Digital Twin Technology
Digital Twin Technology is reshaping the future of industrial innovation by enabling real-time digital replicas of physical systems, processes, or products. This convergence of simulation, sensor data, and intelligent analytics is becoming integral to modern Industrial and Manufacturing Technologies. By synchronizing virtual models with real-world behavior, engineers can predict performance, optimize operations, and reduce downtime across the entire product lifecycle.
From the outset of design, technologies such as Mechanical Design and Computer-Aided Design (CAD) integrate seamlessly with digital twin platforms, providing a foundational blueprint for simulation. These models are then enhanced with data collected through Industrial Automation and Robotics, leading to high-fidelity predictive environments. When applied in Computer-Integrated Manufacturing (CIM), the digital twin acts as a bridge between design and production.
The integration with technologies like Additive Manufacturing (3D Printing) and Advanced Materials and Manufacturing Technologies enables rapid prototyping and custom solutions tailored to real-time feedback. Insights gained can be translated into improved Manufacturing Quality Control and Assurance as well as more refined Manufacturing Process Design and Optimization.
Within the broader context of Smart Manufacturing and Industry 4.0, digital twins empower factories to self-diagnose and adapt to evolving conditions. They enhance responsiveness and resilience in operations by linking with real-time data pipelines and advanced analytics. Complementary to this, Sustainable Manufacturing initiatives benefit from the reduced material use and energy consumption facilitated by virtual testing.
In high-performance sectors such as Automotive Engineering and Biomechanical Engineering, digital twin systems support stress testing, dynamic modeling, and predictive maintenance planning. When embedded within Supply Chain Management, they help mitigate risks by simulating logistics constraints and resource flow in volatile environments.
At the production level, digital twins work in harmony with Energy and Resource Efficiency in Manufacturing, highlighting opportunities for savings and sustainable use. In worker-centric environments, tools informed by Human Factors and Ergonomics in Manufacturing promote better design layouts and interfaces based on real interaction feedback.
The predictive capabilities of digital twins are also rooted in robust engineering principles. Understanding control dynamics is essential, as taught in Control Systems in Mech Engineering, where real-time simulations are often applied. Topics like Fluid Mechanics and Hydraulics, Thermodynamics and Heat Transfer, and Solid Mechanics in Mechanical Engineering also contribute to the realistic modeling of operational environments.
Advanced material behavior and applications are simulated in conjunction with Nanotechnology and Advanced Materials in Mech Eng. On the production floor, real-time coordination between robotic systems and their virtual counterparts supports efficient Robotics and Automation in Mech Eng.
Ultimately, digital twin systems provide a unified platform that connects physical assets to a virtual continuum, enriching every phase from conceptual design to post-deployment analytics. Their role within Manufacturing and Production Engineering highlights a significant shift toward more data-driven, adaptive, and intelligent industrial ecosystems.
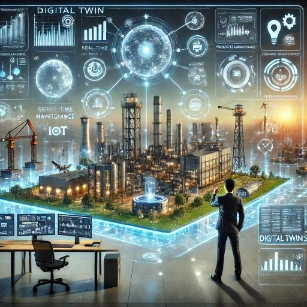
Table of Contents
Core Concepts of Digital Twin Technology
Definition and Framework
- Definition:
- A digital twin is a dynamic virtual model of a physical entity, continuously updated with real-time data.
- Key Components:
- Physical Asset or System:
- The real-world entity being modeled.
- Virtual Model:
- The digital replica of the physical system.
- Data Connectivity:
- Sensors and IoT devices transmit data from the physical system to the virtual model.
- Analytics Engine:
- Algorithms process data to provide insights, predictions, and recommendations.
- Physical Asset or System:
Types of Digital Twins
- Product Twin:
- Simulates a specific product throughout its lifecycle, from design to disposal.
- Process Twin:
- Models industrial processes to optimize workflows and reduce inefficiencies.
- System Twin:
- Represents entire systems, integrating multiple components and processes.
Key Functions
- Simulation:
- Tests various scenarios and configurations in a virtual environment without disrupting real-world operations.
- Monitoring:
- Tracks real-time performance, conditions, and metrics of physical systems.
- Prediction:
- Forecasts potential failures or inefficiencies using historical and real-time data.
- Optimization:
- Identifies opportunities to improve performance, reduce costs, and enhance productivity.
Applications of Digital Twin Technology
Manufacturing
- Applications:
- Monitoring factory operations and optimizing production lines.
- Simulating new layouts or process changes before implementation.
- Examples:
- A digital twin of an automotive assembly line predicting bottlenecks and recommending process adjustments.
- Benefits:
- Reduces downtime, enhances product quality, and increases throughput.
Aerospace and Defense
- Applications:
- Modeling aircraft engines for performance monitoring and predictive maintenance.
- Simulating flight conditions to optimize aerodynamics.
- Examples:
- Rolls-Royce using digital twins to monitor jet engine performance in real time.
- Benefits:
- Improves safety, reduces maintenance costs, and extends the lifecycle of critical components.
Healthcare
- Applications:
- Creating patient-specific digital twins for personalized treatment plans.
- Modeling medical devices to predict wear and improve design.
- Examples:
- Digital twins of hearts for planning complex cardiac surgeries.
- Benefits:
- Enhances patient outcomes, reduces errors, and accelerates medical innovation.
Energy and Utilities
- Applications:
- Monitoring power grids to predict outages and optimize energy distribution.
- Simulating wind turbine performance to maximize energy generation.
- Examples:
- GE Renewable Energy using digital twins to optimize wind farm efficiency.
- Benefits:
- Reduces energy waste, ensures grid reliability, and lowers operational costs.
Smart Cities
- Applications:
- Simulating urban infrastructure to improve traffic flow and resource management.
- Monitoring building energy usage and optimizing HVAC systems.
- Examples:
- Singapore’s Virtual Singapore project, a digital twin of the city for urban planning.
- Benefits:
- Enhances sustainability, reduces congestion, and improves quality of life.
Automotive
- Applications:
- Simulating vehicle performance and predicting maintenance needs.
- Testing autonomous driving algorithms in virtual environments.
- Examples:
- Tesla using digital twins for over-the-air software updates and diagnostics.
- Benefits:
- Speeds up innovation, reduces warranty costs, and enhances user experience.
Key Technologies Enabling Digital Twins
Internet of Things (IoT)
- Role:
- Provides the data backbone for digital twins by connecting physical assets with sensors and devices.
- Applications:
- Real-time monitoring of equipment, environmental conditions, and system performance.
Artificial Intelligence (AI) and Machine Learning
- Role:
- Enables predictive analytics, anomaly detection, and decision-making.
- Applications:
- AI algorithms analyzing data to predict machine failures or optimize energy use.
Cloud Computing
- Role:
- Provides scalable storage and processing power for digital twin simulations and data analysis.
- Applications:
- Hosting complex simulations for global manufacturing facilities.
5G Connectivity
- Role:
- Facilitates high-speed, low-latency data transfer for real-time synchronization between physical systems and digital twins.
- Applications:
- Enabling digital twins in dynamic environments like smart cities or autonomous vehicles.
Simulation Software
- Role:
- Creates virtual models of systems and tests different scenarios.
- Applications:
- Finite Element Analysis (FEA) for structural integrity testing.
Blockchain
- Role:
- Enhances data security and transparency in digital twin ecosystems.
- Applications:
- Tracking the authenticity of components in a supply chain.
Benefits of Digital Twin Technology
- Predictive Maintenance:
- Reduces unexpected downtime by forecasting equipment failures.
- Enhanced Efficiency:
- Optimizes workflows and resource allocation for higher productivity.
- Cost Savings:
- Lowers operational and maintenance costs through data-driven insights.
- Improved Decision-Making:
- Provides actionable intelligence for strategic planning and real-time responses.
- Accelerated Innovation:
- Facilitates rapid prototyping and testing in virtual environments.
- Sustainability:
- Reduces energy consumption and waste by optimizing processes and designs.
Challenges in Implementing Digital Twin Technology
- High Initial Investment:
- Requires significant resources for infrastructure, software, and expertise.
- Data Integration Complexity:
- Consolidating data from diverse sources and systems can be challenging.
- Cybersecurity Risks:
- Protecting sensitive data and preventing cyberattacks on digital twin systems.
- Scalability Issues:
- Expanding digital twin models to large-scale operations may require extensive resources.
- Skill Gaps:
- Need for trained personnel to develop, implement, and maintain digital twin solutions.
Emerging Trends in Digital Twin Technology
- AI-Driven Twins:
- Enhanced intelligence through machine learning for autonomous decision-making.
- Edge Computing Integration:
- Processing data locally to reduce latency and improve real-time responsiveness.
- Digital Twin Networks:
- Linking multiple digital twins across systems and organizations for holistic optimization.
- Sustainability Applications:
- Using digital twins to design eco-friendly systems and monitor carbon footprints.
- Quantum Computing:
- Accelerating complex simulations for materials science, logistics, and healthcare.
Future Directions in Digital Twin Technology
- Universal Adoption in Manufacturing:
- Digital twins becoming standard for process optimization and predictive maintenance.
- Hyper-Personalization:
- Creating individual digital twins for consumers to optimize product usage and services.
- Interdisciplinary Integration:
- Combining digital twins with augmented reality (AR) and virtual reality (VR) for immersive insights.
- Global Collaboration:
- Sharing digital twin models across supply chains to enhance transparency and efficiency.
- Smart Infrastructure:
- Expanding digital twin applications to monitor and manage large-scale infrastructure projects like airports and power grids.
Why Study Digital Twin Technology
Creating Virtual Representations of Physical Systems
Digital twin technology uses real-time data and simulations to mirror physical assets digitally. Students learn how to build models that reflect machines, products, or processes. This enables monitoring, analysis, and control in real time.
Enhancing Performance and Reliability
Digital twins help predict equipment failures and optimize operations. Students study how to apply simulations and sensor feedback for performance tuning. This increases uptime and reduces maintenance costs.
Applications in Smart Manufacturing and Industry 4.0
Students explore how digital twins are used in predictive maintenance, supply chain optimization, and factory automation. These applications are central to Industry 4.0 initiatives. This makes digital twin skills highly relevant and in demand.
Integration with IoT and Cloud Platforms
Digital twins operate on data from IoT devices and are supported by cloud computing. Students learn how to manage connectivity, data flow, and security. These competencies are crucial for digital transformation in manufacturing.
Driving Innovation and Sustainability
Digital twins reduce waste, accelerate prototyping, and support remote monitoring. Students understand how virtual testing saves time and resources. This fosters innovation while promoting sustainable manufacturing practices.
Digital Twin Technology: Conclusion
Digital Twin Technology represents a paradigm shift in how industries approach monitoring, simulation, and optimization. By bridging the physical and digital worlds, digital twins empower organizations to enhance efficiency, reduce costs, and drive innovation. As advancements in AI, IoT, and connectivity continue to evolve, digital twin technology will become an integral tool in transforming industries, ensuring sustainability, and meeting the challenges of an increasingly complex and dynamic world.Digital Twin Technology: Review Questions with Detailed Answers
1. What is Digital Twin Technology and how is it defined in the context of manufacturing?
Answer:
Digital Twin Technology refers to the creation of a virtual replica of a physical object, system, or process that simulates its real-world counterpart’s behavior, characteristics, and performance. In manufacturing, a digital twin is used to model machines, production lines, or entire factories, allowing for real-time monitoring, analysis, and optimization of manufacturing operations.
Concepts:
- Virtual Replica: A digital version that mirrors the physical entity.
- Real-Time Monitoring: Continuously tracking the performance and status of the physical object through its digital twin.
- Simulation and Analysis: Using the digital twin to run simulations and analyze data for better decision-making.
Conclusion: Digital Twin Technology bridges the physical and digital worlds, enabling manufacturers to enhance operational efficiency, predict maintenance needs, and innovate processes through accurate simulations and real-time data insights.
2. What are the primary components of a Digital Twin system in manufacturing?
Answer:
A Digital Twin system in manufacturing typically comprises the following primary components:
- Physical Entity: The actual machine, product, or manufacturing process being replicated.
- Digital Model: The virtual representation of the physical entity, created using CAD software or other modeling tools.
- Sensors and IoT Devices: Devices attached to the physical entity that collect real-time data on various parameters like temperature, pressure, and vibration.
- Data Communication Infrastructure: Networks and protocols that facilitate the transfer of data between the physical entity and the digital model.
- Data Storage and Management: Systems that store and manage the vast amounts of data generated by sensors.
- Analytics and Simulation Tools: Software that processes the data to provide insights, run simulations, and predict future performance.
- User Interface: Dashboards and visualization tools that allow users to interact with and monitor the digital twin.
Concepts:
- Integration: Seamless connection between physical and digital components.
- Real-Time Data Processing: Continuous updating of the digital twin with live data.
Conclusion: These components work together to create an accurate and functional digital twin that mirrors the physical manufacturing environment, enabling enhanced monitoring, analysis, and optimization.
3. How do sensors and IoT devices contribute to the functionality of Digital Twins in manufacturing?
Answer:
Sensors and IoT devices are critical to the functionality of Digital Twins as they provide the real-time data necessary to accurately mirror and monitor the physical entity. These devices collect various types of data, such as temperature, pressure, vibration, and operational status, which are then transmitted to the digital model.
Concepts:
- Data Collection: Gathering information from the physical environment.
- Connectivity: Ensuring continuous and reliable data transmission to the digital twin.
Contributions:
- Real-Time Monitoring: Enables the digital twin to reflect the current state of the physical entity, allowing for immediate detection of anomalies or deviations.
- Predictive Maintenance: Analyzing sensor data helps predict potential failures, enabling proactive maintenance and reducing downtime.
- Performance Optimization: Continuous data flow allows for ongoing analysis and optimization of manufacturing processes based on real-time insights.
- Simulation Accuracy: High-quality data ensures that simulations and models accurately represent the physical entity, enhancing the reliability of predictive analyses.
Conclusion: Sensors and IoT devices are essential for maintaining the accuracy and responsiveness of Digital Twins, making them indispensable tools for modern manufacturing optimization and maintenance strategies.
4. What are the key benefits of implementing Digital Twin Technology in manufacturing operations?
Answer:
Implementing Digital Twin Technology in manufacturing operations offers numerous benefits, including:
Enhanced Operational Efficiency:
- How: Real-time monitoring and data analysis streamline processes.
- Impact: Increases productivity and reduces operational costs.
Predictive Maintenance:
- How: Analyzes sensor data to predict equipment failures.
- Impact: Minimizes downtime and extends machinery lifespan.
Improved Product Quality:
- How: Continuous monitoring ensures adherence to quality standards.
- Impact: Reduces defects and enhances customer satisfaction.
Cost Reduction:
- How: Optimizes resource utilization and minimizes waste.
- Impact: Lowers production costs and increases profitability.
Accelerated Innovation:
- How: Simulations and virtual testing facilitate rapid prototyping.
- Impact: Speeds up product development and time-to-market.
Better Decision-Making:
- How: Provides comprehensive data and insights.
- Impact: Informs strategic and operational decisions with accuracy.
Increased Flexibility and Adaptability:
- How: Enables quick adjustments to production processes based on real-time data.
- Impact: Allows manufacturers to respond swiftly to market changes and demands.
Enhanced Supply Chain Management:
- How: Integrates data across the supply chain for better coordination.
- Impact: Improves inventory management and reduces lead times.
Conclusion: Digital Twin Technology significantly enhances various aspects of manufacturing operations, driving efficiency, quality, and innovation while reducing costs and improving overall competitiveness.
5. How does Digital Twin Technology facilitate predictive maintenance in manufacturing?
Answer:
Digital Twin Technology facilitates predictive maintenance by continuously monitoring the condition and performance of manufacturing equipment through real-time data collected by sensors and IoT devices. This data is analyzed using advanced analytics and machine learning algorithms to predict when a machine is likely to fail or require maintenance.
Concepts:
- Condition Monitoring: Tracking the health and performance of machinery in real-time.
- Predictive Analytics: Using data-driven techniques to forecast future equipment behavior.
Facilitation Process:
- Data Collection: Sensors gather data on various operational parameters such as temperature, vibration, and pressure.
- Data Analysis: Advanced analytics and machine learning models process the data to identify patterns and trends indicative of potential failures.
- Prediction: The digital twin uses the analyzed data to predict the remaining useful life of equipment components.
- Maintenance Scheduling: Based on predictions, maintenance can be scheduled proactively, before a failure occurs.
- Feedback Loop: Insights from maintenance activities are fed back into the digital twin to improve future predictions.
Benefits:
- Reduced Downtime: Predictive maintenance minimizes unexpected equipment failures, ensuring continuous production.
- Cost Savings: Prevents costly repairs and extends the lifespan of machinery by addressing issues early.
- Improved Safety: Reduces the risk of accidents caused by equipment malfunctions.
- Optimized Maintenance Resources: Allocates maintenance resources more effectively based on actual needs rather than fixed schedules.
Conclusion: Digital Twin Technology transforms maintenance strategies from reactive to proactive, enhancing reliability, reducing costs, and improving overall operational efficiency in manufacturing environments.
6. In what ways can Digital Twins be used to optimize manufacturing processes?
Answer:
Digital Twins can optimize manufacturing processes through simulation, real-time monitoring, data analysis, and continuous feedback mechanisms. By providing a virtual representation of the physical manufacturing environment, Digital Twins enable manufacturers to experiment, analyze, and refine processes without disrupting actual production.
Concepts:
- Simulation: Creating virtual scenarios to test and optimize processes.
- Continuous Improvement: Ongoing refinement based on real-time data and feedback.
Optimization Methods:
Process Simulation:
- How: Run simulations of manufacturing processes to identify inefficiencies and test improvements.
- Impact: Allows for experimentation and optimization without impacting actual production.
Real-Time Monitoring:
- How: Continuously track process parameters and performance metrics.
- Impact: Enables immediate adjustments to maintain optimal operating conditions.
Data-Driven Decision Making:
- How: Analyze data from the digital twin to uncover trends and insights.
- Impact: Informs strategic decisions to enhance process efficiency and effectiveness.
Resource Allocation:
- How: Optimize the use of materials, energy, and labor based on real-time data and simulations.
- Impact: Reduces waste and maximizes resource utilization.
Predictive Analytics:
- How: Use predictive models to forecast process performance and potential bottlenecks.
- Impact: Prevents issues before they arise, ensuring smooth and efficient operations.
Quality Control:
- How: Monitor quality metrics in real-time and adjust processes to maintain standards.
- Impact: Ensures consistent product quality and reduces defects.
Production Planning:
- How: Optimize production schedules and workflows based on real-time and predictive data.
- Impact: Enhances throughput and ensures timely delivery of products.
Maintenance Planning:
- How: Integrate predictive maintenance insights to schedule maintenance activities without disrupting production.
- Impact: Maintains equipment performance and reduces downtime.
Conclusion: Digital Twins provide a powerful toolset for optimizing manufacturing processes by enabling detailed analysis, simulation, and real-time adjustments. This leads to enhanced efficiency, reduced costs, improved quality, and greater overall productivity in manufacturing operations.
7. What challenges might manufacturers face when implementing Digital Twin Technology, and how can they overcome these challenges?
Answer:
Implementing Digital Twin Technology in manufacturing can present several challenges, including high initial costs, data integration complexities, cybersecurity concerns, and the need for specialized skills. Manufacturers can overcome these challenges through strategic planning, investment in training, robust security measures, and phased implementation approaches.
Concepts:
- Implementation Challenges: Obstacles that hinder the successful adoption of new technologies.
- Mitigation Strategies: Approaches to address and overcome challenges.
Challenges and Solutions:
High Initial Costs:
- Challenge: The setup of Digital Twin systems requires significant investment in software, hardware, and infrastructure.
- Solution: Start with pilot projects to demonstrate value, seek scalable solutions, and explore financing options or partnerships to spread costs over time.
Data Integration Complexities:
- Challenge: Integrating data from various sources and systems into a cohesive Digital Twin can be technically challenging.
- Solution: Use standardized data formats and protocols, invest in middleware solutions, and ensure interoperability between different systems and devices.
Cybersecurity Concerns:
- Challenge: Digital Twins involve extensive data sharing and connectivity, increasing vulnerability to cyberattacks.
- Solution: Implement robust cybersecurity measures, including encryption, access controls, and regular security audits to protect data integrity and system security.
Need for Specialized Skills:
- Challenge: Developing and managing Digital Twins requires expertise in areas like data analytics, simulation, and IoT.
- Solution: Invest in workforce training and development, hire skilled professionals, and collaborate with technology partners or consultants to bridge skill gaps.
Data Quality and Accuracy:
- Challenge: The effectiveness of a Digital Twin depends on the quality and accuracy of the data it receives.
- Solution: Ensure proper calibration and maintenance of sensors, implement data validation processes, and continuously monitor data integrity.
Scalability Issues:
- Challenge: Scaling Digital Twin solutions to cover entire factories or multiple facilities can be complex and resource-intensive.
- Solution: Design Digital Twins with scalability in mind, using modular architectures and cloud-based solutions that can grow with manufacturing needs.
Resistance to Change:
- Challenge: Employees and management may resist adopting new technologies due to comfort with existing processes or fear of job displacement.
- Solution: Foster a culture of innovation, communicate the benefits of Digital Twins, involve stakeholders in the implementation process, and provide adequate training and support.
Maintenance and Updates:
- Challenge: Keeping the Digital Twin up-to-date with changes in the physical environment and processes requires ongoing effort.
- Solution: Establish regular maintenance schedules, automate data synchronization, and integrate update mechanisms to ensure the Digital Twin remains accurate and relevant.
Conclusion: While implementing Digital Twin Technology presents several challenges, manufacturers can successfully navigate these obstacles through careful planning, investment in the right resources, and a commitment to continuous improvement. By addressing these challenges proactively, manufacturers can fully leverage the benefits of Digital Twins to enhance their manufacturing operations.
8. How can Digital Twins improve the design and development of new products in manufacturing?
Answer:
Digital Twins can significantly improve the design and development of new products in manufacturing by enabling virtual prototyping, simulation, and iterative testing. This approach allows designers and engineers to refine product designs, identify potential issues, and optimize performance before committing to physical production, thereby reducing development time and costs while enhancing product quality.
Concepts:
- Virtual Prototyping: Creating digital models of products to test and evaluate designs without physical prototypes.
- Iterative Testing: Repeatedly testing and refining designs based on feedback and simulation results.
Improvements in Design and Development:
Rapid Prototyping:
- How: Create and test virtual prototypes quickly using Digital Twins.
- Impact: Accelerates the design process by allowing multiple design iterations to be evaluated in a short time frame.
Simulation of Real-World Conditions:
- How: Use Digital Twins to simulate how products will perform under various operational conditions.
- Impact: Identifies potential design flaws and performance issues early, ensuring that the final product meets desired specifications and reliability standards.
Optimization of Design Parameters:
- How: Analyze simulation data to optimize design elements such as material selection, geometry, and structural integrity.
- Impact: Enhances product performance, durability, and cost-effectiveness by refining design parameters based on data-driven insights.
Cost and Time Savings:
- How: Reduce the need for multiple physical prototypes by conducting extensive virtual testing.
- Impact: Lowers development costs and shortens time-to-market, allowing manufacturers to respond more swiftly to market demands and innovations.
Enhanced Collaboration:
- How: Share Digital Twin models with cross-functional teams for collaborative design and review.
- Impact: Improves communication and coordination among designers, engineers, and other stakeholders, leading to more cohesive and well-integrated product designs.
Customization and Personalization:
- How: Utilize Digital Twins to design and test customized products tailored to specific customer needs.
- Impact: Facilitates the development of personalized products without compromising on quality or performance, enhancing customer satisfaction.
Lifecycle Analysis:
- How: Use Digital Twins to assess the entire lifecycle of a product, from design and production to usage and disposal.
- Impact: Identifies opportunities for sustainability improvements, such as material efficiency and end-of-life recyclability, aligning product development with environmental goals.
Risk Mitigation:
- How: Identify and address potential risks in the design phase through comprehensive simulations and testing.
- Impact: Reduces the likelihood of costly recalls, warranty claims, and reputation damage by ensuring that products are robust and reliable.
Conclusion: Digital Twins revolutionize the design and development of new products in manufacturing by providing a comprehensive, data-driven platform for virtual prototyping, simulation, and optimization. This leads to faster development cycles, reduced costs, improved product quality, and greater innovation, ultimately enhancing the competitiveness and responsiveness of manufacturers in the market.
9. In what ways can Digital Twins enhance supply chain management within manufacturing operations?
Answer:
Digital Twins enhance supply chain management within manufacturing operations by providing real-time visibility, predictive analytics, and seamless integration of supply chain data with manufacturing processes. This comprehensive approach enables better coordination, optimization, and responsiveness across the entire supply chain, leading to increased efficiency and reduced costs.
Concepts:
- Supply Chain Visibility: The ability to monitor and track all elements of the supply chain in real-time.
- Predictive Analytics: Using data and algorithms to forecast future supply chain events and trends.
Enhancements to Supply Chain Management:
Real-Time Monitoring and Tracking:
- How: Digital Twins continuously track the movement of materials, components, and finished products throughout the supply chain.
- Impact: Provides real-time visibility into inventory levels, shipment statuses, and potential bottlenecks, enabling timely interventions and adjustments.
Demand Forecasting and Planning:
- How: Analyze data from Digital Twins to predict future demand based on historical trends, market conditions, and production schedules.
- Impact: Improves the accuracy of demand forecasts, ensuring that supply aligns with market needs and reducing the risk of overproduction or stockouts.
Inventory Optimization:
- How: Utilize Digital Twins to monitor inventory levels and predict material requirements based on production plans.
- Impact: Optimizes inventory management, minimizing holding costs and ensuring that materials are available when needed for production.
Supplier Coordination:
- How: Integrate Digital Twins with supplier systems to synchronize production schedules and material deliveries.
- Impact: Enhances collaboration with suppliers, ensures timely procurement of materials, and reduces lead times, supporting uninterrupted production.
Risk Management and Resilience:
- How: Use Digital Twins to simulate supply chain disruptions and assess their impact on manufacturing operations.
- Impact: Identifies vulnerabilities and enables the development of contingency plans, enhancing the resilience of the supply chain against unforeseen events.
Process Synchronization:
- How: Align manufacturing processes with supply chain activities through data integration and real-time communication.
- Impact: Ensures that production schedules are in sync with material availability and delivery timelines, reducing delays and improving overall efficiency.
Cost Reduction:
- How: Optimize logistics, transportation, and inventory levels using insights from Digital Twins.
- Impact: Reduces operational costs associated with transportation, warehousing, and inventory holding, increasing overall profitability.
Enhanced Collaboration:
- How: Facilitate better communication and data sharing among all supply chain partners through the Digital Twin platform.
- Impact: Strengthens relationships with suppliers and distributors, promoting a more coordinated and efficient supply chain network.
Sustainability and Environmental Impact:
- How: Monitor and optimize resource usage and logistics to minimize environmental impact.
- Impact: Supports sustainable supply chain practices by reducing waste, energy consumption, and carbon emissions.
Lifecycle Management:
- How: Track the entire lifecycle of products from raw material sourcing to end-of-life disposal using Digital Twins.
- Impact: Enhances traceability, compliance with regulations, and the ability to implement circular economy practices within the supply chain.
Conclusion: Digital Twins provide a powerful tool for enhancing supply chain management by offering comprehensive visibility, predictive capabilities, and seamless integration of data across the supply chain and manufacturing processes. This leads to more efficient, resilient, and cost-effective supply chain operations, ultimately contributing to the overall success and competitiveness of manufacturing organizations.
10. How can Digital Twins be utilized for training and workforce development in manufacturing settings?
Answer:
Digital Twins can be utilized for training and workforce development in manufacturing settings by providing realistic, interactive simulations that replicate the physical manufacturing environment. This enables employees to gain hands-on experience, practice skills, and understand complex processes in a safe and controlled virtual environment before applying them on the factory floor.
Concepts:
- Virtual Training: Using digital simulations to train employees without the need for physical equipment.
- Interactive Learning: Engaging employees through interactive and immersive training experiences.
Utilization Methods:
Virtual Simulations:
- How: Create Digital Twins of manufacturing equipment and processes for immersive training simulations.
- Impact: Allows employees to practice operating machinery, troubleshooting issues, and executing production tasks without the risk of damaging equipment or disrupting production.
Scenario-Based Training:
- How: Develop training modules that simulate various scenarios, such as equipment malfunctions, safety incidents, or process optimizations.
- Impact: Prepares employees to respond effectively to real-world challenges, enhancing their problem-solving and decision-making skills.
Onboarding and Skill Development:
- How: Use Digital Twins to onboard new employees by providing a virtual overview of manufacturing operations and key processes.
- Impact: Accelerates the learning curve for new hires, ensuring they understand their roles and responsibilities before working on actual production lines.
Continuous Learning and Upskilling:
- How: Provide ongoing training opportunities through Digital Twin platforms that offer updated simulations based on the latest manufacturing technologies and practices.
- Impact: Keeps the workforce current with evolving technologies, fostering a culture of continuous improvement and adaptability.
Safety Training:
- How: Simulate hazardous situations and emergency response scenarios within the Digital Twin environment.
- Impact: Enhances employee preparedness for safety incidents, reducing the likelihood of accidents and improving overall workplace safety.
Performance Evaluation and Feedback:
- How: Monitor employee interactions with Digital Twins to assess their performance and provide personalized feedback.
- Impact: Identifies areas for improvement, supports targeted training efforts, and promotes employee development.
Collaboration and Team Training:
- How: Use Digital Twins to facilitate collaborative training exercises where teams work together to solve complex manufacturing challenges.
- Impact: Enhances teamwork, communication, and collaborative problem-solving skills among employees.
Remote Training Capabilities:
- How: Enable employees to access Digital Twin training modules remotely, providing flexibility in training schedules and locations.
- Impact: Expands training opportunities to a wider workforce, including remote or distributed teams, without the need for physical presence on the factory floor.
Benefits of Utilizing Digital Twins for Training:
- Cost-Effective Training: Reduces the need for physical training setups and minimizes the cost associated with downtime during training sessions.
- Safe Learning Environment: Provides a risk-free platform for employees to experiment and learn without the consequences of real-world mistakes.
- Enhanced Retention: Interactive and immersive training experiences improve knowledge retention and skill acquisition.
- Scalable Training Solutions: Easily scalable to accommodate large numbers of employees and diverse training needs across different manufacturing areas.
Conclusion: Digital Twins offer a versatile and effective tool for training and workforce development in manufacturing settings. By providing realistic simulations, interactive learning experiences, and comprehensive training modules, Digital Twins enhance employee skills, improve safety, and support the continuous development of a skilled and adaptable workforce, ultimately contributing to the success and efficiency of manufacturing operations.
11. How can Digital Twins assist in the lifecycle management of manufacturing products?
Answer:
Digital Twins assist in the lifecycle management of manufacturing products by providing a comprehensive digital representation that spans from design and production to usage and end-of-life stages. This holistic approach enables manufacturers to monitor, analyze, and optimize every phase of a product’s lifecycle, ensuring efficiency, sustainability, and continuous improvement.
Concepts:
- Lifecycle Management: The process of managing a product’s journey from inception to disposal.
- Holistic Monitoring: Overseeing all aspects of a product’s lifecycle through integrated data and insights.
Assistance Methods:
Design Phase:
- How: Utilize Digital Twins to simulate and optimize product designs before physical prototyping.
- Impact: Enhances design accuracy, reduces development time, and ensures that products meet performance and quality standards.
Production Phase:
- How: Monitor and control manufacturing processes in real-time using Digital Twins.
- Impact: Ensures consistent production quality, optimizes resource utilization, and facilitates rapid adjustments to manufacturing workflows as needed.
Operational Phase:
- How: Use Digital Twins to track product performance and usage in real-world conditions.
- Impact: Provides valuable insights into how products perform, identifies areas for improvement, and supports proactive maintenance and support services.
Maintenance and Support:
- How: Leverage Digital Twins to predict maintenance needs and manage service schedules based on actual product usage data.
- Impact: Extends product lifespan, reduces downtime, and enhances customer satisfaction through timely and effective maintenance interventions.
Upgrade and Enhancement:
- How: Analyze data from Digital Twins to identify opportunities for product upgrades and enhancements.
- Impact: Facilitates the development of improved versions of products, ensuring they remain competitive and meet evolving customer needs.
End-of-Life Management:
- How: Use Digital Twins to plan and manage the disposal, recycling, or repurposing of products at the end of their lifecycle.
- Impact: Supports sustainable disposal practices, reduces environmental impact, and aligns with circular economy principles.
Compliance and Reporting:
- How: Maintain comprehensive records of a product’s lifecycle activities through the Digital Twin.
- Impact: Simplifies compliance with regulatory requirements and facilitates detailed reporting for quality assurance and sustainability initiatives.
Feedback and Continuous Improvement:
- How: Incorporate feedback from all lifecycle stages into the Digital Twin to drive continuous product and process improvements.
- Impact: Enhances overall product quality, innovation, and operational efficiency, fostering a culture of continuous improvement.
Benefits of Lifecycle Management with Digital Twins:
- Enhanced Product Quality: Continuous monitoring and optimization ensure products meet high-quality standards throughout their lifecycle.
- Cost Efficiency: Identifies cost-saving opportunities across design, production, and maintenance phases.
- Sustainability: Promotes environmentally responsible practices through optimized resource use and effective end-of-life management.
- Customer Satisfaction: Ensures reliable product performance and timely support, leading to increased customer trust and loyalty.
- Innovation: Facilitates ongoing product enhancements and the development of new features based on real-world performance data.
Conclusion: Digital Twins play a pivotal role in lifecycle management by providing a unified and dynamic platform that oversees every stage of a product’s journey. This comprehensive oversight enables manufacturers to optimize processes, ensure product quality, enhance sustainability, and drive continuous improvement, ultimately leading to more efficient and competitive manufacturing operations.
12. How can Digital Twins contribute to sustainability and environmental responsibility in manufacturing?
Answer:
Digital Twins contribute to sustainability and environmental responsibility in manufacturing by enabling precise monitoring, optimization, and simulation of manufacturing processes and products. This capability allows manufacturers to minimize waste, reduce energy consumption, enhance resource efficiency, and develop environmentally friendly products, thereby supporting broader sustainability goals.
Concepts:
- Sustainable Manufacturing: Practices that minimize environmental impact, conserve resources, and promote social responsibility.
- Environmental Responsibility: Commitment to reducing negative environmental impacts through proactive measures.
Contribution Methods:
Waste Reduction:
- How: Use Digital Twins to simulate and optimize manufacturing processes, identifying inefficiencies and areas where waste can be minimized.
- Impact: Reduces material waste, lowers disposal costs, and minimizes environmental pollution.
Energy Optimization:
- How: Monitor and analyze energy usage in real-time through Digital Twins to identify opportunities for energy savings.
- Impact: Lowers energy consumption, reduces greenhouse gas emissions, and decreases operational costs.
Resource Efficiency:
- How: Optimize the use of raw materials and resources by simulating different production scenarios and selecting the most efficient methods.
- Impact: Enhances resource utilization, reduces dependency on non-renewable resources, and supports sustainable resource management.
Product Lifecycle Assessment:
- How: Utilize Digital Twins to assess the environmental impact of products throughout their lifecycle, from design to disposal.
- Impact: Identifies opportunities to improve product sustainability, such as using eco-friendly materials and designing for recyclability.
Process Optimization for Sustainability:
- How: Analyze manufacturing data to optimize processes for lower environmental impact, such as reducing emissions and improving waste management.
- Impact: Enhances overall sustainability of manufacturing operations, aligning with environmental regulations and corporate sustainability goals.
Simulation of Sustainable Practices:
- How: Simulate the implementation of sustainable practices, such as renewable energy integration or circular economy models, using Digital Twins.
- Impact: Evaluates the feasibility and benefits of sustainable initiatives before actual implementation, ensuring effective and efficient adoption.
Compliance and Reporting:
- How: Maintain accurate records of environmental performance through Digital Twins, facilitating compliance with environmental regulations.
- Impact: Simplifies reporting requirements, ensures adherence to sustainability standards, and enhances transparency.
Innovation in Sustainable Product Design:
- How: Use Digital Twins to explore and develop innovative product designs that prioritize sustainability, such as lightweighting for fuel efficiency or modular designs for easy repair.
- Impact: Leads to the creation of environmentally responsible products that meet market demands for sustainability.
Supply Chain Sustainability:
- How: Integrate supply chain data into Digital Twins to monitor and optimize the environmental impact of suppliers and logistics.
- Impact: Ensures that the entire supply chain adheres to sustainability standards, reducing the overall environmental footprint.
Enhanced Decision-Making for Sustainability Initiatives:
- How: Provide data-driven insights to inform strategic decisions related to sustainability, such as investments in green technologies or process improvements.
- Impact: Enables manufacturers to make informed choices that balance economic performance with environmental responsibility.
Benefits of Sustainability with Digital Twins:
- Environmental Impact Reduction: Minimizes the negative environmental effects of manufacturing operations.
- Cost Savings: Reduces waste and energy consumption, leading to lower operational costs.
- Regulatory Compliance: Ensures adherence to environmental laws and standards, avoiding penalties and enhancing reputation.
- Brand Reputation: Demonstrates commitment to sustainability, attracting environmentally conscious customers and stakeholders.
- Long-Term Viability: Supports the creation of sustainable manufacturing practices that ensure the long-term success and resilience of manufacturing operations.
Conclusion: Digital Twins are instrumental in advancing sustainability and environmental responsibility in manufacturing by providing the tools and insights needed to optimize processes, reduce waste, and develop eco-friendly products. By leveraging Digital Twin Technology, manufacturers can achieve significant environmental benefits while also realizing economic advantages, thereby fostering a sustainable and responsible manufacturing ecosystem.
Conclusion:
The above review questions and detailed answers provide a comprehensive understanding of Digital Twin Technology within the manufacturing sector. Covering fundamental definitions, key components, functionalities, benefits, challenges, and applications, these questions help reinforce essential knowledge and enhance comprehension of how Digital Twins revolutionize manufacturing processes. By engaging with these review questions, students can solidify their grasp of Digital Twin concepts, their integration into manufacturing systems, and their role in driving efficiency, sustainability, and innovation in modern industrial environments.
Digital Twin Technology: Thought-Provoking Questions with Detailed Answers
1. How can Digital Twin Technology transform the traditional manufacturing workflow, and what implications does this have for operational efficiency?
Answer:
Digital Twin Technology revolutionizes traditional manufacturing workflows by creating a dynamic, real-time virtual replica of physical assets, processes, or entire systems. This transformation facilitates a more integrated and seamless workflow, enhancing operational efficiency in several key ways.
Concepts:
- Digital Twin: A virtual model designed to accurately reflect a physical object or system.
- Operational Efficiency: The capability of an organization to deliver products or services to its customers in the most cost-effective manner without compromising quality.
Transformation of Workflow:
Integration of Design and Production:
- How: Digital Twins bridge the gap between design (CAD) and production (CAM), allowing for continuous feedback and iterative improvements.
- Impact: Reduces time from design to production, minimizes errors, and ensures that designs are manufacturable.
Real-Time Monitoring and Control:
- How: Continuous data flow from sensors on physical assets to their digital counterparts enables real-time monitoring.
- Impact: Allows for immediate adjustments to processes, reducing downtime and optimizing performance.
Predictive Maintenance:
- How: Digital Twins analyze data to predict when maintenance should be performed.
- Impact: Prevents unexpected equipment failures, extends asset lifespan, and reduces maintenance costs.
Process Optimization:
- How: Simulation of different scenarios using Digital Twins helps identify the most efficient production methods.
- Impact: Enhances throughput, reduces waste, and lowers operational costs.
Enhanced Collaboration:
- How: Digital Twins provide a unified platform for different departments (engineering, production, maintenance) to collaborate.
- Impact: Improves communication, aligns objectives, and fosters a more cohesive operational environment.
Implications for Operational Efficiency:
- Reduced Production Time: Streamlined workflows and faster design-to-production transitions accelerate manufacturing cycles.
- Lower Costs: Predictive maintenance and process optimizations decrease operational expenses.
- Higher Quality: Real-time adjustments and continuous monitoring ensure products meet quality standards consistently.
- Increased Flexibility: Ability to quickly adapt to changes in demand or production requirements enhances responsiveness.
- Data-Driven Decision Making: Comprehensive data insights support informed strategic and operational decisions, driving continuous improvement.
Conclusion: Digital Twin Technology fundamentally transforms traditional manufacturing workflows by enhancing integration, monitoring, maintenance, and optimization. These changes lead to significant improvements in operational efficiency, enabling manufacturers to produce higher quality products faster and at lower costs while maintaining flexibility and responsiveness to market demands.
2. In what ways can Digital Twin Technology contribute to sustainability in manufacturing, and what are the potential challenges in achieving this?
Answer:
Digital Twin Technology can significantly contribute to sustainability in manufacturing by optimizing resource utilization, reducing waste, enhancing energy efficiency, and facilitating sustainable product design. However, achieving these benefits also presents potential challenges that manufacturers must address.
Concepts:
- Sustainability: Meeting present needs without compromising the ability of future generations to meet their own needs.
- Resource Utilization: Efficient use of materials, energy, and other resources in manufacturing processes.
Contributions to Sustainability:
Resource Optimization:
- How: Digital Twins simulate manufacturing processes to identify the most efficient use of materials and energy.
- Impact: Minimizes resource waste, reduces material costs, and conserves natural resources.
Waste Reduction:
- How: Real-time monitoring and predictive analytics help identify and eliminate sources of waste in production.
- Impact: Lowers environmental impact by decreasing the amount of waste generated and improving recycling rates.
Energy Efficiency:
- How: Digital Twins analyze energy consumption patterns and optimize machinery operations for lower energy use.
- Impact: Reduces greenhouse gas emissions and operational costs by lowering energy consumption.
Sustainable Product Design:
- How: Enables the simulation of product lifecycles to assess environmental impact and identify opportunities for sustainable design.
- Impact: Promotes the creation of eco-friendly products that are easier to recycle or have longer lifespans.
Enhanced Lifecycle Management:
- How: Digital Twins track the entire lifecycle of a product, from design to disposal, facilitating sustainable practices at each stage.
- Impact: Ensures that sustainability considerations are integrated throughout the product’s lifecycle, enhancing overall environmental responsibility.
Potential Challenges:
High Initial Investment:
- Challenge: Implementing Digital Twin Technology requires significant capital investment in software, hardware, and training.
- Impact: Can be a barrier for small to medium-sized enterprises (SMEs) aiming to adopt sustainable practices through Digital Twins.
Data Management Complexities:
- Challenge: Managing and processing the vast amounts of data generated by Digital Twins can be technically challenging.
- Impact: Requires robust data infrastructure and analytics capabilities to effectively leverage data for sustainability goals.
Integration with Existing Systems:
- Challenge: Seamlessly integrating Digital Twins with existing manufacturing systems and processes can be complex.
- Impact: May require substantial modifications to current workflows and systems, leading to potential disruptions during the transition period.
Cybersecurity Risks:
- Challenge: Increased connectivity and data sharing heighten the risk of cyberattacks and data breaches.
- Impact: Compromised data integrity can undermine sustainability efforts and lead to operational disruptions.
Skill Gaps:
- Challenge: Effective use of Digital Twins for sustainability requires specialized skills in data analytics, simulation, and system integration.
- Impact: May necessitate extensive training programs or hiring of skilled personnel, adding to implementation costs and time.
Scalability Issues:
- Challenge: Scaling Digital Twin solutions to cover entire manufacturing operations can be resource-intensive.
- Impact: Ensures that sustainability benefits are realized across all facets of production, not just isolated areas.
Conclusion: Digital Twin Technology holds immense potential to drive sustainability in manufacturing by optimizing resources, reducing waste, and enhancing energy efficiency. However, realizing these benefits requires overcoming challenges related to investment costs, data management, system integration, cybersecurity, and workforce skills. By addressing these challenges strategically, manufacturers can leverage Digital Twins to achieve significant advancements in sustainable manufacturing practices.
3. How does the use of Digital Twins enhance predictive maintenance strategies in manufacturing, and what are the long-term benefits of this enhancement?
Answer:
The use of Digital Twins enhances predictive maintenance strategies in manufacturing by providing a detailed and dynamic virtual representation of physical assets. This enables accurate monitoring, analysis, and prediction of equipment performance and maintenance needs, leading to numerous long-term benefits.
Concepts:
- Predictive Maintenance: Maintenance strategy that uses data-driven insights to predict and address equipment failures before they occur.
- Asset Health Monitoring: Continuous tracking of the condition and performance of equipment to assess its health status.
Enhancements to Predictive Maintenance:
Real-Time Monitoring:
- How: Digital Twins integrate data from sensors installed on physical assets to monitor their real-time performance and condition.
- Impact: Provides continuous insights into equipment health, enabling timely detection of anomalies and potential issues.
Data-Driven Analysis:
- How: Analyzes historical and real-time data to identify patterns and trends indicative of impending failures.
- Impact: Enhances the accuracy of failure predictions, reducing false positives and ensuring maintenance actions are timely and necessary.
Simulation and Scenario Testing:
- How: Digital Twins simulate various operational scenarios to assess how different conditions affect equipment performance.
- Impact: Helps in understanding the root causes of potential failures and in developing effective maintenance strategies.
Lifecycle Assessment:
- How: Tracks the entire lifecycle of equipment through its Digital Twin, from installation to end-of-life.
- Impact: Provides comprehensive insights into wear and tear patterns, enabling proactive maintenance scheduling and extending asset lifespan.
Automated Alerts and Notifications:
- How: Digital Twins can automatically trigger alerts when specific thresholds or conditions are met.
- Impact: Facilitates immediate action by maintenance teams, preventing minor issues from escalating into major failures.
Long-Term Benefits:
Reduced Downtime:
- Benefit: Minimizes unexpected equipment failures and unplanned downtime.
- Impact: Ensures continuous production, enhances productivity, and reduces the costs associated with lost production time.
Extended Equipment Lifespan:
- Benefit: Proactive maintenance extends the operational life of machinery and equipment.
- Impact: Lowers capital expenditure by delaying the need for equipment replacements and reducing depreciation costs.
Cost Savings:
- Benefit: Reduces maintenance costs by addressing issues before they require expensive repairs.
- Impact: Lowers overall operational expenses and improves the financial efficiency of manufacturing operations.
Improved Safety:
- Benefit: Prevents equipment malfunctions that could lead to accidents or hazardous conditions.
- Impact: Enhances workplace safety, reducing the risk of injuries and associated liabilities.
Enhanced Reliability and Quality:
- Benefit: Maintains equipment performance and reliability, ensuring consistent product quality.
- Impact: Increases customer satisfaction and reduces the costs related to product defects and rework.
Optimized Maintenance Resources:
- Benefit: Allocates maintenance resources more effectively based on actual equipment needs.
- Impact: Improves workforce efficiency and reduces the time and effort spent on unnecessary maintenance tasks.
Data-Driven Decision Making:
- Benefit: Provides comprehensive data and insights that inform strategic maintenance and operational decisions.
- Impact: Supports continuous improvement initiatives and fosters a culture of data-driven management.
Conclusion: Digital Twins significantly enhance predictive maintenance strategies by enabling accurate and proactive monitoring of equipment health. The long-term benefits include reduced downtime, extended equipment lifespan, cost savings, improved safety, enhanced reliability and quality, optimized maintenance resources, and data-driven decision making. These advantages contribute to more efficient, cost-effective, and reliable manufacturing operations, ultimately driving sustained business success.
4. In what ways can Digital Twin Technology influence the design and development of new products in manufacturing?
Answer:
Digital Twin Technology profoundly influences the design and development of new products in manufacturing by enabling a more iterative, data-driven, and collaborative approach. This technology allows designers and engineers to simulate, analyze, and refine product designs in a virtual environment before physical prototypes are built, enhancing innovation, reducing development time, and improving product quality.
Concepts:
- Iterative Design: A cyclic process of prototyping, testing, analyzing, and refining a product or process.
- Data-Driven Development: Using data and analytics to inform design decisions and optimize product performance.
Influence on Design and Development:
Virtual Prototyping:
- How: Create detailed virtual models of products using Digital Twins to test and evaluate design concepts.
- Impact: Reduces the need for multiple physical prototypes, lowering development costs and accelerating the design process.
Simulation and Testing:
- How: Use Digital Twins to simulate real-world conditions and test how products perform under various scenarios.
- Impact: Identifies potential design flaws and performance issues early, ensuring that products meet quality and reliability standards before production.
Performance Optimization:
- How: Analyze simulation data to optimize design parameters such as material selection, geometry, and structural integrity.
- Impact: Enhances product performance, durability, and cost-effectiveness by refining designs based on empirical data.
Collaborative Design:
- How: Facilitate collaboration among design, engineering, and manufacturing teams through shared Digital Twin models.
- Impact: Improves communication, ensures alignment of design and manufacturing objectives, and fosters a more cohesive product development process.
Customization and Personalization:
- How: Utilize Digital Twins to design and develop customized products tailored to specific customer needs.
- Impact: Enables mass customization without significant increases in production costs, enhancing customer satisfaction and market competitiveness.
Rapid Iteration and Innovation:
- How: Leverage the flexibility of Digital Twins to quickly iterate on design ideas and implement innovative features.
- Impact: Accelerates the pace of innovation, allowing manufacturers to respond swiftly to market trends and technological advancements.
Lifecycle Integration:
- How: Integrate Digital Twins throughout the product lifecycle, from initial design to end-of-life management.
- Impact: Ensures that sustainability considerations are incorporated into the design phase, promoting eco-friendly product development and lifecycle management.
Risk Mitigation:
- How: Use Digital Twins to assess the impact of design changes and identify potential risks before they manifest in physical prototypes.
- Impact: Reduces the likelihood of costly design revisions and project delays, ensuring a smoother product development journey.
Enhanced Documentation and Traceability:
- How: Maintain comprehensive records of design iterations, simulations, and testing results within the Digital Twin platform.
- Impact: Facilitates easier compliance with regulatory standards, improves traceability, and enhances the ability to conduct root cause analyses for design issues.
Cost Reduction:
- How: Minimize the number of physical prototypes and reduce material waste through virtual testing and optimization.
- Impact: Lowers overall product development costs and improves the return on investment for research and development activities.
Market Responsiveness:
- How: Quickly adapt product designs based on real-time feedback and market demand using Digital Twins.
- Impact: Enhances the ability to launch products that better meet customer needs and preferences, improving market success rates.
Integration with Advanced Technologies:
- How: Combine Digital Twins with other advanced technologies like AI, IoT, and machine learning to enhance design capabilities.
- Impact: Enables more intelligent and adaptive product designs that can evolve based on data-driven insights and real-world performance.
Conclusion: Digital Twin Technology significantly enhances the design and development of new products in manufacturing by enabling virtual prototyping, simulation, performance optimization, and collaborative innovation. This leads to faster development cycles, reduced costs, improved product quality, and greater responsiveness to market demands. By integrating Digital Twins into the product development process, manufacturers can foster a culture of continuous improvement and innovation, driving long-term success and competitiveness in the marketplace.
5. How can Digital Twin Technology be leveraged to enhance quality control in manufacturing processes?
Answer:
Digital Twin Technology can be leveraged to enhance quality control in manufacturing processes by providing continuous monitoring, real-time data analysis, and predictive insights that ensure products meet stringent quality standards consistently. This integration allows for proactive identification and resolution of quality issues, resulting in higher product reliability and customer satisfaction.
Concepts:
- Quality Control: The process of ensuring that products meet defined quality standards and specifications.
- Proactive Quality Management: Identifying and addressing quality issues before they affect the final product.
Enhancements to Quality Control:
Real-Time Monitoring:
- How: Digital Twins continuously monitor production parameters such as temperature, pressure, and machine performance.
- Impact: Enables immediate detection of deviations from quality standards, allowing for prompt corrective actions.
Data-Driven Analysis:
- How: Collect and analyze data from Digital Twins to identify patterns and trends related to product quality.
- Impact: Facilitates the identification of root causes of defects and informs strategies to prevent them.
Automated Inspection:
- How: Integrate automated inspection systems, such as computer vision and AI-powered sensors, with Digital Twins.
- Impact: Enhances the accuracy and consistency of quality inspections, reducing the likelihood of human error and ensuring uniform product quality.
Predictive Quality Assurance:
- How: Use predictive analytics within Digital Twins to forecast potential quality issues based on historical and real-time data.
- Impact: Allows manufacturers to implement preventive measures before defects occur, ensuring continuous quality assurance.
Simulation of Quality Scenarios:
- How: Simulate different production scenarios using Digital Twins to assess their impact on product quality.
- Impact: Identifies optimal manufacturing conditions that maximize quality, enabling informed adjustments to production processes.
Feedback Loops:
- How: Establish continuous feedback loops where quality data is fed back into the Digital Twin for ongoing process refinement.
- Impact: Promotes continuous improvement in manufacturing processes, enhancing overall product quality over time.
Standardization of Processes:
- How: Utilize Digital Twins to standardize manufacturing processes across different production lines and facilities.
- Impact: Ensures consistent quality by maintaining uniform process parameters and reducing variability.
Traceability and Documentation:
- How: Maintain detailed records of production parameters and quality assessments within the Digital Twin.
- Impact: Enhances traceability, simplifies compliance with quality standards, and facilitates root cause analysis in case of defects.
Training and Skill Development:
- How: Use Digital Twins to train quality control personnel by simulating various quality scenarios.
- Impact: Improves the ability of staff to identify and address quality issues effectively, enhancing overall quality control capabilities.
Integration with Supply Chain Quality Data:
- How: Connect Digital Twins with supply chain management systems to monitor the quality of incoming materials and components.
- Impact: Ensures that only high-quality materials are used in production, reducing the risk of defects and enhancing the quality of final products.
Enhanced Customer Feedback Integration:
- How: Incorporate customer feedback data into Digital Twins to identify and address quality issues related to product usage.
- Impact: Aligns manufacturing processes with customer expectations, improving product satisfaction and reducing returns or complaints.
Advanced Quality Metrics and KPIs:
- How: Define and monitor advanced quality metrics within Digital Twins to track performance and identify areas for improvement.
- Impact: Provides a comprehensive view of quality performance, enabling data-driven decisions to enhance quality control practices.
Conclusion: Digital Twin Technology significantly enhances quality control in manufacturing by enabling real-time monitoring, data-driven analysis, predictive insights, and continuous improvement. By leveraging these capabilities, manufacturers can ensure consistent product quality, reduce defects, and meet or exceed customer expectations. This leads to increased reliability, higher customer satisfaction, and a stronger competitive position in the market.
6. What are the potential ethical considerations associated with the deployment of Digital Twin Technology in manufacturing?
Answer:
The deployment of Digital Twin Technology in manufacturing brings several ethical considerations that manufacturers must address to ensure responsible and sustainable use. These considerations encompass data privacy, security, job displacement, environmental impact, and the ethical use of AI and automation.
Concepts:
- Ethical Considerations: Moral principles that govern the use and implementation of technology.
- Sustainable Use: Ensuring that technology benefits society and the environment without causing harm.
Ethical Considerations:
Data Privacy and Security:
- Consideration: Digital Twins rely on extensive data collection from manufacturing processes, raising concerns about the privacy and security of this data.
- Implications: Unauthorized access or data breaches can lead to intellectual property theft, competitive disadvantages, and privacy violations.
- Ethical Approach: Implement robust cybersecurity measures, ensure compliance with data protection regulations, and maintain transparency about data usage.
Job Displacement and Workforce Impact:
- Consideration: Automation and optimization through Digital Twins may reduce the need for certain manual or repetitive jobs.
- Implications: Potential unemployment or job displacement for workers, leading to social and economic challenges.
- Ethical Approach: Invest in workforce retraining and upskilling programs, promote job creation in technology management and maintenance, and ensure fair transition support for affected employees.
Bias in AI and Machine Learning Algorithms:
- Consideration: AI-driven aspects of Digital Twins may inadvertently incorporate biases present in training data or design.
- Implications: Can lead to unfair decision-making, inconsistent quality control, and unequal treatment of different processes or products.
- Ethical Approach: Ensure diverse and representative data sets, regularly audit AI algorithms for biases, and implement fairness and accountability frameworks.
Environmental Impact:
- Consideration: While Digital Twins can enhance sustainability, their deployment also requires significant energy and resource consumption, particularly in data centers.
- Implications: Potential increase in carbon footprint and environmental degradation if not managed sustainably.
- Ethical Approach: Adopt energy-efficient technologies, utilize renewable energy sources, and design Digital Twins with sustainability in mind to minimize environmental impact.
Transparency and Accountability:
- Consideration: The complex nature of Digital Twins can obscure decision-making processes and accountability in manufacturing operations.
- Implications: Difficulty in tracing errors, responsibility for failures, and understanding automated decisions.
- Ethical Approach: Maintain clear documentation of Digital Twin models and decision-making algorithms, ensure traceability of actions, and establish accountability protocols.
Intellectual Property Rights:
- Consideration: Digital Twins can replicate proprietary manufacturing processes and designs, raising concerns about intellectual property theft.
- Implications: Potential loss of competitive advantage and legal disputes over intellectual property rights.
- Ethical Approach: Implement strict access controls, use encryption to protect sensitive data, and establish legal frameworks to safeguard intellectual property.
Consent and Stakeholder Inclusion:
- Consideration: Employees and stakeholders may not be fully informed or consent to the implementation of Digital Twins that monitor their work environments.
- Implications: Can lead to mistrust, reduced morale, and ethical conflicts over surveillance and monitoring.
- Ethical Approach: Engage stakeholders in the decision-making process, provide clear communication about the purpose and benefits of Digital Twins, and obtain informed consent where necessary.
Dependence on Technology:
- Consideration: Over-reliance on Digital Twins may reduce human oversight and critical thinking in manufacturing operations.
- Implications: Increased vulnerability to technological failures, reduced problem-solving skills, and potential neglect of human judgment.
- Ethical Approach: Maintain a balance between automation and human oversight, ensure that critical decisions involve human input, and foster a culture of continuous learning and adaptability.
Accessibility and Inclusivity:
- Consideration: Access to Digital Twin Technology may be limited to larger organizations, exacerbating inequalities in the manufacturing sector.
- Implications: Smaller businesses may struggle to compete, leading to market consolidation and reduced diversity.
- Ethical Approach: Promote affordable and scalable Digital Twin solutions, support initiatives that make advanced technologies accessible to all sizes of businesses, and encourage inclusive innovation.
Regulatory Compliance:
- Consideration: Rapid advancements in Digital Twin Technology may outpace existing regulatory frameworks, leading to gaps in governance.
- Implications: Potential for misuse, lack of standardized practices, and legal uncertainties.
- Ethical Approach: Collaborate with regulatory bodies to develop comprehensive guidelines, adhere to industry standards, and proactively engage in shaping future regulations.
Conclusion: While Digital Twin Technology offers substantial benefits for manufacturing, it also presents a range of ethical considerations that must be carefully managed. By addressing issues related to data privacy, job displacement, AI bias, environmental impact, transparency, intellectual property, stakeholder consent, technological dependence, accessibility, and regulatory compliance, manufacturers can ensure that the deployment of Digital Twins is both responsible and sustainable. Ethical stewardship in the implementation of Digital Twin Technology fosters trust, promotes fairness, and supports long-term success in the manufacturing sector.
7. How can Digital Twin Technology facilitate innovation in manufacturing processes, and what are the potential outcomes of such innovation?
Answer:
Digital Twin Technology facilitates innovation in manufacturing processes by providing a comprehensive and interactive platform for experimentation, simulation, and optimization. This fosters a culture of continuous improvement and allows manufacturers to explore new ideas, implement advanced technologies, and develop novel production methods, leading to significant advancements and competitive advantages.
Concepts:
- Innovation: The introduction of new ideas, methods, or products that add value.
- Continuous Improvement: Ongoing efforts to enhance products, services, or processes.
Facilitation of Innovation:
Virtual Experimentation:
- How: Digital Twins allow manufacturers to test new ideas and modifications in a virtual environment before implementing them in the physical world.
- Impact: Reduces the risk and cost associated with experimentation, enabling more frequent and diverse innovations.
Process Optimization:
- How: Use simulations to identify inefficiencies and optimize production processes for better performance.
- Impact: Enhances productivity, reduces waste, and lowers operational costs, freeing up resources for further innovation.
Integration of Advanced Technologies:
- How: Incorporate emerging technologies such as AI, machine learning, and IoT into Digital Twins to enhance their capabilities.
- Impact: Enables the development of smarter, more adaptive manufacturing systems that can respond dynamically to changing conditions and requirements.
Collaborative Design and Development:
- How: Facilitate collaboration among cross-functional teams through shared Digital Twin models, allowing for integrated design and development efforts.
- Impact: Promotes the exchange of ideas, accelerates the design process, and leads to more innovative and well-rounded product designs.
Rapid Prototyping and Iteration:
- How: Use Digital Twins to create and refine prototypes quickly through virtual testing and feedback.
- Impact: Speeds up the product development cycle, allowing for rapid iteration and faster time-to-market for innovative products.
Predictive Insights for Future Innovations:
- How: Analyze data from Digital Twins to identify trends and forecast future manufacturing needs and opportunities.
- Impact: Informs strategic planning and fosters forward-thinking innovations that anticipate market and technological advancements.
Sustainable Manufacturing Innovations:
- How: Simulate and optimize environmentally friendly production methods and sustainable product designs using Digital Twins.
- Impact: Promotes the development of eco-friendly manufacturing processes and products, enhancing sustainability and meeting regulatory and consumer demands.
Potential Outcomes of Innovation:
Increased Competitiveness:
- Outcome: Adoption of innovative manufacturing processes leads to higher quality products, lower costs, and faster production times.
- Impact: Strengthens the manufacturer’s position in the market, attracting more customers and expanding market share.
Enhanced Product Quality and Performance:
- Outcome: Continuous optimization and innovation improve the overall quality and performance of products.
- Impact: Increases customer satisfaction, reduces returns and defects, and enhances brand reputation.
Cost Reduction and Efficiency Gains:
- Outcome: Optimized processes and resource utilization lower production costs.
- Impact: Increases profitability and allows for reinvestment in further innovation and growth initiatives.
Faster Time-to-Market:
- Outcome: Rapid prototyping and iterative design enable quicker product development cycles.
- Impact: Allows manufacturers to respond swiftly to market trends and demands, capturing new opportunities ahead of competitors.
Sustainability and Environmental Responsibility:
- Outcome: Innovative, sustainable manufacturing practices reduce environmental impact.
- Impact: Aligns with global sustainability goals, enhances corporate social responsibility, and meets regulatory requirements.
New Business Models and Revenue Streams:
- Outcome: Innovation can lead to the development of new products, services, or business models.
- Impact: Diversifies revenue streams, reduces dependency on existing products, and opens up new markets.
Improved Workforce Skills and Engagement:
- Outcome: Engaging in innovative projects enhances employee skills and fosters a culture of creativity and problem-solving.
- Impact: Increases employee satisfaction, reduces turnover, and attracts top talent.
Conclusion: Digital Twin Technology serves as a catalyst for innovation in manufacturing by enabling virtual experimentation, process optimization, and the integration of advanced technologies. The potential outcomes of such innovation include increased competitiveness, enhanced product quality, cost reductions, faster time-to-market, sustainability, new business opportunities, and a more skilled and engaged workforce. By leveraging Digital Twins for innovation, manufacturers can drive continuous improvement, adapt to evolving market demands, and achieve long-term success in a dynamic industrial landscape.
8. How can Digital Twin Technology be integrated with Industry 4.0 initiatives to create a smart manufacturing ecosystem?
Answer:
Digital Twin Technology is a cornerstone of Industry 4.0, which emphasizes the integration of digital technologies to create intelligent, interconnected, and highly efficient manufacturing ecosystems. Integrating Digital Twin Technology with other Industry 4.0 initiatives fosters a smart manufacturing environment that leverages data, automation, and connectivity to drive innovation, efficiency, and flexibility.
Concepts:
- Industry 4.0: The fourth industrial revolution characterized by the use of smart technologies, IoT, and data analytics to create interconnected manufacturing systems.
- Smart Manufacturing: An approach that uses advanced technologies to enhance manufacturing processes, making them more adaptable, efficient, and responsive.
Integration with Industry 4.0 Initiatives:
Internet of Things (IoT) Integration:
- How: Connect IoT devices and sensors to Digital Twins to enable real-time data collection and monitoring.
- Impact: Enhances the capability of Digital Twins to provide accurate and up-to-date representations of physical assets and processes.
Artificial Intelligence (AI) and Machine Learning (ML):
- How: Incorporate AI and ML algorithms into Digital Twins for advanced data analysis, predictive analytics, and autonomous decision-making.
- Impact: Enables smarter automation, optimized processes, and improved predictive maintenance within the smart manufacturing ecosystem.
Cloud Computing:
- How: Utilize cloud platforms to store, process, and manage the vast amounts of data generated by Digital Twins and other Industry 4.0 technologies.
- Impact: Provides scalability, flexibility, and remote accessibility, supporting the seamless integration and operation of smart manufacturing systems.
Cyber-Physical Systems (CPS):
- How: Integrate Digital Twins with CPS to create a tightly coupled interaction between physical manufacturing systems and their digital counterparts.
- Impact: Facilitates real-time control and coordination, enhancing the responsiveness and adaptability of manufacturing operations.
Advanced Robotics and Automation:
- How: Link Digital Twins with advanced robotics to enable precise control and coordination of automated manufacturing tasks.
- Impact: Improves production accuracy, efficiency, and flexibility, allowing for dynamic adjustments based on real-time data.
Big Data and Analytics:
- How: Leverage Big Data analytics tools to process and analyze the extensive data streams from Digital Twins and other connected systems.
- Impact: Provides actionable insights for continuous improvement, strategic planning, and operational optimization within the smart manufacturing ecosystem.
Augmented Reality (AR) and Virtual Reality (VR):
- How: Use AR and VR technologies in conjunction with Digital Twins for enhanced visualization, training, and maintenance.
- Impact: Enhances human-machine interaction, improves training effectiveness, and facilitates remote maintenance and support.
Supply Chain Integration:
- How: Connect Digital Twins with supply chain management systems to synchronize manufacturing processes with supply chain activities.
- Impact: Enhances supply chain visibility, coordination, and responsiveness, ensuring that production aligns with material availability and demand forecasts.
Edge Computing:
- How: Implement edge computing to process data locally at the manufacturing site, reducing latency and improving real-time decision-making.
- Impact: Enhances the performance and responsiveness of Digital Twins, enabling more efficient and timely process optimizations.
Standardization and Interoperability:
- How: Adopt standardized protocols and interfaces to ensure seamless communication between Digital Twins and other Industry 4.0 technologies.
- Impact: Promotes interoperability, facilitating the integration of diverse systems and technologies into a cohesive smart manufacturing ecosystem.
Security and Privacy Measures:
- How: Implement robust cybersecurity measures to protect the data and interactions between Digital Twins and other connected systems.
- Impact: Ensures the integrity, confidentiality, and reliability of the smart manufacturing ecosystem, safeguarding against cyber threats and data breaches.
Continuous Learning and Adaptation:
- How: Utilize feedback from Digital Twins to continuously learn and adapt manufacturing processes based on performance data and changing conditions.
- Impact: Supports a culture of continuous improvement and innovation, ensuring that the smart manufacturing ecosystem evolves with technological advancements and market demands.
Potential Outcomes of Integration:
- Enhanced Efficiency: Streamlined processes and optimized resource utilization lead to higher productivity and lower operational costs.
- Greater Flexibility: Ability to quickly adapt to changes in demand, product specifications, and production conditions.
- Improved Quality: Consistent monitoring and real-time adjustments ensure high product quality and reduced defect rates.
- Faster Time-to-Market: Accelerated design, testing, and production cycles enable quicker product launches.
- Sustainability: Optimized processes and reduced waste contribute to more sustainable manufacturing practices.
- Increased Innovation: Enhanced data insights and simulation capabilities foster continuous innovation and development of advanced manufacturing solutions.
Conclusion: Integrating Digital Twin Technology with Industry 4.0 initiatives creates a smart manufacturing ecosystem that is highly efficient, flexible, and responsive. This integration leverages interconnected systems, advanced analytics, and automation to drive continuous improvement, innovation, and sustainability in manufacturing operations. By embracing these technologies synergistically, manufacturers can achieve significant competitive advantages and meet the evolving demands of the modern industrial landscape.
9. What role do Digital Twins play in facilitating collaboration between different departments within a manufacturing organization?
Answer:
Digital Twins play a pivotal role in facilitating collaboration between different departments within a manufacturing organization by serving as a unified platform that integrates data, processes, and communication. This integration enhances cross-functional teamwork, improves information sharing, and fosters a collaborative environment that drives efficiency and innovation.
Concepts:
- Cross-Functional Collaboration: Cooperation among different departments to achieve common organizational goals.
- Unified Platform: A single system or framework that brings together various functions and data sources.
Facilitation of Collaboration:
Centralized Data Repository:
- How: Digital Twins aggregate data from various departments such as engineering, production, maintenance, and quality control.
- Impact: Provides all departments with access to consistent and up-to-date information, reducing data silos and enhancing informed decision-making.
Enhanced Communication:
- How: Digital Twins offer visualization tools and dashboards that present data in an accessible and understandable format.
- Impact: Improves communication between departments by providing clear insights into processes and performance, facilitating better coordination and alignment.
Integrated Workflow Processes:
- How: Digital Twins link different manufacturing workflows, ensuring that changes in one department automatically reflect across others.
- Impact: Streamlines operations, reduces redundancies, and ensures that all departments are synchronized in their activities, enhancing overall efficiency.
Collaborative Problem Solving:
- How: Departments can use Digital Twins to collaboratively analyze issues, simulate solutions, and implement improvements.
- Impact: Promotes collective problem-solving, leveraging the expertise of different departments to address challenges more effectively and innovatively.
Shared Goals and Objectives:
- How: Digital Twins align the objectives of different departments by providing a comprehensive view of the manufacturing process.
- Impact: Ensures that all departments are working towards common goals, enhancing organizational coherence and strategic alignment.
Real-Time Feedback and Iteration:
- How: Digital Twins enable real-time feedback on process performance and product quality, allowing departments to make immediate adjustments.
- Impact: Facilitates continuous improvement and agile responses to changing conditions, fostering a dynamic and responsive manufacturing environment.
Training and Development:
- How: Use Digital Twins for joint training sessions and simulations that involve multiple departments.
- Impact: Enhances interdepartmental understanding and cooperation, ensuring that teams are well-prepared to work together effectively.
Resource Sharing and Optimization:
- How: Digital Twins provide insights into resource utilization across departments, enabling better allocation and sharing of resources.
- Impact: Maximizes the efficiency of resource use, reduces waste, and ensures that all departments have the necessary tools and materials to perform their tasks.
Innovation and R&D Collaboration:
- How: Research and Development (R&D) teams can use Digital Twins to prototype and test new ideas collaboratively with production and engineering departments.
- Impact: Accelerates the innovation process, ensures that new designs are manufacturable, and integrates R&D efforts with practical manufacturing considerations.
Performance Tracking and Reporting:
- How: Digital Twins enable comprehensive performance tracking across all departments, providing detailed reports and analytics.
- Impact: Enhances accountability, allows for benchmarking and performance comparisons, and supports data-driven improvements across the organization.
Benefits of Facilitated Collaboration:
- Increased Efficiency: Streamlined communication and integrated workflows reduce delays and enhance productivity.
- Higher Quality Products: Collaborative problem-solving and continuous feedback ensure that quality standards are consistently met.
- Faster Innovation: Joint efforts in design, testing, and optimization accelerate the development of new and improved products.
- Enhanced Agility: Ability to respond swiftly to changes and challenges through real-time data and coordinated actions.
- Improved Employee Morale: A collaborative environment fosters teamwork, reduces silos, and enhances job satisfaction.
Conclusion: Digital Twin Technology serves as a central hub that connects different departments within a manufacturing organization, promoting seamless collaboration, effective communication, and integrated workflows. By providing a unified and interactive platform for data sharing, problem-solving, and process optimization, Digital Twins enhance cross-functional teamwork, drive innovation, and improve overall operational efficiency. This collaborative synergy is essential for achieving organizational goals, maintaining competitiveness, and fostering a culture of continuous improvement in modern manufacturing environments.
10. How can Digital Twin Technology be utilized to improve supply chain transparency and traceability in manufacturing?
Answer:
Digital Twin Technology can be utilized to improve supply chain transparency and traceability in manufacturing by providing a detailed, real-time digital representation of the entire supply chain network. This enables manufacturers to monitor, track, and analyze every stage of the supply chain, from raw material procurement to final product delivery, ensuring greater visibility, accountability, and efficiency.
Concepts:
- Supply Chain Transparency: The extent to which all parties in the supply chain have visibility into processes, data, and operations.
- Traceability: The ability to track and verify the history, application, or location of products and materials within the supply chain.
Utilization Methods:
End-to-End Visibility:
- How: Digital Twins create a comprehensive digital model of the entire supply chain, integrating data from suppliers, manufacturers, logistics providers, and distributors.
- Impact: Provides real-time visibility into the status and movement of materials and products, enabling proactive management of supply chain activities.
Real-Time Tracking:
- How: Implement IoT sensors and GPS tracking devices on shipments and materials to feed real-time data into the Digital Twin.
- Impact: Allows for precise tracking of goods as they move through the supply chain, reducing the risk of loss, theft, or delays.
Inventory Management:
- How: Use Digital Twins to monitor inventory levels across different locations and predict future inventory needs based on production schedules and demand forecasts.
- Impact: Optimizes inventory levels, minimizes stockouts and overstock situations, and ensures that materials are available when needed.
Quality Control and Compliance:
- How: Track and document quality inspections and compliance checks throughout the supply chain within the Digital Twin.
- Impact: Ensures that all materials and products meet quality standards and regulatory requirements, enhancing product integrity and consumer trust.
Risk Management:
- How: Utilize Digital Twins to simulate and assess potential supply chain disruptions, such as supplier failures, natural disasters, or geopolitical events.
- Impact: Enables manufacturers to develop contingency plans, diversify suppliers, and enhance the resilience of the supply chain against unforeseen risks.
Supplier Performance Monitoring:
- How: Track key performance indicators (KPIs) of suppliers, such as delivery times, quality metrics, and reliability, within the Digital Twin.
- Impact: Facilitates informed decision-making regarding supplier selection, retention, and improvement, ensuring a reliable and high-quality supply base.
Sustainability and Ethical Sourcing:
- How: Monitor the environmental and social practices of suppliers through data integrated into the Digital Twin.
- Impact: Ensures that materials are sourced sustainably and ethically, aligning with corporate social responsibility goals and consumer expectations.
Data-Driven Decision Making:
- How: Analyze data from the Digital Twin to gain insights into supply chain performance, identify inefficiencies, and optimize processes.
- Impact: Supports strategic planning, enhances operational efficiency, and drives continuous improvement in supply chain management.
Blockchain Integration:
- How: Combine Digital Twin Technology with blockchain to ensure secure, immutable records of transactions and movements within the supply chain.
- Impact: Enhances traceability, prevents fraud, and builds trust among supply chain partners by providing transparent and verifiable data.
Automated Reporting and Documentation:
- How: Generate automated reports and documentation based on real-time data from the Digital Twin for compliance, auditing, and reporting purposes.
- Impact: Simplifies regulatory compliance, reduces manual documentation efforts, and ensures accurate and up-to-date records of supply chain activities.
Collaboration and Communication:
- How: Facilitate seamless communication and data sharing between all stakeholders in the supply chain through the Digital Twin platform.
- Impact: Enhances collaboration, ensures alignment of objectives, and promotes a more coordinated and efficient supply chain network.
Lifecycle Traceability:
- How: Track the entire lifecycle of products from raw material extraction to end-of-life disposal within the Digital Twin.
- Impact: Provides comprehensive traceability, enabling manufacturers to analyze the environmental and economic impacts of their products and implement sustainable practices throughout the product lifecycle.
Benefits of Enhanced Supply Chain Transparency and Traceability:
- Improved Efficiency: Streamlined operations and reduced bottlenecks lead to faster and more efficient supply chain processes.
- Enhanced Customer Trust: Transparent and traceable supply chains build trust with customers by ensuring product authenticity and quality.
- Better Compliance: Ensures adherence to regulatory standards and industry certifications, reducing the risk of legal issues and penalties.
- Increased Agility: Ability to quickly respond to supply chain disruptions and changes in demand enhances overall supply chain agility.
- Cost Savings: Optimized inventory management and reduced waste contribute to significant cost savings across the supply chain.
- Sustainability: Promotes sustainable and ethical sourcing practices, aligning with corporate social responsibility and environmental goals.
Conclusion: Digital Twin Technology plays a crucial role in enhancing supply chain transparency and traceability in manufacturing by providing comprehensive, real-time insights and facilitating seamless integration and coordination across all supply chain activities. This leads to improved efficiency, reduced risks, enhanced quality control, and greater sustainability, ultimately strengthening the overall resilience and competitiveness of manufacturing organizations.
11. How can Digital Twin Technology support continuous improvement and lean manufacturing principles in a production environment?
Answer:
Digital Twin Technology supports continuous improvement and lean manufacturing principles in a production environment by providing detailed, real-time insights into manufacturing processes, enabling the identification and elimination of waste, optimizing workflows, and fostering a culture of data-driven decision-making. This alignment enhances operational efficiency, reduces costs, and promotes sustained quality and productivity improvements.
Concepts:
- Continuous Improvement (Kaizen): Ongoing efforts to improve products, services, or processes incrementally.
- Lean Manufacturing: A methodology focused on minimizing waste without sacrificing productivity, emphasizing value creation for the customer.
Support for Continuous Improvement and Lean Principles:
Real-Time Data Monitoring:
- How: Digital Twins continuously collect and analyze data from production processes.
- Impact: Provides immediate visibility into process performance, enabling quick identification of inefficiencies and areas for improvement.
Waste Identification and Elimination:
- How: Analyze data to pinpoint sources of waste, such as excess inventory, overproduction, waiting times, and defects.
- Impact: Facilitates targeted efforts to eliminate waste, aligning with lean principles to enhance operational efficiency.
Process Optimization:
- How: Use simulations and data analysis within Digital Twins to optimize manufacturing processes for maximum efficiency.
- Impact: Reduces cycle times, lowers operational costs, and increases throughput, supporting lean manufacturing objectives.
Standardization of Best Practices:
- How: Identify and codify optimal process parameters and workflows using insights from Digital Twins.
- Impact: Ensures consistency and reliability across production lines, reducing variability and enhancing product quality.
Predictive Analytics for Continuous Improvement:
- How: Leverage predictive analytics to forecast process performance and identify potential improvements before issues arise.
- Impact: Enables proactive adjustments and refinements to manufacturing processes, fostering a culture of continuous improvement.
Enhanced Quality Control:
- How: Utilize Digital Twins to monitor quality metrics in real-time and implement immediate corrective actions when deviations are detected.
- Impact: Maintains high quality standards, reduces defect rates, and ensures that products meet customer expectations consistently.
Visual Management and Transparency:
- How: Provide dashboards and visualization tools that display key performance indicators (KPIs) and process metrics.
- Impact: Enhances transparency, engages employees in the improvement process, and facilitates data-driven decision-making.
Root Cause Analysis:
- How: Use data from Digital Twins to conduct detailed root cause analysis of process inefficiencies and quality issues.
- Impact: Identifies underlying causes of problems, enabling effective solutions that prevent recurrence and support lean practices.
Flexible and Adaptive Production Lines:
- How: Digital Twins enable quick adjustments to production lines based on real-time data and insights.
- Impact: Enhances the flexibility and adaptability of manufacturing operations, allowing for rapid responses to changing demands and continuous optimization.
Employee Empowerment and Engagement:
- How: Provide employees with access to real-time data and insights through Digital Twins, empowering them to identify and implement improvements.
- Impact: Encourages a proactive and engaged workforce, fostering a culture of continuous improvement and innovation.
Benchmarking and Performance Tracking:
- How: Use Digital Twins to benchmark performance against industry standards and track progress over time.
- Impact: Facilitates the setting of realistic improvement goals and measures the effectiveness of continuous improvement initiatives.
Integration with Lean Tools and Techniques:
- How: Combine Digital Twins with lean tools such as Value Stream Mapping (VSM), 5S, and Just-In-Time (JIT) production.
- Impact: Enhances the effectiveness of lean methodologies by providing data-driven support for process mapping, organization, and production scheduling.
Benefits of Supporting Continuous Improvement and Lean Manufacturing:
- Increased Efficiency: Streamlined processes and reduced waste lead to higher operational efficiency and productivity.
- Cost Reduction: Minimizing waste and optimizing resource utilization result in significant cost savings.
- Enhanced Quality: Consistent monitoring and quality control ensure high product standards, reducing defects and rework.
- Greater Agility: Ability to quickly adapt to changes and implement improvements fosters a more agile and responsive manufacturing environment.
- Employee Satisfaction: Empowered and engaged employees contribute to a positive work culture and higher job satisfaction.
- Sustainable Growth: Continuous improvement and lean practices support long-term operational sustainability and business growth.
Conclusion: Digital Twin Technology is a powerful enabler of continuous improvement and lean manufacturing principles in production environments. By providing real-time data, facilitating process optimization, and promoting a culture of data-driven decision-making, Digital Twins help manufacturers eliminate waste, enhance quality, and achieve greater operational efficiency. This alignment not only drives immediate improvements but also supports sustained growth and competitiveness in the dynamic manufacturing landscape.
12. What future advancements in Digital Twin Technology can further revolutionize manufacturing, and how might these advancements impact the industry?
Answer:
Future advancements in Digital Twin Technology hold the potential to further revolutionize manufacturing by enhancing simulation accuracy, integrating more advanced AI and machine learning capabilities, improving interoperability, and expanding applications beyond current boundaries. These advancements will significantly impact the industry by driving innovation, increasing efficiency, and enabling more sophisticated and responsive manufacturing ecosystems.
Concepts:
- Technological Evolution: Ongoing developments that enhance the capabilities and applications of existing technologies.
- Industry Transformation: Fundamental changes in how industries operate, driven by technological innovations.
Future Advancements:
Enhanced Real-Time Data Processing:
- Advancement: Development of more efficient data processing algorithms and edge computing solutions.
- Impact: Enables faster and more accurate real-time updates to Digital Twins, improving responsiveness and decision-making in dynamic manufacturing environments.
Advanced AI and Machine Learning Integration:
- Advancement: Incorporation of more sophisticated AI and machine learning models into Digital Twins for deeper insights and autonomous optimization.
- Impact: Facilitates smarter automation, predictive analytics, and autonomous decision-making, leading to more efficient and self-optimizing manufacturing processes.
Interoperability and Standardization:
- Advancement: Establishment of industry-wide standards and protocols for Digital Twin interoperability.
- Impact: Promotes seamless integration of Digital Twins across different systems and platforms, enhancing collaboration and data sharing within and between organizations.
Augmented Reality (AR) and Virtual Reality (VR) Enhancements:
- Advancement: Advanced AR and VR integrations with Digital Twins for immersive visualization and interaction.
- Impact: Improves training, maintenance, and design collaboration by providing more intuitive and interactive ways to engage with Digital Twins.
Multi-Scale Digital Twins:
- Advancement: Development of Digital Twins that operate at multiple scales, from individual components to entire manufacturing systems.
- Impact: Enables comprehensive analysis and optimization across all levels of the manufacturing process, enhancing overall system performance and efficiency.
Blockchain Integration:
- Advancement: Combining Digital Twins with blockchain technology for secure and transparent data management.
- Impact: Enhances data integrity, traceability, and security, building greater trust and accountability within manufacturing and supply chain operations.
Bi-Directional Integration:
- Advancement: Enabling seamless two-way data flow between physical assets and their Digital Twins.
- Impact: Ensures that updates and changes in the physical world are instantly reflected in the Digital Twin and vice versa, improving synchronization and operational accuracy.
Self-Healing and Adaptive Systems:
- Advancement: Incorporation of self-healing and adaptive capabilities within Digital Twins to autonomously address issues and optimize processes.
- Impact: Reduces the need for manual intervention, enhances system reliability, and ensures continuous operational efficiency.
Integration with Circular Economy Models:
- Advancement: Utilizing Digital Twins to support circular economy principles by tracking product lifecycles and enabling recycling and reuse.
- Impact: Promotes sustainable manufacturing practices, reduces environmental impact, and aligns with global sustainability goals.
Human-Machine Collaboration:
- Advancement: Enhancing interfaces and interactions between humans and Digital Twins to support collaborative decision-making and control.
- Impact: Improves the effectiveness of human-machine teams, leveraging the strengths of both humans and automated systems for better manufacturing outcomes.
Advanced Simulation Capabilities:
- Advancement: Development of more accurate and comprehensive simulation models that incorporate complex variables and scenarios.
- Impact: Enhances the predictive power of Digital Twins, allowing for more precise forecasting, planning, and optimization in manufacturing processes.
Universal Digital Twin Platforms:
- Advancement: Creation of universal Digital Twin platforms that can be easily customized and adapted to various industries and applications.
- Impact: Increases the accessibility and applicability of Digital Twin Technology, enabling broader adoption across diverse manufacturing sectors and driving industry-wide advancements.
Potential Impacts on the Manufacturing Industry:
- Increased Efficiency and Productivity: Advanced Digital Twins enable more precise and optimized manufacturing processes, leading to higher productivity and lower operational costs.
- Greater Flexibility and Agility: Enhanced adaptability and real-time responsiveness allow manufacturers to quickly pivot and adapt to market changes and technological advancements.
- Enhanced Innovation: More sophisticated simulation and optimization capabilities foster a culture of innovation, enabling the development of cutting-edge products and manufacturing techniques.
- Improved Sustainability: Integration with circular economy models and sustainable practices supports environmentally responsible manufacturing, aligning with global sustainability initiatives.
- Strengthened Competitiveness: Manufacturers leveraging advanced Digital Twins can achieve a significant competitive edge through superior efficiency, quality, and innovation.
- Enhanced Collaboration and Integration: Improved interoperability and collaborative tools facilitate better integration and cooperation within and between organizations, driving collective advancements.
- Greater Data Security and Integrity: Blockchain and advanced cybersecurity measures ensure that data managed by Digital Twins is secure, reliable, and trustworthy, protecting intellectual property and operational integrity.
- Workforce Transformation: Advanced Digital Twins drive the need for more skilled and technologically proficient workers, promoting workforce development and enhancing employee capabilities.
Conclusion: Future advancements in Digital Twin Technology promise to further revolutionize the manufacturing industry by enhancing real-time data processing, integrating advanced AI, improving interoperability, and expanding the applications of Digital Twins. These innovations will lead to increased efficiency, greater flexibility, enhanced sustainability, and sustained competitive advantage for manufacturers. By embracing these future developments, the manufacturing industry can continue to evolve, driving continuous improvement and innovation in an increasingly dynamic and technology-driven landscape.
Conclusion:
The above thought-provoking questions and detailed answers delve into the multifaceted aspects of Digital Twin Technology in manufacturing. Covering transformative workflows, sustainability, predictive maintenance, innovation, quality control, ethical considerations, Industry 4.0 integration, cross-departmental collaboration, supply chain transparency, continuous improvement, and future advancements, these questions encourage students to explore the complexities and transformative potential of Digital Twins. By engaging with these inquiries, students are prompted to think critically about how Digital Twin Technology can drive efficiency, innovation, and sustainability in modern manufacturing environments. This comprehensive exploration fosters a deeper understanding of Digital Twins’ role in shaping the future of manufacturing, promoting both technological proficiency and strategic thinking in industrial operations.