Additive Manufacturing (3D Printing)
Additive Manufacturing (3D Printing) has revolutionized the way we conceive, prototype, and produce objects, breaking away from traditional subtractive processes by building components layer by layer. This innovative approach aligns closely with broader developments in Industrial and Manufacturing Technologies, offering unprecedented design freedom and rapid iteration cycles. It plays a critical role in accelerating product development and creating complex geometries that were previously difficult or impossible to fabricate.
The synergy between additive processes and Advanced Materials and Manufacturing Technologies allows engineers to explore high-performance composites, metals, and polymers tailored for aerospace, biomedical, and automotive sectors. This capability is further amplified by the integration of Computer-Integrated Manufacturing (CIM) systems and Digital Twin Technology, enabling digital workflows that simulate, monitor, and optimize the manufacturing process in real time.
As sustainability becomes central to industrial strategy, additive techniques contribute to Energy and Resource Efficiency in Manufacturing. By minimizing waste, reducing the need for tooling, and enabling local production, 3D printing aligns with the goals of Sustainable Manufacturing. Additionally, its flexibility supports leaner operations, complementing methods taught under Lean Manufacturing.
A successful 3D printing implementation depends on quality assurance and human-centered design. Topics such as Manufacturing Quality Control and Assurance ensure part reliability, while Human Factors and Ergonomics in Manufacturing play a role in optimizing interfaces, equipment usage, and operator comfort. 3D printing is also closely linked to modern frameworks such as Smart Manufacturing and Industry 4.0, where connectivity and automation redefine industrial possibilities.
Beyond prototyping, additive manufacturing reshapes how supply chains function. Its decentralized nature integrates with Supply Chain Management, allowing on-demand production and reduced inventory. It also supports customized fabrication in sectors like Biomechanical Engineering, where prosthetics and implants are tailored to individual anatomical needs.
The growing relevance of 3D printing within Mechanical Engineering is reflected in diverse applications. From lightweight parts in Automotive Engineering to personalized instruments in Robotics and Automation in Mech Eng, additive manufacturing enhances mechanical functionality. Mastery of supporting concepts like Solid Mechanics, Fluid Mechanics and Hydraulics, and Thermodynamics and Heat Transfer is crucial for understanding part performance in real-world conditions.
Design flexibility is a hallmark of additive manufacturing. Coupled with Mechanical Design and Computer-Aided Design (CAD), it allows engineers to create organic, topology-optimized shapes unconstrained by machining limitations. These developments also depend on emerging materials, which are increasingly influenced by Nanotechnology and Advanced Materials in Mech Eng.
3D printing’s integration with Manufacturing and Production Engineering and Control Systems in Mech Engineering demonstrates how modern manufacturing is evolving into a flexible, digitally enabled ecosystem. As additive technologies continue to mature, they redefine not just how we make things—but how we think about engineering, sustainability, and creativity.
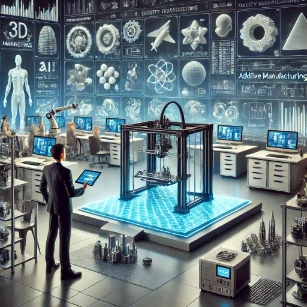
Table of Contents
Core Concepts of Additive Manufacturing
The Additive Manufacturing Process
- Digital Design:
- At the heart of additive manufacturing (AM) lies the digital design process, where engineers and designers create a 3D model using Computer-Aided Design (CAD) software. This virtual prototype serves as the blueprint for the final object, allowing for precise control over geometry, dimensions, and functional features.
- Once the model is finalized, it is exported into a printable format such as STL (Standard Tessellation Language) or OBJ, which breaks the complex geometry into a mesh of triangles that can be interpreted by the printer software. This step is critical, as the accuracy of the digital representation directly influences the quality of the final printed part.
- Slicing:
- Slicing software transforms the 3D model into a series of horizontal layers, often as thin as microns, generating a toolpath that the printer follows. Each layer represents a cross-sectional slice of the final object, and the instructions include print speed, temperature, material deposition rate, and movement coordinates.
- This step also allows for the inclusion of support structures, particularly for overhanging features, which are essential in preventing deformation during printing. The sliced file ensures consistent material flow and structural integrity during layer-by-layer construction.
- Material Deposition:
- The core phase of AM involves depositing material, typically in liquid, powder, or filament form, layer by layer according to the defined toolpath. This additive approach stands in contrast to subtractive manufacturing, where material is removed from a solid block.
- Depending on the technology, materials may be extruded, cured with lasers or UV light, or sintered with heat or energy beams. The sequential nature of layer buildup allows for highly complex geometries, including internal channels and lattice structures, that would be difficult or impossible to produce using traditional methods.
- Post-Processing:
- After printing, post-processing steps refine the object’s appearance, mechanical properties, and functionality. These steps may include removing support structures, washing off residual powders or resins, sanding for smoother surfaces, and thermal treatments to enhance strength.
- Post-processing is particularly important in industries such as aerospace and medical, where surface finish and material integrity are critical. In some cases, additional machining or coating is applied to meet precise engineering standards.
Additive Manufacturing Technologies
- Fused Deposition Modeling (FDM):
- FDM is one of the most accessible and widely used 3D printing technologies. It works by extruding a thermoplastic filament through a heated nozzle, which deposits material in layers to form the final part.
- Commonly used materials include PLA (polylactic acid), ABS (acrylonitrile butadiene styrene), and PETG (polyethylene terephthalate glycol). FDM is particularly useful for rapid prototyping, educational use, and low-volume production.
- Stereolithography (SLA):
- SLA uses an ultraviolet laser to selectively cure a photopolymer resin, building the part layer by layer from a vat of liquid material. This method is renowned for its high resolution and smooth surface finish, making it ideal for applications requiring fine detail.
- It is extensively used in industries such as dentistry, jewelry design, and engineering, where precision is crucial. Despite its detail, SLA-printed parts may require post-curing and handling precautions due to material brittleness.
- Selective Laser Sintering (SLS):
- SLS fuses powdered materials—typically nylon or polymers—using a high-powered laser. As each layer is sintered, fresh powder is spread over the surface, allowing continuous building without the need for support structures.
- SLS is ideal for producing functional prototypes, complex geometries, and short-run production parts. The process is highly valued in automotive and aerospace sectors for producing components with good mechanical strength and thermal resistance.
- Direct Metal Laser Sintering (DMLS) / Selective Laser Melting (SLM):
- These technologies melt or sinter metal powders using high-energy lasers to produce dense, high-strength components. Materials such as titanium, aluminum, and stainless steel are commonly used due to their performance characteristics.
- Applications range from turbine blades and heat exchangers in aerospace to customized orthopedic implants in healthcare. According to GE Additive, metal 3D printing has enabled unprecedented design freedom and material efficiency in industrial manufacturing.
- Binder Jetting:
- This process uses a liquid binding agent to selectively bind layers of powdered material. The unbound powder acts as support, allowing intricate designs to be printed without added structures.
- Binder jetting is often used for producing sand molds in casting or for metal parts that are later sintered. It’s appreciated for its speed and scalability in producing large batches of components.
- Electron Beam Melting (EBM):
- EBM uses a focused beam of electrons to melt metal powders in a high-vacuum environment. This results in fully dense parts suitable for high-performance applications, particularly in aerospace and biomedical sectors.
- Materials like titanium and cobalt-chrome are commonly used, and the process is praised for reducing residual stress in the final parts.
- Material Jetting:
- This technique deposits droplets of photopolymer material layer by layer, which are then cured using UV light. It allows for the use of multiple materials and colors in a single build, making it ideal for realistic prototypes and models.
- Material jetting is popular in design visualization, education, and industries requiring visual prototypes with high fidelity.
- Multi Jet Fusion (MJF):
- Developed by HP, MJF uses a fusing agent and detailing agent combined with thermal energy to bind powdered material into functional parts. It offers high strength, fine detail, and fast print speeds.
- MJF is increasingly being used for end-use parts, fixtures, and tooling in industrial applications due to its robust mechanical properties and cost-effectiveness.
Materials Used in Additive Manufacturing
- Plastics:
- Plastics remain the most common material in additive manufacturing, offering a wide range of properties and ease of use. Thermoplastics like PLA, ABS, and PETG are widely used in FDM, while advanced engineering plastics such as PEEK (polyether ether ketone) and polycarbonate are employed for high-performance needs.
- These materials are chosen based on factors such as flexibility, strength, temperature resistance, and chemical stability.
- Metals:
- Metal additive manufacturing materials include aluminum, titanium, stainless steel, and cobalt-chrome, among others. These are crucial for high-stress and high-temperature applications in sectors like aerospace, automotive, and defense.
- Each metal type offers unique properties—titanium is lightweight and corrosion-resistant, while stainless steel provides strength and durability.
- Composites:
- Composites combine a base material with reinforcements like carbon or glass fiber to enhance strength, stiffness, or thermal performance. These are used in applications requiring lightweight yet strong structures, such as drone parts and sporting equipment.
- Ceramics:
- Ceramic materials are used in AM for their high-temperature resistance, hardness, and chemical stability. Applications include medical implants, aerospace components, and tooling for aggressive environments.
- Biomaterials:
- Used primarily in the medical field, biomaterials such as biocompatible polymers and metals support applications like dental crowns, prosthetics, and bone scaffolds. These materials must meet stringent health and safety regulations while promoting biological integration.
- Concrete and Geopolymers:
- In large-scale applications, additive manufacturing is being used with concrete and geopolymer mixtures to construct homes, infrastructure, and shelters. These processes enable rapid, cost-effective building with less labor and waste.
Applications of Additive Manufacturing
Prototyping
- Rapid Prototyping:
- Additive manufacturing revolutionizes the product development cycle by enabling rapid prototyping, which allows engineers and designers to quickly produce physical models from digital concepts. These models can be tested for design feasibility, user interaction, ergonomics, and mechanical performance, significantly accelerating the iterative development process.
- Applications:
- Consumer electronics prototypes allow companies to evaluate aesthetics, functionality, and assembly before committing to high-cost tooling. For instance, smartphone enclosures and wearable devices can be prototyped with full detail and material approximation.
- Automotive part testing benefits greatly from rapid prototyping, as components such as brackets, vents, housings, and mounts can be evaluated in operational environments without delay. This capability enables faster innovation cycles and more agile design adaptations.
- Functional Prototypes:
- Unlike simple visual models, functional prototypes made through additive manufacturing allow for comprehensive testing of form, fit, and function in real-world conditions. Engineers can assess whether components withstand thermal stress, mechanical loads, or chemical exposure as required by the application.
- These prototypes often use production-grade materials or advanced composites, bridging the gap between concept and final production. This approach is especially valuable in fields such as aerospace, medical devices, and automotive engineering.
Custom Manufacturing
- Mass Customization:
- Additive manufacturing enables scalable customization by eliminating the need for specialized tooling or molds. Products can be tailored to individual preferences or anatomical features while still being manufactured in batches, reducing cost and waste.
- Examples:
- Customized footwear uses 3D scanning and printing to fit individual foot shapes, improving comfort and performance. Eyewear can be produced in bespoke designs that match facial features and style preferences.
- Prosthetics benefit significantly, as each device can be fitted to a patient’s anatomy and functional needs, enhancing mobility and quality of life.
- Low-Volume Production:
- When demand does not justify the high cost of injection molding or CNC setups, additive manufacturing provides a flexible solution for producing limited quantities of complex parts. This is particularly beneficial for startups, medical device developers, and companies needing custom spares or upgrades.
- In sectors such as defense and aviation, where unique components are often required in small quantities, AM delivers both precision and economic viability.
Complex Geometries
- Design Freedom:
- One of the most transformative aspects of additive manufacturing is its ability to fabricate complex geometries that are either impossible or highly inefficient to achieve using traditional methods. Structures such as hollow cores, intricate meshes, or functionally graded materials become feasible and cost-effective.
- Examples:
- Lattice structures for lightweight aerospace components reduce mass without compromising strength or rigidity. These parts are engineered for optimal weight-to-strength ratios and thermal performance.
- Internal channels for cooling systems, such as those in turbine blades or high-performance electronic devices, enhance heat dissipation by allowing customized flow pathways.
Aerospace and Defense
- Lightweight Components:
- Aerospace engineers leverage additive manufacturing to design ultra-lightweight structures that meet stringent performance standards. Components can be topologically optimized for stress distribution, material efficiency, and thermal resilience.
- Applications:
- Engine brackets, fuel nozzles, and structural parts are now 3D-printed from high-performance metals such as titanium and Inconel. These components reduce aircraft weight and fuel consumption while maintaining or enhancing mechanical performance.
- On-Demand Manufacturing:
- In remote or hostile environments, the ability to manufacture parts on demand reduces logistics dependencies and enhances readiness. Military units, for instance, can fabricate replacement parts for vehicles or equipment in the field, minimizing downtime.
- This application also streamlines inventory management and enables decentralized supply chains.
Healthcare and Medical
- Prosthetics and Orthotics:
- Additive manufacturing allows for the creation of custom-fit prosthetic limbs and orthotic devices using scans of patient anatomy. These devices are lighter, more comfortable, and tailored to individual functional needs.
- Medical Implants:
- Patient-specific implants, such as cranial plates or spinal cages, can be printed from biocompatible materials to precisely fit a patient’s anatomy, reducing surgical time and improving outcomes. Dental implants and custom abutments are also widely produced via AM.
- Tissue Engineering:
- Bioprinting uses cells and biomaterials to fabricate structures that support tissue regeneration. Researchers are exploring ways to print entire organs or complex tissues using layer-by-layer deposition of living cells, scaffolds, and growth factors.
- Surgical Planning Models:
- Surgeons use 3D-printed anatomical models derived from CT or MRI scans for pre-operative planning. These models improve understanding of complex pathologies and enhance precision during surgeries.
Automotive
- Tooling and Fixtures:
- Custom jigs, molds, gauges, and fixtures can be printed quickly and at low cost. This improves assembly accuracy and reduces the need for complex machining, streamlining production workflows.
- End-Use Parts:
- Automakers increasingly incorporate 3D-printed parts in finished vehicles. Functional parts like brackets, air vents, dashboard elements, and intake manifolds are tailored for performance and aesthetics, particularly in electric vehicles and luxury brands.
Architecture and Construction
- 3D-Printed Buildings:
- Construction-scale 3D printers extrude concrete, geopolymers, or earth-based composites to build entire structures layer by layer. This method reduces material waste, construction time, and labor costs.
- Applications:
- Affordable housing and disaster relief shelters benefit from this innovation, offering rapid deployment and structural integrity in challenging environments. As seen in [ICON’s 3D printed communities](https://www.iconbuild.com/projects), printed homes can now meet building codes and design standards.
- Scale Models:
- Architectural firms use 3D printing to produce detailed scale models that showcase design concepts to clients and stakeholders. These models can include intricate features, landscaping, and interior layouts, offering immersive visualization for planning approvals and marketing.
Energy and Power
- Wind Turbine Components:
- AM enables the production of lightweight and aerodynamically optimized parts for wind turbines, such as nacelle components and sensor housings. This contributes to improved energy capture and easier transportation of modular parts.
- Turbine Blades:
- In gas turbines, 3D printing allows for the inclusion of intricate internal cooling channels that were previously impossible with casting or machining. This results in more efficient thermal management and longer lifespan of turbine components.
Consumer Goods
- Personalized Products:
- AM empowers consumers to co-create personalized jewelry, fashion accessories, smartphone cases, and even custom kitchenware. By combining digital design platforms with 3D printing services, mass personalization becomes accessible and affordable.
- Fast Iterations:
- Consumer brands use AM for quick iterations of new product lines. Designers can test multiple variations in texture, size, and ergonomics within days, accelerating product launches and improving alignment with consumer preferences.
Emerging Trends in Additive Manufacturing
Hybrid Manufacturing
- Hybrid manufacturing integrates the strengths of both additive and subtractive processes, allowing manufacturers to leverage the design freedom of 3D printing while achieving high precision and excellent surface finishes through traditional machining. This combination bridges the gap between prototyping and production-quality parts, expanding the applicability of additive methods to industries with tight tolerance requirements.
- Example: Components such as aerospace brackets or turbine housings may be 3D-printed in rough shape to take advantage of complex geometry and lightweight structures. After printing, CNC machining is used to refine key surfaces, holes, and threads, ensuring dimensional accuracy and material performance in critical areas.
Multi-Material Printing
- Multi-material printing represents a breakthrough in functional prototyping and end-use manufacturing. By enabling the simultaneous use of different materials—such as rigid plastics, elastomers, and conductive inks—this technology allows for the creation of complex assemblies with varying mechanical, thermal, and electrical properties in a single build.
- Applications include producing objects with built-in gaskets, embedded circuits, or movable joints. In biomedical fields, it enables printing anatomical models with tissue-like gradients or prosthetics with rigid frames and soft contact points tailored to patient needs.
Sustainability and Recycling
- Recycled Materials:
- Sustainability has become a driving force behind innovation in additive manufacturing. Increasingly, recycled plastics, such as PET from water bottles or failed 3D prints, are being reprocessed into filament or powder feedstock. This reduces reliance on virgin materials and supports a circular economy model.
- Some companies are developing closed-loop systems where material waste from one process becomes the input for the next. In education and maker spaces, recycling initiatives promote environmental responsibility and cost savings.
- Localized Manufacturing:
- Localized production through 3D printing dramatically lowers the carbon footprint associated with transportation and warehousing. By printing parts on-site or on-demand near the point of use, manufacturers reduce lead times, eliminate overproduction, and tailor outputs to immediate needs.
- This decentralized approach is particularly beneficial in humanitarian aid and remote engineering projects. For instance, 3D-printed medical supplies and repair parts are produced in the field using compact, solar-powered printers, as showcased in [UNICEF’s field innovations](https://www.unicef.org/innovation/stories/3d-printing-field). This empowers communities to meet their own needs sustainably and efficiently.
High-Speed Printing
- Traditionally seen as slower than conventional manufacturing, additive manufacturing is experiencing a leap forward in speed thanks to innovations in hardware and process design. New printer architectures use continuous deposition, parallel nozzle arrays, or advanced light-curing systems to slash print times by up to 90%.
- For example, techniques like Continuous Liquid Interface Production (CLIP) and High-Speed Sintering (HSS) enable faster production of large batches, making 3D printing more competitive for serial manufacturing. These advancements reduce turnaround time and make just-in-time manufacturing a realistic option.
AI and Machine Learning
- Artificial Intelligence (AI) and Machine Learning (ML) are playing an increasingly vital role in design optimization, process control, and quality assurance in additive manufacturing. AI algorithms can analyze geometric constraints and suggest designs that reduce weight while maintaining or improving structural integrity.
- Generative design software powered by ML explores thousands of iterations and refines designs based on performance goals. In-process monitoring systems use AI to detect defects such as warping or under-extrusion in real-time, triggering corrective actions or halting the print to avoid material waste. These technologies enhance reliability, reduce errors, and accelerate product development cycles.
Automation in 3D Printing
- As additive manufacturing moves toward factory-scale deployment, automation is essential to ensure consistency and throughput. Robotic arms and conveyor systems are being integrated to automate pre-print setup, material replenishment, part removal, and post-processing. This reduces labor costs and enables 24/7 operation with minimal human intervention.
- Automated build platforms can cycle between printing and curing stations, while software tools schedule and manage workflows across multiple printers. In smart factories, entire additive production lines are coordinated using Industrial Internet of Things (IIoT) platforms, enabling real-time performance tracking and predictive maintenance. These developments make additive manufacturing scalable and viable for high-volume production in automotive, aerospace, and consumer goods industries.
Benefits of Additive Manufacturing
- Design Flexibility:
- Additive manufacturing revolutionizes product design by enabling the creation of geometries that are impossible or prohibitively expensive to achieve with traditional subtractive methods. Engineers can implement internal lattices, complex curves, hollow structures, and topology-optimized components to enhance performance while reducing material usage.
This design freedom supports innovation in industries like aerospace, where weight reduction and structural integrity are critical. For instance, aerospace brackets with organic, bone-like geometries offer superior strength-to-weight ratios. In architecture and fashion, additive techniques unlock artistic expression with intricate patterns and fluid forms, unconstrained by mold limitations.
- Additive manufacturing revolutionizes product design by enabling the creation of geometries that are impossible or prohibitively expensive to achieve with traditional subtractive methods. Engineers can implement internal lattices, complex curves, hollow structures, and topology-optimized components to enhance performance while reducing material usage.
- Reduced Waste:
- Unlike subtractive manufacturing, which removes material from a solid block (often discarding up to 90% of it), additive manufacturing builds components layer by layer using only the necessary material. This inherently waste-minimizing process is not only environmentally sustainable but also economically advantageous when working with costly resources like titanium or engineering polymers.
Powder-based processes such as Selective Laser Sintering (SLS) and Direct Metal Laser Sintering (DMLS) often allow for the reuse of unused material, further reducing waste and improving sustainability metrics. Additive manufacturing aligns with the principles of lean manufacturing and the circular economy, contributing to greener industrial practices.
- Unlike subtractive manufacturing, which removes material from a solid block (often discarding up to 90% of it), additive manufacturing builds components layer by layer using only the necessary material. This inherently waste-minimizing process is not only environmentally sustainable but also economically advantageous when working with costly resources like titanium or engineering polymers.
- Customization:
- One of the hallmark benefits of additive manufacturing is the ability to produce one-of-a-kind or highly tailored parts without significant changes in tooling or process setup. This is especially beneficial in healthcare, where personalized prosthetics, orthotics, and implants are designed to match a patient’s exact anatomy.
In the consumer market, personalized products—from custom-fit earbuds to fashion accessories—can be printed on demand, enhancing user experience and brand differentiation. Additive technologies empower mass customization, allowing manufacturers to meet specific customer preferences at scale, transforming how products are conceived and delivered.
- One of the hallmark benefits of additive manufacturing is the ability to produce one-of-a-kind or highly tailored parts without significant changes in tooling or process setup. This is especially beneficial in healthcare, where personalized prosthetics, orthotics, and implants are designed to match a patient’s exact anatomy.
- Shorter Lead Times:
- Traditional manufacturing processes involve extensive lead times due to mold production, tooling, and setup adjustments. Additive manufacturing bypasses these steps, enabling the rapid production of prototypes, tooling components, and even end-use parts within hours or days. This accelerates product development cycles and reduces time-to-market—a crucial advantage in competitive industries.
For example, in automotive design, engineers can iterate multiple versions of a component overnight and test them the next day. During crises such as the COVID-19 pandemic, 3D printing was instrumental in rapidly producing medical devices and PPE, highlighting its agility in time-sensitive scenarios. As noted by [MIT Technology Review](https://www.technologyreview.com/2021/01/15/1016313/3d-printing-pandemic-covid-19-response/), this capability is transforming emergency response and supply chain resilience.
- Traditional manufacturing processes involve extensive lead times due to mold production, tooling, and setup adjustments. Additive manufacturing bypasses these steps, enabling the rapid production of prototypes, tooling components, and even end-use parts within hours or days. This accelerates product development cycles and reduces time-to-market—a crucial advantage in competitive industries.
- Cost Efficiency:
- While the cost per unit for additive manufacturing may be higher than traditional methods in mass production, it becomes significantly more cost-effective in low-volume or high-complexity scenarios. It eliminates the need for expensive molds, dies, and jigs, reducing capital investment and setup time.
This cost efficiency makes it ideal for startups, R&D labs, and custom manufacturers where flexibility is more valuable than scale. Furthermore, the consolidation of parts into a single print reduces assembly time and labor costs. In aerospace and defense, where traditional supply chains can be slow and costly, on-demand additive manufacturing offers a leaner and more adaptive alternative.
- While the cost per unit for additive manufacturing may be higher than traditional methods in mass production, it becomes significantly more cost-effective in low-volume or high-complexity scenarios. It eliminates the need for expensive molds, dies, and jigs, reducing capital investment and setup time.
Challenges in Additive Manufacturing
- Material Limitations:
- One of the foremost limitations in additive manufacturing lies in the restricted variety of printable materials. While traditional manufacturing supports a vast array of metals, polymers, ceramics, and composites with well-understood mechanical properties, AM is still developing equivalent options with consistent performance. Not all metals or plastics are currently suitable for layer-by-layer deposition, and even when available, some materials may not exhibit the same strength, ductility, or heat resistance as their conventionally manufactured counterparts.
Moreover, certain high-performance materials require specific environmental conditions, such as inert atmospheres or high temperatures, which demand specialized (and costly) equipment. Research is ongoing to broaden the spectrum of usable feedstocks, including the development of multi-material capabilities and printable biodegradable composites.
- One of the foremost limitations in additive manufacturing lies in the restricted variety of printable materials. While traditional manufacturing supports a vast array of metals, polymers, ceramics, and composites with well-understood mechanical properties, AM is still developing equivalent options with consistent performance. Not all metals or plastics are currently suitable for layer-by-layer deposition, and even when available, some materials may not exhibit the same strength, ductility, or heat resistance as their conventionally manufactured counterparts.
- Surface Finish:
- Parts created using additive manufacturing often exhibit rough or layered surface textures due to the nature of deposition-based fabrication. This can be problematic for applications requiring tight tolerances, smooth finishes, or aesthetic appeal. Components used in aerospace, automotive, and biomedical industries may need additional machining, polishing, or coating to meet specifications.
The need for post-processing not only increases production time and cost but also introduces variability, particularly if the finishing process is manual. Surface anomalies such as stair-stepping, residual powder, or microvoids may also affect fatigue life or corrosion resistance. Advances in hybrid manufacturing—combining AM with CNC finishing—are helping to address this issue, but it remains a barrier to direct use in many critical applications.
- Parts created using additive manufacturing often exhibit rough or layered surface textures due to the nature of deposition-based fabrication. This can be problematic for applications requiring tight tolerances, smooth finishes, or aesthetic appeal. Components used in aerospace, automotive, and biomedical industries may need additional machining, polishing, or coating to meet specifications.
- High Initial Costs:
- Despite the potential for long-term savings in tooling and material usage, the upfront investment in additive manufacturing can be steep. Industrial-grade 3D printers, particularly those capable of processing metals or advanced polymers, often cost hundreds of thousands of dollars. Additionally, these systems require specialized infrastructure, including ventilation, power regulation, and environmental controls.
Beyond hardware, expenses related to software, training, maintenance, and material procurement can be substantial. This high cost of entry can deter startups, small businesses, or educational institutions from adopting AM technologies. As noted by [Forbes](https://www.forbes.com/sites/tjmccue/2021/04/27/the-business-case-for-3d-printing-why-additive-manufacturing-is-growing/), strategic investments and innovation in open-source and desktop solutions are helping democratize access, but cost remains a significant hurdle.
- Despite the potential for long-term savings in tooling and material usage, the upfront investment in additive manufacturing can be steep. Industrial-grade 3D printers, particularly those capable of processing metals or advanced polymers, often cost hundreds of thousands of dollars. Additionally, these systems require specialized infrastructure, including ventilation, power regulation, and environmental controls.
- Size Constraints:
- The dimensions of 3D printed parts are inherently limited by the build volume of the printer. While small desktop printers may produce parts under 30 cm in any direction, even high-end industrial systems are constrained by chamber size. This poses challenges for sectors like aerospace, construction, and energy where large components are common.
Solutions such as modular printing (assembling parts after printing), gantry-style machines, and mobile concrete 3D printers are being developed, but they often introduce structural weak points or increase production complexity. For now, large-scale additive manufacturing remains a specialized area with limited accessibility.
- The dimensions of 3D printed parts are inherently limited by the build volume of the printer. While small desktop printers may produce parts under 30 cm in any direction, even high-end industrial systems are constrained by chamber size. This poses challenges for sectors like aerospace, construction, and energy where large components are common.
- Regulatory Hurdles:
- Gaining certification and meeting compliance standards is a major barrier for AM-produced parts, especially in tightly regulated fields such as aerospace, medical devices, and defense. Regulatory agencies require robust data on material properties, repeatability, reliability, and long-term performance—criteria that are still evolving in the AM space.
The lack of standardized processes and quality control frameworks across different printers and materials further complicates regulatory approval. Efforts by organizations like ASTM International and ISO are working toward harmonized guidelines, but until universally accepted standards are established, manufacturers must navigate a complex and often time-consuming certification process. This limits the widespread adoption of AM in safety-critical applications despite its technical potential.
- Gaining certification and meeting compliance standards is a major barrier for AM-produced parts, especially in tightly regulated fields such as aerospace, medical devices, and defense. Regulatory agencies require robust data on material properties, repeatability, reliability, and long-term performance—criteria that are still evolving in the AM space.
Future Directions in Additive Manufacturing
- Mass Adoption in Industries:
- Additive manufacturing is steadily moving beyond the prototyping phase into full-scale industrial production. With growing confidence in the reliability and repeatability of AM processes, industries such as automotive, aerospace, healthcare, and consumer goods are embracing the technology for producing end-use parts, custom components, and production tooling. Factors driving this mass adoption include reduced lead times, supply chain flexibility, and enhanced design possibilities.
Furthermore, the development of more robust design for additive manufacturing (DfAM) guidelines and greater collaboration between hardware manufacturers and software developers is enabling seamless integration of AM into traditional manufacturing workflows. In the near future, we can expect hybrid facilities that combine additive and subtractive systems operating in smart factories, achieving optimal cost-efficiency and responsiveness.
- Additive manufacturing is steadily moving beyond the prototyping phase into full-scale industrial production. With growing confidence in the reliability and repeatability of AM processes, industries such as automotive, aerospace, healthcare, and consumer goods are embracing the technology for producing end-use parts, custom components, and production tooling. Factors driving this mass adoption include reduced lead times, supply chain flexibility, and enhanced design possibilities.
- Distributed Manufacturing:
- Distributed manufacturing represents a paradigm shift from centralized production facilities to decentralized networks of localized, on-demand fabrication units. Powered by digital design files and standardized printing protocols, this model allows manufacturers to produce parts closer to the point of use, significantly reducing shipping costs and environmental impact.
In disaster zones, military operations, and remote communities, distributed AM can be a game-changer. A digital file sent from a design center can be printed in real time by local hubs using regionally available materials. This approach also enhances resiliency during supply chain disruptions, as observed during the COVID-19 pandemic when 3D printing was used to locally produce critical medical components like face shields and ventilator parts. The [World Economic Forum](https://www.weforum.org/agenda/2022/01/3d-printing-supply-chains-pandemic) has emphasized the role of 3D printing in building resilient supply chains through distributed manufacturing.
- Distributed manufacturing represents a paradigm shift from centralized production facilities to decentralized networks of localized, on-demand fabrication units. Powered by digital design files and standardized printing protocols, this model allows manufacturers to produce parts closer to the point of use, significantly reducing shipping costs and environmental impact.
- Advancements in Bioprinting:
- Bioprinting is emerging as one of the most transformative subfields of additive manufacturing. Researchers are now able to print biological materials—including cells, hydrogels, and biomaterials—into complex three-dimensional structures that mimic natural tissue architecture. While fully functional organ printing remains a long-term goal, major milestones have been achieved in creating lab-grown skin, cartilage, and vascular structures.
The use of patient-derived cells and customized scaffold designs allows for personalized medicine and regenerative therapies. Bioprinted tissues are also accelerating pharmaceutical testing by enabling drug evaluations on tissue models without human trials. As stem cell research, tissue engineering, and AM technologies converge, bioprinting could revolutionize healthcare, organ transplantation, and biomedical research.
- Bioprinting is emerging as one of the most transformative subfields of additive manufacturing. Researchers are now able to print biological materials—including cells, hydrogels, and biomaterials—into complex three-dimensional structures that mimic natural tissue architecture. While fully functional organ printing remains a long-term goal, major milestones have been achieved in creating lab-grown skin, cartilage, and vascular structures.
- Large-Scale Printing:
- The scale of additive manufacturing is no longer confined to small and medium-sized components. Advances in robotic arms, gantry systems, and concrete-based extrusion are enabling the creation of large-scale structures such as homes, bridges, and aircraft parts. Large-format printers can now build full-sized architectural elements and infrastructure components layer by layer, making AM relevant for the construction and civil engineering sectors.
The ability to 3D print directly on-site reduces construction waste, labor costs, and construction time. In some cases, entire buildings have been completed in under 24 hours using this approach. Moreover, large-scale AM supports innovative geometries that are difficult or impossible with traditional methods, such as curvilinear walls, embedded conduits, and adaptive load-bearing forms.
- The scale of additive manufacturing is no longer confined to small and medium-sized components. Advances in robotic arms, gantry systems, and concrete-based extrusion are enabling the creation of large-scale structures such as homes, bridges, and aircraft parts. Large-format printers can now build full-sized architectural elements and infrastructure components layer by layer, making AM relevant for the construction and civil engineering sectors.
- Space Applications:
- Space agencies such as NASA and ESA are exploring the use of additive manufacturing for extraterrestrial missions. 3D printing tools, replacement parts, and structural elements on-site in space or on planetary surfaces can drastically reduce mission payloads and costs. This “in-situ resource utilization” (ISRU) strategy involves using local materials such as lunar regolith or Martian soil for printing habitats, landing pads, and radiation shields.
In microgravity environments, printers designed to operate without Earth’s gravity are being tested aboard the International Space Station (ISS). These systems allow astronauts to fabricate items on-demand, improving self-sufficiency during long-duration missions. As humanity ventures further into space, additive manufacturing will be pivotal for sustaining life and building infrastructure beyond Earth.
- Space agencies such as NASA and ESA are exploring the use of additive manufacturing for extraterrestrial missions. 3D printing tools, replacement parts, and structural elements on-site in space or on planetary surfaces can drastically reduce mission payloads and costs. This “in-situ resource utilization” (ISRU) strategy involves using local materials such as lunar regolith or Martian soil for printing habitats, landing pads, and radiation shields.
Why Study Additive Manufacturing (3D Printing)
Revolutionizing the Manufacturing Landscape
Additive manufacturing builds objects layer by layer from digital models. Students learn how this technique reduces material waste and enables rapid prototyping. It offers new possibilities in design and fabrication.
Materials and Printing Processes
The course introduces materials like thermoplastics, resins, and metals. Students study printing technologies such as FDM, SLA, and SLS. Understanding these processes enables them to choose the right method for each application.
Design for Additive Manufacturing (DfAM)
Additive manufacturing requires a different approach to design. Students learn to create complex geometries, lightweight structures, and customized parts. This supports innovation in engineering and product development.
Applications Across Disciplines
3D printing is used in healthcare, aerospace, automotive, and education. Students explore its role in producing implants, drones, tools, and teaching aids. This multidisciplinary nature opens a wide range of career opportunities.
Future Trends and Industry Disruption
Students explore how additive manufacturing is transforming supply chains and enabling local production. They study its impact on sustainability, speed-to-market, and customization. This prepares them to lead in a rapidly evolving industry.
Additive Manufacturing: Conclusion
Additive manufacturing (AM), also known as 3D printing, stands at the forefront of a technological revolution that is fundamentally transforming how products are conceptualized, developed, and brought to market. Unlike traditional subtractive manufacturing, which involves removing material to shape objects, AM builds components layer by layer, enabling unprecedented freedom in form and structure. This paradigm shift empowers designers and engineers to transcend the constraints of conventional machining, allowing the creation of intricate geometries, internal cavities, and lattice frameworks that enhance both functionality and material efficiency.
The advantages of AM extend far beyond the design phase. Industries such as aerospace and automotive have embraced AM for its ability to produce lightweight components that maintain structural integrity while improving fuel efficiency and performance. In the medical sector, AM has unlocked a new era of personalized care, enabling the production of patient-specific implants, dental appliances, and surgical guides that improve outcomes and reduce recovery times. Likewise, in construction and architecture, large-scale 3D printers are redefining building practices by facilitating the rapid construction of complex, sustainable structures at reduced costs.
As additive manufacturing continues to evolve, it is increasingly seen not just as a prototyping tool but as a viable method for full-scale production. Developments in high-speed printing, multi-material capabilities, and process automation are paving the way for AM to become integrated into digital, smart factories. The technology’s potential for mass customization allows manufacturers to cater to individual customer needs without the inefficiencies of retooling or large inventories. At the same time, AM promotes localized, on-demand production that can dramatically shorten supply chains, reduce transportation emissions, and enhance manufacturing agility.
Importantly, the sustainability potential of AM cannot be overstated. By using only the necessary amount of material, it minimizes waste while enabling the use of recycled inputs and biodegradable substances. Organizations around the world, including the Massachusetts Institute of Technology, are researching how AM technologies can contribute to circular economies by supporting closed-loop material cycles and decentralized production systems. These efforts align with broader goals of reducing environmental footprints and promoting ethical manufacturing practices.
Looking ahead, the trajectory of additive manufacturing points toward even greater innovation. The convergence of AM with artificial intelligence, machine learning, digital twins, and blockchain will redefine the boundaries of industrial production. From printing organs and habitats in space to developing hyper-efficient turbines and bespoke consumer products, the possibilities are virtually limitless. As educational institutions, governments, and industries invest in skill development and research, the adoption of AM will accelerate, transforming supply chains and reshaping the global economy.
In summary, additive manufacturing is no longer a niche technology—it is a transformative force reshaping how we design, build, and think about manufacturing. Its blend of flexibility, efficiency, customization, and sustainability positions it as a central pillar of the Fourth Industrial Revolution. As we move into a future defined by rapid innovation and urgent environmental challenges, AM will play an indispensable role in driving progress, empowering industries, and building a more responsive and sustainable world.
Additive Manufacturing: Review Questions with Detailed Answers
1. What is additive manufacturing, and how does it differ from traditional subtractive manufacturing methods?
Answer:
Additive manufacturing (AM) is a process of creating three-dimensional objects by layering materials based on digital models. Unlike traditional subtractive manufacturing, which involves removing material from a solid block through cutting, drilling, or milling, AM builds objects layer by layer, adding material only where needed.
Concepts:
- Additive Manufacturing (AM): Building objects by adding material layer upon layer.
- Subtractive Manufacturing: Removing material from a solid block to create the desired shape.
Differences:
- Material Usage: AM typically uses only the necessary material, resulting in less waste compared to subtractive methods.
- Design Complexity: AM allows for the creation of complex geometries and internal structures that are difficult or impossible to achieve with subtractive manufacturing.
- Customization: AM enables easy customization of products without significant additional costs, making it ideal for bespoke applications.
- Production Speed: For low-volume production and prototyping, AM can be faster due to reduced setup times.
Conclusion: Additive manufacturing offers significant advantages in terms of material efficiency, design flexibility, and customization, making it a transformative technology in various industries compared to traditional subtractive methods.
2. What are the most common types of additive manufacturing technologies, and what materials do they typically use?
Answer:
The most common types of additive manufacturing technologies include:
Fused Deposition Modeling (FDM):
- Materials: Thermoplastics like ABS, PLA, PETG, and Nylon.
- Process: Melts and extrudes filament through a heated nozzle to build objects layer by layer.
Stereolithography (SLA):
- Materials: Photopolymer resins.
- Process: Uses a UV laser to cure liquid resin in a vat, creating solid layers.
Selective Laser Sintering (SLS):
- Materials: Nylon, polystyrene, glass-filled polymers, and metals.
- Process: Utilizes a laser to sinter powdered material, fusing it into a solid structure.
Digital Light Processing (DLP):
- Materials: Photopolymer resins similar to SLA.
- Process: Projects an entire layer of UV light at once to cure the resin quickly.
Direct Metal Laser Sintering (DMLS) / Selective Laser Melting (SLM):
- Materials: Metals such as stainless steel, titanium, aluminum, and cobalt-chrome alloys.
- Process: Uses a high-powered laser to fully melt and fuse metallic powders.
Electron Beam Melting (EBM):
- Materials: Titanium alloys and other metals.
- Process: Employs an electron beam in a vacuum to melt and fuse metal powders layer by layer.
Conclusion: Different additive manufacturing technologies cater to various materials and applications, ranging from plastics and resins to advanced metals, each offering unique benefits suited to specific manufacturing needs.
3. What are the primary advantages of using 3D printing in industrial manufacturing?
Answer:
3D printing, a form of additive manufacturing, offers several primary advantages in industrial manufacturing:
Design Flexibility and Complexity:
- Benefit: Allows for the creation of intricate and complex geometries that are difficult or impossible to achieve with traditional manufacturing methods.
- Impact: Enables innovative product designs and functional parts with integrated features.
Customization and Personalization:
- Benefit: Facilitates the production of customized products tailored to specific customer needs without significant additional costs.
- Impact: Enhances customer satisfaction and opens new market opportunities for bespoke products.
Material Efficiency and Waste Reduction:
- Benefit: Uses only the material necessary to build the part, minimizing waste compared to subtractive manufacturing.
- Impact: Reduces material costs and environmental impact.
Rapid Prototyping and Faster Time-to-Market:
- Benefit: Accelerates the prototyping phase by quickly producing physical models from digital designs.
- Impact: Shortens product development cycles and allows for faster iteration and testing.
Cost-Effective for Low-Volume Production:
- Benefit: Eliminates the need for expensive tooling and setup costs, making it economically viable for low-volume production runs.
- Impact: Provides flexibility to produce small batches without incurring high initial investments.
Supply Chain Simplification and On-Demand Production:
- Benefit: Enables on-demand manufacturing, reducing the need for large inventories and streamlining the supply chain.
- Impact: Lowers storage costs and reduces the risk of overproduction and inventory obsolescence.
Lightweight Structures:
- Benefit: Allows for the creation of lightweight parts with internal structures optimized for strength and performance.
- Impact: Enhances product performance, particularly in industries like aerospace and automotive where weight reduction is critical.
Conclusion: 3D printing significantly enhances design capabilities, customization, material efficiency, and production speed, making it a valuable tool for industrial manufacturing across various sectors.
4. What are the key challenges associated with additive manufacturing in industrial applications?
Answer:
While additive manufacturing offers numerous advantages, several key challenges need to be addressed for its effective implementation in industrial applications:
Material Limitations:
- Challenge: Limited availability of suitable materials with desired mechanical properties compared to traditional manufacturing.
- Impact: Restricts the range of applications and performance capabilities of 3D printed parts.
Production Speed and Scalability:
- Challenge: Additive processes can be slower than traditional methods, making them less suitable for high-volume production.
- Impact: Limits the adoption of 3D printing for mass manufacturing needs.
Surface Finish and Accuracy:
- Challenge: 3D printed parts often require post-processing to achieve the desired surface finish and dimensional accuracy.
- Impact: Increases production time and costs, potentially offsetting some of the benefits of AM.
Cost of Equipment and Materials:
- Challenge: High initial investment costs for advanced 3D printers and specialized materials.
- Impact: Acts as a barrier to entry, particularly for small and medium-sized enterprises (SMEs).
Quality Control and Standardization:
- Challenge: Ensuring consistent quality and performance of 3D printed parts across different machines and settings.
- Impact: Difficulty in meeting industry standards and certifications, affecting reliability and trust in AM technologies.
Intellectual Property and Design Protection:
- Challenge: Risks of unauthorized reproduction of digital designs and intellectual property theft.
- Impact: Potential loss of proprietary information and reduced incentive for innovation.
Integration with Existing Manufacturing Processes:
- Challenge: Seamlessly integrating additive manufacturing with traditional manufacturing workflows and supply chains.
- Impact: Requires significant changes in production planning, training, and infrastructure.
Environmental Impact:
- Challenge: While AM can reduce material waste, some processes consume significant energy and use non-recyclable materials.
- Impact: Balancing the environmental benefits with energy consumption and material sustainability is crucial.
Conclusion: Addressing these challenges is essential for the broader adoption and effectiveness of additive manufacturing in industrial applications. Ongoing research, technological advancements, and industry collaboration are key to overcoming these hurdles and maximizing the potential of AM technologies.
5. How do different 3D printing materials affect the properties and applications of the final printed products?
Answer:
The choice of 3D printing materials significantly influences the properties, performance, and suitability of the final printed products for various applications. Different materials offer unique characteristics that cater to specific manufacturing needs:
Thermoplastics (e.g., PLA, ABS, PETG):
- Properties: Lightweight, good strength-to-weight ratio, flexible, and relatively easy to print.
- Applications: Prototyping, consumer products, educational models, and parts requiring flexibility.
Resins (e.g., Standard, Tough, Flexible Resins):
- Properties: High resolution, smooth surface finish, varying degrees of flexibility and durability depending on the type.
- Applications: Detailed prototypes, jewelry, dental models, and applications requiring fine detail and smooth finishes.
Nylon and Polyamide:
- Properties: High strength, durability, flexibility, and resistance to abrasion and chemicals.
- Applications: Functional parts, automotive components, gears, and tools that require robust mechanical properties.
Metal Alloys (e.g., Stainless Steel, Titanium, Aluminum):
- Properties: High strength, durability, heat resistance, and excellent mechanical properties.
- Applications: Aerospace parts, medical implants, tooling, and high-performance engineering components.
Composites (e.g., Carbon Fiber, Glass Fiber Reinforced Polymers):
- Properties: Enhanced strength, stiffness, and lightweight characteristics.
- Applications: High-strength applications such as aerospace components, sporting goods, and automotive parts where performance is critical.
Biomaterials (e.g., Biodegradable Plastics, Bioinks):
- Properties: Biocompatible, biodegradable, and capable of supporting biological functions.
- Applications: Medical devices, tissue engineering, and prosthetics where interaction with biological systems is necessary.
Ceramics:
- Properties: High hardness, heat resistance, and chemical stability.
- Applications: High-temperature applications, dental prosthetics, and decorative objects requiring durability and aesthetic appeal.
Impact on Applications:
- Mechanical Strength: Materials like metal alloys and reinforced composites are used for parts that require high strength and durability.
- Flexibility: Thermoplastics and certain resins provide the necessary flexibility for applications like wearable devices and flexible joints.
- Detail and Precision: Resins used in SLA and DLP printing offer high-resolution details, suitable for intricate designs and fine features.
- Biocompatibility: Biomaterials are essential for medical applications where compatibility with human tissues is critical.
- Thermal Resistance: Metals and ceramics are chosen for applications exposed to high temperatures or requiring thermal stability.
Conclusion: Selecting the appropriate 3D printing material is crucial for achieving the desired properties and functionality of the final product. Understanding the strengths and limitations of each material type allows manufacturers to tailor their choices to meet specific application requirements, ensuring optimal performance and suitability.
6. What are the environmental impacts of additive manufacturing compared to traditional manufacturing methods?
Answer:
Additive manufacturing (AM) presents several environmental impacts that differ significantly from traditional manufacturing methods. These impacts can be both positive and negative, depending on various factors such as material usage, energy consumption, and waste generation.
Positive Environmental Impacts:
Reduced Material Waste:
- AM Advantage: Builds objects layer by layer, using only the necessary amount of material, which minimizes waste.
- Comparison: Traditional subtractive methods often involve cutting away excess material from a solid block, resulting in more waste.
Lightweight Structures:
- AM Advantage: Enables the creation of lightweight parts with optimized internal structures, reducing material usage and overall product weight.
- Impact: Lower material consumption and reduced transportation emissions due to lighter products.
On-Demand Production:
- AM Advantage: Allows for on-demand manufacturing, reducing the need for large inventories and associated storage resources.
- Impact: Decreases energy consumption and resource use in inventory management and warehousing.
Complex Geometries and Optimization:
- AM Advantage: Facilitates the design of complex and efficient geometries that enhance product performance and resource utilization.
- Impact: Improves the efficiency of products, potentially leading to lower operational energy use.
Localized Production:
- AM Advantage: Supports decentralized manufacturing, enabling production closer to the point of use.
- Impact: Reduces transportation-related emissions and supports local economies.
Negative Environmental Impacts:
Energy Consumption:
- AM Disadvantage: Some AM processes, especially metal printing, can be energy-intensive.
- Comparison: Traditional manufacturing methods also consume significant energy, but the specific impact varies based on the process and scale.
Material Limitations and Sustainability:
- AM Disadvantage: Limited availability of sustainable or recyclable materials for certain AM processes.
- Impact: Potential environmental issues if non-renewable or non-recyclable materials are used extensively.
Post-Processing Requirements:
- AM Disadvantage: Many AM parts require post-processing steps such as sanding, painting, or heat treatment, which can consume additional energy and materials.
- Impact: Increases the overall environmental footprint of the manufacturing process.
Emissions and Air Quality:
- AM Disadvantage: Some AM processes emit volatile organic compounds (VOCs) or other pollutants during printing and post-processing.
- Impact: Can contribute to air quality issues and require additional filtration and ventilation systems.
Lifecycle Considerations:
- AM Disadvantage: The overall environmental impact depends on the entire lifecycle of the product, including disposal and recycling.
- Impact: If AM products are not designed for recyclability or longevity, the environmental benefits may be diminished.
Comparison Summary:
- Material Efficiency: AM generally offers superior material efficiency compared to traditional subtractive methods.
- Energy Use: The energy efficiency of AM varies by process and material, and while some AM methods are more energy-efficient, others may consume more energy than traditional methods.
- Waste Generation: AM typically generates less waste, contributing to a lower environmental footprint in this aspect.
- Emissions: AM can produce emissions during certain processes, requiring effective mitigation strategies to minimize environmental harm.
Conclusion: Additive manufacturing holds significant potential for reducing the environmental impact of manufacturing through material efficiency, waste reduction, and optimized product designs. However, challenges related to energy consumption, material sustainability, and emissions must be addressed to fully realize its environmental benefits. Balancing these factors is essential for promoting sustainable practices in the adoption of additive manufacturing technologies.
7. How can additive manufacturing be integrated with traditional manufacturing processes to create hybrid manufacturing systems?
Answer:
Integrating additive manufacturing (AM) with traditional manufacturing processes to create hybrid manufacturing systems combines the strengths of both approaches, enhancing flexibility, efficiency, and innovation in production. Hybrid systems leverage the precision and material capabilities of traditional methods alongside the design freedom and customization of AM.
Concepts:
- Additive Manufacturing (AM): Processes that build objects layer by layer from digital models.
- Traditional Manufacturing: Subtractive processes like milling, drilling, and turning that remove material to create parts.
- Hybrid Manufacturing Systems: Integrated systems that utilize both additive and subtractive manufacturing technologies within a single workflow or setup.
Integration Strategies:
Sequential Processing:
- Action: Perform additive and subtractive processes in sequence on the same part.
- Example: Use AM to create a near-net shape of a part and then apply CNC machining to achieve precise dimensions and surface finishes.
- Benefit: Combines the design flexibility of AM with the precision of traditional machining, optimizing both shape creation and dimensional accuracy.
Multi-Process Machines:
- Action: Utilize machines capable of both additive and subtractive operations, allowing for seamless transitions between building and refining parts.
- Example: A hybrid machine that performs 3D printing and milling without the need to move the part between different setups.
- Benefit: Enhances workflow efficiency, reduces setup times, and minimizes handling errors.
Design for Hybrid Manufacturing:
- Action: Develop parts designed specifically to take advantage of both AM and traditional manufacturing techniques.
- Example: Designing internal channels or complex geometries using AM, and adding functional features or precision elements with CNC machining.
- Benefit: Maximizes the strengths of each manufacturing method, resulting in parts with superior performance and reduced material usage.
Concurrent Manufacturing:
- Action: Perform additive and subtractive processes simultaneously or in overlapping phases.
- Example: While a part is being printed layer by layer, another area can be machined or finished simultaneously.
- Benefit: Increases production throughput and reduces overall manufacturing time.
Supply Chain Integration:
- Action: Integrate AM into the existing supply chain to complement traditional manufacturing processes.
- Example: Use AM for rapid prototyping and low-volume production, while relying on traditional methods for high-volume manufacturing.
- Benefit: Enhances supply chain flexibility, allowing for quick adjustments based on demand and reducing lead times.
Benefits of Hybrid Manufacturing Systems:
Enhanced Flexibility:
- Benefit: Ability to produce complex, customized parts while maintaining the precision and surface finish required for functional components.
Improved Efficiency:
- Benefit: Streamlines production workflows by reducing the need to switch between different machines and setups, thereby saving time and resources.
Cost Savings:
- Benefit: Optimizes material usage and reduces waste by leveraging AM’s additive processes alongside traditional methods’ efficiency in material removal.
Quality Improvement:
- Benefit: Combines the strengths of both manufacturing methods to achieve higher quality parts with accurate dimensions and superior surface finishes.
Innovation and Design Freedom:
- Benefit: Encourages innovative designs that were previously difficult or impossible to manufacture, fostering greater creativity and technological advancement.
Implementation Steps:
Assessment of Manufacturing Needs:
- Evaluate which parts and processes would benefit most from a hybrid approach based on complexity, volume, and material requirements.
Investment in Hybrid Equipment:
- Acquire or upgrade machinery capable of performing both additive and subtractive operations seamlessly.
Training and Skill Development:
- Train workforce members to operate and maintain hybrid systems, ensuring they can leverage the full potential of integrated technologies.
Process Optimization:
- Develop and refine workflows that effectively combine additive and subtractive processes, ensuring optimal performance and quality.
Design Collaboration:
- Foster collaboration between design and manufacturing teams to create parts optimized for hybrid manufacturing, ensuring that designs are manufacturable and efficient.
Quality Control Integration:
- Implement comprehensive quality control measures that encompass both additive and subtractive processes, ensuring consistent quality throughout the production cycle.
Conclusion: Integrating additive manufacturing with traditional manufacturing processes to create hybrid manufacturing systems offers a powerful approach to enhancing production flexibility, efficiency, and innovation. By strategically combining the strengths of both manufacturing methods, manufacturers can produce high-quality, complex parts while optimizing material usage and reducing production times. Successful integration requires careful planning, investment in appropriate technologies, and a skilled workforce to fully realize the benefits of hybrid manufacturing.
8. What are the key factors that determine the selection of a 3D printing technology for a specific industrial application?
Answer:
Selecting the appropriate 3D printing technology for a specific industrial application involves evaluating several key factors to ensure that the chosen method aligns with the desired outcomes in terms of performance, cost, material compatibility, and production requirements.
Key Factors:
Material Requirements:
- Consideration: The type of material needed for the final product, including its mechanical properties, durability, flexibility, and thermal resistance.
- Impact: Different 3D printing technologies support various materials; for example, SLS is suitable for robust plastics, while DMLS is ideal for metal parts.
Product Complexity and Design:
- Consideration: The intricacy of the part’s geometry, including internal structures, fine details, and overhangs.
- Impact: Technologies like SLA and DLP offer high resolution for detailed designs, whereas FDM is suitable for simpler geometries.
Production Volume:
- Consideration: The quantity of parts required, ranging from single prototypes to large-scale production.
- Impact: AM is cost-effective for low-volume, customized production, while traditional manufacturing may be more efficient for high-volume runs.
Surface Finish and Tolerance:
- Consideration: The desired surface quality and dimensional accuracy of the final product.
- Impact: SLA and DLP provide superior surface finishes and tighter tolerances compared to FDM and SLS, which may require post-processing for smoothness.
Build Size and Scale:
- Consideration: The dimensions of the parts to be printed, including height, width, and length.
- Impact: Larger build volumes require specific technologies like FDM or SLS, which can accommodate bigger parts, whereas SLA and DLP are often limited to smaller sizes.
Production Speed:
- Consideration: The time required to produce each part, especially when meeting tight deadlines.
- Impact: Some technologies, like DLP, can print entire layers simultaneously, offering faster production times compared to layer-by-layer methods like FDM.
Cost Considerations:
- Consideration: Budget constraints, including equipment costs, material expenses, and operational costs.
- Impact: FDM is generally more cost-effective for prototyping, whereas metal AM technologies like DMLS have higher costs but provide superior material properties.
Post-Processing Needs:
- Consideration: The extent of finishing required after printing, such as support removal, sanding, painting, or heat treatment.
- Impact: Technologies that produce cleaner prints with fewer supports, like SLA, reduce post-processing time and costs.
Application-Specific Requirements:
- Consideration: Functional requirements such as electrical conductivity, biocompatibility, or thermal stability.
- Impact: Certain applications may dictate the use of specific materials and technologies, such as titanium AM for medical implants or conductive filaments for electronics.
Scalability and Future Needs:
- Consideration: Potential future demands and the ability to scale production as needed.
- Impact: Choosing a technology that can evolve with growing production needs ensures long-term viability and reduces the need for frequent equipment upgrades.
Conclusion: Selecting the right 3D printing technology for an industrial application requires a comprehensive assessment of material needs, design complexity, production volume, quality requirements, build size, speed, cost, post-processing, and specific application demands. By carefully evaluating these factors, manufacturers can choose the most suitable AM technology that meets their operational objectives, ensuring optimal performance, cost-efficiency, and product quality.
9. How does the choice of additive manufacturing technology influence the mechanical properties of the final product?
Answer:
The choice of additive manufacturing (AM) technology plays a crucial role in determining the mechanical properties of the final product. Different AM processes influence factors such as material density, microstructure, layer adhesion, and residual stresses, which collectively affect the strength, durability, flexibility, and overall performance of printed parts.
Key Influences:
Material Density and Porosity:
- Impact: AM technologies vary in their ability to produce fully dense parts. For example, Selective Laser Sintering (SLS) and Direct Metal Laser Sintering (DMLS) can achieve high material density, resulting in stronger parts.
- Consequences: Higher density reduces porosity, enhancing mechanical strength and fatigue resistance. Lower density can lead to weaker parts with reduced load-bearing capacity.
Layer Adhesion and Interlayer Bonding:
- Impact: The strength of the bond between layers significantly affects the overall mechanical properties. Technologies like Stereolithography (SLA) and Digital Light Processing (DLP) typically offer better interlayer bonding due to precise curing of resins.
- Consequences: Strong interlayer bonds improve tensile strength and impact resistance, while weak bonds can result in delamination and reduced structural integrity.
Microstructure and Anisotropy:
- Impact: AM processes influence the microstructure of materials, including grain size and orientation. For instance, Electron Beam Melting (EBM) can produce refined microstructures, enhancing mechanical properties.
- Consequences: Fine microstructures can improve strength and toughness, while anisotropy (directional dependence of properties) may occur if the build orientation affects material properties unevenly.
Residual Stresses and Warping:
- Impact: Rapid heating and cooling cycles in AM can induce residual stresses, leading to warping or distortion of parts. Technologies like DMLS often require post-processing to relieve these stresses.
- Consequences: Residual stresses can compromise part dimensional accuracy and mechanical performance, necessitating additional processing steps to ensure stability.
Material Selection and Process Parameters:
- Impact: Different AM technologies support various materials with inherent mechanical properties. Additionally, process parameters such as laser power, scanning speed, and layer thickness can be optimized to enhance mechanical performance.
- Consequences: Proper material and parameter selection can maximize tensile strength, elongation, and hardness, tailoring parts to specific application requirements.
Support Structures and Post-Processing:
- Impact: The presence of support structures during printing and the extent of post-processing can influence mechanical properties by affecting surface finish and internal structure.
- Consequences: Effective removal of support structures and thorough post-processing can enhance surface integrity and mechanical performance, while inadequate post-processing may leave defects and reduce part strength.
Examples:
- Fused Deposition Modeling (FDM): Typically results in anisotropic parts with lower tensile strength compared to SLS or DMLS due to layer-by-layer extrusion and potential gaps between layers.
- Stereolithography (SLA): Produces parts with high surface finish and good mechanical properties but may require additional curing to enhance strength.
- Direct Metal Laser Sintering (DMLS): Achieves high-density metal parts with excellent mechanical properties suitable for functional applications, but may require heat treatment to optimize performance.
Conclusion: The selection of an additive manufacturing technology profoundly influences the mechanical properties of the final product. Factors such as material density, layer adhesion, microstructure, residual stresses, and process parameters must be carefully considered to achieve the desired mechanical performance. Understanding these influences enables manufacturers to choose the appropriate AM technology and optimize processing conditions to produce parts that meet specific strength, durability, and functionality requirements.
10. What are the potential applications of additive manufacturing in the aerospace industry, and how do they benefit from AM technologies?
Answer:
Additive manufacturing (AM) has revolutionized the aerospace industry by enabling the production of complex, lightweight, and high-performance components. Its unique capabilities offer numerous benefits, including design flexibility, weight reduction, cost savings, and rapid prototyping, which are critical in the demanding aerospace sector.
Potential Applications:
Engine Components:
- Application: Manufacturing intricate parts such as turbine blades, combustion chambers, and fuel nozzles.
- Benefits: AM allows for the creation of complex geometries with internal cooling channels, enhancing engine efficiency and performance while reducing weight.
Structural Parts:
- Application: Producing lightweight structural components like brackets, housings, and load-bearing elements.
- Benefits: Weight reduction through optimized lattice structures and topology optimization improves fuel efficiency and payload capacity.
Tooling and Fixtures:
- Application: Creating customized jigs, fixtures, and tools for assembly and maintenance processes.
- Benefits: AM enables rapid production of tailored tools, reducing lead times and enhancing manufacturing flexibility.
Customized Interior Components:
- Application: Manufacturing personalized cabin parts, including seat components, panels, and lighting fixtures.
- Benefits: Allows for customization to meet specific airline requirements, improving passenger comfort and aesthetic appeal.
Repair and Maintenance Parts:
- Application: Producing spare parts on-demand for in-service aircraft, particularly for obsolete or hard-to-find components.
- Benefits: Reduces inventory costs, minimizes downtime, and extends the service life of aircraft by enabling timely repairs.
Prototyping and Testing:
- Application: Rapid prototyping of new aerospace designs and conducting physical testing of prototypes.
- Benefits: Accelerates the design iteration process, enabling faster development cycles and more efficient testing of new concepts.
Hybrid Components:
- Application: Combining AM with traditional manufacturing methods to produce hybrid parts that incorporate both additive and subtractive features.
- Benefits: Enhances part functionality and performance by integrating complex AM-built structures with precision-machined surfaces.
Fuel System Components:
- Application: Manufacturing fuel lines, pumps, and valves with intricate pathways for improved fuel efficiency.
- Benefits: Enhances fuel flow management, reduces weight, and increases the overall efficiency of the fuel system.
Benefits of AM in Aerospace:
Weight Reduction:
- AM enables the creation of lightweight structures without compromising strength, crucial for improving fuel efficiency and reducing emissions.
Design Optimization:
- Advanced design capabilities allow for the optimization of parts for performance and functionality, incorporating features like internal channels and complex geometries.
Material Efficiency:
- AM reduces material waste by using only the necessary amount to build the part, contributing to cost savings and sustainability.
Customization and Flexibility:
- AM facilitates the production of customized and complex parts tailored to specific aerospace applications, enhancing performance and integration.
Rapid Prototyping and Innovation:
- Accelerates the prototyping process, enabling faster testing and validation of new designs, fostering innovation and reducing time-to-market.
Supply Chain Efficiency:
- On-demand production of spare parts reduces the need for large inventories, streamlines the supply chain, and ensures timely availability of critical components.
Enhanced Performance:
- AM allows for the integration of multiple functions into a single part, improving overall system performance and reducing assembly complexity.
Conclusion: Additive manufacturing offers transformative benefits to the aerospace industry by enabling the production of complex, lightweight, and high-performance components. Its ability to optimize designs, reduce weight, and streamline production processes enhances the efficiency, sustainability, and innovation capabilities of aerospace manufacturers. As AM technologies continue to advance, their integration into aerospace applications is expected to expand, driving further improvements in aircraft performance and operational efficiency.
11. What are the economic implications of adopting additive manufacturing in industrial sectors, and how can businesses assess the return on investment (ROI)?
Answer:
Adopting additive manufacturing (AM) in industrial sectors has significant economic implications, influencing cost structures, production efficiencies, and market competitiveness. Businesses must carefully evaluate these factors to assess the return on investment (ROI) and determine the financial viability of integrating AM technologies.
Economic Implications:
Initial Investment Costs:
- Implication: High upfront costs for purchasing AM equipment, software, and materials can be a barrier, particularly for small and medium-sized enterprises (SMEs).
- Consideration: Assess the capital expenditure required and explore financing options or leasing models to mitigate financial strain.
Reduction in Tooling and Setup Costs:
- Implication: AM eliminates the need for expensive tooling and molds required in traditional manufacturing, reducing setup costs for production runs.
- Benefit: Lowers initial production costs and enables more cost-effective prototyping and small-batch manufacturing.
Material Savings and Efficiency:
- Implication: AM uses only the necessary material to build parts, minimizing waste and reducing material costs compared to subtractive manufacturing.
- Benefit: Enhances cost efficiency and supports sustainable manufacturing practices.
Labor Cost Reduction:
- Implication: Automation and reduced manual intervention in AM processes can lower labor costs.
- Benefit: Increases productivity and reduces expenses related to labor-intensive manufacturing processes.
Inventory and Supply Chain Optimization:
- Implication: AM enables on-demand production, reducing the need for large inventories and associated storage costs.
- Benefit: Streamlines supply chain management, lowers inventory holding costs, and reduces the risk of overproduction and obsolescence.
Customization and Market Differentiation:
- Implication: AM allows for the production of customized and unique products without significant additional costs.
- Benefit: Enables businesses to differentiate their offerings, meet specific customer needs, and tap into niche markets, potentially commanding higher prices.
Shortened Time-to-Market:
- Implication: Rapid prototyping and faster production cycles facilitate quicker product development and deployment.
- Benefit: Enhances competitiveness by enabling businesses to respond swiftly to market demands and emerging trends.
Maintenance and Spare Parts Production:
- Implication: AM allows for the on-demand production of spare parts, reducing downtime and maintenance costs.
- Benefit: Improves operational efficiency and minimizes the financial impact of equipment failures.
Assessing Return on Investment (ROI):
Cost-Benefit Analysis:
- Action: Compare the total costs of adopting AM (equipment, materials, training) against the expected financial benefits (cost savings, increased revenue).
- Benefit: Provides a clear picture of the financial viability and potential profitability of AM adoption.
Break-Even Analysis:
- Action: Determine the point at which the savings and benefits from AM offset the initial investment costs.
- Benefit: Helps in understanding the timeline for achieving profitability from AM investments.
Productivity Metrics:
- Action: Measure changes in production speed, output volume, and labor productivity post-AM adoption.
- Benefit: Quantifies the efficiency gains and their impact on overall production capacity and costs.
Quality Improvement Evaluation:
- Action: Assess the impact of AM on product quality, defect rates, and customer satisfaction.
- Benefit: Higher quality products can lead to increased sales, reduced returns, and enhanced brand reputation.
Supply Chain Impact Assessment:
- Action: Evaluate how AM affects inventory levels, lead times, and supply chain resilience.
- Benefit: Improved supply chain efficiency can lead to cost savings and better market responsiveness.
Customization and Market Expansion Analysis:
- Action: Analyze the potential for offering customized products and entering new markets enabled by AM.
- Benefit: Additional revenue streams from niche markets can enhance overall ROI.
Energy and Resource Savings:
- Action: Calculate reductions in energy consumption and material usage achieved through AM.
- Benefit: Lower operational costs contribute directly to improved ROI and sustainability goals.
Risk Assessment:
- Action: Identify and evaluate potential risks associated with AM adoption, such as technology obsolescence or integration challenges.
- Benefit: Mitigating risks ensures that the investment remains secure and benefits are sustained over time.
Conclusion: Adopting additive manufacturing can offer substantial economic benefits, including cost savings, increased efficiency, and new revenue opportunities. However, businesses must conduct thorough ROI assessments by analyzing costs, benefits, productivity gains, quality improvements, and market opportunities to make informed investment decisions. A strategic approach to evaluating the economic implications ensures that businesses can effectively leverage AM technologies to enhance their competitive edge and achieve long-term financial success.
12. How does additive manufacturing support innovation and design freedom in product development, and what are some examples of innovative products created using AM?
Answer:
Additive manufacturing (AM) significantly enhances innovation and design freedom in product development by enabling the creation of complex, customized, and optimized designs that are difficult or impossible to achieve with traditional manufacturing methods. This capability fosters creativity, accelerates innovation cycles, and allows for the exploration of new product concepts.
Support for Innovation and Design Freedom:
Complex Geometries and Organic Shapes:
- Benefit: AM allows for the production of intricate and organic shapes, including internal structures and lattices, without the constraints of traditional manufacturing tools.
- Impact: Enables the development of parts with optimized strength-to-weight ratios, improved aerodynamics, and unique aesthetic features.
Topology Optimization:
- Benefit: Facilitates the design of parts optimized for specific performance criteria, such as maximum strength with minimal material usage.
- Impact: Results in lightweight, high-performance components suitable for applications in aerospace, automotive, and medical industries.
Customization and Personalization:
- Benefit: Supports the production of customized products tailored to individual customer needs without significant cost increases.
- Impact: Enhances customer satisfaction and allows businesses to cater to niche markets, such as personalized medical implants or bespoke consumer products.
Rapid Prototyping and Iterative Design:
- Benefit: Enables quick production of prototypes for testing and validation, allowing for faster iteration and refinement of designs.
- Impact: Accelerates the product development cycle, reducing time-to-market and fostering continuous innovation.
Integration of Multiple Functions:
- Benefit: Allows for the integration of multiple functional elements within a single part, such as embedding electronics or incorporating moving components.
- Impact: Simplifies assembly processes, reduces part counts, and enhances the functionality of products.
Material and Process Innovation:
- Benefit: Drives the development of new materials and AM processes tailored to specific applications, expanding the range of possible products.
- Impact: Facilitates the creation of products with enhanced properties, such as biocompatible materials for medical devices or high-strength metals for aerospace components.
Examples of Innovative Products Created Using AM:
Aerospace Components:
- Example: GE Aviation’s fuel nozzles for jet engines, manufactured using Direct Metal Laser Sintering (DMLS).
- Innovation: Complex internal cooling channels that improve fuel efficiency and engine performance.
Medical Implants:
- Example: Customized titanium bone implants created using Electron Beam Melting (EBM).
- Innovation: Implants tailored to patient-specific anatomy, enhancing fit and integration with bone tissue.
Automotive Lightweight Parts:
- Example: Ford’s 3D-printed brake calipers for prototype vehicles.
- Innovation: Lightweight designs that maintain strength and durability, contributing to overall vehicle efficiency.
Consumer Products:
- Example: Adidas’ 3D-printed running shoes with customized midsole structures.
- Innovation: Enhanced cushioning and support tailored to individual runner biomechanics, improving performance and comfort.
Architectural Models:
- Example: Complex architectural models with intricate details and internal structures produced using SLA and DLP technologies.
- Innovation: Highly detailed representations that accurately reflect complex design concepts and structural elements.
Robotics Components:
- Example: Custom 3D-printed joints and parts for humanoid robots.
- Innovation: Lightweight and flexible components that enhance robot mobility and functionality.
Prosthetics and Orthotics:
- Example: Personalized prosthetic limbs with customized shapes and enhanced comfort created using FDM and SLA.
- Innovation: Improved fit and functionality, increasing the quality of life for users.
Tooling and Fixtures:
- Example: Rapidly produced 3D-printed jigs and fixtures for manufacturing assembly lines.
- Innovation: Quick customization and adjustment of tooling to match changing production needs, increasing manufacturing agility.
Educational Models:
- Example: Anatomical models for medical training created using high-resolution SLA printers.
- Innovation: Detailed and accurate models that enhance the learning experience for students and professionals.
Art and Sculptures:
- Example: Intricate sculptures and artworks created using advanced AM technologies like SLS and SLA.
- Innovation: Allows artists to realize complex and detailed designs that would be challenging to produce manually.
Conclusion: Additive manufacturing profoundly supports innovation and design freedom in product development by enabling the creation of complex, customized, and optimized designs. This capability fosters creativity, accelerates the innovation process, and opens new possibilities across various industries. Examples of innovative products created using AM demonstrate the transformative potential of additive technologies in enhancing performance, customization, and efficiency, driving advancements in fields such as aerospace, medical, automotive, and consumer goods.
Conclusion:
The above thought-provoking questions and detailed answers provide a comprehensive exploration of additive manufacturing and 3D printing technologies. Covering fundamental concepts, material considerations, environmental impacts, integration with traditional manufacturing, mechanical properties, economic implications, and innovative applications, these inquiries encourage students to critically analyze and engage with the complexities of AM technologies. By delving into these topics, students are equipped with the knowledge and critical thinking skills necessary to excel in the field of additive manufacturing, promoting innovation, sustainability, and efficiency in modern industrial applications. These questions foster a deeper understanding of how AM technologies can be leveraged to achieve operational excellence, drive economic growth, and address contemporary manufacturing challenges, making learning an engaging and dynamic process.