Industrial and Manufacturing Technologies
Industrial and Manufacturing Technologies form the backbone of modern production systems, enabling the transformation of raw materials into finished goods through efficient, scalable, and intelligent processes. The discipline encompasses a wide array of integrated approaches—ranging from Additive Manufacturing (3D Printing) to Energy and Resource Efficiency in Manufacturing—that together drive innovation and sustainability in global industries.
With the increasing complexity of industrial operations, new paradigms such as Smart Manufacturing and Industry 4.0 and Digital Twin Technology are transforming traditional workflows. These technologies allow real-time monitoring, predictive analytics, and closed-loop control systems that improve productivity while minimizing waste. The evolution of Computer-Integrated Manufacturing (CIM) plays a vital role in automating entire production lines for greater flexibility and precision.
To meet growing global demands, modern industries must optimize every aspect of design and delivery. This is where Lean Manufacturing, Sustainable Manufacturing, and Supply Chain Management come into play. These methodologies focus on reducing inefficiencies, conserving resources, and ensuring environmentally conscious production practices.
Material selection and innovation are equally critical. The integration of Advanced Materials and Manufacturing Technologies not only enhances product performance but also enables new applications across aerospace, biomedical, and automotive sectors. The contribution of Nanotechnology and Advanced Materials in Mechanical Engineering further extends the boundaries of what is possible in microfabrication and nanofabrication.
Industrial success relies not just on machines but also on people. Ergonomically sound workplaces—shaped by principles from Human Factors and Ergonomics in Manufacturing—enhance safety, comfort, and performance. Meanwhile, Manufacturing Quality Control and Assurance ensures consistency and compliance with standards at every stage of production.
The role of automation cannot be overstated. From factory floors to precision machining cells, Industrial Automation and Robotics continues to redefine efficiency and adaptability. Its close cousin, Robotics and Automation in Mechanical Engineering, supports interdisciplinary advancements that merge mechanical systems with smart electronics and control strategies.
The field draws from foundational engineering domains. Knowledge of Mechanical Engineering, Thermodynamics and Heat Transfer, and Solid Mechanics provides essential understanding of how machines behave and interact with forces and energy. These principles are applied practically in Manufacturing and Production Engineering and Mechanical Design and CAD, supporting everything from concept sketches to final assembly.
Industry is also evolving toward greater interdisciplinary integration. For example, Automotive Engineering leverages insights from control theory and software development, while Control Systems in Mechanical Engineering enhance system stability and precision. The growing field of Biomechanical Engineering applies manufacturing technologies to health-related innovations, bridging the gap between human physiology and machine design.
By exploring Industrial and Manufacturing Technologies, students prepare to shape the future of industry—one that is smart, sustainable, and human-centered. Whether through digital simulation, advanced automation, or process optimization, this field offers a comprehensive toolkit for driving meaningful innovation in a rapidly evolving world.
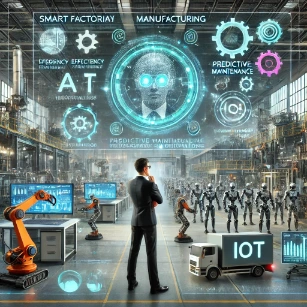
Table of Contents
Sub-Areas of Studies in Industrial and Manufacturing Technologies
Industrial Automation and Robotics
- Involves integrating automated machinery and robotics into production lines.
- Includes the use of AI and machine learning for intelligent automation.
Additive Manufacturing (3D Printing)
- Focuses on creating three-dimensional objects layer by layer from digital models.
- Applications include prototyping, custom manufacturing, and complex geometries.
Lean Manufacturing
- Aims to minimize waste and maximize value in production processes.
- Includes techniques like value stream mapping and Kaizen.
Quality Control and Assurance
- Involves monitoring and improving product quality through statistical analysis and inspection.
- Includes Six Sigma practices for defect reduction.
Supply Chain Management
- Focuses on the efficient flow of goods, information, and finances across the supply chain.
- Includes inventory management, logistics, and procurement.
Smart Manufacturing and Industry 4.0
- Integrates IoT, sensors, and data analytics to create connected and intelligent production environments.
- Enables real-time monitoring and decision-making.
Energy and Resource Efficiency in Manufacturing
- Studies methods to reduce energy consumption and optimize resource utilization in manufacturing.
- Includes renewable energy integration and sustainable practices i manufacturing and other industrial processes.
Manufacturing Process Design and Optimization
- Involves designing efficient manufacturing systems and workflows.
- Uses simulation tools to optimize production layouts and reduce downtime.
Computer-Integrated Manufacturing (CIM)
- Focuses on integrating CAD (Computer-Aided Design) and CAM (Computer-Aided Manufacturing) for seamless production.
- Includes CNC machining and automated assembly lines.
Sustainable Manufacturing
- Develops eco-friendly production techniques to minimize environmental impact.
- Includes recycling, waste reduction, and the use of sustainable materials.
Human Factors and Ergonomics in Manufacturing
- Examines the interaction between workers and machines to improve safety and efficiency.
- Focuses on designing workstations and processes that reduce fatigue and increase productivity.
Advanced Materials and Manufacturing Technologies
- Involves the use of advanced materials like composites, alloys, and nanomaterials.
- Includes research into material properties for specialized applications.
Digital Twin Technology
- Uses virtual models of manufacturing systems to simulate, predict, and optimize real-world processes.
- Enables predictive maintenance and process improvements.
Key Applications in Industrial and Manufacturing Technologies
Automation and Robotics in Assembly Lines
- Modern industrial environments have revolutionized the way goods are produced by integrating advanced robotics and automation technologies into assembly lines. Robots equipped with vision systems and precise end-effectors now handle intricate assembly tasks that were once exclusive to skilled human labor, ensuring higher consistency and repeatability across product lines.
- These robots are programmed to perform operations like welding, painting, screwdriving, and even component testing with remarkable speed and accuracy. Automation reduces the margin of human error and enhances throughput, especially in high-volume manufacturing settings such as automotive and electronics industries.
- Collaborative robots, or cobots, represent a major shift in automation by enabling human-robot teamwork. Unlike traditional industrial robots confined to cages, cobots are designed with safety features such as force sensing and vision guidance, allowing them to operate safely in proximity to humans. These cobots assist workers in tasks like lifting heavy parts, inserting precision components, or assembling delicate mechanisms, thus improving ergonomics and reducing workplace injuries.
- Advanced robotic systems are also integrated with machine learning algorithms that allow them to adapt to changing production conditions, detect anomalies, and self-optimize over time. This dynamic response capability leads to improved process efficiency and adaptability in low-volume, high-mix manufacturing environments.
- Integration of robotics with digital twins—virtual representations of physical systems—enables simulation of manufacturing processes before deployment, reducing commissioning times and optimizing layout design. Companies also leverage cloud-based robotic process management systems to monitor and control operations remotely across multiple facilities.
- According to International Federation of Robotics (IFR), the global industrial robot installation reached nearly 553,000 units in 2022, reflecting rapid adoption across various sectors.
Quality Control Systems and Predictive Maintenance
- Ensuring product quality is critical in maintaining customer trust and complying with international standards. Modern quality control systems use high-resolution cameras, infrared sensors, laser profilers, and X-ray scanning to inspect products in real-time during different stages of production. These systems are capable of detecting minute defects such as scratches, alignment errors, and material inconsistencies.
- Incorporating machine vision technology has drastically improved the accuracy and speed of defect detection. AI-powered visual inspection systems not only identify defects but also classify them based on severity, allowing for automated sorting or rework instructions to be issued without manual intervention.
- Statistical Process Control (SPC) software continuously monitors process variables and flags anomalies that could lead to out-of-spec products. These tools enable engineers to proactively intervene before deviations escalate, ensuring product consistency and reducing waste.
- Predictive maintenance has emerged as a game-changer in industrial operations by shifting the paradigm from reactive to proactive maintenance. Instead of waiting for machinery to fail, manufacturers now use data from vibration sensors, thermography, ultrasound, and oil analysis to forecast wear and degradation patterns.
- Using AI and machine learning models trained on historical equipment data, these systems identify potential failure points and recommend maintenance schedules tailored to real-world usage conditions. This approach not only minimizes unplanned downtime but also extends equipment lifespan and reduces maintenance costs.
- Predictive analytics platforms also integrate with Enterprise Resource Planning (ERP) systems to automate parts ordering, technician scheduling, and reporting. Maintenance dashboards provide managers with real-time KPIs, risk alerts, and cost analysis, facilitating data-driven decisions.
Lean Manufacturing and Six Sigma Practices
- Lean manufacturing emphasizes eliminating non-value-added activities in the production process. By adopting principles like just-in-time inventory, continuous flow, and takt time balancing, manufacturers achieve significant reductions in lead times and inventory holding costs.
- Value Stream Mapping (VSM) is a core tool used to visualize and analyze material and information flows. This allows cross-functional teams to identify bottlenecks, reduce handoffs, and streamline communication across departments. Tools like 5S and Kanban boards support workplace organization and demand-driven production scheduling.
- Kaizen, or continuous improvement, is ingrained in lean culture. It involves empowering frontline workers to suggest and implement process improvements, fostering a culture of collaboration and ownership. Daily Gemba walks and improvement huddles are common practices in lean environments.
- Six Sigma complements lean by focusing on reducing process variation and improving quality. It uses DMAIC (Define, Measure, Analyze, Improve, Control) methodology to tackle complex quality problems. Techniques such as Design of Experiments (DOE), Failure Mode and Effects Analysis (FMEA), and Root Cause Analysis (RCA) help uncover process inefficiencies and prevent recurrence of defects.
- Lean Six Sigma certification programs train professionals to lead improvement projects using statistical tools and data analysis software such as Minitab and JMP. These experts, known as Green Belts and Black Belts, drive initiatives that lead to cost savings, enhanced quality, and customer satisfaction.
- Organizations that embed lean and Six Sigma principles across their value chains often gain a competitive advantage by responding faster to market changes and customer needs while maintaining low operational costs and high product quality.
Supply Chain Optimization and Logistics
- In a globalized economy, efficient supply chain management is essential for timely product delivery and cost control. Advanced supply chain optimization uses real-time data, AI, and predictive analytics to manage inventory, forecast demand, and optimize logistics networks.
- Technologies such as RFID tags, barcoding, and IoT sensors provide granular visibility into product location, condition, and movement. This visibility reduces shrinkage, enhances accountability, and ensures compliance with traceability standards, particularly in food and pharmaceutical industries.
- GPS tracking and geofencing enable dynamic routing of delivery vehicles based on traffic and weather conditions, improving on-time performance and fuel efficiency. Digital twins of logistics networks help simulate disruptions and test contingency plans in a virtual environment before implementation.
- Warehouse automation through Automated Guided Vehicles (AGVs), robotic pickers, and high-density storage systems improves fulfillment speed and space utilization. Integration of these systems with Warehouse Management Systems (WMS) allows for real-time tracking of inventory levels and replenishment planning.
- Advanced planning systems use machine learning algorithms to balance supply and demand, optimize procurement schedules, and reduce stockouts and overproduction. These tools integrate with Customer Relationship Management (CRM) platforms to align inventory levels with market trends and promotional campaigns.
- Blockchain technology is being explored to ensure transparency, trust, and traceability in multi-tier supply chains. For example, verifying product origin and ethical sourcing practices is now possible through immutable digital ledgers.
Current Developments in Industrial and Manufacturing Technologies
Industry 4.0 Integrating IoT and Smart Sensors
- Industry 4.0 represents a transformative phase in industrial evolution where the physical and digital worlds are tightly integrated through the Internet of Things (IoT), cyber-physical systems, and cloud-based platforms. By embedding sensors, actuators, and connectivity into machines, manufacturers are now able to capture real-time data from virtually every component of the production process.
- Smart sensors play a pivotal role by continuously monitoring equipment performance metrics such as temperature, vibration, pressure, and operational speed. These devices feed information into central control systems that can trigger automated responses, such as adjusting machine parameters or initiating maintenance protocols without human intervention.
- IoT-enabled networks ensure seamless data communication between machines (machine-to-machine or M2M), enabling decentralized decision-making and self-optimization across the production line. This results in enhanced operational visibility, fewer production bottlenecks, and faster reaction times to system anomalies.
- Smart factories leverage edge computing to process data locally on devices, reducing latency and bandwidth usage. These systems can detect faults early, issue alerts, and support condition-based monitoring, reducing unplanned downtime and improving productivity.
- By integrating IoT with enterprise software platforms such as MES (Manufacturing Execution Systems) and ERP (Enterprise Resource Planning), companies achieve vertical and horizontal integration across manufacturing operations, supply chains, and business units.
- Adoption of open industrial standards like OPC UA facilitates interoperability between heterogeneous devices and systems, supporting scalability and future-proofing infrastructure. A detailed overview of these technologies and their impact can be found through the World Economic Forum’s Industry 4.0 initiative.
Advanced Manufacturing Techniques like Additive Manufacturing
- Additive manufacturing (AM), commonly referred to as 3D printing, continues to disrupt traditional production methods by enabling the fabrication of parts layer-by-layer directly from digital models. This technique eliminates the need for complex tooling and allows for the creation of highly customized components with intricate internal geometries that are impossible to achieve using subtractive processes.
- Industries ranging from aerospace and automotive to medical device manufacturing utilize AM to produce lightweight components, patient-specific implants, and rapid prototypes. Materials used in additive manufacturing now extend beyond plastics to include metals, ceramics, and composite materials, expanding its applicability in critical structural and functional components.
- Hybrid manufacturing systems are emerging that combine AM with CNC machining, enabling post-processing of printed parts to achieve desired tolerances and surface finishes. This hybrid approach combines the geometric freedom of AM with the precision of traditional machining.
- Advancements in software tools also play a key role. Generative design algorithms create optimal part geometries by simulating load paths and material usage, leading to designs that minimize weight while maintaining structural integrity. These geometries are then directly printed using metal laser sintering or electron beam melting technologies.
- Automation of the entire AM workflow, from design and slicing to printing and post-processing, is helping reduce lead times and improve consistency. Integration with quality assurance systems ensures that parts meet industry standards through in-situ monitoring and validation techniques.
Energy-Efficient and Sustainable Production Processes
- Sustainability is a cornerstone of modern manufacturing, with increasing emphasis on reducing energy consumption, minimizing waste, and lowering emissions. Manufacturing plants are adopting renewable energy sources such as solar photovoltaic panels, wind turbines, and biomass to power production lines, thereby cutting reliance on fossil fuels.
- Advanced building automation systems monitor and manage energy use across lighting, HVAC, and machinery to optimize consumption. In addition, variable frequency drives (VFDs), energy-efficient motors, and regenerative braking systems contribute to energy savings in mechanical systems.
- Lean production principles are integrated with green manufacturing strategies to design processes that reduce resource use per unit of output. This includes redesigning workflows to minimize material movement, optimizing batch sizes, and reusing scrap materials within closed-loop recycling systems.
- Manufacturers are investing in life cycle assessment (LCA) tools to quantify the environmental impact of products from raw material extraction through end-of-life. These assessments guide design decisions that reduce carbon footprints and enhance product sustainability.
- Water conservation measures, such as closed-loop cooling systems and rainwater harvesting, further improve the environmental performance of facilities. Compliance with international standards like ISO 14001 helps ensure environmental management is embedded into the core of manufacturing operations.
AI and Machine Learning in Manufacturing
- Artificial intelligence (AI) and machine learning (ML) are redefining manufacturing by enabling data-driven optimization at every level of the production cycle. Predictive analytics based on historical data sets allow manufacturers to anticipate production issues, forecast demand, and dynamically adjust inventory and schedules.
- ML models are used to analyze vast amounts of sensor and machine data to detect subtle deviations from normal operating conditions. This facilitates predictive maintenance and reduces costly machine breakdowns. AI-powered vision systems enhance quality control by identifying defects that may not be visible to the human eye.
- Natural language processing (NLP) interfaces allow operators to interact with machines using spoken or written commands, improving usability and reducing training requirements. Reinforcement learning algorithms enable robots to improve their performance through trial-and-error interactions with their environment.
- AI is also being used in demand forecasting, pricing optimization, and product design. For example, digital design assistants recommend design alternatives based on performance criteria and historical data. AI algorithms balance multiple objectives such as cost, weight, and manufacturability in real-time.
Digital Twin Technology
- Digital twin technology involves creating a real-time digital replica of a physical asset, such as a machine, production line, or entire factory. These virtual models enable simulation, monitoring, and control of physical systems in a digital environment, allowing for risk-free testing and performance evaluation before implementing changes in the real world.
- By integrating data from sensors, control systems, and enterprise software, digital twins provide a comprehensive view of system behavior under varying conditions. Engineers use them to test process improvements, optimize layouts, and predict system responses to disruptions.
- Predictive analytics based on digital twin data help identify performance trends and anticipate maintenance needs, improving asset reliability and operational efficiency. They also support training programs by providing immersive, hands-on experiences in a virtual space.
- Industries such as aerospace, automotive, and pharmaceuticals leverage digital twins to validate manufacturing processes for regulatory compliance. The use of digital twins is expanding beyond individual machines to encompass entire supply chains, where they simulate demand variability, transport logistics, and supplier dynamics.
Augmented Reality (AR) in Manufacturing
- Augmented Reality (AR) enhances manufacturing operations by overlaying digital information—such as instructions, blueprints, and diagnostic data—onto the physical workspace through smart glasses, tablets, or headsets. This technology streamlines tasks like assembly, maintenance, inspection, and training by providing workers with real-time, hands-free access to critical information.
- AR guides technicians through complex processes by displaying step-by-step instructions and animated 3D models aligned with physical components. This reduces errors, shortens training time, and enables less-experienced staff to perform tasks typically reserved for experts.
- AR-based remote assistance allows field technicians to collaborate with experts located anywhere in the world, who can see what the technician sees and provide guidance in real-time. This accelerates problem resolution and reduces service costs.
- Design and engineering teams use AR to visualize prototypes and production layouts at full scale, enabling early identification of spatial constraints and ergonomic issues. This enhances collaboration between design and manufacturing teams and shortens product development cycles.
Challenges in Industrial and Manufacturing Technologies
Integration of New Technologies
- Integrating cutting-edge technologies such as IoT, artificial intelligence, machine learning, and robotics into traditional manufacturing environments poses complex challenges. Legacy systems may lack compatibility with modern platforms, requiring extensive retrofitting or full replacement. This transition demands both technical and financial resources, often acting as a barrier for small and medium-sized enterprises (SMEs).
- In addition, the implementation phase can disrupt ongoing production due to downtime, calibration needs, or the requirement for extensive employee training. Ensuring interoperability between new and existing equipment—particularly when sourced from different vendors—requires standardized communication protocols and robust middleware solutions.
- Another layer of complexity involves aligning digital transformation efforts with broader business goals. Manufacturers must determine return on investment (ROI) metrics for new technologies while ensuring that integration aligns with productivity, safety, and sustainability objectives. Organizational resistance to change further complicates technology adoption, as teams accustomed to traditional workflows may be hesitant to embrace new systems.
- To address these issues, phased implementation strategies and pilot projects are often adopted to test compatibility and ROI before full deployment. Systems integrators and consultants can play a vital role in streamlining the transition and reducing associated risks.
Sustainability Goals
- As governments, investors, and consumers increasingly prioritize sustainability, manufacturers are under growing pressure to reduce their environmental impact. This includes lowering greenhouse gas emissions, minimizing material waste, optimizing energy usage, and sourcing eco-friendly materials. Achieving these goals, however, often entails additional costs in the short term, such as upgrading to energy-efficient machinery, investing in clean technologies, or reconfiguring supply chains.
- Compliance with international and local environmental regulations requires continuous monitoring and reporting. For example, achieving ISO 14001 certification involves significant documentation, audits, and operational adjustments. Manufacturers must also anticipate and adapt to evolving legislation related to carbon taxation, extended producer responsibility (EPR), and circular economy requirements.
- In some cases, environmentally friendly practices may be at odds with cost-efficiency or productivity goals. For instance, replacing inexpensive plastics with biodegradable materials may raise material costs, while energy-efficient systems might have longer payback periods. Nonetheless, sustainability can be a strategic advantage—enhancing brand reputation and long-term viability—if integrated thoughtfully into core manufacturing processes.
- Many organizations are now adopting environmental KPIs, digital monitoring systems, and green design principles to track and improve performance. A helpful resource for understanding how manufacturers balance profit and sustainability is the McKinsey report on Sustainability and Profit.
Workforce Adaptation
- The transition toward smart manufacturing and Industry 4.0 technologies has reshaped the skills required in modern factories. As automation takes over routine tasks, workers are increasingly expected to manage, troubleshoot, and optimize complex systems involving robotics, AI, and cloud-based platforms. However, the existing workforce may lack the training necessary to adapt to these new demands.
- Manufacturers face the dual challenge of upskilling current employees while also attracting a new generation of workers with expertise in mechatronics, cybersecurity, data analytics, and digital engineering. Traditional vocational training programs may be insufficient, necessitating partnerships with educational institutions, reskilling initiatives, and internal knowledge-sharing platforms.
- Beyond technical proficiency, change management is essential to overcome cultural resistance. Employees may perceive automation as a threat to job security, leading to reduced morale and cooperation. Clear communication, involvement in transformation processes, and retraining programs can help mitigate these concerns and foster a more collaborative environment.
- Organizations that proactively address workforce adaptation not only improve employee engagement but also enhance their competitive edge by creating a flexible and innovation-ready team. Cross-functional training and job rotation strategies further promote versatility and knowledge retention across departments.
Global Supply Chain Disruptions
- Recent events, such as the COVID-19 pandemic, the Russia-Ukraine conflict, and ongoing geopolitical tensions, have highlighted the fragility of global supply chains. Manufacturers dependent on just-in-time delivery models and overseas suppliers have faced material shortages, shipping delays, and volatile prices. Disruptions to raw material sourcing, port operations, and transportation infrastructure continue to challenge supply chain resilience.
- To mitigate these risks, companies are exploring localized or regionalized supply chains, diversifying their supplier base, and investing in supply chain visibility technologies. Digital twins and AI-powered analytics are being deployed to simulate disruption scenarios and identify contingency plans.
- In addition, geopolitical factors like trade tariffs, embargoes, and political instability in supplier regions must be considered in strategic planning. Supply chain managers must now incorporate risk assessment, supplier evaluation, and strategic buffering into their decision-making frameworks.
- Emerging trends such as nearshoring and reshoring are reshaping global manufacturing dynamics, offering new opportunities for regional economies while demanding adaptive strategies from existing production hubs. Blockchain is also being explored for traceability and accountability within complex, multi-tiered supply networks.
Cybersecurity
- As manufacturing systems become increasingly connected, they also become more vulnerable to cyberattacks. Threats such as ransomware, data breaches, and industrial espionage can severely disrupt operations, compromise intellectual property, and jeopardize customer data. The convergence of IT (Information Technology) and OT (Operational Technology) environments creates new attack surfaces that traditional security measures may not adequately protect.
- Securing smart factories requires a multi-layered approach, including network segmentation, firewalls, intrusion detection systems, secure authentication protocols, and regular software updates. Employee training in cybersecurity best practices is equally important, as phishing attacks and human error remain major causes of breaches.
- Manufacturers must also comply with cybersecurity regulations and standards such as NIST, ISO/IEC 27001, and GDPR, particularly when operating across borders. These frameworks ensure that data protection, incident response, and risk management are embedded in operational protocols.
- Incident response planning and cyber insurance are becoming standard components of risk management strategies. Manufacturers should routinely test backup systems, conduct penetration testing, and collaborate with cybersecurity experts to stay ahead of evolving threats.
Future Trends and Opportunities in Industrial and Manufacturing Technologies
Hyper-Automation
- Hyper-automation represents the next evolution in industrial automation by integrating a suite of advanced technologies such as artificial intelligence (AI), machine learning, Internet of Things (IoT), robotic process automation (RPA), and cloud computing to create intelligent, self-operating production systems. The core aim is to minimize human intervention across operational layers—from planning and scheduling to quality assurance and maintenance—by leveraging interconnected systems capable of learning, adapting, and optimizing in real time.
- For example, in a hyper-automated smart factory, AI algorithms analyze production data from IoT sensors to anticipate bottlenecks or equipment failures before they occur. Robotic arms, guided by machine vision and edge computing, autonomously reconfigure themselves for new production runs, while predictive analytics ensure that supply chains remain agile and responsive to changes in demand. This level of automation allows manufacturers to shift from reactive to proactive operations, dramatically increasing productivity and agility.
- The long-term vision for hyper-automation involves fully autonomous facilities that can handle dynamic product portfolios with minimal downtime. These factories will use digital twins to simulate different operational scenarios, blockchain for transparent supply chain traceability, and augmented reality (AR) for real-time diagnostics and support. By embracing hyper-automation, industries can unlock new levels of efficiency, cost savings, and scalability, positioning themselves to meet the rapidly evolving demands of global markets.
Personalized Manufacturing
- Personalized manufacturing, also known as mass customization, is transforming how goods are designed, produced, and delivered. By enabling consumers to tailor products to their unique specifications—whether it’s a custom-fit medical device, a personalized car interior, or tailored fashion—manufacturers are shifting from one-size-fits-all models to flexible, customer-centric production strategies. Technologies such as additive manufacturing (3D printing), digital design platforms, and flexible robotic systems are key enablers of this transformation.
- In the healthcare sector, for instance, 3D printing allows for the rapid production of prosthetics, dental implants, and surgical guides tailored to individual anatomy. In the automotive industry, digital twins and modular assembly lines facilitate the customization of interior layouts, infotainment systems, and even performance parameters based on driver profiles. These advances have led to greater customer satisfaction, reduced inventory overhead, and shorter lead times.
- To support personalized manufacturing, companies are also integrating advanced data analytics and AI to capture and interpret customer preferences. This data is then translated into production instructions without disrupting existing workflows. Cloud-based configurators and virtual showrooms further enhance the experience by allowing customers to visualize their choices in real time before placing an order. As demand for customization grows, manufacturers are investing in flexible, small-batch production technologies that maintain cost-efficiency and quality.
- For deeper insight into how 3D printing is revolutionizing customized product development, the Forbes article on 3D Printing and Personalized Manufacturing provides excellent examples and analysis.
Zero-Waste Manufacturing
- Zero-waste manufacturing aspires to eliminate waste from the production process entirely by rethinking how resources are used, reused, and recovered. Grounded in circular economy principles, this approach prioritizes material efficiency, closed-loop recycling, and energy recovery. By reducing waste generation at the source and reintegrating byproducts into new production cycles, manufacturers can lower environmental impacts, reduce costs, and improve regulatory compliance.
- Key strategies include designing products for disassembly, using biodegradable or recyclable materials, and implementing material flow analyses to identify waste hotspots. Advanced sorting and separation technologies, such as AI-enabled vision systems and sensor-based sorters, facilitate the separation of reusable components. Companies are also adopting modular product architectures that allow worn-out components to be replaced without discarding the entire unit.
- Wastewater from manufacturing processes can be treated and reused, while waste heat is captured for use in other stages of production. Additionally, digital tools like life cycle assessment (LCA) and material flow analysis help companies track and optimize their resource efficiency. By aligning with sustainability goals and stakeholder expectations, zero-waste manufacturing becomes both an environmental necessity and a competitive advantage.
5G Connectivity in Smart Factories
- 5G networks are unlocking new possibilities for smart factories by providing ultra-low latency, high-speed, and reliable wireless communication. Unlike traditional Wi-Fi or 4G systems, 5G can simultaneously support thousands of connected devices, making it ideal for dense industrial environments where robots, sensors, and machines must operate in synchrony. With real-time connectivity, production lines become more responsive, agile, and autonomous.
- In practice, 5G enables seamless communication between mobile robots and automated guided vehicles (AGVs), which navigate warehouses and shop floors with high precision. Maintenance teams use AR headsets connected via 5G for remote support and diagnostics, while machine vision systems transmit high-resolution video streams to central analytics hubs. Moreover, 5G’s network slicing allows for the creation of dedicated virtual networks for different applications, ensuring performance reliability.
- The integration of 5G also enhances safety by enabling faster response times for emergency shutdown systems and remote control of hazardous operations. Cloud-based manufacturing execution systems (MES) can now process and respond to sensor data in milliseconds, optimizing resource allocation and minimizing downtime. As deployment expands, 5G is set to become the digital backbone of Industry 4.0 ecosystems.
Green and Decarbonized Manufacturing
- Green manufacturing focuses on minimizing environmental impact by transitioning to carbon-neutral operations. This includes the use of renewable energy sources like solar, wind, and bioenergy; upgrading equipment for energy efficiency; and adopting green chemistry to replace hazardous substances. The goal is to decouple industrial growth from environmental degradation while maintaining profitability and innovation.
- Companies are now investing in lifecycle carbon accounting to track emissions at every stage of the production chain—from raw material extraction to final delivery. They are also exploring innovations such as carbon capture and storage (CCS), bio-based materials, and low-emission process redesigns. Industrial symbiosis, where waste from one process becomes input for another, is gaining popularity in eco-industrial parks.
- Regulatory bodies and investors are increasingly demanding transparency on environmental performance, prompting manufacturers to publish sustainability reports and participate in carbon disclosure programs. Certification standards like ISO 14064 and Science-Based Targets initiative (SBTi) offer frameworks for setting and verifying emissions reductions. As the urgency to combat climate change intensifies, decarbonized manufacturing will play a central role in building a sustainable global economy.
Human-Machine Collaboration
- Rather than replacing humans, the future of manufacturing lies in enhancing human capabilities through collaboration with intelligent machines. Cobots (collaborative robots) are designed to work safely alongside humans, performing repetitive, dangerous, or ergonomically challenging tasks while allowing workers to focus on higher-level functions. These interactions are facilitated by sophisticated safety systems, force sensors, and intuitive programming interfaces.
- AI-powered assistants can support decision-making by providing real-time insights into production metrics, quality control parameters, and predictive maintenance alerts. Workers equipped with wearable technologies or AR headsets gain instant access to manuals, training modules, and expert guidance, improving efficiency and reducing error rates. Human-centric design ensures that workstations accommodate a wide range of abilities and preferences.
- This collaboration extends beyond the shop floor to include co-design tools and virtual prototyping, where engineers interact with digital models to refine product features. Human input remains vital in managing exceptions, interpreting nuanced data, and driving innovation. Ultimately, human-machine collaboration enhances safety, boosts morale, and ensures inclusive technological adoption.
Career Opportunities in Industrial and Manufacturing Technologies
- Process Engineers:
Responsible for designing, analyzing, and optimizing manufacturing workflows to enhance productivity, reduce waste, and ensure consistency. Process engineers work closely with product designers, quality assurance teams, and operations managers to streamline processes from raw material input to final product output. They utilize tools such as process mapping, simulation software, and Lean Six Sigma methodologies to identify bottlenecks and implement continuous improvement initiatives. These professionals also play a crucial role in scaling up production for new product launches, ensuring compliance with environmental and safety regulations, and maintaining operational efficiency across facilities. - Robotics Engineers:
Tasked with developing, deploying, and maintaining robotic systems that automate repetitive or hazardous tasks in manufacturing environments. Robotics engineers combine knowledge of mechanical engineering, electrical systems, computer programming, and artificial intelligence to build machines capable of performing complex functions with precision. Their work involves designing robotic arms, programming movements, integrating machine vision, and ensuring seamless interaction between robots and human workers (cobots). In industries like automotive, electronics, and pharmaceuticals, robotics engineers help increase throughput, reduce labor costs, and improve workplace safety. These roles are evolving rapidly with the adoption of advanced automation and smart factory technologies. - Quality Assurance Specialists:
Focused on maintaining product excellence by enforcing rigorous quality standards throughout the manufacturing process. They design inspection protocols, conduct audits, and implement statistical process control to detect defects and inconsistencies. These specialists also lead root cause analysis for quality failures and work collaboratively with engineers and production teams to apply corrective and preventive actions. The use of automated inspection systems, such as machine vision and AI-powered quality control platforms, is becoming increasingly prevalent. Certifications such as Six Sigma, ISO 9001, and Total Quality Management (TQM) are often essential for professionals in this role, emphasizing the importance of quality in maintaining brand reputation and customer satisfaction. - Supply Chain Analysts:
Play a key role in ensuring that materials, components, and finished goods move efficiently through the supply chain. They analyze data on supplier performance, inventory levels, transportation logistics, and customer demand to identify areas for improvement. Tools such as ERP systems, predictive analytics, and real-time tracking technologies enable them to reduce lead times, prevent stockouts, and optimize warehouse operations. In a globalized economy, supply chain analysts must also assess risk related to geopolitical factors, climate disruptions, and pandemics. According to the Association for Supply Chain Management (ASCM), professionals with certifications such as CPIM or CSCP have an edge in this dynamic field. - Sustainability Engineers:
Responsible for integrating environmental considerations into industrial and manufacturing systems. They develop strategies to reduce carbon footprints, minimize waste, and optimize resource usage. This involves conducting life cycle assessments, selecting sustainable materials, and designing processes that comply with environmental regulations such as ISO 14001. Sustainability engineers also contribute to circular economy initiatives by promoting recycling, reuse, and renewable energy integration. Their role is critical in aligning manufacturing practices with corporate sustainability goals and in meeting the growing consumer demand for eco-friendly products. They often collaborate with policymakers, NGOs, and research institutions to drive innovation in green manufacturing. - Data Scientists:
Leverage advanced analytics, machine learning, and big data platforms to improve decision-making in manufacturing environments. By analyzing datasets generated from sensors, production logs, supply chains, and quality inspections, data scientists uncover insights that lead to operational improvements, cost savings, and predictive maintenance strategies. Their work enables the development of smart factories where real-time data is used to control production parameters, forecast demand, and prevent equipment failures. Data scientists also support R&D by analyzing experimental results and customer feedback. Proficiency in programming languages like Python or R, and tools such as TensorFlow, SQL, and Tableau, is essential for success in this evolving and impactful role.
Why Study Industrial and Manufacturing Technologies
Improving Production Efficiency and Quality
Industrial and manufacturing technologies involve the use of machines, automation, and systems to produce goods. Students learn how to optimize production lines and ensure consistent quality. This improves productivity and competitiveness.
Design for Manufacturing and Assembly (DFMA)
Students explore how to design products that are easy to manufacture and assemble. This reduces material waste, lowers cost, and shortens lead time. DFMA principles are widely used in modern manufacturing.
Automation and Smart Manufacturing
The course covers robotics, sensors, and industrial control systems. Students learn to integrate these technologies for real-time production monitoring. These innovations support Industry 4.0 and digital transformation.
Lean Manufacturing and Process Improvement
Students study methods like Six Sigma, Kaizen, and value stream mapping. These techniques help identify inefficiencies and drive continuous improvement. This supports sustainable and cost-effective operations.
Applications in Multiple Industries
Manufacturing technologies are used in automotive, electronics, aerospace, food, and more. Students gain transferable skills applicable across sectors. This provides a strong foundation for technical and managerial careers.
Industrial and Manufacturing Technologies: Conclusion
Industrial and manufacturing technologies are pivotal to the transformation and modernization of global industries. These technologies serve as the backbone of production systems, enabling manufacturers to respond swiftly to market demands, enhance efficiency, and maintain competitiveness. The integration of robotics, automation, and digital technologies has not only improved operational precision but also enabled round-the-clock production with minimal human intervention, contributing significantly to productivity gains.
At the heart of this transformation lies the convergence of mechanical systems with information technology, a hallmark of Industry 4.0. This includes the deployment of cyber-physical systems, real-time data analytics, and advanced sensors that communicate across the manufacturing ecosystem to facilitate predictive maintenance, optimize workflows, and enhance supply chain transparency. The rise of smart factories exemplifies this shift, where machines, systems, and humans collaborate seamlessly in adaptive and self-optimizing environments.
Moreover, sustainability has become a central concern. As environmental regulations tighten and consumer expectations evolve, manufacturers are increasingly adopting green technologies and circular economy principles. This means reducing energy consumption, recycling materials, minimizing waste, and designing for disassembly and reuse. Initiatives such as carbon-neutral production lines, closed-loop manufacturing, and environmentally friendly packaging are gaining traction, demonstrating that industrial progress and environmental stewardship can coexist.
Additive manufacturing, or 3D printing, represents another frontier of innovation, allowing companies to prototype rapidly, produce complex geometries, and personalize products with minimal waste. It has opened new avenues in fields like aerospace, healthcare, automotive, and construction. Meanwhile, advanced materials like nanocomposites and smart alloys are redefining the limits of performance and durability in manufacturing applications.
Workforce development is also undergoing transformation. As traditional roles evolve or become automated, new jobs are emerging in areas such as AI integration, robotics maintenance, data science, and industrial cybersecurity. This shift necessitates continuous education and upskilling programs to prepare workers for future manufacturing environments. Organizations are partnering with technical institutes and universities to develop targeted curricula aligned with industry needs.
Policy and global collaboration are playing increasingly important roles in guiding sustainable and equitable industrial growth. Governments are implementing initiatives to promote digital infrastructure, incentivize clean energy use, and support small- and medium-sized enterprises in adopting modern manufacturing techniques. According to McKinsey & Company, companies that effectively adopt digital manufacturing technologies could improve cost-effectiveness by 10–20% while reducing time to market and increasing flexibility.
Looking ahead, the pace of innovation is expected to accelerate. The integration of 5G, edge computing, and digital twins will further refine real-time operations and simulation capabilities. Hyper-automation, personalized manufacturing, and sustainable production models will redefine how products are conceived, made, and delivered. Manufacturers that embrace these advancements will not only drive efficiency but also contribute to broader societal goals, such as reducing emissions, improving labor conditions, and fostering economic resilience.
In conclusion, industrial and manufacturing technologies are not just tools for production—they are engines of transformation. As these technologies continue to evolve, they will unlock new potentials for productivity, customization, and environmental harmony. Their role in shaping a resilient, innovative, and sustainable future cannot be overstated, positioning them as a cornerstone of global development in the 21st century and beyond.
Industrial and Manufacturing Technologies: Review Questions with Detailed Answers:
1. What are the key differences between additive and subtractive manufacturing processes, and in what scenarios is each method most effectively utilized?
Answer:
Additive and subtractive manufacturing are two fundamental approaches in the production of components and products, each with distinct methodologies and applications.
Concepts:
- Additive Manufacturing (AM): Also known as 3D printing, AM involves building objects layer by layer from materials such as plastics, metals, or composites based on digital models.
- Subtractive Manufacturing (SM): SM involves removing material from a solid block (e.g., machining, milling, drilling) to create the desired shape.
Key Differences:
- Material Usage: AM typically uses only the material needed to build the part, resulting in minimal waste, whereas SM removes excess material, leading to more waste.
- Complexity and Design Freedom: AM allows for the creation of complex geometries and internal structures that are difficult or impossible to achieve with SM. SM is generally limited to simpler shapes defined by the cutting tools used.
- Speed and Cost: For low-volume production and prototypes, AM can be faster and more cost-effective due to reduced setup times. SM is often more efficient for high-volume production where tooling costs can be amortized.
- Surface Finish and Precision: SM typically offers better surface finishes and higher precision compared to AM, which may require additional post-processing to achieve similar quality.
Effective Utilization Scenarios:
- Additive Manufacturing: Ideal for prototyping, customized or complex parts, low-volume production, and applications requiring lightweight structures, such as aerospace components and medical implants.
- Subtractive Manufacturing: Best suited for high-precision parts, high-volume production runs, and applications where surface finish and dimensional accuracy are critical, such as automotive engine parts and consumer electronics.
Conclusion: Both additive and subtractive manufacturing have their unique strengths and are often complementary in modern manufacturing environments. Selecting the appropriate method depends on factors like production volume, part complexity, material requirements, and cost considerations.
2. How does automation and robotics enhance efficiency and safety in manufacturing environments?
Answer:
Automation and robotics play a crucial role in modern manufacturing by significantly enhancing efficiency, productivity, and safety within production environments.
Concepts:
- Automation: The use of control systems, such as computers and robots, to operate machinery and processes with minimal human intervention.
- Robotics: The application of programmable mechanical devices (robots) to perform tasks that are typically repetitive, hazardous, or require high precision.
Enhancements in Efficiency:
- Increased Productivity: Robots can operate continuously without fatigue, performing tasks faster and more consistently than human workers.
- Precision and Consistency: Automation ensures high levels of accuracy and uniformity in manufacturing processes, reducing defects and improving product quality.
- Scalability: Automated systems can be easily scaled up to meet increased production demands without significant increases in labor costs.
- Reduced Cycle Times: Automation accelerates production processes, leading to shorter cycle times and faster time-to-market for products.
Enhancements in Safety:
- Hazardous Task Handling: Robots can perform dangerous tasks, such as handling toxic substances, heavy lifting, and operating in extreme environments, thereby reducing the risk of workplace injuries.
- Ergonomic Benefits: Automation minimizes the need for repetitive and physically demanding tasks, decreasing the incidence of musculoskeletal disorders among workers.
- Consistent Monitoring: Automated safety systems can continuously monitor production environments for potential hazards, enabling prompt responses to safety issues.
- Emergency Response: Automated systems can be programmed to shut down operations or initiate safety protocols in case of emergencies, enhancing overall workplace safety.
Additional Benefits:
- Cost Savings: Over time, automation and robotics can lead to significant cost reductions by lowering labor expenses and minimizing waste through improved precision.
- Flexibility: Modern robotic systems can be reprogrammed and reconfigured to handle different tasks, providing manufacturing flexibility to adapt to changing market demands.
Conclusion: Automation and robotics are integral to advancing manufacturing capabilities, offering substantial improvements in efficiency and safety. By automating repetitive, precise, and hazardous tasks, manufacturers can achieve higher productivity, better quality, and safer working conditions, ultimately leading to a more competitive and sustainable production environment.
3. What are the principles of lean manufacturing, and how do they contribute to waste reduction and process improvement?
Answer:
Lean manufacturing is a systematic approach aimed at minimizing waste while maximizing productivity and efficiency in manufacturing processes. It is based on several core principles that guide organizations in optimizing their operations.
Concepts:
- Value: Defining value from the customer’s perspective and focusing on activities that add value to the product.
- Value Stream Mapping: Analyzing the flow of materials and information to identify and eliminate waste in the production process.
- Flow: Ensuring that production processes flow smoothly without interruptions, delays, or bottlenecks.
- Pull Systems: Implementing production systems where work is initiated based on customer demand rather than forecasted demand.
- Continuous Improvement (Kaizen): Fostering a culture of ongoing incremental improvements in processes, products, and services.
Principles of Lean Manufacturing:
- Identify Value: Determine what aspects of the product or service are valued by customers and focus efforts on enhancing those elements.
- Map the Value Stream: Chart all the steps involved in producing the product, highlighting those that add value and those that do not.
- Create Flow: Reorganize production steps to ensure a seamless flow of materials and information, reducing delays and eliminating bottlenecks.
- Establish Pull: Align production with actual customer demand, producing only what is needed when it is needed, thus reducing overproduction.
- Pursue Perfection: Continuously seek ways to improve processes, eliminate waste, and enhance quality, striving for operational excellence.
Contribution to Waste Reduction:
- Overproduction: Lean focuses on producing only what is needed, thereby minimizing excess inventory and reducing storage costs.
- Waiting: By streamlining processes and ensuring a smooth flow, lean reduces idle time and delays in production.
- Transportation: Optimizing the movement of materials and information reduces unnecessary transportation, lowering costs and improving efficiency.
- Overprocessing: Simplifying processes to perform only necessary steps eliminates redundant or excessive work, saving time and resources.
- Inventory: Maintaining minimal inventory levels reduces waste associated with storage, obsolescence, and inventory holding costs.
- Motion: Designing ergonomic and efficient workflows minimizes unnecessary movement of workers and equipment, enhancing productivity.
- Defects: Implementing quality control measures and continuous improvement practices reduces the occurrence of defects, lowering rework and scrap costs.
Contribution to Process Improvement:
- Enhanced Efficiency: Streamlined processes and reduced waste lead to faster production times and lower operational costs.
- Improved Quality: Focus on value-added activities and defect prevention results in higher-quality products that meet or exceed customer expectations.
- Increased Flexibility: Lean practices enable organizations to respond quickly to changes in demand, market conditions, and customer preferences.
- Employee Engagement: Involving employees in continuous improvement initiatives fosters a sense of ownership and motivation, driving further enhancements in processes.
Conclusion: Lean manufacturing principles are fundamental to achieving waste reduction and process improvement in manufacturing environments. By focusing on value, optimizing the value stream, ensuring smooth flow, aligning production with demand, and fostering a culture of continuous improvement, organizations can enhance their operational efficiency, reduce costs, and deliver higher-quality products to customers, thereby gaining a competitive advantage in the market.
4. How does quality control differ from quality assurance in the context of manufacturing, and why are both important?
Answer:
Quality Control (QC) and Quality Assurance (QA) are two essential components of a comprehensive quality management system in manufacturing. While they are closely related, they serve distinct purposes and complement each other in ensuring product quality.
Concepts:
- Quality Control (QC): QC involves the operational techniques and activities used to fulfill quality requirements. It focuses on identifying and correcting defects in the final products.
- Quality Assurance (QA): QA encompasses the systematic processes and procedures implemented to ensure that quality requirements are consistently met throughout the production process. It is proactive and preventive in nature.
Differences Between QC and QA:
- Focus:
- QC: Concentrates on detecting and removing defects in finished products through inspections, testing, and corrective actions.
- QA: Focuses on preventing defects by ensuring that the manufacturing processes are designed and implemented to produce quality products.
- Timing:
- QC: Conducted after production processes, typically during and after manufacturing to identify defects in the final output.
- QA: Embedded in the production process from the beginning, involving planning, process definition, and continuous monitoring to prevent defects.
- Approach:
- QC: Reactive approach, dealing with quality issues as they arise by identifying and correcting defects.
- QA: Proactive approach, aiming to improve and stabilize production processes to prevent defects from occurring.
- Responsibility:
- QC: Primarily the responsibility of the production and inspection teams who perform testing and quality checks.
- QA: A broader responsibility involving all departments, including design, production, procurement, and management, to ensure overall quality standards are met.
Importance of Both QC and QA:
Comprehensive Quality Management: QC and QA work together to ensure that products meet quality standards. QA establishes the framework for quality, while QC verifies that the framework is effective.
Defect Prevention and Detection: QA minimizes the likelihood of defects by
implementing robust processes, while QC detects any defects that may still occur, ensuring that only high-quality products reach the customer.
Customer Satisfaction: By ensuring both the prevention and detection of defects, organizations can consistently deliver products that meet or exceed customer expectations, enhancing satisfaction and loyalty.
Cost Efficiency: QA reduces the occurrence of defects, lowering the costs associated with rework, scrap, and warranty claims. QC ensures that any remaining defects are caught before products reach the market, further minimizing potential financial losses.
Continuous Improvement: Both QC and QA contribute to ongoing process improvement. QA identifies areas for process enhancements to prevent defects, while QC provides feedback on product quality that can inform further process optimizations.
Conclusion: Quality Control and Quality Assurance are integral to a robust quality management system in manufacturing. QC focuses on identifying and correcting defects in finished products, while QA emphasizes preventing defects through effective process management. Together, they ensure that products consistently meet quality standards, leading to increased customer satisfaction, reduced costs, and continuous improvement in manufacturing operations.
5. What is the role of supply chain management in industrial and manufacturing technologies, and how does it impact overall production efficiency?
Answer:
Supply Chain Management (SCM) plays a pivotal role in industrial and manufacturing technologies by overseeing the flow of materials, information, and finances from suppliers to end customers. Effective SCM is essential for optimizing production efficiency, reducing costs, and ensuring timely delivery of products.
Concepts:
- Supply Chain: The interconnected network of organizations, people, activities, information, and resources involved in producing and delivering a product or service.
- Supply Chain Management: The strategic coordination and integration of supply chain activities to maximize value, achieve a sustainable competitive advantage, and meet customer demands efficiently.
Role of SCM in Industrial and Manufacturing Technologies:
- Procurement and Sourcing: Identifying and selecting suppliers that provide high-quality materials at competitive prices, ensuring a reliable supply of inputs for production.
- Inventory Management: Balancing inventory levels to meet production needs without overstocking, reducing holding costs, and minimizing the risk of obsolescence.
- Logistics and Transportation: Managing the efficient movement of materials and finished products between suppliers, manufacturing facilities, distribution centers, and customers.
- Production Planning: Coordinating production schedules with supply chain activities to ensure that materials are available when needed, preventing production delays and bottlenecks.
- Demand Forecasting: Predicting customer demand to align supply chain activities with market needs, enhancing responsiveness and reducing excess inventory.
- Quality Control: Ensuring that suppliers adhere to quality standards, maintaining the integrity and reliability of materials used in manufacturing processes.
- Technology Integration: Utilizing SCM software and technologies like Enterprise Resource Planning (ERP) systems, IoT devices, and data analytics to streamline supply chain operations and enhance visibility across the entire chain.
Impact on Overall Production Efficiency:
- Cost Reduction: Efficient SCM minimizes costs associated with procurement, inventory holding, transportation, and production downtime, leading to overall cost savings.
- Improved Timeliness: Coordinated supply chain activities ensure that materials arrive on time, enabling smooth and uninterrupted production processes and timely delivery of finished products to customers.
- Enhanced Flexibility: A responsive supply chain can quickly adapt to changes in demand, supplier disruptions, or market conditions, maintaining production efficiency and customer satisfaction.
- Quality Assurance: Effective SCM ensures that only high-quality materials are used in production, reducing defects, rework, and returns, thereby enhancing overall product quality.
- Resource Optimization: By optimizing the flow of materials and information, SCM ensures that resources are utilized effectively, reducing waste and improving sustainability in manufacturing operations.
- Competitive Advantage: Companies with efficient supply chains can offer better prices, higher quality, and faster delivery times, distinguishing themselves in the market and attracting more customers.
Conclusion: Supply Chain Management is integral to the success of industrial and manufacturing technologies, significantly impacting production efficiency and overall business performance. By optimizing the flow of materials, information, and finances, SCM enhances cost-effectiveness, timeliness, quality, and flexibility in manufacturing operations. Effective SCM not only drives operational excellence but also provides a strategic advantage in a competitive marketplace, ensuring that organizations can meet customer demands efficiently and sustainably.
6. How do Computer-Aided Design (CAD) and Computer-Aided Manufacturing (CAM) technologies integrate to streamline the manufacturing process?
Answer:
Computer-Aided Design (CAD) and Computer-Aided Manufacturing (CAM) technologies are integral components of modern manufacturing that work together to streamline the production process from design to finished product.
Concepts:
- Computer-Aided Design (CAD): CAD software enables engineers and designers to create detailed digital models and blueprints of products, allowing for precise visualization, modification, and optimization of designs.
- Computer-Aided Manufacturing (CAM): CAM software uses CAD models to generate instructions for manufacturing machinery, automating the production process and ensuring accuracy in manufacturing.
Integration of CAD and CAM:
- Seamless Data Transfer: CAD models are directly imported into CAM software, eliminating the need for manual data entry and reducing the risk of errors during the transfer process.
- Automated Toolpath Generation: CAM software analyzes the CAD model to create optimized toolpaths for machining operations, determining the most efficient paths for cutting, drilling, and shaping materials.
- Simulation and Validation: CAM systems can simulate the manufacturing process based on the CAD model, allowing engineers to identify and address potential issues before actual production begins.
- Real-Time Adjustments: The integration allows for real-time adjustments to be made in the CAD design, which can be immediately reflected in the CAM-generated manufacturing instructions, enhancing flexibility and responsiveness.
- Efficient Workflow: The combined use of CAD and CAM creates a streamlined workflow where design changes can be quickly implemented and tested in the manufacturing process, accelerating the time-to-market for new products.
Streamlining the Manufacturing Process:
- Increased Precision and Consistency: Automation in toolpath generation and machining ensures high levels of precision and consistency in the production of complex parts.
- Reduced Lead Times: The seamless integration between design and manufacturing phases minimizes delays caused by manual data handling and facilitates quicker transition from design to production.
- Enhanced Collaboration: CAD and CAM integration fosters better collaboration between design and manufacturing teams, ensuring that designs are manufacturable and meet quality standards.
- Cost Efficiency: Automated processes reduce labor costs, minimize material waste through optimized cutting paths, and lower the likelihood of production errors, resulting in overall cost savings.
- Innovation and Complexity Handling: The ability to create and manufacture complex geometries and innovative designs becomes feasible, allowing for the development of advanced products that would be difficult to produce using traditional methods.
Conclusion: The integration of CAD and CAM technologies is fundamental to modern manufacturing, enabling a seamless transition from design to production. This synergy enhances precision, reduces lead times, fosters collaboration, and increases overall efficiency and cost-effectiveness in the manufacturing process. By leveraging the combined capabilities of CAD and CAM, manufacturers can produce high-quality, complex products more rapidly and reliably, driving innovation and competitiveness in the industry.
7. What are the benefits and challenges of implementing Industry 4.0 technologies in manufacturing, and how can organizations overcome these challenges?
Answer:
Industry 4.0 refers to the fourth industrial revolution characterized by the integration of digital technologies into manufacturing processes. Implementing Industry 4.0 technologies offers numerous benefits but also presents significant challenges that organizations must navigate to achieve successful transformation.
Concepts:
- Industry 4.0 Technologies: Include the Internet of Things (IoT), artificial intelligence (AI), machine learning, big data analytics, robotics, additive manufacturing, cloud computing, and cyber-physical systems.
- Smart Manufacturing: Utilizing interconnected and intelligent systems to optimize production processes, enhance flexibility, and improve decision-making.
Benefits of Implementing Industry 4.0 Technologies:
- Increased Efficiency and Productivity: Automation, real-time monitoring, and data-driven decision-making streamline operations, reduce downtime, and enhance output.
- Enhanced Flexibility: Smart systems can quickly adapt to changes in demand, production requirements, and market conditions, enabling mass customization and agile manufacturing.
- Improved Quality: Advanced sensors and AI-driven analytics detect defects and optimize processes, ensuring higher product quality and consistency.
- Cost Reduction: Efficient resource utilization, predictive maintenance, and reduced waste lead to significant cost savings in production and operations.
- Data-Driven Insights: Big data analytics provide valuable insights into production performance, enabling continuous improvement and strategic planning.
- Enhanced Supply Chain Integration: Seamless communication and coordination across the supply chain improve transparency, reduce lead times, and enhance overall supply chain resilience.
- Sustainability: Optimized processes and resource management contribute to more sustainable manufacturing practices, reducing environmental impact.
Challenges of Implementing Industry 4.0 Technologies:
- High Initial Investment: The cost of acquiring and integrating advanced technologies can be substantial, posing financial barriers, especially for small and medium-sized enterprises (SMEs).
- Cybersecurity Risks: Increased connectivity and data exchange heighten the vulnerability of manufacturing systems to cyber-attacks and data breaches.
- Skill Gaps: The adoption of Industry 4.0 requires a workforce with specialized skills in digital technologies, data analytics, and system integration, which may be scarce.
- Integration Complexity: Integrating new digital technologies with existing legacy systems can be technically challenging and may disrupt ongoing operations.
- Data Management: Handling large volumes of data, ensuring data quality, and effectively analyzing data to derive actionable insights can be overwhelming.
- Change Management: Organizational resistance to change, lack of leadership commitment, and inadequate training can hinder the successful implementation of Industry 4.0 initiatives.
Overcoming the Challenges:
- Strategic Planning and Investment: Develop a clear roadmap for Industry 4.0 adoption, prioritizing technologies that offer the most significant benefits and aligning investments with long-term business goals.
- Enhancing Cybersecurity: Implement robust cybersecurity measures, including encryption, access controls, and regular security audits, to protect against cyber threats.
- Workforce Development: Invest in training and upskilling programs to equip employees with the necessary digital skills and foster a culture of continuous learning.
- Phased Implementation: Adopt a step-by-step approach to integrating Industry 4.0 technologies, starting with pilot projects to test and refine processes before full-scale deployment.
- Collaborative Partnerships: Partner with technology providers, research institutions, and other organizations to access expertise, share resources, and accelerate technology adoption.
- Effective Data Management: Utilize advanced data management systems and analytics tools to handle large datasets efficiently and extract meaningful insights.
- Leadership and Change Management: Secure strong leadership commitment, communicate the benefits of Industry 4.0 clearly to all stakeholders, and involve employees in the transformation process to reduce resistance and ensure buy-in.
Conclusion: Implementing Industry 4.0 technologies in manufacturing offers substantial benefits in terms of efficiency, flexibility, quality, and sustainability. However, organizations must address challenges related to investment costs, cybersecurity, skill gaps, integration complexity, data management, and change management to realize these benefits fully. By adopting strategic approaches, investing in workforce development, enhancing cybersecurity, and fostering a culture of innovation and collaboration, organizations can overcome these challenges and successfully integrate Industry 4.0 technologies into their manufacturing operations, driving competitive advantage and long-term growth.
8. How does sustainable manufacturing differ from traditional manufacturing, and what practices are essential for achieving sustainability in industrial operations?
Answer:
Sustainable manufacturing emphasizes minimizing environmental impact, conserving resources, and ensuring social responsibility throughout the production process, whereas traditional manufacturing primarily focuses on efficiency and cost-effectiveness without necessarily considering long-term environmental and social implications.
Concepts:
- Sustainable Manufacturing: An approach that integrates environmental, economic, and social considerations into manufacturing processes to create products in a manner that is environmentally responsible, economically viable, and socially equitable.
- Traditional Manufacturing: Focuses on maximizing production output and reducing costs, often prioritizing short-term gains over long-term sustainability.
Differences Between Sustainable and Traditional Manufacturing:
- Resource Efficiency: Sustainable manufacturing prioritizes the efficient use of materials, energy, and water, reducing waste and minimizing resource consumption. Traditional manufacturing may not prioritize resource conservation to the same extent.
- Environmental Impact: Sustainable practices aim to reduce emissions, pollution, and environmental degradation by implementing cleaner production methods and waste management strategies. Traditional manufacturing may result in higher environmental footprints due to less stringent environmental controls.
- Lifecycle Thinking: Sustainable manufacturing considers the entire lifecycle of a product, from design and production to disposal and recycling, ensuring sustainability at each stage. Traditional manufacturing often focuses on the production phase without extensive consideration of the product’s end-of-life impact.
- Social Responsibility: Sustainable manufacturing incorporates fair labor practices, community engagement, and ethical sourcing of materials, ensuring positive social outcomes. Traditional manufacturing may not adequately address social dimensions, potentially leading to labor issues and community conflicts.
- Innovation and Adaptability: Sustainable manufacturing encourages innovation in materials, processes, and technologies to enhance sustainability, whereas traditional manufacturing may resist changes that could disrupt established production efficiencies.
Essential Practices for Achieving Sustainability in Industrial Operations:
- Energy Efficiency: Implement energy-efficient technologies and practices, such as upgrading to energy-efficient machinery, optimizing production processes, and utilizing renewable energy sources.
- Waste Reduction and Recycling: Adopt waste minimization strategies, recycle materials, and implement circular economy principles to reduce the amount of waste generated and promote the reuse of resources.
- Sustainable Material Sourcing: Use eco-friendly and sustainably sourced materials, and prioritize the use of recycled or renewable resources to decrease the environmental impact of raw material extraction.
- Pollution Prevention: Implement measures to control and reduce emissions, effluents, and other pollutants through cleaner production techniques, advanced filtration systems, and proper waste treatment.
- Water Conservation: Optimize water usage in manufacturing processes, implement water recycling systems, and reduce water waste to conserve this vital resource.
- Lifecycle Assessment (LCA): Conduct LCAs to evaluate the environmental impact of products throughout their lifecycle, identifying areas for improvement and making informed decisions to enhance sustainability.
- Green Design: Incorporate eco-design principles that prioritize energy efficiency, material conservation, and ease of recycling during the product design phase.
- Employee Engagement and Training: Foster a culture of sustainability by educating and involving employees in sustainable practices, encouraging innovative ideas, and promoting environmental stewardship.
- Supply Chain Collaboration: Work with suppliers to ensure that sustainable practices are adopted throughout the supply chain, from raw material extraction to final product delivery.
- Compliance and Certification: Adhere to environmental regulations and pursue sustainability certifications, such as ISO 14001, to demonstrate commitment to sustainable manufacturing practices.
Conclusion: Sustainable manufacturing represents a transformative shift from traditional manufacturing by integrating environmental stewardship, resource efficiency, and social responsibility into industrial operations. By adopting essential sustainable practices, manufacturers can reduce their environmental footprint, enhance economic viability, and contribute positively to society. This holistic approach not only ensures long-term sustainability but also positions organizations as leaders in responsible and innovative manufacturing.
9. What are the primary considerations in designing a lean manufacturing system, and how do these considerations contribute to overall operational excellence?
Answer:
Designing a lean manufacturing system involves implementing strategies and practices that eliminate waste, optimize processes, and enhance value creation, thereby contributing to overall operational excellence.
Concepts:
- Lean Manufacturing: A production philosophy focused on minimizing waste and maximizing value through continuous improvement and efficient process management.
- Operational Excellence: Achieving superior performance in manufacturing operations by optimizing processes, enhancing quality, and fostering a culture of excellence.
Primary Considerations in Designing a Lean Manufacturing System:
Value Stream Mapping:
- Definition: A visual tool that outlines all the steps in the production process, identifying value-added and non-value-added activities.
- Contribution: Helps in identifying areas of waste and opportunities for process improvement, ensuring that every step contributes to customer value.
Just-In-Time (JIT) Production:
- Definition: Producing and delivering products only as they are needed in the production process, reducing inventory levels.
- Contribution: Minimizes inventory holding costs, reduces waste from overproduction, and enhances responsiveness to customer demand.
Continuous Improvement (Kaizen):
- Definition: An ongoing effort to improve products, services, and processes incrementally.
- Contribution: Fosters a culture of proactive problem-solving and innovation, leading to sustained operational enhancements and increased efficiency.
Standardized Work:
- Definition: Establishing consistent procedures and practices for performing tasks.
- Contribution: Ensures uniformity in operations, reduces variability, and simplifies training, leading to higher quality and reliability in production.
Waste Elimination (Muda):
- Definition: Identifying and removing non-value-added activities from the production process.
- Types of Waste: Overproduction, waiting, transportation, overprocessing, inventory, motion, and defects.
- Contribution: Streamlines operations, reduces costs, and improves overall efficiency by eliminating activities that do not add value.
Value-Added vs. Non-Value-Added Activities:
- Definition: Differentiating between activities that directly contribute to customer value and those that do not.
- Contribution: Prioritizes resource allocation towards value-added activities, enhancing product quality and customer satisfaction.
Pull Systems (Kanban):
- Definition: A production system where downstream processes signal the need for materials or products, initiating production accordingly.
- Contribution: Aligns production with actual demand, reducing excess inventory and ensuring timely delivery of products.
Flexible Workforce:
- Definition: Training employees to perform multiple tasks and adapt to changing production needs.
- Contribution: Increases workforce adaptability, reduces downtime, and enhances the ability to respond to fluctuations in demand.
5S Methodology:
- Definition: A workplace organization method comprising Sort, Set in order, Shine, Standardize, and Sustain.
- Contribution: Creates a clean, organized, and efficient work environment, improving productivity and reducing the risk of errors and accidents.
Total Quality Management (TQM):
- Definition: An organization-wide approach focused on continuous improvement, customer satisfaction, and quality enhancement.
- Contribution: Integrates quality into every aspect of the manufacturing process, ensuring that products meet or exceed customer expectations.
Contribution to Operational Excellence:
- Enhanced Efficiency: Streamlined processes and waste elimination lead to faster production times and lower operational costs.
- Improved Quality: Standardized work and continuous improvement practices ensure consistent product quality and reduced defect rates.
- Increased Flexibility: A flexible workforce and pull systems allow for quick adaptation to changes in demand and market conditions.
- Higher Employee Engagement: Involving employees in continuous improvement initiatives fosters a sense of ownership and motivation, contributing to a positive work culture.
- Customer Satisfaction: By focusing on value-added activities and quality enhancement, lean manufacturing ensures that customer needs are met effectively, leading to increased satisfaction and loyalty.
- Sustainable Growth: Operational efficiencies and cost savings enable organizations to invest in innovation and expansion, supporting long-term growth and competitiveness.
Conclusion: Designing a lean manufacturing system involves a comprehensive approach that focuses on waste elimination, process optimization, and continuous improvement. By addressing key considerations such as value stream mapping, JIT production, standardized work, and workforce flexibility, organizations can achieve operational excellence, enhancing efficiency, quality, and customer satisfaction. These practices not only improve current performance but also establish a foundation for sustainable and resilient manufacturing operations.
10. How can sustainable manufacturing practices reduce the environmental footprint of industrial operations, and what are some examples of these practices?
Answer:
Sustainable manufacturing practices aim to minimize the environmental footprint of industrial operations by reducing resource consumption, lowering emissions, and promoting the efficient use of materials. These practices contribute to environmental preservation, cost savings, and compliance with regulatory standards.
Concepts:
- Sustainable Manufacturing: The creation of products using processes that minimize negative environmental impacts, conserve energy and natural resources, and are safe for workers and communities.
- Environmental Footprint: The total impact of industrial operations on the environment, including resource use, waste generation, and emissions.
How Sustainable Manufacturing Practices Reduce Environmental Footprint:
Resource Efficiency:
- Energy Conservation: Implementing energy-efficient technologies and optimizing production processes to reduce energy consumption.
- Water Conservation: Using water-saving techniques and recycling water within the manufacturing process to minimize water usage.
Waste Minimization:
- Lean Manufacturing: Reducing waste through process optimization and elimination of non-value-added activities.
- Circular Economy: Designing products for reuse, recycling, and remanufacturing to extend their lifecycle and reduce material waste.
Emission Reduction:
- Pollution Control: Installing advanced filtration and scrubbing systems to capture and reduce air and water pollutants.
- Carbon Footprint Reduction: Adopting renewable energy sources and improving energy efficiency to lower greenhouse gas emissions.
Sustainable Material Sourcing:
- Eco-Friendly Materials: Using renewable, recyclable, or biodegradable materials to reduce environmental impact.
- Responsible Procurement: Selecting suppliers that adhere to sustainable practices and provide environmentally certified materials.
Eco-Design:
- Product Lifecycle Management: Designing products with their entire lifecycle in mind, ensuring ease of disassembly, recycling, and minimal environmental impact.
- Modular Design: Creating products with interchangeable parts to facilitate repairs, upgrades, and recycling.
Green Manufacturing Technologies:
- Additive Manufacturing: Utilizing 3D printing to produce components with less material waste compared to traditional subtractive methods.
- Advanced Manufacturing Processes: Implementing technologies like laser cutting and precision machining to enhance efficiency and reduce waste.
Supply Chain Sustainability:
- Logistics Optimization: Streamlining transportation and distribution to reduce fuel consumption and emissions.
- Supplier Collaboration: Working with suppliers to ensure sustainable practices throughout the supply chain, from raw material extraction to product delivery.
Examples of Sustainable Manufacturing Practices:
- Energy-Efficient Lighting and Machinery: Installing LED lighting and energy-efficient motors to reduce electricity consumption in manufacturing facilities.
- Waste Heat Recovery Systems: Capturing and reusing waste heat from industrial processes to generate additional energy or for heating purposes.
- Solar Power Integration: Incorporating solar panels into manufacturing plants to supply renewable energy and decrease reliance on fossil fuels.
- Closed-Loop Water Systems: Recycling and reusing water within the manufacturing process to minimize freshwater consumption and reduce wastewater discharge.
- Biodegradable Packaging: Using biodegradable or recyclable packaging materials to reduce environmental impact and enhance product sustainability.
- Eco-Friendly Paints and Coatings: Utilizing low-VOC (volatile organic compounds) paints and coatings to decrease air pollution and improve indoor air quality.
- Green Roofs and Vegetation: Implementing green roofs and planting vegetation around manufacturing facilities to absorb rainwater, provide insulation, and enhance biodiversity.
Conclusion: Sustainable manufacturing practices are essential for reducing the environmental footprint of industrial operations. By focusing on resource efficiency, waste minimization, emission reduction, sustainable material sourcing, and eco-design, manufacturers can significantly lower their impact on the environment. Implementing these practices not only contributes to environmental preservation but also offers economic benefits through cost savings, improved efficiency, and enhanced corporate reputation. Embracing sustainability in manufacturing is a strategic imperative that supports long-term business viability and environmental stewardship.
11. What are the critical factors in designing a flexible manufacturing system, and how do these factors enhance production adaptability and efficiency?
Answer:
Designing a flexible manufacturing system (FMS) involves creating a production environment that can adapt quickly and efficiently to changes in product design, production volume, and market demand. Critical factors in designing an FMS include modularity, automation, information systems, workforce versatility, and scalable infrastructure.
Concepts:
- Flexible Manufacturing System (FMS): An integrated system of machines, robots, and computer-controlled tools capable of producing a variety of products with minimal changeover time.
- Production Adaptability: The ability of a manufacturing system to adjust to changes in product types, volumes, and production processes.
- Operational Efficiency: Maximizing productivity and minimizing waste through optimized processes and resource utilization.
Critical Factors in Designing an FMS:
Modularity:
- Definition: Designing production units and equipment that can be easily reconfigured or replaced to accommodate different products.
- Enhancement: Modularity allows for quick adjustments to production lines, enabling manufacturers to switch between products with minimal downtime and cost.
Automation and Robotics:
- Definition: Incorporating automated machinery and robots to perform repetitive, precise, and complex tasks.
- Enhancement: Automation increases production speed, consistency, and accuracy while reducing labor costs and minimizing human error, enhancing overall efficiency.
Advanced Information Systems:
- Definition: Utilizing integrated software systems like Manufacturing Execution Systems (MES) and Enterprise Resource Planning (ERP) to manage production data and operations.
- Enhancement: These systems provide real-time visibility into production processes, enabling better decision-making, coordination, and responsiveness to changes.
Versatile Workforce:
- Definition: Training employees to perform multiple roles and tasks within the manufacturing system.
- Enhancement: A versatile workforce can quickly adapt to different production needs, reducing reliance on specialized labor and enhancing flexibility.
Scalable Infrastructure:
- Definition: Designing manufacturing facilities with the capacity to expand or contract based on production requirements.
- Enhancement: Scalable infrastructure supports growth and allows for adjustments in production volume without significant overhauls, maintaining operational efficiency.
Standardization and Interchangeability:
- Definition: Creating standardized processes and interchangeable parts that can be used across different products.
- Enhancement: Standardization reduces setup times, simplifies maintenance, and ensures consistency in production, facilitating easier adaptation to new products.
Flexible Supply Chain:
- Definition: Developing a supply chain that can respond swiftly to changes in production demands and product variations.
- Enhancement: A flexible supply chain ensures the timely availability of materials and components, supporting the adaptability and efficiency of the manufacturing system.
Quality Control Integration:
- Definition: Embedding quality control measures within the manufacturing process to ensure product consistency and reliability.
- Enhancement: Integrated quality control minimizes defects, reduces rework, and maintains high product standards even when production processes are frequently adjusted.
Enhancements to Production Adaptability and Efficiency:
- Quick Changeovers: Modular and automated systems enable rapid switchovers between different products, reducing downtime and increasing production flexibility.
- Responsive Production: Advanced information systems and a versatile workforce allow for real-time adjustments to production schedules based on market demand and supply chain dynamics.
- Cost Efficiency: Automation and standardization lower operational costs by increasing production speed, reducing waste, and minimizing the need for specialized labor.
- Improved Product Quality: Consistent processes and integrated quality control ensure that product quality remains high, regardless of production changes.
- Scalability: Scalable infrastructure allows manufacturers to adjust production capacity in response to market fluctuations, maintaining efficiency and meeting customer demands effectively.
Conclusion: Designing a flexible manufacturing system involves considering factors such as modularity, automation, advanced information systems, versatile workforce, and scalable infrastructure. These factors collectively enhance production adaptability and efficiency by enabling quick adjustments to changing production needs, optimizing resource utilization, and maintaining high product quality. A well-designed FMS supports operational excellence, reduces costs, and provides a competitive advantage in dynamic and evolving markets.
12. How can predictive maintenance technologies transform maintenance strategies in manufacturing, and what are the benefits of adopting such technologies?
Answer:
Predictive maintenance technologies leverage data analytics, sensors, and machine learning to anticipate equipment failures before they occur, transforming traditional maintenance strategies from reactive and preventive approaches to a more proactive and condition-based model.
Concepts:
- Predictive Maintenance: A maintenance strategy that uses data-driven insights to predict when equipment maintenance should be performed, minimizing downtime and extending asset lifespan.
- Condition-Based Maintenance: Maintenance activities are triggered by real-time monitoring of equipment conditions rather than on a fixed schedule.
Transformation of Maintenance Strategies:
Data Collection and Monitoring:
- Implementation: Installing sensors and IoT devices on machinery to continuously monitor parameters such as temperature, vibration, pressure, and performance metrics.
- Transformation: Provides real-time data on equipment health, enabling continuous assessment and early detection of anomalies.
Data Analysis and Machine Learning:
- Implementation: Utilizing advanced analytics and machine learning algorithms to process collected data, identifying patterns and predicting potential failures.
- Transformation: Transforms raw data into actionable insights, allowing maintenance teams to prioritize and address issues proactively.
Automation and Integration:
- Implementation: Integrating predictive maintenance systems with existing Enterprise Resource Planning (ERP) and Manufacturing Execution Systems (MES) to streamline maintenance workflows.
- Transformation: Automates maintenance scheduling and resource allocation based on predictive insights, enhancing efficiency and coordination.
Decision Support:
- Implementation: Providing maintenance teams with dashboards and alerts that highlight equipment needing attention based on predictive analytics.
- Transformation: Enhances decision-making by prioritizing maintenance activities based on the likelihood and severity of potential failures.
Benefits of Adopting Predictive Maintenance Technologies:
- Reduced Downtime:
- Benefit: By anticipating equipment failures, maintenance can be scheduled during planned downtime, minimizing unexpected interruptions in production.
- Cost Savings:
- Benefit: Predictive maintenance reduces the costs associated with emergency repairs, extends the lifespan of machinery, and lowers the frequency of maintenance activities by addressing issues only when necessary.
- Improved Equipment Performance:
- Benefit: Regular monitoring and timely maintenance ensure that equipment operates at optimal performance levels, enhancing overall production efficiency and product quality.
- Enhanced Safety:
- Benefit: Predictive maintenance helps identify and mitigate potential safety hazards related to equipment malfunctions, protecting workers and reducing the risk of accidents.
- Resource Optimization:
- Benefit: Maintenance resources, including labor and spare parts, are allocated more efficiently based on actual equipment needs, avoiding over-maintenance and reducing inventory costs.
- Data-Driven Insights:
- Benefit: Continuous data collection and analysis provide valuable insights into equipment performance trends, informing future investments in machinery and maintenance practices.
- Sustainability:
- Benefit: Efficient maintenance practices reduce energy consumption and material waste associated with equipment inefficiencies and breakdowns, contributing to more sustainable manufacturing operations.
- Scalability:
- Benefit: Predictive maintenance systems can be scaled across multiple machines and facilities, providing consistent maintenance standards and performance improvements throughout the organization.
Conclusion: Predictive maintenance technologies significantly transform maintenance strategies in manufacturing by enabling a proactive, data-driven approach to equipment management. The adoption of these technologies leads to reduced downtime, cost savings, improved equipment performance, enhanced safety, and optimized resource utilization. By leveraging predictive maintenance, manufacturers can achieve greater operational efficiency, extend the lifespan of their assets, and maintain high standards of product quality and workplace safety, thereby gaining a competitive edge in the industry.
Conclusion: The above questions and detailed answers provide a comprehensive exploration of industrial and manufacturing technologies. Covering essential topics such as additive vs. subtractive manufacturing, automation and robotics, lean manufacturing principles, quality control vs. quality assurance, supply chain management, CAD/CAM integration, Industry 4.0, sustainable manufacturing, flexible manufacturing systems, predictive maintenance, and more, these inquiries encourage students to critically analyze and engage with the complexities of modern manufacturing practices. By delving into these areas, students are equipped with the knowledge and critical thinking skills necessary to excel in the field of industrial and manufacturing technologies, promoting innovation, efficiency, and sustainability in production environments. These questions foster a deeper understanding of how advanced technologies and strategic management practices can be integrated to achieve operational excellence and competitive advantage, making learning an engaging and dynamic process.