shut-off mechanisms and safety interlocks on machinery can prevent accidental starts and protect workers from moving parts.
Benefits of Ergonomics in Workplace Safety:
- Lower Injury Rates: Reduced incidence of musculoskeletal disorders and other ergonomic-related injuries.
- Increased Productivity: Healthier and safer workers are more productive and have fewer absences.
- Enhanced Compliance: Meets regulatory safety standards, avoiding fines and legal issues.
- Improved Worker Morale: Demonstrates a commitment to worker well-being, fostering a positive safety culture.
- Cost Savings: Reduces costs associated with workplace injuries, including medical expenses, compensation claims, and lost productivity.
Conclusion: Ergonomics is a fundamental component of workplace safety in manufacturing environments. By designing work systems that align with human capabilities, ergonomics helps to prevent accidents, reduce injuries, and create a safer and more efficient workplace. Implementing ergonomic principles not only protects workers but also enhances overall operational performance, contributing to the long-term success and sustainability of manufacturing organizations.
Conclusion:
The above review questions and detailed answers provide a comprehensive exploration of human factors and ergonomics in manufacturing. Covering fundamental concepts, ergonomic assessments, hazard identification and mitigation, the role of training, and the integration of ergonomic principles into system design, these questions facilitate a deep understanding of how ergonomics can enhance workplace safety, productivity, and worker well-being. Engaging with these questions equips students and professionals with the knowledge to implement effective ergonomic practices, reduce workplace accidents, and create more efficient and sustainable manufacturing environments. This holistic approach fosters a culture of safety and continuous improvement, ensuring the long-term success and competitiveness of manufacturing operations.
Human Factors and Ergonomics: Thought-Provoking Questions with Detailed Answers:
1. How do human factors and ergonomics (HF&E) contribute to reducing workplace injuries in manufacturing, and what are some specific examples of ergonomic interventions that have proven effective?
Answer:
Human Factors and Ergonomics (HF&E) play a pivotal role in minimizing workplace injuries in manufacturing by designing work environments, tools, and processes that align with human capabilities and limitations. By focusing on the interaction between workers and their tasks, HF&E aims to enhance safety, comfort, and efficiency, thereby reducing the likelihood of injuries and musculoskeletal disorders (MSDs).
Key Contributions of HF&E:
Risk Identification and Mitigation:
- How: HF&E professionals conduct ergonomic assessments to identify potential hazards such as repetitive motions, awkward postures, excessive force, and prolonged static positions.
- Impact: Early identification of risks allows for timely interventions, preventing the onset of injuries.
Workstation Design:
- How: Designing adjustable workstations that accommodate various body sizes and allow workers to maintain neutral postures.
- Impact: Reduces strain on muscles and joints, minimizing the risk of MSDs.
Tool and Equipment Design:
- How: Developing ergonomic tools with features like cushioned grips, appropriate weight distribution, and adjustable components.
- Impact: Enhances comfort and reduces the physical effort required to perform tasks, lowering the risk of repetitive strain injuries.
Task Variation and Rotation:
- How: Implementing job rotation strategies to vary the types of tasks workers perform.
- Impact: Prevents prolonged exposure to repetitive motions, reducing muscle fatigue and injury risk.
Training and Education:
- How: Providing workers with training on proper body mechanics, safe lifting techniques, and the correct use of ergonomic tools.
- Impact: Empowers workers to adopt safe practices, further reducing injury rates.
Specific Examples of Effective Ergonomic Interventions:
Adjustable Workstations:
- Example: Height-adjustable assembly tables allow workers to switch between sitting and standing positions, promoting better posture and reducing back strain.
Ergonomic Hand Tools:
- Example: Screwdrivers with contoured handles and reduced weight decrease hand fatigue and minimize the risk of carpal tunnel syndrome.
Automated Material Handling Systems:
- Example: Conveyor belts and robotic arms handle heavy lifting and repetitive tasks, reducing the physical demands on human workers.
Anti-Fatigue Mats:
- Example: Placing anti-fatigue mats in areas where workers stand for extended periods reduces leg and back discomfort, preventing fatigue-related injuries.
Task Redesign:
- Example: Redesigning assembly processes to minimize excessive reaching and bending, thereby reducing the risk of shoulder and back injuries.
Conclusion: HF&E significantly contributes to creating safer manufacturing environments by proactively addressing ergonomic risks. Through thoughtful design, training, and process optimization, ergonomic interventions not only reduce workplace injuries but also enhance overall productivity and worker satisfaction.
2. In what ways can ergonomic assessments be integrated into the early stages of manufacturing process design to prevent ergonomic issues before they arise?
Answer:
Integrating ergonomic assessments into the early stages of manufacturing process design is crucial for proactively identifying and mitigating potential ergonomic issues. This proactive approach ensures that ergonomic considerations are embedded into the very fabric of the manufacturing process, leading to safer, more efficient, and more comfortable work environments.
Steps to Integrate Ergonomic Assessments Early:
Human-Centered Design Approach:
- How: Adopt a human-centered design philosophy that prioritizes the needs, capabilities, and limitations of workers from the outset.
- Impact: Ensures that the manufacturing process is tailored to human use, minimizing strain and enhancing comfort.
Cross-Functional Collaboration:
- How: Involve ergonomists, engineers, designers, and frontline workers in the design team to provide diverse perspectives.
- Impact: Facilitates comprehensive identification of ergonomic risks and fosters innovative solutions that address multiple aspects of the process.
Ergonomic Risk Assessment Tools:
- How: Utilize standardized ergonomic assessment tools (e.g., REBA, RULA) during the design phase to evaluate potential risks associated with different tasks and workflows.
- Impact: Provides objective data to inform design decisions, ensuring that ergonomic considerations are systematically addressed.
Simulation and Modeling:
- How: Use digital simulations and modeling software to visualize work processes and identify ergonomic issues before physical implementation.
- Impact: Allows for the testing and refinement of designs in a virtual environment, reducing the need for costly and time-consuming modifications later.
Prototype Testing with Worker Feedback:
- How: Develop prototypes of workstations and processes and conduct ergonomic testing with actual workers to gather feedback.
- Impact: Ensures that designs are practical and effective in real-world conditions, incorporating user insights to enhance ergonomics.
Iterative Design Process:
- How: Implement an iterative design process that incorporates continuous ergonomic evaluations and refinements based on assessment findings and worker feedback.
- Impact: Facilitates ongoing improvements, ensuring that ergonomic considerations remain integral throughout the design and development stages.
Benefits of Early Integration:
Cost Savings:
- Impact: Identifying and addressing ergonomic issues early reduces the need for expensive retrofits and modifications after implementation.
Enhanced Productivity:
- Impact: Ergonomically optimized processes minimize worker fatigue and discomfort, leading to higher efficiency and productivity levels.
Improved Worker Satisfaction:
- Impact: Involving workers in the design process fosters a sense of ownership and ensures that their needs are met, enhancing job satisfaction and morale.
Reduced Injury Rates:
- Impact: Proactively addressing ergonomic risks prevents the development of workplace injuries, leading to a healthier workforce.
Compliance with Regulations:
- Impact: Early ergonomic assessments ensure that manufacturing processes comply with occupational safety and health regulations, avoiding legal and financial penalties.
Case Example: A leading automotive manufacturer integrated ergonomic assessments into the design of their assembly line. By involving workers in the design phase and using simulation tools, they identified and eliminated awkward postures and excessive reaching distances. This led to a 30% reduction in reported MSDs and a 20% increase in assembly efficiency.
Conclusion: Integrating ergonomic assessments into the early stages of manufacturing process design is a strategic approach that enhances safety, productivity, and worker well-being. By adopting a proactive and collaborative design process, manufacturers can prevent ergonomic issues before they arise, resulting in more effective and sustainable manufacturing operations.
3. How can the principles of human factors and ergonomics be applied to optimize material handling processes in manufacturing to enhance efficiency and reduce injury risks?
Answer:
Optimizing material handling processes through the principles of human factors and ergonomics (HF&E) involves designing systems and workflows that align with human capabilities, minimize physical strain, and enhance operational efficiency. Effective application of HF&E principles in material handling can significantly reduce injury risks and improve overall productivity.
Key Principles and Applications:
Minimize Physical Exertion:
- How: Design processes to reduce the amount of lifting, carrying, pushing, and pulling required by workers.
- Impact: Decreases the physical strain on workers, lowering the risk of musculoskeletal injuries and fatigue.
Optimize Reach and Repetition:
- How: Arrange materials and tools within easy reach and minimize repetitive motions by using automated systems where feasible.
- Impact: Reduces the need for excessive reaching and repetitive movements, mitigating the risk of repetitive strain injuries.
Enhance Workstation Layout:
- How: Design workstations with adjustable heights and modular configurations to accommodate different tasks and worker sizes.
- Impact: Promotes neutral body postures, reducing the likelihood of awkward postures and associated injuries.
Implement Mechanical Aids:
- How: Utilize forklifts, conveyors, hoists, and other mechanical aids to handle heavy or bulky materials.
- Impact: Reduces the need for manual lifting and carrying, minimizing the risk of back injuries and other musculoskeletal disorders.
Improve Pathway Design:
- How: Design clear and unobstructed pathways for material movement, ensuring that aisles are wide enough and surfaces are even.
- Impact: Prevents trips, slips, and falls, enhancing overall workplace safety.
Standardize Handling Procedures:
- How: Develop and implement standardized procedures for material handling, including safe lifting techniques and proper use of equipment.
- Impact: Ensures consistency in handling practices, reducing the likelihood of injuries and improving efficiency.
Use of Ergonomic Tools:
- How: Provide workers with ergonomically designed tools such as adjustable grips, lightweight containers, and easy-to-use lifting devices.
- Impact: Enhances comfort and reduces the effort required to handle materials, decreasing the risk of injuries.
Incorporate Automation and Robotics:
- How: Deploy automated guided vehicles (AGVs) and robotic arms to perform material handling tasks that are repetitive or require precision.
- Impact: Increases efficiency, reduces human error, and minimizes the physical demands on workers.
Training and Education:
- How: Educate workers on ergonomic principles, proper material handling techniques, and the correct use of mechanical aids.
- Impact: Empowers workers to adopt safe practices, further reducing injury risks and enhancing operational efficiency.
Ergonomic Assessments and Continuous Improvement:
- How: Regularly conduct ergonomic assessments of material handling processes and solicit worker feedback for improvements.
- Impact: Identifies emerging ergonomic risks and facilitates ongoing enhancements to handling processes
.
Benefits of Applying HF&E Principles to Material Handling:
- Reduced Injury Rates:
- Impact: Lower incidence of musculoskeletal disorders and other injuries related to material handling.
- Increased Productivity:
- Impact: Streamlined material handling processes enhance workflow efficiency, leading to higher production rates.
- Enhanced Worker Satisfaction:
- Impact: Ergonomically optimized tasks contribute to greater comfort and job satisfaction, reducing absenteeism and turnover.
- Cost Savings:
- Impact: Reduced injury-related costs, including medical expenses and compensation claims, improve the financial health of the organization.
- Improved Product Quality:
- Impact: Efficient and accurate material handling reduces errors and defects, ensuring consistent product quality.
- Compliance with Safety Regulations:
- Impact: Adhering to ergonomic standards helps meet occupational safety and health regulations, avoiding legal penalties.
Case Example: A food processing plant redesigned its material handling system by integrating adjustable conveyor belts and implementing automated palletizers. This reduced the need for manual lifting by 60%, resulting in a 40% decrease in back injury claims and a 25% increase in material handling efficiency.
Conclusion: Applying human factors and ergonomics principles to material handling processes is essential for enhancing efficiency and reducing injury risks in manufacturing. By focusing on ergonomic design, implementing mechanical aids, optimizing workflows, and fostering a culture of safety, manufacturers can create safer, more productive, and more sustainable operations.
4. What role does cognitive ergonomics play in manufacturing environments, and how can it be leveraged to improve decision-making and reduce errors?
Answer:
Cognitive ergonomics focuses on understanding and optimizing the mental processes of workers, such as perception, memory, reasoning, and decision-making, within the manufacturing environment. By addressing cognitive demands, manufacturers can enhance worker performance, improve decision-making, and reduce errors, thereby increasing overall operational efficiency and safety.
Key Aspects of Cognitive Ergonomics in Manufacturing:
Mental Workload Management:
- How: Design tasks and workflows to balance mental demands, preventing cognitive overload or underload.
- Impact: Ensures that workers remain alert, focused, and capable of performing tasks accurately without excessive stress.
Information Presentation:
- How: Optimize the way information is displayed through clear signage, intuitive interfaces, and effective use of visual aids.
- Impact: Enhances comprehension and quick decision-making, reducing the likelihood of misinterpretation and errors.
Decision Support Systems:
- How: Implement systems that provide real-time data analysis, predictive analytics, and actionable insights to assist workers in making informed decisions.
- Impact: Improves the accuracy and speed of decision-making processes, minimizing the risk of human error.
Human-Machine Interface (HMI) Design:
- How: Design user-friendly interfaces that facilitate seamless interaction between workers and automated systems or machinery.
- Impact: Reduces cognitive strain, simplifies task execution, and enhances operational efficiency.
Training and Skill Development:
- How: Provide comprehensive training programs that enhance cognitive skills such as problem-solving, critical thinking, and situational awareness.
- Impact: Empowers workers to handle complex tasks effectively, improving overall performance and reducing errors.
Error-Proofing (Poka-Yoke):
- How: Incorporate design features and processes that prevent or detect errors before they occur.
- Impact: Minimizes the impact of human errors, ensuring consistent quality and safety in manufacturing operations.
Situational Awareness:
- How: Enhance workers’ awareness of their environment and the status of processes through real-time monitoring and feedback systems.
- Impact: Enables proactive identification of potential issues, allowing for timely interventions and preventing errors.
Leveraging Cognitive Ergonomics to Improve Decision-Making and Reduce Errors:
Simplifying Complex Tasks:
- How: Break down complex tasks into manageable steps and provide clear instructions.
- Impact: Reduces cognitive load, making it easier for workers to focus and execute tasks accurately.
Implementing Redundant Systems:
- How: Use multiple verification methods, such as checklists and automated alerts, to ensure critical steps are not missed.
- Impact: Enhances reliability and reduces the chances of errors due to oversight or forgetfulness.
Enhancing Communication Channels:
- How: Facilitate effective communication between team members and across different levels of the organization.
- Impact: Ensures that critical information is shared promptly and accurately, supporting better decision-making.
Providing Real-Time Feedback:
- How: Use sensors and monitoring systems to provide immediate feedback on performance and process status.
- Impact: Allows workers to make instant adjustments, improving accuracy and reducing error rates.
Designing for Cognitive Diversity:
- How: Create workflows and systems that accommodate different cognitive styles and strengths among workers.
- Impact: Enhances overall team performance by leveraging diverse problem-solving approaches and reducing the risk of cognitive biases.
Benefits of Cognitive Ergonomics in Manufacturing:
Enhanced Decision-Making:
- Impact: Workers make more informed and accurate decisions, leading to improved process outcomes and product quality.
Reduced Error Rates:
- Impact: Fewer mistakes result in lower defect rates, minimizing waste and rework costs.
Increased Productivity:
- Impact: Optimized cognitive processes lead to more efficient task execution and higher throughput.
Improved Worker Well-Being:
- Impact: Balanced mental workloads and reduced cognitive strain contribute to lower stress levels and better overall mental health.
Enhanced Safety:
- Impact: Improved situational awareness and decision-making reduce the likelihood of accidents and injuries.
Case Example: A semiconductor manufacturing facility integrated cognitive ergonomics by redesigning its control room interfaces to display critical process data more intuitively. Additionally, they implemented real-time decision support systems that provided predictive maintenance alerts. As a result, operator errors decreased by 25%, and overall production efficiency increased by 15%.
Conclusion: Cognitive ergonomics plays a crucial role in optimizing the mental aspects of work in manufacturing environments. By focusing on mental workload management, information presentation, decision support, and human-machine interaction, manufacturers can enhance decision-making, reduce errors, and improve overall operational efficiency and safety. Integrating cognitive ergonomics into manufacturing processes leads to a more resilient, productive, and satisfied workforce.
5. How can the design of ergonomic workstations influence employee productivity and job satisfaction in manufacturing settings?
Answer:
The design of ergonomic workstations significantly impacts employee productivity and job satisfaction in manufacturing settings by creating environments that promote comfort, efficiency, and well-being. Ergonomically optimized workstations align with human body mechanics and cognitive processes, enabling workers to perform tasks more effectively while minimizing physical strain and fatigue.
Key Elements of Ergonomic Workstation Design:
Adjustability:
- How: Incorporate adjustable features such as height-adjustable tables, chairs, and monitors to accommodate different worker sizes and preferences.
- Impact: Allows workers to maintain neutral postures, reducing the risk of musculoskeletal disorders and enhancing comfort.
Optimal Layout:
- How: Arrange tools, materials, and equipment within easy reach to minimize unnecessary movements and reduce fatigue.
- Impact: Enhances workflow efficiency, allowing workers to perform tasks more quickly and with greater precision.
Proper Lighting:
- How: Ensure adequate and adjustable lighting to reduce eye strain and improve visibility of tasks.
- Impact: Increases accuracy and reduces errors, contributing to higher productivity and reduced eye fatigue.
Minimized Clutter:
- How: Design workstations with sufficient storage and organized layouts to keep tools and materials orderly.
- Impact: Reduces distractions and the time spent searching for items, improving focus and efficiency.
Comfortable Seating:
- How: Provide ergonomic chairs with adjustable lumbar support, seat height, and armrests.
- Impact: Enhances worker comfort, reducing fatigue and improving concentration and endurance.
Ergonomic Tools and Equipment:
- How: Supply tools and machinery that are designed to fit comfortably in the hand and reduce the effort required to operate them.
- Impact: Decreases physical strain and enhances the ease and speed of task execution.
Noise Control:
- How: Implement noise-reducing materials and designs to minimize ambient noise levels at workstations.
- Impact: Reduces stress and fatigue, improving concentration and overall job satisfaction.
Climate Control:
- How: Maintain optimal temperature and ventilation in work areas to ensure a comfortable working environment.
- Impact: Enhances worker comfort, reducing fatigue and maintaining productivity.
Influence on Employee Productivity:
Reduced Physical Strain:
- Impact: Ergonomic designs minimize discomfort and fatigue, allowing workers to maintain higher levels of productivity over longer periods.
Enhanced Focus and Efficiency:
- Impact: Organized and optimized workstations reduce distractions and streamline workflows, enabling workers to complete tasks more quickly and accurately.
Lower Error Rates:
- Impact: Improved visibility, optimal tool placement, and comfortable postures reduce the likelihood of mistakes, enhancing overall quality and efficiency.
Increased Operational Speed:
- Impact: Efficient workstation layouts and accessible tools enable faster task completion, boosting overall production rates.
Influence on Job Satisfaction:
Improved Comfort and Well-Being:
- Impact: Comfortable and supportive workstations enhance overall well-being, leading to higher job satisfaction and morale.
Enhanced Engagement:
- Impact: Ergonomic environments signal that the organization values worker health and comfort, fostering a sense of appreciation and engagement.
Reduced Stress and Fatigue:
- Impact: Minimizing physical discomfort and fatigue decreases workplace stress, contributing to a more positive work experience.
Higher Retention Rates:
- Impact: Satisfied and comfortable workers are more likely to remain with the organization, reducing turnover and associated recruitment costs.
Case Example: A manufacturing plant redesigned its assembly workstations by introducing adjustable height tables, ergonomic chairs, and optimized tool layouts. Following the redesign, the plant reported a 20% increase in assembly speed, a 30% reduction in worker-reported discomfort, and a 15% improvement in overall job satisfaction scores.
Conclusion: Ergonomic workstation design is a critical factor in enhancing employee productivity and job satisfaction in manufacturing settings. By creating work environments that prioritize comfort, efficiency, and well-being, manufacturers can foster a more engaged, healthy, and productive workforce. Investing in ergonomic workstation design not only benefits employees but also contributes to the overall success and competitiveness of the organization.
6. What are the psychological benefits of ergonomic workplace design for manufacturing workers, and how do these benefits impact overall organizational performance?
Answer:
Ergonomic workplace design not only addresses physical well-being but also offers significant psychological benefits for manufacturing workers. These benefits include reduced stress, increased job satisfaction, enhanced motivation, and improved mental well-being. These psychological advantages, in turn, positively impact overall organizational performance by fostering a more engaged, productive, and resilient workforce.
Key Psychological Benefits of Ergonomic Workplace Design:
Reduced Stress and Mental Fatigue:
- How: Ergonomic designs that promote comfortable postures, minimize physical strain, and streamline workflows reduce the cognitive and emotional burden on workers.
- Impact: Lower stress levels enhance mental clarity, decision-making capabilities, and overall job performance.
Increased Job Satisfaction:
- How: Providing ergonomic workstations demonstrates the organization’s commitment to worker well-being, fostering a sense of appreciation and value.
- Impact: Higher job satisfaction leads to greater employee retention, reduced absenteeism, and a more positive work environment.
Enhanced Motivation and Engagement:
- How: Comfortable and supportive work environments boost worker morale and motivation, encouraging active participation and enthusiasm for tasks.
- Impact: Increased engagement results in higher productivity, creativity, and willingness to go beyond basic job requirements.
Improved Concentration and Focus:
- How: Ergonomic designs that reduce physical discomfort and optimize information presentation help workers maintain better focus on their tasks.
- Impact: Enhanced concentration leads to fewer errors, higher quality output, and more efficient task completion.
Greater Sense of Control and Autonomy:
- How: Adjustable workstations and flexible work arrangements give workers more control over their work environment and how they perform tasks.
- Impact: A greater sense of autonomy fosters intrinsic motivation, job satisfaction, and a stronger connection to the organization.
Enhanced Team Cohesion and Collaboration:
- How: Ergonomic workplace designs that facilitate easy communication and collaboration among workers promote a sense of teamwork and community.
- Impact: Improved team cohesion leads to better problem-solving, innovation, and a supportive work culture.
Positive Organizational Culture:
- How: Prioritizing ergonomics contributes to a culture that values employee health, safety, and well-being.
- Impact: A positive organizational culture attracts and retains top talent, enhances reputation, and drives overall business success.
Impact on Organizational Performance:
Higher Productivity:
- Impact: Psychologically satisfied and motivated workers are more productive, contributing to increased output and efficiency.
Lower Turnover Rates:
- Impact: Enhanced job satisfaction and a positive work environment reduce employee turnover, saving costs associated with recruitment and training.
Improved Quality of Work:
- Impact: Focused and engaged workers produce higher quality work with fewer errors, enhancing product reliability and customer satisfaction.
Enhanced Innovation:
- Impact: A motivated and mentally well workforce is more likely to engage in creative thinking and innovative problem-solving, driving continuous improvement and competitive advantage.
Better Compliance and Safety Performance:
- Impact: Reduced stress and improved focus lead to better adherence to safety protocols and procedures, minimizing accidents and enhancing overall safety performance.
Case Example: A large electronics manufacturing company implemented ergonomic workplace designs, including adjustable workstations, noise-reducing materials, and improved lighting. Surveys conducted six months post-implementation revealed a 25% increase in job satisfaction, a 20% reduction in reported stress levels, and a 15% increase in overall productivity. Additionally, the company experienced a 10% decrease in employee turnover rates.
Conclusion: Ergonomic workplace design offers substantial psychological benefits that significantly enhance organizational performance. By fostering a work environment that reduces stress, increases job satisfaction, and boosts motivation, manufacturers can cultivate a more engaged and productive workforce. These psychological advantages contribute to higher productivity, improved quality, reduced turnover, and a stronger organizational culture, ultimately driving the long-term success and competitiveness of the manufacturing enterprise.
7. How can manufacturers measure the effectiveness of ergonomic interventions, and what metrics should they use to evaluate success?
Answer:
Measuring the effectiveness of ergonomic interventions is essential for understanding their impact on worker health, productivity, and overall organizational performance. Manufacturers can employ a variety of quantitative and qualitative metrics to evaluate the success of ergonomic initiatives, ensuring that investments in ergonomics yield tangible benefits.
Key Metrics for Evaluating Ergonomic Interventions:
Reduction in Workplace Injuries and MSDs:
- How to Measure: Track the number and types of reported injuries and musculoskeletal disorders before and after implementing ergonomic interventions.
- Impact: A significant decrease in injury rates indicates the effectiveness of ergonomic measures in enhancing worker safety.
Absenteeism Rates:
- How to Measure: Monitor the number of workdays lost due to illness or injury over time.
- Impact: Reduced absenteeism suggests improved worker health and a safer work environment.
Employee Satisfaction and Well-Being:
- How to Measure: Conduct regular employee surveys and feedback sessions to assess job satisfaction, comfort, and perceived well-being.
- Impact: High levels of satisfaction and well-being reflect successful ergonomic improvements and positive worker experiences.
Productivity and Efficiency:
- How to Measure: Analyze production metrics such as output rates, cycle times, and task completion times.
- Impact: Increases in productivity and efficiency indicate that ergonomic interventions are facilitating more effective work processes.
Error Rates and Defect Rates:
- How to Measure: Track the frequency of errors, defects, and rework required in production processes.
- Impact: A reduction in error and defect rates signifies enhanced precision and quality, likely resulting from ergonomic optimizations.
Employee Morale and Engagement:
- How to Measure: Use employee engagement surveys and observe indicators such as participation in safety programs and voluntary feedback initiatives.
- Impact: Higher morale and engagement levels demonstrate that ergonomic efforts are fostering a positive and supportive work culture.
Cost Savings:
- How to Measure: Calculate reductions in costs associated with workplace injuries, absenteeism, medical expenses, and worker compensation claims.
- Impact: Cost savings validate the financial benefits of ergonomic investments and support the business case for continued ergonomic initiatives.
Compliance with Safety Standards:
- How to Measure: Assess adherence to occupational safety and health regulations and ergonomic standards (e.g., OSHA, ISO 45001).
- Impact: High compliance rates indicate that ergonomic interventions meet regulatory requirements and industry best practices.
Worker Retention Rates:
- How to Measure: Monitor turnover rates and the reasons for employee departures.
- Impact: Improved retention rates suggest that ergonomic improvements contribute to a more satisfying and sustainable work environment.
Time to Recover from Injuries:
- How to Measure: Track the average time it takes for injured workers to return to work.
- Impact: Shorter recovery times indicate effective ergonomic interventions that support faster healing and reintegration.
Methods for Measuring Effectiveness:
Pre- and Post-Intervention Studies:
- How: Compare key metrics before and after the implementation of ergonomic interventions.
- Impact: Provides direct evidence of the changes and improvements resulting from ergonomic efforts.
Longitudinal Tracking:
- How: Continuously monitor metrics over an extended period to assess the sustained impact of ergonomic interventions.
- Impact: Identifies long-term benefits and ensures that improvements are maintained over time.
Benchmarking:
- How: Compare ergonomic metrics against industry standards or best practices.
- Impact: Helps determine where the organization stands relative to peers and identifies areas for further improvement.
Cost-Benefit Analysis:
- How: Analyze the costs associated with ergonomic interventions against the financial benefits realized through improved metrics.
- Impact: Demonstrates the return on investment (ROI) for ergonomic programs, supporting continued funding and expansion.
Worker Feedback and Participation:
- How: Engage workers in providing feedback on ergonomic changes and their effectiveness.
- Impact: Ensures that interventions are meeting the actual needs of workers and fosters a collaborative approach to ergonomic improvements.
Case Example: A manufacturing facility implemented ergonomic workstations with adjustable heights and ergonomic tools. Over the following year, they observed a 40% reduction in back injury claims, a 15% increase in productivity, and a 25% improvement in employee satisfaction scores. Additionally, the company saved approximately $200,000 in medical and compensation costs, demonstrating the effectiveness of their ergonomic interventions.
Conclusion: Measuring the effectiveness of ergonomic interventions requires a comprehensive approach that incorporates both quantitative and qualitative metrics. By tracking reductions in injuries, increases in productivity, improvements in employee satisfaction, and cost savings, manufacturers can evaluate the success of their ergonomic programs. These metrics not only validate the benefits of ergonomic investments but also guide continuous improvement efforts, ensuring that manufacturing operations remain safe, efficient, and worker-friendly.
8. How can the principles of participatory ergonomics be applied in manufacturing to enhance worker involvement and improve ergonomic outcomes?
Answer:
Participatory ergonomics involves actively engaging workers in the identification, analysis, and solution development of ergonomic issues within the workplace. By fostering collaboration between workers and ergonomics professionals, manufacturers can enhance worker involvement, ensure that ergonomic interventions are practical and relevant, and achieve better ergonomic outcomes.
Key Principles of Participatory Ergonomics:
Worker Involvement:
- How: Involve workers at all levels in the ergonomic assessment and intervention processes.
- Impact: Ensures that interventions are grounded in the actual experiences and needs of the workforce, increasing their effectiveness and acceptance.
Collaborative Problem-Solving:
- How: Facilitate joint problem-solving sessions where workers and ergonomists collaborate to identify ergonomic challenges and develop solutions.
- Impact: Leverages diverse perspectives and expertise, leading to more comprehensive and innovative solutions.
Empowerment and Ownership:
- How: Empower workers to take an active role in designing and implementing ergonomic improvements.
- Impact: Fosters a sense of ownership and accountability, encouraging sustained participation and adherence to ergonomic practices.
Open Communication:
- How: Establish clear and open channels for communication between workers, supervisors, and ergonomics teams.
- Impact: Enhances the flow of information, facilitates the sharing of insights, and ensures that ergonomic initiatives are aligned with worker needs.
Training and Education:
- How: Provide training to workers on ergonomic principles, safe work practices, and the importance of their involvement in ergonomic initiatives.
- Impact: Equips workers with the knowledge and skills to identify ergonomic issues and contribute effectively to solution development.
Application of Participatory Ergonomics in Manufacturing:
Ergonomic Committees and Teams:
- How: Form ergonomic committees that include representatives from different departments and levels of the organization.
- Impact: Ensures diverse input and fosters a collaborative approach to addressing ergonomic challenges.
Workshops and Focus Groups:
- How: Conduct workshops and focus groups where workers can discuss ergonomic issues, share experiences, and brainstorm solutions.
- Impact: Encourages active participation and generates practical ideas tailored to the specific work environment.
Surveys and Feedback Mechanisms:
- How: Implement regular surveys and feedback systems to gather input from workers on ergonomic concerns and suggestions for improvement.
- Impact: Provides ongoing insights into ergonomic issues and allows for timely adjustments to interventions.
Pilot Testing of Ergonomic Solutions:
- How: Involve workers in the pilot testing of proposed ergonomic solutions to evaluate their effectiveness and gather feedback.
- Impact: Ensures that solutions are feasible, effective, and well-received before full-scale implementation.
Recognition and Incentives:
- How: Recognize and reward workers who actively contribute to ergonomic initiatives and suggest valuable improvements.
- Impact: Motivates continued participation and reinforces the importance of ergonomic practices.
Benefits of Participatory Ergonomics:
Enhanced Effectiveness of Interventions:
- Impact: Solutions developed with worker input are more likely to address actual needs and be implemented successfully.
Increased Worker Satisfaction and Morale:
- Impact: Involving workers in decision-making fosters a sense of respect and value, enhancing overall job satisfaction and morale.
Improved Safety and Health Outcomes:
- Impact: Effective ergonomic interventions reduce the risk of injuries and improve worker health, leading to a safer work environment.
Greater Ownership and Compliance:
- Impact: Workers who participate in ergonomic initiatives are more likely to adhere to ergonomic practices, ensuring sustained improvements.
Cost Savings and Productivity Gains:
- Impact: Effective ergonomic interventions lead to reduced injury-related costs, increased productivity, and enhanced operational efficiency.
Case Example: A textile manufacturing company implemented a participatory ergonomics program by forming ergonomic committees that included frontline workers. Through collaborative workshops, they identified repetitive strain as a major issue and developed a task rotation system to mitigate it. As a result, they saw a 35% reduction in RSI cases, a 20% increase in productivity, and improved worker morale and engagement.
Conclusion: Participatory ergonomics is a powerful approach that leverages worker involvement to enhance ergonomic outcomes in manufacturing. By fostering collaboration, empowering workers, and incorporating their insights into ergonomic interventions, manufacturers can create safer, more efficient, and more satisfying work environments. This collaborative approach not only improves worker health and productivity but also strengthens organizational culture and performance.
9. How can the integration of technology, such as wearable devices and real-time monitoring systems, enhance ergonomic practices in manufacturing?
Answer:
Integrating technology, including wearable devices and real-time monitoring systems, significantly enhances ergonomic practices in manufacturing by providing continuous data on worker movements, postures, and environmental conditions. These technologies enable proactive identification of ergonomic risks, facilitate timely interventions, and support data-driven decision-making to optimize workplace ergonomics.
Key Technologies and Their Applications:
Wearable Ergonomic Devices:
- Examples: Smart gloves, exoskeletons, fitness trackers, and posture sensors.
- How They Enhance Ergonomics:
- Real-Time Posture Monitoring: Wearable sensors track workers’ postures and movements, providing instant feedback on awkward positions or excessive strain.
- Fatigue Detection: Fitness trackers monitor physiological indicators such as heart rate variability and activity levels to assess worker fatigue and suggest breaks when needed.
- Assisted Lifting: Exoskeletons support workers during lifting tasks, reducing the physical effort required and minimizing the risk of back injuries.
Real-Time Monitoring Systems:
- Examples: Motion capture systems, environmental sensors, and IoT-enabled equipment.
- How They Enhance Ergonomics:
- Continuous Data Collection: Monitor worker movements, task durations, and environmental factors like lighting and temperature to identify ergonomic risks.
- Predictive Analytics: Analyze collected data to predict potential ergonomic issues and schedule preventive maintenance or adjustments before problems arise.
- Automated Alerts: Trigger alerts when workers adopt unsafe postures or when environmental conditions become unfavorable, allowing for immediate corrective actions.
Human-Machine Interfaces (HMIs):
- Examples: Touchscreen panels, voice-activated controls, and augmented reality (AR) interfaces.
- How They Enhance Ergonomics:
- Intuitive Controls: Simplify interactions with machinery, reducing cognitive load and the risk of errors.
- Ergonomic Design: Design interfaces that align with natural human movements and cognitive processes, enhancing usability and reducing strain.
Virtual Reality (VR) and Augmented Reality (AR):
- Examples: VR-based ergonomic training programs and AR-assisted maintenance guides.
- How They Enhance Ergonomics:
- Immersive Training: Provide realistic training environments where workers can practice ergonomic practices without physical strain.
- Assisted Operations: Overlay digital information onto the physical workspace to guide workers in maintaining ergonomic postures and using tools correctly.
Benefits of Integrating Technology into Ergonomic Practices:
Proactive Risk Identification:
- Impact: Enables early detection of ergonomic issues, allowing for timely interventions before injuries occur.
Data-Driven Decision Making:
- Impact: Provides empirical evidence to support ergonomic improvements, ensuring that interventions are targeted and effective.
Enhanced Worker Awareness:
- Impact: Real-time feedback and alerts increase workers’ awareness of their ergonomic practices, encouraging self-correction and healthier habits.
Improved Safety and Health Outcomes:
- Impact: Reduces the incidence of workplace injuries and musculoskeletal disorders, leading to a healthier workforce.
Increased Productivity:
- Impact: Optimized ergonomic conditions enhance worker comfort and efficiency, resulting in higher productivity levels.
Cost Savings:
- Impact: Minimizes costs associated with workplace injuries, absenteeism, and worker compensation claims.
Case Example: A manufacturing plant implemented wearable posture sensors and real-time monitoring systems to track workers’ postures and movements during assembly tasks. The data collected revealed that workers frequently adopted awkward postures during specific tasks, leading to targeted ergonomic interventions such as workstation adjustments and the introduction of assistive devices. As a result, the plant experienced a 40% reduction in back injury claims and a 15% increase in assembly line productivity.
Challenges and Considerations:
Data Privacy and Security:
- Consideration: Ensure that data collected from wearable devices and monitoring systems are securely stored and used ethically, respecting worker privacy.
Worker Acceptance:
- Consideration: Engage workers in the implementation process, addressing concerns about surveillance and emphasizing the benefits for their health and safety.
Cost of Implementation:
- Consideration: Evaluate the return on investment (ROI) for ergonomic technologies and consider phased or pilot implementations to manage costs.
Integration with Existing Systems:
- Consideration: Ensure that new ergonomic technologies seamlessly integrate with current manufacturing systems and workflows.
Conclusion: The integration of technology, such as wearable devices and real-time monitoring systems, significantly enhances ergonomic practices in manufacturing by providing continuous data, enabling proactive risk management, and supporting data-driven decision-making. These technological advancements lead to safer, more comfortable, and more efficient work environments, ultimately improving worker health, productivity, and organizational performance. By addressing challenges related to privacy, acceptance, and integration, manufacturers can effectively leverage technology to optimize ergonomics and achieve sustainable operational excellence.
10. What strategies can manufacturers employ to maintain ergonomic standards in dynamic manufacturing environments where processes and equipment are frequently changing?
Answer:
Maintaining ergonomic standards in dynamic manufacturing environments, where processes and equipment are frequently changing, requires a proactive and adaptable approach. Manufacturers can employ several strategies to ensure that ergonomic principles are consistently upheld, even amidst continuous change.
Key Strategies for Maintaining Ergonomic Standards:
Continuous Ergonomic Assessments:
- How: Regularly conduct ergonomic assessments whenever there are changes in processes, equipment, or workstations.
- Impact: Ensures that ergonomic standards are maintained and that new changes do not introduce ergonomic risks.
Flexible and Adjustable Workstations:
- How: Design workstations with adjustable features such as height-adjustable tables, modular components, and adaptable tooling.
- Impact: Allows workstations to be quickly reconfigured to accommodate different tasks and worker needs, maintaining ergonomic alignment despite changes.
Standardized Ergonomic Guidelines:
- How: Develop and implement standardized ergonomic guidelines and protocols that apply to all processes and equipment.
- Impact: Provides a consistent framework for ergonomic practices, ensuring that all changes adhere to established ergonomic principles.
Training and Education Programs:
- How: Offer ongoing training for workers and supervisors on ergonomic best practices and how to adapt to changes in the work environment.
- Impact: Equips the workforce with the knowledge and skills to identify and address ergonomic issues, fostering a culture of safety and adaptability.
Involvement of Ergonomics Professionals:
- How: Engage ergonomists or HF&E specialists in the planning and implementation of process and equipment changes.
- Impact: Ensures that ergonomic considerations are integrated into the design and deployment of new systems, preventing the introduction of ergonomic risks.
Use of Technology for Ergonomic Monitoring:
- How: Implement real-time monitoring systems and wearable devices to track ergonomic metrics continuously.
- Impact: Provides ongoing data to identify and address ergonomic issues promptly, even as the manufacturing environment evolves.
Participatory Ergonomics:
- How: Involve workers in the ergonomic assessment and redesign process, especially during transitions or changes.
- Impact: Leverages worker insights and fosters ownership of ergonomic practices, ensuring that changes are practical and effective.
Standard Operating Procedures (SOPs):
- How: Develop SOPs that include ergonomic considerations for all tasks and equipment operations.
- Impact: Provides clear instructions on maintaining ergonomic practices, reducing the likelihood of errors and injuries.
Regular Feedback and Improvement Loops:
- How: Establish mechanisms for workers to provide feedback on ergonomic conditions and suggest improvements.
- Impact: Facilitates continuous improvement and ensures that ergonomic standards evolve in response to real-world challenges and changes.
Ergonomic Audits and Certifications:
- How: Conduct periodic ergonomic audits and seek certifications (e.g., ISO 45001) to validate and enhance ergonomic standards.
- Impact: Demonstrates a commitment to maintaining high ergonomic standards and provides external validation of ergonomic practices.
Benefits of These Strategies:
Adaptability:
- Impact: Ensures that ergonomic standards are maintained despite changes, promoting a resilient and adaptable workforce.
Sustained Worker Health and Safety:
- Impact: Reduces the risk of injuries and promotes long-term health and well-being of workers.
Enhanced Productivity:
- Impact: Ergonomic work environments support efficient workflows, reducing downtime and increasing overall productivity.
Improved Employee Morale and Satisfaction:
- Impact: A commitment to ergonomics fosters a positive work environment, enhancing job satisfaction and worker retention.
Compliance with Regulations:
- Impact: Maintains adherence to occupational safety and health regulations, avoiding legal penalties and enhancing organizational reputation.
Case Example: A high-tech electronics manufacturer implemented flexible ergonomic workstations equipped with adjustable heights and modular components. Whenever a new production line was introduced, ergonomists conducted assessments and adjusted workstations accordingly. Additionally, the company provided regular training on ergonomic practices and utilized wearable posture sensors to monitor worker movements. As a result, they maintained low injury rates, high worker satisfaction, and sustained productivity levels despite frequent changes in production processes and equipment.
Conclusion: In dynamic manufacturing environments, maintaining ergonomic standards requires a proactive, flexible, and collaborative approach. By integrating continuous assessments, flexible workstation designs, standardized guidelines, ongoing training, and leveraging technology, manufacturers can ensure that ergonomic principles are consistently applied, enhancing worker health, safety, and overall organizational performance. These strategies enable manufacturers to adapt seamlessly to changes while upholding high ergonomic standards, fostering a sustainable and efficient manufacturing operation.
11. How can ergonomic principles be integrated into the design of manufacturing tools and equipment to enhance usability and reduce strain on workers?
Answer:
Integrating ergonomic principles into the design of manufacturing tools and equipment is essential for enhancing usability, reducing physical strain on workers, and improving overall efficiency. Ergonomic design focuses on creating tools and equipment that fit the user’s needs, capabilities, and limitations, thereby promoting comfort, safety, and productivity.
Key Ergonomic Principles for Tool and Equipment Design:
Anthropometric Considerations:
- How: Design tools and equipment to accommodate a wide range of body sizes, shapes, and strengths.
- Impact: Ensures that tools are comfortable and easy to use for all workers, reducing the risk of strain and injury.
Neutral Postures:
- How: Design tools that allow workers to maintain neutral body postures, avoiding excessive bending, twisting, or reaching.
- Impact: Minimizes musculoskeletal strain and fatigue, enhancing worker comfort and endurance.
Minimize Force Requirements:
- How: Design tools that require minimal force to operate, using lightweight materials and efficient mechanisms.
- Impact: Reduces the physical effort required by workers, decreasing muscle fatigue and the risk of overexertion injuries.
Enhance Grip Comfort and Control:
- How: Incorporate ergonomic grips with contoured shapes, soft materials, and appropriate sizes to fit the hand naturally.
- Impact: Improves control and precision in tool use, reducing the likelihood of slips and errors while enhancing worker comfort.
Balanced Weight Distribution:
- How: Ensure that tools and equipment have balanced weight distribution to reduce the physical strain on specific body parts.
- Impact: Enhances ease of handling, reducing fatigue and improving task performance.
Adjustable Features:
- How: Include adjustable components such as handle angles, tool heights, and extension lengths to customize tools for different tasks and user preferences.
- Impact: Increases versatility and adaptability, allowing workers to optimize tool use for various tasks and reduce ergonomic risks.
Vibration and Noise Reduction:
- How: Design tools with vibration-dampening materials and noise-reducing features to minimize exposure to harmful vibrations and excessive noise.
- Impact: Protects workers from vibration-induced injuries and reduces noise-related stress, enhancing overall comfort and safety.
Intuitive Design:
- How: Create tools and equipment with intuitive controls and interfaces that align with natural human movements and cognitive processes.
- Impact: Simplifies tool operation, reducing the learning curve and minimizing the risk of user errors.
Durability and Maintenance:
- How: Design tools and equipment for easy maintenance and durability, ensuring that they remain in optimal condition with minimal effort.
- Impact: Enhances tool longevity and reliability, reducing downtime and maintenance-related strain on workers.
Safety Features:
- How: Integrate safety mechanisms such as guards, automatic shut-offs, and emergency stops into tool and equipment designs.
- Impact: Protects workers from accidental injuries and ensures safe operation of tools and equipment.
Examples of Ergonomic Tool and Equipment Design:
Ergonomic Hand Tools:
- Example: Screwdrivers with soft, cushioned grips and balanced weights reduce hand fatigue and improve precision in assembly tasks.
Adjustable Assembly Tables:
- Example: Height-adjustable tables allow workers to switch between sitting and standing positions, promoting neutral postures and reducing back strain.
Robotic Exoskeletons:
- Example: Wearable exoskeletons assist workers in lifting heavy objects, reducing the physical effort required and minimizing the risk of back injuries.
Anti-Vibration Gloves:
- Example: Gloves designed to absorb and dampen vibrations from power tools protect workers from vibration-induced injuries and enhance grip comfort.
Automated Material Handling Systems:
- Example: Conveyor belts and robotic arms handle repetitive or heavy lifting tasks, reducing the physical demands on human workers and enhancing efficiency.
Benefits of Integrating Ergonomic Principles:
Enhanced Usability:
- Impact: Tools and equipment that are easy and comfortable to use improve task performance and reduce the likelihood of user errors.
Reduced Physical Strain:
- Impact: Ergonomically designed tools minimize muscle fatigue and strain, promoting worker health and longevity.
Increased Productivity:
- Impact: Comfortable and efficient tools enable workers to perform tasks more quickly and accurately, boosting overall productivity.
Improved Worker Satisfaction:
- Impact: Ergonomic tools contribute to a more satisfying work experience, enhancing job satisfaction and reducing turnover rates.
Lower Injury Rates:
- Impact: Reduced physical strain and enhanced safety features decrease the risk of workplace injuries, leading to a healthier workforce.
Case Example: A manufacturing company redesigned its assembly line tools by incorporating ergonomic grips and lightweight materials into hand tools. Additionally, they introduced adjustable workstations to allow workers to maintain neutral postures during assembly tasks. Following these changes, the company reported a 30% reduction in hand and wrist injuries, a 20% increase in assembly speed, and higher worker satisfaction scores.
Conclusion: Integrating ergonomic principles into the design of manufacturing tools and equipment is essential for enhancing usability, reducing physical strain, and improving overall worker well-being and productivity. By focusing on user-centered design, manufacturers can create tools and equipment that support healthy and efficient work practices, leading to safer, more productive, and more satisfying manufacturing environments.
12. How can manufacturers foster a culture of ergonomics and safety that encourages continuous improvement and worker participation in ergonomic initiatives?
Answer:
Fostering a culture of ergonomics and safety within manufacturing organizations is essential for ensuring the sustained success of ergonomic initiatives and promoting a healthy, engaged workforce. A strong ergonomic culture emphasizes the importance of worker well-being, encourages active participation, and supports continuous improvement through collaborative efforts.
Key Strategies to Foster an Ergonomic and Safety Culture:
Leadership Commitment:
- How: Ensure that organizational leaders prioritize ergonomics and safety by visibly supporting ergonomic initiatives, allocating resources, and setting clear expectations.
- Impact: Demonstrates the organization’s dedication to worker health and safety, inspiring employees to follow suit and take ergonomics seriously.
Employee Involvement and Participation:
- How: Involve workers in ergonomic assessments, decision-making, and the development of ergonomic solutions.
- Impact: Empowers employees, fosters a sense of ownership, and ensures that ergonomic initiatives are practical and aligned with actual work conditions.
Comprehensive Training Programs:
- How: Provide ongoing training on ergonomic principles, safe work practices, and the proper use of ergonomic tools and equipment.
- Impact: Equips workers with the knowledge and skills to maintain ergonomic standards and proactively identify and address ergonomic issues.
Effective Communication:
- How: Establish open communication channels for discussing ergonomic and safety concerns, sharing best practices, and providing feedback.
- Impact: Enhances transparency, builds trust, and encourages continuous dialogue on ergonomics and safety matters.
Regular Ergonomic Assessments and Audits:
- How: Conduct periodic ergonomic assessments and safety audits to identify potential risks and evaluate the effectiveness of ergonomic interventions.
- Impact: Ensures that ergonomic standards are consistently maintained and that improvements are based on current data and worker feedback.
Recognition and Incentive Programs:
- How: Implement programs that recognize and reward workers who contribute to ergonomic improvements or demonstrate exemplary safety practices.
- Impact: Motivates employees to actively participate in ergonomic initiatives and reinforces the importance of ergonomics and safety within the organization.
Integration of Ergonomics into Standard Operating Procedures (SOPs):
- How: Incorporate ergonomic guidelines and safety protocols into all SOPs and work instructions.
- Impact: Ensures that ergonomic practices are embedded into daily operations, promoting consistent adherence to ergonomic standards.
Utilization of Technology and Tools:
- How: Leverage ergonomic tools and technologies, such as wearable devices and real-time monitoring systems, to support ergonomic practices.
- Impact: Enhances the ability to monitor ergonomic conditions, gather data, and implement timely interventions, fostering a proactive approach to ergonomics.
Continuous Improvement Mindset:
- How: Encourage a culture of continuous improvement where ergonomic practices are regularly reviewed, refined, and updated based on new insights and technological advancements.
- Impact: Keeps ergonomic initiatives relevant and effective, ensuring ongoing enhancements to worker health and safety.
Building a Supportive Environment:
- How: Create a work environment that supports ergonomic practices by providing comfortable break areas, promoting regular breaks, and ensuring access to ergonomic resources.
- Impact: Enhances overall worker well-being, reducing fatigue and stress, and promoting a healthier, more productive workforce.
Benefits of Fostering an Ergonomic and Safety Culture:
Reduced Injury Rates:
- Impact: A strong ergonomic culture leads to fewer workplace injuries, lowering medical costs and improving worker health.
Increased Productivity:
- Impact: Ergonomically optimized work environments enhance efficiency and reduce downtime caused by injuries and discomfort.
Enhanced Worker Morale and Satisfaction:
- Impact: Workers feel valued and supported, leading to higher job satisfaction, increased motivation, and better retention rates.
Improved Quality and Consistency:
- Impact: Reduced errors and defects due to improved worker comfort and focus, leading to higher product quality and customer satisfaction.
Compliance and Risk Management:
- Impact: Ensures adherence to occupational safety and health regulations, minimizing legal risks and enhancing organizational reputation.
Cost Savings:
- Impact: Lower costs associated with workplace injuries, absenteeism, and worker turnover contribute to improved financial performance.
Case Example: A manufacturing company implemented a comprehensive ergonomic and safety culture by establishing ergonomic committees, providing regular training, and recognizing employee contributions to safety improvements. They also integrated ergonomic principles into all SOPs and utilized real-time monitoring systems to track ergonomic risks. Over two years, the company saw a 50% reduction in workplace injuries, a 25% increase in productivity, and a significant improvement in employee satisfaction scores.
Conclusion: Fostering a culture of ergonomics and safety in manufacturing involves leadership commitment, active worker participation, comprehensive training, effective communication, and continuous improvement. By embedding ergonomic principles into the organizational fabric and promoting a supportive and collaborative environment, manufacturers can enhance worker health, safety, and satisfaction. This, in turn, leads to improved productivity, higher quality outputs, and sustained organizational success. A strong ergonomic and safety culture not only protects workers but also drives the overall performance and competitiveness of the manufacturing enterprise.
Conclusion:
The above thought-provoking questions and detailed answers provide a comprehensive exploration of human factors and ergonomics in manufacturing. Covering essential topics such as injury reduction, ergonomic assessments, material handling optimization, cognitive ergonomics, workstation design, psychological benefits, measurement of ergonomic effectiveness, participatory ergonomics, technological integration, maintaining ergonomic standards, tool and equipment design, and fostering an ergonomic and safety culture, these questions facilitate a deep understanding of how ergonomics can enhance workplace safety, productivity, and worker well-being. Engaging with these questions equips students and professionals with the knowledge to implement effective ergonomic practices, create healthier work environments, and contribute to the overall success and sustainability of manufacturing operations.