Advanced Materials and Manufacturing Technologies
The rise of Advanced Materials and Manufacturing Technologies has dramatically reshaped the way industries innovate, produce, and deliver value. These technologies are foundational to modern Industrial and Manufacturing Technologies, supporting the transition from conventional processes to advanced, data-driven, and sustainable systems. As materials science continues to uncover novel composites, smart alloys, and nano-structured surfaces, engineers are increasingly able to meet performance demands that were once unattainable.
These materials find synergistic applications through cutting-edge processes like Additive Manufacturing (3D Printing), which allow for rapid prototyping and complex geometries. They are further integrated into Computer-Integrated Manufacturing (CIM) systems and real-time simulations enabled by Digital Twin Technology, driving manufacturing efficiency and precision.
Sustainability is at the forefront of modern production, and innovative materials support Energy and Resource Efficiency in Manufacturing. Their use reduces material wastage, enhances product lifespan, and minimizes environmental impact, thereby aligning well with Sustainable Manufacturing principles. The role of ergonomics and human-centered design is also critical, as seen in Human Factors and Ergonomics in Manufacturing, where the application of light, durable materials improves usability and safety.
In a rapidly transforming industrial ecosystem, these advanced technologies are embedded within systems of Industrial Automation and Robotics and Smart Manufacturing and Industry 4.0, forming a responsive, adaptable production environment. The integration of materials into intelligent workflows demands rigorous Manufacturing Quality Control and Assurance and optimal Manufacturing Process Design and Optimization to meet exacting industry standards.
Advanced materials contribute significantly to sectors like Mechanical Engineering, including domains such as Automotive Engineering, where they enable fuel-efficient, high-performance vehicle components. Their biomedical applications are explored in Biomechanical Engineering, while intelligent integration into actuators and end-effectors enhances Robotics and Automation in Mech Eng.
The role of simulation and automation requires a strong understanding of foundational areas like Control Systems in Mech Engineering, and fluid-structure interactions studied in Fluid Mechanics and Hydraulics. Material behavior under different loading conditions is critically examined through Solid Mechanics in Mechanical Engineering and heat response patterns addressed in Thermodynamics and Heat Transfer.
Design practices benefit from incorporating these new materials in digital workflows enabled by Mechanical Design and Computer-Aided Design (CAD). For those working in production environments, understanding Manufacturing and Production Engineering principles allows the effective translation of material capabilities into tangible products.
Supporting logistics and global operations, Supply Chain Management strategies must adapt to the unique sourcing, handling, and compliance needs of high-performance materials. Ultimately, the evolution of materials science stands as a cornerstone of 21st-century manufacturing, guiding engineers toward more intelligent, resilient, and responsible solutions.
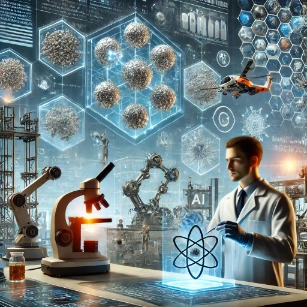
Table of Contents
Core Concepts of Advanced Materials
Advanced Materials
- Definition:
- Advanced materials are engineered substances designed to exhibit superior or unique physical, chemical, and mechanical properties compared to conventional materials. These materials are often developed to meet the growing demands of modern technology and extreme environmental conditions. Their development involves deep interdisciplinary research spanning materials science, physics, chemistry, and engineering, enabling solutions in fields ranging from microelectronics to aerospace engineering. Often, these materials display characteristics such as lightweight structure combined with high strength, tailored electrical conductivity, or exceptional corrosion resistance, making them integral to next-generation innovations.
- Key Types:
- Composites:
- Composites are formed by combining two or more distinct materials to produce a synergistic performance that exceeds the capabilities of the individual components. A prime example is carbon fiber reinforced polymer (CFRP), widely used in aerospace and automotive industries due to its low weight and exceptional tensile strength. These materials typically consist of a matrix (like a polymer resin) and a reinforcement (such as glass or carbon fibers). They are engineered for high performance in applications where weight reduction, impact resistance, and fatigue endurance are crucial, such as wind turbine blades, prosthetics, and sporting goods.
- Alloys:
- Alloys are metallic materials made by combining two or more elements, typically metals, to enhance mechanical strength, corrosion resistance, or heat tolerance. Titanium-aluminum alloys, for example, are valued for their excellent strength-to-weight ratio and are commonly used in jet engine components and spacecraft. The development of superalloys, which can maintain their strength and stability at extremely high temperatures, has revolutionized power generation and aerospace propulsion. These alloys are engineered using advanced processing techniques such as directional solidification and powder metallurgy to tailor their grain structure and performance characteristics.
- Nanomaterials:
- Nanomaterials possess structures at the nanoscale (1–100 nanometers), where quantum effects often dominate, leading to extraordinary properties not observed in bulk materials. These can include superlative strength, electrical and thermal conductivity, and high surface-area-to-volume ratios. Examples include carbon nanotubes (CNTs), graphene, and quantum dots. Due to their unique attributes, nanomaterials are used in flexible electronics, high-performance batteries, medical diagnostics, and filtration systems. Their fabrication involves sophisticated techniques such as atomic layer deposition, chemical vapor deposition, and self-assembly. As highlighted by the Nature Nanotechnology journal, ongoing research continues to uncover novel functionalities of nanomaterials, expanding their potential across emerging technologies.
- Composites:
Material Properties
- Mechanical:
- Mechanical properties define how a material responds to external forces, including strength, ductility, hardness, fatigue resistance, and toughness. Advanced materials are often tailored to endure extreme mechanical stresses without deforming or failing. For example, aerospace composites are designed to resist high fatigue loads during repeated pressurization cycles, while structural steels are developed for earthquake-resistant buildings. Understanding these properties is essential in selecting the appropriate material for each engineering application.
- Thermal:
- Thermal properties encompass a material’s behavior under heat, including thermal conductivity, specific heat capacity, thermal expansion, and resistance to thermal degradation. Materials used in heat exchangers, jet engines, and nuclear reactors must withstand high temperatures without compromising performance. Advanced ceramics and refractory metals are commonly employed in these roles. Engineers also exploit thermal insulation in aerospace re-entry vehicles and spacecraft shielding to protect against drastic temperature changes.
- Chemical:
- Chemical properties refer to how materials interact with other substances, including resistance to corrosion, oxidation, and chemical breakdown. Stainless steels and specialized coatings are used in chemical processing plants to withstand harsh acidic or alkaline environments. In marine applications, advanced polymers and anodized metals help combat saline corrosion. The study of chemical stability is pivotal for material selection in medical devices, fuel cells, and environmental containment systems.
- Electrical:
- Electrical properties involve a material’s ability to conduct, resist, or insulate electrical currents. Conductive materials like copper and silver are used in electronics, while insulators like ceramics and polymers prevent unintended current flow. Recent advancements in conductive nanomaterials and piezoelectric substances have opened new possibilities in flexible electronics, smart sensors, and wearables. Engineers also study dielectric strength and impedance when designing high-voltage systems and capacitors.
Specialized Applications
- Aerospace:
- Advanced materials in aerospace are vital for reducing weight while maintaining high strength and resistance to environmental stressors such as vibration, temperature fluctuations, and UV radiation. Composite materials, titanium alloys, and heat-resistant ceramics are used in fuselages, turbine blades, and thermal protection systems. These innovations contribute to higher fuel efficiency, longer service life, and improved safety in both civil and military aviation.
- Automotive:
- In the automotive sector, advanced materials help improve fuel economy, crash resistance, and thermal management. Aluminum alloys and high-strength steels are used in chassis and body components, while fiber-reinforced composites are being explored for structural parts in electric vehicles. Materials with enhanced heat dissipation and electromagnetic shielding properties are increasingly important in hybrid and autonomous vehicle systems.
- Healthcare:
- Biocompatible advanced materials are used in surgical implants, dental restorations, and prosthetics. Materials like titanium, hydroxyapatite, and shape-memory alloys allow for better integration with human tissues and reduced risk of rejection. Innovations in biodegradable polymers and nanomaterials are also driving progress in drug delivery systems and regenerative medicine, offering solutions for complex health challenges through tailored material behavior.
- Energy:
- Advanced materials play a crucial role in energy systems by enhancing efficiency, safety, and sustainability. High-temperature alloys and ceramics are used in power plants and turbines, while advanced polymers and membranes support energy storage and conversion in batteries and fuel cells. Additionally, lightweight composites and corrosion-resistant coatings are essential for wind and solar energy infrastructure, improving the long-term performance of renewable energy systems.
Advanced Manufacturing Technologies
Additive Manufacturing (3D Printing)
- Definition:
- Additive manufacturing, commonly referred to as 3D printing, involves the layer-by-layer deposition of materials to construct objects directly from digital models. This process contrasts with traditional subtractive manufacturing, which removes material to achieve the final shape. The precision and flexibility of additive manufacturing allow for the creation of complex geometries, lightweight structures, and internal features that would be impossible or highly expensive to produce using conventional methods. This approach minimizes waste, shortens lead times, and enables customization at a granular level.
- Applications:
- In the aerospace industry, components such as brackets and engine parts with internal cooling channels are produced using 3D printing to optimize weight and functionality. Medical applications include custom-designed implants and prosthetics tailored to individual patients’ anatomy, improving outcomes and comfort. Architecture and the construction sector are also exploring large-scale 3D printing for rapid and cost-effective building projects. Additionally, the fashion industry utilizes this technology to design intricate wearables and accessories, while the food industry experiments with edible 3D printed items.
- Materials Used:
- Additive manufacturing employs a diverse range of materials, including metal powders like titanium and aluminum for aerospace-grade parts, polymers such as PLA and ABS for prototyping, and ceramics for heat-resistant applications. Specialized biocompatible materials are also used in medical devices. These materials are often selected based on desired mechanical properties, thermal stability, and biocompatibility. With ongoing material science research, the printable material range continues to grow, enabling new possibilities across industries. For further reading on cutting-edge material developments, visit ScienceDirect’s Additive Manufacturing journal.
Smart Manufacturing
- Definition:
- Smart manufacturing integrates digital technologies such as the Internet of Things (IoT), Artificial Intelligence (AI), big data analytics, and cloud computing into manufacturing systems to optimize efficiency, reduce downtime, and enhance adaptability. Real-time data collection and analysis allow systems to respond dynamically to changes, making factories more agile and responsive. This paradigm shift marks the transition toward Industry 4.0, where cyber-physical systems operate with minimal human intervention while maintaining high precision and reliability.
- Applications:
- AI-driven quality control systems use machine vision to inspect products at production speed, identifying defects with greater accuracy than manual inspection. Predictive maintenance systems analyze equipment performance in real-time and forecast potential failures, allowing for timely interventions that reduce unplanned downtime. Smart manufacturing also enables flexible production lines capable of adjusting to customized orders with minimal reconfiguration, benefiting industries such as automotive, consumer electronics, and pharmaceuticals.
Advanced Machining
- Definition:
- Advanced machining refers to the use of high-precision manufacturing techniques such as Computer Numerical Control (CNC) machining, laser cutting, and electrical discharge machining (EDM) to shape and fabricate intricate components from raw materials. These processes offer sub-millimeter accuracy, high repeatability, and the ability to work with difficult-to-machine materials like hardened steels and ceramics.
- Applications:
- In aerospace manufacturing, advanced machining is essential for producing turbine blades with complex curvature and fine tolerances. Similarly, in the medical device industry, orthopedic implants and surgical tools are manufactured to stringent specifications using CNC systems. Advanced machining also supports the semiconductor industry by fabricating molds, dies, and microcomponents for integrated circuits.
Composite Manufacturing
- Definition:
- Composite manufacturing involves techniques for creating materials composed of two or more constituents with distinct physical or chemical properties. These materials, once combined, produce enhanced performance characteristics such as increased strength, reduced weight, and improved corrosion resistance.
- Methods:
- Common methods include autoclave curing for high-performance aerospace components, filament winding for cylindrical structures such as pressure vessels, and resin transfer molding (RTM) for automotive and consumer goods. These techniques ensure consistent resin distribution and fiber alignment, resulting in durable and high-performance products.
- Applications:
- Composite panels made of carbon fiber are widely used in the aerospace and automotive industries due to their high strength-to-weight ratio. Applications extend to wind turbine blades, bicycle frames, sports equipment, and marine vessels. Their versatility and customization potential make composites ideal for industries seeking performance and efficiency improvements.
Nanomanufacturing
- Definition:
- Nanomanufacturing refers to the production of devices and materials with nanoscale features. This includes top-down approaches such as lithography and etching, as well as bottom-up methods like molecular self-assembly. The objective is to create structures and systems with atomic-level precision for superior functionality.
- Applications:
- Nano-coatings are used to impart self-cleaning, anti-fog, or anti-scratch properties to surfaces. In healthcare, nanosensors detect biomarkers in bodily fluids, enabling early disease diagnosis and personalized medicine. Other applications include drug delivery systems, solar cells with enhanced efficiency, and water purification membranes.
Advanced Coating Technologies
- Definition:
- Advanced coating technologies involve the application of thin film layers to surfaces to enhance characteristics like hardness, reflectivity, corrosion resistance, or thermal insulation. These coatings can be functional, decorative, or protective, depending on the application.
- Applications:
- In marine environments, anti-corrosion coatings extend the lifespan of ships and offshore structures. In aerospace, thermal barrier coatings protect engine parts from extreme heat. Optical coatings improve the performance of lenses and photovoltaic cells, while biomedical coatings enhance implant biocompatibility and resistance to bacterial colonization.
Hybrid Manufacturing
- Definition:
- Hybrid manufacturing integrates additive and subtractive manufacturing techniques to leverage the advantages of both. This synergy allows for greater design freedom, improved surface finish, and enhanced mechanical properties.
- Applications:
- One common application is 3D printing a part’s rough shape followed by precision CNC machining to meet tight dimensional tolerances. Hybrid systems are used in tool and die manufacturing, repair of high-value components, and production of intricate molds. This approach reduces production steps, material waste, and lead time while ensuring superior quality.
Applications of Advanced Materials and Manufacturing Technologies
Aerospace and Defense
- Materials:
- Advanced composites such as carbon fiber reinforced polymers (CFRP), titanium-aluminum alloys, and ceramic matrix composites are key enablers of aerospace innovation. These materials offer superior strength-to-weight ratios, exceptional fatigue resistance, and thermal stability under extreme conditions.
- Applications:
- In aerospace, lightweight airframes constructed with carbon fiber composites reduce fuel consumption and increase payload capacity. High-performance turbine blades made from single-crystal superalloys and coated with ceramic barriers ensure durability at elevated temperatures. Ceramic matrix composites are used in thermal protection systems for spacecraft, allowing them to withstand re-entry heat. Additionally, radar-absorbent materials are employed in stealth aircraft to minimize radar signature.
Automotive Industry
- Materials:
- The automotive sector relies heavily on lightweight materials such as aluminum and magnesium alloys to meet fuel efficiency targets. High-strength steels provide crash protection without adding bulk, while advanced polymers offer corrosion resistance and formability.
- Applications:
- Automotive manufacturers utilize aluminum alloys for engine blocks and body panels to reduce vehicle weight. High-strength steels are employed in structural components like side impact beams and safety cages. Advanced polymers and composites are integrated into EV battery enclosures to enhance thermal stability and impact resistance. In electric vehicles, lightweight chassis and suspension systems significantly extend driving range. Innovations like smart materials for active aerodynamics are emerging trends in the quest for enhanced performance and sustainability.
Healthcare
- Materials:
- Healthcare applications demand materials that are biocompatible, durable, and sometimes biodegradable. These include titanium alloys for implants, biodegradable polymers for tissue engineering, and hydroxyapatite ceramics for bone grafts and coatings.
- Applications:
- Advanced materials have transformed modern medicine. Titanium implants are widely used for joint replacements and dental restorations due to their strength, lightness, and compatibility with human tissue. Biodegradable scaffolds enable the growth of new tissues and organs, a cornerstone of regenerative medicine. Hydroxyapatite coatings on implants improve osseointegration, promoting bone bonding. Drug delivery systems utilize smart polymers that release medication in response to environmental stimuli such as pH or temperature. For deeper insights, explore the National Library of Medicine’s research on biomaterials.
Renewable Energy
- Materials:
- Materials used in renewable energy systems include glass-fiber composites for wind turbine blades, high-temperature alloys for solar thermal plants, and hydrogen-compatible materials for clean energy storage and transport.
- Applications:
- In wind energy, lightweight yet durable glass-fiber and carbon-fiber composites enable the construction of longer, more efficient blades. Concentrated solar power (CSP) plants require alloys that can withstand intense heat cycles without degradation. In hydrogen energy, advanced storage materials like metal hydrides and carbon nanotubes are under development to safely contain hydrogen at high energy densities. Photovoltaic panels benefit from anti-reflective and self-cleaning coatings to boost efficiency and durability. These material innovations play a crucial role in making renewable energy systems more cost-effective and reliable.
Electronics
- Materials:
- Semiconductor materials such as silicon wafers, conductive polymers, gallium arsenide, and emerging 2D materials like graphene and molybdenum disulfide are the backbone of modern electronics. They enable miniaturization, flexibility, and improved performance.
- Applications:
- Silicon is fundamental in microprocessors, memory chips, and integrated circuits. Flexible electronics use conductive polymers and printed electronics techniques to produce wearable devices and foldable displays. Graphene’s exceptional conductivity and strength open avenues in high-speed transistors and supercapacitors. Advanced materials are also critical in battery technology—lithium-ion cells use graphite and metal oxides, while solid-state batteries explore ceramic electrolytes for safety and performance. These innovations enable the rapid growth of smart devices, the Internet of Things (IoT), and next-generation computing.
Construction
- Materials:
- Modern construction leverages self-healing concrete, aerogels, fiber-reinforced composites, and phase-change materials for energy efficiency and longevity. These materials enhance structural integrity, thermal performance, and environmental resilience.
- Applications:
- Self-healing concrete contains capsules of bacteria or chemical agents that react with moisture to repair cracks, significantly extending infrastructure life. Aerogels are used in insulation due to their ultra-low thermal conductivity. Fiber-reinforced composites contribute to seismic resistance and lightweight prefabricated structures. Phase-change materials embedded in walls and windows regulate indoor temperatures by absorbing and releasing heat. These innovations are instrumental in green building design, helping reduce operational energy use and carbon emissions while enhancing occupant comfort.
Research and Development in Advanced Materials and Manufacturing Technologies
Material Testing and Characterization
- Purpose:
- Material testing and characterization serve a foundational role in ensuring the reliability, safety, and suitability of materials for a wide range of applications. These processes aim to understand how materials behave when subjected to different physical, chemical, thermal, and mechanical conditions. Whether it’s for a critical aircraft component or a medical implant, evaluating how a material responds under stress, corrosion, or heat exposure helps prevent failure and ensures long-term performance in real-world conditions.
- Methods:
- Modern laboratories employ a suite of advanced methods to extract comprehensive data about material properties. Tensile testing measures a material’s strength and elongation before it breaks, offering insights into ductility and elasticity. Thermal analysis, such as Differential Scanning Calorimetry (DSC) and Thermogravimetric Analysis (TGA), helps determine phase transitions, heat capacity, and thermal stability. Scanning Electron Microscopy (SEM) and Transmission Electron Microscopy (TEM) reveal microstructural details at magnifications up to millions of times, enabling researchers to observe grain boundaries, inclusions, and fracture behavior.
- Applications:
- Material testing is essential across industries where performance and safety are non-negotiable. In aerospace, it ensures that composites and alloys used in turbines or airframes can withstand extreme stresses during flight. In healthcare, biocompatible materials for implants undergo rigorous characterization to ensure they don’t degrade or cause immune reactions. The construction industry uses mechanical testing to ensure that concrete composites meet building code specifications. These processes are also critical in the certification of materials for additive manufacturing and advanced coatings.
Computational Materials Science
- Definition:
- Computational materials science involves the use of numerical simulation tools, algorithms, and theoretical models to predict the behavior of materials without relying solely on physical experimentation. By leveraging quantum mechanics, molecular dynamics, and continuum mechanics, researchers can explore materials at the atomic and molecular levels, drastically accelerating the pace of material innovation.
- Applications:
- Computational methods enable precise predictions of how a material behaves under conditions such as high temperature, mechanical stress, or exposure to chemicals. Engineers use finite element analysis (FEA) to model material deformation in real-time scenarios. Molecular dynamics simulations provide insight into phase transformations, crack propagation, and diffusion mechanisms. Researchers employ these tools to design high-entropy alloys and metamaterials with novel properties. Moreover, machine learning models are now integrated with simulation data to rapidly screen thousands of potential material candidates. As outlined by the Materials Project by Lawrence Berkeley National Laboratory, open-access databases further accelerate discovery by offering computational data on thousands of compounds.
Nanotechnology
- Focus:
- Nanotechnology research focuses on the manipulation and engineering of matter at the atomic, molecular, and supramolecular scales—typically below 100 nanometers. At this scale, materials exhibit unique properties not seen in their bulk counterparts, including quantum effects, increased surface area-to-volume ratios, and enhanced reactivity or strength. This field aims to exploit these phenomena to develop high-performance materials across multiple domains.
- Applications:
- Nanotechnology has enabled the development of nanocomposites that offer increased mechanical strength, reduced weight, and improved thermal resistance, ideal for aerospace and automotive uses. Carbon nanotubes and graphene are being studied for their exceptional conductivity and tensile strength. In healthcare, silver nanoparticles are utilized for their antibacterial properties in wound dressings and coatings. Nanostructured surfaces on surgical tools reduce friction and improve sterilization. In environmental applications, nanomaterials are used in filters to capture heavy metals and pathogens from water, while nanocoatings on buildings improve energy efficiency and reduce maintenance costs.
Sustainable Materials
- Focus:
- The focus of sustainable materials research is to mitigate the environmental impact of production and disposal by developing eco-friendly alternatives. This includes designing materials that are recyclable, biodegradable, or made from renewable resources such as plant-based polymers or agricultural waste. The goal is to create a closed-loop lifecycle for products while maintaining or enhancing performance standards.
- Applications:
- Bioplastics derived from corn starch, sugarcane, or algae are gaining popularity in packaging and single-use items, helping reduce reliance on petroleum-based plastics. Recycled carbon fiber and polymers are increasingly used in the automotive industry to build lightweight, durable components while reducing landfill waste. Sustainable composites incorporating natural fibers like flax or hemp are employed in construction and furniture. Additionally, researchers are developing concrete with lower carbon footprints and polymers that biodegrade under industrial composting conditions. These materials not only reduce greenhouse gas emissions but also align with circular economy goals and environmental regulations.
Technologies Enabling Advanced Materials Manufacturing Technologies
Artificial Intelligence (AI)
- Role:
- Artificial Intelligence (AI) plays a transformative role in modern materials science and manufacturing by enabling intelligent systems that learn, adapt, and optimize processes without explicit programming. AI algorithms can analyze large datasets derived from simulations, experiments, or operational feedback to uncover patterns and correlations that may be too complex for traditional models to capture. This enhances decision-making at every stage—from materials discovery to process control—improving both efficiency and innovation in manufacturing environments.
- Applications:
- Machine learning models are increasingly used to predict failure modes, mechanical properties, and thermal behavior of advanced materials. For example, convolutional neural networks (CNNs) trained on microstructure images can predict a material’s fatigue life or corrosion resistance. In manufacturing, AI algorithms can fine-tune process parameters in real-time to ensure optimal quality and yield. Reinforcement learning is applied to autonomous robotic arms to adapt to new materials handling scenarios. The integration of AI also extends to predictive maintenance, minimizing downtime by forecasting when equipment is likely to fail. These capabilities are actively supported by platforms such as [NOMAD](https://nomad-lab.eu), which provide open-access AI-ready materials data to accelerate research.
Digital Twins
- Role:
- Digital twin technology enables the creation of high-fidelity virtual replicas of physical systems, including individual components, complete machines, or entire production lines. These virtual models are dynamically linked to their physical counterparts through real-time data, allowing engineers to simulate, monitor, and optimize materials and processes without interrupting live operations. By using digital twins, manufacturers can test hypothetical scenarios, fine-tune performance parameters, and anticipate maintenance needs, thereby improving efficiency, safety, and product reliability.
- Applications:
- In aerospace, digital twins are used to simulate the thermal and mechanical behavior of composite structures during flight. For instance, engineers can analyze how an engine turbine blade reacts to repeated temperature cycling and vibration stress, enabling adjustments before actual failures occur. In additive manufacturing, digital twins help optimize the build sequence by simulating how heat distribution affects part geometry. These virtual environments also support real-time quality assurance by comparing in-process data with ideal performance benchmarks, ultimately improving throughput and reducing rework.
IoT and Smart Sensors
- Role:
- The Internet of Things (IoT) and smart sensors are critical in achieving real-time, data-driven monitoring and control in advanced manufacturing systems. These technologies enable continuous feedback loops by capturing information on temperature, pressure, strain, vibration, and chemical composition directly from production equipment or materials. This data is then transmitted and analyzed to inform decisions on process adjustments, fault detection, and quality control.
- Applications:
- Smart sensors embedded in composite materials can detect internal stresses, delamination, or microcracks that are otherwise invisible during production. These embedded sensing systems enhance structural health monitoring in aerospace, wind energy, and infrastructure applications. In manufacturing lines, IoT networks allow operators to track machine performance remotely, identify bottlenecks, and prevent catastrophic failures. Additionally, smart materials that respond to environmental changes (such as shape memory alloys) can be paired with IoT systems for adaptive functionality in medical and aerospace products.
Automation and Robotics
- Role:
- Automation and robotics revolutionize the production landscape by replacing repetitive manual tasks with high-precision automated systems, thereby increasing throughput, consistency, and workplace safety. These systems can operate 24/7 and are programmable to accommodate complex tasks, reducing human error and variability. Robotics also play a crucial role in environments that are hazardous or require ultra-fine accuracy, such as cleanrooms or high-temperature processes.
- Applications:
- Automated Fiber Placement (AFP) is widely used in aerospace manufacturing to layer composite materials with exact control over fiber orientation and compaction pressure. Robotic arms equipped with vision systems and AI-powered control logic are used to perform delicate assembly tasks in electronics and biomedical devices. Collaborative robots (cobots) enhance flexibility by working alongside human operators on production lines, taking over tasks like welding, inspection, and packaging. Robotic additive manufacturing setups can also scale 3D printing to larger parts or multifunctional builds through continuous motion systems.
Quantum Computing
- Potential:
- Quantum computing holds immense promise for solving complex optimization and simulation problems that are currently intractable using classical computing. In materials science, it enables the modeling of quantum mechanical behavior in atoms and molecules with unprecedented precision. Quantum algorithms such as Variational Quantum Eigensolvers (VQE) and Quantum Phase Estimation (QPE) could drastically accelerate the discovery of novel materials with tailored electronic, thermal, or mechanical properties. Though still in early stages, these advancements could reshape the way materials are designed and manufactured in the future.
Benefits of Advanced Materials and Manufacturing Technologies
- Enhanced Performance:
- Advanced materials such as high-strength alloys, carbon fiber composites, and nanomaterials exhibit superior mechanical, thermal, and chemical properties compared to conventional alternatives. These materials are engineered to perform reliably in extreme environments—ranging from high-stress mechanical loading in aerospace turbines to corrosive marine conditions in shipbuilding. For example, lightweight carbon-fiber composites significantly reduce aircraft weight while maintaining structural integrity, leading to improved fuel efficiency and range. Furthermore, shape memory alloys and self-healing polymers are being developed to autonomously adapt or recover from damage, ensuring prolonged service life and operational safety across industries.
- Increased Efficiency:
- Modern manufacturing technologies like additive manufacturing (AM), laser-assisted machining, and AI-driven process control allow for precise material placement and minimal resource use. By minimizing waste through layer-by-layer fabrication and reusing excess material in closed-loop systems, these methods help manufacturers cut down on raw material usage. Energy-efficient machinery and smart factory automation further reduce power consumption during production. Advanced sensors and real-time monitoring optimize workflow, eliminating inefficiencies in equipment usage and material flow. Collectively, these improvements result in leaner, faster, and more environmentally responsible production cycles.
- Broader Applications:
- The convergence of advanced materials with next-generation manufacturing enables the development of entirely new classes of products and systems across diverse sectors such as biomedical engineering, defense, consumer electronics, and renewable energy. Custom-fabricated implants tailored to patient anatomy, adaptive military armor that changes stiffness upon impact, and foldable displays in smart devices are now practical due to the synergy of novel materials and techniques. Furthermore, the democratization of these innovations is fostered by global platforms like SME’s Advanced Manufacturing which connect research, industry, and policy to accelerate deployment and knowledge sharing across sectors.
- Sustainability:
- Advanced manufacturing techniques emphasize environmentally conscious production by utilizing recyclable, biodegradable, or bio-derived materials. Closed-loop manufacturing systems reuse scrap material, reducing landfill waste. Additive manufacturing minimizes by-products by adding only the material required for the final shape. Innovations such as carbon-negative concrete, algae-based bioplastics, and thermally insulating aerogels contribute to greener buildings, packaging, and energy systems. Renewable-powered factories and digital optimization tools further lower emissions and help industries align with global sustainability goals like those outlined in the UN’s Sustainable Development Goals (SDGs).
- Cost Reduction:
- While initial investments in advanced materials and machinery can be high, the long-term cost benefits are substantial. Durable materials reduce maintenance and replacement needs, and improved efficiency leads to lower operational expenses. Additive manufacturing cuts tooling and storage costs, especially for low-volume or on-demand production. Predictive maintenance systems reduce equipment downtime, and smart inventory systems lower holding costs. These advantages are particularly valuable for small and medium-sized enterprises (SMEs), which can now compete in high-tech markets thanks to scalable, cost-effective technologies tailored to their production needs.
Challenges in Advanced Materials and Manufacturing Technologies
- High Development Costs:
- Developing advanced materials and integrating next-generation manufacturing technologies require substantial financial investment. The costs associated with high-performance raw materials, proprietary synthesis methods, and specialized production tools can be prohibitive, particularly for startups and SMEs. Research and development (R&D) in this field demands long-term funding, access to high-precision testing facilities, and partnerships with academic institutions or national laboratories. Pilot-scale production and prototyping further increase expenditures before commercialization is possible. While economies of scale may reduce costs over time, the initial barriers to entry often delay innovation deployment in smaller or resource-constrained markets.
- Complexity of Production:
- Manufacturing advanced materials such as carbon nanotube composites, shape memory alloys, or biomimetic surfaces typically involves highly controlled environments and multistep fabrication processes. Techniques such as atomic layer deposition, additive-subtractive hybrid methods, and nanolithography require precise calibration and expert handling. The integration of these materials into existing supply chains presents additional challenges, as traditional manufacturing systems are not always compatible. Process variability and repeatability also pose concerns, especially when working at micro- or nanoscale. Achieving uniform quality while scaling production is an ongoing technical and operational hurdle for the industry.
- Scalability Issues:
- Even when laboratory-scale results are promising, translating those findings into cost-effective, large-scale production remains a core challenge. Advanced materials often perform well in small batches under controlled conditions, but maintaining their properties at scale involves overcoming raw material sourcing constraints, optimizing fabrication speed, and ensuring quality assurance throughout. Infrastructure must also be adapted or rebuilt to accommodate high-throughput, precision-based manufacturing lines. For instance, while graphene offers remarkable conductivity and strength, the industry still struggles with its high-quality mass production. According to Nature’s research on materials scalability, bridging the lab-to-market gap is one of the most persistent barriers in material innovation.
- Workforce Training:
- The rapid evolution of tools such as AI-integrated process control, digital twin modeling, and nanomanufacturing demands a technically adept workforce. However, educational and vocational institutions often struggle to keep curricula up-to-date with industry needs. As a result, there is a growing skills gap in areas such as computational materials science, robotics integration, and sustainable manufacturing. Upskilling current employees requires dedicated resources, and attracting new talent may involve revamping training programs and offering competitive incentives. Without targeted workforce development, the adoption of cutting-edge manufacturing solutions is likely to stall or underperform.
- Regulatory Compliance:
- New materials and manufacturing methods must navigate a complex web of regulatory standards pertaining to health, safety, and environmental impact. This is particularly critical in sectors like aerospace, medical devices, and food packaging, where materials must meet strict certification criteria. Advanced manufacturing also raises emerging concerns about nanotoxicity, environmental persistence, and circular economy compatibility. Gaining regulatory approval can be time-consuming and expensive, especially when cross-border trade introduces overlapping jurisdictions. Companies must implement robust compliance strategies and engage early with regulatory bodies to ensure smooth market entry and long-term operational viability.
Emerging Trends in Advanced Materials and Manufacturing Technologies
- Bio-Inspired Materials:
- One of the most promising directions in materials science involves bio-inspiration—drawing on the elegant and efficient designs evolved in nature to develop high-performance synthetic materials. Researchers are developing structural fibers modeled after spider silk, which offers an extraordinary combination of strength, elasticity, and light weight. Other examples include lotus-leaf-inspired hydrophobic surfaces, sharkskin-textured antibacterial films, and nacre-mimicking composites that combine toughness and flexibility. These materials are gaining traction in fields such as defense (for body armor), medical implants (for tissue compatibility), and aerospace (for self-cleaning or drag-reducing coatings). Bio-inspiration is proving to be a powerful paradigm, merging biology with engineering for sustainable innovation.
- Smart Materials:
- Smart materials are designed to respond to environmental stimuli such as temperature, pressure, humidity, or electrical fields. Shape-memory alloys (SMAs) can return to their original form after deformation, making them ideal for actuators and responsive components in aerospace and robotics. Self-healing polymers can autonomously repair micro-cracks or scratches, significantly extending the life span of coatings, structural components, and wearable electronics. Piezoelectric and thermochromic materials are increasingly being used in sensors, textiles, and building automation systems. These materials offer the potential to create systems that are adaptive, resilient, and intelligent, driving the evolution of everything from medical devices to architectural materials.
- Sustainable Manufacturing:
- The global shift toward sustainability has led to a revolution in how materials are processed and products are manufactured. Sustainable manufacturing seeks to minimize waste, reduce emissions, and use resources efficiently throughout the production cycle. This includes adopting biodegradable polymers, recycling composite waste, and utilizing green chemistry methods that reduce the need for harmful solvents. Emerging tools like life cycle assessment (LCA) and closed-loop manufacturing systems are being integrated into factories to track and optimize environmental performance. A growing number of companies are also investing in sustainable certification schemes to attract eco-conscious consumers and comply with tightening regulations. According to the U.S. EPA’s guide to sustainable manufacturing, industries embracing these practices can improve operational efficiency while contributing to environmental stewardship.
- Lightweighting:
- The development of lighter yet stronger materials is a persistent trend, particularly in automotive, aerospace, and rail transportation. Lightweighting leads to improved fuel economy, higher payload capacities, and reduced emissions. Advances in high-strength aluminum alloys, carbon-fiber-reinforced plastics (CFRPs), and metal matrix composites (MMCs) are enabling the replacement of heavier traditional materials. In electric vehicles, for example, lightweight chassis and enclosures offset the mass of batteries, improving overall efficiency and driving range. Engineers are also designing novel sandwich structures and lattice geometries through additive manufacturing, balancing weight reduction with structural integrity. As mobility sectors pursue carbon neutrality, lightweighting continues to be a core strategy.
- 3D-Printed Metals and Composites:
- Additive manufacturing has matured far beyond simple plastic prototyping and now encompasses high-performance metals and composite materials suitable for critical applications. Metal additive manufacturing techniques such as direct metal laser sintering (DMLS), electron beam melting (EBM), and binder jetting are being used to create complex parts with optimized geometries, internal channels, and tailored properties. These parts are seeing adoption in aerospace engine components, orthopedic implants, and defense applications. Similarly, composite-based 3D printing allows for parts that combine the flexibility of polymers with the strength of fibers such as carbon or Kevlar. These materials are ideal for producing lightweight and strong structural components with reduced waste and shorter lead times. Innovations in feedstock formulation and process control are expanding the capabilities of printed metals and composites at an accelerating pace.
Future Directions in Advanced Materials and Manufacturing Technologies
- Material Genomics:
- Material genomics is an emerging interdisciplinary field that applies high-throughput computational and experimental techniques to accelerate the discovery and optimization of materials. By combining artificial intelligence, machine learning, and massive materials databases, scientists can model material behavior, predict performance, and identify ideal candidates for specific applications without relying solely on trial-and-error experimentation. For example, researchers are using AI models to screen thousands of chemical compositions for next-generation battery materials, thermoelectrics, or catalysts. Projects like the Materials Genome Initiative in the U.S. exemplify global efforts to standardize and accelerate materials innovation, promising breakthroughs in energy storage, structural components, and electronic materials within a fraction of traditional development time.
- Circular Economy Integration:
- As sustainability becomes a global imperative, integrating advanced materials into circular economy models is a critical direction. This involves designing materials and products for longevity, reusability, recyclability, and minimal environmental impact. Engineers are now creating high-performance composites and polymers that are not only durable but also easily disassembled or chemically recycled. Advanced materials are also being developed from bio-based feedstocks, reducing dependence on petroleum and enabling biodegradability. The integration of digital tracking technologies such as blockchain and RFID allows for full lifecycle monitoring of materials, enabling efficient collection, sorting, and reuse. According to the Ellen MacArthur Foundation, such closed-loop innovations can reduce industrial waste, lower emissions, and drive systemic change across manufacturing ecosystems.
- Advanced Coatings:
- Future coatings are being engineered to go beyond basic protection, incorporating multiple functionalities to meet the demands of aerospace, defense, and healthcare sectors. Self-cleaning, anti-icing, antimicrobial, and radiation-resistant coatings are in development, using nanostructured surfaces, reactive molecules, or embedded sensors. In aerospace, advanced thermal barrier coatings extend the lifespan of turbine blades under extreme heat. In defense, stealth coatings reduce radar detection while improving environmental resilience. Healthcare applications include antimicrobial coatings for surgical tools and implants, lowering the risk of infection. These innovations not only improve performance and safety but also reduce maintenance costs and extend operational longevity across high-value systems.
- Energy-Efficient Processes:
- Reducing the energy footprint of manufacturing is a major focus of future technological advancement. This includes optimizing traditional techniques such as casting, forging, and machining through process control algorithms, waste heat recovery, and hybrid methods. Newer techniques like cold spray deposition, microwave sintering, and laser-based additive manufacturing are being explored for their lower energy requirements. Furthermore, the integration of AI-powered analytics helps identify energy inefficiencies and recommend corrective actions in real time. As energy costs rise and emission regulations tighten, the shift to low-carbon manufacturing becomes both an economic and environmental imperative, contributing to greener supply chains and enhanced corporate sustainability metrics.
- Quantum-Engineered Materials:
- Advancements in quantum physics are unlocking the potential to engineer materials with extraordinary properties derived from quantum-level phenomena. Quantum dots, topological insulators, and superconductors are examples of materials that exhibit behavior not found in classical systems. These materials hold promise for applications in quantum computing, ultra-sensitive sensors, and energy-efficient electronics. Scientists are investigating how quantum entanglement, tunneling, and coherence can be harnessed to develop breakthroughs in magnetic memory storage, thermoelectric converters, and optoelectronic devices. While still in early stages, quantum-engineered materials may redefine the limits of what’s physically and technologically possible, ushering in a new era of materials science and application potential.
Why Study Advanced Materials and Manufacturing Technologies
Enabling Innovation Through Material Science
Advanced materials such as composites, nanomaterials, and smart materials are revolutionizing manufacturing. Students learn how these materials offer superior strength, lightness, or functionality. This enables the development of innovative products and structures.
High-Performance and Customized Applications
Students study how advanced materials are used in aerospace, biomedical devices, and electronics. These applications demand precision, durability, and specialized properties. Mastering these materials opens doors to high-tech engineering careers.
Modern Manufacturing Techniques
The course introduces cutting-edge processes such as additive manufacturing, laser machining, and microfabrication. Students learn how these technologies improve quality, speed, and sustainability. This prepares them for leadership in next-generation manufacturing.
Material Testing and Characterization
Students explore techniques such as spectroscopy, scanning electron microscopy, and tensile testing. These methods reveal how materials behave under different conditions. Accurate testing ensures reliability and performance in real-world applications.
Driving Sustainable and Efficient Production
Advanced materials reduce energy use, extend product life, and support recycling. Students understand how material choice affects sustainability. This aligns engineering practice with environmental and economic goals.
Advanced Materials and Manufacturing Technologies: Conclusion
Advanced materials and manufacturing technologies are reshaping the industrial landscape by facilitating the design and production of highly functional, sustainable, and cost-effective solutions across a wide spectrum of sectors. Their influence extends far beyond traditional applications, empowering industries to achieve breakthroughs in performance, durability, and environmental stewardship. Whether it’s the development of ultralight composites for next-generation aircraft, bio-compatible implants tailored for individual patients, or energy-saving components that enable a greener grid, the synergy between material innovation and manufacturing precision is unlocking possibilities once thought unattainable.
Composites, nanomaterials, and smart alloys have transcended laboratory boundaries to become critical assets in real-world production, especially when paired with advanced fabrication methods such as additive manufacturing, digital twin simulation, and automated precision machining. These technological combinations enable intricate geometries, optimized mechanical properties, and enhanced thermal or chemical resistance—while minimizing material waste and energy consumption. The ability to tailor materials at the molecular or nanoscale level ensures that performance specifications are met with unprecedented accuracy, leading to safer vehicles, more efficient electronics, and longer-lasting infrastructure.
Moreover, the integration of digital technologies—including AI-driven design optimization, Internet of Things (IoT) sensor networks, and blockchain-enabled supply chain traceability—ensures that manufacturing systems can adapt in real time, learn from performance data, and continuously refine their processes. This digital transformation supports leaner operations, predictive maintenance, and rapid prototyping cycles, drastically reducing time-to-market and enhancing overall competitiveness. In high-risk environments such as defense and aerospace, smart materials and digital manufacturing processes deliver mission-critical reliability while enabling modular upgrades and on-site repairs.
As global challenges such as climate change, population growth, and resource depletion intensify, advanced materials and manufacturing will play a pivotal role in driving sustainable development. Circular economy principles are already influencing material selection and product lifecycle planning, with recyclable composites, bio-based polymers, and energy-efficient production methods gaining traction. At the same time, scalable manufacturing processes are making it economically viable to deploy these innovations across developing economies, democratizing access to high-performance infrastructure and technology.
Looking ahead, the convergence of breakthroughs in quantum materials, biomanufacturing, and smart automation promises to redefine the very limits of industrial capabilities. From programmable matter to shape-shifting polymers, and from zero-waste factories to carbon-negative construction, the possibilities are boundless. As research and development accelerate through international collaboration and open-source innovation, advanced materials and manufacturing technologies will remain at the forefront of humanity’s response to both emerging opportunities and existential challenges—ushering in a future where engineering ingenuity is tightly aligned with ecological and societal well-being.
Advanced Materials and Manufacturing Technologies: Review Questions with Detailed Answers
1. What are advanced materials, and how do they differ from traditional materials used in manufacturing?
Answer:
Advanced materials are substances with superior properties or functionalities compared to traditional materials, enabling enhanced performance in various applications. They often incorporate novel compositions, structures, or processing techniques to achieve characteristics such as higher strength, lighter weight, greater durability, or specialized functionalities.
Concepts:
- Traditional Materials: Commonly used materials like steel, aluminum, plastics, and ceramics.
- Advanced Materials: Include composites, nanomaterials, biomaterials, and smart materials.
Differences:
- Performance: Advanced materials offer improved mechanical, thermal, electrical, or chemical properties.
- Functionality: They can have added functionalities like self-healing, responsiveness to environmental changes, or enhanced conductivity.
- Applications: Advanced materials enable new applications in industries such as aerospace, medical, electronics, and automotive.
Conclusion: Advanced materials provide significant advantages over traditional materials by enhancing product performance, enabling innovative designs, and expanding the range of possible applications in manufacturing.
2. What are composite materials, and what are their primary advantages in manufacturing applications?
Answer:
Composite materials are engineered materials made from two or more constituent materials with different physical or chemical properties. When combined, these materials produce a composite with characteristics superior to the individual components.
Concepts:
- Constituent Materials: Typically include a matrix (e.g., resin, metal) and a reinforcement (e.g., fibers, particles).
- Types of Composites: Fiber-reinforced plastics (FRP), metal matrix composites (MMC), ceramic matrix composites (CMC).
Primary Advantages:
- High Strength-to-Weight Ratio: Composites are often lighter than traditional materials while maintaining or exceeding their strength.
- Corrosion Resistance: Many composites are resistant to environmental degradation, extending the lifespan of products.
- Design Flexibility: Composites can be molded into complex shapes, allowing for innovative and optimized designs.
- Thermal Stability: They can withstand high temperatures without significant loss of properties.
- Tailored Properties: The properties of composites can be customized by selecting appropriate matrix and reinforcement materials.
Conclusion: Composite materials offer enhanced mechanical properties, corrosion resistance, and design flexibility, making them ideal for applications requiring lightweight and high-performance components.
3. How does additive manufacturing (3D printing) contribute to advancements in manufacturing technologies?
Answer:
Additive manufacturing (AM), commonly known as 3D printing, contributes significantly to advancements in manufacturing technologies by enabling the creation of complex, customized, and optimized parts with reduced waste and shorter production cycles.
Concepts:
- Layer-by-Layer Construction: AM builds objects by adding material layer by layer based on digital models.
- Material Efficiency: Minimizes material waste compared to subtractive manufacturing methods.
Contributions:
- Design Freedom: Allows for the production of intricate geometries and internal structures that are difficult or impossible to achieve with traditional manufacturing.
- Customization: Facilitates the creation of bespoke products tailored to individual specifications without significant cost increases.
- Rapid Prototyping: Accelerates the prototyping process, enabling faster design iterations and reduced time-to-market.
- Material Innovation: Supports the use of advanced materials, including metals, polymers, ceramics, and composites, expanding the range of possible applications.
- Supply Chain Optimization: Enables on-demand production, reducing the need for large inventories and streamlining supply chains.
Conclusion: Additive manufacturing revolutionizes manufacturing by enhancing design capabilities, enabling customization, reducing waste, and speeding up production processes, thereby driving innovation and efficiency across various industries.
4. What are nanomaterials, and what unique properties make them valuable in manufacturing applications?
Answer:
Nanomaterials are materials with structural features at the nanoscale, typically between 1 to 100 nanometers. Their unique properties arise from their small size and high surface area-to-volume ratio, which impart novel mechanical, electrical, thermal, and chemical characteristics.
Concepts:
- Types of Nanomaterials: Nanoparticles, nanowires, nanotubes, nanocomposites, and quantum dots.
- Size Scale: Dimensions measured in nanometers, leading to quantum effects and enhanced properties.
Unique Properties:
- Enhanced Strength and Durability: Nanomaterials can significantly improve the mechanical properties of composites, making them stronger and more resistant to wear.
- Improved Electrical Conductivity: Certain nanomaterials, like carbon nanotubes, exhibit superior electrical conductivity, useful in electronics and energy storage.
- Thermal Stability: Nanomaterials can enhance the thermal properties of materials, making them more resistant to temperature changes.
- Increased Surface Area: High surface area enables better catalytic activity and improved bonding in composites.
- Optical Properties: Nanomaterials can have unique optical characteristics, such as improved transparency or enhanced light absorption, beneficial in coatings and sensors.
Conclusion: Nanomaterials offer exceptional properties that enhance the performance and functionality of manufactured products, making them invaluable in applications ranging from aerospace and electronics to medical devices and energy systems.
5. What role do biomaterials play in advanced manufacturing technologies, and what are some common applications?
Answer:
Biomaterials are materials that are compatible with biological systems and are used in medical and healthcare applications. In advanced manufacturing technologies, biomaterials enable the creation of medical devices, implants, and tissue engineering scaffolds with tailored properties to interact safely and effectively with the human body.
Concepts:
- Biocompatibility: The ability of a material to perform with an appropriate host response in a specific application.
- Types of Biomaterials: Metals (e.g., titanium alloys), polymers (e.g., PLA, PEG), ceramics (e.g., hydroxyapatite), and composites.
Common Applications:
- Medical Implants: Customized prosthetics, dental implants, and orthopedic devices that integrate seamlessly with biological tissues.
- Tissue Engineering: Scaffolds for growing tissues and organs, supporting cell growth and differentiation.
- Medical Devices: Components for surgical instruments, diagnostic devices, and wearable health monitors.
- Drug Delivery Systems: Biodegradable materials designed to deliver pharmaceuticals at controlled rates within the body.
- Regenerative Medicine: Materials that support the regeneration of damaged tissues and organs, enhancing healing processes.
Conclusion: Biomaterials are critical in the development of advanced medical technologies, providing safe and effective solutions for implants, tissue engineering, and medical devices, thereby improving patient outcomes and advancing healthcare innovation.
6. How do smart materials integrate with manufacturing technologies to create intelligent systems and products?
Answer:
Smart materials are materials that can respond to external stimuli such as temperature, pressure, light, or electric fields by changing their properties or behavior. Integrating smart materials with manufacturing technologies enables the creation of intelligent systems and products that can adapt, sense, and respond to their environment.
Concepts:
- Types of Smart Materials: Shape memory alloys, piezoelectric materials, electrochromic materials, and self-healing polymers.
- Stimuli-Responsive Behavior: Ability to change shape, color, conductivity, or other properties in response to external triggers.
Integration with Manufacturing Technologies:
Embedded Sensors and Actuators:
- Action: Incorporate smart materials into products to enable sensing and actuation.
- Benefit: Creates products that can monitor their own condition, adjust functionality, or perform autonomous actions.
Adaptive Manufacturing Systems:
- Action: Use smart materials in manufacturing equipment to enable adaptive control and self-optimization.
- Benefit: Enhances precision, reduces downtime, and improves overall efficiency of manufacturing processes.
Self-Healing Systems:
- Action: Integrate self-healing materials into products to automatically repair damage.
- Benefit: Increases product lifespan, reduces maintenance costs, and enhances reliability.
Responsive Structures:
- Action: Utilize shape memory alloys and other smart materials in structural components to allow for dynamic adjustments.
- Benefit: Enables structures to adapt to changing loads, environmental conditions, or operational requirements.
Energy Harvesting:
- Action: Incorporate piezoelectric materials to capture and convert ambient energy into usable electrical power.
- Benefit: Powers embedded electronics and sensors without the need for external power sources.
Conclusion: Integrating smart materials with manufacturing technologies paves the way for intelligent and adaptive products and systems, enhancing functionality, reliability, and efficiency across various applications, including aerospace, automotive, healthcare, and consumer electronics.
7. What are the benefits and challenges of using nanocomposites in advanced manufacturing?
Answer:
Nanocomposites are materials that incorporate nanoscale fillers (such as nanoparticles, nanofibers, or nanotubes) into a matrix material to enhance its properties. They offer significant benefits in advanced manufacturing but also present certain challenges.
Concepts:
- Nanocomposites: Combinations of a matrix material with nanoscale reinforcements to improve mechanical, thermal, electrical, or barrier properties.
- Matrix Materials: Polymers, metals, ceramics, or composites that host the nanoscale fillers.
Benefits:
Enhanced Mechanical Properties:
- Benefit: Increased strength, stiffness, and toughness compared to the base matrix material.
- Impact: Improves durability and performance of manufactured parts.
Improved Thermal Stability:
- Benefit: Higher resistance to heat, allowing for use in high-temperature applications.
- Impact: Extends the range of applications in environments with thermal stress.
Superior Electrical Conductivity:
- Benefit: Enhanced electrical properties for applications in electronics and energy storage.
- Impact: Enables the creation of conductive pathways and smart materials.
Barrier Properties:
- Benefit: Improved resistance to gases, moisture, and chemicals.
- Impact: Extends the shelf life of products and protects sensitive components.
Lightweighting:
- Benefit: Nanocomposites can achieve high strength with reduced weight.
- Impact: Beneficial for industries like aerospace and automotive where weight reduction is crucial.
Challenges:
Dispersion of Nanofillers:
- Challenge: Achieving uniform dispersion of nanoscale fillers within the matrix.
- Impact: Poor dispersion can lead to agglomeration, reducing the effectiveness of the nanocomposite.
Processing Complexity:
- Challenge: Integrating nanocomposites into existing manufacturing processes can require specialized equipment and techniques.
- Impact: Increases production costs and may necessitate process modifications.
Cost of Nanomaterials:
- Challenge: High cost of producing and incorporating nanoscale fillers.
- Impact: Can make nanocomposites economically unfeasible for certain applications.
Health and Safety Concerns:
- Challenge: Potential risks associated with handling and processing nanomaterials, including inhalation and environmental impact.
- Impact: Requires stringent safety protocols and regulatory compliance.
Scalability:
- Challenge: Scaling up the production of nanocomposites from laboratory to industrial levels while maintaining quality and consistency.
- Impact: Limits widespread adoption in mass-market applications.
Conclusion: Nanocomposites offer significant enhancements in material properties, enabling advanced manufacturing applications that require high performance and lightweighting. However, challenges related to dispersion, processing, cost, safety, and scalability must be addressed to fully leverage their potential in industrial settings.
8. How do advanced manufacturing technologies contribute to sustainability in industrial operations?
Answer:
Advanced manufacturing technologies contribute to sustainability in industrial operations by improving resource efficiency, reducing waste and emissions, enabling the use of sustainable materials, and optimizing production processes. These technologies support environmentally responsible practices and promote long-term economic and social sustainability.
Concepts:
- Sustainability: Meeting present needs without compromising the ability of future generations to meet their own needs.
- Resource Efficiency: Maximizing the use of materials, energy, and other resources to minimize waste and environmental impact.
Contributions to Sustainability:
Additive Manufacturing (3D Printing):
- Contribution: Reduces material waste by building objects layer by layer using only the necessary amount of material.
- Benefit: Minimizes resource consumption and lowers the environmental footprint of production.
Energy-Efficient Machinery:
- Contribution: Utilizes advanced, energy-efficient equipment and processes that consume less power while maintaining high productivity.
- Benefit: Reduces energy usage and associated greenhouse gas emissions.
Advanced Material Recycling:
- Contribution: Implements technologies that enable the recycling and reuse of materials within the manufacturing process.
- Benefit: Decreases the need for virgin materials, reduces waste, and supports a circular economy.
Smart Manufacturing and IoT:
- Contribution: Uses interconnected devices and real-time data analytics to optimize production processes, reducing energy consumption and minimizing waste.
- Benefit: Enhances operational efficiency and supports data-driven decision-making for sustainable practices.
Biodegradable and Renewable Materials:
- Contribution: Incorporates sustainable materials such as bioplastics and natural fibers into manufacturing processes.
- Benefit: Reduces reliance on non-renewable resources and lowers environmental impact.
Lean Manufacturing:
- Contribution: Focuses on eliminating waste, optimizing workflows, and improving process efficiency.
- Benefit: Minimizes resource usage, lowers production costs, and enhances overall sustainability.
Closed-Loop Systems:
- Contribution: Designs manufacturing systems that recycle outputs back into the production process, creating a closed-loop cycle.
- Benefit: Reduces waste generation and promotes the continuous use of materials, supporting sustainable resource management.
Emission Control Technologies:
- Contribution: Integrates advanced filtration, scrubbing, and monitoring systems to reduce industrial emissions.
- Benefit: Minimizes air and water pollution, contributing to cleaner production environments.
Conclusion: Advanced manufacturing technologies play a crucial role in promoting sustainability within industrial operations by enhancing resource efficiency, reducing waste and emissions, and enabling the use of sustainable materials. By adopting these technologies, manufacturers can achieve environmentally responsible production, support economic viability, and contribute to the well-being of society.
9. What are the applications of smart manufacturing in the industrial sector, and how do they improve operational efficiency?
Answer:
Smart manufacturing integrates digital technologies, data analytics, and automation to create intelligent and highly efficient production systems. Applications of smart manufacturing in the industrial sector include predictive maintenance, real-time monitoring, automation and robotics, supply chain optimization, and advanced data analytics.
Concepts:
- Smart Manufacturing: The use of interconnected and intelligent systems to optimize production processes and enhance decision-making.
- Industrial Internet of Things (IIoT): Network of connected devices and sensors that collect and exchange data in industrial environments.
Applications and Improvements:
Predictive Maintenance:
- Application: Uses sensors and data analytics to predict equipment failures before they occur.
- Improvement: Reduces unplanned downtime, lowers maintenance costs, and extends the lifespan of machinery.
Real-Time Monitoring and Control:
- Application: Continuously monitors production processes and equipment performance using sensors and IoT devices.
- Improvement: Enables immediate adjustments to optimize efficiency, maintain quality, and prevent disruptions.
Automation and Robotics:
- Application: Deploys automated systems and robots to perform repetitive, precise, and hazardous tasks.
- Improvement: Increases production speed, consistency, and safety while reducing labor costs and human error.
Supply Chain Optimization:
- Application: Utilizes data analytics and connectivity to streamline supply chain operations, including inventory management and logistics.
- Improvement: Enhances supply chain visibility, reduces lead times, and minimizes inventory holding costs.
Advanced Data Analytics:
- Application: Analyzes large volumes of production data to identify trends, optimize processes, and inform strategic decisions.
- Improvement: Drives data-driven decision-making, improves process efficiency, and fosters continuous improvement.
Digital Twins:
- Application: Creates virtual replicas of physical systems to simulate and analyze performance under various conditions.
- Improvement: Facilitates predictive analysis, process optimization, and enhanced product design.
Quality Management:
- Application: Implements automated quality control systems that use vision systems and AI to inspect products.
- Improvement: Ensures consistent product quality, reduces defects, and minimizes rework and scrap.
Energy Management:
- Application: Monitors and optimizes energy usage across manufacturing facilities using smart meters and energy analytics.
- Improvement: Reduces energy consumption, lowers operational costs, and supports sustainability initiatives.
Conclusion: Smart manufacturing applications significantly improve operational efficiency in the industrial sector by enhancing maintenance practices, optimizing production processes, automating tasks, streamlining supply chains, and leveraging data for informed decision-making. These advancements lead to increased productivity, reduced costs, improved quality, and greater overall competitiveness.
10. What are the key components of a smart factory, and how do they interact to enable intelligent manufacturing?
Answer:
A smart factory is an advanced manufacturing environment that leverages interconnected digital technologies, automation, and data analytics to create intelligent and highly efficient production systems. The key components of a smart factory include the Industrial Internet of Things (IIoT), automation and robotics, data analytics and artificial intelligence (AI), cybersecurity, digital twins, and advanced communication networks.
Key Components and Their Interactions:
Industrial Internet of Things (IIoT):
- Role: Connects machines, devices, sensors, and systems to collect and exchange data in real-time.
- Interaction: Provides the foundational connectivity that enables seamless communication between different components of the smart factory.
Automation and Robotics:
- Role: Performs repetitive, precise, and hazardous tasks with minimal human intervention.
- Interaction: Integrates with IIoT devices to receive real-time data and instructions, enhancing operational efficiency and consistency.
Data Analytics and Artificial Intelligence (AI):
- Role: Processes and analyzes vast amounts of data to derive actionable insights, optimize processes, and enable predictive capabilities.
- Interaction: Utilizes data collected from IIoT devices and automated systems to inform decision-making and drive continuous improvement.
Cybersecurity:
- Role: Protects the smart factory’s digital infrastructure from cyber threats and ensures the integrity and confidentiality of data.
- Interaction: Secures data exchanges between IIoT devices, automation systems, and data analytics platforms, maintaining trust and reliability.
Digital Twins:
- Role: Creates virtual replicas of physical assets, processes, or entire factories to simulate and analyze performance under various scenarios.
- Interaction: Uses real-time data from IIoT devices to mirror and predict the behavior of physical systems, enabling proactive maintenance and optimization.
Advanced Communication Networks:
- Role: Facilitates high-speed, reliable, and secure data transmission between all components of the smart factory.
- Interaction: Ensures seamless connectivity and real-time data flow between IIoT devices, automation systems, data analytics platforms, and digital twins.
Human-Machine Interfaces (HMIs):
- Role: Provides intuitive interfaces for human operators to interact with and control smart factory systems.
- Interaction: Allows operators to monitor processes, make informed decisions based on data insights, and intervene when necessary.
Interactions Enabling Intelligent Manufacturing:
- Data Flow: IIoT devices continuously collect data from machines and sensors, transmitting it through advanced communication networks to data analytics and AI systems.
- Automation Control: Data-driven insights from AI inform automation and robotics systems to optimize task execution and production processes.
- Predictive Maintenance: AI analyzes data from IIoT and digital twins to predict equipment failures, scheduling maintenance proactively.
- Continuous Improvement: Feedback from data analytics and digital twins facilitates ongoing process optimization and innovation within the smart factory.
- Security Assurance: Cybersecurity measures protect all data exchanges and system interactions, ensuring the integrity and reliability of the smart factory operations.
Conclusion: A smart factory integrates key components such as IIoT, automation, data analytics, cybersecurity, digital twins, and advanced communication networks to create an intelligent manufacturing environment. These components interact seamlessly to enable real-time data collection, informed decision-making, predictive maintenance, and continuous process optimization, resulting in enhanced efficiency, productivity, and competitiveness in the manufacturing sector.
11. What are the challenges associated with implementing advanced manufacturing technologies in existing industrial setups?
Answer:
Implementing advanced manufacturing technologies in existing industrial setups presents several challenges that organizations must address to ensure successful integration and maximize the benefits of these technologies.
Key Challenges:
High Initial Investment Costs:
- Challenge: Advanced manufacturing technologies often require significant capital expenditure for equipment, software, and infrastructure upgrades.
- Impact: High upfront costs can be a barrier, particularly for small and medium-sized enterprises (SMEs), limiting their ability to adopt new technologies.
Integration with Legacy Systems:
- Challenge: Existing manufacturing systems and processes may not be compatible with new advanced technologies.
- Impact: Integrating new technologies with legacy systems can be technically complex, time-consuming, and may require substantial modifications to existing infrastructure.
Skill Gaps and Workforce Training:
- Challenge: The adoption of advanced technologies necessitates a workforce with specialized skills and expertise.
- Impact: There may be a shortage of qualified personnel, and organizations must invest in training and upskilling programs to prepare employees for new roles and responsibilities.
Data Management and Cybersecurity:
- Challenge: Advanced manufacturing technologies generate large volumes of data that need to be effectively managed and secured.
- Impact: Ensuring data integrity, privacy, and protection against cyber threats requires robust data management strategies and cybersecurity measures, which can be resource-intensive.
Change Management and Organizational Resistance:
- Challenge: Implementing new technologies often requires changes in workflows, processes, and organizational culture.
- Impact: Resistance from employees and management can hinder the adoption process, leading to delays and reduced effectiveness of the new technologies.
Scalability and Flexibility:
- Challenge: Advanced technologies must be scalable to accommodate growth and adaptable to changing production needs.
- Impact: Ensuring that technologies can scale without compromising performance or requiring frequent upgrades is essential for long-term sustainability.
Return on Investment (ROI) Uncertainty:
- Challenge: Predicting the financial benefits and ROI from adopting advanced manufacturing technologies can be difficult.
- Impact: Uncertainty about the return on investment may make organizations hesitant to commit to significant capital expenditures.
Regulatory and Compliance Issues:
- Challenge: Adopting advanced technologies must comply with industry regulations and standards.
- Impact: Navigating complex regulatory landscapes can delay implementation and increase costs associated with compliance.
Supply Chain Disruptions:
- Challenge: Implementing new technologies can temporarily disrupt existing supply chain operations.
- Impact: Managing these disruptions to maintain production continuity requires careful planning and coordination.
Maintenance and Support:
- Challenge: Advanced manufacturing technologies require ongoing maintenance and technical support to ensure optimal performance.
- Impact: Ensuring access to reliable maintenance services and support can be challenging, especially in remote or specialized manufacturing environments.
Conclusion: Implementing advanced manufacturing technologies in existing industrial setups involves navigating challenges related to costs, integration, workforce skills, data management, organizational change, scalability, ROI, compliance, supply chain, and maintenance. Addressing these challenges through strategic planning, investment in training, robust cybersecurity measures, and effective change management practices is essential for successful adoption and realization of the benefits offered by advanced manufacturing technologies.
12. How do digital twins enhance the design and manufacturing processes in advanced manufacturing technologies?
Answer:
Digital twins are virtual replicas of physical assets, processes, or systems that simulate their real-world counterparts’ behavior and performance. In advanced manufacturing technologies, digital twins enhance design and manufacturing processes by enabling real-time monitoring, simulation, and optimization.
Concepts:
- Digital Twin: A dynamic digital model that accurately reflects the physical object or process it represents, incorporating real-time data and analytics.
- Simulation and Modeling: The use of digital twins to test and evaluate scenarios without impacting the actual physical systems.
Enhancements to Design and Manufacturing Processes:
Real-Time Monitoring and Data Integration:
- Enhancement: Digital twins continuously receive data from sensors embedded in physical assets, providing real-time insights into performance and condition.
- Benefit: Enables immediate detection of anomalies, facilitating proactive maintenance and reducing downtime.
Design Optimization:
- Enhancement: Engineers can use digital twins to simulate and analyze different design iterations, assessing their impact on performance and manufacturability.
- Benefit: Accelerates the design process, improves product quality, and reduces the need for multiple physical prototypes.
Predictive Maintenance:
- Enhancement: Digital twins analyze data trends to predict potential equipment failures and maintenance needs.
- Benefit: Minimizes unplanned downtime, extends machinery lifespan, and reduces maintenance costs.
Process Optimization:
- Enhancement: Digital twins model manufacturing processes to identify inefficiencies and optimize workflows.
- Benefit: Enhances operational efficiency, reduces waste, and improves overall production performance.
Virtual Testing and Validation:
- Enhancement: Digital twins allow for virtual testing of products and processes under various conditions without physical trials.
- Benefit: Lowers testing costs, speeds up validation, and ensures products meet quality and safety standards before production.
Enhanced Collaboration:
- Enhancement: Digital twins provide a shared, real-time view of assets and processes, facilitating collaboration among design, engineering, and manufacturing teams.
- Benefit: Improves communication, aligns objectives, and ensures that all stakeholders are working with up-to-date information.
Customization and Flexibility:
- Enhancement: Digital twins support the customization of products by allowing for quick adjustments and simulations based on specific customer requirements.
- Benefit: Enables mass customization, enhancing customer satisfaction and market responsiveness.
Supply Chain Integration:
- Enhancement: Digital twins can model the entire supply chain, identifying bottlenecks and optimizing logistics and inventory management.
- Benefit: Improves supply chain efficiency, reduces lead times, and enhances overall responsiveness to market demands.
Conclusion: Digital twins significantly enhance the design and manufacturing processes in advanced manufacturing technologies by providing real-time monitoring, enabling simulation and optimization, supporting predictive maintenance, and fostering collaboration. By leveraging digital twins, manufacturers can improve product quality, increase operational efficiency, reduce costs, and accelerate innovation, ultimately leading to more competitive and resilient manufacturing operations.
Conclusion:
The above review questions and detailed answers provide a comprehensive understanding of advanced materials and manufacturing technologies. Covering topics such as advanced materials, composites, additive manufacturing, nanomaterials, biomaterials, smart materials, nanocomposites, sustainability, smart manufacturing, digital twins, implementation challenges, and the role of digital twins, these questions help reinforce key concepts and enhance knowledge in the field. By engaging with these review questions, students can solidify their grasp of how advanced materials and manufacturing technologies drive innovation, efficiency, and sustainability in modern industrial operations.
Advanced Materials and Manufacturing Technologies: Thought-Provoking Questions with Detailed Answers:
1. How can nanomaterials revolutionize traditional manufacturing processes, and what potential applications could emerge from their unique properties?
Answer:
Nanomaterials, due to their nanoscale dimensions and enhanced properties, have the potential to revolutionize traditional manufacturing processes by introducing unprecedented levels of strength, flexibility, conductivity, and reactivity. Their unique characteristics enable the creation of materials and components that outperform those made from bulk materials, opening up new possibilities across various industries.
Concepts:
- Nanomaterials: Materials engineered at the nanoscale (1-100 nanometers) that exhibit unique physical and chemical properties.
- Enhanced Properties: Improved mechanical strength, electrical conductivity, thermal stability, and reactivity compared to their bulk counterparts.
Revolutionizing Manufacturing Processes:
Enhanced Material Performance:
- How: Incorporating nanomaterials like carbon nanotubes or graphene into composites can significantly increase tensile strength and durability.
- Impact: Allows for the production of lighter yet stronger components, particularly beneficial in aerospace and automotive industries where weight reduction is crucial.
Advanced Electronics:
- How: Utilizing nanomaterials with superior electrical conductivity and miniaturization capabilities enables the development of smaller, faster, and more efficient electronic devices.
- Impact: Facilitates the creation of advanced sensors, flexible electronics, and high-performance computing components.
Improved Thermal Management:
- How: Nanomaterials with high thermal conductivity, such as graphene, can be integrated into heat sinks and cooling systems.
- Impact: Enhances heat dissipation in electronic devices and industrial machinery, improving performance and longevity.
Catalysis and Chemical Processing:
- How: Nanocatalysts offer higher surface area and reactivity, accelerating chemical reactions.
- Impact: Increases efficiency in chemical manufacturing processes, reducing energy consumption and byproduct formation.
Medical Devices and Implants:
- How: Biocompatible nanomaterials can be used to create implants and medical devices that integrate seamlessly with biological tissues.
- Impact: Improves patient outcomes through enhanced functionality, reduced rejection rates, and the ability to perform complex tasks like targeted drug delivery.
Potential Emerging Applications:
- Smart Textiles: Incorporating nanomaterials to create fabrics that can change color, monitor health metrics, or provide enhanced durability.
- Energy Storage: Developing nanostructured electrodes for batteries and supercapacitors, leading to higher energy densities and faster charging times.
- Environmental Remediation: Using nanomaterials to remove pollutants from air and water through advanced filtration and adsorption techniques.
Conclusion: Nanomaterials hold transformative potential for manufacturing by enabling the creation of materials and components with superior properties. Their integration into traditional manufacturing processes can lead to innovations across multiple sectors, fostering advancements in technology, sustainability, and performance.
2. In what ways do smart materials contribute to the development of adaptive and responsive manufacturing systems?
Answer:
Smart materials possess the ability to change their properties or behavior in response to external stimuli such as temperature, pressure, light, or electric fields. Their integration into manufacturing systems contributes to the development of adaptive and responsive environments that enhance efficiency, precision, and functionality.
Concepts:
- Smart Materials: Materials that can respond dynamically to environmental changes by altering their physical or chemical properties.
- Adaptive Manufacturing Systems: Manufacturing setups that can adjust operations in real-time based on feedback and changing conditions.
Contributions to Adaptive and Responsive Systems:
Real-Time Process Control:
- How: Smart materials like piezoelectric sensors can detect vibrations or pressure changes and provide immediate feedback to control systems.
- Impact: Enables precise adjustments to machinery operations, maintaining optimal performance and reducing defects.
Self-Healing Components:
- How: Incorporating self-healing polymers that can autonomously repair minor damages or wear.
- Impact: Increases the longevity and reliability of manufacturing equipment, reducing maintenance costs and downtime.
Temperature Regulation:
- How: Using shape memory alloys that change shape in response to temperature variations to control cooling or heating processes.
- Impact: Maintains consistent temperature conditions, ensuring uniform product quality and preventing thermal-related defects.
Dynamic Tooling:
- How: Implementing actuators made from smart materials to adjust tool positions or shapes during manufacturing.
- Impact: Enhances the flexibility of production lines, allowing for the manufacture of diverse product designs without extensive retooling.
Energy Efficiency:
- How: Utilizing electrochromic materials that adjust light transmission in response to electrical signals to optimize lighting and reduce energy consumption.
- Impact: Creates more energy-efficient manufacturing environments, lowering operational costs and environmental impact.
Enhanced Safety Systems:
- How: Integrating smart materials that respond to hazardous conditions by triggering alarms or shutting down machinery.
- Impact: Improves workplace safety by providing immediate responses to potential dangers, protecting workers and equipment.
Achieving Adaptive and Responsive Systems:
- Integration of Sensors: Embedding smart materials with sensing capabilities into manufacturing equipment for continuous monitoring.
- Advanced Control Algorithms: Developing software that can interpret sensor data and make real-time adjustments based on predefined parameters.
- Modular Design: Designing manufacturing systems with interchangeable components that can be easily updated or replaced with smart materials.
- Interdisciplinary Collaboration: Encouraging collaboration between material scientists, engineers, and IT specialists to effectively integrate smart materials into manufacturing processes.
Conclusion: Smart materials play a pivotal role in advancing adaptive and responsive manufacturing systems by providing dynamic capabilities that enhance control, efficiency, and safety. Their ability to interact with environmental stimuli fosters the creation of intelligent manufacturing environments that can swiftly adapt to changing conditions, driving innovation and operational excellence.
3. How do biomaterials influence the design and functionality of medical devices in advanced manufacturing technologies?
Answer:
Biomaterials are engineered to interact with biological systems, making them integral to the design and functionality of medical devices. In advanced manufacturing technologies, biomaterials enable the creation of devices that are biocompatible, functional, and tailored to specific medical applications, enhancing patient outcomes and device performance.
Concepts:
- Biomaterials: Materials designed to interact with biological tissues for medical purposes.
- Advanced Manufacturing Technologies: Techniques such as additive manufacturing, CNC machining, and injection molding that enable precise and customized production of medical devices.
Influence on Design and Functionality:
Biocompatibility:
- How: Biomaterials like titanium alloys and certain polymers are non-toxic and do not elicit adverse immune responses.
- Impact: Ensures that medical implants and devices integrate seamlessly with the body, reducing the risk of rejection and complications.
Customization and Personalization:
- How: Advanced manufacturing allows for the production of patient-specific devices using biomaterials, such as custom prosthetics or implants.
- Impact: Enhances fit and functionality, improving comfort and effectiveness for individual patients.
Functional Integration:
- How: Incorporating biomaterials with specific properties, such as elasticity or strength, to match the mechanical requirements of different body parts.
- Impact: Creates devices that mimic natural tissue properties, enhancing performance and longevity.
Drug Delivery Systems:
- How: Using biodegradable biomaterials to create implants or coatings that can deliver drugs at controlled rates.
- Impact: Provides localized and sustained drug release, improving therapeutic outcomes and reducing systemic side effects.
Tissue Engineering and Regenerative Medicine:
- How: Utilizing scaffolds made from biomaterials to support cell growth and tissue regeneration.
- Impact: Facilitates the development of artificial organs and tissues, advancing regenerative medicine and reducing the dependency on donor organs.
Smart Biomaterials:
- How: Developing materials that can respond to biological signals or environmental changes, such as temperature or pH, to perform specific functions.
- Impact: Enables the creation of intelligent medical devices that can adapt to changing conditions within the body, enhancing their functionality and effectiveness.
Achieving Enhanced Design and Functionality:
- Material Selection: Choosing appropriate biomaterials based on their compatibility, mechanical properties, and functionality for specific medical applications.
- Precision Manufacturing: Utilizing advanced manufacturing techniques to ensure the accurate and consistent production of complex biomaterial-based devices.
- Interdisciplinary Research: Collaborating with biomedical engineers, material scientists, and healthcare professionals to innovate and refine biomaterial applications.
- Regulatory Compliance: Ensuring that biomaterial-based medical devices meet stringent regulatory standards for safety and efficacy.
Conclusion: Biomaterials significantly influence the design and functionality of medical devices by providing the necessary biocompatibility, customization, and functional properties required for effective medical applications. Advanced manufacturing technologies facilitate the precise and innovative use of biomaterials, leading to the development of advanced medical devices that improve patient care and expand the possibilities of regenerative medicine.
4. In what ways do smart manufacturing and Industry 4.0 technologies enhance the sustainability of industrial operations?
Answer:
Smart manufacturing and Industry 4.0 technologies enhance the sustainability of industrial operations by optimizing resource usage, reducing waste, improving energy efficiency, and enabling more efficient and transparent supply chains. These technologies integrate digitalization, automation, and data analytics to create more intelligent and responsive manufacturing systems that support environmental and economic sustainability.
Concepts:
- Smart Manufacturing: The use of interconnected systems and advanced technologies to create more flexible, efficient, and intelligent manufacturing processes.
- Industry 4.0: The fourth industrial revolution characterized by the integration of cyber-physical systems, the Internet of Things (IoT), cloud computing, and cognitive computing in manufacturing.
Enhancements to Sustainability:
Resource Optimization:
- How: Utilizing real-time data and analytics to monitor and optimize the use of materials, energy, and water in manufacturing processes.
- Impact: Minimizes resource consumption, reduces costs, and lowers the environmental footprint of operations.
Waste Reduction:
- How: Implementing predictive maintenance and quality control systems to prevent defects and reduce scrap and rework.
- Impact: Decreases waste generation, enhancing both economic efficiency and environmental sustainability.
Energy Efficiency:
- How: Using smart sensors and energy management systems to monitor and control energy usage across manufacturing facilities.
- Impact: Reduces energy consumption and associated greenhouse gas emissions, contributing to lower operational costs and environmental benefits.
Circular Economy Integration:
- How: Facilitating the reuse, recycling, and remanufacturing of products and materials through advanced tracking and management systems.
- Impact: Promotes sustainable resource cycles, reduces reliance on virgin materials, and minimizes waste.
Supply Chain Transparency:
- How: Leveraging IoT and blockchain technologies to provide real-time visibility into supply chain operations, ensuring sustainable sourcing and logistics.
- Impact: Enhances the ability to trace materials, ensure ethical sourcing, and optimize logistics for reduced emissions and improved efficiency.
Flexible and Adaptive Production:
- How: Utilizing advanced manufacturing systems that can quickly adapt to changing demands and production requirements, reducing overproduction and underutilization.
- Impact: Aligns production closely with actual demand, preventing waste and improving resource allocation.
Enhanced Monitoring and Reporting:
- How: Implementing comprehensive monitoring systems that track sustainability metrics and provide data for informed decision-making.
- Impact: Facilitates continuous improvement in sustainability practices and ensures compliance with environmental regulations.
Smart Logistics:
- How: Optimizing transportation routes and methods using data analytics to reduce fuel consumption and emissions.
- Impact: Lowers the environmental impact of logistics operations and enhances overall supply chain efficiency.
Achieving Sustainability through Smart Manufacturing:
- Investment in Technology: Allocating resources to adopt smart technologies that support sustainable practices.
- Employee Training: Educating the workforce on the importance of sustainability and how to leverage smart technologies to achieve it.
- Collaborative Efforts: Engaging with suppliers, partners, and stakeholders to promote sustainability across the entire value chain.
- Continuous Improvement: Regularly reviewing and enhancing sustainability strategies based on data insights and technological advancements.
Conclusion: Smart manufacturing and Industry 4.0 technologies play a crucial role in enhancing the sustainability of industrial operations by enabling more efficient use of resources, reducing waste and emissions, and promoting transparent and responsible supply chains. By integrating these advanced technologies, manufacturers can achieve significant environmental and economic benefits, supporting long-term sustainability goals and fostering a more resilient and responsible industrial ecosystem.
5. How do digital twins transform the maintenance and lifecycle management of advanced manufacturing systems?
Answer:
Digital twins, which are virtual replicas of physical systems, transform the maintenance and lifecycle management of advanced manufacturing systems by enabling real-time monitoring, predictive maintenance, and data-driven decision-making. This integration enhances the reliability, efficiency, and longevity of manufacturing equipment and processes.
Concepts:
- Digital Twin: A digital representation of a physical object or system that simulates its real-time performance and behavior.
- Lifecycle Management: The process of managing the entire lifecycle of a product or system, from design and manufacturing to maintenance and disposal.
Transformations in Maintenance and Lifecycle Management:
Real-Time Monitoring:
- How: Digital twins continuously receive data from sensors embedded in manufacturing systems, providing real-time insights into equipment performance and health.
- Impact: Enables immediate detection of anomalies and performance deviations, allowing for timely interventions before issues escalate.
Predictive Maintenance:
- How: Utilizing data analytics and machine learning algorithms within digital twins to predict potential equipment failures based on historical and real-time data.
- Impact: Shifts maintenance from reactive and scheduled approaches to proactive strategies, reducing unexpected downtime and extending equipment lifespan.
Simulation and Scenario Analysis:
- How: Digital twins allow for the simulation of various operational scenarios and stress conditions without impacting actual manufacturing systems.
- Impact: Facilitates testing and optimization of maintenance strategies, process improvements, and system upgrades in a risk-free virtual environment.
Optimized Maintenance Scheduling:
- How: Analyzing data from digital twins to determine the optimal times for maintenance activities based on equipment usage and condition.
- Impact: Minimizes production interruptions, balances maintenance workloads, and reduces overall maintenance costs.
Enhanced Decision-Making:
- How: Providing comprehensive data and insights from digital twins to support informed decision-making regarding equipment upgrades, replacements, and process changes.
- Impact: Improves the accuracy and effectiveness of maintenance and lifecycle management decisions, leading to better resource allocation and operational efficiency.
Lifecycle Tracking and Documentation:
- How: Maintaining detailed records of equipment performance, maintenance activities, and lifecycle stages within digital twins.
- Impact: Streamlines documentation processes, ensures compliance with regulatory requirements, and provides valuable historical data for future reference and analysis.
Integration with Supply Chain Management:
- How: Linking digital twins with supply chain systems to ensure timely availability of spare parts and maintenance resources based on predictive insights.
- Impact: Enhances supply chain responsiveness, reduces lead times for parts procurement, and ensures that necessary resources are available when needed.
Continuous Improvement and Innovation:
- How: Leveraging insights from digital twins to identify opportunities for process improvements, energy savings, and innovation in manufacturing systems.
- Impact: Drives continuous improvement initiatives, fostering a culture of innovation and operational excellence within the organization.
Achieving Effective Transformation:
- Data Integration: Ensuring seamless integration of digital twins with existing manufacturing systems and data sources for comprehensive monitoring.
- Advanced Analytics: Employing sophisticated data analytics and machine learning techniques to extract actionable insights from digital twin data.
- Cross-Functional Collaboration: Facilitating collaboration between maintenance teams, engineers, and IT professionals to effectively utilize digital twin capabilities.
- Scalability and Flexibility: Designing digital twin implementations that can scale with the growth of manufacturing operations and adapt to changing requirements.
Conclusion: Digital twins revolutionize the maintenance and lifecycle management of advanced manufacturing systems by providing a dynamic and intelligent platform for real-time monitoring, predictive maintenance, and informed decision-making. This integration enhances the reliability, efficiency, and longevity of manufacturing equipment, driving operational excellence and supporting sustainable manufacturing practices.
6. How do nanocomposites enhance the performance of traditional materials, and what are the challenges in their widespread adoption in manufacturing?
Answer:
Nanocomposites enhance the performance of traditional materials by incorporating nanoscale reinforcements, such as nanoparticles, nanofibers, or nanotubes, into a matrix material. These nanostructures significantly improve mechanical, thermal, electrical, and barrier properties, making nanocomposites superior to their conventional counterparts. However, their widespread adoption in manufacturing faces several challenges that need to be addressed.
Concepts:
- Nanocomposites: Composite materials where one of the phases has at least one dimension in the nanometer range.
- Matrix and Reinforcement: The matrix binds the reinforcements, distributing stress and enhancing overall material properties.
Enhancements in Performance:
Mechanical Strength:
- How: Nanofillers like carbon nanotubes increase the tensile strength and stiffness of the composite.
- Impact: Produces materials that are stronger and more durable, suitable for high-stress applications in aerospace and automotive industries.
Thermal Stability:
- How: Incorporating nanoparticles with high thermal conductivity improves heat dissipation and thermal resistance.
- Impact: Enables the use of nanocomposites in environments with extreme temperatures, enhancing the safety and reliability of components.
Electrical Conductivity:
- How: Adding conductive nanomaterials like graphene enhances the electrical properties of the composite.
- Impact: Facilitates the development of advanced electronics, sensors, and energy storage devices with improved performance.
Barrier Properties:
- How: Nanofillers can create a tortuous path for gas and moisture molecules, reducing permeability.
- Impact: Improves the barrier properties of packaging materials, extending the shelf life of food products and protecting sensitive electronics.
Lightweighting:
- How: Nanocomposites can achieve high strength with lower weight compared to traditional materials.
- Impact: Reduces the overall weight of products, enhancing fuel efficiency in transportation and reducing energy consumption in various applications.
Challenges in Widespread Adoption:
Dispersion and Homogeneity:
- Challenge: Achieving uniform dispersion of nanofillers within the matrix to maximize property enhancements.
- Impact: Poor dispersion can lead to agglomeration, resulting in inconsistent material properties and reduced performance.
Manufacturing Processes:
- Challenge: Integrating nanocomposite production into existing manufacturing workflows requires specialized equipment and techniques.
- Impact: Increases production complexity and costs, hindering scalability and economic feasibility.
Cost of Nanomaterials:
- Challenge: High costs associated with producing and incorporating nanomaterials into composites.
- Impact: Limits the affordability of nanocomposites for mass-market applications, making them more suitable for high-value or specialized uses.
Health and Safety Concerns:
- Challenge: Potential health risks associated with handling nanomaterials, including inhalation and environmental impact.
- Impact: Necessitates stringent safety protocols and regulatory compliance, increasing operational costs and complexity.
Standardization and Quality Control:
- Challenge: Lack of standardized testing methods and quality control measures for nanocomposites.
- Impact: Leads to variability in material properties and reliability, reducing trust and acceptance in critical applications.
Environmental Impact:
- Challenge: Ensuring that nanocomposites are recyclable and do not pose environmental hazards during disposal.
- Impact: Addresses sustainability concerns, aligning with global environmental regulations and consumer expectations.
Regulatory Hurdles:
- Challenge: Navigating complex regulatory landscapes governing the use of nanomaterials in products.
- Impact: Delays the commercialization and adoption of nanocomposite technologies, increasing time-to-market and costs.
Conclusion: Nanocomposites offer significant performance enhancements over traditional materials, making them valuable for a wide range of high-performance applications. However, challenges related to dispersion, manufacturing integration, cost, health and safety, standardization, environmental impact, and regulatory compliance must be addressed to facilitate their widespread adoption in manufacturing. Overcoming these hurdles will unlock the full potential of nanocomposites, driving innovation and advancing material science in industrial applications.
7. How do advanced manufacturing technologies facilitate the development of sustainable and eco-friendly products?
Answer:
Advanced manufacturing technologies facilitate the development of sustainable and eco-friendly products by enabling efficient resource utilization, reducing waste, incorporating renewable materials, and optimizing production processes. These technologies integrate digitalization, automation, and precision engineering to create products that are environmentally responsible throughout their lifecycle.
Concepts:
- Sustainable Manufacturing: Production methods that minimize environmental impact, conserve energy and resources, and promote social responsibility.
- Eco-Friendly Products: Products designed with consideration for their environmental impact, including material selection, energy consumption, and end-of-life disposal.
Facilitations through Advanced Technologies:
Additive Manufacturing (3D Printing):
- How: Builds products layer by layer, using only the necessary material, which significantly reduces material waste compared to subtractive methods.
- Impact: Minimizes resource consumption and supports the creation of lightweight structures, enhancing energy efficiency in product use.
Lean Manufacturing:
- How: Focuses on eliminating waste, optimizing workflows, and improving process efficiency through techniques such as Just-In-Time (JIT) production.
- Impact: Reduces excess inventory, minimizes resource usage, and lowers production costs, contributing to more sustainable operations.
Automation and Robotics:
- How: Enhances precision and consistency in manufacturing processes, reducing defects and the need for rework.
- Impact: Decreases material waste, improves product quality, and increases operational efficiency, supporting sustainable production goals.
Advanced Material Recycling:
- How: Utilizes technologies that enable the recycling and reuse of materials within the manufacturing process, such as closed-loop recycling systems.
- Impact: Reduces the need for virgin materials, lowers environmental impact, and promotes a circular economy.
Energy-Efficient Machinery:
- How: Incorporates energy-efficient equipment and smart energy management systems to monitor and optimize energy usage.
- Impact: Lowers energy consumption, reduces greenhouse gas emissions, and decreases operational costs, aligning with sustainability objectives.
Digital Twins and Simulation:
- How: Uses virtual models to simulate and optimize manufacturing processes, identifying areas for improvement without physical trials.
- Impact: Enhances process efficiency, reduces trial-and-error waste, and minimizes the environmental footprint of product development.
Smart Supply Chain Management:
- How: Implements IoT and data analytics to optimize supply chain operations, ensuring efficient logistics and reducing transportation emissions.
- Impact: Enhances supply chain transparency, reduces lead times, and lowers the carbon footprint associated with logistics and inventory management.
Biodegradable and Renewable Materials:
- How: Incorporates materials that are biodegradable, renewable, or have a lower environmental impact into product design and manufacturing.
- Impact: Reduces reliance on non-renewable resources, lowers environmental pollution, and supports sustainable product lifecycles.
Process Optimization and Continuous Improvement:
- How: Employs advanced analytics and machine learning to continuously monitor and optimize manufacturing processes for efficiency and sustainability.
- Impact: Identifies and implements improvements that reduce resource consumption, minimize waste, and enhance overall sustainability.
Eco-Design Principles:
- How: Integrates eco-design strategies that consider the entire product lifecycle, from material selection and manufacturing to use and disposal.
- Impact: Ensures that products are designed for sustainability, facilitating easier recycling, reducing environmental impact, and enhancing product longevity.
Achieving Sustainable and Eco-Friendly Products:
- Holistic Approach: Combining multiple advanced manufacturing technologies to address various aspects of sustainability, such as material efficiency, energy consumption, and waste reduction.
- Collaboration and Innovation: Encouraging collaboration between engineers, material scientists, and sustainability experts to innovate and develop eco-friendly solutions.
- Regulatory Compliance: Ensuring that manufacturing practices and products comply with environmental regulations and standards, promoting responsible production.
- Consumer Engagement: Educating consumers about the sustainability benefits of advanced manufacturing products, fostering demand for eco-friendly options.
Conclusion: Advanced manufacturing technologies play a critical role in developing sustainable and eco-friendly products by enabling efficient resource use, reducing waste, incorporating renewable materials, and optimizing production processes. These technologies support the creation of products that are not only high in quality and performance but also environmentally responsible, contributing to the broader goals of sustainability and ecological preservation.
8. What role do nanotechnology and advanced materials play in the development of next-generation energy storage systems?
Answer:
Nanotechnology and advanced materials are pivotal in the development of next-generation energy storage systems by enhancing the performance, efficiency, and capacity of batteries and supercapacitors. These innovations address the increasing demand for reliable, high-density, and long-lasting energy storage solutions essential for applications ranging from portable electronics to electric vehicles and renewable energy integration.
Concepts:
- Nanotechnology: The manipulation of matter on an atomic or molecular scale to create materials with novel properties.
- Advanced Materials: Materials engineered to exhibit superior characteristics, such as high conductivity, large surface area, and enhanced mechanical properties.
Roles in Energy Storage Development:
Enhanced Electrode Materials:
- How: Utilizing nanostructured materials like graphene, carbon nanotubes, and silicon nanoparticles in battery electrodes.
- Impact: Increases the surface area for electrochemical reactions, enhancing charge capacity and reducing charging times.
Improved Conductivity:
- How: Incorporating conductive nanomaterials into electrodes and electrolytes to facilitate efficient electron and ion transport.
- Impact: Enhances the overall conductivity of the energy storage system, leading to faster charge/discharge rates and higher power outputs.
Increased Energy Density:
- How: Developing advanced nanomaterials that can store more energy per unit volume or mass.
- Impact: Enables the creation of batteries and supercapacitors with higher energy densities, extending the runtime of portable devices and the range of electric vehicles.
Durability and Longevity:
- How: Engineering nanomaterials that mitigate degradation mechanisms, such as electrode cracking and electrolyte decomposition.
- Impact: Extends the lifespan of energy storage systems, reducing the need for frequent replacements and lowering lifecycle costs.
Lightweight Structures:
- How: Using nanocomposites and lightweight nanomaterials in battery casings and components.
- Impact: Reduces the overall weight of energy storage devices, which is particularly beneficial for applications in aerospace and electric transportation.
Flexible and Wearable Energy Storage:
- How: Developing nanomaterials that enable the creation of flexible and stretchable batteries.
- Impact: Facilitates the integration of energy storage systems into wearable electronics and flexible devices, expanding their functionality and usability.
Thermal Management:
- How: Incorporating nanomaterials with high thermal conductivity to dissipate heat generated during charging and discharging.
- Impact: Prevents overheating, enhancing safety and performance stability of energy storage systems.
Sustainable and Eco-Friendly Materials:
- How: Utilizing environmentally benign nanomaterials and advanced recycling techniques.
- Impact: Promotes the development of sustainable energy storage solutions that minimize environmental impact and support circular economy principles.
Achieving Next-Generation Energy Storage:
- Research and Development: Investing in R&D to discover and optimize nanomaterials for specific energy storage applications.
- Scalability: Developing manufacturing processes that can produce nanomaterials at scale while maintaining quality and performance.
- Integration with Existing Systems: Ensuring compatibility of advanced materials with current energy storage architectures and electronics.
- Cost Reduction: Innovating cost-effective synthesis and fabrication methods to make nanotechnology-based energy storage systems economically viable.
Conclusion: Nanotechnology and advanced materials are instrumental in driving the evolution of energy storage systems, offering substantial improvements in energy density, power output, durability, and efficiency. These advancements are essential for meeting the growing energy demands of modern technologies and supporting the transition to sustainable energy solutions. By leveraging the unique properties of nanomaterials, the development of next-generation energy storage systems can achieve higher performance, greater reliability, and enhanced sustainability.
9. How can the integration of AI and machine learning with advanced materials accelerate innovation in manufacturing technologies?
Answer:
The integration of Artificial Intelligence (AI) and Machine Learning (ML) with advanced materials accelerates innovation in manufacturing technologies by enabling data-driven design, optimizing material properties, predicting performance, and automating complex manufacturing processes. This synergy fosters a more efficient and innovative approach to material science and manufacturing, driving advancements across various industries.
Concepts:
- Artificial Intelligence (AI): The simulation of human intelligence processes by machines, particularly computer systems.
- Machine Learning (ML): A subset of AI that involves algorithms and statistical models enabling machines to improve their performance on tasks through experience.
Acceleration of Innovation:
Predictive Material Design:
- How: AI and ML algorithms analyze vast datasets of material properties and performance metrics to predict new material compositions and structures.
- Impact: Speeds up the discovery of novel materials with desired characteristics, reducing the time and cost associated with experimental testing.
Optimization of Material Properties:
- How: ML models identify the optimal combinations of material components and processing parameters to achieve specific properties such as strength, flexibility, or conductivity.
- Impact: Enhances the performance of materials tailored for particular applications, improving product quality and functionality.
Process Automation and Control:
- How: AI-driven systems monitor and adjust manufacturing processes in real-time based on feedback from sensors and predictive models.
- Impact: Increases manufacturing precision, reduces variability, and minimizes defects, leading to more consistent and high-quality products.
Failure Prediction and Maintenance:
- How: ML algorithms analyze data from manufacturing equipment to predict potential failures and schedule preventive maintenance.
- Impact: Reduces downtime, extends equipment lifespan, and ensures uninterrupted production, enhancing overall manufacturing efficiency.
Supply Chain Optimization:
- How: AI systems analyze supply chain data to forecast demand, optimize inventory levels, and streamline logistics.
- Impact: Improves resource allocation, reduces lead times, and minimizes waste, supporting sustainable manufacturing practices.
Customization and Personalization:
- How: AI algorithms enable the mass customization of products by analyzing consumer data and adjusting manufacturing processes accordingly.
- Impact: Facilitates the production of personalized products without sacrificing efficiency, enhancing customer satisfaction and market competitiveness.
Accelerated Prototyping and Testing:
- How: AI and ML streamline the prototyping phase by predicting performance outcomes and identifying optimal design iterations.
- Impact: Reduces the time required to develop and validate new products, accelerating time-to-market and fostering innovation.
Enhanced Simulation and Modeling:
- How: AI-powered simulations model complex material behaviors and manufacturing processes, providing deeper insights into system performance.
- Impact: Enables more accurate predictions of how materials and processes will perform under various conditions, guiding informed decision-making.
Energy Efficiency Improvements:
- How: AI optimizes energy usage in manufacturing processes by analyzing consumption patterns and identifying opportunities for reduction.
- Impact: Lowers energy costs and minimizes the environmental impact of manufacturing operations, aligning with sustainability goals.
Advanced Quality Control:
- How: ML algorithms analyze data from quality inspections to detect patterns and identify root causes of defects.
- Impact: Enhances quality assurance processes, ensuring that products meet stringent quality standards and reducing the incidence of faulty products.
Achieving Accelerated Innovation:
- Data Integration: Consolidating data from various sources to provide comprehensive inputs for AI and ML models.
- Collaborative Platforms: Creating environments where data scientists, material scientists, and engineers can collaborate effectively.
- Continuous Learning: Implementing systems that continuously learn and adapt based on new data and outcomes, ensuring ongoing improvement and innovation.
- Investment in Infrastructure: Providing the necessary computational resources and software tools to support AI and ML integration with advanced materials research and manufacturing.
Conclusion: The integration of AI and machine learning with advanced materials significantly accelerates innovation in manufacturing technologies by enabling smarter design, optimized processes, predictive maintenance, and enhanced customization. This convergence fosters a more efficient, responsive, and innovative manufacturing landscape, driving advancements that meet the evolving demands of various industries and promoting sustainable and high-performance production practices.
10. What ethical considerations must be addressed when developing and implementing advanced materials in manufacturing technologies?
Answer:
When developing and implementing advanced materials in manufacturing technologies, several ethical considerations must be addressed to ensure responsible innovation, protect human health and the environment, and promote social equity. These considerations encompass the entire lifecycle of materials, from research and development to production, use, and disposal.
Concepts:
- Ethical Manufacturing: The practice of producing goods in a manner that is socially responsible, environmentally sustainable, and economically viable.
- Lifecycle Assessment: Evaluating the environmental, social, and economic impacts of a material or product throughout its entire lifecycle.
Ethical Considerations:
Environmental Impact:
- Concern: Advanced materials may have unintended environmental consequences during production, use, or disposal.
- Addressing It: Conduct comprehensive lifecycle assessments to understand and mitigate environmental impacts, promote the use of eco-friendly materials, and implement recycling and waste reduction strategies.
Health and Safety:
- Concern: Exposure to certain nanomaterials or advanced composites may pose health risks to workers and consumers.
- Addressing It: Ensure rigorous safety testing, implement proper handling protocols, and adhere to regulatory standards to protect human health.
Sustainable Sourcing:
- Concern: The extraction and sourcing of raw materials for advanced materials can lead to environmental degradation and social injustices.
- Addressing It: Source materials responsibly, prioritize renewable or abundant resources, and ensure fair labor practices in the supply chain.
Transparency and Disclosure:
- Concern: Lack of transparency about the composition and potential risks of advanced materials can undermine trust and accountability.
- Addressing It: Maintain transparency in material disclosures, provide clear information about potential risks and benefits, and engage stakeholders in informed decision-making.
Intellectual Property and Access:
- Concern: Patents and proprietary technologies can limit access to advanced materials, exacerbating social and economic disparities.
- Addressing It: Promote fair licensing practices, support open research initiatives, and ensure equitable access to advanced materials technologies.
Privacy and Data Security:
- Concern: Advanced materials development often involves the collection and analysis of sensitive data, which may be vulnerable to breaches.
- Addressing It: Implement robust data security measures, comply with data protection regulations, and ensure ethical data management practices.
Bias and Fairness in AI Integration:
- Concern: When AI and ML are used to develop and implement advanced materials, biases in algorithms can lead to unfair or discriminatory outcomes.
- Addressing It: Ensure diverse and representative data sets, regularly audit algorithms for bias, and implement fairness-aware AI practices.
Social Responsibility and Inclusivity:
- Concern: Advanced materials technologies may inadvertently exclude marginalized communities or fail to address their specific needs.
- Addressing It: Engage with diverse communities, consider the social implications of material applications, and design inclusive technologies that benefit a broad range of users.
Long-Term Sustainability:
- Concern: Advanced materials may offer short-term benefits but contribute to long-term sustainability challenges.
- Addressing It: Prioritize the development of materials that support sustainable practices, promote durability and longevity, and facilitate end-of-life recycling and reuse.
Regulatory Compliance and Ethical Standards:
- Concern: Rapid advancements in materials science may outpace existing regulations, leading to ethical dilemmas and compliance issues.
- Addressing It: Collaborate with regulatory bodies to develop and adhere to updated standards, participate in policy discussions, and proactively address potential ethical concerns.
Implementing Ethical Practices:
- Ethical Frameworks: Establish organizational ethical guidelines that govern the development and use of advanced materials.
- Stakeholder Engagement: Involve diverse stakeholders in the decision-making process to ensure that multiple perspectives are considered.
- Continuous Monitoring: Regularly assess the ethical implications of advanced materials technologies and adjust practices accordingly to address emerging concerns.
- Education and Training: Provide education and training to employees and stakeholders about the ethical considerations and responsibilities associated with advanced materials.
Conclusion: Developing and implementing advanced materials in manufacturing technologies requires a careful consideration of ethical implications to ensure responsible innovation. By addressing environmental impacts, health and safety, sustainable sourcing, transparency, intellectual property, data security, bias, social responsibility, long-term sustainability, and regulatory compliance, manufacturers can promote ethical practices that benefit society, protect the environment, and foster trust and accountability in advanced materials technologies.
11. How can the use of biodegradable materials in advanced manufacturing contribute to reducing environmental pollution, and what are the limitations of these materials?
Answer:
The use of biodegradable materials in advanced manufacturing plays a significant role in reducing environmental pollution by minimizing waste accumulation, lowering the dependency on non-renewable resources, and promoting sustainable disposal practices. However, while biodegradable materials offer numerous environmental benefits, they also come with certain limitations that must be addressed to maximize their effectiveness.
Concepts:
- Biodegradable Materials: Materials that can be broken down by microorganisms into natural substances like water, carbon dioxide, and biomass.
- Environmental Pollution: The introduction of harmful substances into the environment, leading to adverse effects on ecosystems and human health.
Contributions to Reducing Environmental Pollution:
Waste Reduction:
- How: Biodegradable materials decompose naturally over time, reducing the volume of waste that ends up in landfills and oceans.
- Impact: Mitigates the accumulation of persistent pollutants and decreases the burden on waste management systems.
Lower Carbon Footprint:
- How: Many biodegradable materials are derived from renewable resources, which typically have a lower carbon footprint compared to fossil fuel-based materials.
- Impact: Reduces greenhouse gas emissions associated with material production and disposal, contributing to climate change mitigation.
Resource Conservation:
- How: Utilizing biodegradable materials often involves using renewable resources such as plant-based polymers, which are replenished naturally.
- Impact: Decreases reliance on finite non-renewable resources, promoting sustainable resource management.
Reduced Microplastic Pollution:
- How: Unlike conventional plastics, biodegradable materials break down into non-toxic substances, preventing the formation of microplastics.
- Impact: Protects marine and terrestrial ecosystems from the harmful effects of microplastic ingestion and accumulation.
Enhanced Soil Health:
- How: Biodegradable materials can enrich soil as they decompose, providing nutrients for plant growth.
- Impact: Improves soil fertility and supports agricultural productivity without the need for synthetic fertilizers.
Limitations of Biodegradable Materials:
Degradation Conditions:
- Limitation: Biodegradable materials often require specific conditions, such as industrial composting facilities with controlled temperature and humidity, to break down effectively.
- Impact: Inadequate disposal infrastructure can result in incomplete degradation, limiting environmental benefits.
Mechanical and Thermal Properties:
- Limitation: Biodegradable materials may exhibit inferior mechanical strength, flexibility, or thermal resistance compared to traditional materials.
- Impact: Restricts their use in applications that demand high durability or performance, necessitating further material innovation.
Cost Factors:
- Limitation: Biodegradable materials can be more expensive to produce than conventional materials, affecting their economic viability.
- Impact: Higher costs may limit widespread adoption, particularly in cost-sensitive industries and applications.
Shelf Life and Stability:
- Limitation: Some biodegradable materials may have shorter shelf lives or be more susceptible to degradation over time, even under non-degradative conditions.
- Impact: Reduces their practicality for long-term storage and use, requiring careful handling and storage solutions.
Resource Competition:
- Limitation: The production of biodegradable materials from agricultural resources can compete with food production, leading to potential food security concerns.
- Impact: Balances the benefits of biodegradability with the need to ensure sustainable and ethical sourcing of raw materials.
Recycling Challenges:
- Limitation: Biodegradable materials are often incompatible with existing recycling systems, complicating waste segregation and processing.
- Impact: Requires the development of specialized recycling facilities and public education to ensure proper disposal.
Performance Limitations:
- Limitation: In certain applications, biodegradable materials may not match the performance levels of traditional materials, limiting their functional use.
- Impact: Necessitates the continued research and development of advanced biodegradable materials that can meet diverse performance requirements.
Achieving Effective Use of Biodegradable Materials:
- Infrastructure Development: Investing in industrial composting facilities and improving waste management systems to support the effective degradation of biodegradable materials.
- Material Innovation: Enhancing the mechanical and thermal properties of biodegradable materials through research and the incorporation of nanomaterials or other additives.
- Economic Incentives: Providing subsidies or incentives to lower the production costs of biodegradable materials, encouraging broader adoption.
- Public Awareness: Educating consumers and industries about the proper disposal and benefits of biodegradable materials to ensure effective end-of-life management.
- Sustainable Sourcing: Developing biodegradable materials from non-food renewable resources to avoid competition with food production and ensure ethical sourcing.
Conclusion: Biodegradable materials significantly contribute to reducing environmental pollution by enabling sustainable waste management, lowering carbon footprints, conserving resources, and preventing microplastic pollution. However, their effectiveness is limited by factors such as degradation conditions, material properties, costs, and recycling challenges. Addressing these limitations through infrastructure development, material innovation, economic incentives, public awareness, and sustainable sourcing is essential to fully harness the environmental benefits of biodegradable materials in advanced manufacturing technologies.
12. How can the development of smart composites impact the future of aerospace manufacturing, and what are the potential benefits and challenges associated with their use?
Answer:
The development of smart composites, which are advanced materials integrating sensors, actuators, or other smart functionalities into composite structures, has the potential to significantly impact the future of aerospace manufacturing. These materials enable the creation of intelligent aircraft components that can monitor their own health, adapt to changing conditions, and enhance overall performance and safety.
Concepts:
- Smart Composites: Composite materials embedded with sensing and actuation capabilities to provide real-time data and responsive functionalities.
- Aerospace Manufacturing: The production of aircraft and spacecraft, requiring materials that offer high performance, durability, and reliability under extreme conditions.
Impact on Aerospace Manufacturing:
Structural Health Monitoring:
- How: Integrating sensors into smart composites allows for continuous monitoring of structural integrity, detecting issues such as cracks, delamination, or stress concentrations.
- Benefit: Enables proactive maintenance, reduces the risk of in-flight failures, and enhances overall safety by ensuring that structural issues are identified and addressed before they escalate.
Adaptive Aerodynamics:
- How: Actuators embedded in smart composites can adjust the shape or surface properties of aircraft components in response to aerodynamic conditions.
- Benefit: Improves fuel efficiency, enhances maneuverability, and optimizes aerodynamic performance under varying flight conditions, contributing to reduced operational costs and environmental impact.
Lightweighting:
- How: Smart composites can achieve high strength with lower weight, integrating multiple functionalities into a single material.
- Benefit: Reduces the overall weight of aircraft, leading to improved fuel efficiency, increased payload capacity, and enhanced performance.
Energy Harvesting:
- How: Incorporating piezoelectric or thermoelectric materials into smart composites enables the harvesting of energy from vibrations or temperature gradients.
- Benefit: Powers embedded sensors and electronics without the need for external power sources, increasing the autonomy and sustainability of aircraft systems.
Enhanced Durability and Longevity:
- How: Smart composites can respond to environmental stressors by adapting their properties or activating protective measures.
- Benefit: Extends the lifespan of aircraft components, reduces maintenance frequency, and lowers lifecycle costs by minimizing wear and tear.
Potential Benefits:
Increased Safety:
- Real-time monitoring and adaptive functionalities enhance the ability to prevent accidents and ensure the structural integrity of aircraft.
Operational Efficiency:
- Lightweight and adaptive materials contribute to better fuel economy and reduced emissions, aligning with sustainability goals.
Cost Savings:
- Proactive maintenance and extended component lifespans reduce maintenance costs and downtime, improving the overall economic efficiency of aerospace operations.
Innovative Design Possibilities:
- The integration of multiple functionalities into smart composites allows for more innovative and optimized aircraft designs, pushing the boundaries of aerospace engineering.
Challenges Associated with Smart Composites:
Complex Manufacturing Processes:
- Challenge: Embedding sensors and actuators into composite materials requires advanced manufacturing techniques and precise integration methods.
- Impact: Increases production complexity, time, and costs, potentially limiting scalability and widespread adoption.
Reliability and Durability of Embedded Systems:
- Challenge: Ensuring that embedded sensors and actuators maintain functionality and accuracy over the long-term operational life of aircraft.
- Impact: Requires robust design and testing to prevent failures that could compromise safety and performance.
Data Management and Analysis:
- Challenge: Collecting and processing vast amounts of data from smart composites necessitates advanced data management and analytics systems.
- Impact: Increases the complexity of maintenance and monitoring systems, requiring skilled personnel and sophisticated software solutions.
Cost Considerations:
- Challenge: The initial cost of developing and implementing smart composites can be high, driven by material costs and the need for specialized manufacturing equipment.
- Impact: May limit adoption to high-value applications initially, delaying broader integration across the aerospace industry.
Regulatory and Certification Hurdles:
- Challenge: Ensuring that smart composites meet stringent aerospace regulations and standards requires extensive testing and certification processes.
- Impact: Lengthens the development timeline and increases costs, necessitating close collaboration with regulatory bodies.
Integration with Existing Systems:
- Challenge: Incorporating smart composites into existing aircraft structures and systems requires compatibility and seamless integration.
- Impact: May require redesigning certain components and updating maintenance protocols, complicating the adoption process.
Achieving Successful Implementation:
- Research and Development: Investing in R&D to innovate manufacturing techniques and enhance the reliability of smart composites.
- Collaboration: Engaging with industry partners, academic institutions, and regulatory bodies to develop standards and best practices for smart composite integration.
- Training and Education: Equipping the workforce with the necessary skills and knowledge to manufacture, maintain, and utilize smart composites effectively.
- Cost-Benefit Analysis: Conducting thorough analyses to demonstrate the long-term economic and safety benefits of smart composites, justifying initial investments.
Conclusion: Smart composites have the potential to transform aerospace manufacturing by enhancing safety, efficiency, and innovation through their intelligent functionalities. While they offer substantial benefits, challenges related to manufacturing complexity, reliability, cost, data management, regulatory compliance, and system integration must be addressed to realize their full potential. Overcoming these challenges through dedicated research, collaboration, and strategic investment will pave the way for the widespread adoption of smart composites in the aerospace industry, driving advancements in aircraft performance and sustainability.
Conclusion:
The above thought-provoking questions and detailed answers delve into the complexities and innovations associated with advanced materials and manufacturing technologies. Covering topics such as nanomaterials, smart composites, biomaterials, sustainability, AI integration, and ethical considerations, these questions encourage students to explore the transformative impact of these technologies on various industries. By engaging with these inquiries, students are prompted to think critically about how advanced materials can drive innovation, enhance performance, and promote sustainable practices in manufacturing. This approach not only deepens their understanding but also fosters a proactive mindset towards addressing the challenges and opportunities presented by the evolving landscape of industrial and manufacturing technologies, making learning an engaging and dynamic process.