Robotics and Automation in Electrical and Electronics Engineering
The field of Robotics and Automation in Electrical and Electronic Engineering (E&E) is transforming industries and everyday life through intelligent machines capable of performing complex tasks with precision. These systems are powered by advances in Signal Processing, which enables robots to interpret data from sensors and make decisions in real time. In environmental domains, robotics play a vital role in fields such as Environmental Engineering and Air Quality Engineering, where autonomous systems monitor and manage pollution, contributing to sustainability goals.
Modern automation systems are instrumental in addressing global challenges like Climate Change Mitigation and Adaptation. Drones and automated water management systems are enhancing practices in Ecological Engineering and Environmental Monitoring and Data Analysis. These robotic applications provide scalable solutions for environmental restoration and resource conservation, supported by frameworks from Environmental Policy and Management.
The integration of robotics into sustainable infrastructure has been further enabled through Green Building and Sustainable Design and Industrial Ecology and Circular Economy. These technologies support smart waste segregation in Waste Management Engineering and automated irrigation systems in Water Resources Engineering. Robotics also underpin energy generation efficiency in Renewable Energy Systems Engineering.
Manufacturing industries are the heart of robotic deployment. Foundational skills in Industrial and Manufacturing Technologies are essential for understanding how robots are used in smart factories and assembly lines. Technologies such as Additive Manufacturing (3D Printing) and Advanced Materials and Manufacturing Technologies enhance robot precision and functionality. The introduction of Digital Twin Technology allows real-time simulation and control, while Computer-Integrated Manufacturing (CIM) bridges digital models with physical processes.
Sustainable automation also emphasizes Energy and Resource Efficiency in Manufacturing and the integration of Human Factors and Ergonomics in Manufacturing. Robotics support safer working environments and enhance quality control measures in Manufacturing Quality Control and Assurance. Meanwhile, operational strategies such as Lean Manufacturing and supply chain optimization via Supply Chain Management are increasingly supported by robotic solutions. All of this converges in the domain of Smart Manufacturing and Industry 4.0, where robotics, AI, and connected technologies form a dynamic and efficient production ecosystem.
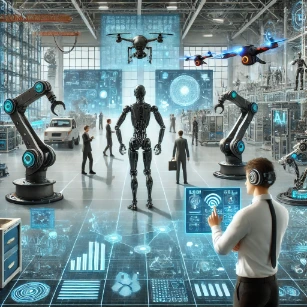
Table of Contents
Core Components of Robotics and Automation in Electrical and Electronics Engineering
- Mechanical Systems
Robots consist of physical components such as actuators, motors, joints, and linkages. These enable movement and interaction with the environment, forming the mechanical backbone of robotic systems. - Electronics and Sensors
Sensors are critical in robotics, allowing robots to perceive their environment. Key sensors include:- Vision Sensors: Cameras and LiDAR for object detection and navigation.
- Proximity Sensors: Ultrasonic or infrared sensors for obstacle avoidance.
- Force and Tactile Sensors: Measure physical interactions like pressure and touch.
- Environmental Sensors: Detect temperature, humidity, or other environmental factors.
- Control Systems
Control systems manage a robot’s movement and functions. They use feedback from sensors to adjust actions in real-time, ensuring precision and adaptability. - Software and Programming
Robots are programmed to perform specific tasks using algorithms and AI. Advanced robots can learn and adapt to new environments through machine learning techniques. - Power Systems
Robotics systems require energy sources such as batteries, fuel cells, or tethered power supplies. Energy efficiency and longevity are critical for mobile robots.
Applications of Robotics and Automation
- Manufacturing and Industrial Automation
Robots are widely used in manufacturing for tasks like assembly, welding, painting, and quality inspection. Key benefits include:- Increased Productivity: Robots work faster and longer than humans, boosting output.
- Precision and Consistency: Automated systems reduce errors and improve product quality.
- Safety: Robots perform hazardous tasks, minimizing risks to human workers.
Emerging trends include collaborative robots (cobots) that work alongside humans and flexible automation systems that adapt to different tasks.
- Healthcare and Medical Robotics
Robotics is transforming healthcare through applications such as:- Surgical Robots: Systems like the da Vinci Surgical System allow for minimally invasive procedures with high precision.
- Rehabilitation Robots: Assist patients in recovering mobility and strength after injuries.
- Robotic Prosthetics: Advanced prosthetics with sensors and AI enable natural movements.
- Caregiving Robots: Assist elderly or disabled individuals with daily tasks and monitoring.
- Autonomous Vehicles and Drones
- Self-Driving Cars: Autonomous vehicles use AI, sensors, and control systems to navigate roads safely. Companies like Tesla, Waymo, and others are advancing this technology.
- Drones (Unmanned Aerial Vehicles): Drones are used for delivery, surveillance, agricultural monitoring, and disaster response.
- Service Robots
Service robots assist in non-industrial tasks, including:- Hospitality: Robots serve as hotel concierges, waitstaff, or cleaners.
- Retail: Robots assist customers, manage inventory, or handle checkout processes.
- Household Robots: Devices like robotic vacuum cleaners, lawn mowers, and personal assistants (e.g., Alexa or Google Home).
- Agriculture (Agri-Robotics)
Robots are used in agriculture for tasks such as:- Planting and Harvesting: Automated systems increase efficiency and reduce labor costs.
- Monitoring and Maintenance: Drones and ground robots monitor crop health, detect pests, and apply fertilizers or pesticides.
- Precision Farming: Ensures optimal resource use by targeting specific areas for intervention.
- Logistics and Supply Chain
Robotics and automation streamline logistics processes, including:- Warehouse Automation: Robots manage inventory, sort packages, and handle goods.
- Autonomous Delivery: Robots and drones deliver products to customers.
- Automated Guided Vehicles (AGVs): Transport goods within factories or warehouses.
- Military and Defense
Robotics are used in defense for applications such as bomb disposal, reconnaissance, and surveillance. Autonomous systems can operate in hostile environments, reducing risks to human soldiers. - Space Exploration
Robots like NASA’s Perseverance Rover and robotic arms on the International Space Station perform tasks in extreme environments where human presence is challenging. - Entertainment and Media
Robots are used for special effects in movies, interactive exhibits, and even as performers in theme parks or events.
Challenges in Robotics and Automation
- High Development Costs
Designing and deploying advanced robotic systems require significant investment in research, development, and infrastructure. Developing cutting-edge robots involves expenses related to hardware prototyping, software engineering, testing environments, and specialized facilities. Companies often face a steep barrier to entry due to the capital-intensive nature of robotic technologies, particularly in industries like aerospace, manufacturing, and medical robotics. Beyond initial investment, ongoing maintenance and upgrades further strain financial resources, making it difficult for smaller enterprises or startups to compete with larger, well-funded players. Additionally, high development costs can slow innovation cycles and limit the speed at which new robotic applications reach the market, particularly in cost-sensitive sectors. - Technical Complexity
Integrating sensors, artificial intelligence (AI), machine learning algorithms, and control systems into reliable, functional robots poses significant engineering challenges. Each subsystem—mechanical, electrical, computational—must work seamlessly under unpredictable conditions. For example, autonomous vehicles must process input from multiple sensors such as LiDAR, radar, GPS, and cameras in real time to make safe navigation decisions. These integrations require precise calibration and synchronization, demanding cross-disciplinary collaboration and sophisticated testing protocols. Furthermore, technical glitches in a robot’s perception or movement subsystem can lead to failures in critical applications like surgical robotics or defense systems. As robotics expands into human-centric environments, systems must be robust against variability in user behavior and environment, a goal that remains difficult to achieve with current technologies. - Workforce Displacement
Automation may lead to job displacement in certain industries, raising concerns about the social and economic impact. Sectors like manufacturing, retail, and logistics are particularly susceptible to automation-driven restructuring, where repetitive or routine tasks are gradually offloaded to machines. While automation often creates new roles in programming, maintenance, and oversight, these positions require reskilling and may not be accessible to displaced workers without significant educational investment. This shift has led to heated debates on labor policy, minimum income guarantees, and the ethical responsibility of corporations in workforce transition. A comprehensive examination of this issue is provided in this Brookings Institution report on automation and job markets, which highlights the uneven regional and demographic impact of job losses caused by robotics and AI. - Ethical and Legal Concerns
Autonomous robots raise pressing questions about accountability, privacy, and safety, especially in applications like surveillance, predictive policing, or military operations. When a robot makes an error—such as misidentifying a threat or failing to respond to human intent—assigning liability becomes complex. Additionally, robots deployed in public or semi-public spaces often involve surveillance capabilities that may infringe upon civil liberties. Regulatory bodies worldwide are still developing legal frameworks to govern robotic deployment, particularly around data collection, bias in AI decision-making, and the appropriate level of human oversight. In high-risk applications such as autonomous weapons or law enforcement drones, these questions become not only legal but moral, prompting discussions about the limits of machine autonomy in life-and-death scenarios. - Energy Consumption
Mobile robots and autonomous vehicles must balance functionality with energy efficiency, particularly for long-duration or mission-critical tasks. Energy constraints affect battery-operated drones, robotic arms, delivery bots, and autonomous vehicles, which require lightweight yet high-capacity power systems. Inefficient energy management can lead to frequent recharging, reduced operational range, and system downtime. This is particularly challenging for robots operating in remote or inaccessible locations, such as disaster zones or deep-sea exploration, where energy resupply is not feasible. Furthermore, as AI processing becomes more sophisticated, it also becomes more energy-intensive, requiring more efficient hardware architectures and power-optimized software algorithms to sustain functionality without compromising performance.
Future Trends in Robotics and Automation
- AI-Powered Robotics
Robots integrated with AI and machine learning will become smarter, enabling them to learn from experience, make decisions, and perform complex tasks. - Soft Robotics
Soft robots, made from flexible materials, are being developed for delicate tasks, such as handling fragile items or assisting in medical procedures. - Swarm Robotics
Inspired by nature, swarm robotics involves multiple robots working collaboratively, much like ants or bees. Applications include search-and-rescue missions and environmental monitoring. - Human-Robot Collaboration
Collaborative robots (cobots) are designed to work safely alongside humans, enhancing productivity and enabling new applications in manufacturing, healthcare, and beyond. - Autonomous Systems
Advances in sensors, AI, and edge computing are driving the development of fully autonomous robots capable of operating independently in dynamic environments. - Miniaturization
Micro-robots and nanobots are being developed for applications like targeted drug delivery, minimally invasive surgeries, and environmental sensing. - Robotics as a Service (RaaS)
The RaaS model allows businesses to deploy robots without significant upfront investment, paying for usage as needed. - Advanced Haptics and Interfaces
Enhanced tactile feedback and intuitive control systems will make robots more accessible and easier to use in various applications.
Societal and Economic Impact of Robotics and Automation
The integration of robotics and automation is reshaping industries, economies, and daily life:
- Economic Growth: Increased productivity and innovation lead to economic expansion and new business opportunities.
- Improved Quality of Life: Robots reduce the burden of repetitive or hazardous tasks, allowing humans to focus on creative and strategic roles.
- Sustainability: Automated systems optimize resource use, reduce waste, and enhance energy efficiency.
Why Study Robotics and Automation in E&E
Integrating Electrical and Electronic Systems
Robotics and automation in electrical and electronic engineering (E&E) involves combining sensors, actuators, and controllers. Students learn how to build systems that perceive, decide, and act autonomously. This integration is essential for developing intelligent machines.
Industrial Applications and Smart Manufacturing
Students study automation technologies used in factories, logistics, and assembly lines. They learn how robots improve productivity, safety, and precision. These skills support Industry 4.0 and modern manufacturing systems.
Control Systems and Mechatronics
Robotics relies on precise control of motion and interaction. Students explore feedback systems, motor drivers, and real-time programming. This prepares them to design responsive and adaptive robotic platforms.
Artificial Intelligence and Machine Learning
Students explore how AI and machine learning enhance robotic capabilities. They learn how robots can learn from data, adapt to new environments, and make intelligent decisions. This knowledge positions them at the forefront of autonomous systems.
Emerging Fields and Career Prospects
Robotics and automation are expanding into healthcare, agriculture, and service industries. Students can work in research, development, or deployment of robotic systems. The field offers dynamic careers with real-world impact.
Robotics and Automation: Conclusion
By continuously evolving, robotics and automation are unlocking new possibilities, driving technological progress, and addressing global challenges. These technologies are redefining how society approaches everything from manufacturing to medicine, creating more efficient systems while also raising important ethical and policy considerations. Their impact extends well beyond industrial robots on factory floors—they are becoming embedded in everyday life through smart home devices, autonomous transportation, and AI-driven healthcare assistants. This integration is not only streamlining operations but also transforming the relationship between humans and machines.
In the workplace, robotics and automation are enabling organizations to increase productivity, improve safety, and reimagine roles that were once constrained by human limitations. Automated solutions are revolutionizing logistics and supply chains, while collaborative robots—or cobots—are enhancing human capabilities rather than replacing them entirely. In the healthcare sector, robotic systems are assisting in surgeries, physical therapy, and even mental health support, bringing precision and consistency to sensitive tasks. The adaptability of these technologies is fostering more inclusive environments where people with disabilities can benefit from assistive devices that enhance mobility and independence.
In transportation, autonomous vehicles and drones are streamlining delivery systems and enhancing mobility. These advancements are also being applied in disaster relief and search-and-rescue missions, where robotic systems can access environments that are dangerous or inaccessible to humans. Furthermore, agriculture is being transformed by precision robotics capable of planting, harvesting, and monitoring crops with minimal human intervention. These innovations are helping to address the growing global demand for food while minimizing environmental impact.
The educational and research sectors are also seeing significant benefits from automation. Robotics kits and programming platforms are being introduced at younger educational levels, cultivating future generations of engineers, scientists, and innovators. In advanced research environments, robots are being used to conduct experiments with extreme accuracy and speed, freeing human researchers to focus on theoretical and creative work. These developments not only advance knowledge but also democratize access to technological tools.
Despite their vast potential, robotics and automation bring with them critical considerations related to job displacement, data privacy, and algorithmic bias. Governments, industries, and educational institutions must work together to establish policies and training programs that ensure these technologies benefit all segments of society equitably. For instance, reskilling programs can help displaced workers transition into emerging fields, while ethical frameworks can guide the responsible deployment of autonomous systems in sensitive sectors.
As robotics continues to intersect with emerging technologies like AI, IoT, and quantum computing, its potential grows exponentially. This convergence is giving rise to smarter, more autonomous systems capable of learning, adapting, and making complex decisions in real time. By fostering interdisciplinary collaboration and investing in responsible innovation, society can harness robotics not only to solve technical problems but to improve quality of life on a global scale.
For an in-depth overview of recent developments in robotic systems and their societal impact, the IEEE Spectrum’s robotics section provides excellent analysis and case studies that capture the rapid pace of advancement in the field.
Ultimately, robotics and automation are not just technological tools—they are enablers of human potential. By embracing these technologies thoughtfully and strategically, we can address urgent global challenges such as aging populations, climate change, and food insecurity, while also unlocking entirely new realms of possibility. Their evolution will remain a cornerstone of innovation, shaping the future of work, healthcare, transportation, and beyond for generations to come.
Robotics and Automation: Review Questions with Answers:
1. What fundamental aspects of electrical engineering form the backbone of robotics and automation, and why are they crucial?
Answer:
Robotics and automation rely heavily on control theory, power electronics, and signal processing. Control theory provides the mathematical framework for guiding robot movements and automated processes. Power electronics ensure actuators, sensors, and microcontrollers receive stable, precise power. Signal processing interprets sensor data, enabling robots to perceive their surroundings accurately. By mastering these three pillars, engineers can design reliable, high-performance robots that respond dynamically to their environment or production line demands.
2. How do sensors and actuators collaborate to create an interactive feedback loop within robotic systems?
Answer:
Sensors capture real-world data—such as proximity, force, or temperature—and feed that information back to the robot’s controller. The controller processes these signals and commands actuators, including motors or pneumatic systems, to execute tasks like movement or gripping. This loop allows the robot to correct its actions if an error is detected or adapt to changing conditions. A well-designed feedback loop ensures accuracy, reduces energy wastage, and boosts safety in environments ranging from manufacturing to surgical robotics.
3. Why is the concept of degrees of freedom (DOF) essential in robotic arm design, and how does it affect a robot’s capabilities?
Answer:
Degrees of freedom refer to the number of independent ways a robot can move or orient itself. For instance, a robotic arm with six DOF can pivot, twist, and reach like a human arm. More DOF typically allow for more complex tasks and greater maneuverability. However, each additional DOF raises design complexity, cost, and control demands. Engineers balance necessary mobility with system simplicity—especially in industrial applications where a highly specialized robot might only need three or four DOF to effectively perform a repetitive task.
4. How does artificial intelligence (AI) enhance automation, and what challenges arise when integrating AI into robotic systems?
Answer:
AI—particularly machine learning and deep learning—helps robots make decisions or adapt behaviors. By analyzing sensor data or learned patterns, they can detect anomalies, predict equipment failures, or refine navigation in uncertain settings. Challenges include the computational intensity of AI algorithms, requiring powerful onboard or cloud-based processing. Additionally, ensuring safety and interpretability is vital: if an AI-driven robot’s decisions are opaque or unpredictable, it can undermine reliability. Through careful system design, robust training datasets, and fail-safes, engineers can harness AI to boost automation efficiency and adaptability.
5. Why is real-time control important in industrial automation, and how do engineers ensure minimal latency within robotic applications?
Answer:
Many processes—like welding lines, assembly operations, or collaborative robot tasks—demand millisecond-level responsiveness to maintain quality and safety. Engineers employ real-time operating systems (RTOS) or field-programmable gate arrays (FPGAs) to guarantee deterministic execution of control loops. Prioritizing critical tasks in software architecture and employing dedicated communication protocols (e.g., EtherCAT) also helps minimize latency. By carefully managing these factors, robots can sense and respond almost instantly to dynamic conditions on the factory floor, enhancing throughput and reducing error rates.
6. What advantages does robotic automation offer over manual labor in industrial environments, and when might manual processes still be preferable?
Answer:
Robotic automation excels in repetitive, hazardous, or high-speed tasks, improving productivity, consistency, and worker safety. Robots can work continuously without fatigue and maintain exacting precision, reducing rework and defects. However, manual processes remain advantageous for highly flexible tasks requiring dexterity or human judgment, especially when production volumes are low or parts vary significantly. In such cases, the cost of developing and deploying specialized robots may outweigh the benefits. A hybrid approach—human-robot collaboration—often delivers the best of both worlds, combining human adaptability with robotic strength.
7. How do collaborative robots (cobots) differ from traditional industrial robots, and what new design considerations do they introduce?
Answer:
Cobots are built to work safely alongside humans, featuring lightweight structures, force-limited joints, and advanced sensors that detect accidental contact. Safety measures (such as rounded edges, vision systems, or torque feedback) minimize the risk of injury. This differs from traditional industrial robots, which are typically fenced off because of high-speed, high-force operations. Designing cobots demands careful attention to collision detection, ergonomic interfaces, and intuitive programming methods. The result is a flexible, user-friendly machine that complements human labor rather than replacing it outright.
8. Why is energy efficiency becoming a greater priority in robotics and automation, and what methods can optimize energy consumption?
Answer:
As factories scale up automation, the cumulative power draw of numerous robots, actuators, and control systems grows significantly. Energy efficiency not only lowers operational costs but also aligns with sustainability targets. Methods to optimize consumption include lightweight robot arm designs that require less torque, regenerative braking in servo motors, and smart control algorithms that minimize movement or idle states. Engineers also implement power-saving modes, turning off non-essential subsystems when idle. By monitoring power flows in real time, systems can automatically adjust parameters to maintain throughput while minimizing waste.
9. What safety protocols govern automated production lines, and how do engineers incorporate fail-safes to protect workers and equipment?
Answer:
Standards like ISO 10218 and ANSI/RIA R15.06 define safety requirements for industrial robots and collaborative applications. Designers implement safety-rated sensors (light curtains, safety scanners) that halt robot motion if a person enters a restricted area. Emergency stop buttons, redundant controllers, and monitored start-up procedures further reduce risks. In advanced setups, geofencing or dynamic speed adaptation prevents collisions with mobile workers. Regular inspections, risk assessments, and training ensure that both humans and machines function optimally within clearly established operational limits.
10. How might emerging technologies, such as soft robotics and swarm automation, reshape the future of electrical engineering in robotics and automation?
Answer:
Soft robotics uses compliant, flexible materials to mimic biological organisms, enabling safer human interaction and the ability to handle delicate objects. This could expand automation to tasks previously unsuited for rigid machines, like fruit harvesting or surgical assistance. Swarm automation envisions large groups of simpler robots collaborating to complete complex tasks—reconfiguring themselves dynamically or covering large areas cooperatively. Both trends demand inventive approaches to control, power distribution, and communication protocols. For electrical engineers, it opens new frontiers in sensor integration, distributed processing, and biologically inspired circuit design, setting the stage for more adaptive, efficient, and resilient automated systems.
Robotics and Automation: Thought-Provoking Questions
1. How do control theory principles underpin robotic movements, and why is feedback crucial in creating precise and adaptive behaviors?
Answer:
Robotic systems rely on control theory to process sensory inputs and adjust actuator outputs in real time. The fundamental loop starts when sensors measure variables like position or velocity. A controller then calculates any differences from a target value (often called the error) and commands motors or other actuators to correct for that error. Feedback ensures that the robot constantly compares the measured state to the desired state, making small corrections as needed. This mechanism helps robots maintain balance, follow paths, or perform tasks accurately—even when unexpected changes occur. By incorporating advanced algorithms (like PID or more complex model-based strategies), robotics engineers fine-tune the response so that a system remains stable, responsive, and capable of adapting to dynamic environments.
2. How do electronic sensors shape a robot’s “awareness” of its surroundings, and what design considerations influence sensor selection?
Answer:
Sensors serve as the robot’s eyes, ears, and tactile interfaces, translating physical phenomena—light, force, distance—into electrical signals. Selection depends on the task: for instance, a robotic arm may rely on force-torque sensors to safely handle objects, while an autonomous vehicle uses LIDAR or radar to detect obstacles. Design factors include measurement range, accuracy, response time, and susceptibility to noise or interference. Because each environment poses distinct challenges—dusty factories, underwater operations, or bright outdoor conditions—engineers must weigh robustness, energy consumption, and cost. The right sensor suite is key for ensuring reliable perception that supports precise manipulation or navigation in real-world conditions.
3. In what ways do artificial intelligence and machine learning propel robotic automation beyond pre-programmed actions, and what new challenges arise?
Answer:
Traditional robots follow fixed routines, operating best in structured, unchanging settings. AI-driven robots, on the other hand, can learn from data, adapt to uncertainties, and even make predictive decisions. For example, a machine learning model might enable a robot to detect defects on an assembly line or identify the safest route through a crowded warehouse. While this flexibility enhances utility and productivity, it also introduces challenges like ensuring reliable real-time performance, managing huge datasets for training, and interpreting the “black box” decisions AI systems make. Additionally, safety and accountability become paramount, as robots that autonomously learn must not inadvertently violate operational constraints or pose risks to humans.
4. Why is system integration a significant hurdle in robotics and automation projects, and how can engineers mitigate complexity during development?
Answer:
A complete robotic system comprises many interdependent layers—mechanical design, electronics, sensors, power distribution, and control software. Coordinating these layers demands precise synchronization; a minor change in sensor data processing can cascade through the control logic, affecting actuator demands. Communication interfaces among modules must be both reliable and capable of real-time updates. To handle this complexity, engineers often adopt modular architectures where each subsystem is well-defined, with standardized communication protocols (like CAN bus or Ethernet-based industrial networks). Rigorous testing, simulation, and iterative prototyping help catch integration flaws early. Maintaining clear documentation and employing version control also foster collaboration, especially in larger, multi-disciplinary teams.
5. How do collaborative robots (cobots) transform human-robot interaction, and why is safety engineering vital for these applications?
Answer:
Cobots are designed to operate side by side with humans, handling tasks like repetitive assembly or heavy lifting while allowing people to manage more creative or intricate work. Because they share workspaces with humans, cobots must have built-in safety features: sensitive force-limited joints, proximity detection, and soft edges to minimize injury risks. Sensors that detect contact or unexpected obstructions are crucial for automatically slowing or halting movement. Achieving this safe collaboration requires balancing performance (like speed and payload capacity) with protective measures, so cobots can boost productivity without compromising human well-being. Proper hazard analysis, compliance with safety standards, and user training further ensure that cobots contribute effectively while staying safe to operate around people.
6. Why is energy efficiency increasingly important in automated systems, and which strategies can robotics engineers employ to reduce power consumption?
Answer:
As factories and warehouses scale up automation, the collective energy footprint of robots and auxiliary equipment can become significant. Energy efficiency lowers operational costs and aids sustainability goals. To achieve it, engineers may adopt lightweight materials or optimized mechanical designs that minimize torque requirements. Regenerative braking systems in robotic arms or mobile robots capture and reuse energy during deceleration or lowering motions. Intelligent power management—switching components off or to low-power states when idle—further reduces waste. On the software side, smoother motion planning helps robots avoid abrupt starts and stops, saving power while maintaining throughput. These techniques collectively deliver “green automation,” promoting both economic and environmental benefits.
7. How do advanced simulation and digital twins accelerate robotics development and deployment, and what limitations should teams be aware of?
Answer:
Simulation tools and digital twins let developers test robot behavior virtually, speeding up design iterations and lowering the costs of physical prototypes. By modeling everything from kinematics to sensor feedback and environmental factors, teams can refine control algorithms, verify collision avoidance, or optimize work cell layouts before building hardware. Digital twins—a real-time, data-driven mirror of the physical robot—enable performance monitoring and predictive maintenance. However, simulations only approximate reality; inaccuracies in modeling friction, sensor noise, or unforeseen human interactions can yield misleading results. To mitigate these gaps, regular validation against real-world tests is essential. This combined physical-virtual approach ensures that final deployments align closely with actual operational conditions.
8. In what scenarios does the complexity or cost of robotic automation outweigh the benefits, and why might manual processes remain preferred?
Answer:
High customization tasks—like artisan crafts or one-off product assembly—may prove too complex to automate cost-effectively. Designing and programming a specialized robot for low-volume, highly variable tasks can be both time-consuming and expensive. Maintenance and retooling further add overhead. Meanwhile, a trained human worker can switch techniques or tools on the fly. If the process demands nuanced judgment or highly dexterous manipulation, a human’s adaptability may outperform current robotic precision. Thus, while automation revolutionizes high-volume, predictable operations, a judicious analysis of cost, flexibility, and quality often decides if manual labor is more practical in certain niches.
9. How does global connectivity and the Industrial Internet of Things (IIoT) expand the role of automation in electrical engineering, and what challenges come with connected robots?
Answer:
IIoT-enabled robots link to cloud services, sharing sensor data for remote monitoring or advanced analytics. This connectivity supports preventive maintenance—identifying parts near failure before downtime occurs—and dynamic optimization, adjusting production lines based on real-time demand. Yet, such open communication channels can expose robots to cyber threats or data breaches if not secured rigorously. Latency can also affect real-time control, pushing critical tasks back to on-premise hardware. Achieving seamless integration calls for robust network infrastructure, strict cybersecurity protocols, and carefully chosen edge-cloud partitioning. When done right, connected automation fosters agility, letting factories reconfigure lines swiftly in response to global market shifts.
10. What educational paths and skill sets equip aspiring engineers to thrive in the evolving field of robotics and automation, and how can they remain adaptable?
Answer:
A solid foundation in electrical and mechanical engineering forms a core skill set. Further study in control systems, embedded programming, and sensor technology refines one’s knowledge of how robots sense and act. Familiarity with AI or machine learning broadens future opportunities as data-driven approaches expand. Just as importantly, strong problem-solving, teamwork, and communication skills enable engineers to collaborate across disciplines. Hands-on experience with robotics kits, internships, and hackathons can spark creativity and practical know-how. Because automation evolves rapidly, continual learning—through online courses, industry events, and cross-functional projects—ensures engineers stay ahead of emergent technologies and best practices.
11. How might future robots incorporate soft robotics or biomimetic designs, and what advantages do these approaches offer?
Answer:
Soft robotics replaces rigid metal joints with compliant materials—silicones, textiles, or shape-memory alloys—allowing robots to squeeze, stretch, or conform without damaging delicate items or surroundings. Biomimetic designs mimic nature’s solutions, from gecko-inspired grippers to octopus-like tentacles, opening possibilities for handling irregular shapes or maneuvering in tight spaces. These methods can be more robust to collisions and safer around humans. Engineers integrate sensors directly into the material, measuring strain or contact forces continuously. However, controlling flexible structures can be complex, requiring advanced kinematic models. Despite the challenges, soft and biomimetic designs herald a new generation of versatile robots that effortlessly adapt to the environment.
12. What societal impacts may arise as robotics and automation expand into new sectors, and how can engineers design systems responsibly?
Answer:
Automation can boost efficiency, productivity, and even safety by handling dangerous tasks. However, it may displace certain jobs, prompting discussions about retraining the workforce and reshaping economic roles. Engineers bear responsibility for ensuring inclusive designs—robots that aren’t just cost-effective but also considerate of human factors like ergonomics, skill levels, and cultural contexts. Transparent processes, open communication with stakeholders, and user-centered design can mitigate negative effects. By anticipating ethical dilemmas—data privacy, AI-driven decision-making, or potential misuse—engineers can build robust safeguards, align innovations with societal values, and contribute positively to job transformation and overall well-being.