Industrial Automation and Robotics
Industrial automation and robotics have revolutionized how modern factories operate, transforming traditional manufacturing into highly responsive, efficient, and intelligent systems. This field sits at the heart of Industrial and Manufacturing Technologies, blending mechanical precision with advanced computing to enhance productivity, consistency, and adaptability. From robotic arms in automotive assembly lines to fully automated warehouse logistics, automation reduces human error and labor costs while enabling new levels of scalability.
The integration of robotics with Computer-Integrated Manufacturing (CIM) enables seamless coordination of machines and systems across production floors. In parallel, innovations in Digital Twin Technology allow virtual replicas of production environments to be tested and optimized before real-world implementation. This synergy is core to realizing the full potential of Smart Manufacturing and Industry 4.0.
Advanced materials are also reshaping the scope of robotic design. The use of lightweight composites and responsive smart materials—explored further in Advanced Materials and Manufacturing Technologies—enhances robotic agility and energy efficiency. Complementing this, Energy and Resource Efficiency in Manufacturing aligns automation with sustainability goals, reducing operational costs and environmental impacts.
Automation is not limited to hardware; intelligent systems benefit from ergonomic design and human interaction analysis, as explored in Human Factors and Ergonomics in Manufacturing. Moreover, as factories adopt practices from Lean Manufacturing, automation helps eliminate waste and increase flexibility. These improvements extend to areas like Manufacturing Quality Control and Assurance, where sensor-driven systems enable real-time defect detection and process correction.
The importance of automation extends into the broader industrial ecosystem. Enhanced coordination is critical in Supply Chain Management, where robots streamline logistics and inventory tracking. Similarly, a commitment to Sustainable Manufacturing is reinforced through automated monitoring and precision resource allocation. Even niche areas like Additive Manufacturing (3D Printing) gain efficiency when integrated with robotic platforms that handle part removal, inspection, or post-processing.
Industrial automation intersects strongly with foundational engineering disciplines. In Mechanical Engineering, students explore actuators, gear systems, and kinematics essential to robot movement. Specialized applications, such as Automotive Engineering and Biomechanical Engineering, further demonstrate how robotics serve diverse fields—from driverless vehicles to rehabilitation devices.
Robotic control logic builds upon principles taught in Control Systems in Mech Engineering and is often realized in simulations via Mechanical Design and CAD software. These tools are critical for refining performance and ensuring coordination between hardware and software. Physical insights from Fluid Mechanics and Hydraulics, Thermodynamics and Heat Transfer, and Solid Mechanics inform design constraints, thermal regulation, and actuator performance.
Looking ahead, students exploring Robotics and Automation in Mech Eng and related fields will continue to push the boundaries of intelligent, human-aware, and sustainable automation. The blend of cyber-physical systems, real-time data, and adaptive machinery makes industrial automation one of the most transformative and interdisciplinary domains in engineering education today.
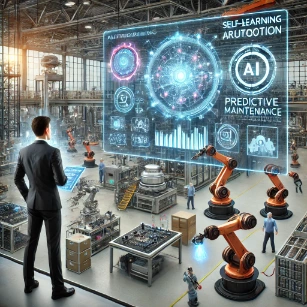
Table of Contents
Core Concepts of Industrial Automation and Robotics
Industrial Automation
- Definition:
- The use of control systems, machinery, and information technologies to automate tasks that were traditionally performed by human labor.
- Types of Automation:
- Fixed Automation:
- Designed for high-volume production with minimal flexibility.
- Example: Conveyor belts in automotive assembly lines.
- Programmable Automation:
- Machines can be reprogrammed to handle different tasks or products.
- Example: CNC machines.
- Flexible Automation:
- Systems capable of handling a variety of products with minimal reconfiguration time.
- Example: Robots in multi-product assembly.
- Fixed Automation:
Robotics in Industry
- Definition:
- The design, construction, and application of robots to perform repetitive or complex tasks in manufacturing and industrial settings.
- Key Components of Robots:
- Manipulators:
- Mechanical arms with joints for movement.
- End Effectors:
- Tools attached to robots for specific tasks, such as grippers, welders, or spray nozzles.
- Sensors:
- Provide feedback on the robot’s environment and operational status.
- Control Systems:
- Software and hardware that govern robot actions.
- Power Supply:
- Provides energy to actuate the robot’s components.
- Manipulators:
Integration of AI and Machine Learning
AI in Industrial Automation
- Role of AI:
- Enhances the decision-making capabilities of automation systems.
- Applications:
- Predictive maintenance using AI to forecast machine failures.
- Quality control through computer vision systems.
Machine Learning for Adaptive Systems
- Definition:
- Algorithms that enable systems to learn from data and improve their performance over time.
- Applications:
- Real-time optimization of production lines.
- Adaptive control systems that adjust parameters based on changing inputs.
Edge Computing and IoT
- Edge Computing:
- Enables local data processing for real-time automation decisions, reducing latency.
- Industrial Internet of Things (IIoT):
- Connects machinery, robots, and sensors for data collection and remote monitoring.
Applications of Industrial Automation and Robotics
Manufacturing and Production
- Assembly Lines:
- Automated systems handle welding, screwing, and assembling components with high precision.
- Material Handling:
- Automated guided vehicles (AGVs) and robotic arms manage logistics within factories.
- 3D Printing:
- Additive manufacturing processes automated for rapid prototyping and production.
Automotive Industry
- Robotic Welding:
- Robots perform precise welding tasks, ensuring consistent quality.
- Painting and Coating:
- Automated systems reduce material waste and improve finish consistency.
- Assembly and Testing:
- Robots assemble components like engines and perform safety tests.
Electronics Manufacturing
- Printed Circuit Boards (PCBs):
- Automated machines place components on PCBs with extreme accuracy.
- Inspection and Testing:
- AI-powered systems detect defects in microchips and devices.
Food and Beverage Industry
- Packaging and Sorting:
- Robotic systems automate the sorting and packaging of food products.
- Quality Control:
- Vision systems inspect food for defects or contamination.
- Palletizing:
- Robots stack and organize goods for transport.
Pharmaceutical and Healthcare
- Drug Manufacturing:
- Automated systems ensure consistency and compliance in drug production.
- Robotic Surgery:
- Precision robots assist in complex surgical procedures.
- Laboratory Automation:
- Robots handle sample preparation, testing, and data analysis.
Aerospace and Defense
- Component Assembly:
- Robots assemble intricate components like aircraft wings and engines.
- Maintenance and Inspection:
- Automated drones and robots inspect aircraft for damage.
- Composite Material Processing:
- Robots manufacture lightweight composite materials for aerospace applications.
Energy and Utilities
- Renewable Energy:
- Robotics in solar panel manufacturing and wind turbine assembly.
- Maintenance Automation:
- Robots inspect and repair power grids and pipelines.
Key Technologies in Industrial Automation and Robotics
Programmable Logic Controllers (PLCs)
- Role:
- Centralized control of machinery, ensuring coordination between systems.
- Applications:
- Control of conveyor belts, robotic arms, and production lines.
Sensors and Actuators
- Sensors:
- Measure physical parameters such as temperature, pressure, and position.
- Example: Optical sensors for defect detection.
- Actuators:
- Convert control signals into physical motion or actions.
- Example: Hydraulic actuators for lifting heavy loads.
Human-Machine Interfaces (HMIs)
- Definition:
- Interfaces that allow operators to interact with automated systems.
- Applications:
- Touchscreen panels in manufacturing plants.
Collaborative Robots (Cobots)
- Definition:
- Robots designed to work alongside humans safely.
- Applications:
- Assisting in tasks requiring manual dexterity and human oversight.
Digital Twin Technology
- Definition:
- Virtual replicas of physical systems used for simulation and optimization.
- Applications:
- Predicting machine performance and optimizing production workflows.
Benefits of Industrial Automation and Robotics
- Increased Productivity:
- 24/7 operations with minimal downtime.
- Improved Quality:
- Consistency in processes reduces errors and defects.
- Cost Reduction:
- Lower labor costs and reduced waste.
- Enhanced Safety:
- Robots handle hazardous tasks, reducing workplace accidents.
- Scalability:
- Systems can be easily adapted to changes in production volume or complexity.
Challenges in Industrial Automation and Robotics
- High Initial Costs:
- Significant investment required for equipment, integration, and training.
- Skill Gap:
- Need for specialized knowledge to operate and maintain advanced systems.
- Cybersecurity Risks:
- Connected systems are vulnerable to hacking and data breaches.
- Integration Complexity:
- Compatibility issues between legacy systems and new technologies.
- Ethical Concerns:
- Impact on employment and the workforce.
Emerging Trends in Industrial Automation and Robotics
- Artificial Intelligence (AI) Integration:
- Real-time decision-making and adaptive learning for smarter automation.
- 5G Connectivity:
- High-speed communication for seamless coordination in smart factories.
- Sustainability Initiatives:
- Energy-efficient robots and automation systems to reduce carbon footprints.
- Autonomous Systems:
- Robots and AGVs capable of independent operation without human intervention.
- Edge Computing:
- Localized processing for faster response times in critical applications.
Future Directions in Industrial Automation and Robotics
- Hyperautomation:
- Combining AI, robotics, and IoT to automate complex workflows end-to-end.
- Zero-Touch Manufacturing:
- Fully automated production lines with minimal human intervention.
- Global Industry 4.0 Adoption:
- Widespread implementation of smart factories and digital twins.
- Robotics-as-a-Service (RaaS):
- Subscription-based access to robotic systems for small and medium enterprises.
- Resilient Supply Chains:
- Automation to mitigate disruptions and enhance supply chain efficiency.
Why Study Industrial Automation and Robotics
Transforming Manufacturing Through Automation
Industrial automation and robotics involve using machines and control systems to perform tasks with minimal human intervention. Students learn how automation enhances consistency, speed, and precision in production processes. This transformation supports modern, efficient, and scalable manufacturing.
Design and Integration of Robotic Systems
Students study how to program and integrate robotic arms, conveyor systems, and vision systems. They explore how robots collaborate with machines and humans on factory floors. This knowledge enables flexible and adaptive production.
Control Systems and Programmable Logic Controllers (PLCs)
The course introduces students to sensors, actuators, and PLCs that manage automated systems. They learn to configure logic-based programs to control equipment. This skill is foundational to all industrial automation applications.
Human-Robot Collaboration and Safety
Collaborative robots (cobots) are designed to work safely alongside people. Students learn safety protocols, ergonomics, and interaction design. This prepares them to implement automation in a way that enhances human productivity.
Global Applications and Career Potential
Automation and robotics are transforming industries such as automotive, electronics, food processing, and logistics. Students develop in-demand skills for roles in design, maintenance, and systems integration. This field offers exciting and future-proof careers.