Chemical Materials Engineering
Chemical Materials Engineering lies at the core of innovation in product development, manufacturing, and sustainability. It builds upon the broad foundations of Chemical Engineering and focuses on the properties, processing, and performance of materials used in industries ranging from aerospace to biomedicine. Insights from Biochemical Engineering also influence material design in biocompatible scaffolds and biosensors.
Central to many chemical processes is the need for materials that facilitate or withstand reactions, making Chemical Catalysis and Reaction Engineering a key area of overlap. Similarly, in applications like energy storage and conversion, engineers often collaborate with those in Chemical Energy Systems Engineering to develop advanced electrode and fuel cell materials. The integration of these materials within entire systems also benefits from the systems-level insight of Chemical Process Engineering.
Modern tools from Computational Chemical Engineering are increasingly used to simulate and optimize materials at molecular and mesoscopic scales. These capabilities are critical in industries like Food and Beverage Engineering, where material surfaces and packaging interact with product quality. New frontiers are opened with Nanotechnology in Chemical Engineering, where nanoparticles and nanostructures offer novel functionalities and reactivities.
The development of specialized polymers, coatings, and composites is directly addressed within Polymer and Plastics Engineering. These materials are also vital in civil infrastructure, where durability and strength must be engineered carefully, as seen in Civil Engineering. Collaborations with Construction Management ensure practical deployment and cost efficiency.
For materials used in disaster-prone regions, engineers rely on knowledge from Earthquake and Disaster Engineering and Geotechnical Engineering to ensure performance under extreme loads. Frameworks and reinforcements are often designed using principles from Structural Engineering, while transportation systems benefit from material choices analyzed within Transportation Engineering and Urban and Regional Planning.
Water treatment membranes and filtration materials find their application in Water Resources Engineering. In electronics and power sectors, conductive polymers, dielectrics, and semiconductors are explored in Electrical and Electronic Engineering and its subfields such as Biomedical Electronics and Communication Engineering.
Advanced control of production and testing environments is made possible through Control Systems Engineering. Microfabrication techniques and integrated materials are topics of focus in Electronics Engineering and Embedded Systems and Microelectronics. To ensure real-time quality assurance and process compliance, tools from Instrumentation and Measurement are essential across all stages of Chemical Materials Engineering.
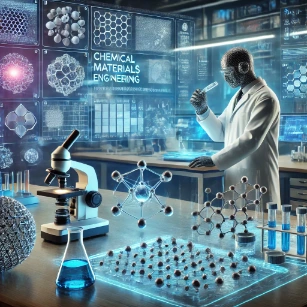
Table of Contents
Core Concepts in Chemical Materials Engineering
Materials Synthesis and Processing
- Definition:
The design and production of materials with specific chemical compositions and structures to achieve desired properties. - Techniques:
- Polymerization: Chemical synthesis of polymers with controlled molecular weight and structure.
- Sol-Gel Processing: Creation of ceramics and glass materials from chemical precursors.
- Powder Metallurgy: Fabrication of metal parts from powdered materials.
- Additive Manufacturing (3D Printing): Layer-by-layer fabrication of complex material structures.
Structure-Property Relationships
- Definition:
Understanding how the internal structure of materials (atomic, molecular, or crystalline) influences their physical and chemical properties. - Examples:
- Nanostructured materials offer higher strength-to-weight ratios.
- Composite materials exhibit superior mechanical performance due to synergistic effects between components.
Materials Characterization
- Definition:
Analyzing material properties to ensure quality, performance, and reliability. - Techniques:
- X-Ray Diffraction (XRD): Identifies crystal structures.
- Scanning Electron Microscopy (SEM): Examines material surfaces and microstructures.
- Spectroscopy (FTIR, Raman): Analyzes chemical bonds and molecular structures.
- Mechanical Testing: Measures hardness, tensile strength, and elasticity.
Materials Performance and Degradation
- Definition:
Studying how materials behave under various environmental and operational conditions. - Factors Affecting Performance:
- Mechanical stress and fatigue.
- Thermal cycling and oxidation.
- Chemical corrosion and wear.
Sustainable and Green Materials
- Definition:
Developing environmentally friendly materials and production methods to reduce ecological impact. - Strategies:
- Biodegradable Polymers: Materials that decompose naturally.
- Recyclable Composites: Designed for easy disassembly and reuse.
- Green Synthesis Processes: Minimizing hazardous chemicals and waste.
Key Classes of Materials in Chemical Materials Engineering
Polymers
- Definition:
Long-chain molecules composed of repeating monomer units, offering versatility in design and application. - Types of Polymers:
- Thermoplastics: Can be melted and reshaped (e.g., polyethylene, polystyrene).
- Thermosetting Plastics: Harden permanently after curing (e.g., epoxy, phenolic resins).
- Elastomers: Highly elastic materials (e.g., rubber, silicone).
- Applications:
- Packaging materials, medical devices, automotive parts, and textiles.
Composite Materials
- Definition:
Materials made by combining two or more distinct substances to achieve enhanced properties. - Types of Composites:
- Fiber-Reinforced Composites: Carbon fiber or glass fiber in polymer matrices.
- Metal Matrix Composites (MMC): Metals reinforced with ceramics or fibers.
- Ceramic Matrix Composites (CMC): Ceramics reinforced with fibers for high-temperature applications.
- Applications:
- Aerospace structures, automotive components, and sports equipment.
Nanomaterials
- Definition:
Materials engineered at the nanoscale (1–100 nm) to exploit unique physical and chemical properties. - Types of Nanomaterials:
- Carbon Nanotubes (CNTs): High strength and electrical conductivity.
- Quantum Dots: Semiconductor nanoparticles used in displays and imaging.
- Nanocomposites: Enhanced mechanical and barrier properties.
- Applications:
- Electronics, drug delivery, energy storage, and coatings.
Metals and Alloys
- Definition:
Metallic materials engineered for strength, durability, and thermal/electrical conductivity. - Common Alloys:
- Steel: Iron-carbon alloy for construction and manufacturing.
- Aluminum Alloys: Lightweight materials for aerospace and automotive industries.
- Titanium Alloys: High strength-to-weight ratio and corrosion resistance for medical implants and aerospace.
Ceramics and Glasses
- Definition:
Inorganic, non-metallic materials known for their hardness, heat resistance, and electrical insulation. - Types of Ceramics:
- Structural Ceramics: Used in aerospace and defense.
- Bio-Ceramics: Used in dental and orthopedic implants.
- Applications:
- Engine components, biomedical implants, and electronics.
Applications of Chemical Materials Engineering
Construction and Infrastructure
Chemical materials engineering plays a transformative role in the modern built environment. Advanced building materials such as fiber-reinforced composites, ultra-high-performance concrete, and corrosion-resistant coatings have revolutionized how we design and maintain infrastructure. These innovations offer superior strength-to-weight ratios, extended durability, and improved resistance to extreme environmental conditions.
In the pursuit of sustainable construction, chemical engineers have developed energy-efficient insulation systems using aerogels and phase-change materials, which not only enhance indoor thermal comfort but also significantly lower heating and cooling energy demands. Moreover, engineered self-healing materials are now being used to automatically seal cracks in concrete, reducing maintenance needs and increasing structural longevity.
Electronics and Semiconductors
In the ever-evolving electronics sector, chemical materials engineering contributes to the fabrication of next-generation devices through innovations in conductive polymers, dielectric materials, and thermal interface solutions. These materials enhance the performance of transistors, integrated circuits, and other microelectronic components while reducing energy consumption and improving heat dissipation.
The rise of flexible and wearable technologies has led to the development of stretchable electronics using polymer composites and organic semiconductors. These materials enable the creation of devices that conform to human skin, opening doors to medical wearables, electronic textiles, and smart sensors. Researchers are also leveraging nanomaterials and 2D structures like graphene to push the boundaries of miniaturization and speed in microelectronics.
Aerospace and Automotive Industries
For aerospace and automotive engineers, chemical materials engineering is essential to the development of lighter, safer, and more efficient vehicles. Carbon fiber composites, aluminum-lithium alloys, and advanced polymers are used to reduce weight without compromising strength, thereby improving fuel efficiency and reducing emissions.
Thermal protection systems are another critical area, especially in aerospace, where vehicles must withstand intense heat during high-speed travel or re-entry. Ceramics and ablative materials offer the thermal stability needed for engine components and heat shields. In motorsports and electric vehicles, engineers are incorporating phase-change materials to manage thermal loads and enhance performance.
Medical Devices and Healthcare
In medicine, the integration of chemical materials engineering with biology has given rise to cutting-edge solutions in diagnostics, therapeutics, and prosthetics. Titanium alloys, ceramics, and biocompatible polymers are widely used in implants, artificial joints, and bone scaffolds. These materials are engineered to resist corrosion, minimize inflammation, and promote tissue integration.
Smart materials such as shape-memory alloys and magneto-responsive hydrogels enable dynamic functions in medical devices—ranging from self-adjusting stents to controlled drug delivery systems. Such innovations are expanding the frontier of minimally invasive surgery, tissue regeneration, and patient-centered healthcare.
Energy Storage and Conversion
The shift toward renewable energy systems is heavily reliant on innovations in materials for energy conversion and storage. Battery materials have evolved rapidly, with engineers developing solid-state electrolytes, lithium-sulfur chemistries, and silicon anodes to increase energy density, safety, and cycle life.
In fuel cells, the design of high-performance membranes and electrocatalysts has enabled more efficient electrochemical conversion processes. The use of proton exchange membranes (PEMs) and platinum-free catalysts is making hydrogen fuel cells more viable and cost-effective. Additionally, chemical materials engineering supports breakthroughs in solar photovoltaic materials, including perovskites, which promise high efficiency and low manufacturing costs.
For example, recent advancements in hydrogen storage systems, as seen in this hydrogen storage study, are being implemented in smart grids and fuel cell vehicles. These technologies are vital for reducing carbon emissions and supporting the global transition to clean energy.
Emerging Technologies in Chemical Materials Engineering
3D Printing of Functional Materials
Three-dimensional printing, also known as additive manufacturing, is reshaping the landscape of chemical materials engineering by enabling the creation of complex, custom-designed structures with high precision. 3D printing of functional materials allows for the layer-by-layer deposition of polymers, metals, ceramics, and composites to produce everything from biomedical implants to aerospace parts.
One major area of innovation involves the printing of bioinks—hydrogels embedded with living cells—which can be used to fabricate tissues for regenerative medicine. Engineers are also developing composite materials with enhanced thermal, electrical, or mechanical properties for advanced electronics, wearable technologies, and even space applications.
Additionally, 3D printing enables rapid prototyping, reducing design iteration cycles in research and product development. In sectors such as dentistry, orthopedics, and microfluidics, custom solutions can now be delivered with unprecedented speed and personalization. Research is also advancing toward multi-material and hybrid 3D printing, which combines different substances in a single print job to mimic natural gradients or interfaces within materials.
Smart and Responsive Materials
Smart materials are engineered to sense and react to their environment, offering dynamic responses such as shape change, color shift, or conductivity adjustment. These materials respond to external stimuli like temperature, pH, light, pressure, or magnetic fields, making them valuable in diverse applications ranging from aerospace to biomedical engineering.
Examples include shape-memory alloys used in stents and actuators, hydrogels for pH-responsive drug delivery, and piezoelectric materials that generate electricity from mechanical deformation. Self-healing coatings that repair microcracks autonomously extend the life of industrial components and infrastructure.
Smart textiles are also emerging, integrating responsive polymers into fabrics that change properties in real time—ideal for health monitoring or adaptive climate control. When embedded with electronic sensors, these materials contribute to the growing field of soft robotics and wearable diagnostics.
Sustainable and Green Materials
With rising global awareness of climate change and environmental degradation, chemical materials engineers are developing materials that support a circular and low-carbon economy. Sustainable and green materials include bioplastics made from agricultural waste, composites reinforced with natural fibers, and products designed for end-of-life recyclability.
Green chemistry methods enable the synthesis of materials with minimal use of toxic solvents or by-products. Moreover, advances in process intensification and solvent-free manufacturing are reducing the environmental footprint of production.
High-performance building materials such as hempcrete and low-carbon concrete are gaining traction for eco-friendly construction. Meanwhile, degradable packaging materials are replacing traditional plastics in consumer goods, helping reduce microplastic pollution in oceans and soil ecosystems.
Advanced Nanomaterials
Nanomaterials are engineered at the scale of atoms and molecules, typically less than 100 nanometers in size, and they exhibit extraordinary properties due to their high surface area, quantum effects, and tunable structure. Advanced nanomaterials are used in applications ranging from clean energy production to advanced drug delivery.
In catalysis, nanostructured materials enhance surface reactivity and selectivity, increasing efficiency in processes like water splitting and CO₂ reduction. In medicine, nanoparticles can be designed to target specific cells, enabling precision treatment in cancer and inflammatory diseases.
Engineers are also applying nanotechnology in coatings for antimicrobial resistance, UV protection, and thermal insulation. Innovations in 2D materials like graphene are leading to breakthroughs in flexible electronics, next-generation batteries, and advanced sensors. Nanomaterials are even being explored for environmental cleanup—such as magnetic nanoparticles that remove heavy metals or oil spills from water.
As interdisciplinary research advances, combining machine learning with nanomaterials discovery is streamlining the development of new materials with customized properties for niche applications. Ongoing exploration of these emerging technologies is essential for solving some of the world’s most urgent challenges.
Challenges in Chemical Materials Engineering
Sustainability and Environmental Impact:
One of the most urgent challenges in chemical materials engineering is addressing the environmental consequences of material production and disposal. As industries scale up, emissions, toxic byproducts, and non-degradable waste can accumulate, posing long-term risks to ecosystems and public health. Engineers are increasingly expected to integrate environmental science principles into every stage of materials design to reduce greenhouse gas emissions and water consumption.
Developing closed-loop systems where materials can be reused or biodegraded without harming the environment is essential for sustainability. Innovations in green chemistry, such as solvent-free synthesis and benign catalysts, are gaining traction. In addition, eco-labeling and life cycle assessment tools help manufacturers and consumers evaluate the environmental burden of materials across their entire life cycle—from raw material extraction to end-of-life disposal or recycling.
Public demand for sustainable products is also reshaping markets. Governments and international organizations are imposing stricter regulations and sustainability standards, urging the materials industry to transition to cleaner technologies. As a result, sustainability is no longer a peripheral concern but a central engineering constraint that must be addressed alongside mechanical and economic requirements.
Scalability of Advanced Materials:
Although many high-performance materials are being discovered in laboratory settings, translating these findings into scalable industrial applications remains a significant hurdle. The path from research prototype to commercial product often involves overcoming issues such as production complexity, process control, consistency, and supply chain integration.
Advanced materials like carbon nanotubes, graphene, and self-healing polymers show exceptional properties in small-scale tests but are difficult to produce cost-effectively at larger volumes. Engineers must redesign synthesis protocols and processing techniques to accommodate bulk production while maintaining the desired performance characteristics.
Scaling challenges also involve interdisciplinary collaboration. Chemical engineers must work with automation experts, quality control specialists, and business strategists to streamline production lines. In recent years, digital twin technology and AI-driven optimization have emerged as promising tools for simulating large-scale operations before physical scaling takes place.
Material Cost and Resource Availability:
Developing high-performance materials often requires rare elements or complex manufacturing techniques, driving up the cost and limiting accessibility. For instance, elements like cobalt, used in batteries, or indium, used in transparent electronics, are geographically limited and subject to price volatility due to geopolitical tensions.
To reduce dependency on rare and expensive resources, researchers are exploring abundant alternatives, such as replacing platinum catalysts with transition metals or substituting synthetic polymers with bio-based resins. However, maintaining comparable performance while ensuring long-term stability and recyclability is a delicate balancing act.
The growing emphasis on circular economy strategies also demands innovation in resource efficiency. Engineers are designing materials with second-life applications in mind, using modular construction, standardized formats, and minimal material variety to simplify disassembly and reuse. Exploring ways to recover critical materials from e-waste is a parallel effort with increasing relevance.
Several organizations now support open-access databases and global tracking systems for material flows, allowing industries to forecast shortages and coordinate sustainable sourcing strategies. For instance, platforms such as the Chatham House Resource Trade Database help policymakers and engineers make informed decisions about supply chains and material economics.
Durability and Lifecycle Management:
High durability is a key goal in many material applications, from aerospace to infrastructure, but it often conflicts with recyclability and sustainability. The engineering challenge lies in developing materials that perform well under stress, corrosion, and fatigue, while still being easy to reprocess at the end of their useful life.
For example, aerospace composites are designed to endure extreme conditions but are notoriously difficult to recycle. Likewise, multi-layer packaging films used for food preservation are often non-recyclable because of their complex structure. Innovations in depolymerization, reversible crosslinking, and single-polymer designs are helping to overcome these problems.
In response, engineers are incorporating design-for-disassembly principles, enabling more efficient material recovery. Techniques such as molecular tagging, smart labeling, and thermal-triggered separation are being explored to enhance end-of-life management of advanced materials.
Furthermore, the adoption of digital product passports, as promoted by initiatives like the European Circular Economy Action Plan, allows detailed tracking of materials through their entire lifespan, facilitating better recycling and re-use decisions across industries.
Future Directions in Chemical Materials Engineering
Circular Economy Integration:
The integration of circular economy principles into chemical materials engineering is rapidly transforming how materials are designed, manufactured, and recovered. Rather than following a linear model of make-use-dispose, the circular approach emphasizes a continuous lifecycle, where materials are conceived from the start for disassembly, reuse, and regeneration. Engineers are developing modular components, reversible adhesives, and mono-material structures that simplify recycling while maintaining high performance standards.
Innovations such as closed-loop polymers and upcyclable composites are enabling industries to minimize raw material extraction and reduce landfill waste. Smart labeling technologies are also emerging, helping to track material origin and composition to support intelligent recovery. As sustainability regulations tighten worldwide, frameworks like Ellen MacArthur Foundation’s Circular Economy model are becoming blueprints for future materials development.
Bioinspired and Biomimetic Materials:
Looking to nature for inspiration, engineers are increasingly exploring biomimicry to design high-performance materials that are both sustainable and adaptive. By studying structures like the lightweight strength of a bird’s bone, the water-repellent surface of lotus leaves, or the energy-absorbing properties of spider silk, researchers can create materials that outperform synthetic alternatives while reducing environmental impact.
Applications include self-healing coatings, responsive textiles, and eco-friendly composites. Biomimetic designs are also being applied to smart surfaces that alter their structure in response to stimuli such as heat or light. In the medical field, these principles are giving rise to scaffolds for tissue regeneration that mimic the extracellular matrix of human tissues, enhancing compatibility and healing outcomes.
Multi-Functional Materials:
The demand for materials that serve multiple purposes simultaneously is driving the next wave of material innovation. Instead of assembling separate components for mechanical strength, electrical conductivity, and thermal regulation, engineers are creating integrated materials that unify these properties within a single structure. Examples include graphene composites that offer strength, electrical performance, and flexibility in wearable electronics.
Multi-functional materials are critical in aerospace, where reducing weight and component count can dramatically improve performance. In consumer electronics, they allow for thinner, more durable, and energy-efficient devices. Advanced metamaterials are also gaining momentum, exhibiting properties not found in nature—such as negative refractive indices or tunable acoustic insulation—unlocking new potential in optics and thermal regulation.
Artificial Intelligence (AI) in Material Discovery:
The incorporation of AI into material science is revolutionizing how new substances are discovered and optimized. Machine learning algorithms can now analyze vast datasets of molecular structures and performance metrics to predict promising material candidates with unprecedented speed and accuracy. This accelerates the research timeline from years to months or even weeks.
Tools such as materials informatics platforms and neural networks are allowing engineers to fine-tune compositions for properties like tensile strength, corrosion resistance, or thermal stability. AI is also being applied to simulate how materials behave under extreme conditions, guiding the design of next-generation materials for aerospace, energy storage, and medicine.
For example, the Materials Project provides open-access computational data for predicting material behavior, significantly lowering entry barriers for research institutions and startups alike. As AI continues to mature, it is expected to work synergistically with high-throughput experimentation, robotics, and 3D printing to usher in a new era of rapid, intelligent materials innovation.
Why Study Chemical Materials Engineering
Understanding Material Behavior and Composition
Chemical materials engineering focuses on the relationship between material structure and performance. Students learn how atomic and molecular arrangements influence strength, conductivity, and reactivity. This understanding guides the development of new and improved materials.
Designing Functional Materials
Students explore how to engineer materials for specific applications, such as batteries, catalysts, and coatings. They study polymers, ceramics, composites, and nanomaterials. These skills are crucial for innovation in energy, electronics, and medicine.
Characterization and Testing Techniques
The course teaches students how to analyze material properties using spectroscopy, microscopy, and mechanical testing. These techniques ensure materials meet performance and safety standards. Proficiency in testing supports research and product development.
Applications in Advanced Manufacturing
Chemical materials engineering is central to additive manufacturing, semiconductor fabrication, and surface engineering. Students contribute to high-tech industries by designing materials tailored to specific processing techniques. This expands opportunities in cutting-edge fields.
Impact on Sustainability and Innovation
Materials engineers help reduce waste, improve recyclability, and develop eco-friendly alternatives. Students play a role in creating sustainable solutions for modern challenges. Their work drives innovation and supports global sustainability goals.
Chemical Materials Engineering: Conclusion
Chemical Materials Engineering stands at the forefront of innovation, acting as the backbone of modern technological advancements across countless industries. By blending principles from chemistry, physics, and engineering, professionals in this field design and produce materials that are lighter, stronger, more durable, and environmentally responsible. Their contributions are critical in transforming visionary concepts into real-world applications—whether it’s developing ultra-lightweight carbon composites for aerospace components, or engineering self-healing polymers that can extend the life of infrastructure and reduce maintenance costs.
One of the most transformative impacts of chemical materials engineering lies in the medical sector. Biocompatible implants—crafted using specialized polymers and metallic alloys—are enabling longer-lasting prosthetics and safer surgical tools. In fact, technologies like adaptive biomedical materials are now being used to mimic biological tissue behaviors, offering patients faster recovery and improved integration of medical implants. These developments are not only improving quality of life, but are also revolutionizing regenerative medicine and personalized care.
At the same time, materials engineers are pushing the boundaries of sustainability. From creating fully recyclable packaging solutions and biodegradable plastics to designing membranes that filter pollutants from industrial wastewater, chemical materials engineering is leading the way toward greener production practices. Innovations in battery technology, including solid-state electrolytes and high-capacity anodes, are being explored to support the global shift toward electrified transport and renewable energy storage. According to insights from the U.S. Department of Energy, such advanced materials are instrumental in increasing energy efficiency while minimizing environmental impact.
Looking ahead, the convergence of nanotechnology, artificial intelligence, and materials genomics is expected to further accelerate breakthroughs. By using AI-driven simulations and machine learning algorithms, researchers can now model material behaviors under extreme conditions before even producing physical samples. This predictive capability not only shortens development cycles but also reduces costs and experimental waste. Future innovations may include self-cleaning building materials, programmable matter, and next-generation semiconductors capable of powering ultra-fast computing systems.
In conclusion, Chemical Materials Engineering is more than a technical discipline—it’s a vital enabler of progress in health, sustainability, energy, and technology. As the world grapples with climate change, resource limitations, and the growing demand for high-performance systems, this field will remain at the heart of material solutions that are not just functional, but also responsible. By fostering collaboration across science, industry, and policy, chemical materials engineers are poised to deliver resilient, intelligent, and sustainable materials that will define the fabric of future society.
Chemical Materials Engineering: Review Questions and Answers:
What is chemical materials engineering, and how does it differ from traditional chemical engineering?
Answer: Chemical materials engineering focuses on the design, synthesis, and application of materials with specific properties and functions. While traditional chemical engineering emphasizes large-scale chemical production and process optimization, chemical materials engineering delves into understanding material structures at the molecular or atomic level to develop new materials with tailored characteristics for specific applications.
What are the primary classes of materials studied in chemical materials engineering?
Answer: The primary classes of materials include:
Metals: Characterized by high electrical and thermal conductivity, malleability, and ductility; used in construction, transportation, and electronics.
Polymers: Composed of long chains of repeating units; versatile with applications in packaging, textiles, and biomedical devices.
Ceramics: Inorganic, non-metallic materials known for their hardness, brittleness, and heat resistance; used in aerospace, electronics, and medical implants.
Composites: Materials made by combining two or more different materials to achieve properties superior to the individual components; used in automotive, aerospace, and sports equipment.
How does the structure of a material at the atomic or molecular level influence its macroscopic properties?
Answer: The arrangement of atoms or molecules within a material determines its macroscopic properties. For example, the crystalline structure of metals allows for dislocation movement, contributing to their ductility. In polymers, the degree of polymerization and cross-linking affects their elasticity and tensile strength. Understanding these relationships enables engineers to manipulate structures to achieve desired properties.
What role does thermodynamics play in the development of new materials?
Answer: Thermodynamics helps predict the stability of materials and the feasibility of chemical reactions during material synthesis. By analyzing Gibbs free energy changes, engineers can determine the conditions under which a material will form or transform, guiding the design of processes for creating new materials with desired properties.
How are nanomaterials different from their bulk counterparts, and what unique applications do they offer?
Answer: Nanomaterials have dimensions on the nanometer scale, leading to a high surface area-to-volume ratio and quantum effects that are not present in bulk materials. These differences result in unique optical, electrical, and mechanical properties. Applications include targeted drug delivery in medicine, improved catalysts in chemical reactions, and enhanced strength materials in aerospace engineering.
What is the significance of phase diagrams in materials engineering?
Answer: Phase diagrams graphically represent the stability of different phases of a material under varying temperature and pressure conditions. They are essential tools for understanding material behavior during processing, such as melting, solidification, and alloy formation, enabling engineers to predict and control material properties during manufacturing.
How do composite materials combine the properties of their constituent materials to achieve enhanced performance?
Answer: Composite materials are engineered by combining two or more distinct materials to create a new material with superior properties. For instance, fiberglass combines glass fibers (which provide strength) with a polymer matrix (which offers flexibility), resulting in a material that is both strong and lightweight, suitable for applications like boat hulls and sports equipment.
What are smart materials, and how are they utilized in modern engineering applications?
Answer: Smart materials can respond to external stimuli—such as temperature, light, pressure, or electric fields—by changing their properties. Examples include shape-memory alloys that return to a predefined shape when heated and piezoelectric materials that generate an electric charge under mechanical stress. These materials are used in applications like actuators, sensors, and adaptive structures in aerospace and biomedical devices.
How does the field of materials engineering contribute to advancements in sustainable technologies?
Answer: Materials engineering plays a crucial role in developing sustainable technologies by creating materials that are more efficient, durable, and environmentally friendly. This includes designing catalysts that reduce energy consumption in chemical processes, developing biodegradable polymers to minimize plastic waste, and creating materials for renewable energy applications, such as more efficient photovoltaic cells and lightweight composites for wind turbine blades.
What are the challenges associated with scaling up the production of newly developed materials from the laboratory to industrial scale?
Answer: Scaling up material production involves challenges such as maintaining uniformity and quality, ensuring the reproducibility of properties, and developing cost-effective manufacturing processes. Laboratory synthesis methods may not be directly applicable to large-scale production, requiring the development of new techniques and equipment. Additionally, considerations like environmental impact, safety, and regulatory compliance become more significant at the industrial scale.
These questions and answers aim to provide a comprehensive understanding of chemical materials engineering, highlighting its principles, material types, and applications across various industries.
Thought-Provoking Questions and Detailed Answers on Chemical Materials Engineering
How do the atomic and molecular structures of materials influence their macroscopic properties and performance in engineering applications?
- Answer: The atomic arrangement in materials, such as the crystalline structure in metals or the amorphous structure in glass, directly impacts properties like strength, conductivity, and transparency. For example, tightly packed atoms in metals facilitate electrical conductivity, while the random arrangement in polymers provides flexibility. Understanding these relationships allows engineers to manipulate material structures through heat treatment or doping to achieve desired properties.
Why is it important to consider environmental sustainability in the development of new materials, and how can engineers address these concerns?
- Answer: Sustainable materials reduce environmental impact by minimizing resource depletion, pollution, and energy consumption. Engineers can address this by designing materials that are recyclable, biodegradable, or sourced from renewable resources. For instance, using bioplastics made from plant-based polymers reduces reliance on fossil fuels and lowers carbon emissions.
What challenges arise in creating composite materials, and how can these challenges be mitigated in the design and production process?
- Answer: Challenges include achieving strong bonding between components, uniform distribution of reinforcement materials, and preventing defects during manufacturing. Engineers mitigate these issues by selecting compatible matrix and reinforcement materials, optimizing fabrication techniques like resin infusion, and conducting rigorous quality control to ensure consistency.
How can nanotechnology revolutionize the field of chemical materials engineering, and what are its potential risks?
- Answer: Nanotechnology enables the creation of materials with enhanced properties, such as higher strength-to-weight ratios or improved electrical conductivity, by manipulating structures at the atomic level. However, potential risks include environmental and health concerns related to nanoparticle exposure. Engineers must develop safe synthesis methods and conduct thorough risk assessments to balance innovation with safety.
In what ways can advanced computational tools and simulations accelerate material discovery and innovation?
- Answer: Computational tools allow engineers to model and predict material behavior under various conditions, reducing the need for extensive physical testing. Techniques like density functional theory and molecular dynamics simulations enable the exploration of new material combinations, speeding up the discovery of materials for specific applications, such as lightweight alloys for aerospace.
How do phase transformations in materials affect their properties, and how can these transformations be controlled?
- Answer: Phase transformations, such as solid-to-liquid or solid-to-solid transitions, alter properties like hardness, ductility, and thermal conductivity. Engineers control these transformations through temperature, pressure, or alloying elements. For example, annealing steel induces phase changes that enhance its toughness and reduce brittleness.
What role does materials engineering play in the development of renewable energy technologies?
- Answer: Materials engineering is critical for creating efficient solar cells, durable wind turbine blades, and advanced batteries for energy storage. For instance, improving the efficiency of photovoltaic materials, such as perovskites, can make solar energy more affordable and accessible. Similarly, developing corrosion-resistant materials ensures the longevity of offshore wind turbines.
How do smart materials respond to external stimuli, and what innovative applications could they enable in the future?
- Answer: Smart materials, like shape-memory alloys and piezoelectric ceramics, change their properties in response to stimuli such as temperature, pressure, or electric fields. These materials are used in applications like self-healing coatings and energy-harvesting devices. Future innovations could include adaptive building materials that adjust insulation based on weather conditions.
What factors must be considered when selecting materials for extreme environments, such as space or deep-sea applications?
- Answer: Materials must withstand harsh conditions like extreme temperatures, high pressures, and corrosive environments. Engineers consider properties such as thermal stability, mechanical strength, and resistance to oxidation or corrosion. For instance, titanium alloys are chosen for aerospace applications due to their high strength-to-weight ratio and resistance to temperature variations.
How does recycling impact the properties of materials, and what strategies can ensure the quality of recycled materials?
- Answer: Recycling can degrade material properties, such as reducing the strength of recycled plastics or the purity of metals. Strategies to maintain quality include incorporating additives, improving sorting processes to minimize contamination, and developing advanced recycling technologies, such as chemical recycling for plastics.
Why is the study of failure mechanisms, such as fatigue and fracture, essential in materials engineering?
- Answer: Understanding failure mechanisms helps engineers design materials that can withstand long-term use and extreme conditions. For example, studying fatigue in metals used in bridges allows engineers to predict lifespan and implement preventative measures, such as periodic inspections and material upgrades, to ensure safety and reliability.
How can interdisciplinary collaboration enhance advancements in chemical materials engineering?
- Answer: Collaboration across disciplines like chemistry, physics, and computer science fosters innovative solutions. For example, combining expertise in computational modeling with material synthesis can accelerate the design of high-performance materials. Interdisciplinary efforts also address complex challenges, such as developing multifunctional materials for biomedical implants that integrate mechanical strength with biocompatibility.
These questions and answers encourage critical thinking, creativity, and a deeper understanding of the field, making learning engaging and thought-provoking.