Manufacturing Quality Control and Assurance
Manufacturing quality control and assurance form the backbone of consistent, safe, and reliable industrial production. In a competitive manufacturing environment, delivering defect-free products that meet customer specifications is not only a strategic advantage but also a regulatory necessity. Rooted in the broader field of Industrial and Manufacturing Technologies, this discipline blends rigorous inspection methods with system-wide process monitoring to identify, correct, and prevent errors throughout the production cycle.
The evolution of quality assurance has paralleled the rise of digital tools. For instance, Digital Twin Technology allows manufacturers to simulate real-world performance, identifying potential issues before physical production begins. Similarly, Computer-Integrated Manufacturing (CIM) enables end-to-end digital oversight of machining, assembly, and testing processes.
Attention to materials is critical, especially with the adoption of Advanced Materials and Manufacturing Technologies and novel techniques such as Additive Manufacturing (3D Printing). Quality professionals must develop new inspection standards to evaluate mechanical strength, porosity, and microstructure. These innovations are central to Smart Manufacturing and Industry 4.0, which emphasizes data-driven feedback loops and real-time defect detection.
An effective quality framework supports other operational pillars, including Lean Manufacturing, which focuses on eliminating waste while maintaining output standards. Similarly, Sustainable Manufacturing integrates environmentally sound practices without compromising product performance. These goals are often realized through meticulous Energy and Resource Efficiency in Manufacturing.
Incorporating human oversight remains essential. The study of Human Factors and Ergonomics in Manufacturing ensures that inspection tasks are performed reliably and safely. Meanwhile, advances in Industrial Automation and Robotics automate precision testing and visual inspection in high-volume production lines.
Process design has a direct impact on quality. Seamless integration of design practices covered under Mechanical Design and CAD with robust Supply Chain Management ensures traceability and defect prevention across the entire value chain. These approaches complement topics in Manufacturing Process Design and Optimization.
The relevance of quality assurance spans many domains. Applications range from Automotive Engineering, where tight tolerances affect safety, to high-stakes fields like Biomechanical Engineering, where small flaws can jeopardize human health. Supportive knowledge from Solid Mechanics, Fluid Mechanics and Hydraulics, and Thermodynamics and Heat Transfer enhances the analytical rigor behind quality measurements.
Underlying many of these efforts are essential engineering foundations. Subjects such as Control Systems in Mechanical Engineering ensure that manufacturing conditions stay within optimal boundaries. Advanced fabrication techniques are also supported by insights from Nanotechnology and Advanced Materials in Mechanical Engineering and Robotics and Automation in Mechanical Engineering.
Ultimately, the pursuit of quality is not an isolated activity, but a continuous loop of measurement, feedback, and improvement across all levels of production. A solid grounding in quality control and assurance prepares students to uphold standards in a manufacturing world that demands precision, consistency, and trustworthiness.
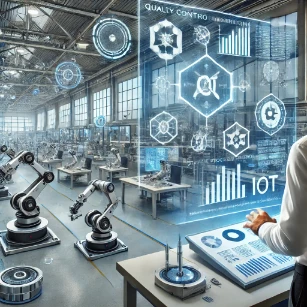
Table of Contents
Core Concepts of Quality Control and Assurance
Effective quality management in manufacturing depends on two foundational pillars: Quality Control (QC) and Quality Assurance (QA). These complementary practices ensure that both products and the processes that create them consistently meet or exceed customer expectations. While QC focuses on identifying and fixing defects in outputs, QA emphasizes building defect prevention into the production system itself. Understanding and applying both concepts is essential for achieving consistent performance, reducing waste, and enhancing customer trust.
Quality Control (QC)
- Definition:
- Quality Control is a reactive process dedicated to identifying and rectifying nonconformities in final products or during key stages of production. It serves as the last line of defense before products reach the customer, ensuring that defective units are detected and either corrected or rejected.
- Key Activities:
- Regular inspections and testing: These are performed on incoming materials, in-process units, and finished goods to assess conformity to design specifications and industry standards.
- Sampling techniques: Statistical sampling is often used to efficiently check large batches of products without testing every item, balancing inspection accuracy and time constraints.
- Implementing corrective actions: When deviations are identified, immediate responses such as rework, adjustments, or process halts are initiated to maintain overall product quality.
- Focus Areas:
- Defect detection: QC ensures that defects are identified before a product is shipped, thereby reducing the risk of customer dissatisfaction, recalls, or warranty claims.
- Conformance to criteria: Checks and measurements are designed to ensure that each product meets predefined tolerances, functionality requirements, and visual standards.
Quality Assurance (QA)
- Definition:
- Quality Assurance is a proactive and systematic approach focused on building quality into processes from the beginning. It aims to prevent defects by establishing, auditing, and improving process controls, documentation, and organizational practices.
- Key Activities:
- Developing SOPs (Standard Operating Procedures): These define best practices and expected performance for every critical task, ensuring consistency across shifts, operators, and production runs.
- Conducting audits and assessments: QA teams monitor process capability and compliance with established standards through periodic reviews, internal audits, and capability studies such as Cp and Cpk analysis.
- Risk management: QA involves proactively identifying areas where defects might arise and introducing control measures, mistake-proofing mechanisms (poka-yoke), or automation to reduce that risk.
- Focus Areas:
- Process design and reliability: QA focuses on embedding quality in the system, so that processes produce defect-free outputs as a natural result of their design and operation.
- Continuous improvement: QA drives initiatives such as Six Sigma, Total Quality Management (TQM), and Lean to continuously analyze and refine workflows, reducing variability and increasing value.
- As explained by the American Society for Quality (ASQ), QA builds the foundation upon which QC operates by ensuring that defects are minimized at their source.
Difference Between QC and QA
Aspect | Quality Control (QC) | Quality Assurance (QA) |
---|---|---|
Focus | Detecting and fixing defects | Preventing defects through process control |
Nature | Reactive | Proactive |
Objective | Product quality | Process quality |
Methods | Inspection, testing, and correction | Planning, documentation, and process audits |
Key Practices in Quality Control and Assurance
Statistical Process Control (SPC)
- Definition:
- Statistical Process Control (SPC) is a powerful quality control methodology that employs statistical tools to monitor and regulate production processes. By systematically analyzing variation, it allows manufacturers to detect deviations early and take corrective action before defective products are produced.
- Key Tools:
- Control charts: Visual graphs used to plot process data over time and compare it against control limits, helping identify trends, patterns, or abnormalities.
- Process capability analysis (Cp and Cpk): Metrics that assess how well a process meets specification limits, indicating whether it is capable of producing within tolerance consistently.
- Applications:
- SPC is widely used in industries like automotive, electronics, and pharmaceuticals to continuously monitor performance and quality. For instance, in semiconductor manufacturing, real-time control charts help track wafer thickness or doping levels to minimize rejects.
- It supports predictive maintenance by identifying subtle drifts in process parameters that may precede equipment failure, allowing preemptive servicing.
Inspections and Testing
- Inspections:
- Inspections are structured evaluations of product characteristics—visual, dimensional, or functional—performed to ensure that outputs meet specified quality criteria. They may occur at various stages: incoming materials, in-process parts, and final products.
- Examples: Inspecting welds in automotive chassis to verify penetration quality or visually examining PCBs (printed circuit boards) for solder defects.
- Testing:
- Testing involves applying mechanical, electrical, thermal, or chemical procedures to assess product performance under operational conditions. It validates that a product functions as intended and withstands the environments in which it will be used.
- Examples: Tensile testing on steel components to assess strength or conducting electrical conductivity tests on circuit assemblies.
Quality Management Systems (QMS)
- Definition:
- A Quality Management System is a comprehensive framework of policies, procedures, documentation, and standards aimed at ensuring consistent quality across the organization. It integrates all quality-related activities and aligns them with business goals.
- Examples:
- ISO 9001: A globally recognized standard that defines criteria for a QMS, focusing on customer satisfaction, risk-based thinking, and continual improvement.
- IATF 16949: Tailored for the automotive industry, this standard emphasizes defect prevention and the reduction of variation and waste across the supply chain.
- Additional frameworks like AS9100 (aerospace) and ISO 13485 (medical devices) ensure sector-specific quality compliance as detailed by the International Organization for Standardization.
Failure Modes and Effects Analysis (FMEA)
- Definition:
- FMEA is a proactive technique used to identify, evaluate, and prioritize potential failure modes in a process or product design, along with their causes and consequences. This helps teams mitigate risks before issues arise.
- Applications:
- Engineers rank risks using a Risk Priority Number (RPN), calculated by multiplying severity, occurrence, and detection scores. High RPNs signal urgent need for corrective actions.
- FMEA is applied across industries—from aerospace component design to hospital patient care processes—to enhance safety and reliability.
Six Sigma Methodology
- Definition:
- Six Sigma is a structured, data-driven methodology aimed at reducing process variation and eliminating defects. It combines statistical analysis, disciplined project management, and a strong customer focus to drive quality improvements.
- Key Concepts:
- DMAIC Framework: A five-phase approach: Define the problem, Measure performance, Analyze root causes, Improve processes, and Control results to sustain gains.
- Defect Reduction: Six Sigma targets performance levels with fewer than 3.4 defects per million opportunities (DPMO), representing near-perfect quality.
- Applications:
- Used in manufacturing, finance, logistics, and healthcare to reduce waste, cut costs, and improve service delivery.
- In a manufacturing line, Six Sigma might be used to identify sources of product weight inconsistencies and recalibrate equipment accordingly.
Root Cause Analysis (RCA)
- Definition:
- Root Cause Analysis is a systematic approach to uncovering the fundamental origin of a problem or defect, rather than merely addressing its symptoms. By resolving the true root, recurrence can be prevented.
- Techniques:
- Fishbone diagram (Ishikawa): Categorizes potential causes under major headings like Methods, Machines, Materials, and Manpower to visually trace the origin of a problem.
- 5 Whys: A simple but effective method of asking “why?” repeatedly (typically five times) to peel back layers of symptoms and reach the root cause.
Total Quality Management (TQM)
- Definition:
- Total Quality Management is a holistic, organization-wide philosophy where all employees at every level work collaboratively to improve processes, products, and services. It integrates quality into the organizational culture.
- Key Principles:
- Customer focus: Understanding and exceeding customer needs is central to every decision and action.
- Employee involvement: Quality is a shared responsibility; empowered employees are vital contributors to improvement.
- Continuous improvement: Quality is seen as a dynamic target, requiring persistent effort and evaluation.
- Applications:
- Widely adopted in both manufacturing and service sectors. For example, hospitality companies use TQM to improve guest experiences by analyzing feedback loops and employee service standards.
Continuous Improvement (Kaizen)
- Definition:
- Kaizen is a Japanese philosophy emphasizing incremental improvements carried out regularly and collaboratively. It focuses on improving productivity, quality, and workplace morale without large capital investments.
- Key Elements:
- Employee involvement: Workers closest to the processes are encouraged to suggest changes and identify inefficiencies.
- Routine evaluations: Small adjustments—like rearranging tools or standardizing work instructions—are made frequently to refine performance over time.
Risk-Based Thinking
- Definition:
- Risk-based thinking involves systematically identifying, evaluating, and addressing potential threats to product or process quality before they materialize. This proactive mindset helps organizations become more resilient and consistent.
- Applications:
- Applied in supply chain audits, design validation, and new product introductions to minimize disruptions or recalls.
- In pharmaceutical manufacturing, risk-based approaches are used to prevent cross-contamination and ensure regulatory compliance.
Applications of Quality Control and Assurance
Manufacturing
- Automotive:
- In the automotive industry, quality control is essential to ensure that every component—from brake pads to transmission systems—meets strict dimensional and performance specifications. Advanced QC techniques such as Coordinate Measuring Machines (CMMs) are used to verify tolerances in engine parts, ensuring that precision-engineered components fit and function flawlessly.
- Quality assurance also plays a vital role by embedding quality checks into the production workflow. For example, using a Failure Modes and Effects Analysis (FMEA), automotive engineers can proactively identify design or process weaknesses during vehicle development.
- Example: Toyota’s adoption of Six Sigma methodologies has led to substantial reductions in rework and warranty claims by addressing root causes of variation at the source, rather than relying solely on post-production inspection.
- Electronics:
- Electronics manufacturing demands exacting QC due to the minute scale and sensitivity of components. Processes such as solder joint inspection, X-ray analysis of multilayer PCBs, and continuity testing ensure reliable electrical performance in devices like smartphones and laptops.
- QA systems govern process documentation, training, and supplier certification to maintain consistent quality throughout the global supply chain. Controlled environments and cleanroom procedures are often mandated to prevent contamination during assembly.
- Example: Companies like Intel utilize Statistical Process Control (SPC) to monitor wafer fabrication processes in real time, ensuring that each batch conforms to design tolerances and electrical specifications.
- Pharmaceuticals:
- In pharmaceuticals, QC and QA are tightly regulated and integral to product safety and efficacy. Laboratory analysis confirms that drug formulations meet potency, purity, and stability requirements. Routine batch testing ensures uniformity across production runs.
- Quality assurance involves adherence to Good Manufacturing Practices (GMP), which include proper documentation, training, validation protocols, and cleanroom conditions. This system ensures that processes are controlled and deviations are traceable.
- Example: During the COVID-19 pandemic, firms like Moderna implemented real-time release testing and automated batch verification as part of a GMP-compliant, QA-centric framework to accelerate vaccine delivery.
Construction
- Material Quality Testing:
- Quality control in construction ensures that materials like concrete, steel, asphalt, and aggregates meet project specifications. For instance, concrete undergoes compressive strength testing at various curing stages to validate its structural integrity.
- QC laboratories often perform destructive and non-destructive testing to verify compliance with ASTM or ISO standards. These tests are critical in ensuring that foundations, beams, and columns can bear design loads safely.
- Inspection Standards:
- Regular site inspections are mandated to ensure that construction activities adhere to building codes, safety regulations, and design documents. QA protocols include documentation of inspections, contractor qualifications, and schedule compliance.
- Tools like checklists and photographic records are used in quality audits. Digital project management systems are increasingly employed to track non-conformance reports (NCRs) and corrective actions in real time.
Healthcare
- Medical Devices:
- In healthcare, QC and QA are crucial for ensuring the safety and reliability of diagnostic and therapeutic devices. Products like pacemakers and surgical robots are subject to rigorous testing under simulated use conditions, including mechanical stress, electrical insulation, and biocompatibility testing.
- Quality assurance involves compliance with standards such as ISO 13485 and FDA regulations, including design controls, risk assessments, and traceability. Devices must undergo certification by notified bodies before being released to market.
- Hospital Management:
- Hospitals implement QA systems to manage quality in patient care, from sterilization procedures to medication administration. These systems include audit protocols, incident reporting, and compliance tracking using Electronic Health Records (EHRs).
- Performance metrics such as hospital-acquired infection rates, readmission rates, and patient satisfaction scores are used to continuously assess and improve healthcare delivery.
Food and Beverage
- HACCP (Hazard Analysis and Critical Control Points):
- HACCP is a globally recognized quality assurance methodology for food safety. It involves identifying potential biological, chemical, and physical hazards in the production process and establishing preventive controls at critical points.
- Implementation includes maintaining hygiene protocols, monitoring temperature controls, and documenting each stage of production. Compliance with HACCP is often required by regulatory bodies and international trading partners.
- Batch Testing:
- Quality control involves systematic sampling and analysis of food and beverage batches to ensure they meet specifications for taste, texture, pH, microbial content, and nutritional labeling.
- Companies such as Nestlé and PepsiCo use laboratory and sensory testing in conjunction with automated inspection systems for consistency and regulatory compliance as outlined by the U.S. FDA.
Software Development
- Quality Assurance:
- QA in software development ensures that coding standards, version control, documentation, and development workflows meet project requirements. It includes design validation, peer reviews, and risk assessments.
- QA frameworks such as Agile and DevOps integrate testing and validation throughout the development lifecycle to reduce errors and accelerate releases.
- Testing:
- Testing includes unit testing, integration testing, system testing, and acceptance testing. Manual testing ensures usability, while automated testing validates code logic, scalability, and security.
- Tools such as Selenium, JUnit, and Postman are widely used for automated functional and regression testing. Continuous testing in CI/CD pipelines helps deliver reliable software at speed.
Tools and Technologies in Quality Control and Assurance
Statistical Tools
- Control charts are foundational tools in Statistical Process Control (SPC), used to track process behavior over time. By plotting key quality metrics such as dimensions, temperature, or pressure, these charts help differentiate between common cause variation and special cause variation. Types include X-bar, R, and p-charts, each suited for different types of data (e.g., variable or attribute).
- Pareto analysis is a decision-making technique that helps prioritize improvement efforts by identifying the “vital few” causes that account for the majority of quality issues. Based on the 80/20 rule, this tool allows teams to focus resources on the most impactful problems. It is often used in conjunction with cause-and-effect diagrams to guide root cause investigations and corrective action planning.
Software Tools
- Quality Management Software (QMS) systems provide a centralized platform for managing documentation, standard operating procedures (SOPs), audit findings, training records, non-conformance reports, and corrective/preventive actions (CAPAs). These systems support compliance with standards such as ISO 9001 and IATF 16949 and often integrate with ERP and MES systems for real-time data synchronization.
- In software development, automated testing systems are critical to verifying that applications function as intended. These tools execute thousands of test cases during development and deployment, identifying bugs and regressions early in the software lifecycle. Examples include Selenium for UI testing, JUnit for unit testing, and Jenkins for continuous integration and testing pipelines.
Advanced Testing Equipment
- Non-Destructive Testing (NDT) encompasses methods that inspect the structural integrity of materials without causing damage. Common NDT techniques include ultrasonic testing (UT), which uses sound waves to detect internal flaws; radiographic testing (X-ray), which visualizes internal features; and magnetic particle inspection (MPI) for identifying surface and near-surface cracks in ferromagnetic materials. These tools are widely used in aerospace, automotive, and construction industries.
- Automated Optical Inspection (AOI) systems are employed in electronics manufacturing to detect defects such as missing components, solder bridges, and misalignments. High-resolution cameras and image processing algorithms compare production units against reference models, ensuring that printed circuit boards (PCBs) and microchips meet design and quality standards. AOI can operate in-line for real-time inspection or offline for batch review.
Artificial Intelligence (AI) and Machine Learning
- AI-driven defect detection uses computer vision algorithms trained on thousands of images to identify minute defects such as surface scratches, voids, or discolorations that human inspectors might overlook. These systems offer consistent inspection capabilities, especially in high-speed or high-precision manufacturing environments. They are often integrated with robotic vision systems to enable adaptive manufacturing adjustments.
- Predictive analytics, powered by machine learning, identifies trends and anomalies in production data to forecast potential quality failures before they occur. By analyzing variables like machine vibration, temperature, or process cycle time, these systems alert operators to intervene proactively. As a result, manufacturers can significantly reduce scrap rates and downtime. AI quality systems are also gaining traction in regulated sectors like pharmaceuticals and medical devices according to NIST research on AI in quality assurance.
Blockchain for Traceability
- Blockchain technology enhances traceability and transparency by providing immutable records of each transaction or event along a product’s journey. Each block in the chain contains a timestamp and a cryptographic link to the previous block, making the data tamper-evident and verifiable across stakeholders. This is especially useful in industries like food, aerospace, and pharmaceuticals, where traceability is essential for safety, compliance, and recalls.
- Example: In food production, blockchain is used to trace the origin and handling of ingredients such as produce, dairy, and meat. Companies like Walmart and IBM have partnered to implement blockchain platforms that trace items from farm to shelf, enhancing consumer trust and enabling rapid response during contamination events. Blockchain also enables validation of organic or fair-trade certifications by recording audits and inspection outcomes on the ledger.
Benefits of Quality Control and Assurance
- Enhanced Customer Satisfaction:
- Consistently delivering high-quality products and services directly impacts customer perception and loyalty. When customers receive defect-free, reliable goods that meet or exceed their expectations, their confidence in the brand strengthens. This leads to increased repeat purchases, favorable reviews, and word-of-mouth recommendations. Quality assurance processes, such as rigorous testing and proactive defect prevention, ensure that customer feedback loops are closed and used to drive continual improvement.
- For instance, in the electronics sector, customers demand products with zero tolerance for malfunctions. Quality control ensures that each unit is tested against defined standards before shipping. This precision fosters satisfaction and enhances the perceived value of the brand in the competitive market.
- Reduced Costs:
- Implementing robust quality control and assurance programs helps organizations minimize rework, scrap, and warranty claims—leading to significant cost savings. By catching defects early in the production process or eliminating them altogether through preventive measures, companies avoid the high costs associated with recalls, customer complaints, and legal liabilities.
- Moreover, streamlined quality procedures reduce variability and inefficiencies that often inflate production costs. Lean methodologies integrated with quality assurance initiatives further reduce waste and improve resource utilization. According to a report by the American Society for Quality (ASQ), organizations can save millions annually by identifying and controlling quality-related costs proactively.
- Improved Brand Reputation:
- Consistent delivery of high-quality products and adherence to established standards enhances a company’s credibility and brand reputation. When customers associate a brand with quality, it differentiates the company from competitors and strengthens market position. Companies like Toyota, Apple, and Siemens have built reputations on their commitment to quality, which directly contributes to their long-term success.
- Quality assurance practices ensure that branding messages are not undermined by poor performance or inconsistent results. External stakeholders such as investors and partners also perceive reliable quality control as a sign of organizational competence and sustainability.
- Regulatory Compliance:
- Many industries—including pharmaceuticals, aerospace, medical devices, and food production—are subject to strict regulatory frameworks. Quality control and assurance systems are essential to ensuring compliance with local and international standards such as ISO 9001, FDA regulations, or GMP (Good Manufacturing Practices). Regular audits, process validation, and documentation trails provided by QMS help meet regulatory expectations and avoid penalties or operational shutdowns.
- In heavily regulated environments, quality assurance serves not only as a tool for compliance but also as a strategic enabler of market access. For instance, a manufacturer certified under IATF 16949 gains entry into global automotive supply chains due to their demonstrated ability to meet automotive-specific quality criteria.
- Employee Empowerment:
- Quality control and assurance frameworks often emphasize employee involvement in process improvement. Empowering workers to identify issues, propose enhancements, and take ownership of quality leads to increased job satisfaction and innovation. Employees on the production floor have intimate knowledge of the day-to-day operations and are best positioned to spot inefficiencies or risks.
- Approaches such as Total Quality Management (TQM) and Kaizen rely heavily on employee engagement. Workers are encouraged to participate in cross-functional teams, quality circles, and regular feedback sessions. This not only improves product and process quality but also fosters a culture of collaboration and continuous learning throughout the organization.
Challenges in Quality Control and Assurance
- High Implementation Costs:
- One of the foremost challenges organizations face when adopting quality control and assurance systems is the high initial investment. This includes the cost of purchasing advanced inspection equipment, implementing quality management software, and upgrading existing infrastructure to support new processes. Companies may also need to invest in extensive staff training to ensure employees are proficient in using these tools and adhering to quality protocols.
- In regulated industries such as pharmaceuticals or aerospace, certification costs and compliance audits further increase financial burdens. These expenses can deter small- and medium-sized enterprises from fully adopting robust quality systems. Additionally, ongoing operational expenses—such as calibration of instruments, frequent quality audits, and maintenance of data systems—can strain budgets over time.
- Resistance to Change:
- Organizational culture plays a pivotal role in the success or failure of quality initiatives. Employees who are accustomed to legacy systems may resist changes, especially when new practices introduce unfamiliar routines, performance monitoring, or stricter documentation requirements. Such resistance is particularly pronounced when quality measures are perceived as burdensome or punitive rather than supportive.
- Leadership must foster a culture of continuous improvement and demonstrate the value of quality in achieving business goals. Engaging employees early in the change process, offering adequate training, and recognizing contributions to quality improvement can reduce pushback and build buy-in across all levels of the organization.
- Data Overload:
- Modern quality control systems generate vast amounts of data through IoT sensors, real-time monitoring platforms, and enterprise systems. While this data is valuable, managing and interpreting it can be overwhelming without proper tools and strategies. Quality teams must sift through performance metrics, audit trails, inspection reports, and compliance data to identify actionable insights.
- Without effective data governance and visualization tools, key signals may be missed, or teams may suffer from analysis paralysis. To overcome this, organizations are increasingly adopting data analytics platforms that filter and prioritize quality issues, but these solutions come with additional complexity. According to [Forbes](https://www.forbes.com/sites/forbestechcouncil/2021/04/29/five-ways-to-overcome-data-overload/?sh=31fa96f922de), managing data overload requires combining automation, clear data governance, and team training to make informed decisions without being overwhelmed.
- Global Supply Chains:
- As manufacturing becomes more globalized, ensuring consistent quality across geographically dispersed suppliers and facilities poses significant challenges. Variations in local standards, regulations, supplier capabilities, and communication practices can result in inconsistencies and delays. Even when quality protocols are established centrally, enforcing them uniformly across the supply chain requires meticulous coordination.
- Auditing overseas suppliers, validating raw materials, and synchronizing quality data across different IT systems introduce logistical and technological hurdles. Moreover, political and economic disruptions—such as tariffs or transportation delays—can hinder real-time monitoring and quality verification. Mitigating these challenges demands a strong supplier qualification program, standardized metrics, and sometimes the use of third-party auditors or quality certification bodies to maintain uniformity across borders.
Emerging Trends in Quality Control and Assurance
- Integration with Industry 4.0:
- The emergence of Industry 4.0 has revolutionized quality control by embedding intelligence into manufacturing systems. Through the integration of smart sensors, cyber-physical systems, and IoT devices, quality parameters can now be monitored in real-time with unprecedented accuracy. These connected systems enable continuous tracking of temperature, pressure, vibration, and other critical factors that affect product quality during production.
- Additionally, data from these devices can be collected and analyzed instantaneously, allowing for immediate corrective actions and process adjustments. For example, if a vibration sensor detects an anomaly in a CNC machine, the system can automatically trigger maintenance alerts or slow operations to prevent defective outputs. This predictive capability reduces downtime and ensures that quality deviations are addressed before affecting large batches.
- AI and Automation:
- Artificial intelligence (AI) is playing a pivotal role in advancing quality assurance by automating complex decision-making processes and improving the accuracy of defect detection. Machine learning models can be trained on large datasets to identify subtle patterns and deviations that might be missed by human inspectors. AI-powered vision systems, for instance, can examine products for surface defects, dimensional inconsistencies, or misalignments with high precision.
- Moreover, automation allows for continuous inspection at scale. Automated optical inspection (AOI) systems are now widely used in electronics manufacturing to inspect printed circuit boards (PCBs) without human intervention. This not only increases throughput but also ensures consistent inspection standards across all units. As reported by Quality Magazine, AI-driven inspection technologies are transforming traditional quality control from reactive to proactive, enabling smarter production environments.
- Sustainability in QA:
- Quality management is increasingly being aligned with sustainability goals. Modern QA systems are being designed to minimize environmental impact by reducing waste, conserving energy, and encouraging the use of sustainable materials. For example, companies are now integrating life-cycle assessments (LCAs) into their quality frameworks to ensure that products not only meet performance standards but also adhere to eco-friendly criteria.
- Furthermore, certifications such as ISO 14001 are being adopted alongside traditional quality standards to formalize sustainability practices. Quality control now includes monitoring emissions, resource usage, and recycling rates as part of its scope. This holistic approach helps organizations build environmentally responsible supply chains while maintaining high product standards.
- Advanced Analytics:
- The use of big data and advanced analytics is reshaping how organizations approach quality assurance. By collecting and analyzing large volumes of structured and unstructured data, companies can gain deeper insights into root causes of defects, supplier performance trends, and process inefficiencies. These insights are used to make evidence-based decisions that enhance both product and process quality.
- Predictive analytics, in particular, enables quality teams to forecast potential quality issues before they occur. For instance, historical machine data can be analyzed to predict when a component is likely to fail, allowing for preventive action. Visualization tools like dashboards and heat maps provide real-time quality metrics across production lines, facilitating faster and more informed responses.
- Remote Auditing:
- The COVID-19 pandemic accelerated the adoption of remote auditing, and it continues to gain momentum as a viable long-term solution. Using video conferencing tools, cloud-based documentation systems, and secure digital platforms, auditors can now assess quality systems, review procedures, and interview employees without being physically present. This has made quality compliance audits more flexible, cost-effective, and globally accessible.
- Remote auditing also enhances collaboration across geographically distributed teams. Suppliers in different countries can now be evaluated in real time without the logistical burden of travel. While remote audits do pose challenges in terms of hands-on inspection, they are increasingly being supported by augmented reality (AR) and mobile camera systems to provide detailed visual assessments of facilities and practices.
Future Directions in Quality Control and Assurance
- Smart Factories:
- The future of quality control lies in the widespread adoption of smart factory environments. These advanced manufacturing facilities are equipped with interconnected machines, sensors, and control systems that enable end-to-end automation of quality monitoring. In smart factories, quality assurance becomes an embedded function, rather than a standalone checkpoint.
- Data from every stage of production is continuously captured and analyzed in real-time, allowing for immediate detection of anomalies and deviations from quality norms. For instance, sensors on a production line can instantly identify surface defects or dimensional inaccuracies and trigger automated adjustments or halt the process for intervention. This dramatically reduces the lag between defect detection and corrective action, ensuring that quality is built into the process rather than inspected at the end.
- Real-Time Quality Assurance:
- Real-time quality assurance represents a shift from periodic inspections to continuous oversight of production activities. This involves deploying smart devices and cloud-based platforms that aggregate and analyze data instantaneously to ensure compliance with quality standards as products are being manufactured. It also supports just-in-time decision-making, allowing operators to intervene precisely when an issue is about to arise, not after the fact.
- For example, in pharmaceutical manufacturing, real-time QA systems monitor parameters like humidity, temperature, and formulation ratios during drug production to prevent deviations that could compromise efficacy. This approach aligns with the FDA’s Process Analytical Technology (PAT) framework, which emphasizes designing, analyzing, and controlling manufacturing processes through real-time measurements.
- Collaborative QA Systems:
- Future quality initiatives will be increasingly collaborative, involving not just internal teams but also customers, suppliers, and third-party stakeholders. This shared responsibility model ensures that quality standards are maintained throughout the entire value chain—from raw materials to final delivery. Transparency, communication, and mutual accountability become central to quality governance.
- One emerging practice is supplier quality integration, where suppliers are granted access to the manufacturer’s quality systems and are actively involved in defining and auditing quality requirements. Customers, too, are playing a more proactive role by participating in co-creation processes, providing real-time feedback, and influencing design specifications. According to a report from Deloitte Insights, digital collaboration platforms are streamlining how stakeholders jointly address quality risks, driving better outcomes and faster resolution of issues.
- Sustainable Quality Practices:
- Environmental responsibility is becoming a key pillar of quality assurance. Future QA frameworks will integrate sustainable practices that align with circular economy principles—emphasizing resource efficiency, product longevity, and recyclability. This involves designing products that are easier to reuse or recycle, reducing emissions during production, and adopting eco-friendly materials and packaging.
- Quality audits will increasingly assess a company’s environmental impact, not just product performance. For example, organizations may be required to validate that suppliers meet environmental compliance benchmarks or that their production processes minimize hazardous waste. Certifications like ISO 14001 will complement traditional quality standards, signaling a shift toward environmentally conscious quality management systems.
- Personalized Quality Metrics:
- As industries move toward mass customization and customer-specific offerings, the traditional one-size-fits-all quality benchmarks will give way to personalized quality metrics. These are tailored standards and criteria developed based on individual customer expectations, use cases, and regional regulations. Manufacturers will need to implement dynamic quality systems capable of adapting to this level of customization without compromising operational efficiency.
- This trend is especially prominent in sectors like aerospace, medical devices, and custom electronics, where clients often specify stringent tolerances, unique testing protocols, or traceability requirements. Real-time feedback loops, customer-facing dashboards, and configurable quality controls will empower organizations to meet diverse needs while maintaining robust quality assurance frameworks.
Why Study Manufacturing Quality Control and Assurance
Ensuring Consistent Product Quality
Quality control and assurance focus on meeting product specifications and customer expectations. Students learn how to detect defects, maintain standards, and reduce variability. This supports reliability and brand reputation.
Quality Tools and Statistical Methods
Students explore control charts, process capability analysis, and Six Sigma techniques. They learn how to use statistical tools to monitor performance and drive improvement. These methods ensure data-based decision-making.
Inspection, Testing, and Documentation
The course teaches how to conduct inspections and tests for materials, components, and final products. Students also learn the importance of documentation for traceability and compliance. This ensures accountability and transparency.
Quality Management Systems (QMS)
Students study systems like ISO 9001 and Total Quality Management (TQM). These frameworks provide structured approaches to managing and improving quality. Mastery of QMS is essential for regulatory and competitive success.
Customer Focus and Continuous Improvement
Quality assurance emphasizes customer satisfaction and long-term improvement. Students learn to collect feedback, resolve issues, and evolve processes. This enhances value delivery and organizational growth.
Quality Control and Assurance: Conclusion
Quality control (QC) and quality assurance (QA) represent more than operational necessities—they are strategic pillars that shape the trustworthiness, competitiveness, and long-term viability of organizations across all sectors. By embedding quality deeply into every process, from product design and sourcing to manufacturing and customer service, businesses can build resilient systems that consistently deliver high value to consumers and stakeholders.
Modern QC and QA practices leverage a diverse toolkit that includes well-established frameworks such as Six Sigma, Total Quality Management (TQM), and Statistical Process Control (SPC), all of which aim to eliminate defects, reduce variability, and ensure consistent outcomes. These methodologies help organizations move beyond reactive fixes toward predictive and preventive strategies that align with broader goals of efficiency and customer delight.
The role of technology in elevating quality practices cannot be overstated. With the integration of the Internet of Things (IoT), artificial intelligence (AI), and cloud-based platforms, real-time monitoring, automated inspections, and predictive analytics are revolutionizing how quality is managed. Smart sensors and machine learning algorithms allow manufacturers to detect anomalies before they lead to costly failures, while cloud-connected systems ensure data is accessible, traceable, and actionable across global supply chains.
In parallel, industry-specific standards such as ISO 9001, IATF 16949, and GMP ensure regulatory compliance and provide structured guidance for maintaining excellence in complex environments. These standards promote consistency, transparency, and accountability, which are increasingly important in an era of globalized trade, heightened customer expectations, and rigorous legal oversight.
Sustainability is also becoming a core theme in quality assurance. Organizations are not only expected to deliver defect-free products but also to ensure ethical sourcing, environmentally responsible production, and safe disposal or recyclability. This evolution broadens the scope of QA and introduces metrics such as carbon footprint, water usage, and lifecycle impact into traditional quality scorecards.
Furthermore, the workforce plays a critical role in sustaining quality initiatives. Empowering employees through training, feedback mechanisms, and cross-functional collaboration nurtures a culture where continuous improvement becomes second nature. Quality becomes everyone’s responsibility—from engineers and operators to executives and partners. As noted in an article from Harvard Business Review, strong leadership and organizational alignment are essential to driving quality transformations that stick.
In conclusion, quality control and assurance are not static checklists but dynamic disciplines that evolve with technological progress, regulatory landscapes, and market expectations. Organizations that embed quality into their DNA are better positioned to innovate, adapt, and thrive. As industries increasingly embrace digital transformation and sustainable development, QC and QA will remain indispensable tools for navigating complexity and achieving excellence in an ever-changing world.
Quality Control and Assurance: Review Questions with Detailed Answers
1. What are the primary objectives of quality control and assurance in manufacturing?
Answer:
The primary objectives of quality control (QC) and quality assurance (QA) in manufacturing are to ensure that products meet or exceed customer expectations, comply with regulatory standards, and maintain consistency and reliability throughout the production process. Specifically, the objectives include:
Ensure Product Quality:
- Objective: Deliver products that meet predefined quality standards and specifications.
- Impact: Enhances customer satisfaction, reduces returns and complaints, and builds brand reputation.
Reduce Defects and Variability:
- Objective: Minimize the occurrence of defects and inconsistencies in products.
- Impact: Lowers production costs associated with rework and scrap, and improves overall efficiency.
Compliance with Standards:
- Objective: Adhere to industry regulations, safety standards, and certification requirements.
- Impact: Ensures legal compliance, avoids penalties, and opens up market opportunities.
Continuous Improvement:
- Objective: Implement ongoing enhancements to processes and systems to boost quality and efficiency.
- Impact: Drives long-term operational excellence and adaptability to changing market demands.
Enhance Process Reliability:
- Objective: Develop and maintain stable and predictable manufacturing processes.
- Impact: Ensures consistent product quality and reduces downtime caused by process disruptions.
Cost Efficiency:
- Objective: Optimize quality-related costs by preventing defects rather than correcting them.
- Impact: Improves profitability by reducing waste and increasing resource utilization.
Customer Confidence:
- Objective: Build trust with customers through reliable and high-quality products.
- Impact: Fosters customer loyalty and encourages repeat business.
Conclusion: Quality control and assurance are integral to manufacturing, focusing on delivering superior products, minimizing costs, ensuring compliance, and fostering continuous improvement. Achieving these objectives leads to enhanced customer satisfaction, operational efficiency, and sustained business success.
2. How do Quality Control (QC) and Quality Assurance (QA) differ in their roles within the manufacturing process?
Answer:
Quality Control (QC) and Quality Assurance (QA) are two distinct but complementary components of a comprehensive quality management system in manufacturing. Understanding their differences is crucial for effective implementation and operational success.
Quality Control (QC):
Definition:
- QC refers to the operational techniques and activities used to fulfill quality requirements by identifying defects in finished products.
Focus:
- Product-Oriented: Concentrates on detecting and correcting defects in the final products.
- Reactive Approach: Responds to quality issues after they have occurred.
Activities:
- Inspection and Testing: Examining products for defects through various testing methods.
- Statistical Process Control (SPC): Using statistical tools to monitor and control production processes.
- Defect Tracking: Recording and analyzing defects to identify patterns and causes.
Objective:
- Ensure that only products meeting quality standards reach the customer.
Quality Assurance (QA):
Definition:
- QA encompasses the systematic activities and processes designed to ensure that quality requirements will be fulfilled.
Focus:
- Process-Oriented: Concentrates on improving and stabilizing production processes to prevent defects.
- Proactive Approach: Aims to prevent quality issues before they occur.
Activities:
- Process Design and Development: Establishing robust manufacturing processes.
- Standardization: Developing and enforcing standard operating procedures (SOPs).
- Training and Education: Ensuring employees are knowledgeable about quality standards and practices.
- Auditing and Compliance: Regularly reviewing processes to ensure adherence to standards.
Objective:
- Create an environment and processes that consistently produce high-quality products.
Key Differences:
Aspect | Quality Control (QC) | Quality Assurance (QA) |
---|---|---|
Primary Focus | Detecting defects in final products | Preventing defects through process improvement |
Approach | Reactive | Proactive |
Orientation | Product-oriented | Process-oriented |
Activities | Inspection, testing, defect tracking | Process design, standardization, training |
Objective | Ensure only defect-free products reach customers | Ensure processes are capable of producing quality products consistently |
Conclusion: While QC and QA have different focuses and approaches, they are both essential for maintaining high standards in manufacturing. QC ensures that defects are identified and addressed in the final products, whereas QA focuses on creating processes that prevent defects from occurring in the first place. Together, they form a robust quality management system that enhances product reliability, customer satisfaction, and operational efficiency.
3. What are the key quality control tools used in manufacturing, and how do they contribute to quality improvement?
Answer:
Quality Control (QC) tools are essential for identifying, analyzing, and addressing quality issues in manufacturing. These tools help in monitoring processes, detecting defects, and implementing improvements to enhance overall product quality. The key QC tools include:
Pareto Chart:
- Description: A bar graph that ranks causes of defects or problems in descending order of frequency.
- Contribution: Helps identify the most significant factors contributing to quality issues, allowing manufacturers to prioritize improvement efforts based on the 80/20 rule (80% of problems are often caused by 20% of causes).
Cause-and-Effect Diagram (Fishbone Diagram):
- Description: A visual tool that maps out potential causes of a specific problem, categorized into major areas such as methods, machines, materials, and manpower.
- Contribution: Facilitates brainstorming and systematic identification of root causes of defects, enabling targeted corrective actions.
Control Charts:
- Description: Graphs used to monitor process behavior over time, showing upper and lower control limits.
- Contribution: Detects variations in the manufacturing process, distinguishing between common cause (inherent) and special cause (external) variations, thus helping maintain process stability and consistency.
Histogram:
- Description: A bar graph representing the distribution of data points within specified intervals.
- Contribution: Provides a visual summary of process performance, highlighting patterns, central tendency, and variability, which are crucial for understanding and improving processes.
Scatter Diagram:
- Description: A graph that plots two variables against each other to identify relationships or correlations.
- Contribution: Helps determine if there is a relationship between process variables, which can be leveraged to improve quality by adjusting related factors.
Check Sheet:
- Description: A structured form for collecting and analyzing data systematically.
- Contribution: Facilitates the organized collection of defect data, making it easier to identify trends and patterns that inform quality improvement initiatives.
Flowchart:
- Description: A diagram that outlines the sequential steps of a process.
- Contribution: Provides a clear visualization of the manufacturing process, identifying inefficiencies, redundancies, and areas for improvement.
Failure Mode and Effects Analysis (FMEA):
- Description: A systematic method for evaluating potential failure modes and their impact on the system.
- Contribution: Proactively identifies and addresses potential failures, enhancing product reliability and preventing defects before they occur.
Root Cause Analysis (RCA):
- Description: A methodical approach to identifying the underlying causes of defects or problems.
- Contribution: Ensures that corrective actions address the true causes of issues, preventing recurrence and fostering long-term quality improvements.
Statistical Process Control (SPC):
- Description: The use of statistical methods to monitor and control a process.
- Contribution: Ensures that the process operates efficiently, producing more specification-conforming products with less waste.
Benefits of Using QC Tools:
- Data-Driven Decision Making: Provides objective data to guide quality improvement efforts.
- Root Cause Identification: Helps uncover the underlying causes of defects, enabling effective corrective actions.
- Process Monitoring: Continuously tracks process performance to maintain stability and consistency.
- Waste Reduction: Identifies and eliminates non-value-adding activities and defects, reducing waste and costs.
- Enhanced Communication: Facilitates clear communication and collaboration among team members through visual representations of data and processes.
- Continuous Improvement: Supports ongoing efforts to refine and enhance manufacturing processes, fostering a culture of quality and excellence.
Conclusion: Quality Control tools are indispensable for manufacturing organizations striving to achieve high product quality and operational efficiency. By systematically identifying, analyzing, and addressing quality issues, these tools contribute to continuous improvement, cost reduction, and enhanced customer satisfaction. Implementing and effectively utilizing these QC tools enables manufacturers to maintain competitive advantage and sustain long-term success in the market.
4. What is Statistical Process Control (SPC), and how is it applied in manufacturing quality assurance?
Answer:
Statistical Process Control (SPC) is a method of quality control that employs statistical techniques to monitor and control a manufacturing process. The primary goal of SPC is to ensure that the process operates at its maximum potential to produce conforming products with minimal variation.
Key Components of SPC:
Control Charts:
- Description: Graphical tools used to plot process data over time, displaying upper and lower control limits.
- Application: Monitor process stability by distinguishing between common cause variation (inherent to the process) and special cause variation (external factors). When data points fall outside control limits or show non-random patterns, it signals that the process may be out of control and requires investigation.
Process Capability Analysis:
- Description: Evaluates how well a process can produce output within specified limits.
- Application: Determines the capability indices (Cp, Cpk) to assess if the process is capable of consistently producing products that meet quality standards.
Sampling Methods:
- Description: Techniques for selecting representative samples from the production process for analysis.
- Application: Ensures that data collected for SPC is unbiased and accurately reflects the process performance.
Pareto Analysis:
- Description: Identifies the most significant factors contributing to defects or variations.
- Application: Focuses improvement efforts on the few key areas that have the most substantial impact on quality.
Application of SPC in Manufacturing Quality Assurance:
Process Monitoring:
- Implementation: Regularly collect data from critical process parameters (e.g., temperature, pressure, dimensions) and plot them on control charts.
- Benefit: Enables real-time monitoring of process performance, allowing for immediate detection of deviations from standards.
Early Defect Detection:
- Implementation: Use control charts to identify trends or shifts in the process that may lead to defects.
- Benefit: Facilitates prompt corrective actions before defects occur, reducing scrap and rework costs.
Process Improvement:
- Implementation: Analyze control chart data to identify sources of variation and implement process enhancements.
- Benefit: Enhances process stability and capability, leading to higher quality products and increased efficiency.
Decision Making:
- Implementation: Utilize SPC data to make informed decisions regarding process adjustments, equipment maintenance, and quality improvements.
- Benefit: Promotes data-driven decision-making, reducing reliance on intuition or guesswork.
Documentation and Compliance:
- Implementation: Maintain records of SPC data and analysis for auditing and compliance purposes.
- Benefit: Demonstrates adherence to quality standards and regulatory requirements, enhancing credibility and trust with customers.
Benefits of SPC in Quality Assurance:
- Consistency and Reliability: Ensures that processes produce consistent and reliable products by maintaining control over process variations.
- Cost Savings: Reduces costs associated with defects, rework, and waste by identifying and addressing issues early.
- Continuous Improvement: Supports ongoing efforts to enhance process performance and product quality through systematic analysis and improvement.
- Enhanced Customer Satisfaction: Delivers high-quality products that meet or exceed customer expectations, fostering loyalty and repeat business.
- Proactive Management: Shifts quality control from a reactive to a proactive approach, anticipating and preventing issues rather than merely detecting them.
Case Example: A beverage manufacturer implemented SPC to monitor the carbonation levels in its bottled drinks. By tracking carbonation measurements on control charts, they identified a recurring pattern of under-carbonation during certain shifts. Investigating further, they discovered that a specific batch of CO₂ cylinders was faulty. Replacing the cylinders and adjusting the filling process brought carbonation levels back within control limits, ensuring consistent product quality and reducing customer complaints.
Conclusion: Statistical Process Control is a fundamental tool in manufacturing quality assurance, providing a structured approach to monitoring, controlling, and improving production processes. By leveraging statistical methods to detect and address variations, SPC enhances process stability, reduces defects, and fosters a culture of continuous improvement. Implementing SPC effectively leads to higher quality products, cost savings, and increased customer satisfaction, thereby strengthening the overall competitiveness and success of manufacturing organizations.
5. What is Total Quality Management (TQM), and how does it differ from traditional quality control methods?
Answer:
Total Quality Management (TQM) is a comprehensive, organization-wide approach focused on continuously improving the quality of products, services, and processes by involving all employees in quality initiatives. TQM emphasizes long-term success through customer satisfaction, fostering a culture of continuous improvement and collaboration across all levels of the organization.
Key Principles of TQM:
Customer Focus:
- Emphasis: Understanding and meeting customer needs and expectations.
- Impact: Drives all quality improvement efforts towards enhancing customer satisfaction and loyalty.
Total Employee Involvement:
- Emphasis: Engaging all employees in quality initiatives and decision-making.
- Impact: Promotes a sense of ownership and responsibility for quality across the organization.
Process-Centric Approach:
- Emphasis: Focusing on optimizing and improving processes to achieve desired outcomes.
- Impact: Enhances efficiency, reduces waste, and ensures consistent quality.
Integrated System:
- Emphasis: Aligning all organizational processes and functions towards common quality goals.
- Impact: Ensures coherence and synergy in quality efforts, eliminating silos and fostering collaboration.
Strategic and Systematic Approach:
- Emphasis: Incorporating quality improvement into the organization’s strategic planning.
- Impact: Aligns quality initiatives with overall business objectives, ensuring sustainable improvement.
Continual Improvement:
- Emphasis: Committing to ongoing enhancements in processes, products, and services.
- Impact: Drives innovation and adaptability, ensuring the organization remains competitive.
Fact-Based Decision Making:
- Emphasis: Utilizing data and statistical analysis to guide decisions.
- Impact: Enhances the accuracy and effectiveness of quality improvement efforts.
Communication:
- Emphasis: Promoting open and effective communication throughout the organization.
- Impact: Facilitates the sharing of ideas, feedback, and best practices, enhancing collective quality efforts.
Differences Between TQM and Traditional Quality Control Methods:
Aspect | Total Quality Management (TQM) | Traditional Quality Control Methods |
---|---|---|
Scope | Organization-wide, involving all departments and employees | Limited to specific departments, often QC teams |
Approach | Proactive, focusing on prevention and continuous improvement | Reactive, focusing on detection and correction of defects |
Employee Involvement | High, with all employees participating in quality initiatives | Low to moderate, primarily involving QC personnel |
Focus | Comprehensive improvement of processes, products, and services | Specific focus on product inspection and defect elimination |
Goals | Long-term customer satisfaction and organizational excellence | Short-term defect reduction and compliance |
Methodology | Integrates various quality tools and principles (e.g., Lean, Six Sigma) | Primarily inspection and testing techniques |
Cultural Emphasis | Cultivates a culture of quality and continuous improvement | Maintains quality standards through established protocols |
Measurement | Uses a wide range of metrics aligned with strategic goals | Relies on specific quality metrics and defect rates |
Conclusion: Total Quality Management represents a holistic and integrated approach to quality, involving every aspect of an organization and promoting a culture of continuous improvement and employee engagement. In contrast, traditional quality control methods are more narrowly focused on inspecting and correcting defects within specific areas. TQM’s comprehensive scope and proactive nature make it more effective for achieving sustained quality excellence and long-term organizational success.
6. How does Six Sigma methodology contribute to quality assurance in manufacturing?
Answer:
Six Sigma is a data-driven methodology aimed at improving quality by identifying and eliminating defects and minimizing variability in manufacturing processes. It uses statistical tools and structured problem-solving techniques to achieve near-perfection in product and process quality.
Key Components of Six Sigma:
DMAIC Framework:
- Define: Identify the problem, project goals, and customer requirements.
- Measure: Collect and analyze data to understand current process performance.
- Analyze: Identify root causes of defects and process variations.
- Improve: Develop and implement solutions to eliminate root causes.
- Control: Monitor the improved process to sustain gains and prevent recurrence.
Statistical Tools:
- Examples: Regression analysis, hypothesis testing, control charts, process capability analysis.
- Contribution: Provides rigorous quantitative analysis to identify defects, understand process behavior, and validate improvements.
Focus on Customer Requirements:
- How: Align quality improvement efforts with customer needs and expectations.
- Impact: Ensures that quality enhancements directly contribute to increased customer satisfaction and loyalty.
Reduction of Process Variability:
- How: Implement controls and improvements to minimize variations in manufacturing processes.
- Impact: Leads to more consistent product quality and reduces the likelihood of defects.
Root Cause Analysis:
- How: Utilize tools like Fishbone Diagrams and the 5 Whys to identify underlying causes of quality issues.
- Impact: Ensures that solutions address the true sources of defects, preventing recurrence and fostering long-term improvements.
Contribution of Six Sigma to Quality Assurance:
Defect Reduction:
- Impact: Aims for a defect rate of 3.4 defects per million opportunities (DPMO), significantly enhancing product quality and reliability.
Process Improvement:
- Impact: Streamlines manufacturing processes, increases efficiency, and reduces waste by eliminating non-value-adding activities.
Data-Driven Decision Making:
- Impact: Ensures that quality improvement initiatives are based on objective data and statistical analysis, increasing the effectiveness of solutions.
Enhanced Predictability:
- Impact: Reduces process variability, leading to more predictable and stable manufacturing outcomes.
Cost Savings:
- Impact: Lowers costs associated with defects, rework, scrap, and warranty claims, contributing to improved profitability.
Employee Empowerment:
- Impact: Involves employees at all levels in quality improvement projects, fostering a culture of continuous improvement and accountability.
Compliance and Standards:
- Impact: Helps organizations meet stringent industry standards and regulatory requirements by maintaining high-quality processes.
Case Example: A manufacturing company producing automotive components implemented Six Sigma to address high defect rates in its stamping process. Using the DMAIC framework, they defined the problem, measured current performance, analyzed data to identify variations in material thickness as the root cause, and improved the process by standardizing material inputs and enhancing machine calibration. As a result, defect rates decreased by 50%, production costs were reduced by 20%, and customer satisfaction improved significantly.
Conclusion: Six Sigma methodology plays a pivotal role in quality assurance within manufacturing by providing a structured, data-driven approach to identify and eliminate defects, reduce process variability, and enhance overall product quality. Its emphasis on statistical analysis, root cause identification, and continuous improvement ensures that manufacturing processes are efficient, reliable, and capable of meeting high-quality standards, thereby driving organizational success and customer satisfaction.
7. What is the role of Total Productive Maintenance (TPM) in ensuring manufacturing quality, and how does it integrate with quality assurance practices?
Answer:
Total Productive Maintenance (TPM) is a holistic maintenance strategy aimed at maximizing the operational efficiency of equipment by involving all employees in maintenance activities. TPM focuses on proactive and preventive maintenance to ensure that machinery operates reliably, minimizing downtime and defects, which are critical for maintaining high manufacturing quality.
Role of TPM in Ensuring Manufacturing Quality:
Equipment Reliability:
- Function: Ensures that machinery and equipment are consistently operating at optimal performance levels.
- Impact: Reduces the likelihood of equipment-related defects and production interruptions, leading to higher product quality.
Preventive Maintenance:
- Function: Implements scheduled maintenance activities based on data and predictive analytics to prevent equipment failures.
- Impact: Minimizes unplanned downtime and extends the lifespan of machinery, ensuring continuous and stable production processes.
Autonomous Maintenance:
- Function: Empowers operators to perform routine maintenance tasks such as cleaning, lubricating, and inspecting equipment.
- Impact: Increases operator ownership and responsibility for equipment, leading to early detection of potential issues and enhanced overall equipment reliability.
Focused Improvement (Kaizen):
- Function: Conducts continuous improvement initiatives to identify and eliminate root causes of equipment-related losses.
- Impact: Drives targeted enhancements that improve equipment performance and support quality objectives by reducing variability and defects.
Quality Maintenance:
- Function: Ensures that equipment is maintained to produce defect-free products by preventing equipment-related quality issues.
- Impact: Enhances product quality, reduces rework and scrap, and aligns with quality assurance goals of delivering consistent and reliable products.
Training and Education:
- Function: Provides comprehensive training to employees on equipment operation, maintenance practices, and TPM principles.
- Impact: Equips workers with the necessary skills and knowledge to effectively maintain and improve equipment, fostering a culture of continuous improvement and quality focus.
Integration of TPM with Quality Assurance Practices:
Synergistic Objectives:
- Alignment: Both TPM and QA aim to ensure high product quality and process reliability.
- Integration: TPM’s focus on equipment reliability complements QA’s emphasis on consistent product standards, creating a cohesive quality management system.
Data Sharing and Analysis:
- Integration: Utilize data collected from TPM activities (e.g., equipment performance metrics, maintenance logs) in QA processes.
- Benefit: Enhances the ability to identify correlations between equipment performance and product quality, facilitating more informed quality improvement actions.
Cross-Functional Collaboration:
- Integration: Encourage collaboration between maintenance teams (TPM) and quality assurance teams to address quality issues related to equipment performance.
- Benefit: Promotes a unified approach to problem-solving and continuous improvement, ensuring that quality issues are comprehensively addressed.
Continuous Improvement:
- Integration: Use TPM’s Kaizen events to support QA’s continuous improvement initiatives.
- Benefit: Drives ongoing enhancements in both equipment performance and quality processes, fostering a culture of excellence and adaptability.
Standardization and Documentation:
- Integration: Incorporate TPM’s standardized maintenance procedures into QA documentation and quality management systems.
- Benefit: Ensures consistency in maintenance practices, reducing process variability and supporting standardized quality outcomes.
Benefits of Integrating TPM with Quality Assurance:
- Enhanced Equipment Reliability: Ensures that machinery operates consistently, reducing defects and improving product quality.
- Reduced Downtime: Minimizes unplanned equipment failures, ensuring continuous production and timely delivery of products.
- Improved Quality Consistency: Aligns maintenance practices with quality standards, ensuring that products meet or exceed customer expectations.
- Cost Savings: Reduces costs associated with equipment repairs, downtime, and quality-related rework and scrap.
- Employee Engagement: Involves employees in maintenance and quality initiatives, fostering a sense of ownership and responsibility for quality outcomes.
- Sustainable Quality Improvements: Ensures that quality improvements are maintained over time through ongoing maintenance and continuous improvement efforts.
Case Example: A manufacturing plant integrated TPM with Lean Manufacturing by implementing autonomous maintenance practices and using Overall Equipment Effectiveness (OEE) to monitor equipment performance. Operators were trained to perform daily maintenance tasks, and predictive maintenance schedules were established based on real-time data. This integration led to a 35% reduction in equipment downtime, a 20% increase in overall productivity, and a significant improvement in product quality, demonstrating the effectiveness of combining TPM with quality assurance practices.
Conclusion: Total Productive Maintenance plays a crucial role in ensuring manufacturing quality by enhancing equipment reliability, reducing downtime, and supporting continuous improvement initiatives. When integrated with quality assurance practices, TPM provides a comprehensive approach to maintaining high standards of product quality and process efficiency. This synergy not only reduces defects and operational costs but also fosters a culture of quality and continuous improvement, driving sustained success and competitive advantage in the manufacturing sector.
Quality Control and Assurance: More Review Questions
1. What are the fundamental principles of Total Quality Management (TQM) in manufacturing?
Answer:
Total Quality Management (TQM) is a holistic approach aimed at embedding quality in every aspect of manufacturing processes. The fundamental principles of TQM include:
Customer Focus:
- Principle: Prioritize customer needs and strive to exceed customer expectations.
- Impact: Enhances customer satisfaction and loyalty, driving repeat business and positive word-of-mouth.
Total Employee Involvement:
- Principle: Engage all employees in quality initiatives and decision-making processes.
- Impact: Fosters a sense of ownership and responsibility for quality, leading to proactive problem-solving and continuous improvement.
Process-Centric Approach:
- Principle: Focus on optimizing and improving processes to achieve desired outcomes.
- Impact: Increases efficiency, reduces waste, and ensures consistent quality across production.
Integrated System:
- Principle: Align all organizational processes and functions towards common quality goals.
- Impact: Promotes coherence and synergy in quality efforts, eliminating silos and enhancing collaboration.
Strategic and Systematic Approach:
- Principle: Incorporate quality improvement into the organization’s strategic planning.
- Impact: Ensures that quality initiatives are aligned with long-term business objectives and sustained over time.
Continual Improvement:
- Principle: Commit to ongoing enhancements in processes, products, and services.
- Impact: Drives innovation and adaptability, ensuring the organization remains competitive and responsive to changing market demands.
Fact-Based Decision Making:
- Principle: Use data and statistical analysis to guide decisions and measure performance.
- Impact: Enhances the accuracy and effectiveness of quality improvement efforts, reducing reliance on intuition or guesswork.
Communication:
- Principle: Promote open and effective communication throughout the organization.
- Impact: Facilitates the sharing of ideas, feedback, and best practices, enhancing collective quality efforts.
Conclusion: TQM integrates these principles to create a culture of quality and continuous improvement within manufacturing organizations. By emphasizing customer satisfaction, employee involvement, process optimization, and data-driven decision-making, TQM ensures that quality is maintained and enhanced across all facets of the manufacturing process, leading to sustained operational excellence and competitive advantage.
2. How does ISO 9001 certification benefit manufacturing organizations in terms of quality assurance?
Answer:
ISO 9001 is an internationally recognized standard for quality management systems (QMS). Achieving ISO 9001 certification offers numerous benefits to manufacturing organizations in terms of quality assurance:
Standardization of Processes:
- Benefit: Establishes uniform procedures and processes across the organization.
- Impact: Ensures consistency in product quality and operational efficiency, reducing variability and defects.
Enhanced Customer Confidence:
- Benefit: Demonstrates the organization’s commitment to quality and continuous improvement.
- Impact: Builds trust with customers, leading to increased satisfaction, loyalty, and potential for repeat business.
Improved Process Efficiency:
- Benefit: Identifies and eliminates inefficiencies through systematic process evaluation and improvement.
- Impact: Reduces waste, lowers operational costs, and increases overall productivity.
Risk Management:
- Benefit: Incorporates risk-based thinking to identify and mitigate potential quality issues.
- Impact: Prevents defects and disruptions, ensuring smoother operations and reliable product delivery.
Continuous Improvement:
- Benefit: Emphasizes ongoing enhancements in processes and quality management practices.
- Impact: Drives innovation and adaptability, allowing the organization to stay competitive and responsive to market changes.
Employee Engagement:
- Benefit: Involves employees in quality initiatives and decision-making processes.
- Impact: Fosters a culture of accountability and continuous improvement, enhancing employee morale and productivity.
Regulatory Compliance:
- Benefit: Helps ensure adherence to industry regulations and standards.
- Impact: Reduces the risk of non-compliance penalties and enhances the organization’s reputation in the market.
Market Access:
- Benefit: Many customers and partners require ISO 9001 certification as a prerequisite for doing business.
- Impact: Expands market opportunities and enhances the organization’s credibility and competitive edge.
Data-Driven Decision Making:
- Benefit: Promotes the use of data and statistical analysis in managing quality.
- Impact: Enhances the accuracy and effectiveness of quality-related decisions, leading to better outcomes.
Supplier Relationships:
- Benefit: Encourages the selection and maintenance of suppliers who also adhere to quality standards.
- Impact: Ensures that raw materials and components meet quality requirements, supporting the overall product quality.
Conclusion: ISO 9001 certification significantly benefits manufacturing organizations by establishing a robust framework for quality assurance. It promotes process standardization, enhances customer confidence, improves efficiency, and fosters a culture of continuous improvement. These advantages not only lead to higher product quality and customer satisfaction but also contribute to the organization’s long-term success and competitiveness in the global market.
3. What are the key steps involved in implementing a Quality Management System (QMS) in a manufacturing facility?
Answer:
Implementing a Quality Management System (QMS) in a manufacturing facility involves a series of structured steps to ensure that quality objectives are met and maintained. The key steps include:
Define Quality Objectives:
- Action: Establish clear, measurable quality goals aligned with the organization’s strategic objectives.
- Impact: Provides direction and focus for QMS implementation, ensuring that efforts contribute to overall business success.
Obtain Management Commitment:
- Action: Secure support and active involvement from top management.
- Impact: Ensures adequate resources, prioritization, and leadership necessary for successful QMS implementation.
Conduct a Gap Analysis:
- Action: Assess the current quality practices against the desired QMS standards (e.g., ISO 9001).
- Impact: Identifies areas that require improvement and helps in developing a roadmap for implementation.
Develop a QMS Plan:
- Action: Create a detailed plan outlining the scope, objectives, resources, timelines, and responsibilities for QMS implementation.
- Impact: Provides a structured approach, ensuring that all necessary activities are planned and executed systematically.
Design and Document Processes:
- Action: Identify and document key manufacturing processes, standard operating procedures (SOPs), and work instructions.
- Impact: Establishes clear guidelines and standards for consistent and quality-focused operations.
Employee Training and Involvement:
- Action: Train employees on QMS principles, procedures, and their specific roles in maintaining quality.
- Impact: Enhances employee understanding and engagement, fostering a culture of quality and continuous improvement.
Implement Quality Control Measures:
- Action: Introduce QC tools and techniques (e.g., inspection, testing, SPC) to monitor and control process performance.
- Impact: Ensures that products meet quality standards and defects are identified and addressed promptly.
Establish Documentation and Record-Keeping:
- Action: Maintain comprehensive records of quality activities, audits, inspections, and corrective actions.
- Impact: Provides evidence of compliance, facilitates traceability, and supports continuous improvement efforts.
Conduct Internal Audits:
- Action: Regularly perform internal audits to assess the effectiveness of the QMS and identify areas for improvement.
- Impact: Ensures that the QMS is functioning as intended and highlights opportunities for enhancing quality practices.
Implement Corrective and Preventive Actions (CAPA):
- Action: Develop and execute actions to address identified non-conformities and prevent their recurrence.
- Impact: Continuously improves the QMS by addressing root causes and mitigating potential quality issues.
Management Review:
- Action: Conduct periodic reviews by top management to evaluate QMS performance, analyze audit findings, and set new quality objectives.
- Impact: Ensures ongoing alignment of the QMS with organizational goals and fosters strategic decision-making for quality improvement.
Certification and Continuous Improvement:
- Action: Pursue external certification (e.g., ISO 9001) and commit to ongoing enhancements based on feedback and performance data.
- Impact: Validates the effectiveness of the QMS and ensures that quality standards are maintained and improved over time.
Conclusion: Implementing a Quality Management System in a manufacturing facility requires a systematic approach involving clear objectives, management commitment, process documentation, employee training, and continuous monitoring and improvement. By following these key steps, organizations can establish a robust QMS that ensures consistent product quality, enhances customer satisfaction, and drives long-term operational excellence.
4. What are the common quality assurance methodologies used in manufacturing, and how do they differ from each other?
Answer:
Quality Assurance (QA) methodologies in manufacturing are structured approaches aimed at ensuring that products and processes meet specified quality standards. The common QA methodologies include:
Six Sigma:
- Description: A data-driven methodology focused on reducing defects and process variability using the DMAIC (Define, Measure, Analyze, Improve, Control) framework.
- Key Features: Emphasizes statistical analysis, root cause identification, and process optimization.
- Difference: Highly structured and quantitative, focusing on near-perfection with a target of 3.4 defects per million opportunities.
Lean Manufacturing:
- Description: A methodology centered on eliminating waste (non-value-adding activities) and optimizing processes to enhance efficiency and customer value.
- Key Features: Utilizes tools like Value Stream Mapping, 5S, Kanban, and Just-In-Time (JIT) production.
- Difference: Primarily focuses on process efficiency and waste reduction rather than defect elimination.
Total Quality Management (TQM):
- Description: A holistic approach that involves all employees in continuous quality improvement efforts to enhance product quality and customer satisfaction.
- Key Features: Emphasizes organizational culture, employee involvement, and customer focus.
- Difference: Comprehensive and culturally driven, integrating quality into every aspect of the organization.
ISO 9001:
- Description: An international standard for Quality Management Systems (QMS) that provides a framework for consistent quality practices.
- Key Features: Focuses on documentation, process standardization, and continuous improvement.
- Difference: Certification-based, providing a recognized benchmark for quality assurance.
Kaizen:
- Description: A philosophy of continuous, incremental improvement involving all employees.
- Key Features: Encourages small, ongoing changes to improve processes and eliminate waste.
- Difference: Highly participative and incremental, focusing on fostering a culture of ongoing improvement.
Failure Mode and Effects Analysis (FMEA):
- Description: A proactive tool used to identify potential failure modes, assess their impact, and implement corrective actions.
- Key Features: Focuses on risk assessment and mitigation to prevent defects before they occur.
- Difference: Specific to risk management and failure prevention within processes.
Statistical Process Control (SPC):
- Description: Utilizes statistical methods to monitor and control manufacturing processes.
- Key Features: Employs control charts and statistical analysis to detect process variations.
- Difference: Focuses on real-time monitoring and control of process stability and consistency.
Benchmarking:
- Description: Involves comparing an organization’s processes and performance metrics to industry bests or best practices from other companies.
- Key Features: Identifies areas for improvement by learning from others’ successes.
- Difference: External comparison-based, seeking to adopt proven practices from other organizations.
Differences Between QA Methodologies:
Methodology | Focus | Key Tools/Techniques | Primary Objective |
---|---|---|---|
Six Sigma | Defect reduction and variability control | DMAIC, statistical analysis | Achieve near-perfect process performance |
Lean | Waste elimination and process efficiency | Value Stream Mapping, 5S, Kanban | Enhance efficiency and customer value |
TQM | Organizational culture and continuous improvement | Employee involvement, customer focus | Integrate quality into every aspect of the organization |
ISO 9001 | Standardization and compliance | Documentation, process audits | Establish a certified QMS aligned with international standards |
Kaizen | Continuous, incremental improvement | Small, ongoing changes | Foster a culture of continuous improvement |
FMEA | Risk assessment and failure prevention | Risk prioritization, corrective actions | Identify and mitigate potential failures before they occur |
SPC | Real-time process monitoring | Control charts, statistical tools | Maintain process stability and consistency |
Benchmarking | External comparison and adoption of best practices | Performance metrics comparison | Identify and implement best practices from other organizations |
Conclusion: While all QA methodologies aim to enhance product quality and process efficiency, they differ in their focus, tools, and approaches. Six Sigma emphasizes defect reduction through statistical analysis, Lean focuses on waste elimination and efficiency, TQM integrates quality into organizational culture, and ISO 9001 provides a standardized framework for quality management. Understanding these differences allows manufacturing organizations to select and combine methodologies that best suit their specific quality assurance needs and strategic objectives.
5. How can Lean Manufacturing principles be integrated with Six Sigma to create a synergistic approach to quality improvement?
Answer:
Integrating Lean Manufacturing principles with Six Sigma creates a powerful synergistic approach known as Lean Six Sigma, which combines the strengths of both methodologies to achieve comprehensive quality improvement. This integration leverages Lean’s focus on waste elimination and process efficiency with Six Sigma’s emphasis on defect reduction and variability control, resulting in enhanced operational performance and customer satisfaction.
Steps to Integrate Lean and Six Sigma:
Align Objectives:
- Action: Define common goals that encompass both Lean’s efficiency and Six Sigma’s quality focus.
- Impact: Ensures that improvement initiatives address both waste reduction and defect elimination simultaneously.
Adopt a Unified Framework:
- Action: Utilize Six Sigma’s DMAIC (Define, Measure, Analyze, Improve, Control) framework within Lean projects.
- Impact: Provides a structured approach that incorporates both process optimization and statistical analysis.
Combine Tools and Techniques:
- Action: Integrate Lean tools (e.g., Value Stream Mapping, 5S) with Six Sigma tools (e.g., Control Charts, FMEA).
- Impact: Enhances the ability to identify and eliminate waste while simultaneously reducing process variability and defects.
Foster a Culture of Continuous Improvement:
- Action: Promote a culture that values both efficiency and quality, encouraging employees to seek ongoing improvements.
- Impact: Drives sustained quality enhancements and operational efficiencies across the organization.
Train and Empower Employees:
- Action: Provide comprehensive training on both Lean and Six Sigma principles and tools.
- Impact: Equips employees with the skills needed to implement integrated improvement initiatives effectively.
Cross-Functional Collaboration:
- Action: Encourage collaboration between Lean and Six Sigma teams to leverage diverse expertise.
- Impact: Facilitates holistic problem-solving and ensures that improvement efforts are comprehensive and aligned.
Data-Driven Decision Making:
- Action: Use data from Six Sigma’s statistical analysis to inform Lean’s process optimization efforts.
- Impact: Ensures that quality improvements are based on objective data and insights, enhancing their effectiveness.
Implement Rapid Improvements:
- Action: Utilize Lean’s quick-changeover techniques and Six Sigma’s root cause analysis for swift implementation of improvements.
- Impact: Accelerates the pace of quality and efficiency enhancements, yielding faster results.
Benefits of Lean Six Sigma Integration:
Comprehensive Quality Improvement:
- Benefit: Addresses both process inefficiencies and quality defects, leading to more robust and reliable manufacturing processes.
Enhanced Efficiency and Quality:
- Benefit: Achieves greater operational efficiency while simultaneously ensuring high product quality and consistency.
Cost Reduction:
- Benefit: Eliminates waste and reduces defects, resulting in significant cost savings related to materials, labor, and rework.
Increased Customer Satisfaction:
- Benefit: Delivers high-quality products efficiently, meeting or exceeding customer expectations and enhancing satisfaction and loyalty.
Improved Process Stability:
- Benefit: Reduces process variability and enhances stability, ensuring consistent production outcomes and minimizing disruptions.
Employee Engagement and Empowerment:
- Benefit: Involves employees in continuous improvement efforts, fostering a sense of ownership and enhancing morale and productivity.
Sustainable Competitive Advantage:
- Benefit: Establishes a culture of excellence and continuous improvement, enabling the organization to adapt to changing market demands and maintain a competitive edge.
Case Example: A manufacturing company producing electronic components integrated Lean Six Sigma to optimize its assembly line. Lean tools like 5S and Kanban were used to organize the workspace and manage inventory efficiently, while Six Sigma’s DMAIC framework addressed defects in soldering processes. This integration led to a 40% reduction in production lead time, a 35% decrease in defect rates, and a 25% reduction in operational costs, demonstrating the effectiveness of combining Lean and Six Sigma for comprehensive quality improvement.
Conclusion: Integrating Lean Manufacturing principles with Six Sigma creates a synergistic approach that leverages the strengths of both methodologies to achieve comprehensive quality and efficiency improvements. Lean Six Sigma enables manufacturing organizations to eliminate waste, reduce defects, optimize processes, and enhance customer satisfaction, leading to sustained operational excellence and competitive advantage. By fostering a culture of continuous improvement and empowering employees with the necessary tools and training, organizations can effectively implement Lean Six Sigma to drive significant and lasting quality enhancements.
6. What is the importance of ISO 9001 certification for manufacturing companies, and what are the key requirements to achieve it?
Answer:
ISO 9001 is an internationally recognized standard for Quality Management Systems (QMS). Achieving ISO 9001 certification is highly beneficial for manufacturing companies, as it demonstrates a commitment to quality, enhances credibility, and can provide a competitive advantage in the marketplace.
Importance of ISO 9001 Certification for Manufacturing Companies:
Enhanced Credibility and Reputation:
- Importance: ISO 9001 certification is a globally recognized indicator of quality.
- Impact: Builds trust with customers, suppliers, and stakeholders, enhancing the company’s reputation and marketability.
Customer Satisfaction:
- Importance: Focuses on meeting customer requirements and improving satisfaction.
- Impact: Leads to increased customer loyalty, repeat business, and positive word-of-mouth referrals.
Process Standardization:
- Importance: Establishes standardized procedures and processes across the organization.
- Impact: Ensures consistency in product quality, reduces variability, and enhances operational efficiency.
Continuous Improvement:
- Importance: Emphasizes ongoing enhancements to processes and systems.
- Impact: Drives long-term operational excellence, innovation, and adaptability to changing market conditions.
Regulatory Compliance:
- Importance: Helps ensure adherence to industry regulations and standards.
- Impact: Reduces the risk of non-compliance penalties and enhances the ability to enter regulated markets.
Operational Efficiency:
- Importance: Identifies and eliminates inefficiencies through systematic process evaluation.
- Impact: Lowers operational costs, reduces waste, and improves resource utilization.
Employee Engagement:
- Importance: Involves employees in quality initiatives and continuous improvement efforts.
- Impact: Fosters a culture of quality, accountability, and teamwork, enhancing employee morale and productivity.
Market Access:
- Importance: Many customers and partners require ISO 9001 certification as a prerequisite for doing business.
- Impact: Expands market opportunities and facilitates partnerships with larger organizations and international clients.
Key Requirements to Achieve ISO 9001 Certification:
Scope Definition:
- Requirement: Clearly define the scope of the QMS, specifying the products, services, and processes covered.
- Purpose: Ensures that the QMS is focused and relevant to the organization’s operations.
Leadership Commitment:
- Requirement: Top management must demonstrate commitment to the QMS by providing resources, setting quality objectives, and fostering a quality-centric culture.
- Purpose: Ensures that quality initiatives are prioritized and supported at the highest levels of the organization.
Customer Focus:
- Requirement: Understand and meet customer needs and expectations, aiming to enhance customer satisfaction.
- Purpose: Aligns quality efforts with customer requirements, driving satisfaction and loyalty.
Quality Policy and Objectives:
- Requirement: Develop a quality policy and set measurable quality objectives aligned with organizational goals.
- Purpose: Provides direction and targets for quality improvement initiatives.
Risk-Based Thinking:
- Requirement: Identify and address risks and opportunities that could impact the QMS and product quality.
- Purpose: Enhances proactive management of potential issues, preventing defects and disruptions.
Process Approach:
- Requirement: Manage activities as interconnected processes that function as a coherent system.
- Purpose: Improves efficiency, consistency, and effectiveness of operations by understanding and optimizing process interactions.
Documented Information:
- Requirement: Maintain comprehensive documentation, including procedures, work instructions, and records, to support the QMS.
- Purpose: Ensures clarity, consistency, and traceability of quality-related activities.
Competence and Training:
- Requirement: Ensure that employees are competent through appropriate training and education.
- Purpose: Enhances the ability of employees to perform their roles effectively, contributing to overall quality.
Monitoring and Measurement:
- Requirement: Implement mechanisms to monitor, measure, analyze, and evaluate the performance of the QMS.
- Purpose: Provides data-driven insights to assess the effectiveness of quality initiatives and identify areas for improvement.
Internal Audits and Reviews:
- Requirement: Conduct regular internal audits and management reviews to evaluate QMS performance and compliance.
- Purpose: Ensures that the QMS remains effective, compliant, and aligned with quality objectives.
Continuous Improvement:
- Requirement: Establish processes for continuous improvement, including corrective and preventive actions.
- Purpose: Drives ongoing enhancements to the QMS, ensuring sustained quality and operational excellence.
Conclusion: ISO 9001 certification is a valuable asset for manufacturing companies, offering numerous benefits related to quality assurance, operational efficiency, and market competitiveness. By adhering to its key requirements, organizations can establish a robust QMS that ensures consistent product quality, enhances customer satisfaction, and supports continuous improvement. Achieving ISO 9001 certification not only validates the organization’s commitment to quality but also opens up new business opportunities and strengthens its position in the global market.
7. How does the concept of Continuous Improvement (Kaizen) enhance quality control in manufacturing?
Answer:
Continuous Improvement (Kaizen) is a core principle of Lean Manufacturing that focuses on making incremental, ongoing enhancements to processes, products, and services. In the context of quality control in manufacturing, Kaizen plays a pivotal role in fostering a culture of excellence and driving systematic quality improvements.
How Kaizen Enhances Quality Control:
Employee Involvement and Empowerment:
- Mechanism: Encourages all employees, from operators to management, to contribute ideas for process improvements.
- Enhancement: Leverages the collective knowledge and experience of the workforce, leading to innovative solutions and greater ownership of quality outcomes.
Systematic Problem-Solving:
- Mechanism: Utilizes structured approaches such as the PDCA (Plan-Do-Check-Act) cycle to identify, analyze, and resolve quality issues.
- Enhancement: Ensures that quality problems are addressed methodically, preventing recurrence and fostering sustainable improvements.
Waste Elimination:
- Mechanism: Identifies and eliminates non-value-adding activities (waste) that do not contribute to product quality.
- Enhancement: Streamlines processes, reduces complexity, and focuses resources on activities that enhance quality, leading to more efficient and effective quality control.
Standardization and Documentation:
- Mechanism: Develops and updates standard operating procedures (SOPs) based on best practices and successful improvements.
- Enhancement: Ensures consistency in quality control practices, reducing variability and enhancing the reliability of quality outcomes.
Data-Driven Decision Making:
- Mechanism: Collects and analyzes data related to quality metrics to identify trends and areas for improvement.
- Enhancement: Provides objective insights that inform quality control strategies, ensuring that improvements are based on factual evidence rather than assumptions.
Incremental Improvements:
- Mechanism: Focuses on making small, manageable changes that cumulatively lead to significant quality enhancements.
- Enhancement: Allows for continuous progress without overwhelming the organization, ensuring that quality control remains adaptable and responsive to changes.
Rapid Implementation and Feedback:
- Mechanism: Implements improvements quickly and gathers immediate feedback to assess their effectiveness.
- Enhancement: Facilitates swift validation of changes, enabling the organization to refine and optimize quality control measures in real-time.
Enhanced Process Understanding:
- Mechanism: Encourages detailed analysis and understanding of manufacturing processes to identify root causes of quality issues.
- Enhancement: Leads to deeper insights into how processes impact quality, enabling more effective and targeted quality control interventions.
Benefits of Kaizen in Quality Control:
- Improved Product Quality: Continuous, incremental improvements lead to higher quality products with fewer defects.
- Increased Efficiency: Eliminating waste and optimizing processes enhances overall manufacturing efficiency.
- Higher Employee Morale: Involving employees in quality improvement fosters a sense of purpose and satisfaction, boosting morale and productivity.
- Reduced Costs: Enhancing quality and efficiency reduces costs associated with defects, rework, and waste.
- Greater Flexibility: Continuous improvement enables the organization to adapt quickly to changing customer demands and market conditions.
- Sustained Competitive Advantage: A culture of Kaizen ensures that the organization remains committed to excellence and innovation, maintaining its competitive edge.
Case Example: A manufacturing plant producing automotive parts implemented Kaizen by establishing regular improvement meetings where employees could suggest process enhancements. One such suggestion involved reorganizing the assembly line layout to reduce unnecessary movement and handling of components. After implementing this change, the plant observed a 15% reduction in assembly time and a 20% decrease in defect rates, demonstrating the effectiveness of Kaizen in enhancing quality control.
Conclusion: Continuous Improvement (Kaizen) significantly enhances quality control in manufacturing by fostering a proactive, employee-driven culture of excellence. Through systematic problem-solving, waste elimination, data-driven decision making, and incremental improvements, Kaizen ensures that quality control processes are continuously refined and optimized. This leads to higher product quality, increased operational efficiency, reduced costs, and sustained competitive advantage, making Kaizen an indispensable component of effective quality control in manufacturing.
8. What are the key components of a Quality Management System (QMS) in manufacturing, and how do they contribute to overall quality assurance?
Answer:
A Quality Management System (QMS) in manufacturing is a structured framework of policies, processes, procedures, and resources designed to ensure that products meet customer requirements and quality standards consistently. The key components of a QMS and their contributions to overall quality assurance are as follows:
Quality Policy and Objectives:
- Component: A formal statement by top management outlining the organization’s commitment to quality and setting measurable quality goals.
- Contribution: Provides a clear direction and focus for quality initiatives, aligning them with the organization’s strategic objectives and ensuring that all employees understand their role in achieving quality targets.
Quality Manual:
- Component: A document that describes the QMS, including the scope, processes, and interactions within the system.
- Contribution: Serves as a reference guide for employees, ensuring consistency in quality practices and facilitating understanding of the QMS structure and requirements.
Standard Operating Procedures (SOPs) and Work Instructions:
- Component: Detailed documents outlining the steps and methods for performing specific tasks and processes.
- Contribution: Ensures uniformity in operations, reduces variability, and provides clear guidance to employees, thereby enhancing process consistency and product quality.
Process Documentation:
- Component: Comprehensive records of all manufacturing processes, including flowcharts, process maps, and descriptions.
- Contribution: Facilitates process understanding, identifies potential areas for improvement, and ensures that processes are performed correctly and consistently.
Document Control:
- Component: Procedures for managing and controlling documents and records to ensure that only current and approved documents are in use.
- Contribution: Maintains the integrity and accuracy of documentation, preventing errors and ensuring compliance with quality standards and regulatory requirements.
Employee Training and Competence:
- Component: Programs and initiatives to train employees on QMS principles, procedures, and their specific roles in maintaining quality.
- Contribution: Ensures that employees are knowledgeable and skilled, enhancing their ability to perform tasks accurately and contribute to quality assurance efforts.
Internal Audits:
- Component: Regular, systematic examinations of the QMS to assess compliance with standards and identify areas for improvement.
- Contribution: Provides objective evaluations of the QMS’s effectiveness, ensuring that processes are functioning as intended and highlighting opportunities for enhancement.
Non-Conformance Management:
- Component: Procedures for identifying, documenting, and addressing deviations from quality standards.
- Contribution: Ensures that defects and non-conformities are promptly addressed, preventing their recurrence and minimizing their impact on product quality.
Corrective and Preventive Actions (CAPA):
- Component: Processes for investigating root causes of quality issues and implementing actions to eliminate them and prevent future occurrences.
- Contribution: Enhances the organization’s ability to respond to quality issues effectively, driving continuous improvement and reducing the likelihood of recurring problems.
Performance Measurement and Monitoring:
- Component: Metrics and key performance indicators (KPIs) to track the effectiveness of the QMS and quality-related processes.
- Contribution: Provides data-driven insights into process performance, enabling informed decision-making and targeted quality improvement initiatives.
Management Review:
- Component: Regular evaluations by top management of the QMS performance, including audit results, performance metrics, and improvement initiatives.
- Contribution: Ensures that the QMS remains aligned with organizational goals, addresses any identified issues, and promotes continuous improvement.
Continuous Improvement:
- Component: Ongoing efforts to enhance processes, products, and the QMS based on feedback, performance data, and evolving quality standards.
- Contribution: Drives the evolution and refinement of the QMS, ensuring that the organization consistently meets or exceeds quality expectations and adapts to changing market demands.
Conclusion: A Quality Management System in manufacturing encompasses various interconnected components that collectively ensure the consistent delivery of high-quality products. By establishing clear policies, standardizing processes, engaging and training employees, and implementing systematic monitoring and improvement practices, a QMS provides a robust framework for quality assurance. This comprehensive approach not only enhances product quality and customer satisfaction but also drives operational efficiency and organizational excellence, positioning the manufacturing company for sustained success in a competitive market.
9. How can Manufacturing Execution Systems (MES) support quality control and assurance in manufacturing operations?
Answer:
Manufacturing Execution Systems (MES) are computerized systems used in manufacturing to track and document the transformation of raw materials into finished products. MES plays a crucial role in supporting quality control and assurance by providing real-time data, process visibility, and integration across various manufacturing operations. Here’s how MES supports quality initiatives:
Real-Time Monitoring and Data Collection:
- Function: Continuously captures data from machines, sensors, and operators during the production process.
- Support for Quality Control: Enables immediate detection of deviations from quality standards, allowing for prompt corrective actions to prevent defects.
Process Traceability:
- Function: Tracks the complete history of each product, including materials used, process steps, and environmental conditions.
- Support for Quality Assurance: Facilitates root cause analysis by providing detailed traceability, helping identify the sources of quality issues and ensuring accountability.
Standardized Work Instructions:
- Function: Provides operators with clear, step-by-step instructions for each manufacturing process.
- Support for Quality Control: Ensures that processes are performed consistently and correctly, reducing variability and enhancing product quality.
Quality Data Integration:
- Function: Integrates quality inspection data with production data, providing a comprehensive view of quality performance.
- Support for Quality Assurance: Allows for correlation between production variables and quality outcomes, enabling data-driven quality improvements.
Automated Quality Checks:
- Function: Implements automated quality inspections and checks at various stages of production.
- Support for Quality Control: Increases the frequency and accuracy of quality inspections, reducing the likelihood of undetected defects.
Non-Conformance Management:
- Function: Records and manages instances of non-conformance, including defect types, locations, and corrective actions.
- Support for Quality Assurance: Streamlines the process of addressing quality issues, ensuring that corrective actions are tracked and implemented effectively.
Reporting and Analytics:
- Function: Generates detailed reports and analytics on quality metrics, trends, and performance indicators.
- Support for Quality Assurance: Provides insights into quality performance, helping identify areas for improvement and measure the effectiveness of quality initiatives.
Integration with ERP and QMS:
- Function: Connects with Enterprise Resource Planning (ERP) and Quality Management Systems (QMS) to ensure seamless data flow and process alignment.
- Support for Quality Control: Enhances coordination between production and quality teams, ensuring that quality standards are maintained throughout the manufacturing process.
Predictive Maintenance:
- Function: Uses data analytics to predict equipment failures and schedule maintenance proactively.
- Support for Quality Assurance: Prevents equipment-related quality issues by ensuring that machines operate reliably and are maintained before defects occur.
Compliance and Documentation:
- Function: Maintains comprehensive records of production and quality activities to ensure compliance with industry standards and regulations.
- Support for Quality Assurance: Provides evidence of compliance and facilitates audits by ensuring that all quality-related documentation is accurate and up-to-date.
Benefits of MES in Quality Control and Assurance:
- Enhanced Visibility: Provides real-time insights into production and quality metrics, enabling proactive quality management.
- Improved Efficiency: Streamlines quality control processes, reducing the time and resources required for inspections and defect management.
- Higher Quality Standards: Ensures that quality standards are consistently met through standardized procedures and automated checks.
- Data-Driven Decisions: Empowers quality teams with actionable data to identify trends, predict issues, and implement effective quality improvements.
- Reduced Defects: Minimizes the occurrence of defects by enabling immediate detection and correction of quality deviations during production.
- Regulatory Compliance: Simplifies compliance with industry standards and regulations by maintaining accurate and comprehensive quality records.
Case Example: A pharmaceutical manufacturer implemented an MES to integrate its production and quality control processes. The MES provided real-time monitoring of critical process parameters and automated quality inspections at key production stages. By correlating production data with quality outcomes, the company identified and addressed a recurring defect related to temperature fluctuations during a critical manufacturing step. This led to a 25% reduction in defect rates, improved compliance with regulatory standards, and enhanced overall product quality.
Conclusion: Manufacturing Execution Systems play a vital role in supporting quality control and assurance in manufacturing operations. By providing real-time data, process visibility, standardized procedures, and seamless integration with other systems, MES enhances the ability to monitor, manage, and improve quality throughout the production lifecycle. This leads to higher product quality, increased operational efficiency, reduced costs, and stronger compliance with industry standards, ultimately driving sustained success and customer satisfaction in manufacturing organizations.
10. What are the benefits of implementing a Statistical Process Control (SPC) system in manufacturing, and how does it enhance quality assurance?
Answer:
Implementing a Statistical Process Control (SPC) system in manufacturing offers numerous benefits that significantly enhance quality assurance. SPC utilizes statistical methods to monitor and control manufacturing processes, ensuring that they operate at their full potential to produce conforming products with minimal variability.
Benefits of Implementing an SPC System:
Enhanced Process Stability and Consistency:
- Benefit: Monitors process performance in real-time to detect and address variations.
- Enhancement: Ensures that processes remain stable and consistent, reducing the likelihood of defects and enhancing overall product quality.
Early Detection of Issues:
- Benefit: Identifies deviations from control limits before defects occur.
- Enhancement: Allows for immediate corrective actions, preventing defects from being produced and minimizing waste and rework costs.
Data-Driven Decision Making:
- Benefit: Provides objective data on process performance through control charts and statistical analysis.
- Enhancement: Facilitates informed and accurate decision-making, ensuring that quality improvements are based on factual evidence rather than intuition.
Reduction in Process Variability:
- Benefit: Identifies and minimizes sources of variability in manufacturing processes.
- Enhancement: Leads to more consistent product quality, as reduced variability ensures that products meet specifications more reliably.
Cost Savings:
- Benefit: Decreases costs associated with defects, scrap, and rework by preventing defects from occurring.
- Enhancement: Improves profitability by reducing waste and increasing the efficiency of resource utilization.
Improved Compliance and Traceability:
- Benefit: Maintains detailed records of process performance and quality metrics.
- Enhancement: Facilitates compliance with industry standards and regulations by providing traceable evidence of quality control efforts.
Continuous Improvement:
- Benefit: Uses statistical data to identify trends and areas for ongoing process enhancements.
- Enhancement: Supports a culture of continuous improvement, enabling manufacturers to incrementally enhance process performance and quality over time.
Better Understanding of Processes:
- Benefit: Provides insights into how different factors influence process performance and product quality.
- Enhancement: Enhances the ability to optimize processes by understanding the relationships between variables and their impact on quality.
Employee Empowerment:
- Benefit: Involves employees in monitoring and controlling processes through data analysis and interpretation.
- Enhancement: Empowers workers to take ownership of quality control, fostering a proactive approach to quality assurance and improvement.
Enhanced Customer Satisfaction:
- Benefit: Consistently delivers high-quality products that meet or exceed customer expectations.
- Enhancement: Increases customer satisfaction, loyalty, and repeat business, contributing to the organization’s long-term success.
How SPC Enhances Quality Assurance:
- Real-Time Monitoring: Enables continuous oversight of manufacturing processes, ensuring that any deviations from quality standards are detected and addressed promptly.
- Proactive Quality Management: Shifts quality control from a reactive approach (detecting defects after they occur) to a proactive approach (preventing defects by maintaining process control).
- Statistical Analysis: Utilizes statistical tools to analyze process data, identifying patterns and trends that inform quality improvement strategies.
- Integration with QMS: Complements other Quality Management System (QMS) components by providing data and insights that support comprehensive quality assurance efforts.
- Root Cause Identification: Assists in pinpointing the underlying causes of process variations, enabling targeted corrective actions that enhance process reliability and quality.
Case Example: A beverage manufacturer implemented an SPC system to monitor the carbonation levels in its bottled drinks. By using control charts to track carbonation in real-time, they identified a recurring pattern of under-carbonation during specific shifts. Further analysis revealed that a particular batch of CO₂ cylinders was faulty. Replacing the cylinders and adjusting the filling process brought carbonation levels back within control limits, ensuring consistent product quality and reducing customer complaints.
Conclusion: Statistical Process Control is a critical tool in manufacturing quality assurance, providing the means to monitor, control, and improve manufacturing processes systematically. By implementing an SPC system, manufacturers can achieve greater process stability, reduce defects, enhance efficiency, and foster a culture of continuous improvement. These benefits collectively contribute to higher product quality, increased customer satisfaction, and improved financial performance, positioning the organization for sustained success in a competitive market.
11. How does the integration of IoT technologies enhance the real-time monitoring and control of manufacturing processes?
Answer:
Integrating Internet of Things (IoT) technologies into manufacturing processes significantly enhances real-time monitoring and control by enabling continuous data collection, connectivity, and intelligent automation. This integration transforms traditional manufacturing into a smart, connected ecosystem that optimizes performance, increases efficiency, and ensures high-quality production.
Enhancements to Real-Time Monitoring and Control through IoT Integration:
Continuous Data Collection:
- How: Deploy IoT sensors and devices to collect real-time data on various process parameters (e.g., temperature, pressure, machine vibrations).
- Impact: Provides a constant stream of data, allowing for immediate detection of anomalies and process deviations.
Remote Monitoring:
- How: Utilize cloud-based platforms to access process data from anywhere, enabling remote supervision.
- Impact: Enhances flexibility and allows managers to monitor operations in real-time without being physically present, improving responsiveness.
Predictive Analytics:
- How: Analyze data from IoT devices using machine learning algorithms to predict equipment failures and maintenance needs.
- Impact: Enables proactive maintenance scheduling, reducing unplanned downtime and extending equipment lifespan.
Automated Control Systems:
- How: Integrate IoT with control systems to enable automatic adjustments based on real-time data.
- Impact: Enhances process stability and efficiency by maintaining optimal conditions without manual intervention.
Enhanced Quality Control:
- How: Monitor quality parameters continuously and use IoT data to identify and correct quality issues in real-time.
- Impact: Ensures consistent product quality, reduces defect rates, and minimizes rework and scrap.
Energy Management:
- How: Track and analyze energy usage across different parts of the manufacturing process using IoT sensors.
- Impact: Identifies energy-saving opportunities, reduces energy consumption, and lowers operational costs.
Supply Chain Integration:
- How: Use IoT to track inventory levels, material movements, and supplier performance in real-time.
- Impact: Enhances supply chain visibility, reduces lead times, and ensures timely availability of materials, supporting Just-In-Time (JIT) production.
Real-Time Dashboards and Visualization:
- How: Implement dashboards that display real-time data and key performance indicators (KPIs) for easy monitoring.
- Impact: Facilitates quick decision-making and ensures that all stakeholders have access to up-to-date information.
Scalability and Flexibility:
- How: Easily scale IoT deployments to cover additional processes or facilities as needed.
- Impact: Supports growing manufacturing operations and the integration of new technologies without significant overhauls.
Enhanced Safety and Compliance:
- How: Monitor safety parameters and ensure compliance with regulatory standards through real-time data.
- Impact: Enhances workplace safety, reduces the risk of accidents, and ensures adherence to industry regulations.
Benefits of IoT Integration in Real-Time Monitoring and Control:
- Improved Efficiency: Real-time insights enable immediate adjustments to optimize process performance.
- Reduced Downtime: Predictive maintenance and automated controls minimize equipment failures and operational interruptions.
- Enhanced Quality: Continuous monitoring ensures that products meet quality standards consistently.
- Cost Savings: Optimized energy usage and reduced waste lower operational costs.
- Increased Agility: Real-time data allows manufacturers to quickly respond to changes in demand or production conditions.
- Better Decision-Making: Data-driven insights support informed and strategic decision-making, enhancing overall operational performance.
- Enhanced Collaboration: Shared real-time data fosters better communication and collaboration among teams and departments.
Case Example: A semiconductor manufacturer integrated IoT sensors across its fabrication equipment to monitor temperature and pressure in real-time. The data was analyzed using predictive analytics to forecast potential equipment failures. By implementing proactive maintenance based on these insights, the manufacturer reduced unplanned downtime by 30%, increased overall equipment effectiveness (OEE) by 20%, and maintained consistent product quality, leading to higher customer satisfaction and reduced operational costs.
Conclusion: The integration of IoT technologies into manufacturing processes revolutionizes real-time monitoring and control by providing continuous data, enhancing connectivity, and enabling intelligent automation. This integration leads to improved efficiency, reduced downtime, enhanced quality, and significant cost savings, positioning manufacturers for sustained operational excellence and competitive advantage in the evolving industrial landscape.
12. How can manufacturers integrate ergonomic principles into the design of manufacturing tools and equipment to enhance usability and reduce strain on workers?
Answer:
Integrating ergonomic principles into the design of manufacturing tools and equipment is essential for enhancing usability, reducing physical strain on workers, and improving overall productivity and job satisfaction. Ergonomically designed tools and equipment align with the natural movements and capabilities of workers, minimizing the risk of musculoskeletal disorders (MSDs) and other injuries.
Key Ergonomic Principles for Tool and Equipment Design:
Anthropometric Considerations:
- How: Design tools and equipment to accommodate a wide range of body sizes, shapes, and strengths.
- Impact: Ensures that tools are comfortable and easy to use for all workers, reducing the risk of strain and injury.
Neutral Postures:
- How: Design tools that allow workers to maintain neutral body postures, avoiding excessive bending, twisting, or reaching.
- Impact: Minimizes musculoskeletal strain and fatigue, enhancing worker comfort and endurance.
Minimize Force Requirements:
- How: Design tools that require minimal force to operate, using lightweight materials and efficient mechanisms.
- Impact: Reduces the physical effort required by workers, decreasing muscle fatigue and the risk of overexertion injuries.
Enhance Grip Comfort and Control:
- How: Incorporate ergonomic grips with contoured shapes, soft materials, and appropriate sizes to fit the hand naturally.
- Impact: Improves control and precision in tool use, reducing the likelihood of slips and errors while enhancing worker comfort.
Balanced Weight Distribution:
- How: Ensure that tools and equipment have balanced weight distribution to reduce the physical strain on specific body parts.
- Impact: Enhances ease of handling, reducing fatigue and improving task performance.
Adjustable Features:
- How: Include adjustable components such as handle angles, tool heights, and extension lengths to customize tools for different tasks and user preferences.
- Impact: Increases versatility and adaptability, allowing workers to optimize tool use for various tasks and reduce ergonomic risks.
Vibration and Noise Reduction:
- How: Design tools with vibration-dampening materials and noise-reducing features to minimize exposure to harmful vibrations and excessive noise.
- Impact: Protects workers from vibration-induced injuries and reduces noise-related stress, enhancing overall comfort and safety.
Intuitive Design:
- How: Create tools and equipment with intuitive controls and interfaces that align with natural human movements and cognitive processes.
- Impact: Simplifies tool operation, reducing the learning curve and minimizing the risk of user errors.
Durability and Maintenance:
- How: Design tools and equipment for easy maintenance and durability, ensuring that they remain in optimal condition with minimal effort.
- Impact: Enhances tool longevity and reliability, reducing downtime and maintenance-related strain on workers.
Safety Features:
- How: Integrate safety mechanisms such as guards, automatic shut-offs, and emergency stops into tool and equipment designs.
- Impact: Protects workers from accidental injuries and ensures safe operation of tools and equipment.
Examples of Ergonomic Tool and Equipment Design:
Ergonomic Hand Tools:
- Example: Screwdrivers with soft, cushioned grips and balanced weights reduce hand fatigue and improve precision in assembly tasks.
Adjustable Assembly Tables:
- Example: Height-adjustable tables allow workers to switch between sitting and standing positions, promoting neutral postures and reducing back strain.
Robotic Exoskeletons:
- Example: Wearable exoskeletons assist workers in lifting heavy objects, reducing the physical effort required and minimizing the risk of back injuries.
Anti-Vibration Gloves:
- Example: Gloves designed to absorb and dampen vibrations from power tools protect workers from vibration-induced injuries and enhance grip comfort.
Automated Material Handling Systems:
- Example: Conveyor belts and robotic arms handle repetitive or heavy lifting tasks, reducing the physical demands on human workers and enhancing efficiency.
Benefits of Integrating Ergonomic Principles:
Enhanced Usability:
- Impact: Tools and equipment that are easy and comfortable to use improve task performance and reduce the likelihood of user errors.
Reduced Physical Strain:
- Impact: Ergonomically designed tools minimize muscle fatigue and strain, promoting worker health and longevity.
Increased Productivity:
- Impact: Comfortable and efficient tools enable workers to perform tasks more quickly and accurately, boosting overall productivity.
Improved Worker Satisfaction:
- Impact: Ergonomic tools contribute to a more satisfying work experience, enhancing job satisfaction and reducing turnover rates.
Lower Injury Rates:
- Impact: Reduced physical strain and enhanced safety features decrease the risk of workplace injuries, leading to a healthier workforce.
Case Example: A manufacturing company redesigned its assembly line tools by incorporating ergonomic grips and lightweight materials into hand tools. Additionally, they introduced adjustable workstations to allow workers to maintain neutral postures during assembly tasks. Following these changes, the company reported a 30% reduction in hand and wrist injuries, a 20% increase in assembly speed, and higher worker satisfaction scores.
Conclusion: Integrating ergonomic principles into the design of manufacturing tools and equipment is essential for enhancing usability, reducing physical strain, and improving overall worker well-being and productivity. By focusing on user-centered design, manufacturers can create tools and equipment that support healthy and efficient work practices, leading to safer, more productive, and more satisfying manufacturing environments.
Conclusion:
The above review questions and detailed answers provide a comprehensive exploration of Manufacturing Quality Control and Assurance. Covering essential topics such as Total Quality Management (TQM), ISO 9001 certification, Continuous Improvement (Kaizen), Quality Management Systems (QMS), Manufacturing Execution Systems (MES), Statistical Process Control (SPC), and the integration of ergonomic principles, these questions facilitate a deep understanding of how to ensure and enhance quality in manufacturing processes. Engaging with these questions equips students and professionals with the knowledge to implement best practices, overcome quality challenges, and achieve sustained excellence in competitive manufacturing environments.