Chemical Catalysis and Reaction Engineering
Chemical Catalysis and Reaction Engineering form the heart of modern chemical process industries, where transformation of raw materials into valuable products occurs with optimal efficiency and control. Students entering this field must build a firm foundation in Chemical Engineering, as it offers the basic principles of mass, heat, and momentum transfer essential to reactor design. Closely related areas such as Biochemical Engineering explore catalytic reactions driven by enzymes and microorganisms, blending biology with classical reaction engineering.
The ability to manage energy efficiently is essential in catalytic systems, linking this field with Chemical Energy Systems Engineering. The nature and durability of catalysts also demand expertise in Chemical Materials Engineering, where high-temperature behavior, surface area, and stability of materials are critical. To implement industrial-scale transformations, students need to master Chemical Process Engineering, which integrates reactors into plant-wide systems.
Modern chemical engineers increasingly rely on simulations and digital optimization, making Computational Chemical Engineering an indispensable tool for analyzing kinetics, modeling heat release, and minimizing by-products. Real-world applications extend to sectors like Food and Beverage Engineering, where enzymes or heterogeneous catalysts accelerate safe and consistent food processing. Research on surface reactions at the nano-level is advancing rapidly under Nanotechnology in Chemical Engineering.
Innovations in reactor lining, catalyst carriers, and polymers require knowledge of Polymer and Plastics Engineering. Large-scale chemical production facilities must work in harmony with structural elements planned by Civil Engineering experts, while execution logistics are typically coordinated through Construction Management. The safety of high-temperature or high-pressure catalytic operations also intersects with the knowledge found in Earthquake and Disaster Engineering.
Infrastructure planning for reactors must consider soil behavior, requiring collaboration with Geotechnical Engineering. Industrial reactor buildings are designed with principles from Structural Engineering to withstand mechanical loads and thermal expansion. Distribution and delivery of raw materials or products call on expertise in Transportation Engineering and broader layout designs informed by Urban and Regional Planning.
Water is a critical medium in many catalytic processes, whether as solvent or coolant, making Water Resources Engineering relevant for sustainability and environmental compliance. Electrical infrastructure for sensors, heaters, and mixers ties in closely with Electrical and Electronic Engineering. Emerging monitoring technologies from Biomedical Electronics can also be adapted for chemical safety systems.
Industrial communication protocols used in plant-wide process control stem from Communication Engineering. Control algorithms ensure that reactors operate under optimal temperature and concentration conditions, supported by Control Systems Engineering. Engineers deploy microcontrollers, actuators, and safety switches designed in Electronics Engineering and Embedded Systems and Microelectronics. Finally, the precision required in tracking reaction progress and maintaining compliance with regulatory bodies is made possible through Instrumentation and Measurement, cementing its importance in this discipline.
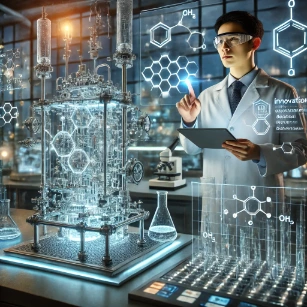
Table of Contents
Core Concepts in Chemical Catalysis and Reaction Engineering
Catalysis
- Definition: The process of increasing the rate of a chemical reaction by introducing a catalyst. Catalysts work by lowering the activation energy required for a reaction, allowing it to proceed more quickly and efficiently.
- Types of Catalysis:
- Homogeneous Catalysis: Catalysts and reactants are in the same phase (typically liquid).
- Heterogeneous Catalysis: Catalysts and reactants are in different phases (usually solid catalyst with gaseous or liquid reactants).
- Enzymatic (Biocatalysis): Biological catalysts (enzymes) are used for reactions under mild conditions.
- Catalyst Properties:
- Activity: Ability to accelerate reaction rates.
- Selectivity: Ability to direct the reaction toward a desired product.
- Stability: Resistance to deactivation over time.
Reaction Engineering
- Definition: The study and design of chemical reactors where chemical reactions occur. It involves analyzing reaction kinetics, thermodynamics, and transport processes to optimize production efficiency.
- Key Aspects:
- Reaction Kinetics: Study of reaction rates and mechanisms.
- Thermodynamics: Understanding energy changes and equilibrium.
- Mass and Heat Transfer: Ensuring efficient distribution of heat and reactants.
- Types of Reactors:
- Batch Reactors: Used for small-scale, high-value reactions.
- Continuous Stirred-Tank Reactors (CSTR): Well-mixed continuous processes.
- Plug Flow Reactors (PFR): High-efficiency continuous reactors for large-scale production.
- Packed Bed Reactors: Common in catalytic processes with solid catalysts.
Reaction Kinetics and Mechanisms
- Reaction Rate Laws: Mathematical expressions relating the rate of a reaction to the concentration of reactants.
- Catalytic Mechanisms:
- Adsorption: Reactants bind to the catalyst surface.
- Reaction: Transformation of adsorbed species into products.
- Desorption: Products detach from the catalyst surface.
Catalyst Design and Optimization
- Active Sites: Specific regions on the catalyst where reactions occur.
- Support Materials: Porous materials (e.g., alumina, silica) that disperse the active phase.
- Promoters and Inhibitors: Additives that enhance or suppress catalytic activity.
Process Integration and Scale-Up
- Lab-to-Plant Transition: Scaling up catalytic reactions from laboratory studies to industrial production.
- Process Intensification: Improving efficiency through novel reactor designs and heat integration.
Key Applications of Chemical Catalysis and Reaction Engineering
Petrochemical and Refining Industry
- Catalytic Cracking: Breaking down large hydrocarbon molecules into lighter fuels (e.g., gasoline, diesel) using zeolite catalysts.
- Hydrotreating: Removing sulfur and nitrogen compounds from fuels to meet environmental regulations.
- Catalytic Reforming: Converting low-octane hydrocarbons into high-octane gasoline components.
Chemical and Polymer Production
- Ammonia Synthesis (Haber-Bosch Process): Iron-based catalysts facilitate the production of ammonia for fertilizers.
- Ethylene Oxide Production: Silver catalysts oxidize ethylene to create a precursor for plastics and antifreeze.
- Polymerization Catalysts: Ziegler-Natta and metallocene catalysts for producing polyethylene and polypropylene.
Environmental and Emission Control
- Automotive Catalytic Converters: Platinum, palladium, and rhodium catalysts convert toxic gases (CO, NOₓ, hydrocarbons) into harmless emissions (CO₂, N₂, H₂O).
- Selective Catalytic Reduction (SCR): Converts nitrogen oxides (NOₓ) into nitrogen and water using ammonia and catalysts.
- Carbon Capture and Utilization (CCU): Catalytic processes for converting captured CO₂ into fuels and chemicals.
Renewable Energy and Sustainable Processes
- Hydrogen Production:
- Steam Methane Reforming (SMR): Uses nickel-based catalysts to produce hydrogen.
- Water Splitting: Photocatalysts and electrocatalysts split water into hydrogen and oxygen.
- Fuel Cells: Platinum-based catalysts drive electrochemical reactions to generate electricity.
- Biomass Conversion: Catalytic pyrolysis and hydroprocessing turn biomass into biofuels.
Fine Chemicals and Pharmaceuticals
- Asymmetric Catalysis: Producing chiral drugs with high purity using specialized catalysts.
- Green Chemistry: Catalytic reactions that minimize waste and energy consumption.
Emerging Technologies in Chemical Catalysis and Reaction Engineering
Nanocatalysis
- Definition: Utilizing nanoparticles as catalysts to increase surface area and activity.
- Applications:
- Hydrogen production, pollution control, and chemical synthesis.
Photocatalysis
- Definition: Using light-activated catalysts to drive chemical reactions.
- Applications:
- Water purification and solar fuel generation.
Electrocatalysis
- Definition: Catalysis of electrochemical reactions, essential for batteries, electrolyzers, and fuel cells.
- Applications:
- Green hydrogen production and CO₂ reduction.
Single-Atom Catalysts (SACs)
- Definition: Catalysts with isolated metal atoms dispersed on supports for maximum efficiency.
- Applications:
- Fine chemical synthesis and environmental remediation.
Artificial Intelligence (AI) in Catalyst Design
- Applications:
- Accelerating catalyst discovery and process optimization through machine learning.
Challenges in Chemical Catalysis and Reaction Engineering
-
Catalyst Deactivation:
- Loss of activity due to sintering, poisoning, fouling, or structural changes.
-
Selectivity Control:
- Designing catalysts to produce only the desired product while minimizing by-products.
-
Scale-Up and Process Integration:
- Transitioning novel catalytic processes from the lab to industrial scale.
-
Cost of Precious Metals:
- Reducing dependence on expensive catalysts like platinum and palladium.
-
Environmental Impact:
- Developing sustainable and green catalytic processes.
Future Directions in Chemical Catalysis and Reaction Engineering
-
Sustainable Catalysis:
- Developing recyclable and bio-based catalysts for greener processes.
-
Carbon Neutral Processes:
- Designing catalytic systems for carbon capture and utilization.
-
Integration with Renewable Energy:
- Using renewable electricity for catalytic hydrogen production.
-
Advanced Reactor Designs:
- Microreactors and modular reactors for process intensification.
-
Circular Economy Catalysis:
- Catalytic recycling of plastics and chemical waste.
Why Study Chemical Catalysis and Reaction Engineering
Understanding Chemical Reactions
This field examines how reactions occur and how to control them efficiently. Students study kinetics, thermodynamics, and reactor design. This knowledge is vital for developing industrial-scale chemical processes.
Catalyst Design and Mechanism
Students learn how catalysts accelerate reactions and influence selectivity. They explore material properties, surface science, and catalyst deactivation. Designing effective catalysts improves yields and reduces costs.
Reactor Engineering and Scale-Up
The course covers different reactor types and scale-up considerations. Students analyze residence time, mixing, and heat transfer. These skills support safe and efficient chemical production.
Applications in Green Chemistry
Catalysis enables cleaner and more sustainable chemical reactions. Students explore how to reduce waste and use renewable feedstocks. This aligns chemical engineering with environmental goals.
Industrial and Research Opportunities
Reaction engineering is critical in petrochemicals, pharmaceuticals, and materials science. Students can pursue roles in process development, R&D, or plant operations. The field is central to industrial innovation and efficiency.
Chemical Catalysis and Reaction Engineering: Conclusion
Chemical Catalysis and Reaction Engineering are at the core of modern chemical manufacturing, driving advancements in energy efficiency, sustainability, and environmental protection. Through innovative catalyst design and reactor optimization, this field enables the production of fuels, chemicals, and clean energy while reducing waste and emissions. As the global demand for sustainable solutions grows, catalysis and reaction engineering will continue to lead the way in transforming industries for a greener, more efficient future.Chemical Catalysis and Reaction Engineering: Review Questions and Answers:
What is chemical catalysis, and why is it important in industrial processes?
Answer: Chemical catalysis involves the acceleration of chemical reactions by substances called catalysts, which are not consumed in the reaction. Catalysts lower the activation energy required for reactions, increasing reaction rates and selectivity. In industrial processes, catalysis is crucial for enhancing efficiency, reducing energy consumption, and minimizing byproduct formation, leading to cost-effective and environmentally friendly manufacturing.
What are the main differences between homogeneous and heterogeneous catalysis?
Answer: In homogeneous catalysis, the catalyst and reactants are in the same phase, typically liquid, allowing for uniform interaction at the molecular level. This can lead to high selectivity but may pose challenges in catalyst separation and recovery. Heterogeneous catalysis involves catalysts in a different phase, usually solid, with reactants in liquid or gas phases. This facilitates easy separation and catalyst reuse but may involve complexities related to surface interactions and mass transfer limitations.
How does the design of a catalyst influence its activity and selectivity?
Answer: Catalyst design focuses on optimizing surface area, active site distribution, and electronic properties to enhance activity and selectivity. Porous materials with high surface areas provide more active sites for reactions. Modifying the electronic environment of active sites can alter adsorption energies, influencing reaction pathways and product distribution. Additionally, incorporating promoters or inhibitors can fine-tune catalyst performance for specific reactions.
What is reaction engineering, and how does it integrate with catalysis in chemical processes?
Answer: Reaction engineering involves the study and optimization of chemical reactions to design efficient reactors and processes. It integrates principles of kinetics, thermodynamics, and transport phenomena to scale reactions from the laboratory to industrial production. When combined with catalysis, reaction engineering focuses on selecting appropriate catalysts, designing reactors that maximize catalyst effectiveness, and controlling reaction conditions to achieve desired outcomes.
What are the key factors to consider in the design of a chemical reactor?
Answer: Designing a chemical reactor requires consideration of factors such as reaction kinetics, heat and mass transfer, mixing, residence time distribution, and pressure drop. Engineers must ensure that the reactor provides optimal conditions for the desired reaction, maintains temperature control to manage exothermic or endothermic processes, and allows for efficient removal of products to prevent inhibition or degradation.
How do fixed-bed and fluidized-bed reactors differ in terms of operation and applications?
Answer: Fixed-bed reactors consist of a stationary bed of catalyst particles through which reactants flow, typically used in processes like catalytic cracking and hydrogenation. They are simple in design but may face issues with heat and mass transfer limitations. Fluidized-bed reactors suspend catalyst particles in an upward flow of gas or liquid, enhancing mixing and heat transfer. They are suitable for reactions requiring uniform temperature distribution and are commonly used in processes like fluid catalytic cracking and gas-phase polymerization.
What role does mass transfer play in catalytic reactions, and how can limitations be addressed?
Answer: Mass transfer refers to the movement of reactants to and products away from the catalyst surface. In catalytic reactions, limitations in mass transfer can reduce reaction rates and catalyst effectiveness. To address these limitations, engineers can increase turbulence to enhance mixing, reduce catalyst particle size to shorten diffusion paths, or design reactors that promote better contact between reactants and catalysts.
How can reaction kinetics inform the optimization of industrial chemical processes?
Answer: Understanding reaction kinetics provides insights into the rates of chemical reactions and the influence of variables such as temperature, pressure, and concentration. This knowledge allows engineers to optimize conditions to maximize yield, selectivity, and efficiency. Kinetic models can predict reactor performance, guide scale-up from laboratory to industrial scale, and assist in troubleshooting operational issues.
What are some common methods for catalyst deactivation, and how can they be mitigated?
Answer: Catalyst deactivation can occur due to sintering (loss of active surface area), poisoning (strong adsorption of impurities), fouling (deposition of carbonaceous materials), or thermal degradation. Mitigation strategies include operating under conditions that minimize deactivation mechanisms, regenerating catalysts through treatments like oxidation or reduction, and designing catalysts with higher resistance to deactivation.
How is computational modeling utilized in the development of catalytic processes and reactor design?
Answer: Computational modeling employs mathematical simulations to predict the behavior of catalytic processes and reactor performance. Models can simulate reaction kinetics, mass and heat transfer, and fluid dynamics, providing insights that guide catalyst selection, reactor design, and process optimization. This approach reduces the need for extensive experimental trials, accelerates development, and enhances the understanding of complex reaction systems.
These questions and answers aim to provide a comprehensive understanding of chemical catalysis and reaction engineering, highlighting their significance in industrial applications and process optimization.
Thought-Provoking Questions with Detailed and Elaborate Answers on Chemical Catalysis and Reaction Engineering
Why are catalysts not consumed in a reaction, and how does this property make them indispensable in chemical processes?
- Answer: Catalysts facilitate chemical reactions by lowering the activation energy required for reactants to transform into products. They achieve this by providing an alternative reaction pathway with lower energy requirements. Since they do not chemically alter themselves in the process, they can repeatedly participate in reactions without being consumed. This property makes them highly efficient, allowing for continuous reactions and reduced operational costs in industrial processes.
What are the primary factors that influence the efficiency of a catalyst, and how can they be optimized?
- Answer: Catalyst efficiency is influenced by factors such as surface area, active site availability, and structural stability. Optimization involves increasing the catalyst’s surface area through nanostructuring, ensuring uniform distribution of active sites, and enhancing stability under operating conditions. Using promoters or modifying the electronic environment around the active sites can further enhance catalytic activity and selectivity.
How do homogeneous and heterogeneous catalysts differ in their applications, and what are the advantages and disadvantages of each?
- Answer: Homogeneous catalysts operate in the same phase as reactants, typically liquid, allowing for uniform interaction at the molecular level. They excel in selectivity but are challenging to separate and recycle. Heterogeneous catalysts exist in a different phase, often solid, and facilitate easier separation and reuse. However, they may encounter limitations in mass transfer and uniformity. The choice between the two depends on the specific reaction requirements and scalability.
What challenges arise when scaling up a catalytic process from the laboratory to an industrial scale, and how can these challenges be addressed?
- Answer: Challenges include maintaining reaction kinetics, heat and mass transfer efficiency, and catalyst stability at larger scales. Addressing these challenges involves using computational models to simulate scaling effects, designing reactors with optimized geometry, and conducting pilot-scale trials to refine operational parameters. Ensuring consistency in catalyst quality and performance across scales is also critical.
Why is reaction kinetics crucial for designing chemical reactors, and how can understanding reaction rates improve reactor performance?
- Answer: Reaction kinetics provides insights into the speed of chemical reactions and the factors affecting them, such as temperature, pressure, and reactant concentration. This knowledge is essential for designing reactors that maximize yield and efficiency. For example, understanding exothermic or endothermic reactions allows engineers to incorporate temperature control systems, preventing thermal runaway or inefficiencies.
How does the choice of reactor type impact the efficiency of catalytic reactions, and what factors determine the selection of a reactor?
- Answer: Reactor type impacts how reactants interact with the catalyst and the overall reaction efficiency. For example, fixed-bed reactors are ideal for stable processes with minimal fouling, while fluidized-bed reactors are preferred for processes requiring uniform temperature and high mass transfer rates. Factors like reaction kinetics, heat generation, product separation, and scalability influence reactor selection.
What role does surface chemistry play in heterogeneous catalysis, and how can it be tailored to improve catalyst performance?
- Answer: Surface chemistry determines how reactants adsorb, react, and desorb on a catalyst’s surface. Tailoring surface properties, such as roughness, porosity, and electronic configuration, enhances reaction rates and selectivity. For instance, doping a catalyst with specific metals can modify the electronic structure of active sites, influencing how reactants interact and reducing unwanted byproducts.
What are the environmental implications of using catalysts in chemical processes, and how can sustainable catalysis be achieved?
- Answer: Catalysts reduce energy consumption and byproduct formation, minimizing the environmental footprint of chemical processes. Sustainable catalysis can be achieved by developing catalysts from abundant, non-toxic materials, enhancing catalyst recyclability, and designing processes that use renewable feedstocks. These approaches align industrial practices with environmental sustainability goals.
How can reaction engineering contribute to the development of green chemistry principles in industrial applications?
- Answer: Reaction engineering supports green chemistry by designing processes that maximize atom economy, reduce hazardous waste, and utilize safer solvents. For example, engineers can optimize reaction conditions to eliminate unnecessary steps or intermediates, reducing energy and resource consumption. Incorporating renewable feedstocks and alternative energy sources like microwaves or solar energy further promotes green practices.
Why is catalyst deactivation a major challenge in industrial applications, and what strategies can be employed to mitigate it?
- Answer: Catalyst deactivation occurs due to fouling, poisoning, thermal degradation, or sintering. This reduces efficiency and increases operational costs. Strategies to mitigate deactivation include periodic regeneration, using more robust catalyst materials, and implementing pre-treatment steps to remove impurities from reactants. Engineering processes to operate within the catalyst’s stability range is also essential.
What is the significance of designing multi-functional catalysts, and how do they enhance reaction pathways?
- Answer: Multi-functional catalysts combine different active sites to facilitate sequential or simultaneous reactions, improving efficiency and selectivity. For example, in a tandem reaction, one active site may activate the reactant while another catalyzes the desired transformation. These catalysts reduce the need for separate reaction steps, saving energy and time.
How can advancements in artificial intelligence and machine learning accelerate innovations in catalysis and reaction engineering?
- Answer: AI and machine learning analyze large datasets to identify patterns, predict catalyst behavior, and optimize reaction conditions. These technologies enable faster screening of catalyst candidates, real-time process control, and predictive maintenance of reactors. By reducing trial-and-error experiments, AI accelerates innovation and enhances the efficiency of catalytic processes.
These thought-provoking questions aim to encourage critical thinking and exploration of the intricate concepts and applications in chemical catalysis and reaction engineering, fostering curiosity and innovation.