Robotics and Automation
Robotics and automation in mechanical engineering play a critical role in transforming how industries design, manufacture, and deliver products. These technologies enable the execution of complex tasks with high speed, precision, and repeatability. Their impact is most visible in areas like industrial and manufacturing technologies, where automation reduces human error and increases efficiency. Modern applications span across sectors including automotive engineering and biomechanical engineering, where autonomous systems enhance safety and performance.
Core innovations in this field are supported by emerging tools such as digital twin technology, which allows real-time monitoring and simulation of robotic systems, and smart manufacturing, which integrates automation with data analytics for adaptive production. Engineers must also master principles from control systems, solid mechanics, and thermodynamics to design reliable robotic components and systems.
The integration of automation within manufacturing and production engineering improves workflow efficiency and enables lean manufacturing by minimizing waste. Robotics further enhances quality control through precise and consistent operations. Innovations in 3D printing and CAD-based mechanical design have enabled the rapid prototyping of robotic parts with custom geometries and embedded sensors.
Students entering this field will benefit from a solid foundation in mechanical engineering fundamentals and familiarity with disciplines such as fluid mechanics and vibrations and acoustics. Emerging materials, including those studied under nanotechnology, contribute to lighter and more durable robotic systems. Meanwhile, attention to ergonomics ensures that collaborative robots (cobots) are safe for human interaction.
Robotics also influences macro-level operations. Understanding supply chain management and energy efficiency is crucial for scaling automation sustainably. Advances in sustainable manufacturing promote greener robotic solutions. By combining knowledge from areas such as materials science and vehicle systems, students and professionals alike can build intelligent, responsive, and efficient machines to meet the evolving demands of modern industry.
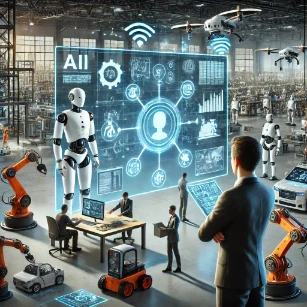
Table of Contents
Core Concepts of Robotics and Automation
Robotics
Robotics is an interdisciplinary field that integrates mechanical engineering, electrical engineering, computer science, and control systems to create intelligent machines capable of performing a range of tasks autonomously or semi-autonomously. Robots are increasingly central to both industrial processes and emerging service applications, driven by advances in materials, computation, and artificial intelligence.
- Mechanical Systems:
- At the core of every robot lies its mechanical architecture. Mechanical systems define how a robot moves, interacts with the environment, and maintains structural integrity.
- Examples:
- Multi-jointed robotic arms mimic human limb flexibility, allowing complex manipulation tasks such as welding, assembly, or surgical operations.
- Mobile bases—ranging from wheeled and tracked platforms to legged locomotion—provide navigation capabilities across diverse terrains, including factory floors and rough outdoor landscapes.
- Specialized end-effectors like vacuum grippers, magnetic clamps, or anthropomorphic hands expand a robot’s functional range.
- Sensors and Perception:
- Modern robots rely on sensors to perceive their surroundings, enabling them to interpret context, avoid hazards, and adapt dynamically. Sensor fusion techniques combine data from multiple sources to build accurate environmental models.
- Common Sensors:
- LiDAR: Generates 3D maps using laser pulses for precise localization and navigation, particularly in autonomous vehicles and drones.
- Cameras: Enable object detection, facial recognition, and scene understanding, crucial in service and social robots.
- Proximity Sensors: Detect nearby obstacles to prevent collisions in automated guided vehicles (AGVs) and collaborative robots (cobots).
- Force Sensors: Measure interaction forces, supporting delicate operations like gripping fragile objects or performing tactile inspections.
- Actuators:
- Actuators convert electrical, hydraulic, or pneumatic energy into motion. Their choice determines a robot’s speed, strength, and precision.
- Types:
- Electric Motors: Found in most industrial robots for their responsiveness and control over angular displacement and torque.
- Hydraulic Actuators: Provide high power density, often used in heavy-duty applications like robotic arms for construction or aerospace.
- Pneumatic Actuators: Offer rapid movement with simple control schemes, ideal for tasks like packaging or sorting.
- Control Systems:
- Robotic control systems govern motion trajectories, sensor feedback processing, and task execution, forming the “brain” of the machine.
- Types:
- Open-Loop Control: Suitable for predictable environments, where robots follow preprogrammed paths without real-time feedback.
- Closed-Loop Control: Integrates continuous feedback from sensors, enabling adaptive behavior and corrections based on environmental changes or user interaction.
Automation
Automation extends beyond robotics to encompass systems and software that reduce or eliminate human intervention across industrial and commercial processes. The evolution of automation has revolutionized sectors such as manufacturing, logistics, energy, and even finance by enhancing efficiency, consistency, and scalability. Automation technologies are often categorized by their flexibility and adaptability to changing tasks and environments.
- Types of Automation:
- Fixed Automation: Characterized by high-volume production with predefined sequences. Examples include automobile assembly lines, bottling plants, and semiconductor fabrication.
- Programmable Automation: Suitable for batch production. CNC (Computer Numerical Control) machines exemplify this type, allowing engineers to change programming for different products.
- Flexible Automation: Combines programmable systems with sensor feedback and robotic adaptability, enabling facilities to switch tasks rapidly with minimal downtime. Widely used in smart factories and Industry 4.0 environments.
- Key Components of Automation Systems:
- Programmable Logic Controllers (PLCs): Rugged digital computers used to control machinery. PLCs receive inputs from sensors, process logic instructions, and actuate outputs accordingly.
- Supervisory Control and Data Acquisition (SCADA): These systems oversee large-scale processes like power grids or water treatment plants by offering centralized monitoring, data logging, and control.
- Sensors and Actuators: Serve as the interface between the digital world and physical reality. Sensors collect real-time data, while actuators perform actions such as rotating motors or opening valves.
Together, robotics and automation are reshaping the future of work and production. Their convergence enables cyber-physical systems capable of responding to complex environments with minimal human oversight. From robotic arms on the assembly line to smart automation systems managing warehouses, their applications are nearly limitless. According to industry insights from Robotics.org, innovation in these fields is accelerating rapidly, making it critical for professionals to develop expertise in both domains to remain competitive.
Applications of Robotics and Automation
Industrial Automation
Robotics and automation have become foundational to modern manufacturing, offering transformative impacts in efficiency, precision, consistency, and scalability. From assembly lines to smart factories, the integration of robots and automated systems enables companies to meet growing demands while reducing labor costs and improving product quality. Industrial automation encompasses a range of robotic technologies that handle everything from basic material handling to advanced fabrication.
- Assembly Lines:
- Robotic systems in assembly lines have revolutionized manufacturing by enabling high-speed, high-precision execution of tasks such as welding, painting, and fastening. These systems minimize human error and fatigue, ensuring consistent product quality.
- Example: In the automotive industry, robotic arms equipped with sensors and vision systems assemble car bodies with millimeter accuracy, often working in coordinated cells for increased throughput.
- Material Handling:
- Automated guided vehicles (AGVs) and conveyor systems transport raw materials, components, and finished products across the factory floor, reducing the need for manual lifting and transportation.
- Advanced material handling robots can navigate dynamic environments using SLAM (Simultaneous Localization and Mapping) algorithms.
- Quality Control:
- Machine vision systems integrated with AI detect surface defects, dimensional inaccuracies, and color inconsistencies. These systems provide real-time feedback, allowing immediate correction in the manufacturing process and reducing waste.
- Packaging and Palletizing:
- Robots equipped with suction cups, grippers, or specialized manipulators can package items, arrange them in boxes, and stack them onto pallets. Automation in this area enhances speed, ensures consistency, and improves workplace safety by reducing repetitive strain injuries.
- Additive Manufacturing:
- Robots are increasingly being integrated into 3D printing operations, enabling the fabrication of complex parts in aerospace, automotive, and biomedical sectors. Robotic arms can control the extrusion path, monitor quality, and even perform post-processing tasks like finishing and inspection.
Healthcare and Medical Robotics
Robotics and automation are reshaping the healthcare industry by enhancing diagnostic accuracy, improving surgical outcomes, and enabling personalized patient care. These technologies offer a combination of precision, reliability, and adaptability, supporting both practitioners and patients in hospitals, rehabilitation centers, and laboratories.
- Surgical Robots:
- Systems like the da Vinci Surgical Robot enable minimally invasive procedures with enhanced precision, flexibility, and control. These systems translate a surgeon’s hand movements into micro-movements of tiny instruments inside the patient’s body, minimizing trauma and reducing recovery time.
- Features:
- 3D high-definition imaging for detailed internal visualization.
- Wristed instruments with seven degrees of freedom for enhanced dexterity.
- Rehabilitation Robots:
- Used to assist patients during physical therapy, rehabilitation robots provide repetitive and adjustable motion therapy, helping stroke victims or those with spinal cord injuries regain function. These systems also collect data to personalize and monitor treatment plans.
- Diagnostic Systems:
- AI-enhanced imaging robots and automated analyzers assist in diagnostics by rapidly processing samples and providing consistent, high-accuracy results. These technologies are used in blood analysis, radiology, and pathology labs.
- Pharmaceutical Automation:
- From formulation and compounding to packaging and distribution, robots manage sensitive tasks in sterile environments, improving safety and reducing contamination risks. Automated pill counters and robotic arms also optimize logistics in pharmacies.
- Exoskeletons:
- Wearable robotic systems help individuals with limited mobility by enhancing strength and stability. These exosuits are used in clinical rehabilitation, military applications, and by workers performing strenuous tasks.
Space Exploration
In the hostile and unpredictable environments of space, robots are essential for exploration, research, and construction. These intelligent machines enable humanity to extend its reach across the solar system and beyond, performing tasks that would be risky or impossible for astronauts.
- Planetary Rovers:
- NASA’s Perseverance and Curiosity rovers have traversed the Martian surface, collecting geological data, capturing high-resolution images, and searching for signs of microbial life. Their systems include autonomous navigation, environmental sampling, and communication relays.
- Capabilities:
- Obstacle detection and avoidance using LiDAR, stereo cameras, and ultrasonic sensors.
- Drilling and scooping tools for soil and rock collection.
- Robotic Arms:
- Deployed on platforms like the ISS, robotic arms such as Canadarm2 perform satellite deployments, docking maneuvers, and maintenance tasks. They are also used to support spacewalks and manipulate scientific instruments.
- Autonomous Spacecraft:
- AI-guided spacecraft handle docking, course correction, and repair activities with minimal ground control input, reducing response time and increasing mission efficiency.
- Space Habitats:
- Future missions aim to use autonomous robots to build lunar and Martian habitats using local materials. These robots will need to work collaboratively and adaptively in extreme conditions.
Agriculture and Food Processing
Automation is transforming agriculture into a high-tech industry capable of addressing food security and environmental sustainability. Robots in farming and food processing reduce labor dependency, increase productivity, and ensure product quality from field to fork.
- Precision Agriculture:
- Drones equipped with multispectral cameras monitor crop health, identify nutrient deficiencies, and detect pests. Ground-based robots autonomously navigate fields to deliver fertilizers and pesticides precisely where needed, minimizing waste and runoff.
- Automated Harvesting:
- Robots with sophisticated vision systems and gripping mechanisms selectively pick fruits and vegetables based on ripeness, size, and location, reducing damage to produce and increasing yield.
- Food Packaging:
- High-speed automation systems handle everything from sorting and portioning to sealing and labeling, ensuring hygiene, reducing human error, and meeting stringent food safety regulations.
Transportation and Logistics
Automation in transportation and logistics has led to faster, more reliable delivery networks and reshaped the future of mobility. The use of robots, self-driving vehicles, and intelligent routing systems enables businesses to meet demand with agility and accuracy.
- Autonomous Vehicles:
- Driverless cars and trucks leverage GPS, LiDAR, radar, and cameras to navigate roads safely, even in complex urban settings. Their applications include passenger ride-sharing, last-mile delivery, and long-haul freight transportation.
- These technologies are supported by advances in autonomous vehicle AI platforms that enable real-time decision-making.
- Warehouse Automation:
- Automated guided robots, such as Amazon’s Kiva systems, transport shelving units across warehouses, significantly reducing the time and labor required for inventory picking and restocking. These systems improve order accuracy and throughput in e-commerce operations.
- Drones:
- Unmanned aerial vehicles are used for inventory monitoring, infrastructure inspection, and rapid delivery of medical supplies or retail goods. Their ability to reach remote or hazardous locations makes them ideal for disaster response as well.
Key Technologies Driving Robotics and Automation
Artificial Intelligence (AI) and Machine Learning
Artificial Intelligence (AI) and Machine Learning (ML) form the cognitive core of modern robotics and automation systems. These technologies enable machines to perform complex tasks that traditionally required human intelligence. AI encompasses a range of capabilities, including perception, reasoning, decision-making, and language understanding, while ML involves training algorithms to recognize patterns and improve performance over time. The integration of AI allows robots to adapt to dynamic environments, respond to new inputs, and continuously refine their behavior through experience.
- AI algorithms empower robots with the ability to process massive datasets and identify optimal courses of action without explicit programming.
- Applications:
- Real-time navigation in autonomous vehicles, using deep learning to detect road conditions, obstacles, and traffic signals.
- Predictive maintenance in industrial settings, where AI models analyze sensor data to forecast equipment failure and reduce downtime.
- Voice and image recognition for human-robot interaction in service industries and healthcare environments.
- Adaptive learning in robotic arms for customized manufacturing or medical procedures.
Internet of Things (IoT)
The Internet of Things (IoT) connects physical devices, machines, and sensors into a unified digital network, enabling seamless data communication and centralized control. In the context of robotics and automation, IoT provides the infrastructure for smart environments where machines can collaborate, monitor each other, and respond to real-time data inputs. IoT enhances transparency, traceability, and operational efficiency across sectors such as manufacturing, logistics, agriculture, and energy.
- IoT-enabled systems allow devices to transmit status updates, environmental metrics, and performance data to control systems and cloud servers.
- Applications:
- Smart factories with interconnected robots and sensors that autonomously coordinate assembly lines and optimize production schedules.
- Automated supply chain management systems that monitor inventory levels, track shipments in real time, and dynamically adjust logistics routes.
- Remote diagnostics and firmware updates for robotic equipment, ensuring minimal human intervention and faster response times.
- Connected wearable devices that transmit biometric data to healthcare robots for tailored patient care.
Vision Systems
Vision systems give robots the ability to see, recognize, and understand visual environments. These systems incorporate high-resolution cameras, LiDAR, infrared sensors, and machine vision algorithms that enable perception-driven decision-making. Advanced vision technologies are vital for enabling robots to interact with unstructured environments, manipulate delicate objects, and inspect components with micron-level precision.
- Applications of robotic vision include:
- Object detection and sorting in warehouses using AI-powered classification systems.
- Real-time quality inspection on production lines, identifying surface defects, dimensional deviations, or contamination.
- Guided surgery robots that use endoscopic cameras and depth sensors for accurate positioning.
- Autonomous drones that rely on stereo vision and optical flow to maintain flight stability and avoid collisions.
Edge Computing
Edge computing refers to processing data closer to the source—such as a robot or sensor—rather than relying solely on distant cloud servers. By reducing the latency associated with data transmission, edge computing enables real-time decision-making, faster response times, and improved reliability in critical applications. This is especially important in scenarios where milliseconds matter, such as robotic surgery, autonomous vehicles, and industrial automation.
- Robots equipped with edge processors can independently execute control algorithms, perform diagnostics, and maintain operational continuity even during connectivity loss.
- Example applications include:
- Mobile robots navigating dynamic warehouses while processing sensor data locally to avoid collisions.
- Smart cameras performing on-the-spot image analysis to trigger alerts in security and quality control.
Cloud Robotics
Cloud robotics leverages cloud computing to extend the capabilities of robots by providing access to vast computational resources, shared databases, and collective learning. Robots connected to the cloud can download software updates, share experiences, and collaboratively solve problems, even if they have limited onboard processing power. This model is highly scalable and cost-effective, allowing developers to deploy complex functionalities without the need for high-end hardware.
- Benefits of cloud robotics include:
- Access to powerful AI algorithms hosted on cloud platforms for image recognition, natural language processing, or environmental modeling.
- Global fleets of robots improving performance collectively by uploading sensor data and downloading optimized behaviors.
- Remote diagnostics and monitoring through cloud dashboards, enabling predictive maintenance and real-time oversight.
- Examples include collaborative robots (cobots) in logistics that coordinate tasks via cloud orchestration platforms such as Google Cloud Robotics Core.
Additive Manufacturing
Additive manufacturing, or 3D printing, is becoming increasingly intertwined with robotics to enable the production of complex and customized components directly from digital designs. When combined with robotic arms, additive manufacturing systems can build parts layer by layer with exceptional precision, using materials ranging from polymers and ceramics to advanced metals. This synergy facilitates rapid prototyping, on-demand manufacturing, and design flexibility not achievable with traditional methods.
- Robotic integration in additive manufacturing allows:
- Automated multi-axis printing, enabling the fabrication of curved and multi-material structures.
- Post-processing and inspection performed by the same robotic unit to reduce production cycles.
- In-situ quality monitoring using integrated vision systems for real-time correction.
- Applications in aerospace, medical implants, and automotive tooling where lightweight and optimized geometries are critical.
Emerging Trends in Robotics and Automation
Collaborative Robots (Cobots)
Collaborative robots, or “cobots,” represent a major shift in how humans and machines interact in industrial, commercial, and healthcare settings. Unlike traditional industrial robots that operate in isolated cages for safety, cobots are specifically engineered to work side-by-side with humans. They are equipped with advanced sensors, force limiters, and artificial intelligence algorithms that enable safe and intuitive interaction. This fosters a hybrid workforce where robots support human capabilities, enhancing productivity, reducing fatigue, and minimizing errors.
- Key features of cobots include real-time responsiveness, ease of programming through teach-by-demonstration interfaces, and the ability to switch between tasks with minimal reconfiguration.
- Applications:
- Assisting workers in precision assembly tasks on manufacturing lines, where cobots handle repetitive or ergonomically challenging actions.
- Medical applications like aiding surgeons in complex procedures by holding instruments or assisting with endoscopic imaging.
- Laboratory automation for sample preparation and diagnostics in pharmaceutical research.
- Customer-facing roles in retail and hospitality where cobots greet visitors or assist in basic queries.
Autonomous Systems
Autonomous systems are robotic platforms that function independently without human oversight, relying on advanced perception, reasoning, and decision-making algorithms. These systems are designed to sense, interpret, and act upon complex real-world environments. The autonomy spectrum ranges from basic obstacle avoidance to fully self-sufficient machines capable of executing entire missions or workflows without external input.
- Examples of autonomous systems include:
- Delivery drones that navigate urban airspaces to transport packages using GPS and vision-based navigation.
- Autonomous underwater vehicles (AUVs) used for oceanographic mapping, pipeline inspections, and environmental monitoring.
- Self-driving cars that combine LiDAR, radar, and AI to make split-second decisions in real-time traffic scenarios.
- Security robots patrolling perimeters and detecting unauthorized activities using AI-enabled threat recognition.
Swarm Robotics
Swarm robotics draws inspiration from social insects like ants and bees, utilizing many simple robots working together to achieve complex tasks. Rather than relying on a central controller, swarm robots communicate locally and follow distributed algorithms to coordinate behavior. This decentralization makes them robust, scalable, and fault-tolerant. Swarm robotics is emerging as a powerful tool for applications requiring adaptability and resilience in unpredictable or hazardous environments.
- Applications of swarm robotics include:
- Disaster recovery missions where robots search rubble for survivors or assess structural safety.
- Search and rescue operations in remote or dangerous regions where deploying humans would be risky.
- Environmental monitoring across vast areas to collect data on air quality, soil health, or wildlife migration.
- Cooperative transport, where multiple small robots jointly move large or heavy objects.
Soft Robotics
Soft robotics refers to the design and construction of robots using compliant and flexible materials rather than rigid joints and links. Inspired by biological organisms like octopuses and caterpillars, soft robots can deform, squeeze through tight spaces, and safely interact with fragile or irregularly shaped objects. This innovation opens up new possibilities in fields requiring dexterous manipulation, gentle touch, or adaptive morphology.
- Soft robotic technologies often use materials such as silicone, hydrogels, and electroactive polymers that bend or expand in response to electrical or thermal stimuli.
- Applications:
- Robotic grippers used in food processing plants to handle delicate fruits and baked goods without bruising or damage.
- Medical devices like catheter-assisting robots that can navigate inside the human body with minimal invasiveness.
- Wearable exosuits that provide flexible assistance to elderly or disabled individuals.
Bio-Inspired Robotics
Bio-inspired robotics aims to replicate the adaptability, efficiency, and robustness of living organisms in mechanical systems. By studying nature’s engineering solutions—like gecko feet, bird wings, or fish fins—researchers create robots that exhibit natural locomotion, sensory integration, and decision-making abilities. These robots are often better suited for navigating complex terrains or performing agile tasks than their traditional counterparts.
- Examples of bio-inspired designs include:
- Robotic insects with flapping wings for urban surveillance or environmental monitoring.
- Quadrupedal robots mimicking mammals for stable mobility on rocky or inclined surfaces.
- Snake-like robots used in search and rescue or pipeline inspection due to their ability to slither through tight spaces.
- Underwater robots modeled after fish that move quietly and efficiently through marine ecosystems.
Sustainable Automation
Sustainability is becoming a core consideration in the design and deployment of robotics and automation systems. Sustainable automation focuses on developing robots that consume less energy, use eco-friendly materials, and contribute to green practices in manufacturing and logistics. This trend is increasingly vital as industries align with global sustainability goals and environmental regulations. According to insights from the World Economic Forum, robotics is a key enabler for reducing carbon footprints and achieving circular economy models.
- Key elements of sustainable automation include:
- Designing energy-efficient motors and control algorithms that minimize power consumption.
- Utilizing biodegradable, recyclable, or lightweight materials to reduce waste and emissions.
- Robots for renewable energy applications, such as solar panel maintenance and wind turbine inspections.
- Reducing overproduction and waste in manufacturing through just-in-time robotic systems.
Challenges in Robotics and Automation
- Complexity of Integration:
- Integrating robotics and automation into existing infrastructures presents one of the most substantial challenges for industries. Legacy systems, designed decades ago without consideration for modern automation technologies, often lack compatibility with robotic components, sensors, and control systems. This mismatch necessitates extensive retrofitting, reprogramming, and sometimes complete overhauls of operational procedures. The complexity increases in multi-vendor environments where various software platforms and proprietary protocols must communicate seamlessly. Furthermore, physical constraints in older facilities—such as limited floor space, power supply limitations, or outdated safety standards—can hinder robotic deployment, requiring costly architectural modifications. Engineering teams must also resolve issues of synchronization between automated systems and human workflows, particularly in hybrid environments like warehouses or hospitals.
- Workforce Adaptation:
- The successful implementation of robotics hinges not only on the technology itself but also on the human capital managing it. A significant barrier to widespread adoption is the need for upskilling or reskilling existing workers to operate, troubleshoot, and program robotic systems. Many employees may lack foundational knowledge in robotics, AI, or digital interfaces, leading to hesitation or resistance. Effective adaptation requires comprehensive training programs that span both technical and soft skills—ranging from safety protocols and machine operation to critical thinking and digital literacy. Employers also face challenges in attracting new talent with advanced skills in robotics engineering, mechatronics, and automation integration. Bridging this talent gap is critical to avoiding inefficiencies and underutilization of expensive systems. Educational institutions are increasingly aligning with industry needs by offering targeted training programs and certifications.
- Ethical Concerns:
- Automation inevitably raises questions about the displacement of human labor. While robots enhance efficiency and reduce human exposure to hazardous tasks, they can also render certain job roles obsolete. This disruption disproportionately affects low-skilled workers and may exacerbate social inequalities if not mitigated by policy and economic intervention. Ethical concerns extend beyond employment to include algorithmic bias in AI decision-making, accountability for robot-induced accidents, and the moral implications of autonomous military systems. There is growing debate around the ethical limits of automating healthcare, education, and caregiving—sectors where human empathy plays a vital role. Governments, companies, and researchers must work together to establish responsible AI guidelines and ensure that robotic technologies benefit society inclusively.
- Cybersecurity Risks:
- As automation systems become increasingly networked and cloud-based, they become more susceptible to cybersecurity threats. Industrial robots, autonomous vehicles, and medical devices connected via the Internet of Things (IoT) are vulnerable to hacking, data breaches, and system manipulation. A compromised robot can malfunction or leak sensitive information, causing physical harm or financial losses. For example, tampering with a surgical robot’s software could result in life-threatening consequences. To address these threats, developers must embed strong encryption, secure communication protocols, intrusion detection systems, and regular firmware updates. Organizations also need to invest in cybersecurity training and simulate attack scenarios to improve their response readiness. According to a report from McKinsey & Company, the proliferation of smart devices and industrial automation is creating new vulnerabilities that traditional IT security approaches are ill-equipped to handle.
- System Reliability:
- Robots must operate in diverse and unpredictable environments, ranging from spotless semiconductor fabs to rugged mining fields. Ensuring consistent and safe performance under such variability is a technical and operational challenge. Unanticipated obstacles, sensor malfunctions, or software glitches can lead to costly downtime or even catastrophic failures. Redundancy, fault tolerance, and rigorous testing protocols are essential in mission-critical applications like aviation or healthcare robotics. Environmental factors such as extreme temperatures, electromagnetic interference, dust, and vibration can impair robot functionality. Continuous performance monitoring and predictive maintenance strategies are crucial to extending system lifespan and reducing unplanned outages. Furthermore, as robotic systems become more complex and autonomous, it becomes increasingly difficult to trace root causes of errors or system failures, necessitating advancements in explainable AI and diagnostics.
Future Directions for Robotics and Automation
- Human-Robot Collaboration:
- As industries and service sectors become more reliant on robotic systems, future advancements will focus heavily on seamless human-robot collaboration. Unlike traditional industrial robots confined behind safety cages, next-generation collaborative robots (cobots) are designed to work safely alongside humans in shared workspaces. These robots will be equipped with advanced perception technologies—such as depth cameras, touch sensors, and force feedback systems—to detect human presence and adapt behavior dynamically to ensure safety and comfort. Real-time gesture recognition and voice command systems will further enhance interaction, enabling intuitive control and smoother task delegation. In fields like healthcare and elder care, robots will provide physical assistance while maintaining human empathy through emotionally intelligent interfaces. Researchers are also exploring wearable exoskeletons that amplify human strength and endurance, offering enhanced mobility in physically demanding jobs.
- AI-Powered Robotics:
- Artificial Intelligence will serve as the cornerstone of future robotic development, empowering machines with the capacity to learn, reason, and improve autonomously. Traditional robotics relies on pre-programmed actions, but AI-driven robots will learn from past experiences, recognize patterns, and make data-informed decisions in unstructured environments. Reinforcement learning, deep neural networks, and natural language processing will allow robots to master complex tasks—ranging from adaptive warehouse operations to customer service in retail environments. These systems will also integrate with digital twins—virtual replicas of physical assets—to simulate and optimize robot behavior before deployment. As AI continues to evolve, ethical design and explainability will become priorities to ensure that intelligent robots behave transparently and align with human values.
- Space Exploration Robots:
- The next frontier for robotics lies in extraterrestrial exploration. Robots will play an indispensable role in the colonization of Mars, construction of lunar habitats, and asteroid mining. These tasks involve extreme environments, unpredictable terrains, and significant communication delays with Earth—making robotic autonomy and resilience critical. Advanced planetary rovers will be capable of self-navigation, terrain mapping, and geological sampling with minimal human input. Robotic arms and 3D printers will assist in constructing shelters using in-situ materials like lunar regolith. Swarm robots may be deployed to collaborate on large-scale operations, such as solar panel deployment or tunnel excavation. The long-term vision includes the development of humanoid robots capable of maintaining spacecraft and assisting astronauts in real-time. According to NASA’s Robotic Future Initiative, robotic systems will serve as pathfinders for human missions, performing reconnaissance and laying foundational infrastructure in deep space environments.
- Healthcare Innovations:
- Robotics will revolutionize healthcare delivery by combining precision engineering with AI-driven diagnostics and treatment personalization. Future surgical robots will offer real-time decision support, augmented reality guidance, and haptic feedback to enhance surgical accuracy and reduce recovery times. Diagnostic robots will analyze imaging data and patient histories using AI models, flagging anomalies and recommending treatments with minimal clinician intervention. In elderly care, companion robots will monitor vital signs, administer medication, and engage patients through conversation and activities, promoting both physical and mental well-being. Personalized rehabilitation robots will use adaptive learning algorithms to tailor exercises to individual recovery rates. The integration of bio-compatible materials and soft robotics will further allow robots to safely interact with the human body in ways that were previously unachievable.
- Global Supply Chain Automation:
- In the future, global supply chains will be reimagined as fully automated ecosystems where goods are manufactured, stored, transported, and delivered with minimal human oversight. Intelligent robotics will be integrated from production floors to last-mile delivery networks. Automated guided vehicles (AGVs), drones, and autonomous trucks will operate in synchrony with AI-powered logistics platforms, optimizing routes and reducing transit times. Warehouse automation will feature dynamic shelving systems, robotic pickers with computer vision, and real-time inventory analytics. These innovations will drastically reduce human error, labor costs, and downtime while increasing speed and traceability. Supply chain resilience will also improve, as automation enables rapid adaptation to disruptions such as pandemics or geopolitical conflicts. Predictive analytics and digital twins will be used to model entire supply networks, allowing real-time forecasting and scenario testing to ensure agility in decision-making.
Why Study Robotics and Automation in Mech Eng
Industry 4.0 and Smart Manufacturing
Robotics and automation are at the heart of Industry 4.0, enabling smart manufacturing environments. These technologies facilitate the integration of sensors, actuators, and control systems, leading to increased productivity and efficiency. Understanding how these systems work allows engineers to innovate and optimize production processes.
Enhanced Precision and Efficiency
Automated robotic systems consistently perform repetitive tasks with high precision and minimal error. This enhances quality control, reduces waste, and ensures uniformity in manufacturing outputs. Mechanical engineering students who understand automation can design and implement systems that streamline industrial workflows.
Multidisciplinary Skill Development
Studying robotics involves integrating knowledge from mechanical design, electronics, programming, and systems engineering. This multidisciplinary approach equips students with diverse technical skills that are highly valued in the modern workforce. Such a foundation is essential for tackling complex engineering problems in real-world settings.
Human-Robot Collaboration
Modern automation emphasizes collaboration between humans and robots, known as cobots. Understanding safety, ergonomics, and adaptive control systems is vital for designing robots that work alongside people. This prepares students to create technologies that enhance human capabilities rather than replace them.
Global Technological Trends
With the global push towards automation in all sectors, from automotive to healthcare, knowledge of robotics is increasingly in demand. Mechanical engineers who specialize in automation are positioned to contribute to innovative solutions and technological leadership. This knowledge aligns with future career opportunities and emerging global needs.
Robotics and Automation: Conclusion
Robotics and automation have emerged as the defining forces behind the Fourth Industrial Revolution, reshaping how industries function, how services are delivered, and how societies adapt to technological change. These technologies are no longer confined to factory floors or science fiction—they have become embedded in everyday life, from intelligent home appliances to robotic surgical tools and AI-enabled logistics networks. Their transformative power lies in the ability to amplify human capabilities, eliminate routine and hazardous tasks, and drive productivity across sectors. By automating processes, organizations are not only reducing costs and increasing precision but also enabling round-the-clock operations that can adapt to fluctuating market demands.
In the manufacturing sector, robotics has elevated production speed and accuracy, supporting just-in-time workflows and mass customization. Automation has also become critical in supply chain resilience, where robotic systems handle complex inventory tasks, predictive logistics, and rapid delivery. Healthcare has witnessed groundbreaking developments through robotic surgery, AI-powered diagnostics, and assistive robots that support aging populations. In agriculture, drones and autonomous tractors enhance yield prediction, precision planting, and sustainable farming practices. Meanwhile, sectors like retail, hospitality, and finance are using robotic process automation (RPA) to streamline customer service, inventory tracking, and administrative functions.
One of the most remarkable expansions lies in mobility and exploration. Autonomous vehicles, both terrestrial and aerial, are poised to redefine personal transportation, last-mile delivery, and emergency response. In space exploration, robots continue to break barriers, operating in remote, dangerous, or extraterrestrial environments with little or no human support. Machines like NASA’s Perseverance rover demonstrate how robotics can operate intelligently in unpredictable terrains while collecting valuable scientific data. On Earth, disaster response robots aid rescue missions in environments too dangerous for human entry.
As enabling technologies such as artificial intelligence, machine learning, cloud computing, edge analytics, and the Internet of Things (IoT) advance, robotics and automation are evolving toward greater autonomy, context awareness, and real-time adaptability. Robots can now learn from their environments, interact safely with humans, and dynamically update their decision-making processes. This convergence of disciplines is giving rise to smart environments where robots communicate seamlessly with each other and with infrastructure, forming the backbone of smart factories, smart cities, and intelligent healthcare systems. According to insights from McKinsey’s future of robotics in manufacturing, the integration of collaborative robots and AI will significantly enhance human-machine synergy and redefine job roles across the global economy.
Nonetheless, this rapid evolution brings challenges that must be addressed, including cybersecurity vulnerabilities, workforce displacement, ethical considerations in AI-driven decisions, and the need for robust regulatory frameworks. Responsible innovation is essential—ensuring that the benefits of robotics are equitably distributed while fostering transparency, accountability, and long-term sustainability.
Looking forward, robotics and automation will be central to solving some of the world’s most pressing challenges. From mitigating labor shortages and reducing environmental impact to improving healthcare access and enabling extraterrestrial colonization, the potential applications are limitless. Educational systems must therefore evolve in parallel, equipping future professionals with interdisciplinary skills in robotics, AI, ethics, and systems thinking. The shift will not just be technological but cultural—reshaping how societies define productivity, interaction, and even intelligence.
In conclusion, robotics and automation are no longer emerging technologies—they are integral to our present and indispensable to our future. As innovations continue to emerge at the intersection of engineering, computer science, and biology, we are entering an era where machines don’t merely assist us—they collaborate, learn, adapt, and even anticipate our needs. The journey ahead is as promising as it is challenging, but with thoughtful development and inclusive policymaking, robotics and automation will continue to unlock new horizons for humanity.
Robotics and Automation: Review Questions
1. What are the key components of a robotic system in mechanical engineering, and how do they interact to perform automated tasks?
Answer:
A robotic system in mechanical engineering typically comprises the following key components:
Mechanical Structure: This includes the physical framework or chassis of the robot, consisting of joints, links, and actuators that provide mobility and flexibility. The design of the mechanical structure determines the robot’s range of motion and the types of tasks it can perform.
Actuators: Actuators, such as motors (electric, hydraulic, pneumatic), provide the necessary force and movement to the robot’s joints. They convert energy into mechanical motion, enabling the robot to perform actions like lifting, rotating, or moving objects.
Sensors: Sensors collect data from the robot’s environment and internal state. Common sensors include cameras, proximity sensors, force sensors, and gyroscopes. This information allows the robot to perceive its surroundings, detect obstacles, and respond to changes dynamically.
Control System: The control system, often consisting of a central processing unit (CPU) or microcontroller, interprets sensor data and sends commands to actuators. It executes algorithms and control logic to coordinate the robot’s movements and actions accurately.
End Effector: The end effector is the tool or device attached to the robot’s arm, such as a gripper, welding torch, or paint sprayer. It interacts directly with objects or materials, enabling the robot to perform specific tasks like assembling, welding, or painting.
Power Supply: The power supply provides the necessary energy for the robot’s components. It can be electrical (batteries or direct power), hydraulic, or pneumatic, depending on the robot’s design and application.
Interaction to Perform Automated Tasks:
- Perception: Sensors gather data about the environment and the task requirements.
- Processing: The control system processes sensor inputs, executing programmed instructions or real-time algorithms to make decisions.
- Actuation: Based on the processed data, the control system sends commands to actuators to move the mechanical structure.
- Execution: Actuators drive the mechanical structure and end effector to perform the desired action, such as picking up an object or assembling a component.
- Feedback: Sensors continuously monitor the outcome, providing feedback to the control system for adjustments and ensuring precision.
This seamless interaction between components allows robotic systems to perform complex, repetitive, and precise tasks autonomously, enhancing efficiency and accuracy in mechanical engineering applications.
2. How has automation revolutionized manufacturing processes in mechanical engineering, and what are the primary benefits it offers?
Answer:
Automation has profoundly revolutionized manufacturing processes in mechanical engineering by introducing advanced technologies that streamline production, enhance precision, and increase overall efficiency. Key ways automation has transformed manufacturing include:
Increased Productivity: Automated systems can operate continuously without breaks, significantly boosting production rates compared to manual labor. Robots can perform repetitive tasks faster and more consistently, leading to higher output.
Enhanced Precision and Quality: Automation minimizes human error, ensuring that components are manufactured with exact specifications and consistent quality. Precision machinery and robots can achieve tolerances that are difficult to attain manually, reducing defects and enhancing product reliability.
Cost Efficiency: While the initial investment in automation technology can be substantial, the long-term savings are considerable. Automation reduces labor costs, minimizes waste through precise material usage, and lowers the costs associated with errors and rework.
Improved Safety: Automated systems handle hazardous tasks, such as working with toxic chemicals, heavy lifting, or high-temperature processes, thereby reducing the risk of workplace injuries and improving overall safety for human workers.
Flexibility and Scalability: Modern automated systems are highly adaptable, allowing manufacturers to switch between different products or adjust production volumes with minimal downtime. This flexibility enables rapid responses to market demands and customization requests.
Data Collection and Analysis: Automation systems are often integrated with data analytics tools, enabling real-time monitoring and optimization of manufacturing processes. This data-driven approach facilitates continuous improvement, predictive maintenance, and informed decision-making.
Space and Energy Efficiency: Automated machinery is often more compact and energy-efficient than traditional manufacturing setups. Optimized layouts and reduced energy consumption contribute to more sustainable and environmentally friendly manufacturing practices.
Primary Benefits of Automation in Manufacturing:
- Consistency and Reliability: Automated systems perform tasks uniformly, ensuring that every product meets the same quality standards.
- Reduction in Labor Costs: Automation decreases the need for manual labor, lowering overall production costs and reallocating human resources to more strategic roles.
- Faster Production Cycles: Automation accelerates manufacturing processes, enabling quicker turnaround times from design to finished product.
- Enhanced Innovation: By handling routine tasks, automation frees engineers and designers to focus on innovation, research, and development of new products and technologies.
- Competitive Advantage: Companies that leverage automation can achieve higher efficiency, better quality, and lower costs, providing a significant edge in competitive markets.
In summary, automation has transformed manufacturing in mechanical engineering by driving efficiency, enhancing quality, reducing costs, and improving safety. These benefits enable manufacturers to produce high-quality products at scale, respond swiftly to market changes, and maintain a competitive position in the industry.
3. What are the different types of robots used in mechanical engineering, and what specific applications do they serve in industrial settings?
Answer:
In mechanical engineering, various types of robots are employed to perform a wide range of tasks in industrial settings. The primary types include:
Articulated Robots:
- Description: Feature rotary joints and multiple axes (usually 4 to 7), providing a wide range of motion and flexibility.
- Applications:
- Welding: Articulated robots are widely used in spot welding and arc welding due to their precision and ability to follow complex paths.
- Assembly: Used for assembling components in automotive and electronics manufacturing, where precision and flexibility are essential.
- Material Handling: Employed in tasks such as palletizing, packaging, and transferring materials between processes.
SCARA Robots (Selective Compliance Assembly Robot Arm):
- Description: Consist of two parallel rotary joints that provide movement in the XY plane, with additional vertical movement.
- Applications:
- Pick and Place: Ideal for high-speed, precise pick-and-place operations in electronics assembly and packaging.
- Assembly: Used for assembling small to medium-sized parts where horizontal movement and precision are required.
- Testing: Employed in automated testing systems for repetitive and precise handling tasks.
Cartesian Robots (Gantry Robots):
- Description: Operate on three linear axes (X, Y, Z) and move along straight lines within a rectangular coordinate system.
- Applications:
- 3D Printing: Utilized in additive manufacturing for precise layer-by-layer deposition.
- Machining: Used for milling, drilling, and cutting operations where linear precision is critical.
- Material Handling: Employed in automated storage and retrieval systems for moving materials across fixed paths.
Cylindrical Robots:
- Description: Feature a cylindrical work envelope with a combination of rotary and linear joints, allowing movement within a cylindrical coordinate system.
- Applications:
- Assembly: Used for assembling parts that require movement along a cylindrical axis, such as in the automotive industry.
- Packaging: Employed in packaging lines for tasks that involve rotating and stacking products.
- Handling: Used for handling cylindrical objects like pipes, tubes, and barrels in manufacturing processes.
Delta Robots (Parallel Link Robots):
- Description: Consist of multiple arms connected to a base, forming a parallel linkage system. Known for their high speed and precision.
- Applications:
- Pick and Place: Ideal for high-speed pick-and-place tasks in food packaging, pharmaceuticals, and electronics assembly.
- Sorting: Used in sorting systems to quickly and accurately separate different types of products.
- Assembly: Employed in lightweight assembly tasks where rapid and precise movements are necessary.
Collaborative Robots (Cobots):
- Description: Designed to work alongside human workers, featuring safety features such as force-limiting capabilities and sensors to detect human presence.
- Applications:
- Assembly Assistance: Assist human workers in assembling complex products by handling repetitive or ergonomically challenging tasks.
- Machine Tending: Operate alongside humans to load and unload machines, increasing efficiency and reducing manual labor.
- Quality Inspection: Perform inspection tasks in collaboration with humans, combining precision with human judgment.
Mobile Robots:
- Description: Equipped with wheels or tracks, allowing them to move freely within a workspace.
- Applications:
- Logistics and Warehousing: Used for transporting materials, managing inventory, and automating storage systems.
- Inspection and Maintenance: Perform routine inspections and maintenance tasks in large facilities, such as factories or warehouses.
- Delivery: Employed in on-site delivery of parts and tools within manufacturing plants, enhancing workflow efficiency.
Specific Industrial Applications:
Automotive Manufacturing: Articulated and SCARA robots are extensively used for welding, painting, and assembly of vehicles, ensuring high precision and repeatability.
Electronics Assembly: Delta and SCARA robots handle delicate components with speed and accuracy, essential for assembling electronic devices and circuit boards.
Food and Beverage Industry: Collaborative and Delta robots perform packaging, sorting, and quality inspection tasks, maintaining hygiene standards while increasing throughput.
Aerospace Manufacturing: Articulated and Cartesian robots are used for machining, assembly, and inspection of complex aerospace components, ensuring high standards of precision and quality.
Pharmaceutical Industry: SCARA and collaborative robots manage packaging, labeling, and handling of sensitive pharmaceutical products, maintaining compliance with regulatory standards.
In summary, the diverse types of robots used in mechanical engineering cater to various industrial applications, enhancing efficiency, precision, and safety across multiple sectors. Their specialized capabilities enable the automation of complex and repetitive tasks, driving innovation and productivity in modern manufacturing environments.
4. How do control systems in robotics enable precise and coordinated movements, and what are the differences between open-loop and closed-loop control systems?
Answer:
Control systems in robotics are fundamental for enabling precise and coordinated movements by managing the robot’s actuators based on input from sensors and predefined instructions. These systems interpret commands, process feedback, and adjust actions to achieve desired outcomes accurately.
Control Systems in Robotics:
Components:
- Controller: The brain of the robot, often a microcontroller or computer, which processes input signals and sends commands to actuators.
- Actuators: Devices such as motors and servos that perform physical movements based on controller commands.
- Sensors: Devices that provide feedback on the robot’s position, velocity, force, and other parameters, allowing the controller to make informed decisions.
- Software: Algorithms and programs that define how the robot should interpret sensor data and generate movement commands.
Functionality:
- Path Planning: Determines the trajectory the robot should follow to move from one point to another.
- Motion Control: Executes the path by controlling the actuators to achieve smooth and accurate movements.
- Feedback Processing: Continuously monitors sensor data to ensure the robot follows the intended path and adjusts movements as necessary.
Open-Loop vs. Closed-Loop Control Systems:
Open-Loop Control Systems:
- Definition: Operate without using feedback to adjust actions. Commands are sent to actuators based solely on predefined instructions.
- Characteristics:
- Simplicity: Easier to design and implement since they do not require sensors or feedback mechanisms.
- Cost-Effective: Generally cheaper due to fewer components.
- No Correction Mechanism: Cannot compensate for disturbances, errors, or changes in the system.
- Applications:
- Basic Automation: Tasks where precision is not critical, such as simple conveyor belt movements.
- Timed Operations: Processes that follow a set sequence without the need for adjustments, like irrigation systems.
- Limitations:
- Lack of Precision: Susceptible to errors due to system disturbances or variations.
- Inflexibility: Cannot adapt to changes in the environment or task requirements.
Closed-Loop Control Systems:
- Definition: Utilize feedback from sensors to continuously monitor and adjust the robot’s actions, ensuring that the desired outcome is achieved.
- Characteristics:
- Precision and Accuracy: Can correct errors and compensate for disturbances, leading to more accurate and reliable movements.
- Complexity: More complex to design and implement due to the need for sensors and feedback algorithms.
- Higher Cost: Generally more expensive because of additional components and processing requirements.
- Applications:
- High-Precision Manufacturing: Tasks requiring exact positioning and movement, such as CNC machining and robotic welding.
- Adaptive Robotics: Robots that operate in dynamic environments, such as autonomous vehicles and service robots.
- Force-Controlled Tasks: Applications where the robot must respond to variations in load or force, like assembly operations.
- Advantages:
- Error Correction: Continuously adjusts to minimize discrepancies between desired and actual positions.
- Adaptability: Can respond to changes in the environment or task parameters, enhancing versatility.
Examples of Control Systems in Robotics:
Open-Loop Example: A simple robotic arm that moves to predefined positions without sensing its actual location. It follows the programmed path regardless of any external interference or load changes.
Closed-Loop Example: A robotic arm equipped with encoders and force sensors that monitor its position and the force applied during tasks. The control system adjusts motor inputs in real-time to ensure the arm follows the intended trajectory precisely, compensating for any deviations or unexpected loads.
Conclusion: Control systems are essential for achieving precise and coordinated movements in robotics. While open-loop systems offer simplicity and cost advantages for basic tasks, closed-loop systems provide the necessary precision, adaptability, and reliability required for complex and high-stakes applications in mechanical engineering. The choice between open-loop and closed-loop control depends on the specific requirements of the task, including the need for accuracy, responsiveness, and flexibility.
5. In what ways has the integration of artificial intelligence (AI) enhanced the capabilities of robotics and automation in mechanical engineering?
Answer:
The integration of artificial intelligence (AI) has significantly enhanced the capabilities of robotics and automation in mechanical engineering by enabling smarter, more adaptive, and autonomous systems. AI brings several advancements to robotics, including:
Enhanced Perception and Sensing:
- Machine Vision: AI-powered computer vision allows robots to interpret and understand visual data from cameras and sensors, enabling tasks like object recognition, defect detection, and navigation.
- Sensor Fusion: AI algorithms integrate data from multiple sensors (e.g., LIDAR, ultrasonic, infrared) to create a comprehensive understanding of the robot’s environment, improving decision-making and situational awareness.
Advanced Decision-Making and Planning:
- Path Planning: AI algorithms optimize the robot’s movement paths, enabling efficient navigation around obstacles and minimizing energy consumption.
- Task Scheduling: AI systems manage and prioritize tasks in real-time, optimizing workflow and resource allocation in dynamic manufacturing environments.
Autonomous Operation:
- Self-Navigation: AI enables mobile robots to autonomously navigate complex and changing environments without human intervention, essential for applications like warehouse logistics and autonomous vehicles.
- Adaptive Control: AI allows robots to adapt to new tasks and environments by learning from experience, enhancing their versatility and reducing the need for reprogramming.
Predictive Maintenance:
- Failure Prediction: AI analyzes sensor data to predict potential equipment failures before they occur, enabling proactive maintenance and reducing downtime.
- Performance Optimization: AI systems continuously monitor and adjust robot performance parameters to maintain optimal efficiency and longevity.
Human-Robot Collaboration:
- Safety Enhancements: AI improves the ability of robots to detect and respond to human presence, ensuring safe interactions in shared workspaces.
- Adaptive Interfaces: AI-driven interfaces allow robots to understand and respond to human gestures, voice commands, and behavioral cues, facilitating seamless collaboration.
Quality Control and Inspection:
- Defect Detection: AI-powered image analysis identifies defects and anomalies in products with higher accuracy and speed than manual inspections.
- Process Optimization: AI analyzes production data to identify inefficiencies and optimize manufacturing processes, improving quality and reducing waste.
Customization and Flexibility:
- Dynamic Reconfiguration: AI enables robots to reconfigure their tasks and workflows dynamically, supporting customized production runs and small-batch manufacturing.
- Learning and Adaptation: Robots equipped with machine learning capabilities can learn new tasks from demonstration or data, enhancing their adaptability to diverse applications.
Energy Efficiency:
- Optimized Energy Use: AI algorithms manage and optimize energy consumption in robotic systems, reducing operational costs and enhancing sustainability.
- Smart Scheduling: AI schedules robotic operations to align with energy availability and peak demand periods, improving overall energy efficiency.
Specific Examples of AI Integration in Robotics and Automation:
Autonomous Guided Vehicles (AGVs): AGVs in warehouses use AI for real-time navigation, obstacle avoidance, and efficient route planning, streamlining logistics and inventory management.
Collaborative Robots (Cobots): Cobots equipped with AI can learn from human workers, adapt to varying tasks, and ensure safe interactions, enhancing productivity and flexibility in assembly lines.
Robotic Welding Systems: AI-driven welding robots optimize welding parameters in real-time based on sensor feedback, ensuring consistent weld quality and adapting to variations in material properties.
Inspection Robots: AI-powered inspection robots use machine vision to identify defects in manufactured parts, providing high-precision quality control and reducing the need for manual inspections.
Benefits of AI-Enhanced Robotics and Automation:
Increased Efficiency: AI optimizes robotic operations, reducing cycle times and increasing throughput in manufacturing processes.
Improved Quality: Enhanced precision and consistency lead to higher product quality and lower defect rates.
Cost Savings: Automation driven by AI reduces labor costs, minimizes waste, and lowers maintenance expenses through predictive maintenance.
Enhanced Flexibility: AI enables robots to adapt to new tasks and environments, supporting a wide range of applications and fostering innovation.
Safety Improvements: AI enhances the ability of robots to operate safely alongside humans, reducing workplace accidents and improving overall safety standards.
Conclusion: The integration of artificial intelligence into robotics and automation has fundamentally transformed mechanical engineering by enabling smarter, more autonomous, and highly efficient systems. AI-enhanced robots can perceive their environment, make informed decisions, adapt to changing conditions, and collaborate seamlessly with human workers, driving significant advancements in productivity, quality, and safety across various industrial applications.
6. What are the main challenges faced in implementing robotics and automation in mechanical engineering industries, and how can these challenges be overcome?
Answer:
Implementing robotics and automation in mechanical engineering industries presents several challenges, which can be addressed through strategic planning, investment in technology, workforce training, and continuous improvement. The main challenges include:
High Initial Investment Costs:
- Challenge: The upfront costs for purchasing, installing, and integrating robotic systems can be prohibitively high, especially for small and medium-sized enterprises (SMEs).
- Solutions:
- Cost-Benefit Analysis: Conduct thorough analyses to demonstrate long-term savings and return on investment (ROI).
- Leasing and Financing Options: Explore leasing or financing arrangements to spread out costs over time.
- Government Grants and Incentives: Utilize available government programs that support automation adoption.
Integration with Existing Systems:
- Challenge: Integrating new robotic systems with legacy equipment and existing workflows can be complex and time-consuming.
- Solutions:
- Modular and Flexible Systems: Invest in modular robotic systems that can be easily adapted and scaled.
- Standardized Interfaces: Use standardized communication protocols and interfaces to facilitate seamless integration.
- Professional Expertise: Engage automation specialists or consultants to ensure smooth integration and minimize disruption.
Workforce Resistance and Skill Gaps:
- Challenge: Employees may resist automation due to fear of job displacement, and there may be a lack of skilled workers to operate and maintain robotic systems.
- Solutions:
- Employee Training Programs: Invest in training and upskilling programs to prepare the workforce for new roles in managing and maintaining automation systems.
- Change Management: Implement effective change management strategies to address concerns, communicate benefits, and foster a culture of innovation.
- Collaborative Robotics (Cobots): Use cobots that work alongside humans, enhancing productivity without replacing jobs entirely.
Maintenance and Downtime:
- Challenge: Robotic systems require regular maintenance to operate effectively, and unexpected downtime can disrupt production.
- Solutions:
- Predictive Maintenance: Implement predictive maintenance strategies using IoT sensors and AI to anticipate and prevent failures.
- Service Contracts: Establish service agreements with robotic vendors for timely maintenance and support.
- Redundancy Planning: Design systems with redundancy to ensure continuity during maintenance or repairs.
Complexity of Programming and Operation:
- Challenge: Programming and operating robotic systems can be technically challenging, requiring specialized knowledge.
- Solutions:
- User-Friendly Interfaces: Invest in robots with intuitive programming interfaces and visual programming tools that simplify the programming process.
- Training and Education: Provide comprehensive training for operators and engineers to develop the necessary skills.
- Vendor Support: Utilize vendor-provided training, support, and resources to ease the learning curve.
Safety Concerns:
- Challenge: Ensuring the safety of human workers when operating alongside robots is paramount to prevent accidents and injuries.
- Solutions:
- Safety Standards Compliance: Adhere to international safety standards and regulations for robotics in the workplace.
- Advanced Safety Features: Utilize robots equipped with sensors, force-limiting technologies, and emergency stop mechanisms to enhance safety.
- Risk Assessments: Conduct regular safety risk assessments and implement appropriate safeguards to protect workers.
Scalability and Flexibility:
- Challenge: Scaling robotic systems to accommodate varying production volumes and adapting them to different tasks can be challenging.
- Solutions:
- Flexible Automation Solutions: Implement flexible robotic systems that can be easily reprogrammed and reconfigured for different tasks.
- Scalable Infrastructure: Design production facilities with scalable infrastructure that can support the expansion of robotic systems as needed.
- Modular Robotics: Use modular robotic units that can be added or reconfigured based on production requirements.
Data Management and Cybersecurity:
- Challenge: Managing the vast amounts of data generated by robotic systems and protecting them from cyber threats is crucial.
- Solutions:
- Robust Data Management Systems: Implement centralized data management platforms that handle data storage, processing, and analysis efficiently.
- Cybersecurity Measures: Employ strong cybersecurity protocols, including encryption, firewalls, and regular security audits, to protect robotic systems and data.
- Employee Training: Educate employees on best practices for data security and cyber threat prevention.
Conclusion: Implementing robotics and automation in mechanical engineering industries involves navigating various challenges, including high costs, integration complexities, workforce issues, maintenance, safety, scalability, and cybersecurity. By adopting strategic approaches such as investing in training, leveraging advanced technologies, ensuring safety compliance, and fostering a culture of innovation, industries can successfully overcome these challenges. This enables them to reap the substantial benefits of robotics and automation, including increased productivity, enhanced quality, and improved competitiveness in the global market.
7. How do collaborative robots (cobots) differ from traditional industrial robots, and what advantages do they offer in mechanical engineering applications?
Answer:
Collaborative robots, or cobots, are designed to work alongside human operators in a shared workspace, distinguishing them from traditional industrial robots, which typically operate in isolation or within fenced-off environments. The key differences and advantages of cobots in mechanical engineering applications include:
Differences Between Cobots and Traditional Industrial Robots:
Design and Safety Features:
- Cobots: Equipped with advanced sensors, force-limiting capabilities, and compliant joints to detect and respond to human presence, ensuring safe interactions. They often include features like padded exteriors and speed reduction in the presence of humans.
- Traditional Robots: Generally designed for high-speed, high-precision tasks with limited or no built-in safety features. They operate at higher speeds and forces, often requiring physical barriers to ensure human safety.
Programming and Ease of Use:
- Cobots: Feature user-friendly programming interfaces, such as hand-guiding, teach pendants, or visual programming tools, making them accessible to operators with minimal programming experience.
- Traditional Robots: Require specialized programming knowledge and expertise, often involving complex coding languages and integration processes.
Flexibility and Adaptability:
- Cobots: Highly flexible and easily reprogrammable for different tasks, enabling quick changes in production processes without significant downtime or reconfiguration.
- Traditional Robots: Typically specialized for specific tasks, making them less adaptable to changes and requiring substantial reprogramming or retooling to perform different functions.
Payload and Speed:
- Cobots: Generally have lower payload capacities and operate at slower speeds compared to traditional robots, aligning with tasks that require careful handling and precision alongside human workers.
- Traditional Robots: Designed for high payloads and fast operation, suitable for heavy-duty tasks such as welding, material handling, and large-scale assembly.
Advantages of Cobots in Mechanical Engineering Applications:
Enhanced Flexibility:
- Benefit: Cobots can be easily redeployed for various tasks within the production line, supporting multiple operations such as assembly, inspection, packaging, and machine tending.
- Example: In a small-scale assembly line, a cobot can switch between assembling different components without requiring extensive reprogramming.
Cost-Effectiveness:
- Benefit: Cobots typically require lower upfront investment compared to traditional industrial robots and reduce the need for additional safety infrastructure like barriers or cages.
- Example: SMEs can adopt cobots for automation without the prohibitive costs associated with traditional robotic systems, enabling them to enhance productivity without significant financial burden.
Improved Ergonomics and Worker Safety:
- Benefit: Cobots handle repetitive, strenuous, or hazardous tasks, reducing physical strain on human workers and minimizing the risk of injuries.
- Example: Cobots can perform lifting and moving of heavy parts, allowing human workers to focus on more intricate and less physically demanding tasks.
Ease of Integration:
- Benefit: Cobots are designed for easy integration into existing workflows and workspaces, often requiring minimal setup and programming.
- Example: A cobot can be quickly installed on a workstation to assist with assembly tasks, seamlessly blending into the current production process without major disruptions.
Increased Productivity and Quality:
- Benefit: By collaborating with human workers, cobots can enhance overall productivity and ensure consistent quality in tasks that require precision and repeatability.
- Example: In quality inspection, cobots can assist human inspectors by handling repetitive measurements, allowing inspectors to focus on analysis and decision-making, thereby increasing both speed and accuracy.
Scalability:
- Benefit: Cobots can be easily scaled up or down based on production demands, providing flexibility to adapt to fluctuating workloads without significant changes to the production setup.
- Example: During peak production periods, additional cobots can be deployed to meet increased demand, and scaled back during off-peak times to optimize resource utilization.
Enhanced Human-Robot Collaboration:
- Benefit: Cobots work alongside humans, leveraging the strengths of both to achieve better outcomes than either could alone.
- Example: In a mixed assembly task, cobots can handle repetitive positioning while humans perform complex fastening, combining efficiency with dexterity.
Conclusion: Collaborative robots offer significant advantages over traditional industrial robots in mechanical engineering applications by providing enhanced flexibility, cost-effectiveness, safety, and ease of integration. Their ability to work alongside human operators enables more efficient and adaptable production processes, making cobots an invaluable asset in modern manufacturing environments. As technology advances, the role of cobots is expected to expand, further transforming the landscape of mechanical engineering and automation.
8. What role do sensors play in the functionality of automated systems in mechanical engineering, and how do different types of sensors contribute to system performance?
Answer:
Sensors are integral to the functionality of automated systems in mechanical engineering, providing critical data that enable real-time monitoring, control, and optimization of processes. They act as the eyes and ears of automated systems, allowing them to perceive their environment, assess internal states, and respond appropriately to changes. Different types of sensors contribute to system performance in various ways:
Roles of Sensors in Automated Systems:
- Perception: Sensors gather information about the environment and the system’s status, enabling automated systems to make informed decisions.
- Monitoring: Continuously track parameters such as position, speed, temperature, pressure, and force to ensure optimal performance and detect anomalies.
- Control: Provide feedback that allows control systems to adjust actions and maintain desired operational states.
- Safety: Detect hazardous conditions and trigger safety mechanisms to prevent accidents and protect both equipment and personnel.
- Quality Assurance: Monitor process variables to ensure products meet specified quality standards and detect defects early in the production cycle.
Types of Sensors and Their Contributions:
Proximity Sensors:
- Function: Detect the presence or absence of objects without physical contact.
- Types: Inductive, capacitive, ultrasonic, infrared.
- Contribution to Performance: Enable tasks like object detection, positioning, and collision avoidance, ensuring precise and safe operations.
Position and Displacement Sensors:
- Function: Measure the position or movement of a component within the system.
- Types: Linear Variable Differential Transformers (LVDTs), rotary encoders, potentiometers.
- Contribution to Performance: Provide accurate feedback for motion control, ensuring components move to the correct locations and maintain alignment.
Force and Torque Sensors:
- Function: Measure the force or torque applied to a component.
- Types: Strain gauges, piezoelectric sensors, load cells.
- Contribution to Performance: Ensure that operations such as assembly, gripping, and machining are performed with the appropriate force, preventing damage and ensuring quality.
Temperature Sensors:
- Function: Monitor the temperature of components or environments.
- Types: Thermocouples, Resistance Temperature Detectors (RTDs), infrared sensors.
- Contribution to Performance: Maintain optimal operating temperatures, prevent overheating, and ensure materials perform within their thermal limits.
Vision Systems (Cameras and Image Sensors):
- Function: Capture visual information for analysis and decision-making.
- Types: 2D cameras, 3D cameras, high-speed cameras.
- Contribution to Performance: Enable tasks like inspection, quality control, object recognition, and guidance for robotic manipulation, enhancing precision and reliability.
Flow and Pressure Sensors:
- Function: Measure the flow rate and pressure of fluids within systems.
- Types: Differential pressure sensors, flow meters, piezoelectric pressure sensors.
- Contribution to Performance: Ensure proper fluid dynamics in processes like lubrication, cooling, and pneumatic/hydraulic systems, maintaining system efficiency and preventing failures.
Accelerometers and Gyroscopes:
- Function: Measure acceleration and rotational motion.
- Types: MEMS accelerometers, MEMS gyroscopes.
- Contribution to Performance: Enable motion tracking, vibration analysis, and stability control in dynamic systems, improving operational stability and reducing wear.
Humidity Sensors:
- Function: Measure the moisture level in the environment.
- Types: Capacitive humidity sensors, resistive humidity sensors.
- Contribution to Performance: Protect sensitive components from moisture-related damage and maintain optimal environmental conditions for manufacturing processes.
pH and Chemical Sensors:
- Function: Monitor the chemical composition and pH levels in fluids.
- Types: Glass electrode pH sensors, ion-selective electrodes.
- Contribution to Performance: Ensure chemical processes operate within desired parameters, preventing corrosion, scaling, and ensuring product quality.
Light Sensors:
- Function: Detect light intensity and changes in lighting conditions.
- Types: Photodiodes, phototransistors, ambient light sensors.
- Contribution to Performance: Control lighting in automated systems, enable vision-based applications, and adjust operations based on ambient light conditions.
Integration of Sensors for Enhanced System Performance:
Sensor Fusion: Combining data from multiple sensors to create a comprehensive understanding of the system and its environment, leading to more accurate and reliable decision-making.
Real-Time Monitoring: Continuous data collection allows for immediate adjustments to operations, ensuring consistent performance and rapid response to changes or disturbances.
Predictive Maintenance: Analyzing sensor data to predict potential failures before they occur, enabling proactive maintenance and reducing unplanned downtime.
Adaptive Control: Using sensor feedback to dynamically adjust control parameters, optimizing system performance under varying conditions.
Conclusion: Sensors are vital to the functionality and performance of automated systems in mechanical engineering. By providing critical data for perception, monitoring, control, safety, and quality assurance, different types of sensors enable precise, efficient, and reliable operations. The integration and intelligent use of sensor data through advanced control systems and AI further enhance the capabilities of robotics and automation, driving innovation and excellence in mechanical engineering applications.
9. How does the use of additive manufacturing (3D printing) intersect with robotics and automation in mechanical engineering, and what benefits does this combination bring to the production process?
Answer:
Additive manufacturing (AM), commonly known as 3D printing, intersects with robotics and automation in mechanical engineering by integrating advanced manufacturing techniques with automated handling, assembly, and quality control processes. This synergy enhances the production process by increasing efficiency, flexibility, and precision while reducing costs and lead times.
Intersection of Additive Manufacturing, Robotics, and Automation:
Automated Material Handling:
- Integration: Robotics systems handle the loading and unloading of 3D printers, managing raw materials and finished parts autonomously.
- Benefit: Reduces manual labor, minimizes human error, and increases throughput by enabling continuous production cycles without human intervention.
Robotic Assembly:
- Integration: Robots perform post-processing tasks such as cleaning, curing, and assembling printed components.
- Benefit: Ensures consistent quality and precision in the assembly of complex parts, streamlining the production workflow and enabling the creation of intricate assemblies that would be challenging manually.
Quality Control and Inspection:
- Integration: Automated inspection systems, including vision-based sensors and AI algorithms, assess the quality of 3D printed parts in real-time.
- Benefit: Enhances quality assurance by detecting defects and deviations immediately, allowing for prompt corrective actions and maintaining high standards of product quality.
Design Optimization and Iteration:
- Integration: Automated systems use CAD and CAM software to optimize designs for additive manufacturing, adjusting parameters to improve printability and performance.
- Benefit: Accelerates the design iteration process, enabling rapid prototyping and optimization without extensive manual adjustments, thus speeding up innovation and product development cycles.
Hybrid Manufacturing Systems:
- Integration: Combines additive and subtractive manufacturing processes within a single automated system, where a robot can switch between 3D printing and CNC machining.
- Benefit: Enables the creation of complex geometries with high precision, leveraging the strengths of both additive and traditional manufacturing techniques for enhanced product capabilities.
Customization and On-Demand Production:
- Integration: Automated systems facilitate the production of customized parts tailored to specific requirements, adjusting the printing process based on real-time data.
- Benefit: Supports mass customization, allowing manufacturers to produce unique or limited-run products efficiently without the need for extensive retooling or setup changes.
Benefits of Combining Additive Manufacturing with Robotics and Automation:
Increased Efficiency:
- Benefit: Automation reduces the time and labor required for various stages of the additive manufacturing process, from material preparation to post-processing, resulting in faster production cycles.
Enhanced Precision and Consistency:
- Benefit: Robotic systems ensure precise handling and consistent execution of tasks, minimizing variations and defects in 3D printed parts, thus improving overall product quality.
Scalability:
- Benefit: Automated additive manufacturing systems can be scaled up to meet increasing production demands without a proportional increase in labor costs, supporting larger-scale manufacturing operations.
Flexibility and Adaptability:
- Benefit: The combination allows for quick changes in production lines to accommodate different designs and products, enhancing the ability to respond to market demands and technological advancements swiftly.
Cost Reduction:
- Benefit: Automation lowers operational costs by reducing the need for manual labor, minimizing material waste through precise printing and handling, and decreasing the likelihood of errors and rework.
Improved Safety:
- Benefit: Robots handle hazardous tasks, such as operating high-temperature printers or managing toxic materials, enhancing workplace safety by reducing human exposure to dangerous conditions.
Innovation and Complexity:
- Benefit: The integration enables the production of highly complex and intricate designs that are difficult or impossible to achieve with traditional manufacturing methods, fostering innovation in product development.
Data Integration and Smart Manufacturing:
- Benefit: Automated systems can collect and analyze data from the additive manufacturing process, providing insights for continuous improvement, predictive maintenance, and optimized production strategies.
Specific Applications:
Aerospace Industry: Automated AM systems produce lightweight, high-strength components with complex geometries, such as turbine blades and structural parts, enhancing aircraft performance and fuel efficiency.
Medical Devices: Robotics-integrated AM facilitates the production of customized implants, prosthetics, and surgical tools, improving patient outcomes and enabling personalized medicine.
Automotive Industry: Hybrid manufacturing systems create intricate engine parts, lightweight components, and custom accessories, supporting advanced vehicle designs and performance enhancements.
Electronics Manufacturing: Automated AM enables the production of complex electronic housings, antennas, and cooling systems, improving the functionality and integration of electronic devices.
Conclusion: The intersection of additive manufacturing with robotics and automation brings significant advancements to mechanical engineering by enhancing efficiency, precision, flexibility, and scalability in the production process. This combination supports the creation of complex and customized products, reduces costs, and fosters innovation, making it a pivotal element in the evolution of modern manufacturing practices.
10. What are the ethical and societal implications of increasing automation and robotics in mechanical engineering, and how can engineers address these concerns responsibly?
Answer:
The increasing adoption of automation and robotics in mechanical engineering brings forth a range of ethical and societal implications that require careful consideration and responsible action from engineers. Key implications and strategies to address them include:
Ethical and Societal Implications:
Job Displacement and Workforce Impact:
- Implication: Automation can lead to the displacement of workers, particularly in roles involving repetitive and manual tasks, resulting in unemployment and economic disparities.
- Addressing the Concern:
- Reskilling and Upskilling: Implement training programs to help workers acquire new skills relevant to emerging roles in robotics, maintenance, and advanced manufacturing.
- Job Creation: Focus on creating new job opportunities in areas such as robotics programming, system integration, and oversight, which require higher skill levels.
- Collaborative Robotics: Utilize cobots that work alongside humans, enhancing productivity without entirely replacing human workers.
Economic Inequality:
- Implication: The benefits of automation may be concentrated in large corporations and developed regions, exacerbating economic inequalities and limiting access to advanced technologies in smaller businesses and developing countries.
- Addressing the Concern:
- Inclusive Technology Development: Promote the development and distribution of affordable automation solutions that can be adopted by small and medium-sized enterprises (SMEs).
- Global Collaboration: Encourage international partnerships and knowledge sharing to ensure equitable access to automation technologies worldwide.
Privacy and Data Security:
- Implication: Automated systems often rely on data collection and processing, raising concerns about privacy, data ownership, and the potential for misuse or cyberattacks.
- Addressing the Concern:
- Robust Data Protection: Implement strong cybersecurity measures, encryption, and access controls to protect sensitive data.
- Transparent Data Practices: Clearly communicate data collection and usage policies to stakeholders, ensuring transparency and building trust.
- Compliance with Regulations: Adhere to data protection laws and standards, such as GDPR, to safeguard privacy rights.
Safety and Liability:
- Implication: As robots become more autonomous and capable, ensuring their safe operation and determining liability in case of accidents or malfunctions becomes more complex.
- Addressing the Concern:
- Safety Standards Compliance: Adhere to established safety standards and guidelines for robotics and automation, such as ISO 10218 for industrial robots.
- Redundancy and Fail-Safes: Design systems with redundant safety features and fail-safe mechanisms to prevent accidents.
- Clear Liability Frameworks: Establish clear legal frameworks that define liability in cases of robotic system failures or accidents, ensuring accountability.
Environmental Impact:
- Implication: Automation and robotics can lead to increased energy consumption and electronic waste if not managed sustainably.
- Addressing the Concern:
- Energy-Efficient Designs: Develop robotic systems that prioritize energy efficiency, utilizing renewable energy sources where possible.
- Sustainable Manufacturing Practices: Implement recycling and waste reduction strategies for robotic components and materials.
- Lifecycle Assessment: Conduct comprehensive lifecycle assessments to understand and mitigate the environmental impact of automation technologies.
Ethical Use of AI and Decision-Making:
- Implication: The integration of AI in robotics raises ethical questions about decision-making autonomy, bias, and accountability.
- Addressing the Concern:
- Ethical AI Development: Ensure that AI algorithms are designed with fairness, transparency, and accountability in mind, avoiding biases that could lead to discriminatory practices.
- Human Oversight: Maintain human oversight in critical decision-making processes to ensure ethical considerations are upheld.
- Ethical Guidelines: Adhere to ethical guidelines and frameworks for AI and robotics, promoting responsible innovation.
Social Acceptance and Trust:
- Implication: Public perception and trust in automated systems and robots can influence their adoption and integration into society.
- Addressing the Concern:
- Engagement and Education: Engage with communities and stakeholders to educate them about the benefits and safety measures of automation and robotics.
- Transparency: Maintain transparency in the development and deployment of robotic systems, building trust through open communication and accountability.
- User-Centric Design: Design robots and automated systems with user needs and societal values in mind, ensuring they complement rather than disrupt human activities.
Strategies for Responsible Addressing:
Inclusive Design and Development:
- Involve diverse stakeholders, including workers, community members, and ethicists, in the design and implementation of automation technologies to ensure they meet societal needs and ethical standards.
Policy and Regulation:
- Collaborate with policymakers to develop regulations that address the ethical and societal implications of robotics and automation, ensuring that technological advancements align with societal values and public interests.
Corporate Social Responsibility (CSR):
- Companies implementing automation should adopt CSR practices that prioritize the well-being of employees, communities, and the environment, balancing profit motives with social and ethical responsibilities.
Continuous Monitoring and Evaluation:
- Regularly assess the impact of automation and robotics on society and the environment, making necessary adjustments to practices and technologies to mitigate negative effects and enhance positive outcomes.
Conclusion: The increasing automation and robotics in mechanical engineering present significant ethical and societal challenges, including job displacement, economic inequality, privacy concerns, safety issues, environmental impact, ethical AI use, and social acceptance. Engineers and organizations must proactively address these concerns through inclusive design, robust safety and data protection measures, ethical AI development, workforce reskilling, sustainable practices, and transparent communication. By adopting responsible strategies, the benefits of automation and robotics can be harnessed while minimizing adverse impacts, ensuring that technological advancements contribute positively to society and the environment.
11. How does machine learning contribute to the advancement of automation systems in mechanical engineering, and what are some practical applications of machine learning in this field?
Answer:
Machine learning (ML), a subset of artificial intelligence (AI), significantly contributes to the advancement of automation systems in mechanical engineering by enabling systems to learn from data, adapt to new conditions, and optimize performance without explicit programming. ML enhances the capabilities of automated systems, making them more intelligent, efficient, and capable of handling complex tasks.
Contribution of Machine Learning to Automation Systems:
Predictive Maintenance:
- Function: ML algorithms analyze historical and real-time sensor data to predict equipment failures before they occur.
- Impact: Reduces downtime, extends equipment lifespan, and lowers maintenance costs by enabling proactive maintenance schedules.
Quality Control and Defect Detection:
- Function: ML models process data from vision systems and sensors to identify defects and ensure product quality.
- Impact: Enhances precision and consistency in quality assurance, reduces human error, and increases the speed of inspection processes.
Process Optimization:
- Function: ML algorithms analyze production data to identify inefficiencies and optimize manufacturing parameters.
- Impact: Improves production efficiency, reduces waste, and enhances product quality by continuously refining process settings.
Adaptive Control Systems:
- Function: ML enables control systems to adapt to changing conditions and optimize performance in real-time.
- Impact: Enhances the flexibility and responsiveness of automated systems, allowing them to maintain optimal performance under varying operational conditions.
Robotic Path Planning and Motion Control:
- Function: ML algorithms optimize the paths and movements of robots for efficiency and collision avoidance.
- Impact: Increases the speed and accuracy of robotic operations, reduces energy consumption, and improves the overall performance of robotic systems.
Energy Management:
- Function: ML models predict and optimize energy usage in automated systems and manufacturing processes.
- Impact: Reduces energy consumption, lowers operational costs, and contributes to sustainability by optimizing energy efficiency.
Human-Robot Collaboration:
- Function: ML enables robots to learn from human actions and adapt their behavior to work more effectively alongside humans.
- Impact: Enhances the synergy between human workers and robots, improving productivity and ensuring safer interactions in collaborative environments.
Supply Chain Optimization:
- Function: ML algorithms forecast demand, manage inventory, and optimize logistics in automated supply chains.
- Impact: Improves the efficiency and reliability of supply chain operations, ensuring timely delivery of materials and reducing costs associated with overstocking or stockouts.
Practical Applications of Machine Learning in Mechanical Engineering Automation:
Automotive Manufacturing:
- Application: ML algorithms optimize assembly line operations, predict equipment failures, and enhance quality control through defect detection in vehicle components.
- Benefit: Increases production efficiency, reduces downtime, and ensures high-quality vehicle manufacturing.
Aerospace Industry:
- Application: ML models analyze data from aerospace components to predict maintenance needs, optimize flight simulations, and enhance the design of aerodynamic structures.
- Benefit: Enhances the reliability and performance of aerospace systems, reducing maintenance costs and improving safety.
Robotic Welding Systems:
- Application: ML algorithms optimize welding parameters based on real-time sensor data, ensuring consistent weld quality and adapting to variations in materials.
- Benefit: Improves weld quality, reduces defects, and increases the flexibility of welding operations in diverse manufacturing environments.
Additive Manufacturing (3D Printing):
- Application: ML models predict and control printing parameters to enhance print quality, reduce defects, and optimize material usage.
- Benefit: Increases the reliability and efficiency of 3D printing processes, enabling the production of high-quality and complex components.
Smart Factories:
- Application: ML drives the automation and optimization of entire manufacturing systems, integrating data from various sources to enhance decision-making and operational efficiency.
- Benefit: Transforms traditional factories into smart, data-driven environments that are more responsive, efficient, and competitive.
Energy Management in Manufacturing:
- Application: ML algorithms optimize energy consumption in manufacturing processes by predicting energy needs and adjusting operations accordingly.
- Benefit: Reduces energy costs and supports sustainability initiatives by enhancing energy efficiency.
Supply Chain and Logistics:
- Application: ML forecasts demand, optimizes inventory levels, and improves logistics planning in automated supply chains.
- Benefit: Enhances the efficiency and reliability of supply chain operations, ensuring timely and cost-effective material flow.
Maintenance and Repairs:
- Application: Predictive maintenance systems use ML to analyze equipment data and predict potential failures, scheduling maintenance proactively.
- Benefit: Minimizes unexpected downtime, extends equipment lifespan, and reduces maintenance costs through timely interventions.
Process Control in Manufacturing:
- Application: ML algorithms continuously monitor and adjust manufacturing processes to maintain optimal conditions and product quality.
- Benefit: Ensures consistent product quality, reduces variability, and enhances process efficiency through real-time optimization.
Safety Monitoring:
- Application: ML-driven safety systems detect anomalies and hazardous conditions in real-time, triggering alarms or automated responses.
- Benefit: Enhances workplace safety by preventing accidents and responding swiftly to potential dangers, protecting workers and equipment.
Conclusion: Machine learning plays a pivotal role in advancing automation systems within mechanical engineering by enabling intelligent data analysis, predictive capabilities, and adaptive control. Its integration into various applications enhances efficiency, precision, and reliability, driving significant improvements in manufacturing processes, quality control, maintenance, and overall system performance. As ML technologies continue to evolve, their impact on automation in mechanical engineering is expected to grow, fostering innovation and enabling more sophisticated and responsive automated systems.
12. What future trends do you foresee in robotics and automation within mechanical engineering, and how should engineers prepare to adapt to these changes?
Answer:
The future of robotics and automation within mechanical engineering is poised for significant advancements driven by technological innovation, evolving industry demands, and societal changes. Key trends and strategies for engineers to adapt include:
Future Trends in Robotics and Automation:
Artificial Intelligence and Machine Learning Integration:
- Trend: Increasing incorporation of AI and ML into robotic systems for enhanced decision-making, adaptability, and autonomy.
- Impact: Robots will become more intelligent, capable of learning from their environments, optimizing tasks in real-time, and performing complex operations with minimal human intervention.
Collaborative and Cobots Expansion:
- Trend: Growth in the use of collaborative robots that work alongside humans in shared workspaces.
- Impact: Enhances human-robot collaboration, improves productivity, and enables more flexible and adaptive manufacturing processes.
Advanced Sensing and Perception:
- Trend: Development of sophisticated sensors and vision systems that provide robots with better environmental awareness and situational understanding.
- Impact: Robots will achieve higher precision, improved obstacle avoidance, and the ability to perform tasks in more dynamic and unpredictable environments.
Autonomous Mobile Robots (AMRs):
- Trend: Expansion of autonomous mobile robots for logistics, warehousing, and material handling.
- Impact: Increases efficiency in supply chain operations, reduces labor costs, and enhances the scalability of logistics solutions.
Human-Robot Interaction (HRI) Enhancements:
- Trend: Advances in HRI technologies, including natural language processing, gesture recognition, and haptic feedback.
- Impact: Facilitates more intuitive and seamless interactions between humans and robots, improving usability and collaboration.
Flexible and Reconfigurable Automation Systems:
- Trend: Development of automation systems that can be easily reconfigured for different tasks and product lines.
- Impact: Enhances manufacturing flexibility, allowing quick adaptation to changing market demands and customization requirements.
Sustainable and Green Robotics:
- Trend: Focus on developing energy-efficient and environmentally friendly robotic systems.
- Impact: Reduces the environmental footprint of automation, aligns with sustainability goals, and supports eco-friendly manufacturing practices.
Integration with Internet of Things (IoT) and Industry 4.0:
- Trend: Enhanced connectivity of robotic systems with IoT devices and integration into smart factory ecosystems.
- Impact: Enables real-time data exchange, predictive maintenance, and holistic optimization of manufacturing processes through interconnected systems.
Soft Robotics:
- Trend: Emergence of soft robotics, which utilizes flexible and adaptable materials to create robots capable of performing delicate and intricate tasks.
- Impact: Expands the range of applications for robots, including handling fragile objects, biomedical applications, and soft assembly tasks.
Robotic Process Automation (RPA) in Design and Engineering:
- Trend: Utilization of RPA for automating repetitive and time-consuming tasks in design, simulation, and engineering workflows.
- Impact: Increases efficiency in the engineering design process, reduces errors, and frees engineers to focus on more strategic and creative tasks.
Strategies for Engineers to Adapt to Future Trends:
Continuous Learning and Skill Development:
- Action: Engage in lifelong learning through courses, certifications, and training programs focused on emerging technologies such as AI, ML, advanced sensors, and IoT.
- Benefit: Keeps engineers updated with the latest advancements, enhancing their ability to work with cutting-edge technologies.
Interdisciplinary Collaboration:
- Action: Collaborate with professionals from other disciplines, such as computer science, data analytics, and materials science, to foster innovation and holistic problem-solving.
- Benefit: Promotes a broader understanding of integrated systems and enhances the ability to develop versatile and effective automation solutions.
Emphasis on Soft Skills:
- Action: Develop soft skills such as critical thinking, problem-solving, communication, and teamwork.
- Benefit: Enhances the ability to work effectively in collaborative environments and adapt to changing project requirements.
Hands-On Experience with Advanced Technologies:
- Action: Gain practical experience with robotics platforms, simulation software, and automation tools through projects, internships, or laboratory work.
- Benefit: Builds proficiency in using advanced technologies, preparing engineers for real-world applications and challenges.
Focus on Sustainability:
- Action: Incorporate sustainable design principles and energy-efficient practices in automation projects.
- Benefit: Aligns with global sustainability goals, making engineers valuable assets in organizations committed to eco-friendly practices.
Stay Informed About Industry Trends:
- Action: Regularly follow industry publications, attend conferences, and participate in professional networks to stay abreast of the latest trends and innovations.
- Benefit: Enables proactive adaptation to emerging trends, ensuring that engineers remain relevant and competitive in the field.
Innovative Thinking and Creativity:
- Action: Encourage innovative thinking and experimentation with new ideas and technologies in engineering projects.
- Benefit: Drives the development of novel solutions and advancements in robotics and automation.
Ethical and Responsible Engineering Practices:
- Action: Adhere to ethical guidelines and consider the societal impacts of automation and robotics in engineering decisions.
- Benefit: Promotes responsible innovation, ensuring that technological advancements benefit society while minimizing negative consequences.
Investment in Research and Development:
- Action: Engage in or support R&D activities focused on advancing robotics and automation technologies.
- Benefit: Contributes to the development of cutting-edge solutions and positions engineers at the forefront of technological innovation.
Adoption of Agile and Flexible Methodologies:
- Action: Implement agile project management and flexible design methodologies to accommodate rapid changes and iterative development.
- Benefit: Enhances the ability to respond swiftly to new information, market demands, and technological advancements, ensuring successful project outcomes.
Conclusion: The future of robotics and automation in mechanical engineering is characterized by increasing intelligence, flexibility, sustainability, and integration with advanced technologies. Engineers must proactively adapt by continuously developing their skills, embracing interdisciplinary collaboration, and staying informed about emerging trends. By doing so, they can effectively harness the potential of these advancements, driving innovation and maintaining a competitive edge in the rapidly evolving landscape of mechanical engineering.
Robotics and Automation: Thought-Provoking Questions
1. Question:
How has the evolution of sensor technology impacted the capabilities and applications of robotics and automation in mechanical engineering?
Answer:
The evolution of sensor technology has significantly enhanced the capabilities and expanded the applications of robotics and automation in mechanical engineering. Advanced sensors provide robots with improved perception, enabling them to interact more intelligently and safely with their environments. Key impacts include:
Enhanced Perception and Awareness: Modern sensors, such as LiDAR, infrared, ultrasonic, and high-resolution cameras, allow robots to accurately detect and interpret their surroundings. This improved perception is crucial for tasks like autonomous navigation, obstacle avoidance, and precise manipulation in dynamic environments.
Improved Precision and Accuracy: High-precision sensors, including encoders and force sensors, enable robots to perform tasks with greater accuracy. In applications like assembly and machining, this precision ensures that components are positioned and manipulated correctly, reducing errors and improving product quality.
Real-Time Feedback and Adaptation: Advanced sensors provide real-time data that robots use to adjust their actions instantaneously. For instance, in welding applications, temperature sensors monitor heat levels, allowing robots to adjust their welding parameters on the fly to maintain consistent weld quality.
Safety Enhancements: Proximity sensors and collision detection systems enhance the safety of human-robot interactions. These sensors enable robots to detect human presence and halt operations if a potential collision is detected, thereby preventing accidents and ensuring safe collaborative work environments.
Extended Applications: The integration of sophisticated sensors has enabled robots to perform complex and sensitive tasks across various industries. In the medical field, for example, robotic surgery systems use advanced sensors to provide surgeons with precise control and real-time feedback, enhancing the safety and effectiveness of surgical procedures.
Data Collection and Analytics: Sensors continuously collect vast amounts of data, which can be analyzed to optimize robot performance, predict maintenance needs, and improve overall system efficiency. This data-driven approach facilitates continuous improvement and innovation in automated systems.
In summary, the advancement of sensor technology has been pivotal in transforming robotics and automation in mechanical engineering, making robots more capable, adaptable, and safe while enabling their application in a broader range of complex and high-precision tasks.
2. Question:
What are the ethical considerations associated with the deployment of autonomous robots in manufacturing, and how can mechanical engineers address these concerns?
Answer:
The deployment of autonomous robots in manufacturing introduces several ethical considerations that mechanical engineers must thoughtfully address to ensure responsible and beneficial integration of technology. Key ethical concerns include:
Job Displacement and Workforce Impact: Automation can lead to the displacement of workers, particularly in roles involving repetitive and manual tasks. This raises ethical questions about the societal responsibility of engineers and companies to support affected workers.
Addressing the Concern:
- Reskilling and Upskilling Programs: Implement training initiatives to help displaced workers transition to new roles that require different skill sets, such as robot maintenance, programming, and oversight.
- Collaborative Robotics: Utilize collaborative robots (cobots) that work alongside humans, enhancing productivity without entirely replacing human workers, thereby preserving employment opportunities.
Privacy and Data Security: Autonomous robots often rely on extensive data collection to operate effectively, raising concerns about the privacy of workers and the security of sensitive manufacturing data.
Addressing the Concern:
- Robust Data Protection Measures: Implement strong cybersecurity protocols to protect data collected by robots, ensuring that sensitive information is safeguarded against breaches and unauthorized access.
- Transparent Data Policies: Establish clear policies regarding data collection, usage, and storage, and communicate these policies to all stakeholders to build trust and ensure compliance with privacy regulations.
Safety and Liability: Ensuring the safety of human workers interacting with autonomous robots is paramount. Additionally, determining liability in case of accidents or malfunctions poses legal and ethical challenges.
Addressing the Concern:
- Comprehensive Safety Standards: Adhere to international safety standards and guidelines for robotic systems, incorporating features like emergency stop buttons, collision detection, and force-limiting technologies.
- Clear Liability Frameworks: Develop and follow clear protocols for accountability and liability in the event of accidents, ensuring that responsibilities are well-defined and legally compliant.
Bias and Fairness: Autonomous robots programmed with AI and machine learning algorithms may inadvertently perpetuate biases present in their training data, leading to unfair treatment of certain groups of workers or stakeholders.
Addressing the Concern:
- Bias Mitigation Strategies: Employ techniques to identify and eliminate biases in data sets used to train AI algorithms, ensuring that robot decision-making processes are fair and unbiased.
- Inclusive Design Practices: Involve diverse teams in the design and programming of autonomous robots to incorporate multiple perspectives and reduce the risk of inherent biases.
Environmental Impact: The production, operation, and disposal of autonomous robots can have significant environmental consequences, including energy consumption and electronic waste generation.
Addressing the Concern:
- Sustainable Design Principles: Design robots with energy efficiency in mind, utilizing recyclable materials and minimizing waste during production.
- Lifecycle Assessments: Conduct comprehensive assessments of the environmental impact of robots throughout their lifecycle, implementing strategies to mitigate negative effects and promote sustainability.
Human Dignity and Autonomy: The increasing reliance on autonomous robots may impact the sense of autonomy and dignity among workers, particularly if robots take over tasks that provide meaningful work and personal fulfillment.
Addressing the Concern:
- Human-Centric Automation: Design robotic systems that complement human work rather than replace it, allowing workers to engage in more creative, strategic, and fulfilling tasks.
- Stakeholder Engagement: Involve workers and other stakeholders in the planning and implementation phases of automation projects to ensure that their needs and concerns are addressed, fostering a collaborative and respectful work environment.
Conclusion: Mechanical engineers play a crucial role in addressing the ethical implications of deploying autonomous robots in manufacturing. By prioritizing job preservation, data security, safety, fairness, environmental sustainability, and human-centric design, engineers can ensure that automation advancements contribute positively to society while minimizing adverse impacts. Ethical considerations should be integrated into every stage of the design, development, and implementation process to promote responsible and equitable use of robotics and automation technologies.
3. Question:
In what ways can robotics and automation contribute to sustainable manufacturing practices, and what specific technologies are most effective in reducing the environmental footprint of mechanical engineering industries?
Answer:
Robotics and automation can significantly contribute to sustainable manufacturing practices by enhancing efficiency, reducing waste, optimizing resource utilization, and minimizing energy consumption. Specific technologies within robotics and automation are particularly effective in lowering the environmental footprint of mechanical engineering industries:
Energy-Efficient Robotics:
- Technology: Robots equipped with energy-efficient motors and smart control systems that optimize power usage based on task requirements.
- Contribution: Reduces overall energy consumption in manufacturing processes, leading to lower carbon emissions and operational costs.
Precision Manufacturing:
- Technology: Automated systems with high precision and repeatability, such as CNC machines and robotic assembly lines.
- Contribution: Enhances material utilization by minimizing errors and reducing scrap rates, thereby conserving raw materials and lowering waste generation.
Additive Manufacturing (3D Printing):
- Technology: 3D printers integrated with automated material handling and recycling systems.
- Contribution: Enables on-demand production, reducing overproduction and material waste. Additionally, additive manufacturing often uses less material compared to traditional subtractive methods.
Automated Recycling and Waste Management:
- Technology: Robotics systems designed for sorting, disassembling, and recycling materials from manufacturing waste streams.
- Contribution: Improves the efficiency and effectiveness of recycling processes, reducing landfill waste and promoting the reuse of valuable materials.
Smart Manufacturing and IoT Integration:
- Technology: Internet of Things (IoT) sensors and AI-driven analytics integrated with automated manufacturing systems.
- Contribution: Facilitates real-time monitoring and optimization of energy and resource usage, identifying inefficiencies and enabling proactive adjustments to minimize environmental impact.
Collaborative Robots (Cobots) for Resource Optimization:
- Technology: Cobots that work alongside humans to optimize workflows and reduce energy and material usage.
- Contribution: Enhances the flexibility and efficiency of manufacturing processes, allowing for better resource management and reduced operational waste.
Automated Quality Control and Defect Detection:
- Technology: Vision systems and AI algorithms integrated into automated inspection processes.
- Contribution: Detects defects early in the production cycle, reducing the need for rework and minimizing material waste associated with faulty products.
Renewable Energy Integration:
- Technology: Automated systems that manage and integrate renewable energy sources, such as solar panels and wind turbines, into manufacturing operations.
- Contribution: Enhances the sustainability of manufacturing facilities by increasing the use of clean energy and reducing reliance on fossil fuels.
Material Handling and Logistics Automation:
- Technology: Automated guided vehicles (AGVs) and robotic logistics systems for efficient material transport and inventory management.
- Contribution: Optimizes the flow of materials, reducing energy consumption and minimizing the carbon footprint associated with transportation within manufacturing facilities.
Lifecycle Assessment and Environmental Monitoring:
- Technology: Integrated software and automation tools that conduct lifecycle assessments and monitor environmental parameters.
- Contribution: Provides comprehensive insights into the environmental impact of products and processes, enabling informed decisions to enhance sustainability throughout the product lifecycle.
Case Studies and Examples:
Automotive Industry:
- Example: Automated assembly lines equipped with energy-efficient robots and precision welding systems reduce energy consumption and material waste, contributing to more sustainable vehicle manufacturing.
Aerospace Manufacturing:
- Example: Additive manufacturing techniques used for producing lightweight aerospace components minimize material usage and reduce the overall weight of aircraft, enhancing fuel efficiency and lowering emissions.
Electronics Manufacturing:
- Example: Automated recycling systems for electronic waste ensure the efficient recovery and reuse of valuable materials like metals and plastics, reducing environmental pollution and resource depletion.
Conclusion: Robotics and automation play a pivotal role in advancing sustainable manufacturing practices within mechanical engineering industries. By leveraging energy-efficient technologies, precision manufacturing, additive manufacturing, automated recycling, and smart manufacturing systems, industries can significantly reduce their environmental footprint. These technologies not only enhance operational efficiency and product quality but also contribute to the broader goals of sustainability and environmental stewardship, ensuring that manufacturing processes are both economically viable and environmentally responsible.
4. Question:
How do control algorithms in robotic systems influence their performance in complex manufacturing environments, and what advancements are being made to enhance these algorithms?
Answer:
Control algorithms are fundamental to the performance of robotic systems, particularly in complex manufacturing environments where precision, adaptability, and reliability are critical. These algorithms dictate how robots interpret sensor data, make decisions, and execute movements, directly impacting their efficiency and effectiveness. Key influences and advancements include:
Influence of Control Algorithms on Robotic Performance:
Precision and Accuracy: Sophisticated control algorithms ensure that robots perform tasks with high precision and accuracy, crucial for operations like assembly, welding, and machining where tolerances are tight.
Adaptability and Flexibility: Advanced algorithms enable robots to adapt to varying conditions and handle unexpected changes in the manufacturing environment, such as variations in material properties or dynamic obstacles.
Efficiency and Speed: Optimized control algorithms enhance the speed and efficiency of robotic movements, reducing cycle times and increasing throughput without compromising quality.
Stability and Reliability: Robust control algorithms maintain the stability of robotic systems under different loads and operational conditions, ensuring consistent performance and reducing the likelihood of errors or mechanical failures.
Energy Optimization: Control algorithms can manage the energy consumption of robotic systems by optimizing movements and power usage, contributing to more sustainable manufacturing practices.
Advancements in Control Algorithms:
Machine Learning and Adaptive Control:
- Advancement: Incorporation of machine learning (ML) techniques allows control algorithms to learn from data, adapt to new tasks, and optimize performance based on past experiences.
- Impact: Enhances the ability of robots to perform complex and varied tasks autonomously, improving flexibility and reducing the need for manual reprogramming.
Predictive Control:
- Advancement: Predictive control algorithms use models to forecast future states of the system and make proactive adjustments to maintain desired performance.
- Impact: Increases the accuracy and responsiveness of robotic systems, enabling them to anticipate and compensate for disturbances before they affect operations.
Real-Time Optimization:
- Advancement: Development of algorithms capable of real-time optimization of robotic trajectories and actions based on immediate sensor feedback.
- Impact: Enhances the efficiency and adaptability of robots in dynamic environments, allowing them to make instantaneous adjustments for optimal performance.
Hybrid Control Systems:
- Advancement: Combining different types of control strategies, such as deterministic and probabilistic methods, to leverage the strengths of each.
- Impact: Improves the robustness and versatility of control systems, enabling robots to handle a wider range of tasks and uncertainties in manufacturing environments.
Decentralized Control:
- Advancement: Implementing decentralized control architectures where multiple robots operate independently but cohesively within a system.
- Impact: Enhances scalability and fault tolerance in multi-robot systems, allowing for more complex and coordinated manufacturing processes.
Human-Robot Interaction (HRI) Control:
- Advancement: Developing control algorithms that facilitate intuitive and safe interactions between humans and robots, incorporating gesture recognition and natural language processing.
- Impact: Improves collaboration and safety in shared workspaces, making robots more user-friendly and accessible to non-expert operators.
Cyber-Physical Systems Integration:
- Advancement: Integrating control algorithms with cyber-physical systems (CPS) to enable seamless communication and coordination between digital and physical components.
- Impact: Enhances the synchronization and efficiency of automated manufacturing processes, allowing for more intelligent and interconnected robotic systems.
Case Studies and Examples:
Automotive Assembly Lines:
- Example: Advanced control algorithms enable robotic arms to adjust their welding parameters in real-time based on sensor feedback, ensuring consistent weld quality even with variations in material thickness or joint alignment.
Electronics Manufacturing:
- Example: Machine learning-based control systems allow robots to adapt to different circuit board layouts, automating the placement and soldering of components with high precision and minimal human intervention.
Aerospace Component Fabrication:
- Example: Predictive control algorithms manage the complex machining processes required for aerospace components, optimizing tool paths and reducing cycle times while maintaining stringent quality standards.
Conclusion: Control algorithms are pivotal in determining the performance and capabilities of robotic systems in complex manufacturing environments. Ongoing advancements in machine learning, predictive control, real-time optimization, and hybrid systems are enhancing the adaptability, precision, and efficiency of robots, enabling them to perform increasingly sophisticated tasks autonomously. As these algorithms continue to evolve, they will drive further innovations in robotics and automation, fostering more intelligent, reliable, and sustainable manufacturing practices in mechanical engineering.
5. Question:
What are the key differences between industrial robots and service robots in the context of mechanical engineering, and how do these differences influence their design and application?
Answer:
Industrial robots and service robots serve distinct purposes within mechanical engineering, each tailored to specific environments and tasks. Understanding the key differences between them is essential for their effective design and application.
Key Differences:
Purpose and Application:
- Industrial Robots:
- Purpose: Designed for repetitive, high-precision manufacturing tasks in controlled environments.
- Applications: Welding, painting, assembly, material handling, packaging, and machining in industries like automotive, electronics, and aerospace.
- Service Robots:
- Purpose: Designed to assist humans in non-manufacturing tasks, often in dynamic and less controlled environments.
- Applications: Healthcare (surgical robots, rehabilitation), domestic (vacuum cleaners, lawn mowers), hospitality (receptionists, delivery robots), and public services (security, maintenance).
- Industrial Robots:
Operating Environment:
- Industrial Robots:
- Environment: Typically operate in clean, structured, and controlled settings with minimal variability.
- Design Considerations: Robustness to industrial conditions, resistance to dust and chemicals, and integration with manufacturing systems.
- Service Robots:
- Environment: Operate in dynamic, unstructured, and variable environments alongside humans.
- Design Considerations: Adaptability to different settings, ability to navigate obstacles, safety features for human interaction, and user-friendly interfaces.
- Industrial Robots:
Mobility:
- Industrial Robots:
- Mobility: Generally stationary or mounted on fixed bases, though some, like Automated Guided Vehicles (AGVs), are mobile within defined paths.
- Design Focus: High payload capacity, precise positioning, and repeatability.
- Service Robots:
- Mobility: Often equipped with wheels, tracks, or legs to navigate various terrains and environments.
- Design Focus: Maneuverability, agility, and the ability to operate autonomously in diverse settings.
- Industrial Robots:
Interaction with Humans:
- Industrial Robots:
- Interaction: Limited or no direct interaction with humans; designed to work in segregated zones to ensure safety.
- Safety Measures: Physical barriers, safety cages, and emergency stop mechanisms to prevent accidents.
- Service Robots:
- Interaction: Frequent and direct interaction with humans, requiring advanced safety features and intuitive communication interfaces.
- Safety Measures: Collision detection, force-limiting actuators, and compliant materials to ensure safe and seamless human-robot collaboration.
- Industrial Robots:
Programming and Flexibility:
- Industrial Robots:
- Programming: Typically programmed for specific, repetitive tasks with high precision and speed.
- Flexibility: Limited flexibility; reprogramming for different tasks can be time-consuming and require specialized knowledge.
- Service Robots:
- Programming: Often equipped with AI and machine learning capabilities to adapt to new tasks and learn from interactions.
- Flexibility: High flexibility; designed to perform a wide range of tasks and adapt to changing requirements without extensive reprogramming.
- Industrial Robots:
Payload and Task Complexity:
- Industrial Robots:
- Payload: Capable of handling heavy loads and performing complex manufacturing operations with high precision.
- Task Complexity: Focused on complex, high-speed, and high-precision tasks that are critical to production efficiency and quality.
- Service Robots:
- Payload: Typically handle lighter loads, such as delivering items or performing household chores.
- Task Complexity: Emphasize versatility, user interaction, and the ability to perform a variety of tasks in different contexts.
- Industrial Robots:
Influence on Design and Application:
Design Priorities:
- Industrial Robots: Prioritize durability, precision, speed, and integration with manufacturing systems. They are built to withstand harsh industrial conditions and perform tasks consistently over long periods.
- Service Robots: Prioritize adaptability, safety, user-friendliness, and the ability to navigate complex environments. They are designed to interact smoothly with humans and adapt to varying tasks and settings.
Technological Integration:
- Industrial Robots: Often integrated with Manufacturing Execution Systems (MES) and Enterprise Resource Planning (ERP) systems for streamlined production workflows.
- Service Robots: Integrated with smart home systems, healthcare databases, and user interfaces to provide personalized and context-aware services.
Market and Economic Factors:
- Industrial Robots: Targeted towards large-scale manufacturing enterprises seeking to enhance production efficiency, reduce labor costs, and improve product quality.
- Service Robots: Targeted towards consumers, healthcare facilities, hospitality businesses, and public services aiming to enhance service delivery, improve convenience, and increase operational efficiency.
Conclusion: Industrial robots and service robots serve fundamentally different roles within mechanical engineering, each requiring distinct design considerations and technological features. Industrial robots are optimized for high-precision, repetitive manufacturing tasks in controlled environments, focusing on durability and integration with production systems. In contrast, service robots are designed for flexibility, safety, and adaptability, operating alongside humans in dynamic and unstructured settings. Understanding these differences is crucial for engineers to develop and implement robotic solutions that effectively meet the specific needs and challenges of their intended applications.
6. Question:
How do collaborative robots (cobots) enhance human-robot interaction in manufacturing settings, and what design features make them suitable for such environments?
Answer:
Collaborative robots, or cobots, are specifically designed to work alongside human workers in shared workspaces, enhancing human-robot interaction in manufacturing settings. Cobots bring several advantages that improve productivity, safety, and flexibility, making them highly suitable for collaborative environments. Key enhancements and design features include:
Enhancements to Human-Robot Interaction:
Increased Productivity: Cobots can handle repetitive, strenuous, or precise tasks, freeing human workers to focus on more complex and value-added activities. This division of labor enhances overall productivity and efficiency.
Flexibility and Adaptability: Cobots are easily reprogrammed and redeployed for different tasks, allowing manufacturers to adapt quickly to changing production demands without significant downtime or reconfiguration.
Safety and Ergonomics: Cobots are designed to operate safely alongside humans, reducing the risk of accidents and injuries. By taking over physically demanding tasks, they also contribute to better ergonomics and worker well-being.
Enhanced Precision: Cobots can perform tasks with high precision and repeatability, ensuring consistent quality in manufacturing processes while complementing the nuanced skills of human workers.
Ease of Use: Cobots are user-friendly, often featuring intuitive programming interfaces such as hand-guiding or teach pendants, allowing non-expert users to program and operate them with minimal training.
Design Features Making Cobots Suitable for Collaborative Environments:
Force and Speed Limiting:
- Feature: Cobots are equipped with sensors and control systems that limit their force and speed, preventing excessive force in case of unintended collisions with humans.
- Benefit: Ensures safe interactions by minimizing the risk of injury, making cobots suitable for close-proximity work alongside humans.
Advanced Sensing and Vision Systems:
- Feature: Cobots incorporate advanced sensors, such as proximity sensors, cameras, and tactile sensors, to detect human presence and respond accordingly.
- Benefit: Enhances situational awareness, enabling cobots to navigate around humans, adjust movements in real-time, and operate safely in dynamic environments.
Compliance and Lightweight Design:
- Feature: Cobots are designed with compliant joints and lightweight materials, allowing for more natural and flexible movements.
- Benefit: Facilitates smooth and adaptable interactions with human workers, enabling cobots to perform a variety of tasks without rigid constraints.
Intuitive Programming Interfaces:
- Feature: User-friendly programming tools, such as graphical interfaces, teach pendants, and hand-guiding capabilities, simplify the programming process.
- Benefit: Allows human workers with minimal technical expertise to program and customize cobots for specific tasks quickly and efficiently.
Modular and Compact Construction:
- Feature: Cobots often have a compact and modular design, allowing for easy integration into existing workstations and production lines.
- Benefit: Maximizes workspace utilization and facilitates the seamless addition of cobots to manufacturing processes without requiring extensive modifications.
End Effector Versatility:
- Feature: Cobots can be equipped with a variety of end effectors, such as grippers, welders, or assembly tools, tailored to specific tasks.
- Benefit: Enhances the versatility of cobots, enabling them to perform a wide range of functions and adapt to different manufacturing needs.
Real-Time Feedback and Learning:
- Feature: Some cobots incorporate machine learning algorithms that allow them to learn from human actions and improve their performance over time.
- Benefit: Enhances the ability of cobots to work more effectively with humans, optimizing their actions based on observed behaviors and preferences.
Collaborative Control Systems:
- Feature: Integrated control systems that facilitate smooth and coordinated movements between cobots and human workers.
- Benefit: Ensures harmonious collaboration, reducing the likelihood of interference and enhancing overall workflow efficiency.
Case Studies and Examples:
Automotive Assembly Lines:
- Example: Cobots assist human workers in assembling vehicle components, such as attaching parts or performing quality inspections. Their precision and consistency improve assembly quality while allowing workers to focus on tasks requiring dexterity and decision-making.
Electronics Manufacturing:
- Example: In electronics assembly, cobots handle delicate components like circuit boards, performing soldering or component placement with high accuracy. Human workers oversee the process and handle tasks that require intricate manipulation or problem-solving.
Food and Beverage Industry:
- Example: Cobots automate packaging and sorting processes, working alongside humans to increase throughput while maintaining hygiene standards. Their ability to handle repetitive tasks ensures consistent packaging quality.
Conclusion: Collaborative robots significantly enhance human-robot interaction in manufacturing settings by offering safe, flexible, and user-friendly automation solutions. Their advanced sensing capabilities, intuitive design features, and adaptability make them ideal for working alongside human workers, improving productivity, quality, and workplace safety. As cobot technology continues to evolve, their integration into diverse manufacturing environments will further transform mechanical engineering practices, fostering more efficient and harmonious human-robot collaborations.
7. Question:
What are the implications of integrating Internet of Things (IoT) technologies with robotics and automation in mechanical engineering, and how can this integration drive innovation in manufacturing processes?
Answer:
Integrating Internet of Things (IoT) technologies with robotics and automation in mechanical engineering has profound implications, driving innovation and transforming manufacturing processes. This convergence enables smarter, more connected, and highly efficient manufacturing environments, often referred to as “smart factories.” Key implications and drivers of innovation include:
Implications of IoT Integration:
Enhanced Connectivity and Communication:
- Implication: IoT enables seamless communication between robotic systems, machines, and other devices within the manufacturing ecosystem.
- Impact: Facilitates real-time data exchange, coordinated operations, and synchronized workflows, leading to more efficient and streamlined manufacturing processes.
Real-Time Monitoring and Control:
- Implication: IoT sensors collect and transmit data on various parameters such as temperature, pressure, vibration, and performance metrics.
- Impact: Provides real-time visibility into manufacturing operations, allowing for immediate adjustments, optimizing performance, and ensuring consistent quality.
Predictive Maintenance and Reduced Downtime:
- Implication: IoT-enabled robots and machinery can monitor their own health and predict potential failures before they occur.
- Impact: Minimizes unplanned downtime, extends the lifespan of equipment, and reduces maintenance costs by enabling proactive maintenance strategies.
Data-Driven Decision Making:
- Implication: The vast amount of data generated by IoT devices can be analyzed to gain insights into production trends, inefficiencies, and areas for improvement.
- Impact: Supports informed decision-making, continuous improvement, and strategic planning, enhancing overall manufacturing performance and competitiveness.
Increased Automation and Autonomy:
- Implication: IoT integration allows robots and automated systems to operate more autonomously, making decisions based on real-time data and predefined algorithms.
- Impact: Enhances the ability of manufacturing systems to adapt to changing conditions, perform complex tasks without human intervention, and increase overall operational efficiency.
Supply Chain Optimization:
- Implication: IoT connects manufacturing systems with supply chain partners, providing visibility into inventory levels, production status, and logistics.
- Impact: Enables just-in-time manufacturing, reduces lead times, and improves coordination across the supply chain, enhancing responsiveness and reducing costs.
Customization and Flexibility:
- Implication: IoT technologies allow for greater flexibility in manufacturing processes, enabling the production of customized products on-demand.
- Impact: Supports mass customization, allowing manufacturers to meet diverse customer needs without sacrificing efficiency or increasing costs significantly.
Driving Innovation in Manufacturing Processes:
Smart Manufacturing and Industry 4.0:
- Innovation: The integration of IoT with robotics is a cornerstone of Industry 4.0, driving the transformation of traditional manufacturing into smart, interconnected systems.
- Benefit: Enhances overall manufacturing intelligence, enabling systems to learn, adapt, and optimize themselves autonomously, leading to more resilient and efficient production environments.
Advanced Analytics and Machine Learning:
- Innovation: Leveraging IoT data with advanced analytics and machine learning algorithms enables predictive insights and optimization of manufacturing processes.
- Benefit: Drives continuous improvement, reduces waste, and enhances product quality by identifying patterns and trends that inform process adjustments and innovations.
Autonomous Production Lines:
- Innovation: IoT-enabled robots can autonomously manage production lines, adjusting workflows based on real-time demand, supply availability, and operational conditions.
- Benefit: Increases production agility, allowing manufacturers to respond swiftly to market changes and customer demands without significant delays or disruptions.
Enhanced Human-Robot Collaboration:
- Innovation: IoT facilitates better coordination between humans and robots, enabling more effective collaborative workflows and shared responsibilities.
- Benefit: Improves productivity and safety by ensuring that human workers and robots complement each other’s strengths, leading to more efficient and harmonious manufacturing operations.
Energy Management and Sustainability:
- Innovation: IoT technologies enable precise monitoring and management of energy usage within manufacturing facilities.
- Benefit: Optimizes energy consumption, reduces costs, and supports sustainability initiatives by identifying and eliminating energy inefficiencies.
Remote Monitoring and Control:
- Innovation: IoT allows for remote monitoring and control of manufacturing systems, enabling operations from virtually anywhere.
- Benefit: Increases operational flexibility, supports decentralized manufacturing models, and enhances the ability to manage multiple facilities from a central location.
Case Studies and Examples:
Automotive Manufacturing:
- Example: IoT-enabled robots in automotive assembly lines continuously monitor their performance and environmental conditions, adjusting their operations to optimize efficiency and maintain high-quality standards.
Electronics Production:
- Example: In electronics manufacturing, IoT sensors integrated with robotic systems provide real-time feedback on component placement and soldering quality, allowing for immediate corrections and reducing defect rates.
Aerospace Industry:
- Example: Aerospace manufacturers use IoT-connected robots to perform precision machining of complex components, with real-time monitoring ensuring adherence to strict tolerances and reducing material waste.
Conclusion: The integration of IoT technologies with robotics and automation is revolutionizing mechanical engineering by creating more intelligent, connected, and efficient manufacturing systems. This convergence drives innovation by enabling real-time monitoring, predictive maintenance, data-driven decision-making, and enhanced flexibility, ultimately leading to smarter manufacturing processes that are more responsive, sustainable, and competitive. As IoT and robotics continue to advance, their synergistic integration will play a crucial role in shaping the future of manufacturing, fostering continuous improvement and technological excellence.
8. Question:
How does the implementation of machine vision systems in robotics improve quality control in manufacturing, and what are the challenges associated with their deployment?
Answer:
The implementation of machine vision systems in robotics significantly enhances quality control in manufacturing by enabling automated inspection, precise measurements, and real-time defect detection. These systems leverage advanced imaging technologies and algorithms to analyze products during the manufacturing process, ensuring that only items meeting specified standards proceed through production. Key improvements and associated challenges include:
Improvements in Quality Control:
Automated Inspection:
- Benefit: Machine vision systems automate the inspection process, reducing the need for manual quality checks and increasing inspection speed.
- Impact: Enhances productivity by allowing continuous, high-speed inspections without fatigue, ensuring consistent quality across large production volumes.
Precision and Accuracy:
- Benefit: Machine vision systems provide high-resolution imaging and precise measurements, enabling the detection of minute defects that may be overlooked by human inspectors.
- Impact: Improves product quality by ensuring that all components meet stringent tolerances and specifications, reducing the likelihood of defective products reaching customers.
Real-Time Defect Detection:
- Benefit: Machine vision systems can identify defects in real-time, allowing for immediate corrective actions to be taken during the manufacturing process.
- Impact: Minimizes waste and rework by addressing issues promptly, ensuring that only quality products continue through the production line.
Data Collection and Analysis:
- Benefit: Machine vision systems collect extensive data on product quality, which can be analyzed to identify trends, root causes of defects, and opportunities for process improvement.
- Impact: Facilitates continuous improvement initiatives, enhancing overall manufacturing efficiency and product reliability.
Consistency and Reliability:
- Benefit: Machine vision systems operate with consistent performance, unaffected by human factors such as fatigue or distraction.
- Impact: Ensures uniform quality standards across all products, enhancing brand reputation and customer satisfaction.
Cost Reduction:
- Benefit: By reducing the reliance on manual inspections and minimizing defects, machine vision systems lower labor costs and decrease the expenses associated with rework and scrap.
- Impact: Increases profitability by optimizing quality control processes and reducing operational costs.
Challenges Associated with Deployment:
High Initial Investment:
- Challenge: The cost of purchasing, installing, and integrating machine vision systems can be substantial, particularly for small and medium-sized enterprises (SMEs).
- Solution: Conduct a thorough cost-benefit analysis to demonstrate long-term savings and ROI. Explore financing options or phased implementation strategies to spread out costs over time.
Complex Setup and Calibration:
- Challenge: Setting up machine vision systems requires precise calibration and configuration to ensure accurate inspections, which can be time-consuming and technically challenging.
- Solution: Invest in training for technical staff and work closely with system vendors to ensure proper setup and calibration. Utilize automated calibration tools where available to simplify the process.
Integration with Existing Systems:
- Challenge: Integrating machine vision systems with existing manufacturing equipment and control systems can be complex, requiring compatibility and seamless communication.
- Solution: Select machine vision systems that offer compatibility with current manufacturing infrastructure and standardized communication protocols. Collaborate with automation specialists to facilitate smooth integration.
Lighting and Environmental Conditions:
- Challenge: Variations in lighting and environmental conditions can affect the performance of machine vision systems, leading to inconsistent inspections.
- Solution: Implement controlled lighting environments and use appropriate lighting techniques, such as backlighting or structured lighting, to enhance image quality and consistency. Employ environmental sensors to monitor and adjust conditions as needed.
Software and Algorithm Development:
- Challenge: Developing and fine-tuning image processing algorithms to accurately detect defects can be complex and requires expertise in computer vision and machine learning.
- Solution: Utilize pre-built software solutions and libraries provided by machine vision vendors. Invest in training or collaborate with experts in computer vision to develop and optimize custom algorithms tailored to specific inspection needs.
Maintenance and Upkeep:
- Challenge: Machine vision systems require regular maintenance to ensure optimal performance, including cleaning lenses, updating software, and replacing components as needed.
- Solution: Establish a routine maintenance schedule and train staff to perform basic upkeep tasks. Implement monitoring systems to detect and address issues proactively before they impact inspections.
Scalability:
- Challenge: Scaling machine vision systems to accommodate increased production volumes or additional inspection points can be challenging and may require significant additional investment.
- Solution: Design systems with scalability in mind, selecting modular and expandable machine vision solutions that can be easily upgraded or expanded as production demands grow.
False Positives and Negatives:
- Challenge: Machine vision systems may produce false positives (incorrectly identifying defects) or false negatives (failing to detect actual defects), impacting the reliability of quality control.
- Solution: Continuously refine and train machine vision algorithms using diverse and representative data sets to improve accuracy. Implement multi-sensor validation or redundant inspection methods to enhance reliability.
Conclusion: Machine vision systems significantly enhance quality control in manufacturing by automating inspections, increasing precision, and enabling real-time defect detection. While their deployment presents challenges such as high initial costs, complex setup, and the need for specialized expertise, these can be effectively addressed through strategic planning, investment in training, and collaboration with technology providers. The benefits of improved product quality, increased efficiency, and cost savings make machine vision systems a valuable asset in modern mechanical engineering manufacturing environments.
9. Question:
How does the concept of Industry 4.0 integrate robotics and automation in mechanical engineering, and what transformative effects does this integration have on traditional manufacturing paradigms?
Answer:
Industry 4.0, often referred to as the Fourth Industrial Revolution, represents the convergence of digital technologies with manufacturing processes, fundamentally transforming traditional manufacturing paradigms. Central to Industry 4.0 are robotics and automation, which are integrated with advanced technologies such as the Internet of Things (IoT), artificial intelligence (AI), big data analytics, and cyber-physical systems. This integration leads to smarter, more efficient, and highly adaptable manufacturing environments. The transformative effects on traditional manufacturing paradigms include:
Integration of Robotics and Automation in Industry 4.0:
Connected Robotics:
- Integration: Robotics systems are interconnected through IoT networks, enabling seamless communication and data exchange with other machines, sensors, and control systems.
- Effect: Facilitates real-time monitoring, coordination, and optimization of robotic operations within the manufacturing ecosystem, enhancing overall system efficiency and responsiveness.
Smart Factories:
- Integration: Automated robots operate within smart factories equipped with interconnected devices and intelligent systems that continuously collect and analyze data.
- Effect: Creates highly flexible and adaptive production environments where manufacturing processes can be dynamically adjusted based on real-time data and predictive analytics.
Cyber-Physical Systems (CPS):
- Integration: Robotics and automation are integrated with CPS, which link physical processes with digital information systems through sensors, actuators, and computational algorithms.
- Effect: Enhances the synchronization between physical manufacturing operations and digital management systems, enabling more precise control, simulation, and optimization of production processes.
Data-Driven Decision Making:
- Integration: Robotics systems generate vast amounts of data during operations, which are analyzed using big data analytics and machine learning algorithms.
- Effect: Enables informed decision-making, predictive maintenance, process optimization, and continuous improvement, driving higher productivity and quality.
Autonomous Supply Chains:
- Integration: Automated robots manage inventory, handle logistics, and coordinate with supply chain partners through connected systems.
- Effect: Creates more efficient, transparent, and responsive supply chains that can adapt to changes in demand, supply disruptions, and other variables with minimal human intervention.
Transformative Effects on Traditional Manufacturing Paradigms:
Increased Flexibility and Customization:
- Traditional Paradigm: Manufacturing systems were often rigid, optimized for mass production of standardized products.
- Industry 4.0 Integration: Robotics and automation enable highly flexible production lines capable of producing customized and small-batch products efficiently, meeting diverse and changing consumer demands.
Enhanced Efficiency and Productivity:
- Traditional Paradigm: Production efficiency was limited by manual processes, labor constraints, and slower operational speeds.
- Industry 4.0 Integration: Automated robots operate continuously with high precision and speed, significantly boosting productivity and reducing cycle times.
Improved Quality and Consistency:
- Traditional Paradigm: Quality control relied heavily on manual inspections, which were time-consuming and prone to human error.
- Industry 4.0 Integration: Robotics equipped with machine vision and AI algorithms ensure consistent quality through precise, automated inspections and real-time adjustments, minimizing defects and variability.
Reduced Operational Costs:
- Traditional Paradigm: High labor costs, material waste, and inefficiencies contributed to elevated operational expenses.
- Industry 4.0 Integration: Automation reduces the need for manual labor, optimizes material usage, and minimizes waste, leading to lower production costs and higher profitability.
Enhanced Sustainability:
- Traditional Paradigm: Manufacturing processes often resulted in significant energy consumption and environmental impact.
- Industry 4.0 Integration: Smart automation systems optimize energy usage, reduce waste, and enable sustainable manufacturing practices through efficient resource management and eco-friendly production techniques.
Data-Driven Innovation:
- Traditional Paradigm: Innovation was slower due to limited data availability and reliance on traditional engineering approaches.
- Industry 4.0 Integration: The extensive data generated by automated systems drives continuous innovation, enabling the development of new products, processes, and business models based on empirical insights and advanced analytics.
Improved Workforce Roles:
- Traditional Paradigm: Workers were primarily engaged in manual, repetitive tasks with limited opportunities for skill development.
- Industry 4.0 Integration: The role of the workforce shifts towards more skilled positions involving programming, maintenance, data analysis, and oversight of automated systems, fostering a more knowledgeable and adaptable workforce.
Case Studies and Examples:
Automotive Manufacturing:
- Example: Leading automotive manufacturers have implemented interconnected robotic assembly lines that adapt in real-time to changes in production demand, enabling mass customization and reducing time-to-market for new models.
Electronics Production:
- Example: Electronics manufacturers use smart robots with integrated machine vision systems for precise component placement and soldering, ensuring high-quality products while minimizing defects and rework.
Aerospace Industry:
- Example: Aerospace manufacturers utilize cyber-physical systems to coordinate robotic machining and inspection processes, ensuring the production of complex and high-precision components required for aircraft and spacecraft.
Conclusion: The integration of robotics and automation within the framework of Industry 4.0 fundamentally transforms traditional manufacturing paradigms by introducing greater flexibility, efficiency, quality, and sustainability. This convergence fosters a more intelligent, responsive, and data-driven manufacturing environment, enabling mechanical engineering industries to innovate continuously, meet evolving market demands, and maintain a competitive edge in the global landscape. As Industry 4.0 technologies continue to advance, the synergy between robotics, automation, and digital systems will play a crucial role in shaping the future of manufacturing.
10. Question:
What role does human-robot collaboration play in modern mechanical engineering workplaces, and how can the integration of collaborative robots (cobots) influence workplace dynamics and productivity?
Answer:
Human-robot collaboration (HRC) is increasingly integral to modern mechanical engineering workplaces, fostering synergistic interactions between human workers and robotic systems. The integration of collaborative robots (cobots) profoundly influences workplace dynamics and productivity in several key ways:
Role of Human-Robot Collaboration:
Augmentation of Human Capabilities:
- Function: Cobots handle repetitive, strenuous, or hazardous tasks, allowing human workers to focus on tasks that require creativity, critical thinking, and complex decision-making.
- Impact: Enhances overall productivity by leveraging the strengths of both humans and robots, leading to more efficient and effective operations.
Improved Ergonomics and Worker Safety:
- Function: Cobots assist with heavy lifting, precise assembly, and repetitive motions, reducing the physical strain on human workers.
- Impact: Decreases the risk of musculoskeletal injuries and workplace accidents, promoting a healthier and safer work environment.
Enhanced Flexibility and Adaptability:
- Function: Cobots are easily reprogrammable and redeployable for different tasks, adapting to changing production needs without significant downtime.
- Impact: Increases the flexibility of manufacturing processes, enabling rapid adjustments to production schedules, product variations, and market demands.
Increased Productivity and Efficiency:
- Function: Cobots operate with high precision and consistency, performing tasks faster and more accurately than humans alone.
- Impact: Boosts production rates, reduces cycle times, and enhances overall operational efficiency, leading to higher output and lower production costs.
Facilitation of Knowledge Transfer and Skill Development:
- Function: Cobots can serve as training tools, assisting less experienced workers and facilitating the transfer of skills and knowledge.
- Impact: Enhances the skill levels of the workforce, fostering continuous learning and development, and preparing workers for more advanced roles in automation and robotics.
Influence on Workplace Dynamics:
Enhanced Teamwork and Collaboration:
- Impact: Promotes a collaborative environment where humans and robots work together seamlessly, enhancing teamwork and communication among workers.
- Example: In an assembly line, cobots handle repetitive screwdriving while humans manage component placement and quality inspection, creating a cohesive workflow that maximizes each participant’s strengths.
Shift in Workforce Roles:
- Impact: Transforms traditional job roles by shifting workers from manual, repetitive tasks to more strategic, supervisory, and maintenance-oriented roles.
- Example: Workers may transition to roles such as robotic system supervisors, maintenance technicians, or process analysts, requiring new skills and expertise.
Increased Job Satisfaction and Engagement:
- Impact: Reduces the burden of monotonous and physically demanding tasks, allowing workers to engage in more meaningful and intellectually stimulating activities.
- Example: Employees can focus on optimizing production processes, innovating new products, or engaging in creative problem-solving, leading to higher job satisfaction and morale.
Change in Workplace Culture:
- Impact: Encourages a culture of innovation, continuous improvement, and technological proficiency as workers interact with and rely on advanced robotic systems.
- Example: A proactive approach to integrating cobots fosters a forward-thinking mindset, where workers are encouraged to embrace new technologies and contribute to their effective utilization.
Potential for Workforce Upskilling:
- Impact: Necessitates the acquisition of new skills related to robotics, programming, and system management, driving workforce upskilling and professional development.
- Example: Training programs focused on robotic maintenance, programming, and data analysis empower workers to manage and optimize collaborative robotic systems effectively.
Productivity Enhancements:
Reduced Downtime:
- Impact: Cobots can operate continuously without fatigue, ensuring consistent production flow and minimizing downtime associated with human breaks or fatigue-related errors.
- Example: In a packaging line, cobots can work alongside humans to maintain a steady pace, ensuring that production targets are met without interruptions.
Improved Quality and Consistency:
- Impact: Cobots perform tasks with high precision and repeatability, ensuring consistent product quality and reducing the incidence of defects.
- Example: In quality control, cobots equipped with machine vision systems can perform precise inspections, ensuring that only products meeting quality standards proceed through the production line.
Scalability and Rapid Deployment:
- Impact: Cobots can be quickly scaled up or down based on production needs, allowing manufacturers to respond swiftly to market fluctuations and demand spikes.
- Example: During peak production periods, additional cobots can be deployed to handle increased workloads, maintaining efficiency without the need for lengthy hiring processes.
Enhanced Data Collection and Process Optimization:
- Impact: Cobots equipped with sensors collect valuable data on production processes, enabling real-time monitoring and data-driven optimization.
- Example: Analyzing data from cobots performing assembly tasks can identify bottlenecks, optimize workflow sequences, and improve overall production efficiency.
Challenges and Considerations:
Initial Investment and ROI:
- Challenge: The upfront cost of acquiring and implementing cobots can be significant, and demonstrating a clear return on investment (ROI) is essential.
- Solution: Conduct comprehensive cost-benefit analyses to project ROI through increased productivity, reduced labor costs, and improved quality. Explore financing options or phased implementation to manage costs.
Training and Skill Development:
- Challenge: Workers need to acquire new skills to effectively collaborate with and manage cobots, necessitating investment in training programs.
- Solution: Implement ongoing training and professional development initiatives focused on robotics, programming, and system management to ensure workers are equipped to handle evolving technologies.
Integration with Existing Systems:
- Challenge: Integrating cobots into existing manufacturing systems and workflows can be complex and may require significant adjustments.
- Solution: Utilize modular and flexible cobot designs that can be easily adapted to existing processes. Collaborate with cobot vendors to ensure seamless integration and minimal disruption to operations.
Maintenance and Reliability:
- Challenge: Ensuring the reliable operation of cobots and minimizing downtime due to maintenance or technical issues is crucial for sustained productivity.
- Solution: Establish robust maintenance schedules, employ predictive maintenance techniques using IoT data, and ensure access to technical support and spare parts to maintain cobot reliability.
Conclusion: Human-robot collaboration, facilitated by collaborative robots (cobots), plays a pivotal role in modern mechanical engineering workplaces by augmenting human capabilities, enhancing productivity, and improving workplace safety and satisfaction. The integration of cobots fosters a collaborative environment where humans and robots complement each other’s strengths, driving efficiency, quality, and innovation. By addressing challenges related to investment, training, integration, and maintenance, engineers and manufacturers can effectively harness the benefits of HRC, transforming workplace dynamics and achieving higher levels of operational excellence.
11. Question:
What advancements in artificial intelligence (AI) are enhancing the autonomy and decision-making capabilities of robots in mechanical engineering applications?
Answer:
Advancements in artificial intelligence (AI) are significantly enhancing the autonomy and decision-making capabilities of robots in mechanical engineering applications. These advancements enable robots to perform complex tasks, adapt to dynamic environments, and make informed decisions without constant human intervention. Key AI advancements and their impacts include:
1. Machine Learning and Deep Learning:
- Advancement: Machine learning (ML) and deep learning (DL) algorithms allow robots to learn from data, recognize patterns, and improve their performance over time.
- Impact: Enables robots to adapt to new tasks and environments by learning from past experiences and optimizing their actions based on accumulated knowledge.
- Example: In quality control, robots can use ML algorithms to identify defects in products by analyzing large datasets of images, improving defect detection accuracy and speed.
2. Computer Vision:
- Advancement: Advanced computer vision techniques, powered by AI, enable robots to interpret and understand visual data from cameras and sensors.
- Impact: Enhances robots’ ability to perform tasks such as object recognition, navigation, and manipulation with high precision.
- Example: In assembly lines, robots equipped with computer vision can identify and handle components accurately, even when they are irregularly placed or oriented.
3. Natural Language Processing (NLP):
- Advancement: NLP allows robots to understand and respond to human language, facilitating more intuitive and seamless interactions between humans and robots.
- Impact: Enables robots to follow verbal instructions, engage in dialogue, and collaborate more effectively with human workers.
- Example: Service robots in manufacturing facilities can receive verbal commands from supervisors, allowing for more flexible and efficient task management.
4. Reinforcement Learning:
- Advancement: Reinforcement learning (RL) enables robots to learn optimal actions through trial and error, receiving rewards or penalties based on their performance.
- Impact: Facilitates the development of autonomous robots that can optimize their behavior in complex and uncertain environments.
- Example: Autonomous mobile robots can use RL to navigate through dynamic warehouse environments, improving their routing and task completion efficiency over time.
5. Autonomous Decision-Making:
- Advancement: AI-driven decision-making systems allow robots to analyze data, assess situations, and make informed decisions independently.
- Impact: Enhances the autonomy of robots, enabling them to handle unexpected scenarios and make real-time adjustments to their operations.
- Example: In predictive maintenance, robots can autonomously decide when to perform maintenance tasks based on sensor data and predictive analytics, reducing downtime and extending equipment lifespan.
6. Swarm Intelligence:
- Advancement: Swarm intelligence algorithms enable multiple robots to work collaboratively, sharing information and coordinating their actions to achieve common goals.
- Impact: Improves the efficiency and scalability of robotic systems, allowing for complex tasks to be completed more effectively through collective intelligence.
- Example: In large-scale manufacturing, swarm robots can coordinate to manage inventory, perform assembly tasks, and optimize production workflows collaboratively.
7. Cognitive Computing:
- Advancement: Cognitive computing integrates AI technologies that mimic human thought processes, enabling robots to understand, reason, and learn from experiences.
- Impact: Enhances robots’ ability to perform higher-level cognitive tasks, such as problem-solving, decision-making, and learning from unstructured data.
- Example: Cognitive robots in research and development can assist engineers by analyzing complex data sets, generating insights, and suggesting design improvements.
8. Edge AI and Real-Time Processing:
- Advancement: Edge AI involves processing AI algorithms locally on the robot or within the manufacturing facility, enabling real-time data analysis and decision-making without relying on cloud computing.
- Impact: Reduces latency, enhances data privacy, and allows robots to respond immediately to changes in their environment, improving overall system responsiveness and reliability.
- Example: Real-time quality inspections using edge AI enable robots to detect and correct defects instantly, maintaining high production standards without delays.
Challenges and Considerations:
Data Quality and Quantity:
- Challenge: AI algorithms require large and high-quality datasets to train effectively.
- Solution: Implement robust data collection and management practices, ensuring that robots have access to comprehensive and accurate data for training and operation.
Computational Resources:
- Challenge: Advanced AI algorithms can demand significant computational power, which may be limited in embedded robotic systems.
- Solution: Utilize efficient AI models, leverage edge computing capabilities, and invest in hardware upgrades to support AI-driven functionalities.
Integration Complexity:
- Challenge: Integrating AI technologies with existing robotic systems can be complex and may require specialized expertise.
- Solution: Collaborate with AI and robotics experts, adopt modular and scalable AI frameworks, and invest in training for engineers to facilitate seamless integration.
Ethical and Safety Concerns:
- Challenge: Autonomous decision-making by robots raises ethical questions and safety concerns, particularly in collaborative environments.
- Solution: Develop and adhere to ethical guidelines for AI usage, implement robust safety protocols, and ensure transparency in decision-making processes to build trust and accountability.
Conclusion: Advancements in artificial intelligence are pivotal in enhancing the autonomy and decision-making capabilities of robots in mechanical engineering applications. By leveraging machine learning, computer vision, reinforcement learning, and other AI technologies, robots become more intelligent, adaptable, and capable of performing complex tasks with minimal human intervention. These advancements drive innovation, improve efficiency, and enable the creation of smarter manufacturing environments. As AI continues to evolve, its integration with robotics will further transform mechanical engineering, fostering more autonomous, reliable, and versatile robotic systems that meet the dynamic demands of modern manufacturing.
12. Question:
What are the key considerations for ensuring the cybersecurity of automated robotic systems in mechanical engineering, and how can vulnerabilities be effectively mitigated?
Answer:
Ensuring the cybersecurity of automated robotic systems in mechanical engineering is critical to protect against unauthorized access, data breaches, and potential disruptions to manufacturing operations. As robotics and automation become more interconnected and reliant on digital technologies, the risk of cyber threats increases. Key considerations and effective mitigation strategies include:
Key Considerations for Cybersecurity:
Network Security:
- Consideration: Automated robotic systems are often connected to local networks and the Internet, making them susceptible to cyber-attacks such as hacking, malware, and ransomware.
- Mitigation Strategy:
- Firewall Implementation: Deploy robust firewalls to control incoming and outgoing network traffic, preventing unauthorized access.
- Network Segmentation: Separate critical robotic systems from other network segments to limit the spread of potential cyber threats.
- Virtual Private Networks (VPNs): Use VPNs for secure remote access to robotic systems, ensuring encrypted data transmission.
Access Control:
- Consideration: Unauthorized access to robotic systems can lead to manipulation, data theft, or operational disruptions.
- Mitigation Strategy:
- Authentication Mechanisms: Implement strong authentication methods, such as multi-factor authentication (MFA), to verify user identities before granting access.
- Role-Based Access Control (RBAC): Assign permissions based on user roles, ensuring that individuals only have access to the systems and data necessary for their tasks.
- Regular Audits: Conduct periodic access audits to review and update user permissions, ensuring that access levels remain appropriate.
Data Protection:
- Consideration: Robotic systems generate and process vast amounts of data, which may include sensitive information related to manufacturing processes, intellectual property, and personal data.
- Mitigation Strategy:
- Encryption: Encrypt data at rest and in transit to protect it from unauthorized access and breaches.
- Data Minimization: Collect and store only the data necessary for robotic operations, reducing the potential impact of data breaches.
- Secure Data Storage: Use secure databases and storage solutions with built-in security features to safeguard sensitive information.
Software and Firmware Security:
- Consideration: Vulnerabilities in software and firmware can be exploited to gain unauthorized control over robotic systems.
- Mitigation Strategy:
- Regular Updates and Patches: Keep software and firmware up to date with the latest security patches to address known vulnerabilities.
- Secure Development Practices: Adopt secure coding practices during the development of robotic software to minimize vulnerabilities.
- Integrity Checks: Implement integrity verification mechanisms to ensure that software and firmware have not been tampered with.
Intrusion Detection and Prevention:
- Consideration: Detecting and responding to cyber threats in real-time is essential to prevent damage and minimize disruptions.
- Mitigation Strategy:
- Intrusion Detection Systems (IDS): Deploy IDS to monitor network traffic and identify suspicious activities that may indicate cyber-attacks.
- Intrusion Prevention Systems (IPS): Use IPS to automatically block or mitigate identified threats, preventing them from reaching critical robotic systems.
- Behavioral Monitoring: Implement behavioral analysis tools that detect anomalies in robotic system operations, indicating potential security breaches.
Physical Security:
- Consideration: Unauthorized physical access to robotic systems can lead to tampering, sabotage, or theft of hardware and data.
- Mitigation Strategy:
- Secure Access Points: Restrict physical access to robotic systems through secure doors, locks, and surveillance cameras.
- Authentication for Physical Access: Use access control systems, such as keycards or biometric scanners, to verify identities before granting physical access to sensitive areas.
Employee Training and Awareness:
- Consideration: Human error and lack of awareness can lead to security breaches, such as phishing attacks or inadvertent exposure of sensitive information.
- Mitigation Strategy:
- Cybersecurity Training: Provide regular training sessions for employees on cybersecurity best practices, recognizing threats, and responding to incidents.
- Security Policies: Establish and enforce comprehensive security policies that outline acceptable use, data handling, and incident reporting procedures.
Incident Response Planning:
- Consideration: Despite preventive measures, cyber incidents may still occur, necessitating a prepared and effective response.
- Mitigation Strategy:
- Incident Response Team: Assemble a dedicated team responsible for managing and mitigating cyber incidents involving robotic systems.
- Response Protocols: Develop and document clear incident response procedures, including containment, eradication, recovery, and communication strategies.
- Regular Drills: Conduct simulated cyber-attack drills to test and refine incident response plans, ensuring readiness in the event of an actual breach.
Effective Mitigation of Vulnerabilities:
Comprehensive Risk Assessment:
- Action: Conduct regular risk assessments to identify and evaluate potential cybersecurity threats to robotic systems.
- Benefit: Enables proactive identification of vulnerabilities and prioritization of security measures based on risk levels.
Adoption of Security Frameworks and Standards:
- Action: Implement industry-recognized cybersecurity frameworks and standards, such as ISO/IEC 27001 or NIST Cybersecurity Framework, to guide security practices.
- Benefit: Ensures that robotic systems adhere to best practices and meet established security criteria, enhancing overall protection.
Zero Trust Architecture:
- Action: Adopt a Zero Trust security model that assumes no implicit trust within the network, verifying every access request regardless of its origin.
- Benefit: Minimizes the risk of unauthorized access by continuously validating and enforcing security policies across all network interactions.
Redundancy and Backup Systems:
- Action: Implement redundant systems and regular data backups to ensure continuity and recovery in case of cyber incidents.
- Benefit: Enhances resilience by enabling quick restoration of operations and data integrity after a security breach or system failure.
Vendor and Supply Chain Security:
- Action: Evaluate and ensure the cybersecurity practices of vendors and suppliers involved in the development and maintenance of robotic systems.
- Benefit: Reduces the risk of supply chain-related vulnerabilities that could compromise the security of robotic systems.
Conclusion: Cybersecurity is a critical aspect of deploying automated robotic systems in mechanical engineering. By addressing key considerations such as network security, access control, data protection, and employee training, and by implementing robust mitigation strategies, engineers can effectively safeguard robotic systems against cyber threats. Ensuring the cybersecurity of these systems not only protects sensitive data and manufacturing processes but also maintains the integrity and reliability of automated operations, ultimately supporting the long-term success and sustainability of mechanical engineering industries.
12. Question:
How do advancements in collaborative robotics (cobots) influence the design principles and operational strategies in mechanical engineering manufacturing processes?
Answer:
Advancements in collaborative robotics (cobots) are fundamentally reshaping design principles and operational strategies in mechanical engineering manufacturing processes. These advancements enhance the synergy between human workers and robotic systems, driving more efficient, flexible, and innovative manufacturing environments. Key influences include:
Influence on Design Principles:
Human-Centric Design:
- Principle: Design manufacturing systems with a focus on augmenting human capabilities and ensuring safe and intuitive interactions between humans and cobots.
- Impact: Leads to the development of cobots that are ergonomically designed, easy to program, and capable of adapting to diverse human workflows, enhancing overall system usability and worker satisfaction.
Modularity and Flexibility:
- Principle: Design cobots with modular and flexible architectures that can be easily reconfigured for different tasks and integrated into various manufacturing setups.
- Impact: Enables rapid reconfiguration of production lines to accommodate new products or changes in demand, enhancing the adaptability and responsiveness of manufacturing systems.
Scalability:
- Principle: Develop scalable cobot solutions that can grow with manufacturing needs, allowing for incremental additions of cobots to meet increasing production demands.
- Impact: Facilitates gradual investment in automation, allowing manufacturers to scale operations without significant upfront costs or disruptions to existing workflows.
Safety by Design:
- Principle: Incorporate safety features into the design of cobots to ensure safe human-robot interactions, such as force-limiting actuators, collision detection, and compliant joints.
- Impact: Reduces the risk of accidents and injuries, promoting a safer workplace and enabling the integration of cobots in close proximity to human workers without the need for extensive safety barriers.
Intuitive Programming Interfaces:
- Principle: Design user-friendly programming interfaces that allow non-expert users to easily program and configure cobots for specific tasks.
- Impact: Lowers the barrier to entry for automation, enabling more widespread adoption of cobots across various manufacturing settings and empowering workers to customize cobot operations without specialized training.
Integration with Digital Systems:
- Principle: Ensure seamless integration of cobots with existing digital systems such as Manufacturing Execution Systems (MES), Enterprise Resource Planning (ERP) systems, and IoT platforms.
- Impact: Facilitates data exchange and coordination between cobots and other manufacturing components, enhancing overall system intelligence and enabling more efficient production management.
Influence on Operational Strategies:
Collaborative Workflows:
- Strategy: Develop workflows that leverage the strengths of both human workers and cobots, assigning tasks based on capabilities and optimizing the division of labor.
- Impact: Enhances overall productivity by ensuring that repetitive or physically demanding tasks are handled by cobots, while humans focus on tasks requiring creativity, problem-solving, and fine motor skills.
Continuous Improvement and Adaptation:
- Strategy: Implement continuous improvement practices that involve monitoring cobot performance, collecting feedback from workers, and iteratively refining cobot operations.
- Impact: Drives ongoing optimization of manufacturing processes, ensuring that cobots remain effective and aligned with evolving production needs and quality standards.
Flexible Production Lines:
- Strategy: Design production lines that can be easily reconfigured to switch between different products or adapt to changes in production volumes using cobots.
- Impact: Increases the flexibility and responsiveness of manufacturing systems, allowing for rapid adjustments to meet market demands and reducing lead times for product launches.
Enhanced Data Utilization:
- Strategy: Leverage data collected by cobots to gain insights into production processes, identify bottlenecks, and optimize operations through data-driven decision-making.
- Impact: Improves manufacturing efficiency, reduces waste, and enhances product quality by enabling informed adjustments and strategic planning based on empirical data.
Employee Empowerment and Engagement:
- Strategy: Involve employees in the integration and operation of cobots, fostering a collaborative environment where workers are engaged in optimizing and managing automated systems.
- Impact: Enhances job satisfaction and morale by enabling workers to focus on higher-value tasks and participate actively in the evolution of manufacturing processes.
Rapid Prototyping and Innovation:
- Strategy: Utilize cobots for rapid prototyping and experimentation, enabling quick iterations and testing of new designs and manufacturing techniques.
- Impact: Accelerates the innovation cycle, allowing manufacturers to develop and implement new products and processes more swiftly and effectively.
Sustainability and Resource Efficiency:
- Strategy: Implement cobot-driven processes that optimize material usage, reduce energy consumption, and minimize waste.
- Impact: Enhances the sustainability of manufacturing operations by promoting resource-efficient practices and reducing the environmental footprint of production processes.
Case Studies and Examples:
Automotive Assembly:
- Example: In automotive assembly lines, cobots assist with tasks such as installing components and performing quality inspections. Their flexibility allows for easy adaptation to different vehicle models, enhancing production efficiency and quality.
Electronics Manufacturing:
- Example: Electronics manufacturers use cobots for delicate tasks like soldering and component placement. The intuitive programming interfaces enable workers to quickly set up cobots for different circuit board designs, improving precision and reducing defects.
Aerospace Component Fabrication:
- Example: In aerospace manufacturing, cobots handle complex assembly tasks and perform inspections with high accuracy. Their integration with digital systems allows for real-time monitoring and optimization of production processes, ensuring adherence to stringent quality standards.
Conclusion: Advancements in collaborative robotics (cobots) are fundamentally influencing the design principles and operational strategies within mechanical engineering manufacturing processes. By focusing on human-centric design, flexibility, safety, and seamless integration with digital systems, cobots enhance human-robot collaboration, driving increased productivity, quality, and innovation. Their ability to adapt to diverse tasks and work alongside human workers transforms traditional manufacturing paradigms, enabling more efficient, responsive, and sustainable production environments. As cobot technology continues to evolve, their role in shaping the future of mechanical engineering and manufacturing will become increasingly pivotal, fostering more intelligent and collaborative industrial ecosystems.