Energy and Resource Efficiency in Manufacturing
Energy and resource efficiency in manufacturing has become an essential pillar of sustainable industrial development. With the dual pressures of environmental responsibility and economic competitiveness, today’s manufacturing systems are evolving rapidly to reduce waste, optimize inputs, and minimize emissions. This shift is tightly connected with broader advances in Industrial and Manufacturing Technologies, where integration of digital tools, lean practices, and system redesign is transforming both production and resource use.
The implementation of Sustainable Manufacturing strategies is central to this transformation, aiming for high performance with minimal environmental impact. Technologies such as Smart Manufacturing and Industry 4.0 and Digital Twin Technology allow factories to simulate operations, monitor real-time data, and make energy-aware decisions dynamically. These capabilities are enhanced when combined with Computer-Integrated Manufacturing (CIM) platforms that synchronize energy management with production scheduling.
Improvements in material utilization are being driven by innovations in Additive Manufacturing (3D Printing) and Advanced Materials and Manufacturing Technologies. These methods support localized production, complex part optimization, and material recovery—all of which contribute to energy savings across the supply chain. Their effectiveness is further enhanced by robust Manufacturing Quality Control and Assurance processes that reduce defects and prevent resource loss.
Efficient energy use is also enabled through intelligent automation. Integration with Industrial Automation and Robotics and careful attention to Human Factors and Ergonomics in Manufacturing ensure that energy is spent effectively in both human and machine activity. By adopting Lean Manufacturing principles, operations are further streamlined to eliminate inefficiencies that drain energy or consume excess resources.
Systems-level efficiency is also shaped by strategic Supply Chain Management. From sourcing to logistics, each decision can impact total energy consumption. Digital coordination across the production network leads to better-informed procurement and transportation choices that support sustainable goals. These logistics are tightly coupled with disciplines such as Manufacturing and Production Engineering and Mechanical Design and CAD, which define the geometry and material flows of production.
Energy efficiency efforts must be grounded in sound physical science. Knowledge from Thermodynamics and Heat Transfer, Fluid Mechanics and Hydraulics, and Solid Mechanics underpins the thermal and mechanical systems being optimized. The intelligent application of these principles is seen in sectors like Automotive Engineering and Biomechanical Engineering, where efficiency is key to performance and sustainability.
A holistic energy strategy must also consider systems control, as taught in Control Systems in Mech Engineering. These systems maintain process balance and avoid unnecessary energy expenditure. Likewise, nanotechnology innovations—explored in Nanotechnology and Advanced Materials in Mech Eng—enable advanced coatings and materials that improve thermal regulation and energy retention in equipment.
Finally, these strategies are brought to life by people and technologies working together. In the context of Robotics and Automation in Mech Eng and systems-wide digital design integration, engineers are empowered to transform vision into scalable, efficient reality. The field continues to evolve with every development in Mechanical Engineering, bridging tradition and transformation in pursuit of a more sustainable industrial future.
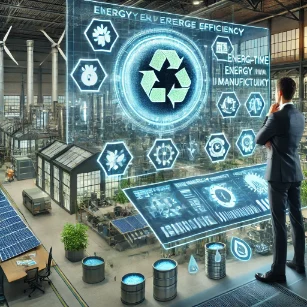
Table of Contents
Core Concepts in Energy and Resource Efficiency
Energy Efficiency
- Definition:
- Using less energy to achieve the same output, thereby reducing energy waste. This principle involves optimizing systems, technologies, and behaviors to minimize energy input without compromising productivity.
- Goals:
- Lowering energy costs by decreasing consumption across industrial processes, lighting, HVAC systems, and machinery.
- Reducing greenhouse gas (GHG) emissions, which directly contributes to climate change mitigation and compliance with global climate agreements.
- Enhancing operational efficiency by streamlining processes, minimizing idle energy use, and incorporating smart energy management systems that adjust to load and demand.
- Examples:
- Upgrading to energy-efficient motors and lighting systems like LED bulbs and high-efficiency HVAC units, as well as retrofitting older buildings with energy-smart insulation and control systems.
- Deploying variable frequency drives (VFDs) in motor operations to reduce unnecessary energy use during low-load periods.
- Implementing real-time energy monitoring platforms to identify inefficiencies and optimize energy use dynamically.
Resource Efficiency
- Definition:
- Maximizing the value extracted from raw materials while minimizing waste and losses. It encourages designing systems where each material is used for its full potential before being discarded or repurposed.
- Goals:
- Extending the lifecycle of materials by promoting reuse, refurbishment, and remanufacturing practices.
- Reducing reliance on virgin resources through the use of secondary raw materials and closed-loop systems.
- Enhancing recyclability of components and packaging by selecting materials that can be easily separated, sorted, and repurposed at end-of-life.
- Examples:
- Using lightweight materials in automotive manufacturing to reduce resource consumption while improving fuel efficiency and lowering emissions.
- Designing modular products that facilitate repair and component replacement rather than full disposal.
- Adopting water-efficient production processes and recovering waste heat in thermal systems.
Sustainable Manufacturing Practices
- Definition:
- Production methods that minimize environmental impacts and ensure sustainable resource use, aligning with long-term ecological balance and economic viability.
- Goals:
- Reduce pollution and waste through cleaner production techniques, closed-loop systems, and real-time environmental monitoring.
- Promote circular economy principles such as product lifecycle extension, reuse of industrial byproducts, and regenerative design.
- Adopt renewable energy and green technologies that reduce fossil fuel dependency and harmful emissions. For example, as detailed by the U.S. Department of Energy’s Advanced Manufacturing Office, clean energy initiatives are transforming industrial sectors through innovation.
Circular Economy Integration
- Definition:
- Designing processes and products to minimize waste and enable reuse, recycling, and regeneration of resources. This strategy challenges the traditional linear model of “take-make-dispose.”
- Applications:
- Using recycled plastics to manufacture new consumer goods while reducing environmental burdens from virgin plastic production.
- Designing products for disassembly and material recovery, allowing manufacturers to retrieve high-value components at end-of-life and reduce dependency on new material inputs.
- Creating reverse logistics systems to collect used goods for reintegration into the production cycle.
Renewable Energy Integration
- Definition:
- Incorporating renewable energy sources like solar, wind, and biomass into manufacturing operations to decarbonize production and improve energy security.
- Benefits:
- Reduces dependence on fossil fuels and exposure to volatile energy markets.
- Cuts operational carbon emissions significantly, supporting sustainability goals and corporate social responsibility targets.
- Examples:
- Solar panels powering manufacturing facilities and supplementing grid electricity, especially during peak demand hours.
- Biomass boilers providing heat for industrial processes using organic waste as a fuel source, creating closed-loop systems and reducing landfill use.
- Wind turbines deployed on industrial campuses to support direct consumption of clean electricity and feed surplus energy into the grid.
Strategies for Energy and Resource Efficiency in Manufacturing
Energy Management Systems (EnMS)
- Definition:
- Frameworks for systematically improving energy efficiency in manufacturing, such as ISO 50001. These systems encourage a structured approach to identifying inefficiencies, setting performance goals, and measuring progress toward those objectives on a continual basis.
- Key Components:
- Energy Audits: Identify areas of energy waste by analyzing equipment, building insulation, and utility bills to pinpoint underperforming systems.
- Performance Monitoring: Use IoT sensors to track energy usage in real-time, providing a data-rich environment for better decision-making.
- Target Setting: Establish goals for energy reduction based on benchmarking and predictive modeling techniques that align with corporate sustainability strategies.
- Example:
- A factory reducing energy consumption by optimizing HVAC systems and production schedules, resulting in decreased utility costs and improved air quality control.
Process Optimization
- Definition:
- Refining manufacturing processes to minimize resource and energy use while maximizing productivity. This involves analyzing workflows, identifying inefficiencies, and applying corrective strategies.
- Techniques:
- Implementing Lean Manufacturing principles to reduce waste by eliminating non-value-adding activities.
- Using advanced control systems and real-time analytics to ensure process precision and reduce variability.
- Example:
- A chemical plant optimizing reaction temperatures and pressures to save energy while improving reaction yields and product consistency.
Waste Heat Recovery
- Definition:
- Capturing and reusing heat generated during industrial processes to reduce overall energy demand and enhance process efficiency.
- Applications:
- Preheating raw materials using exhaust heat from combustion systems, which reduces fuel consumption.
- Generating electricity from waste heat in power plants using Organic Rankine Cycle systems or thermoelectric converters.
- Example:
- A steel mill using waste heat recovery systems to power auxiliary equipment like cranes and conveyors, contributing to reduced operating costs and emissions.
Material Efficiency
- Definition:
- Reducing material waste by improving design, production, and recycling practices to achieve more with fewer inputs.
- Techniques:
- Using high-precision cutting tools and CNC machining to minimize scrap and improve dimensional accuracy.
- Designing products with fewer components or modular parts to reduce material complexity and facilitate disassembly and recycling.
- Example:
- Lightweighting in automotive manufacturing to reduce metal consumption, improve fuel efficiency, and lower emissions during the vehicle’s lifecycle.
Water Conservation and Recycling
- Definition:
- Reducing water usage and recycling wastewater in manufacturing processes to preserve freshwater resources and cut utility costs.
- Techniques:
- Installing closed-loop water systems to reuse cooling water, especially in heat-intensive industries such as steel and chemicals.
- Treating and reusing greywater for non-potable purposes such as floor washing, landscaping, or toilet flushing.
- Example:
- A semiconductor plant reusing treated wastewater for cleaning operations, reducing the demand for freshwater intake and improving environmental compliance. For additional insights into sustainable water management, the EPA’s Sustainable Management of Water page offers practical strategies for industries.
Renewable Energy Adoption
- Definition:
- Powering manufacturing operations with renewable energy sources such as solar, wind, geothermal, or biomass to reduce dependence on fossil fuels and meet carbon neutrality goals.
- Applications:
- Installing rooftop solar panels for energy-intensive facilities to offset daytime energy usage with clean electricity.
- Using wind energy to power heavy machinery or storage systems during periods of high demand.
- Example:
- A textile factory running on solar and wind energy to reduce its carbon footprint and earn sustainability certifications that boost brand reputation.
Digital Twin Technology
- Definition:
- Creating virtual replicas of physical systems to simulate and optimize energy and resource use, allowing for proactive decision-making and performance forecasting.
- Applications:
- Predicting energy savings from process changes by running simulations of modified production setups.
- Simulating resource flows, temperature control, and equipment lifecycles to identify inefficiencies and potential improvements.
- Example:
- A factory using digital twins to test energy-efficient production schedules, adjust runtime variables, and align maintenance windows with energy-saving opportunities.
Automation and Robotics
- Definition:
- Automating repetitive tasks to enhance precision and reduce resource waste, thereby increasing consistency, safety, and scalability in manufacturing operations.
- Applications:
- Robots in assembly lines to minimize material errors, improve repeatability, and eliminate human fatigue-related defects.
- Automated quality control systems using vision sensors and AI algorithms to identify flawed components and reduce defective product rates.
- Example:
- A robotic arm ensuring precise application of adhesives, reducing waste and improving product reliability across multiple shifts with minimal supervision.
Technologies Supporting Energy and Resource Efficiency
IoT and Smart Sensors
- Role:
- Provide real-time data on energy consumption and resource usage, offering granular visibility into manufacturing systems and utilities.
- Applications:
- Monitoring machine performance to identify inefficiencies such as overuse of energy, leaks, or suboptimal operating conditions, enabling proactive adjustments.
- Example:
- IoT sensors tracking electricity usage in industrial machines to flag anomalies, schedule maintenance, and shut down idle equipment automatically during non-peak hours.
Artificial Intelligence (AI)
- Role:
- Analyze large datasets to identify patterns and optimize energy use, often through machine learning algorithms that adapt over time.
- Applications:
- Predictive analytics for energy demand forecasting, enabling companies to align consumption with supply in real time and participate in smart grid systems.
- Example:
- AI systems adjusting equipment operation during low energy demand periods to take advantage of lower utility rates and reduce overall energy bills, while still meeting production schedules efficiently.
Additive Manufacturing
- Role:
- Reduces material waste by building products layer by layer, unlike subtractive manufacturing methods which generate excess scrap material.
- Applications:
- Producing lightweight components for aerospace applications that improve fuel efficiency, reduce emissions, and minimize lifecycle environmental impact.
- Example:
- 3D printing prototypes to avoid waste from traditional machining, which often involves cutting away large amounts of material, particularly from high-value metals like titanium or aluminum.
Blockchain Technology
- Role:
- Enhances traceability and accountability in resource use by creating secure, tamper-proof records across supply chains and production processes.
- Applications:
- Verifying the sustainability of raw materials, documenting ethical sourcing, and ensuring compliance with environmental standards throughout procurement and production.
- Example:
- Blockchain tracking the origin of recycled materials to validate claims of eco-friendly product composition, support certifications, and build consumer trust. A related initiative can be explored through IBM’s blockchain supply chain solutions, which provide detailed frameworks for traceable and efficient resource management.
Renewable Energy Systems
- Role:
- Powering operations with clean, renewable energy, helping businesses reduce reliance on fossil fuels, meet decarbonization goals, and enhance energy resilience.
- Examples:
- Solar farms providing decentralized power for remote facilities, wind turbines driving mechanical or electrical systems in real-time, and geothermal energy systems offering consistent heating and cooling solutions with low emissions and high reliability.
Applications of Energy and Resource Efficiency in Industries
Automotive Manufacturing
- Energy Reduction:
- Using lightweight materials to improve fuel efficiency in vehicles while also reducing the energy required during manufacturing due to simpler handling and reduced processing demands.
- Renewable Energy Integration:
- Solar-powered manufacturing plants with rooftop panels, energy storage systems, and real-time energy management dashboards to ensure optimal energy usage throughout production cycles.
- Example:
- BMW’s energy-efficient paint shops using renewable energy and robotic systems to minimize water, electricity, and chemical usage during surface treatments, contributing to their corporate sustainability goals.
Food and Beverage Industry
- Water Conservation:
- Reusing water from cleaning processes through filtration, sterilization, and closed-loop systems to drastically lower total water withdrawal and discharge volumes.
- Energy Efficiency:
- Waste heat recovery in brewing and baking by capturing exhaust energy from ovens and boilers to preheat incoming water or air, reducing fuel consumption and operating costs.
- Example:
- Breweries capturing CO₂ emissions for reuse in carbonation, refrigeration, or as an input for fertilizer production, demonstrating circularity in emissions and resource usage. Further innovations are highlighted in UNIDO’s green brewing sector projects, showcasing global efforts in efficiency and emissions reduction.
Electronics Manufacturing
- Resource Optimization:
- Reducing rare earth material usage in components by redesigning products to utilize fewer critical minerals or integrating substitute materials with similar functionality but lower environmental impact.
- Waste Management:
- Recycling defective products and e-waste through disassembly, precious metal recovery, and circuit board reclamation to reduce landfill disposal and resource depletion.
- Example:
- Apple using recycled aluminum in device casings, sourcing material from its own product take-back programs, thereby reducing carbon emissions and mining dependencies.
Cement and Steel Industries
- Energy Efficiency:
- Using alternative fuels and waste heat recovery to lower the carbon footprint and energy demands of high-temperature processing operations like clinker and steel production.
- Material Recycling:
- Incorporating industrial byproducts like fly ash, slag, and construction debris to reduce reliance on virgin raw materials and enhance product performance in concrete and steel blends.
- Example:
- Steel plants using electric arc furnaces powered by renewable energy to melt scrap metal, achieving significant emission reductions compared to traditional blast furnaces and promoting circularity in materials.
Textile Industry
- Water Recycling:
- Treating wastewater from dyeing processes for reuse using advanced filtration, ozone oxidation, and membrane bioreactors to meet environmental discharge standards and conserve water.
- Renewable Energy:
- Solar and wind energy powering textile mills, including spinning, weaving, and finishing operations, often integrated with smart grid systems to ensure energy reliability and cost savings.
- Example:
- Factories using waterless dyeing technologies, such as supercritical CO₂ dyeing, to eliminate the need for water altogether while improving colorfastness and reducing chemical loads in production.
Benefits of Energy and Resource Efficiency
- Cost Savings:
- Reducing energy consumption and waste lowers operational costs significantly. By optimizing systems, automating energy-intensive operations, and reducing dependency on non-renewable resources, companies can achieve long-term financial gains. These savings not only contribute to a healthier bottom line but also free up capital for investment in innovation and sustainability initiatives.
- Enhanced Productivity:
- Streamlined processes improve output and efficiency by minimizing delays, energy losses, and material handling errors. When manufacturing lines are optimized for energy use and resource flow, it leads to quicker cycle times, fewer defects, and smoother transitions between production phases, which collectively elevate overall productivity and competitiveness.
- Environmental Sustainability:
- Reduces carbon emissions and conserves natural resources through smarter consumption and improved process management. Energy-efficient operations produce fewer greenhouse gases, while resource-efficient practices minimize landfill contributions and depletion of critical materials. These strategies support broader environmental goals and help align industrial activities with international climate agreements such as the Paris Accord. For example, organizations following IEA energy efficiency strategies report measurable environmental and economic benefits.
- Regulatory Compliance:
- Meets environmental standards and avoids penalties by proactively adhering to energy and resource efficiency benchmarks. Implementing best practices reduces the likelihood of violations, helps secure permits faster, and ensures smooth audits. In some regions, efficiency standards are tied to incentives, so compliant businesses can also benefit from tax relief or preferential procurement status.
- Improved Brand Reputation:
- Demonstrates commitment to sustainability, appealing to eco-conscious consumers, investors, and partners. Transparent reporting on resource use and sustainability metrics enhances trust and positions companies as responsible and forward-thinking. Brands that integrate green practices into their identity often see increased loyalty, stronger media attention, and better long-term market performance.
Challenges in Implementation of Energy and Resource Efficiency
- High Initial Costs:
- Significant investment required for new technologies and infrastructure can deter small and medium enterprises from adopting energy-efficient practices. The upfront costs associated with retrofitting facilities, acquiring smart equipment, and implementing renewable energy systems often create financial barriers. While the long-term savings are substantial, the payback period may appear lengthy, influencing decision-makers to delay action or opt for less transformative changes.
- Complexity of Integration:
- Adapting legacy systems to modern technologies can be challenging, especially in facilities with deeply embedded traditional workflows. Integration often requires system overhauls, custom interfaces, and downtime during installation. Additionally, ensuring compatibility between disparate platforms—such as PLCs, IoT devices, and cloud services—requires cross-disciplinary expertise, and misalignments can lead to reduced efficiency or data loss.
- Data Management:
- Handling and analyzing large datasets from smart systems is essential for optimization but can overwhelm existing IT infrastructure. Energy and resource monitoring generate continuous streams of data, necessitating robust storage, analytics tools, and cybersecurity measures. Poor data quality or lack of real-time insights may hinder the ability to respond effectively to inefficiencies or anomalies, limiting the benefits of digitization. Organizations can refer to guides like the EPA’s Sustainable Materials Management Tools for managing such complexity.
- Workforce Training:
- Educating employees on sustainable practices and advanced technologies is vital but time-consuming. The transition to energy-efficient operations requires reskilling personnel to interact with automated systems, interpret data dashboards, and maintain new equipment. Without proper training, workers may resist change or use the systems ineffectively, leading to inconsistent outcomes and undermining efficiency goals.
- Supply Chain Collaboration:
- Ensuring energy and resource efficiency across global supply chains introduces challenges in coordination, transparency, and enforcement. Suppliers may vary in their commitment to sustainability, data reporting practices, or access to efficient technologies. Establishing shared metrics, conducting audits, and aligning on environmental goals require long-term partnerships and, in some cases, third-party mediation to foster trust and compliance throughout the chain.
Future Trends in Energy and Resource Efficiency
- Net-Zero Manufacturing:
- Achieving carbon neutrality by adopting renewable energy and efficient processes is expected to become a cornerstone of industrial transformation. Manufacturers are increasingly aiming for zero emissions by implementing energy-saving technologies, shifting to 100% renewable power, and participating in carbon offset programs. Net-zero strategies also involve redesigning supply chains to reduce carbon intensity and investing in clean energy infrastructure such as solar microgrids and hydrogen fuel cells.
- Circular Economy Models:
- Emphasizing recycling, reuse, and resource recovery enables industries to shift from linear production to closed-loop systems. Circular practices include designing products for disassembly, sourcing secondary raw materials, and developing remanufacturing capabilities. These models reduce waste, extend product lifecycles, and improve environmental outcomes, aligning with global sustainability goals and resource security initiatives.
- AI-Driven Optimization:
- Leveraging AI to identify efficiency opportunities will revolutionize energy and resource management. Machine learning algorithms can analyze real-time data from equipment and environmental sensors to detect anomalies, forecast demand, and optimize operations. Predictive maintenance, smart load balancing, and energy usage modeling are just a few of the emerging applications. For instance, platforms like Schneider Electric’s EcoStruxure use AI and IoT to improve sustainability and efficiency in manufacturing and infrastructure.
- Green Manufacturing Standards:
- Adopting globally recognized frameworks for sustainable production ensures consistent environmental performance across industries. Standards like ISO 14001 and LEED certification encourage resource efficiency, waste minimization, and continuous improvement. Compliance with these benchmarks can drive innovation, reduce liabilities, and enhance a company’s reputation, especially as regulatory scrutiny intensifies worldwide.
- Decentralized Energy Systems:
- On-site renewable energy generation to reduce dependency on central grids is gaining traction in the push for energy resilience and sustainability. Factories are integrating solar rooftops, wind turbines, and biomass converters into their infrastructure. These systems not only lower transmission losses and electricity costs but also provide energy autonomy during grid disruptions. Coupled with smart energy storage and demand-side management, decentralized solutions are reshaping the future of industrial energy supply.
Why Study Energy and Resource Efficiency in Manufacturing
Reducing Environmental Footprints
Energy and resource efficiency aims to minimize waste, emissions, and resource use. Students learn how to measure and reduce the environmental impacts of production. This supports global goals for climate action and sustainability.
Process Optimization and Cleaner Production
Students explore methods like lean manufacturing, process integration, and energy audits. These tools identify inefficiencies and opportunities for savings. This improves both environmental and economic performance.
Designing for Sustainability
Sustainable manufacturing starts at the design stage. Students learn how to select materials and processes that require less energy and create less waste. This supports life-cycle thinking and green innovation.
Measuring Efficiency and Performance
The course introduces key metrics such as energy intensity, yield ratios, and carbon footprint. Students use data to track improvements and guide decisions. These insights drive accountability and continuous improvement.
Policy, Standards, and Global Impact
Students study regulations, certifications, and sustainability reporting standards. They learn how to align industrial practices with international frameworks. This prepares them for leadership roles in sustainable manufacturing.
Energy and Resource Efficiency: Conclusion
Energy and resource efficiency in manufacturing is critical for fostering sustainability, reducing costs, and meeting global environmental challenges. As industries confront rising energy prices, resource scarcity, and increasingly stringent environmental regulations, efficiency becomes more than a best practice—it becomes a necessity. By adopting advanced technologies such as AI-driven analytics, digital twins, and IoT-based monitoring, companies can transform data into actionable insights that drive continuous improvement and smarter resource management.
Integrating renewable energy sources like solar, wind, and biomass helps decarbonize operations and contributes to climate targets, while innovations in water recycling, material optimization, and waste heat recovery enhance operational resilience. Promoting sustainable practices not only benefits the environment but also improves brand reputation and customer trust, especially as consumers increasingly favor eco-friendly companies.
Furthermore, global initiatives and policies such as the European Green Deal and the UN’s Sustainable Development Goals are accelerating the transition toward greener industrial models. Resources such as the International Energy Agency’s Energy Efficiency hub provide valuable guidance and benchmarking tools for organizations looking to scale up their efforts.
As global priorities shift toward sustainability and circular economy principles, energy and resource efficiency will remain a key driver of innovation, competitiveness, and long-term resilience in manufacturing and other industrial processes. Embracing this transformation positions industries to thrive in a future that values not only economic performance but also environmental stewardship and social responsibility.
Energy and Resource Efficiency: Review Questions with Detailed Answers
1. What is energy efficiency in the context of manufacturing, and why is it important?
Answer:
Energy efficiency in manufacturing refers to the optimal use of energy resources to perform production processes with minimal waste. It involves implementing technologies and practices that reduce energy consumption while maintaining or improving production output and quality.
Concepts:
- Energy Efficiency: The ratio of useful output of services from a system to the input of energy.
- Sustainability: Practices that meet current needs without compromising future generations’ ability to meet theirs.
Importance:
Cost Reduction:
- How: Lower energy consumption directly reduces utility bills and operational costs.
- Impact: Increases profitability by decreasing the cost of production.
Environmental Impact:
- How: Reduces greenhouse gas emissions and lowers the carbon footprint.
- Impact: Contributes to mitigating climate change and promoting environmental sustainability.
Regulatory Compliance:
- How: Adheres to energy-related regulations and standards set by governments.
- Impact: Avoids penalties and enhances the company’s reputation as a responsible entity.
Competitive Advantage:
- How: Demonstrates commitment to sustainability and efficiency.
- Impact: Attracts environmentally conscious customers and partners, differentiating the company in the market.
Resource Conservation:
- How: Efficient use of energy preserves natural resources.
- Impact: Ensures long-term availability of energy resources, supporting sustained manufacturing operations.
Conclusion: Energy efficiency is crucial in manufacturing for reducing costs, minimizing environmental impact, complying with regulations, gaining competitive advantage, and conserving resources. Implementing energy-efficient practices not only benefits the organization financially but also contributes to broader sustainability goals.
2. How does resource efficiency differ from energy efficiency in manufacturing, and what are its key components?
Answer:
Resource efficiency in manufacturing encompasses the optimal use of all inputs—materials, water, energy, and labor—to maximize output while minimizing waste and environmental impact. While energy efficiency specifically focuses on reducing energy consumption, resource efficiency takes a holistic approach to conserving and optimizing all resources involved in the production process.
Concepts:
- Resource Efficiency: Maximizing the value obtained from resources while minimizing negative impacts on the environment.
- Sustainable Manufacturing: Practices that reduce resource consumption and waste generation.
Key Components:
Material Efficiency:
- How: Minimizes the use of raw materials through process optimization, recycling, and reuse.
- Impact: Reduces material costs and waste disposal needs.
Water Efficiency:
- How: Implements water-saving technologies and recycling systems.
- Impact: Decreases water consumption and lowers costs associated with water procurement and treatment.
Energy Efficiency:
- How: Uses energy-efficient machinery, lighting, and HVAC systems.
- Impact: Lowers energy consumption and operational costs.
Waste Minimization:
- How: Adopts lean manufacturing principles to eliminate non-value-added activities and reduce scrap.
- Impact: Decreases waste disposal costs and environmental footprint.
Process Optimization:
- How: Streamlines production processes to enhance efficiency and reduce resource use.
- Impact: Increases productivity and reduces resource consumption.
Product Design for Efficiency:
- How: Designs products that require fewer resources to manufacture and are easier to recycle or reuse.
- Impact: Enhances product sustainability and reduces lifecycle costs.
Supply Chain Optimization:
- How: Collaborates with suppliers to ensure efficient resource use and reduce transportation-related resource consumption.
- Impact: Lowers overall resource usage and enhances supply chain sustainability.
Employee Training and Engagement:
- How: Educates employees on resource-efficient practices and encourages participation in sustainability initiatives.
- Impact: Fosters a culture of sustainability and continuous improvement.
Conclusion: Resource efficiency in manufacturing goes beyond energy savings to encompass the optimal use of all inputs, including materials, water, and labor. By focusing on material efficiency, water conservation, waste minimization, process optimization, and sustainable product design, manufacturers can achieve significant cost savings, reduce environmental impact, and enhance overall sustainability.
3. What are the primary strategies for improving energy efficiency in manufacturing facilities?
Answer:
Improving energy efficiency in manufacturing facilities involves implementing a combination of strategies that optimize energy use, reduce waste, and enhance overall operational performance. These strategies encompass technological upgrades, process improvements, and behavioral changes aimed at minimizing energy consumption while maintaining or increasing production output.
Concepts:
- Energy Audits: Comprehensive assessments to identify energy-saving opportunities.
- Benchmarking: Comparing energy performance against industry standards or best practices.
Primary Strategies:
Conducting Energy Audits:
- How: Perform detailed assessments of energy consumption patterns to identify inefficiencies.
- Impact: Provides a roadmap for targeted energy-saving measures.
Upgrading to Energy-Efficient Equipment:
- How: Replace outdated machinery, lighting, and HVAC systems with energy-efficient alternatives.
- Impact: Reduces energy consumption and lowers operational costs.
Implementing Variable Frequency Drives (VFDs):
- How: Use VFDs on motors to adjust their speed based on demand.
- Impact: Optimizes energy use and extends the lifespan of equipment.
Optimizing Process Heating and Cooling:
- How: Improve insulation, recover waste heat, and optimize temperature controls.
- Impact: Enhances thermal efficiency and reduces energy waste.
Adopting Lean Manufacturing Principles:
- How: Streamline production processes to eliminate waste and reduce energy consumption.
- Impact: Increases efficiency and minimizes unnecessary energy use.
Implementing Energy Management Systems (EMS):
- How: Utilize software to monitor, control, and optimize energy usage in real-time.
- Impact: Enables proactive energy management and identifies areas for improvement.
Enhancing Lighting Efficiency:
- How: Replace incandescent bulbs with LED lighting and utilize natural light where possible.
- Impact: Reduces electricity consumption and maintenance costs.
Employee Training and Engagement:
- How: Educate employees on energy-saving practices and encourage participation in energy conservation initiatives.
- Impact: Promotes a culture of energy awareness and continuous improvement.
Energy Recovery and Reuse:
- How: Implement systems to capture and reuse waste energy, such as heat exchangers or cogeneration units.
- Impact: Maximizes energy utilization and reduces overall energy demand.
Scheduling and Automation:
- How: Optimize production schedules and use automation to reduce energy use during peak and off-peak hours.
- Impact: Balances energy demand and improves overall energy efficiency.
Conclusion: Enhancing energy efficiency in manufacturing requires a multifaceted approach that includes conducting energy audits, upgrading equipment, optimizing processes, implementing management systems, and engaging employees. By adopting these strategies, manufacturers can significantly reduce energy consumption, lower operational costs, and contribute to environmental sustainability.
4. How does resource efficiency contribute to sustainable manufacturing, and what are some best practices to achieve it?
Answer:
Resource efficiency is a cornerstone of sustainable manufacturing, as it focuses on maximizing the value derived from resources while minimizing waste and environmental impact. By optimizing the use of materials, water, energy, and labor, manufacturers can achieve greater sustainability, reduce costs, and enhance their competitive advantage.
Concepts:
- Sustainable Manufacturing: Manufacturing practices that minimize environmental impact, conserve resources, and promote social responsibility.
- Circular Economy: An economic system aimed at eliminating waste and the continual use of resources through recycling, reuse, and regeneration.
Contribution to Sustainable Manufacturing:
Reduced Resource Consumption:
- How: Efficient use of materials and energy decreases the overall demand for resources.
- Impact: Preserves natural resources and reduces the environmental footprint of manufacturing operations.
Minimized Waste Generation:
- How: Implementing lean manufacturing and recycling practices to reduce waste.
- Impact: Lowers disposal costs, reduces pollution, and supports waste management sustainability.
Enhanced Operational Efficiency:
- How: Optimizing production processes and resource allocation.
- Impact: Increases productivity and reduces operational costs, contributing to economic sustainability.
Improved Product Lifecycle Management:
- How: Designing products for durability, repairability, and recyclability.
- Impact: Extends product lifespan, reduces the need for new materials, and supports a circular economy.
Best Practices to Achieve Resource Efficiency:
Implementing Lean Manufacturing:
- How: Streamline production processes to eliminate non-value-added activities and reduce waste.
- Impact: Enhances efficiency and minimizes resource consumption.
Adopting Just-In-Time (JIT) Production:
- How: Align production schedules with demand to reduce inventory levels and material waste.
- Impact: Minimizes excess inventory and lowers storage and handling costs.
Utilizing Advanced Recycling Technologies:
- How: Implement recycling systems to recover and reuse materials from production waste.
- Impact: Reduces the need for virgin materials and lowers waste disposal costs.
Optimizing Supply Chain Management:
- How: Collaborate with suppliers to ensure efficient material use and reduce transportation-related resource consumption.
- Impact: Enhances supply chain sustainability and reduces overall resource use.
Investing in Energy-Efficient Technologies:
- How: Upgrade to energy-efficient machinery, lighting, and HVAC systems.
- Impact: Reduces energy consumption and operational costs, contributing to environmental sustainability.
Water Conservation Measures:
- How: Implement water recycling and efficient water management systems.
- Impact: Decreases water usage and lowers costs associated with water procurement and treatment.
Employee Training and Engagement:
- How: Educate employees on resource-efficient practices and encourage participation in sustainability initiatives.
- Impact: Fosters a culture of sustainability and continuous improvement within the organization.
Design for Manufacturability (DFM):
- How: Design products that are easy to manufacture with minimal resource use and waste.
- Impact: Enhances production efficiency and reduces material consumption.
Lifecycle Assessment (LCA):
- How: Conduct LCAs to evaluate the environmental impact of products throughout their lifecycle.
- Impact: Identifies opportunities for reducing resource use and enhancing sustainability in product design and manufacturing.
Adopting Digital Twin Technology:
- How: Use Digital Twins to simulate and optimize resource use in manufacturing processes.
- Impact: Enables data-driven decision-making for resource efficiency and sustainability improvements.
Conclusion: Resource efficiency is integral to sustainable manufacturing, enabling manufacturers to optimize resource use, reduce waste, and enhance operational efficiency. By adopting best practices such as lean manufacturing, JIT production, recycling technologies, and employee engagement, manufacturers can achieve significant sustainability goals, reduce costs, and maintain a competitive edge in the market.
5. What role do energy management systems (EMS) play in enhancing energy efficiency in manufacturing, and how are they implemented?
Answer:
Energy Management Systems (EMS) play a critical role in enhancing energy efficiency in manufacturing by providing a structured framework for monitoring, controlling, and optimizing energy usage across all facets of production operations. An EMS enables manufacturers to systematically manage energy consumption, identify inefficiencies, and implement targeted energy-saving measures, thereby reducing costs and minimizing environmental impact.
Concepts:
- Energy Management Systems (EMS): Integrated systems that collect, monitor, and analyze energy usage data to optimize energy performance.
- ISO 50001: An international standard that specifies requirements for establishing, implementing, maintaining, and improving an EMS.
Role of EMS in Enhancing Energy Efficiency:
Comprehensive Energy Monitoring:
- How: EMS continuously tracks energy consumption across different departments, machines, and processes.
- Impact: Provides detailed visibility into energy usage patterns, identifying high-consumption areas and potential inefficiencies.
Data Analysis and Reporting:
- How: Analyzes energy data to identify trends, anomalies, and opportunities for improvement.
- Impact: Enables informed decision-making and supports the development of targeted energy-saving strategies.
Setting Energy Goals and Targets:
- How: Establishes specific, measurable energy performance goals based on baseline data.
- Impact: Provides clear objectives for reducing energy consumption and enhances accountability within the organization.
Implementing Energy-Saving Measures:
- How: Identifies and implements initiatives such as equipment upgrades, process optimizations, and behavioral changes to reduce energy use.
- Impact: Achieves tangible reductions in energy consumption and operational costs.
Continuous Improvement:
- How: Regularly reviews energy performance and updates strategies to enhance efficiency.
- Impact: Ensures sustained energy savings and adapts to changing operational conditions and technological advancements.
Compliance and Certification:
- How: Adheres to energy-related regulations and standards, and seeks certifications like ISO 50001.
- Impact: Demonstrates commitment to energy efficiency and sustainability, enhancing the organization’s reputation and market position.
Implementation of EMS:
Energy Assessment:
- How: Conduct a thorough assessment to establish a baseline of current energy usage and identify major energy-consuming processes and equipment.
- Impact: Provides a foundation for setting realistic energy goals and identifying improvement opportunities.
Setting Up the EMS Framework:
- How: Define the scope, objectives, and policies for energy management within the organization.
- Impact: Establishes a clear structure and direction for energy efficiency initiatives.
Installing Monitoring Equipment:
- How: Deploy sensors and meters to collect real-time energy data from various parts of the manufacturing facility.
- Impact: Enables accurate and comprehensive energy monitoring.
Data Collection and Integration:
- How: Integrate energy data into the EMS software platform for centralized analysis and management.
- Impact: Facilitates seamless data access and enhances analytical capabilities.
Training and Engagement:
- How: Educate employees about the EMS, its benefits, and their roles in achieving energy efficiency goals.
- Impact: Promotes a culture of energy awareness and encourages active participation in energy-saving efforts.
Developing Energy Management Plans:
- How: Create detailed plans outlining specific actions, timelines, and responsibilities for energy efficiency projects.
- Impact: Provides a roadmap for implementing energy-saving measures and tracking progress.
Implementing Energy-Saving Projects:
- How: Execute identified projects such as upgrading to energy-efficient lighting, optimizing HVAC systems, or improving process controls.
- Impact: Achieves direct reductions in energy consumption and operational costs.
Monitoring and Reporting:
- How: Continuously monitor energy usage and generate regular reports to track performance against set goals.
- Impact: Ensures transparency, accountability, and facilitates ongoing improvements.
Review and Optimization:
- How: Regularly review EMS performance and adjust strategies based on data insights and changing conditions.
- Impact: Maintains the effectiveness of the EMS and ensures continuous improvement in energy efficiency.
Conclusion: Energy Management Systems are essential tools for enhancing energy efficiency in manufacturing. By providing comprehensive monitoring, data-driven analysis, goal setting, and continuous improvement frameworks, EMS enables manufacturers to systematically reduce energy consumption, lower operational costs, and promote sustainable practices. Proper implementation of an EMS, supported by employee engagement and strategic planning, ensures long-term energy efficiency and operational excellence.
6. What are the key technologies and innovations that drive energy and resource efficiency in modern manufacturing?
Answer:
Key technologies and innovations play a pivotal role in driving energy and resource efficiency in modern manufacturing by enabling smarter, more optimized, and sustainable production processes. These advancements leverage digitalization, automation, and data analytics to enhance operational efficiency, reduce waste, and promote sustainability.
Concepts:
- Digitalization: Integration of digital technologies into all aspects of manufacturing, transforming operations and business models.
- Automation: Use of control systems and machinery to perform tasks with minimal human intervention.
Key Technologies and Innovations:
Internet of Things (IoT) and Industrial IoT (IIoT):
- How: Connects machines, sensors, and devices to collect and exchange data in real-time.
- Impact: Enables real-time monitoring and optimization of energy and resource use, enhancing efficiency and reducing waste.
Artificial Intelligence (AI) and Machine Learning (ML):
- How: Utilizes AI and ML algorithms to analyze data, predict maintenance needs, and optimize production processes.
- Impact: Improves decision-making, enhances predictive maintenance, and optimizes resource allocation, leading to reduced energy consumption and increased operational efficiency.
Energy Management Systems (EMS):
- How: Implements software and hardware solutions to monitor, control, and optimize energy usage across manufacturing facilities.
- Impact: Provides detailed insights into energy consumption patterns, identifies inefficiencies, and facilitates the implementation of energy-saving measures.
Advanced Robotics and Automation:
- How: Deploys intelligent robots and automated systems to perform repetitive and precise tasks.
- Impact: Enhances production efficiency, reduces human error, and optimizes resource use, leading to lower energy consumption and increased productivity.
Additive Manufacturing (3D Printing):
- How: Uses 3D printing technologies to produce complex parts and prototypes with minimal material waste.
- Impact: Reduces material consumption, lowers energy use in production, and enables rapid prototyping and customization.
Digital Twin Technology:
- How: Creates virtual replicas of physical assets, processes, or systems to simulate and optimize their performance.
- Impact: Facilitates real-time monitoring, predictive maintenance, and process optimization, enhancing energy and resource efficiency.
Big Data Analytics:
- How: Analyzes large volumes of data from various sources to uncover patterns and insights.
- Impact: Enables data-driven decision-making, identifies opportunities for efficiency improvements, and optimizes resource use.
Renewable Energy Integration:
- How: Incorporates renewable energy sources such as solar and wind power into manufacturing operations.
- Impact: Reduces reliance on fossil fuels, lowers energy costs, and enhances sustainability by decreasing carbon emissions.
Smart Manufacturing Systems:
- How: Integrates digital technologies, automation, and data analytics to create interconnected and intelligent manufacturing environments.
- Impact: Enhances flexibility, efficiency, and resource optimization, supporting lean manufacturing and sustainability goals.
Sustainable Materials and Recycling Technologies:
- How: Uses eco-friendly materials and advanced recycling methods to minimize environmental impact.
- Impact: Reduces material waste, lowers the environmental footprint, and promotes the circular economy by enabling the reuse and recycling of materials.
Energy-Efficient Lighting and HVAC Systems:
- How: Implements LED lighting, smart lighting controls, and energy-efficient heating, ventilation, and air conditioning systems.
- Impact: Reduces energy consumption, lowers operational costs, and enhances workplace comfort and safety.
Supply Chain Optimization Tools:
- How: Uses software and analytics to optimize supply chain operations, including inventory management, logistics, and procurement.
- Impact: Enhances resource efficiency, reduces transportation-related energy consumption, and minimizes waste across the supply chain.
Conclusion: Modern manufacturing leverages a range of advanced technologies and innovations to drive energy and resource efficiency. From IoT and AI to digital twins and additive manufacturing, these technologies enable manufacturers to optimize processes, reduce waste, and enhance sustainability. By adopting and integrating these key technologies, manufacturers can achieve significant improvements in operational efficiency, cost savings, and environmental responsibility, positioning themselves for long-term success in a competitive and increasingly sustainable marketplace.
7. How can lean manufacturing principles be integrated with energy and resource efficiency initiatives to achieve sustainable production?
Answer:
Integrating lean manufacturing principles with energy and resource efficiency initiatives creates a synergistic approach to achieving sustainable production. Lean principles focus on eliminating waste, optimizing processes, and enhancing value, while energy and resource efficiency aim to minimize resource consumption and environmental impact. Combining these approaches leads to more efficient, cost-effective, and sustainable manufacturing operations.
Concepts:
- Lean Manufacturing: A methodology focused on minimizing waste without sacrificing productivity.
- Sustainability: Practices that meet present needs without compromising future generations’ ability to meet theirs.
Integration Strategies:
Value Stream Mapping (VSM) with Energy Audits:
- How: Combine VSM with energy audits to identify both process inefficiencies and energy waste.
- Impact: Provides a comprehensive view of where to eliminate waste and optimize energy use, enhancing overall efficiency and sustainability.
Just-In-Time (JIT) Production:
- How: Implement JIT to reduce inventory levels and minimize material waste.
- Impact: Lowers storage costs, reduces resource consumption, and decreases energy use associated with maintaining large inventories.
5S Workplace Organization:
- How: Apply the 5S principles (Sort, Set in order, Shine, Standardize, Sustain) to organize the workplace efficiently.
- Impact: Enhances operational efficiency, reduces unnecessary movements and energy use, and creates a safer, more productive work environment.
Kaizen Continuous Improvement:
- How: Encourage ongoing, incremental improvements focused on both process optimization and energy/resource conservation.
- Impact: Promotes a culture of continuous improvement, leading to sustained reductions in waste and resource consumption over time.
Standardized Work Processes:
- How: Develop and implement standardized procedures that incorporate energy and resource efficiency best practices.
- Impact: Ensures consistent application of efficiency measures, reducing variability and enhancing overall production sustainability.
Total Productive Maintenance (TPM):
- How: Integrate TPM with energy-efficient maintenance practices to ensure equipment operates at peak efficiency.
- Impact: Reduces energy consumption, extends equipment lifespan, and minimizes downtime, contributing to more sustainable production.
Energy-Efficient Equipment and Machinery:
- How: Select and maintain energy-efficient equipment as part of lean equipment planning and replacement strategies.
- Impact: Lowers energy consumption, reduces operational costs, and supports lean manufacturing goals of efficiency and waste reduction.
Waste Minimization and Recycling:
- How: Implement lean waste minimization techniques alongside recycling and reusing materials.
- Impact: Decreases material waste, lowers disposal costs, and enhances resource efficiency, supporting both lean and sustainability objectives.
Cross-Functional Teams:
- How: Form cross-functional teams to identify and implement energy and resource efficiency improvements within lean projects.
- Impact: Fosters collaboration, leverages diverse expertise, and ensures that efficiency initiatives are integrated across all aspects of production.
Performance Metrics and KPIs:
- How: Establish KPIs that measure both lean performance (e.g., cycle time, waste reduction) and energy/resource efficiency (e.g., energy per unit produced, material usage).
- Impact: Provides a balanced view of performance, ensuring that both lean and efficiency goals are being met and driving continuous improvement.
Benefits of Integration:
- Enhanced Efficiency: Combining lean and efficiency initiatives leads to more streamlined processes and optimized resource use.
- Cost Savings: Reductions in waste and energy consumption lower operational costs, improving profitability.
- Improved Sustainability: Minimizing resource use and waste contributes to environmental sustainability and corporate social responsibility.
- Increased Productivity: Efficient processes and optimized resource allocation enhance overall productivity and operational performance.
- Employee Engagement: Involving employees in continuous improvement and efficiency initiatives fosters a culture of sustainability and ownership.
Conclusion: Integrating lean manufacturing principles with energy and resource efficiency initiatives creates a powerful framework for achieving sustainable production. By eliminating waste, optimizing processes, and conserving resources, manufacturers can enhance operational efficiency, reduce costs, and promote environmental sustainability. This holistic approach ensures that manufacturing operations are not only efficient and productive but also responsible and sustainable, positioning organizations for long-term success in a competitive and eco-conscious marketplace.
8. What are some common challenges manufacturers face when trying to improve energy and resource efficiency, and how can they overcome these challenges?
Answer:
Manufacturers striving to improve energy and resource efficiency often encounter several challenges that can impede progress. Understanding these obstacles and implementing effective strategies to overcome them is crucial for achieving sustainability goals and enhancing operational performance.
Concepts:
- Barriers to Efficiency: Factors that hinder the adoption and implementation of energy and resource efficiency measures.
- Mitigation Strategies: Approaches to address and overcome challenges.
Common Challenges and Solutions:
High Initial Investment Costs:
- Challenge: Implementing energy-efficient technologies and systems often requires significant upfront capital.
- Solution:
- How: Seek financial incentives, grants, and rebates offered by governments or organizations.
- Impact: Reduces the financial burden and makes energy-efficient investments more feasible.
- Alternative: Implement projects in phases to spread out costs over time.
Lack of Awareness and Expertise:
- Challenge: Insufficient knowledge about energy and resource efficiency practices and technologies.
- Solution:
- How: Invest in training programs and hire experts in energy management.
- Impact: Enhances the workforce’s ability to identify and implement efficiency measures.
- Collaboration: Partner with energy consultants or service providers to gain specialized knowledge.
Data Collection and Analysis Difficulties:
- Challenge: Gathering accurate data on energy and resource usage can be complex and time-consuming.
- Solution:
- How: Implement advanced monitoring systems and energy management software.
- Impact: Facilitates efficient data collection, real-time monitoring, and comprehensive analysis for informed decision-making.
Resistance to Change:
- Challenge: Employees and management may resist adopting new processes or technologies due to comfort with existing practices.
- Solution:
- How: Foster a culture of continuous improvement and communicate the benefits of efficiency initiatives.
- Impact: Encourages buy-in and active participation from all levels of the organization.
- Incentives: Provide incentives and recognition for contributions to energy and resource efficiency.
Integration with Existing Systems:
- Challenge: Difficulty in integrating new energy-efficient technologies with legacy systems and processes.
- Solution:
- How: Use interoperable technologies and ensure compatibility during the planning phase.
- Impact: Smoothens the integration process, minimizing disruptions to ongoing operations.
- Upgrades: Gradually replace outdated systems to facilitate seamless integration.
Measuring and Tracking Efficiency Gains:
- Challenge: Difficulty in accurately measuring and attributing energy and resource savings.
- Solution:
- How: Establish clear metrics and benchmarks for energy and resource efficiency.
- Impact: Enables accurate tracking of progress and identification of areas needing improvement.
- Reporting: Utilize dashboards and reporting tools to visualize efficiency gains.
Supply Chain Constraints:
- Challenge: Dependence on suppliers who may not prioritize energy and resource efficiency.
- Solution:
- How: Collaborate with suppliers to encourage and support their adoption of efficient practices.
- Impact: Enhances overall supply chain sustainability and ensures consistency in efficiency efforts.
- Standards: Set sustainability criteria for supplier selection and performance evaluation.
Technological Limitations:
- Challenge: Existing technologies may not fully support desired levels of energy and resource efficiency.
- Solution:
- How: Invest in research and development to innovate and adopt cutting-edge technologies.
- Impact: Enables the implementation of more effective and efficient solutions.
- Upgrades: Regularly update and maintain equipment to ensure optimal performance and efficiency.
Regulatory and Compliance Issues:
- Challenge: Navigating complex regulations related to energy and resource usage.
- Solution:
- How: Stay informed about relevant regulations and seek guidance from regulatory experts.
- Impact: Ensures compliance and avoids potential legal issues or fines.
- Proactive Measures: Implement proactive measures to exceed regulatory requirements and enhance sustainability.
Short-Term Focus Over Long-Term Benefits:
- Challenge: Emphasis on immediate cost savings rather than long-term sustainability gains.
- Solution:
- How: Develop long-term sustainability goals and integrate them into the organization’s strategic planning.
- Impact: Balances short-term operational needs with long-term sustainability objectives, ensuring sustained efficiency improvements.
- Education: Educate stakeholders on the long-term financial and environmental benefits of energy and resource efficiency.
Conclusion: Manufacturers face a range of challenges when striving to improve energy and resource efficiency, including high initial costs, lack of expertise, data management issues, resistance to change, and supply chain constraints. By implementing targeted solutions such as securing financial incentives, investing in training, adopting advanced monitoring systems, fostering a culture of continuous improvement, and collaborating with suppliers, manufacturers can overcome these obstacles. Successfully addressing these challenges enables organizations to achieve significant energy and resource efficiency gains, leading to cost savings, enhanced sustainability, and improved competitiveness in the market.
9. How can digitalization and automation technologies be leveraged to enhance energy and resource efficiency in manufacturing?
Answer:
Digitalization and automation technologies are pivotal in enhancing energy and resource efficiency in manufacturing by enabling real-time monitoring, data-driven decision-making, process optimization, and reduced human intervention. These technologies transform traditional manufacturing operations into smarter, more efficient, and sustainable systems.
Concepts:
- Digitalization: Integration of digital technologies into all aspects of manufacturing, transforming operations and business models.
- Automation: Use of control systems and machinery to perform tasks with minimal human intervention.
Leveraging Digitalization and Automation:
Real-Time Monitoring and Data Collection:
- How: Utilize IoT sensors and connected devices to continuously monitor energy and resource usage across manufacturing processes.
- Impact: Provides detailed visibility into consumption patterns, identifying areas of inefficiency and enabling timely interventions to reduce waste.
Advanced Data Analytics:
- How: Apply big data analytics and machine learning algorithms to analyze collected data and uncover insights into energy and resource use.
- Impact: Facilitates predictive maintenance, process optimization, and informed decision-making to enhance efficiency and reduce consumption.
Automated Control Systems:
- How: Implement programmable logic controllers (PLCs) and distributed control systems (DCS) to automate and optimize manufacturing processes.
- Impact: Ensures precise control over operations, reducing energy and resource use by maintaining optimal process conditions and minimizing variability.
Energy Management Systems (EMS):
- How: Integrate EMS with digital and automated systems to manage and optimize energy use across the facility.
- Impact: Enables centralized monitoring and control of energy consumption, identifying opportunities for savings and enhancing overall energy efficiency.
Smart Manufacturing Platforms:
- How: Use integrated digital platforms that connect various manufacturing systems and provide a unified view of operations.
- Impact: Enhances coordination and optimization of resources, reducing redundancies and improving efficiency across the production process.
Robotics and Automated Machinery:
- How: Deploy energy-efficient robots and automated machinery to perform repetitive and precise tasks.
- Impact: Reduces energy consumption by optimizing task execution and minimizing idle times, while also enhancing productivity and consistency.
Digital Twin Technology:
- How: Create digital replicas of physical manufacturing systems to simulate and optimize energy and resource use.
- Impact: Enables testing and refinement of processes in a virtual environment, identifying the most efficient configurations before implementation in the physical world.
Predictive Maintenance:
- How: Use automation and data analytics to predict equipment failures and schedule maintenance proactively.
- Impact: Prevents unexpected downtime, ensures machines operate at peak efficiency, and reduces energy waste associated with malfunctioning equipment.
Supply Chain Digitalization:
- How: Digitize supply chain processes to optimize material flow and reduce transportation-related energy use.
- Impact: Enhances resource efficiency by ensuring timely delivery of materials, reducing excess inventory, and minimizing energy consumption in logistics.
Virtual and Augmented Reality (VR/AR):
- How: Utilize VR and AR for training, maintenance, and process visualization.
- Impact: Improves operational efficiency by enhancing workforce skills, reducing errors, and enabling more efficient troubleshooting and maintenance processes.
Benefits of Leveraging Digitalization and Automation:
- Increased Efficiency: Streamlined processes and optimized resource use lead to higher productivity and lower operational costs.
- Reduced Energy Consumption: Precise control and real-time optimization minimize energy waste and enhance sustainability.
- Enhanced Flexibility: Digital and automated systems allow for quick adjustments to changing production demands, improving responsiveness.
- Improved Quality: Consistent and precise operations reduce defects and enhance product quality.
- Cost Savings: Lower energy and resource use translate into significant cost reductions, improving profitability.
- Sustainability: Reduced environmental impact through optimized energy and resource use aligns with corporate sustainability goals and regulatory requirements.
Conclusion: Digitalization and automation technologies are essential drivers of energy and resource efficiency in modern manufacturing. By enabling real-time monitoring, data-driven optimization, precise control, and proactive maintenance, these technologies transform manufacturing operations into highly efficient and sustainable systems. Embracing digital and automated solutions not only enhances operational performance and reduces costs but also supports broader sustainability objectives, positioning manufacturers for long-term success in a competitive and eco-conscious market.
10. What role does employee training and engagement play in achieving energy and resource efficiency in manufacturing, and how can organizations foster this?
Answer:
Employee training and engagement are critical components in achieving energy and resource efficiency in manufacturing. Educated and motivated employees are essential for identifying inefficiencies, implementing best practices, and sustaining energy and resource-saving initiatives. Organizations can foster effective training and engagement through a combination of education, incentives, participation, and a supportive culture.
Concepts:
- Employee Training: Providing education and skills development to enhance employee capabilities.
- Employee Engagement: Involving and motivating employees to actively participate in organizational goals and initiatives.
Role of Employee Training and Engagement:
Awareness and Understanding:
- How: Educate employees about the importance of energy and resource efficiency and how their actions impact overall performance.
- Impact: Increases awareness and fosters a sense of responsibility towards conserving resources and reducing energy consumption.
Skill Development:
- How: Provide training on the use of energy-efficient technologies, best practices for resource management, and identification of inefficiencies.
- Impact: Equips employees with the necessary skills to implement and sustain energy and resource-saving measures effectively.
Encouraging Innovation:
- How: Involve employees in brainstorming and implementing energy and resource efficiency initiatives.
- Impact: Leverages diverse perspectives and ideas, leading to innovative solutions and continuous improvement in efficiency efforts.
Empowering Employees:
- How: Give employees the authority and tools to make decisions that contribute to energy and resource efficiency.
- Impact: Enhances employee ownership of efficiency initiatives, leading to more proactive and sustained efforts.
Creating a Culture of Sustainability:
- How: Foster an organizational culture that values and prioritizes sustainability and efficiency through leadership support and communication.
- Impact: Encourages collective commitment and alignment towards energy and resource efficiency goals.
Recognition and Incentives:
- How: Implement recognition programs and incentives for employees who contribute significantly to energy and resource-saving initiatives.
- Impact: Motivates employees to actively participate and excel in efficiency efforts, reinforcing positive behaviors.
Continuous Feedback and Improvement:
- How: Provide regular feedback on energy and resource performance and involve employees in reviewing and refining efficiency strategies.
- Impact: Promotes a continuous improvement mindset, ensuring that efficiency measures remain effective and relevant.
Strategies to Foster Employee Training and Engagement:
Comprehensive Training Programs:
- How: Develop and deliver structured training programs that cover energy and resource efficiency concepts, technologies, and practices.
- Impact: Ensures that all employees have a foundational understanding and the skills needed to contribute to efficiency efforts.
Interactive Workshops and Seminars:
- How: Conduct interactive sessions where employees can engage in hands-on learning and discuss real-world efficiency challenges and solutions.
- Impact: Enhances engagement and practical understanding, encouraging active participation and collaboration.
Green Teams and Sustainability Committees:
- How: Establish dedicated teams or committees focused on driving energy and resource efficiency initiatives.
- Impact: Provides a structured platform for employee involvement and leadership in sustainability efforts.
Internal Communication and Awareness Campaigns:
- How: Use newsletters, posters, and digital platforms to communicate the importance of efficiency initiatives and share success stories.
- Impact: Keeps energy and resource efficiency top-of-mind and maintains ongoing engagement and motivation among employees.
Incentive Programs:
- How: Offer rewards, bonuses, or recognition for employees who identify and implement significant energy and resource-saving measures.
- Impact: Encourages proactive efforts and reinforces the value of employee contributions to efficiency goals.
Leadership Involvement:
- How: Ensure that organizational leaders actively support and participate in energy and resource efficiency initiatives.
- Impact: Demonstrates commitment from the top, inspiring employees to follow suit and prioritize sustainability.
Accessible Resources and Tools:
- How: Provide employees with access to tools, guidelines, and resources that facilitate energy and resource efficiency practices.
- Impact: Empowers employees to take action and implement efficiency measures effectively.
Feedback Mechanisms:
- How: Implement systems for employees to provide feedback, suggestions, and report inefficiencies or opportunities for improvement.
- Impact: Engages employees in the continuous improvement process and ensures that efficiency initiatives are responsive to on-the-ground insights.
Conclusion: Employee training and engagement are essential for achieving energy and resource efficiency in manufacturing. By educating employees, fostering a culture of sustainability, encouraging innovation, and providing incentives, organizations can empower their workforce to actively contribute to efficiency initiatives. Effective training and engagement strategies ensure that energy and resource-saving measures are implemented successfully and sustained over time, leading to significant cost savings, enhanced operational performance, and a positive environmental impact.
Conclusion:
The above review questions and detailed answers offer a comprehensive exploration of energy and resource efficiency in manufacturing. Covering fundamental concepts, strategies, technologies, challenges, and the importance of employee involvement, these questions facilitate a deep understanding of how manufacturers can optimize their operations for greater sustainability and efficiency. Engaging with these questions equips students and professionals with the knowledge to implement effective energy and resource-saving measures, drive continuous improvement, and contribute to sustainable manufacturing practices that benefit both organizations and the environment.
Energy and Resource Efficiency: Thought-Provoking Questions with Detailed Answers:
1. How does energy and resource efficiency in manufacturing contribute to overall business sustainability, and what are the long-term economic benefits?
Answer:
Energy and resource efficiency in manufacturing plays a crucial role in enhancing business sustainability by optimizing the use of essential inputs—such as energy, raw materials, and water—while minimizing waste and environmental impact. This strategic approach not only supports environmental stewardship but also offers significant long-term economic benefits that contribute to the enduring success of a business.
Concepts:
- Business Sustainability: The ability of a company to operate continuously without depleting its resources or harming the environment.
- Economic Benefits: Financial gains that result from implementing efficient practices, including cost savings, increased profitability, and competitive advantage.
Contribution to Sustainability:
Cost Reduction:
- How: Efficient use of energy and resources directly lowers utility bills, raw material costs, and waste disposal expenses.
- Impact: Reduces overall operational costs, thereby increasing profit margins and financial stability.
Enhanced Competitive Advantage:
- How: Businesses that adopt energy and resource-efficient practices often lead in sustainability, attracting environmentally conscious customers and investors.
- Impact: Differentiates the company in the marketplace, fostering brand loyalty and potentially allowing for premium pricing.
Regulatory Compliance and Risk Mitigation:
- How: Meeting or exceeding environmental regulations avoids fines, sanctions, and legal liabilities.
- Impact: Ensures uninterrupted operations and builds a reputation for responsible governance, which can be appealing to stakeholders.
Innovation and Process Optimization:
- How: Focusing on efficiency drives innovation in production processes, leading to the development of new technologies and methods.
- Impact: Enhances productivity, reduces cycle times, and fosters a culture of continuous improvement, positioning the company for long-term growth.
Resource Security:
- How: Efficient use of resources ensures their availability for future operations and reduces dependency on volatile markets.
- Impact: Provides stability and resilience against supply chain disruptions, safeguarding the company’s operations over the long term.
Long-Term Economic Benefits:
Increased Profit Margins:
- Benefit: Lower operational costs translate directly into higher profit margins.
- Impact: Enhances the company’s financial health and provides funds for reinvestment and growth initiatives.
Attraction of Investment:
- Benefit: Investors are increasingly favoring companies with strong sustainability practices.
- Impact: Easier access to capital and potentially better financing terms, supporting expansion and innovation.
Market Expansion Opportunities:
- Benefit: Sustainable practices can open new markets and customer segments that prioritize environmental responsibility.
- Impact: Expands the company’s market reach and revenue streams, contributing to sustained business growth.
Long-Term Cost Savings:
- Benefit: Investments in energy-efficient technologies and processes often lead to ongoing savings.
- Impact: Compounds over time, significantly reducing the total cost of ownership and enhancing financial performance.
Enhanced Employee Satisfaction and Retention:
- Benefit: Employees are more likely to be engaged and committed in organizations that prioritize sustainability.
- Impact: Reduces turnover costs, attracts top talent, and fosters a motivated and productive workforce.
Conclusion: Energy and resource efficiency is a cornerstone of business sustainability, offering substantial long-term economic benefits such as cost reductions, enhanced competitive advantage, regulatory compliance, innovation, and resource security. By investing in efficient practices, manufacturers not only contribute to environmental preservation but also secure their financial future, ensuring sustained growth and success in a competitive and increasingly eco-conscious marketplace.
2. What are the most effective technologies currently available to improve energy and resource efficiency in manufacturing, and how do they work?
Answer:
Improving energy and resource efficiency in manufacturing involves the adoption of advanced technologies that optimize production processes, reduce waste, and enhance the utilization of essential inputs. The most effective technologies currently available encompass a range of solutions, from automation and smart systems to energy-efficient machinery and data analytics. These technologies work synergistically to create more efficient, sustainable, and cost-effective manufacturing environments.
Concepts:
- Energy-Efficient Machinery: Equipment designed to use less energy while maintaining or improving performance.
- Smart Systems: Integrated systems that utilize sensors, IoT, and data analytics to monitor and optimize operations in real-time.
Effective Technologies:
Internet of Things (IoT) and Industrial IoT (IIoT):
- How It Works: IoT devices and sensors collect real-time data on various aspects of the manufacturing process, such as energy consumption, machine performance, and resource usage.
- Impact: Enables continuous monitoring and optimization of operations, identifies inefficiencies, and facilitates predictive maintenance, thereby reducing energy and resource waste.
Energy Management Systems (EMS):
- How It Works: EMS integrate hardware and software to monitor, control, and optimize energy usage across the facility.
- Impact: Provides detailed insights into energy consumption patterns, identifies opportunities for savings, and automates energy-saving measures to enhance overall efficiency.
Advanced Robotics and Automation:
- How It Works: Robots and automated systems perform repetitive and precise tasks with minimal human intervention.
- Impact: Increases production efficiency, reduces energy consumption by optimizing task execution, and minimizes material waste through precise operations.
High-Efficiency HVAC Systems:
- How It Works: Utilizes advanced heating, ventilation, and air conditioning technologies designed to maximize energy efficiency.
- Impact: Reduces energy consumption associated with climate control, lowers operational costs, and enhances workplace comfort, contributing to overall energy savings.
Variable Frequency Drives (VFDs):
- How It Works: VFDs adjust the speed of motors based on real-time demand, optimizing energy use.
- Impact: Reduces energy consumption by ensuring motors operate only at the necessary speed, thereby lowering electricity usage and extending equipment lifespan.
LED Lighting and Smart Lighting Controls:
- How It Works: Replaces traditional lighting with LED technology and integrates smart controls that adjust lighting based on occupancy and natural light availability.
- Impact: Significantly reduces energy consumption for lighting, lowers maintenance costs, and enhances energy management within manufacturing facilities.
Additive Manufacturing (3D Printing):
- How It Works: Produces complex parts and prototypes layer by layer, minimizing material waste compared to traditional subtractive manufacturing.
- Impact: Reduces material consumption, lowers energy use in production, and allows for rapid prototyping and customization, enhancing resource efficiency.
Digital Twin Technology:
- How It Works: Creates a virtual replica of physical assets or processes to simulate and optimize performance.
- Impact: Enables real-time monitoring, predictive maintenance, and process optimization, leading to enhanced energy and resource efficiency through data-driven decision-making.
Big Data Analytics and Machine Learning:
- How It Works: Analyzes large volumes of data from manufacturing operations to identify patterns and optimize processes.
- Impact: Facilitates predictive maintenance, optimizes energy usage, and improves resource allocation, resulting in reduced waste and increased operational efficiency.
Heat Recovery Systems:
- How It Works: Captures and reuses waste heat generated during manufacturing processes.
- Impact: Reduces the need for additional energy input by repurposing waste heat, thereby lowering overall energy consumption and enhancing resource efficiency.
Water Recycling and Treatment Systems:
- How It Works: Implements systems to recycle and treat water used in manufacturing processes.
- Impact: Minimizes water consumption, reduces costs associated with water procurement and disposal, and supports sustainable resource management.
Supply Chain Optimization Tools:
- How It Works: Utilizes software and analytics to streamline supply chain operations, ensuring efficient material flow and reducing transportation-related energy use.
- Impact: Enhances resource efficiency by optimizing inventory levels, reducing transportation distances, and minimizing energy consumption across the supply chain.
Conclusion: The adoption of advanced technologies such as IoT, EMS, automation, high-efficiency HVAC systems, VFDs, LED lighting, additive manufacturing, digital twins, big data analytics, heat recovery systems, water recycling, and supply chain optimization tools significantly enhances energy and resource efficiency in manufacturing. These technologies work by providing real-time monitoring, optimizing processes, reducing waste, and enabling data-driven decision-making, thereby driving sustainability, reducing operational costs, and improving overall manufacturing performance.
3. How can manufacturers measure and benchmark their energy and resource efficiency, and what tools or frameworks are most effective for this purpose?
Answer:
Measuring and benchmarking energy and resource efficiency is essential for manufacturers to identify inefficiencies, track progress, and implement targeted improvements. Effective measurement and benchmarking involve establishing clear metrics, utilizing appropriate tools and frameworks, and continuously monitoring performance against industry standards or internal goals.
Concepts:
- Benchmarking: Comparing a company’s performance metrics to industry standards or best practices to identify areas for improvement.
- Key Performance Indicators (KPIs): Quantifiable measures used to evaluate the success of an organization in achieving objectives.
Measuring Energy and Resource Efficiency:
Establishing Baselines:
- How: Conduct an initial energy audit to determine current energy and resource usage levels across all manufacturing processes.
- Impact: Provides a reference point for measuring future improvements and identifying areas of high consumption.
Defining Key Performance Indicators (KPIs):
- Examples:
- Energy Consumption per Unit Produced: Measures the amount of energy used to produce one unit of product.
- Water Usage per Unit Produced: Quantifies the volume of water used per unit of production.
- Material Efficiency: Assesses the ratio of raw materials used to finished products.
- Waste Generation per Unit Produced: Tracks the amount of waste generated per unit of production.
- Examples:
Utilizing Energy Management Systems (EMS):
- How: Implement EMS to continuously monitor and collect data on energy and resource consumption.
- Impact: Provides real-time visibility into usage patterns, enabling timely identification of inefficiencies and tracking progress against KPIs.
Conducting Regular Energy Audits:
- How: Perform periodic energy audits to reassess energy and resource usage and identify new opportunities for improvement.
- Impact: Ensures that energy efficiency measures remain effective and adapts to changes in production processes or equipment.
Adopting International Standards and Frameworks:
- ISO 50001: An international standard for establishing, implementing, maintaining, and improving an Energy Management System.
- How: Follow the guidelines and requirements of ISO 50001 to systematically manage energy performance.
- Impact: Provides a structured approach to improving energy efficiency and achieving continuous improvement.
- Lean Manufacturing Principles: Utilize lean methodologies to identify and eliminate waste, optimizing resource use.
- How: Apply lean tools such as Value Stream Mapping (VSM), 5S, and Kaizen to streamline processes and reduce resource consumption.
- Impact: Enhances overall resource efficiency and operational performance.
- ISO 50001: An international standard for establishing, implementing, maintaining, and improving an Energy Management System.
Benchmarking Against Industry Standards:
- How: Compare performance metrics against industry benchmarks or best practices to gauge efficiency levels.
- Impact: Identifies gaps and sets realistic targets for improvement, fostering a culture of continuous enhancement.
Leveraging Data Analytics and Reporting Tools:
- How: Use data analytics platforms to analyze collected data, identify trends, and generate comprehensive reports on energy and resource usage.
- Impact: Facilitates informed decision-making and highlights areas where efficiency can be improved.
Engaging Third-Party Assessors:
- How: Hire external experts to conduct independent assessments of energy and resource efficiency.
- Impact: Provides unbiased insights and recommendations, ensuring objectivity in measuring and benchmarking performance.
Effective Tools and Frameworks:
Energy Management Systems (EMS):
- Features: Real-time monitoring, data collection, analytics, and reporting capabilities.
- Benefits: Streamlines the process of tracking energy usage, identifying inefficiencies, and implementing corrective actions.
ISO 50001 Energy Management Standard:
- Features: Framework for establishing energy policies, setting objectives, and implementing energy management practices.
- Benefits: Facilitates systematic energy performance improvement and ensures alignment with international best practices.
Lean Manufacturing Tools:
- Tools: Value Stream Mapping (VSM), 5S, Kaizen, and Total Productive Maintenance (TPM).
- Benefits: Identifies and eliminates waste, optimizes processes, and enhances resource efficiency through continuous improvement.
Benchmarking Software:
- Examples: Benchmarking dashboards and comparative analysis tools.
- Benefits: Enables comparison of performance metrics against industry standards, facilitating the identification of improvement opportunities.
Data Analytics Platforms:
- Examples: Big data analytics tools, machine learning algorithms, and business intelligence (BI) software.
- Benefits: Analyzes large volumes of data to uncover patterns, predict future energy needs, and optimize resource allocation.
Energy Auditing Tools:
- Examples: Portable energy meters, thermal imaging cameras, and energy assessment software.
- Benefits: Provides accurate measurements of energy consumption and identifies specific areas where efficiency can be improved.
Conclusion: Measuring and benchmarking energy and resource efficiency is fundamental for manufacturers aiming to optimize their operations and achieve sustainability goals. By establishing clear baselines, defining relevant KPIs, utilizing advanced tools and frameworks such as EMS and ISO 50001, and continuously monitoring and analyzing performance data, manufacturers can identify inefficiencies, implement targeted improvements, and sustain long-term energy and resource efficiency. Effective measurement and benchmarking not only drive cost savings and operational excellence but also contribute to the broader sustainability and environmental objectives of the organization.
4. What are the environmental impacts of inefficient energy and resource use in manufacturing, and how can improving efficiency mitigate these impacts?
Answer:
Inefficient energy and resource use in manufacturing have significant environmental impacts, contributing to pollution, resource depletion, and climate change. Improving energy and resource efficiency can mitigate these adverse effects by reducing the consumption of natural resources, lowering greenhouse gas emissions, minimizing waste generation, and promoting sustainable production practices.
Concepts:
- Environmental Impact: The effect of manufacturing activities on the natural environment.
- Sustainability: Meeting present needs without compromising the ability of future generations to meet theirs.
Environmental Impacts of Inefficient Energy and Resource Use:
Increased Greenhouse Gas Emissions:
- Impact: High energy consumption, particularly from fossil fuels, leads to increased emissions of carbon dioxide (CO₂) and other greenhouse gases.
- Consequences: Contributes to global warming, climate change, and associated extreme weather events.
Resource Depletion:
- Impact: Excessive use of raw materials and natural resources accelerates their depletion.
- Consequences: Leads to scarcity of essential resources, higher extraction costs, and environmental degradation from mining and extraction activities.
Pollution and Waste Generation:
- Impact: Inefficient processes often result in higher levels of industrial waste, including solid, liquid, and gaseous pollutants.
- Consequences: Contaminates air, water, and soil, harming ecosystems, wildlife, and human health.
Water Consumption and Pollution:
- Impact: High water usage in manufacturing processes can strain local water resources and lead to water pollution if not managed properly.
- Consequences: Affects aquatic life, reduces water availability for other uses, and degrades water quality.
Energy Waste and Thermal Pollution:
- Impact: Inefficient energy use generates excess heat, contributing to thermal pollution.
- Consequences: Alters local climate conditions, affects aquatic ecosystems, and increases cooling demands, further escalating energy consumption.
Habitat Destruction and Biodiversity Loss:
- Impact: Intensive resource extraction and waste disposal can lead to habitat destruction and loss of biodiversity.
- Consequences: Disrupts ecosystems, reduces species diversity, and weakens ecological resilience.
Mitigation Through Improved Efficiency:
Reduction in Greenhouse Gas Emissions:
- How: Lower energy consumption, especially from fossil fuels, decreases CO₂ and other greenhouse gas emissions.
- Impact: Mitigates climate change, reduces carbon footprint, and aligns with global emission reduction targets.
Conservation of Natural Resources:
- How: Efficient use of materials and resources extends their availability and reduces the need for excessive extraction.
- Impact: Preserves natural ecosystems, ensures resource sustainability, and lowers the environmental impact of resource extraction.
Minimization of Waste Generation:
- How: Streamlined processes and resource optimization reduce the amount of waste produced during manufacturing.
- Impact: Lowers pollution levels, decreases landfill usage, and reduces the environmental footprint of waste management.
Enhanced Water Management:
- How: Implement water-efficient technologies and recycling systems to reduce water consumption and prevent pollution.
- Impact: Conserves water resources, maintains water quality, and supports the health of aquatic ecosystems.
Reduction of Thermal Pollution:
- How: Optimize energy use and implement heat recovery systems to minimize excess heat generation.
- Impact: Reduces thermal pollution, lowers cooling energy demands, and mitigates local climate impacts.
Preservation of Biodiversity:
- How: Sustainable resource use and waste management practices protect habitats and support biodiversity.
- Impact: Maintains ecological balance, supports resilient ecosystems, and preserves wildlife populations.
Promotion of Circular Economy Practices:
- How: Embrace recycling, reuse, and remanufacturing to extend the lifecycle of materials and products.
- Impact: Reduces resource extraction, minimizes waste, and fosters sustainable production and consumption patterns.
Compliance with Environmental Regulations:
- How: Meeting or exceeding energy and resource efficiency standards ensures adherence to environmental laws.
- Impact: Prevents legal penalties, enhances corporate reputation, and demonstrates commitment to environmental stewardship.
Conclusion: Inefficient energy and resource use in manufacturing pose severe environmental challenges, including greenhouse gas emissions, resource depletion, pollution, and biodiversity loss. By improving energy and resource efficiency, manufacturers can significantly mitigate these impacts, promoting environmental sustainability and reducing their ecological footprint. Enhanced efficiency not only supports regulatory compliance and corporate responsibility but also contributes to the preservation of natural ecosystems, ensuring a healthier planet for future generations.
5. How can lean manufacturing principles be applied to enhance energy and resource efficiency, and what are the potential challenges in integrating these principles?
Answer:
Lean manufacturing principles focus on eliminating waste, optimizing processes, and enhancing value creation. Applying these principles to energy and resource efficiency involves systematically identifying and removing inefficiencies in the use of energy and materials, thereby promoting sustainable and cost-effective manufacturing practices. However, integrating lean principles with energy and resource efficiency initiatives presents certain challenges that organizations must navigate to achieve successful outcomes.
Concepts:
- Lean Manufacturing: A methodology that aims to maximize value by minimizing waste within manufacturing processes.
- Waste (Muda): Any activity that consumes resources without adding value to the product or service.
Application of Lean Principles to Enhance Efficiency:
Value Stream Mapping (VSM):
- How: Analyze and visualize the flow of materials and information through the production process to identify areas of waste.
- Impact: Highlights inefficiencies in energy and resource use, enabling targeted improvements to streamline operations and reduce consumption.
5S Workplace Organization:
- How: Implement the 5S methodology (Sort, Set in order, Shine, Standardize, Sustain) to organize the workplace efficiently.
- Impact: Enhances operational efficiency, reduces unnecessary movements and energy use, and creates a safer, more productive work environment.
Kaizen (Continuous Improvement):
- How: Foster a culture of continuous improvement where employees are encouraged to identify and implement small, incremental changes.
- Impact: Leads to ongoing enhancements in energy and resource efficiency through sustained, collaborative efforts.
Just-In-Time (JIT) Production:
- How: Align production schedules with actual demand to minimize inventory levels and reduce material waste.
- Impact: Lowers storage costs, reduces energy consumption associated with maintaining large inventories, and minimizes the risk of overproduction.
Total Productive Maintenance (TPM):
- How: Implement proactive maintenance practices to ensure equipment operates at peak efficiency.
- Impact: Reduces energy consumption by preventing equipment malfunctions and optimizing machine performance, thereby enhancing resource efficiency.
Standardized Work Procedures:
- How: Develop and implement standardized procedures for energy and resource use across all production processes.
- Impact: Ensures consistent and efficient use of resources, reducing variability and waste in operations.
Elimination of Non-Value-Added Activities:
- How: Identify and remove activities that do not add value to the product, such as excessive transportation, waiting times, and overprocessing.
- Impact: Decreases energy and resource consumption by streamlining operations and focusing on value-adding tasks.
Poka-Yoke (Error Proofing):
- How: Implement error-proofing mechanisms to prevent mistakes that can lead to waste.
- Impact: Reduces defects and rework, minimizing the associated energy and resource costs of correcting errors.
Potential Challenges in Integrating Lean Principles with Efficiency:
Cultural Resistance:
- Challenge: Employees and management may resist changes associated with lean initiatives due to comfort with existing practices.
- Solution: Foster a culture of continuous improvement, provide training, and involve employees in the change process to gain buy-in and support.
Initial Implementation Costs:
- Challenge: Implementing lean principles and energy-efficient technologies may require significant upfront investment.
- Solution: Conduct cost-benefit analyses to demonstrate the long-term savings and return on investment, and consider phased implementation to spread costs over time.
Complexity of Processes:
- Challenge: Complex manufacturing processes can make it difficult to identify and eliminate waste effectively.
- Solution: Use comprehensive tools like Value Stream Mapping to gain a clear understanding of processes and systematically address inefficiencies.
Sustainability of Improvements:
- Challenge: Maintaining lean and efficiency improvements over time can be challenging without continuous monitoring and reinforcement.
- Solution: Establish ongoing training, regular audits, and performance reviews to ensure that improvements are sustained and further enhancements are pursued.
Balancing Efficiency with Flexibility:
- Challenge: Striving for maximum efficiency may reduce the flexibility needed to respond to changing market demands or customization requests.
- Solution: Design lean processes that incorporate flexibility and adaptability, allowing for efficient yet responsive manufacturing operations.
Integration with Existing Systems:
- Challenge: Aligning lean principles with existing energy and resource management systems may require significant adjustments.
- Solution: Ensure that lean initiatives are integrated seamlessly with current systems by using compatible tools and aligning objectives across departments.
Measurement and Tracking Difficulties:
- Challenge: Accurately measuring the impact of lean initiatives on energy and resource efficiency can be complex.
- Solution: Define clear KPIs and utilize advanced monitoring tools to track performance and quantify the benefits of lean implementations.
Conclusion: Applying lean manufacturing principles to enhance energy and resource efficiency offers significant benefits, including reduced waste, lower operational costs, and improved sustainability. However, integrating these principles requires overcoming challenges such as cultural resistance, initial costs, and maintaining sustainability of improvements. By fostering a culture of continuous improvement, investing in training and technology, and systematically addressing inefficiencies, manufacturers can successfully merge lean methodologies with energy and resource efficiency initiatives, achieving sustainable and cost-effective production operations.
6. What are the barriers to implementing energy and resource efficiency initiatives in manufacturing, and how can organizations overcome them?
Answer:
Implementing energy and resource efficiency initiatives in manufacturing can be challenging due to a variety of barriers that hinder adoption and effectiveness. Understanding these obstacles and developing strategies to overcome them is essential for organizations aiming to enhance their sustainability and operational efficiency.
Concepts:
- Barriers to Efficiency: Factors that impede the adoption and successful implementation of energy and resource efficiency measures.
- Mitigation Strategies: Approaches and solutions designed to address and overcome barriers.
Common Barriers and Solutions:
High Initial Investment Costs:
- Barrier: Implementing energy-efficient technologies and systems often requires substantial upfront capital.
- Solution:
- How: Conduct thorough cost-benefit analyses to demonstrate the long-term savings and return on investment.
- Impact: Helps secure funding and justifies the initial expenditure by highlighting future financial gains.
- Alternative: Explore financing options, grants, and incentives offered by governments or organizations to offset initial costs.
Lack of Awareness and Expertise:
- Barrier: Insufficient knowledge about energy and resource efficiency practices and technologies can hinder effective implementation.
- Solution:
- How: Invest in training programs and hire experts in energy management and sustainability.
- Impact: Enhances the workforce’s ability to identify and implement efficiency measures.
- Collaboration: Partner with energy consultants or service providers to gain specialized knowledge and support.
Data Collection and Analysis Challenges:
- Barrier: Gathering accurate and comprehensive data on energy and resource usage can be technically complex and time-consuming.
- Solution:
- How: Implement advanced monitoring systems and energy management software to automate data collection and analysis.
- Impact: Streamlines the process of data gathering, ensures accuracy, and provides actionable insights for decision-making.
Resistance to Change:
- Barrier: Employees and management may resist adopting new processes or technologies due to comfort with existing practices or fear of job displacement.
- Solution:
- How: Foster a culture of continuous improvement and communicate the benefits of efficiency initiatives.
- Impact: Encourages buy-in and active participation from all levels of the organization.
- Incentives: Provide incentives and recognition for contributions to energy and resource efficiency efforts.
Integration with Existing Systems:
- Barrier: Difficulty in integrating new energy-efficient technologies with legacy systems and processes.
- Solution:
- How: Use interoperable technologies and ensure compatibility during the planning and implementation phases.
- Impact: Facilitates seamless integration, minimizing disruptions to ongoing operations.
- Upgrades: Gradually replace outdated systems to facilitate smoother integration and enhance overall efficiency.
Measurement and Tracking Difficulties:
- Barrier: Accurately measuring and tracking the impact of efficiency initiatives can be challenging without proper tools and frameworks.
- Solution:
- How: Define clear KPIs and utilize advanced monitoring and reporting tools to track performance.
- Impact: Enables precise measurement of efficiency gains and supports data-driven decision-making.
- Frameworks: Adopt international standards such as ISO 50001 to structure energy management and performance tracking.
Supply Chain Constraints:
- Barrier: Dependence on suppliers who may not prioritize energy and resource efficiency can limit the effectiveness of initiatives.
- Solution:
- How: Collaborate with suppliers to encourage and support their adoption of efficient practices.
- Impact: Enhances overall supply chain sustainability and ensures consistency in efficiency efforts.
- Standards: Set sustainability criteria for supplier selection and performance evaluation to promote aligned practices.
Technological Limitations:
- Barrier: Existing technologies may not fully support the desired levels of energy and resource efficiency.
- Solution:
- How: Invest in research and development to innovate and adopt cutting-edge technologies that enhance efficiency.
- Impact: Enables the implementation of more effective and efficient solutions, driving greater energy and resource savings.
- Upgrades: Regularly update and maintain equipment to ensure optimal performance and efficiency.
Regulatory and Compliance Issues:
- Barrier: Navigating complex and evolving regulations related to energy and resource usage can be challenging.
- Solution:
- How: Stay informed about relevant regulations and seek guidance from regulatory experts.
- Impact: Ensures compliance and avoids potential legal issues or fines.
- Proactive Measures: Implement proactive measures to exceed regulatory requirements and enhance sustainability practices.
Short-Term Focus Over Long-Term Benefits:
- Barrier: Emphasis on immediate cost savings rather than long-term sustainability gains can hinder the adoption of efficiency initiatives.
- Solution:
- How: Develop long-term sustainability goals and integrate them into the organization’s strategic planning.
- Impact: Balances short-term operational needs with long-term sustainability objectives, ensuring sustained efficiency improvements.
- Education: Educate stakeholders on the long-term financial and environmental benefits of energy and resource efficiency.
Complexity of Manufacturing Processes:
- Barrier: Complex and highly specialized manufacturing processes can make it difficult to identify and eliminate inefficiencies.
- Solution:
- How: Use comprehensive tools like Value Stream Mapping (VSM) to gain a clear understanding of processes and systematically address inefficiencies.
- Impact: Enables targeted and effective improvements, enhancing overall energy and resource efficiency.
Maintaining Continuous Improvement:
- Barrier: Sustaining energy and resource efficiency initiatives over time requires ongoing commitment and effort.
- Solution:
- How: Establish regular review processes, continuous training, and monitoring systems to maintain and build upon initial improvements.
- Impact: Ensures that efficiency gains are sustained and that the organization continues to adapt and improve its practices in response to changing conditions and technologies.
Conclusion: Manufacturers face a range of barriers when implementing energy and resource efficiency initiatives, including high initial costs, lack of expertise, data challenges, resistance to change, and supply chain constraints. By adopting strategic solutions such as investing in training, leveraging advanced technologies, fostering a culture of continuous improvement, and collaborating with suppliers, organizations can overcome these obstacles. Successfully addressing these barriers enables manufacturers to achieve significant energy and resource efficiency gains, leading to cost savings, enhanced sustainability, and improved competitiveness in the market.
7. How can digitalization and automation technologies be leveraged to enhance energy and resource efficiency in manufacturing?
Answer:
Digitalization and automation technologies are pivotal in enhancing energy and resource efficiency in manufacturing by enabling real-time monitoring, data-driven decision-making, process optimization, and reduced human intervention. These technologies transform traditional manufacturing operations into smarter, more efficient, and sustainable systems.
Concepts:
- Digitalization: Integration of digital technologies into all aspects of manufacturing, transforming operations and business models.
- Automation: Use of control systems and machinery to perform tasks with minimal human intervention.
Leveraging Digitalization and Automation:
Real-Time Monitoring and Data Collection:
- How: Utilize IoT sensors and connected devices to continuously monitor energy and resource usage across manufacturing processes.
- Impact: Provides detailed visibility into consumption patterns, identifying areas of inefficiency and enabling timely interventions to reduce waste.
Advanced Data Analytics:
- How: Apply big data analytics and machine learning algorithms to analyze collected data and uncover insights into energy and resource use.
- Impact: Facilitates predictive maintenance, process optimization, and informed decision-making to enhance efficiency and reduce consumption.
Automated Control Systems:
- How: Implement programmable logic controllers (PLCs) and distributed control systems (DCS) to automate and optimize manufacturing processes.
- Impact: Ensures precise control over operations, reducing energy and resource use by maintaining optimal process conditions and minimizing variability.
Energy Management Systems (EMS):
- How: Integrate EMS with digital and automated systems to manage and optimize energy use across the facility.
- Impact: Enables centralized monitoring and control of energy consumption, identifying opportunities for savings and enhancing overall energy efficiency.
Smart Manufacturing Platforms:
- How: Use integrated digital platforms that connect various manufacturing systems and provide a unified view of operations.
- Impact: Enhances coordination and optimization of resources, reducing redundancies and improving efficiency across the production process.
Robotics and Automated Machinery:
- How: Deploy energy-efficient robots and automated machinery to perform repetitive and precise tasks.
- Impact: Reduces energy consumption by optimizing task execution and minimizing idle times, while also enhancing productivity and consistency.
Digital Twin Technology:
- How: Create digital replicas of physical manufacturing systems to simulate and optimize energy and resource use.
- Impact: Enables real-time monitoring, predictive maintenance, and process optimization, leading to enhanced energy and resource efficiency through data-driven decision-making.
Predictive Maintenance:
- How: Use automation and data analytics to predict equipment failures and schedule maintenance proactively.
- Impact: Prevents unexpected downtime, ensures machines operate at peak efficiency, and reduces energy waste associated with malfunctioning equipment.
Supply Chain Digitalization:
- How: Digitize supply chain processes to optimize material flow and reduce transportation-related energy use.
- Impact: Enhances resource efficiency by ensuring timely delivery of materials, reducing excess inventory, and minimizing energy consumption in logistics.
Virtual and Augmented Reality (VR/AR):
- How: Utilize VR and AR for training, maintenance, and process visualization.
- Impact: Improves operational efficiency by enhancing workforce skills, reducing errors, and enabling more efficient troubleshooting and maintenance processes.
Benefits of Leveraging Digitalization and Automation:
- Increased Efficiency: Streamlined processes and optimized resource use lead to higher productivity and lower operational costs.
- Reduced Energy Consumption: Precise control and real-time optimization minimize energy waste and enhance sustainability.
- Enhanced Flexibility: Digital and automated systems allow for quick adjustments to changing production demands, improving responsiveness.
- Improved Quality: Consistent and precise operations reduce defects and enhance product quality.
- Cost Savings: Lower energy and resource use translate into significant cost reductions, improving profitability.
- Sustainability: Reduced environmental impact through optimized energy and resource use aligns with corporate sustainability goals and regulatory requirements.
Conclusion: Digitalization and automation technologies are essential drivers of energy and resource efficiency in modern manufacturing. By enabling real-time monitoring, data-driven optimization, precise control, and proactive maintenance, these technologies transform manufacturing operations into highly efficient and sustainable systems. Embracing digital and automated solutions not only enhances operational performance and reduces costs but also supports broader sustainability objectives, positioning manufacturers for long-term success in a competitive and eco-conscious market.
8. What role does employee training and engagement play in achieving energy and resource efficiency in manufacturing, and how can organizations foster this?
Answer:
Employee training and engagement are critical components in achieving energy and resource efficiency in manufacturing. Educated and motivated employees are essential for identifying inefficiencies, implementing best practices, and sustaining energy and resource-saving initiatives. Organizations can foster effective training and engagement through a combination of education, incentives, participation, and a supportive culture.
Concepts:
- Employee Training: Providing education and skills development to enhance employee capabilities.
- Employee Engagement: Involving and motivating employees to actively participate in organizational goals and initiatives.
Role of Employee Training and Engagement:
Awareness and Understanding:
- How: Educate employees about the importance of energy and resource efficiency and how their actions impact overall performance.
- Impact: Increases awareness and fosters a sense of responsibility towards conserving resources and reducing energy consumption.
Skill Development:
- How: Provide training on the use of energy-efficient technologies, best practices for resource management, and identification of inefficiencies.
- Impact: Equips employees with the necessary skills to implement and sustain energy and resource-saving measures effectively.
Encouraging Innovation:
- How: Involve employees in brainstorming and implementing energy and resource efficiency initiatives.
- Impact: Leverages diverse perspectives and ideas, leading to innovative solutions and continuous improvement in efficiency efforts.
Empowering Employees:
- How: Give employees the authority and tools to make decisions that contribute to energy and resource efficiency.
- Impact: Enhances employee ownership of efficiency initiatives, leading to more proactive and sustained efforts.
Creating a Culture of Sustainability:
- How: Foster an organizational culture that values and prioritizes sustainability and efficiency through leadership support and communication.
- Impact: Encourages collective commitment and alignment towards energy and resource efficiency goals.
Recognition and Incentives:
- How: Implement recognition programs and incentives for employees who contribute significantly to energy and resource-saving measures.
- Impact: Motivates employees to actively participate and excel in efficiency efforts, reinforcing positive behaviors.
Continuous Feedback and Improvement:
- How: Provide regular feedback on energy and resource performance and involve employees in reviewing and refining efficiency strategies.
- Impact: Promotes a continuous improvement mindset, ensuring that efficiency measures remain effective and relevant.
Strategies to Foster Employee Training and Engagement:
Comprehensive Training Programs:
- How: Develop and deliver structured training programs that cover energy and resource efficiency concepts, technologies, and practices.
- Impact: Ensures that all employees have a foundational understanding and the skills needed to contribute to efficiency efforts.
Interactive Workshops and Seminars:
- How: Conduct interactive sessions where employees can engage in hands-on learning and discuss real-world efficiency challenges and solutions.
- Impact: Enhances engagement and practical understanding, encouraging active participation and collaboration.
Green Teams and Sustainability Committees:
- How: Establish dedicated teams or committees focused on driving energy and resource efficiency initiatives.
- Impact: Provides a structured platform for employee involvement and leadership in sustainability efforts.
Internal Communication and Awareness Campaigns:
- How: Use newsletters, posters, and digital platforms to communicate the importance of efficiency initiatives and share success stories.
- Impact: Keeps energy and resource efficiency top-of-mind and maintains ongoing engagement and motivation among employees.
Incentive Programs:
- How: Offer rewards, bonuses, or recognition for employees who identify and implement significant energy and resource-saving measures.
- Impact: Encourages proactive efforts and reinforces the value of employee contributions to efficiency goals.
Leadership Involvement:
- How: Ensure that organizational leaders actively support and participate in energy and resource efficiency initiatives.
- Impact: Demonstrates commitment from the top, inspiring employees to follow suit and prioritize sustainability.
Accessible Resources and Tools:
- How: Provide employees with access to tools, guidelines, and resources that facilitate energy and resource efficiency practices.
- Impact: Empowers employees to take action and implement efficiency measures effectively.
Feedback Mechanisms:
- How: Implement systems for employees to provide feedback, suggestions, and report inefficiencies or opportunities for improvement.
- Impact: Engages employees in the continuous improvement process and ensures that efficiency initiatives are responsive to on-the-ground insights.
Conclusion: Employee training and engagement are essential for achieving energy and resource efficiency in manufacturing. By educating employees, fostering a culture of sustainability, encouraging innovation, and providing incentives, organizations can empower their workforce to actively contribute to efficiency initiatives. Effective training and engagement strategies ensure that energy and resource-saving measures are implemented successfully and sustained over time, leading to significant cost savings, enhanced operational performance, and a positive environmental impact.
9. What role do energy management systems (EMS) play in enhancing energy efficiency in manufacturing, and how are they implemented?
Answer:
Energy Management Systems (EMS) play a critical role in enhancing energy efficiency in manufacturing by providing a structured framework for monitoring, controlling, and optimizing energy usage across all facets of production operations. An EMS enables manufacturers to systematically manage energy consumption, identify inefficiencies, and implement targeted improvements, thereby reducing costs and minimizing environmental impact.
Concepts:
- Energy Management Systems (EMS): Integrated systems that collect, monitor, and analyze energy usage data to optimize energy performance.
- ISO 50001: An international standard that specifies requirements for establishing, implementing, maintaining, and improving an EMS.
Role of EMS in Enhancing Energy Efficiency:
Comprehensive Energy Monitoring:
- How: EMS continuously tracks energy consumption across different departments, machines, and processes.
- Impact: Provides detailed visibility into energy usage patterns, identifying high-consumption areas and potential inefficiencies.
Data Analysis and Reporting:
- How: Analyzes energy data to identify trends, anomalies, and opportunities for improvement.
- Impact: Enables informed decision-making and supports the development of targeted energy-saving strategies.
Setting Energy Goals and Targets:
- How: Establishes specific, measurable energy performance goals based on baseline data.
- Impact: Provides clear objectives for reducing energy consumption and enhances accountability within the organization.
Implementing Energy-Saving Measures:
- How: Identifies and implements initiatives such as equipment upgrades, process optimizations, and behavioral changes to reduce energy use.
- Impact: Achieves tangible reductions in energy consumption and operational costs.
Continuous Improvement:
- How: Regularly reviews energy performance and updates strategies to enhance efficiency.
- Impact: Ensures sustained energy savings and adapts to changing operational conditions and technological advancements.
Compliance and Certification:
- How: Adheres to energy-related regulations and standards, and seeks certifications like ISO 50001.
- Impact: Demonstrates commitment to energy efficiency and sustainability, enhancing the organization’s reputation and market position.
Implementation of EMS:
Energy Assessment:
- How: Conduct a thorough assessment to establish a baseline of current energy usage and identify major energy-consuming processes and equipment.
- Impact: Provides a foundation for setting realistic energy goals and identifying improvement opportunities.
Setting Up the EMS Framework:
- How: Define the scope, objectives, and policies for energy management within the organization.
- Impact: Establishes a clear structure and direction for energy efficiency initiatives.
Installing Monitoring Equipment:
- How: Deploy sensors and meters to collect real-time energy data from various parts of the manufacturing facility.
- Impact: Enables accurate and comprehensive energy monitoring.
Data Collection and Integration:
- How: Integrate energy data into the EMS software platform for centralized analysis and management.
- Impact: Facilitates seamless data access and enhances analytical capabilities.
Training and Engagement:
- How: Educate employees about the EMS, its benefits, and their roles in achieving energy efficiency goals.
- Impact: Promotes a culture of energy awareness and encourages active participation in energy conservation efforts.
Developing Energy Management Plans:
- How: Create detailed plans outlining specific actions, timelines, and responsibilities for energy efficiency projects.
- Impact: Provides a roadmap for implementing energy-saving measures and tracking progress.
Implementing Energy-Saving Projects:
- How: Execute identified projects such as upgrading to energy-efficient lighting, optimizing HVAC systems, or improving process controls.
- Impact: Achieves direct reductions in energy consumption and operational costs.
Monitoring and Reporting:
- How: Continuously monitor energy usage and generate regular reports to track performance against set goals.
- Impact: Ensures transparency, accountability, and facilitates ongoing improvements.
Review and Optimization:
- How: Regularly review EMS performance and adjust strategies based on data insights and changing conditions.
- Impact: Maintains the effectiveness of the EMS and ensures continuous improvement in energy efficiency.
Conclusion: Energy Management Systems are essential tools for enhancing energy efficiency in manufacturing. By providing comprehensive monitoring, data-driven analysis, goal setting, and continuous improvement frameworks, EMS enables manufacturers to systematically reduce energy consumption, lower operational costs, and promote sustainable practices. Proper implementation of an EMS, supported by employee engagement and strategic planning, ensures long-term energy efficiency and operational excellence.
10. How can manufacturers measure and benchmark their energy and resource efficiency, and what tools or frameworks are most effective for this purpose?
Answer:
Measuring and benchmarking energy and resource efficiency is essential for manufacturers to identify inefficiencies, track progress, and implement targeted improvements. Effective measurement and benchmarking involve establishing clear metrics, utilizing appropriate tools and frameworks, and continuously monitoring performance against industry standards or internal goals.
Concepts:
- Benchmarking: Comparing a company’s performance metrics to industry standards or best practices to identify areas for improvement.
- Key Performance Indicators (KPIs): Quantifiable measures used to evaluate the success of an organization in achieving objectives.
Measuring Energy and Resource Efficiency:
Establishing Baselines:
- How: Conduct an initial energy audit to determine current energy and resource usage levels across all manufacturing processes.
- Impact: Provides a reference point for measuring future improvements and identifying areas of high consumption.
Defining Key Performance Indicators (KPIs):
- Examples:
- Energy Consumption per Unit Produced: Measures the amount of energy used to produce one unit of product.
- Water Usage per Unit Produced: Quantifies the volume of water used per unit of production.
- Material Efficiency: Assesses the ratio of raw materials used to finished products.
- Waste Generation per Unit Produced: Tracks the amount of waste generated per unit of production.
- Examples:
Utilizing Energy Management Systems (EMS):
- How: Implement EMS to continuously monitor and collect data on energy and resource consumption.
- Impact: Provides real-time visibility into usage patterns, enabling timely identification of inefficiencies and tracking progress against KPIs.
Conducting Regular Energy Audits:
- How: Perform periodic energy audits to reassess energy and resource usage and identify new opportunities for improvement.
- Impact: Ensures that energy efficiency measures remain effective and adapts to changes in production processes or equipment.
Adopting International Standards and Frameworks:
- ISO 50001: An international standard for establishing, implementing, maintaining, and improving an Energy Management System.
- How: Follow the guidelines and requirements of ISO 50001 to systematically manage energy performance.
- Impact: Provides a structured approach to improving energy efficiency and achieving continuous improvement.
- Lean Manufacturing Principles: Utilize lean methodologies to identify and eliminate waste, optimizing resource use.
- How: Apply lean tools such as Value Stream Mapping (VSM), 5S, and Kaizen to streamline processes and reduce resource consumption.
- Impact: Enhances overall resource efficiency and operational performance.
- ISO 50001: An international standard for establishing, implementing, maintaining, and improving an Energy Management System.
Benchmarking Against Industry Standards:
- How: Compare performance metrics against industry benchmarks or best practices to gauge efficiency levels.
- Impact: Identifies gaps and sets realistic targets for improvement, fostering a culture of continuous enhancement.
Leveraging Data Analytics and Reporting Tools:
- How: Use data analytics platforms to analyze collected data, identify trends, and generate comprehensive reports on energy and resource usage.
- Impact: Facilitates informed decision-making and highlights areas where efficiency can be improved.
Engaging Third-Party Assessors:
- How: Hire external experts to conduct independent assessments of energy and resource efficiency.
- Impact: Provides unbiased insights and recommendations, ensuring objectivity in measuring and benchmarking performance.
Effective Tools and Frameworks:
Energy Management Systems (EMS):
- Features: Real-time monitoring, data collection, analytics, and reporting capabilities.
- Benefits: Streamlines the process of tracking energy usage, identifying inefficiencies, and implementing corrective actions.
ISO 50001 Energy Management Standard:
- Features: Framework for establishing energy policies, setting objectives, and implementing energy management practices.
- Benefits: Facilitates systematic energy performance improvement and ensures alignment with international best practices.
Lean Manufacturing Tools:
- Tools: Value Stream Mapping (VSM), 5S, Kaizen, and Total Productive Maintenance (TPM).
- Benefits: Identifies and eliminates waste, optimizes processes, and enhances resource efficiency through continuous improvement.
Benchmarking Software:
- Examples: Benchmarking dashboards and comparative analysis tools.
- Benefits: Enables comparison of performance metrics against industry standards, facilitating the identification of improvement opportunities.
Data Analytics Platforms:
- Examples: Big data analytics tools, machine learning algorithms, and business intelligence (BI) software.
- Benefits: Analyzes large volumes of data to uncover patterns, predict future energy needs, and optimize resource allocation.
Energy Auditing Tools:
- Examples: Portable energy meters, thermal imaging cameras, and energy assessment software.
- Benefits: Provides accurate measurements of energy consumption and identifies specific areas where efficiency can be improved.
Conclusion: Measuring and benchmarking energy and resource efficiency is fundamental for manufacturers aiming to optimize their operations and achieve sustainability goals. By establishing clear baselines, defining relevant KPIs, utilizing advanced tools and frameworks such as EMS and ISO 50001, and continuously monitoring and analyzing performance data, manufacturers can identify inefficiencies, implement targeted improvements, and sustain long-term energy and resource efficiency. Effective measurement and benchmarking not only drive cost savings and operational excellence but also contribute to the broader sustainability and environmental objectives of the organization.
11. How can manufacturers implement water conservation measures without compromising production quality or efficiency?
Answer:
Implementing water conservation measures in manufacturing is essential for reducing environmental impact and operational costs. However, manufacturers must ensure that these measures do not compromise production quality or efficiency. Achieving this balance requires a strategic approach that integrates water-efficient technologies, process optimizations, and best practices while maintaining high-quality standards and operational performance.
Concepts:
- Water Conservation: Strategies and practices aimed at reducing water usage and promoting sustainable water management.
- Production Quality: The standard of a product’s performance, reliability, and durability as defined by design specifications and customer expectations.
Strategies for Water Conservation:
Water Audits and Assessment:
- How: Conduct comprehensive water audits to identify areas of high water consumption and potential inefficiencies.
- Impact: Provides a clear understanding of current water usage patterns, enabling targeted conservation efforts without affecting production quality.
Implementing Water Recycling and Reuse Systems:
- How: Install systems that treat and recycle wastewater for use in non-critical processes such as cooling, cleaning, or landscaping.
- Impact: Reduces overall water consumption and dependence on external water sources, while maintaining sufficient water supply for essential production activities.
Adopting Closed-Loop Water Systems:
- How: Design and implement closed-loop systems that continuously recycle water within the manufacturing process.
- Impact: Minimizes water waste and ensures consistent water quality, preventing disruptions to production and maintaining product standards.
Upgrading to Water-Efficient Equipment:
- How: Replace outdated machinery and equipment with water-efficient alternatives that use less water without compromising functionality.
- Impact: Lowers water consumption while maintaining or enhancing production efficiency and quality.
Optimizing Process Water Usage:
- How: Analyze and streamline manufacturing processes to reduce unnecessary water use through precision dosing, improved flow controls, and minimizing leaks.
- Impact: Enhances water efficiency without affecting the quality or quantity of production outputs.
Implementing Advanced Treatment Technologies:
- How: Use technologies such as reverse osmosis, ultrafiltration, or UV treatment to purify and reuse water within the manufacturing process.
- Impact: Ensures high-quality water reuse, maintaining production standards while conserving water resources.
Employee Training and Awareness:
- How: Educate employees about the importance of water conservation and train them on best practices for reducing water use.
- Impact: Encourages proactive participation in water-saving initiatives, fostering a culture of sustainability that supports efficient water use without impacting production.
Regular Maintenance and Monitoring:
- How: Implement routine maintenance schedules and monitoring systems to detect and fix leaks or inefficiencies promptly.
- Impact: Prevents water loss due to leaks and ensures that water-efficient systems operate effectively, maintaining production quality.
Implementing Demand-Controlled Water Systems:
- How: Use automated systems that adjust water flow based on real-time demand and production needs.
- Impact: Ensures that water is used only when necessary, optimizing usage without affecting production processes.
Collaborating with Suppliers and Partners:
- How: Work with suppliers to source water-efficient materials and technologies that support overall water conservation goals.
- Impact: Extends water conservation efforts beyond the manufacturing facility, enhancing sustainability throughout the supply chain.
Ensuring Production Quality and Efficiency:
Pilot Testing and Validation:
- How: Conduct pilot tests of water conservation measures to evaluate their impact on production quality and efficiency before full-scale implementation.
- Impact: Identifies potential issues and allows for adjustments to ensure that conservation measures do not negatively affect production outcomes.
Continuous Monitoring and Feedback:
- How: Use real-time monitoring systems to track the performance of water conservation initiatives and gather feedback from production teams.
- Impact: Enables continuous adjustments and optimizations to maintain production quality and efficiency while conserving water.
Integrated Approach:
- How: Align water conservation efforts with overall production goals and quality standards, ensuring that initiatives support both sustainability and operational objectives.
- Impact: Creates a harmonious balance between water conservation and production efficiency, maintaining high-quality outputs.
Quality Control Measures:
- How: Implement stringent quality control protocols to monitor product quality during and after the implementation of water conservation measures.
- Impact: Ensures that any changes in water usage do not compromise the integrity or performance of the final products.
Conclusion: Manufacturers can implement water conservation measures without compromising production quality or efficiency by adopting a strategic approach that includes water audits, recycling systems, efficient equipment, process optimizations, advanced treatment technologies, and employee engagement. By integrating these measures thoughtfully and continuously monitoring their impact, organizations can achieve significant water savings while maintaining high standards of production quality and operational performance. This balance not only supports environmental sustainability but also enhances operational resilience and cost-effectiveness.
12. How can circular economy principles be integrated into manufacturing processes to enhance resource efficiency, and what are the benefits of such integration?
Answer:
Integrating circular economy principles into manufacturing processes significantly enhances resource efficiency by promoting the continual use of resources, minimizing waste, and fostering sustainable production and consumption patterns. The circular economy model contrasts with the traditional linear economy by emphasizing the reuse, recycling, and regeneration of materials, thereby creating a closed-loop system that sustains resources and reduces environmental impact.
Concepts:
- Circular Economy: An economic system aimed at eliminating waste and the continual use of resources through recycling, reuse, and regeneration.
- Resource Efficiency: Maximizing the value obtained from resources while minimizing waste and environmental impact.
Integration of Circular Economy Principles:
Design for Longevity and Durability:
- How: Develop products that are built to last longer, with components that can be easily repaired or replaced.
- Impact: Extends the lifecycle of products, reducing the need for frequent replacements and conserving resources.
Design for Disassembly and Recycling:
- How: Create products with modular components that can be easily disassembled and recycled at the end of their lifecycle.
- Impact: Facilitates the efficient recovery and reuse of materials, minimizing waste and supporting a closed-loop system.
Material Selection and Innovation:
- How: Choose sustainable, recyclable, or bio-based materials for product manufacturing.
- Impact: Enhances resource efficiency by using materials that have lower environmental impact and are easier to recycle or regenerate.
Implementing Reverse Logistics:
- How: Establish systems for collecting, returning, and processing used products or materials from customers.
- Impact: Enables the reuse and recycling of materials, reducing the demand for virgin resources and minimizing waste.
Recycling and Remanufacturing:
- How: Develop processes to recycle waste materials and remanufacture used products into new ones.
- Impact: Conserves resources, reduces environmental pollution, and lowers production costs by reusing existing materials.
Product-as-a-Service (PaaS) Models:
- How: Shift from selling products to providing products as services, retaining ownership and responsibility for product lifecycle management.
- Impact: Encourages manufacturers to design products for longevity and ease of maintenance, promoting resource efficiency and reducing waste.
Resource Sharing and Collaborative Consumption:
- How: Facilitate the sharing of resources and products among multiple users or organizations.
- Impact: Maximizes the utilization of resources, reduces the need for new products, and minimizes overall resource consumption.
Energy and Resource Recovery:
- How: Implement systems to recover and reuse energy and materials from waste streams.
- Impact: Enhances resource efficiency by converting waste into usable energy or materials, supporting a closed-loop system.
Lifecycle Assessment (LCA):
- How: Conduct LCAs to evaluate the environmental impact of products throughout their lifecycle, from raw material extraction to disposal.
- Impact: Identifies opportunities for improving resource efficiency and reducing environmental impact at each stage of the product lifecycle.
Digital Technologies and Automation:
- How: Use digital twins, IoT, and automation to monitor, track, and optimize resource use throughout the manufacturing process.
- Impact: Enhances the ability to implement circular economy practices by providing real-time data and insights into resource flows and waste generation.
Benefits of Integrating Circular Economy Principles:
Enhanced Resource Efficiency:
- Benefit: Maximizes the utilization of materials and reduces the need for virgin resources.
- Impact: Lowers production costs, conserves natural resources, and supports sustainable growth.
Waste Minimization:
- Benefit: Reduces the generation of waste through recycling, reuse, and remanufacturing.
- Impact: Lowers disposal costs, minimizes environmental pollution, and supports regulatory compliance.
Cost Savings:
- Benefit: Decreases material costs by reusing and recycling existing resources.
- Impact: Improves profitability and financial resilience by reducing dependency on fluctuating raw material prices.
Environmental Sustainability:
- Benefit: Lowers the environmental footprint by reducing resource extraction, energy consumption, and waste generation.
- Impact: Contributes to climate change mitigation, biodiversity conservation, and overall environmental health.
Innovation and Competitive Advantage:
- Benefit: Drives innovation in product design, materials, and manufacturing processes.
- Impact: Differentiates the company in the market, attracting environmentally conscious customers and partners.
Regulatory Compliance and Risk Mitigation:
- Benefit: Aligns with increasing regulatory requirements for sustainability and waste reduction.
- Impact: Avoids legal penalties, enhances corporate reputation, and reduces operational risks associated with environmental non-compliance.
Improved Brand Image and Customer Loyalty:
- Benefit: Demonstrates commitment to sustainability, enhancing the company’s reputation.
- Impact: Builds trust and loyalty among customers, leading to increased sales and market share.
Resilience and Adaptability:
- Benefit: Creates a more resilient supply chain by reducing dependency on scarce or volatile resources.
- Impact: Enhances the ability to adapt to market changes and resource availability, ensuring long-term operational stability.
Employee Engagement and Satisfaction:
- Benefit: Fosters a culture of sustainability and innovation, engaging employees in meaningful initiatives.
- Impact: Enhances employee morale, reduces turnover, and attracts talent aligned with sustainability values.
Long-Term Financial Performance:
- Benefit: Sustainable practices lead to cost savings, increased efficiency, and new revenue streams.
- Impact: Contributes to long-term financial health and shareholder value.
Conclusion: Integrating circular economy principles into manufacturing processes significantly enhances resource efficiency by promoting the continual use of materials, minimizing waste, and fostering sustainable production practices. The benefits of such integration include cost savings, environmental sustainability, innovation, competitive advantage, and improved brand reputation. By embracing circular economy models, manufacturers can create more resilient, efficient, and sustainable operations that meet the demands of modern markets while contributing positively to the environment and society.
Conclusion:
The above thought-provoking questions and detailed answers provide a comprehensive exploration of energy and resource efficiency in manufacturing. Covering fundamental concepts, strategies, technologies, challenges, and the integration of sustainable practices, these questions facilitate a deep understanding of how manufacturers can optimize their operations for greater sustainability and efficiency. Engaging with these questions equips students and professionals with the knowledge to implement effective energy and resource-saving measures, drive continuous improvement, and contribute to sustainable manufacturing practices that benefit both organizations and the environment.